简化的自动化HP-RTM
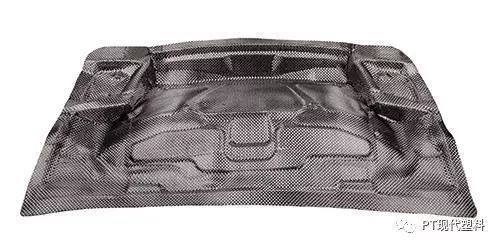
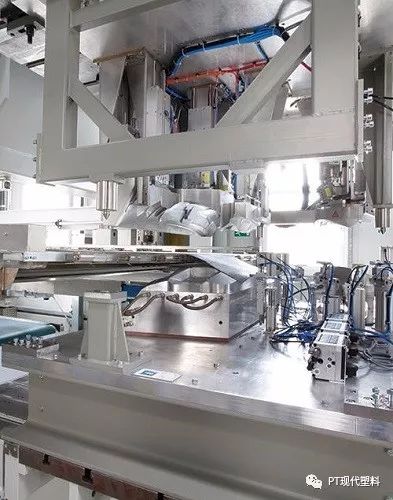
单一的穿梭系统:这台迪芬巴赫的 PreformCenter预成型设备正在利用一个穿梭式输送机,将碳纤维织物叠层放到模具上,成型出用于汽车行李箱盖内板的近净形状的预成型件。然后,该预成型件被放入RTM模具中,浇注树脂,固化后成型出最终部件
自2009年以来,迪芬巴赫还与宝马公司一起,开发了用于交替操作的“穿梭台”,它为压制CFRP结构部件而提供了最经济的方法。
一个穿梭台从压机中出来,便于CFRP部件的脱模,以及将下一个预成型件放入下模中。与此同时,另一个穿梭台进入压机,完成树脂浇注和固化。切换时间只需15秒。
在开发自动化的HP-RTM系统的过程中,这种穿梭台还启用了多种未知的管理,包括:循环时间、如何清洁模具、放入预成型件所需要的时间以及是否需要在闭合模具前进行在线检测以确保定位精准。
对应每个上半模,这种穿梭台需要两个下半模。
对模具而言,只要保持加热和电气元件的连接,所有的功能都能运行。
“自动化的HP-RTM系统现在已经是一项得到验证的技术。我们不必在每次循环后都要清洁模具,内脱模系统已取得了进步,偶尔清洗模具就可以实现连续的循环生产。”迪芬巴赫技术和业务开发总监Matthias Graf介绍说,“将预成型件放入压机中后,也没有必要进行质量检查,而且脱模不是一个大问题。”
迪芬巴赫还提供双穿梭台系统,但这要增加50%的工装投资。
基于每天三班倒的生产,一台单一的带有自动换模系统的迪芬巴赫压机(配一副拥有一个上模和一个下模的模具),一年可以生产出12万个部件,根据部件尺寸的不同,可以实现2~3分钟的循环时间。
“我们能够用90秒钟完成预成型。”Graf 说,“在此方面的进步包括减少了材料浪费。”
用于航空部件的自动化RTM系统
凭借位于德国奥格斯堡和德国斯塔德这两个主要研究基地的轻量化生产技术中心,德国国家航空航天研究机构DLR专注于自动化地生产用于航空、交通运输和能源领域的碳纤维增强塑料(CFRP)结构件。
DLR开发了EVo自动化生产线,每年能生产10万个复杂的复合材料部件。
作为开发工具,该生产线模拟现实生产环境来试用不同的材料、工艺参数和自动化概念。
EVo最初是为制造飞机框架和桁梁而设计的。它起始于2009年,当时,宝马正在大批量的生产中大量应用CFRP。也就在那时,下一代的空客A320正在被设想成采用CFRP来制造,但障碍在于,如何通过手工铺层预浸料来实现每年500架飞机的产量。
对于每架飞机200种机身框架以及每年500架飞机的产量而言,相当于每年要生产10万个框架,所以需要一条自动化的生产线。
开始,DLR想向一家供应商购买一条集成的生产线,但最终将这条生产线分成了6个单独的部分:
➤ 铺层制备
➤ 预成型
➤ 精细修整
➤ RTM
➤ 加热炉
➤ 软件
DLR找到了一家供应商,他能够与其他供应商合作,并能够开发一种标准,以实现所有单元的彼此“对话”。
