其中路线图包括轻量化技术在内的节能汽车、纯电动和混合动力汽车、燃料电池汽车、智能网联汽车和汽车制造、动力电池技术、汽车制造技术7大方向,内容如下图所示。
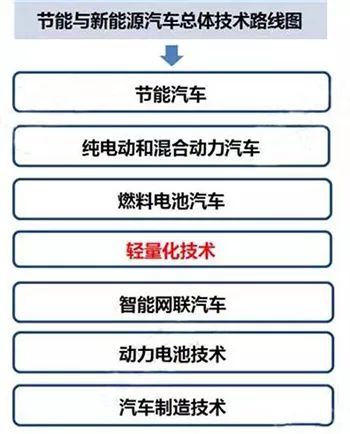
轻量化技术领域的相关研究得出,重量的减轻直接意味着续航里程的增加。如纯电动汽车整车重量若降低 10kg,续驶里程则可增加 2.5km,中国科学院杨院生教授在接受采访时表示,同样认同此结论,并补充到,提升电动汽车的续驶里程,除了加强电池和驱动系统之外,与车身轻量化的程度也密不可分,而车身轻量化最明显的特征就是材料的选择。目前,应用于新能源汽车的轻量化材料主要有高强度钢、铝合金、镁合金、碳纤维等几种。
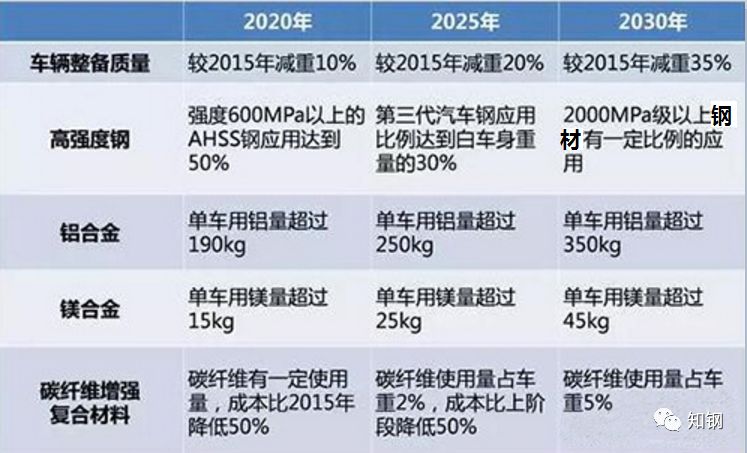
图示:轻量化材料的选择
接下来,小编就对以下几种轻量化材料的特性及应用做出梳理,供大家参考。
1、轻量化材料——高强度钢
应用于新能源汽车领域的高强度钢根据强化机理的不同,可分为普通高强度钢(Conventional HSS)和先进高强度钢(AHSS),先进高强度钢延塑性更好,在满足工艺性能的同时也具有更高的轻量化潜力。
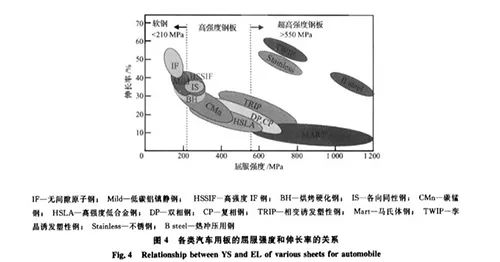
图示:高强度钢屈服强度情况
目前,国际主流车型的高强度钢占车身的比例已达70%以上,其中自主品牌中高强钢的应用已达45%。据了解,中国是高强度钢应用最普遍的国家,车身使用比例接近50%,预计未来可高达60-65%,但是超高强度和先进高强度钢材大幅落后,目前使用比例仅有5%,预计未来将有3倍提升空间。
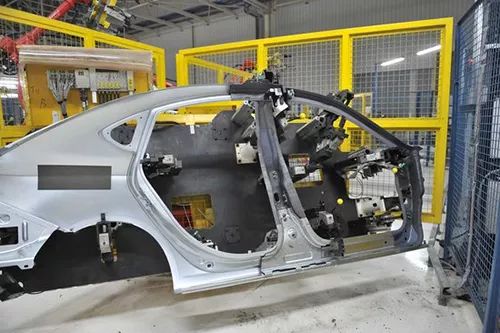
图示:高强度钢车身
业内专家认为,在抗碰撞性能、加工工艺和成本方面,高强度钢相比铝、镁合金具有明显的优势,能够满足减轻汽车质量和提高碰撞安全性能的双重需要,甚至从成本与性能角度来看,是目前满足车身轻量化、提高碰撞安全性的最佳材料。