DLR的净形状 RTM团队经理 Sven Torstrick介绍说,“他们做了主命令模块,它能创建加工方案、监控工艺过程并控制‘开始’和‘停止’功能。”
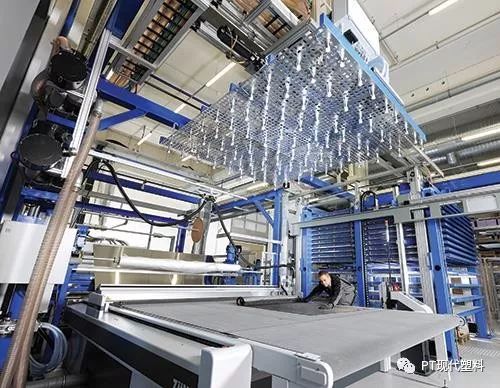
DLR的 EVo全自动 RTM生产线采用了集成在一起的自动化的切割机和铺层模块
“铺层制备”模块操作织物料卷,并将它们送到自动裁切机上。在此,依据数字裁切文件,不同的材料和铺层取向得到了制备。然后,将切下的叠层储存到一个货架系统中,机器人由此拾取叠层并将其放到一个与预成型区域交接的转送台上。
一个安装在屋顶的摄像系统,能够将信息反馈给机器人,然后机器人拾起这个叠层并将其放到部件上。
下一个模块是采用一台真空隔膜压机来对这些叠层进行组合:在隔膜上施加气压,在从叠层下方抽出空气的同时,采用红外加热来激活材料上的环氧粘结剂粉末,以使预成型件得到固结。
在机器人的操作下,“精细修整”模块将稳定的预成型件修整成净形状。这还使得EVo成为更加强大的生产设施,因为它防止了树脂在预成型件的周围流动,而这种流动会导致干点。
一副4部分的RTM模具,其外模拥有所有的加热通道。一台机器人将净形状的预成型件放入该模具的内/芯模中。芯模闭合,整套模具被移入RTM压机中,然后进入烤箱进行后固化。
EVo能够即刻浇注并固化不同的部件。试制的第一个部件是一个2m长的飞机框架,拥有V形曲线轮廓,其厚度和曲率半径沿长度而发生变化。
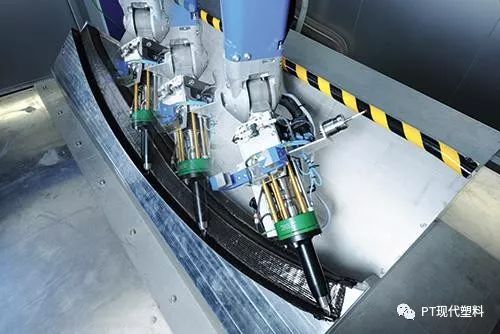
测试 EVo系统的局限性:此图显示的是 EVo 全自动 RTM 生产线中的 “精细修整 ” 模块正在修整一个测试用的 “Frankenframe” 预成型件,该预成型件的构思是,用于挑战该系统的能力,以在成型前获得净形状
“虽然还没有这样的实际部件,但我们收集了所有的潜在问题,并将它们集中到一个部件中,我们称其为‘Frankenframe’。”Torstrick解释说。
EVo生产线能够加工2.5m×2m×40cm的部件,从一个部件到下一个部件的目标时间是30~40min.,这能够显著减少快速固化树脂的用量。
“我们还能够生产汽车的车顶,并通过改变‘精细修整’区域,来纳入泡沫研磨操作,从而制造三明治结构的部件。”Torstrick说。
每分钟一个热塑性复合材料部件
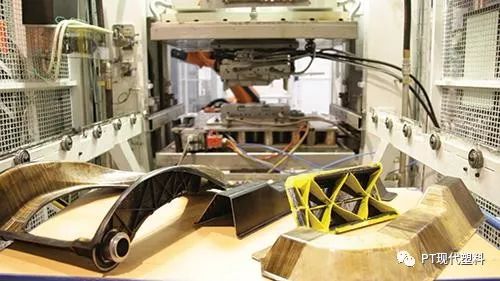
采用 QSP工艺试制的部件包括悬架臂(左下)、包覆成型的支架,以及主要采用碳纤维或天然纤维增强的尼龙 6制成的车身板(右下)
法国Pinette Emidecau Industries公司(简称“PEI”)是欧洲第一家为空中客车公司尝试使用热塑性复合材料而提供设备的供应商。
荷兰Fokker公司利用一台PEI的巨型Pinette压机来制造A330/A340的J型鼻翼结构。
目前,PEI正在将其专业知识转移到汽车复合材料的应用中:与一个联盟一起,为实现快速循环时间(即一分钟一个部件)而开发Quilted Stratum Process (QSP)工艺。
该联盟由法国机械工业技术中心Cetim、法国Loiretech公司和法国专业的模具公司Compose组成。
QSP工艺连同随后开发的一台冲压成形机,是法国用于生产复合材料结构的高速、高产量生产线的前两个组成部分。
利用QSP工艺,可以自动生产出采用多种叠层、厚度和材料取向的预成型件,同时还实现了功能集成并减少了废料。
安装在Cetim的这条原型生产线,主要用于加工尼龙6和碳纤维增强材料,但实际上,它可以采用一系列的热塑性材料生产出具有局部增强和订制增强的多种材料的预成型件。结合PEI压机的精度(足以确保实现模内涂层),其目标是A级表面。
采用QSP工艺试制的部件包括悬架臂、包覆成型的支架以及汽车车身板。
这条完全集成的生产线只用40~90s的循环时间,即生产出了8层、每层采用4个带材的预成型件。
确保高速生产的因素主要有:采用了高速红外加热炉和自动换模技术,该自动换模技术实现了60秒的即时换模(简称“SMED”)这一众所周知的精益制造标准。
除汽车部件外,QSP工艺的目标应用还包括飞机夹板、框架、座椅和发动机部件,以及起重机和农机的部件及连杆。
满足汽车行业的大批量生产需求

Fives Cincinnati公司用于生产汽车复合材料的集成的生产系统包括两套自动化的生产单元:第一套是集成了层切割机的铺带机,可提供近净形状的叠层套料(上);在一个成型-固化单元(下)中,输送带接收并将叠层套料放入模压成型设备中
美国Fives Cincinnati公司推出了一个含两套自动化制造单元的集成系统,用于汽车复合材料的生产:
➤ 一台带有层裁切机的铺带设备,可提供近净形状的套料叠层;
➤ 在成型-固化单元中,传送带收取并将这些套料叠层放入一台模压设备中,该设备由技术开发合作伙伴大陆结构塑料公司(美国密歇根州奥本山)提供。
与大陆结构塑料公司共同开发的这一热压成型工艺,适用于采用连续纤维增强复合材料生产结构部件。
Fives Cincinnati公司正在将其航空技术转移到汽车领域:第一步是采用其自动铺带技术或纤维铺放机来制备待用的平面料,目标是,在一步操作中,直接将二维的待用料变成三维的部件,但基于形状的复杂性,要求先对一些部件预成型,然后将预成型件送到固化模具中。
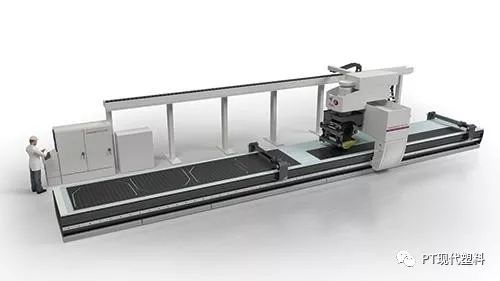
Fives Cincinnati用于生产汽车复合材料的集成的生产系统还包括第二套自动化的生产单元,即此图显示的成型-固化单元
该系统的设计,可以支持采用热塑性和热固性的聚合物材料。
Fives Cincinnati公司已经证实,生产一个二维的热固性待用料,循环时间不到3分钟。其目标是,利用自动化的纤维铺放工艺,实现90秒的循环时间。该纤维铺放工艺可将废料减少到低于5%。
该公司产品战略及开发总监Dan Allman介绍说,环氧树脂的成型-固化循环时间需要4分钟,而采用一分钟固化的新的创新聚合物材料,成型-固化周期降低到90秒。“采用热塑性材料,我们能够用不到90秒的循环时间轻易地生产出汽车部件。”
这是一个非常灵活的生产系统,可以依据产量来订制自动化技术。其生产演示主要采用了单向带以及玻璃纤维和碳纤维的丝束,也采用了编织材料和无卷曲织物。
来源:PT现代塑料
作者:Ginger Gardiner