2、轻量化材料——铝合金
铝的密度仅有钢铁的 1/3,导热性却比铁高出3倍有余。最值得一提的是,铝代钢的结构设计优化可以实现二次减重,效果可直接减重50%-100%。相关研究表明,汽车使用1 kg铝可替代自重2.25 kg钢材,减重比例高达125%,整个使用寿命周期内可减少废气排放20 kg。由此可见,铝合金凭借其高强度、可循环性、耐腐蚀、密度低等优质性能成为汽车减重首选材料,铝材在汽车上的使用量将快速增长,汽车用铝进入黄金期。
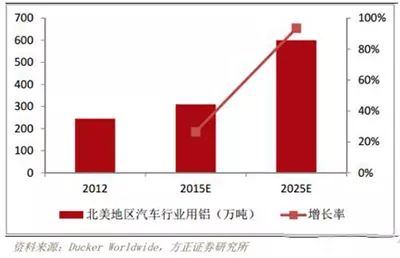
而国内车企对铝合金材料的应用中,就不得不提奇瑞新能源汽车,公司推出的新一代纯电动微型车——小蚂蚁(代号eQ1),在结构上采用了”全铝空间结构+全复合材料外覆盖件“的组合形式,很好的控制了车身重量,降低制造成本,实现了更好的车身轻量化。
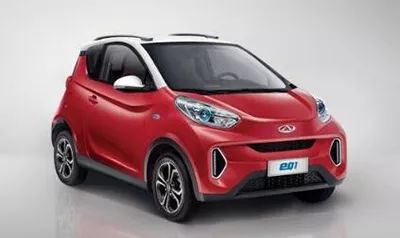
图示:小蚂蚁
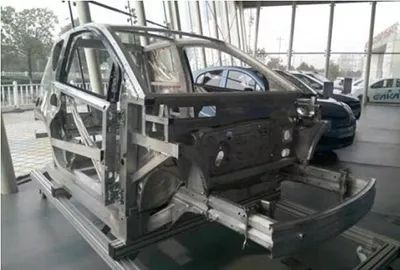
图示:全铝框架+复合材料外覆盖件
但全铝身的不足同样不容小觑,当车身受到碰撞损坏时,铝合金材质整形难度较高,一旦操作不当,零部件则很可能会出现裂纹甚至断裂,一般铝合金部件损坏后,如果钣金工艺无法调整好,基本上就只能整体更换。另外,铝合金材质需要特殊的工艺才能焊接。因此,全铝车身意味着后期的维修成本可能会更高。
特斯拉作为全球纯电动车的开拓者,在汽车轻量化的道路上也早已开始探索。其标志性车型Model S的车身就用到了大量的铝合金,并且通过特殊的焊接技术实现了铝合金构件与钢构件的链接。
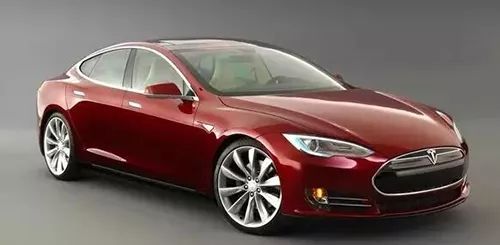
图示:特斯拉MODEL 3全铝车身
来源:纳米金属