卢学茹
(北京汽车股份有限公司,北京 101300)
0 引言
汽车涂装SE分析的主要内容是对产品设计可能存在的问题在设计图纸、数模、数据方面进行审核,预先对产品或生产线体进行优化改善,尽可能避免将来在生产线上出现各种问题,使新车型在涂装质量、成本、产能、可操作性、生产线柔性化、工艺性等方面得到一定的保证。按专业类型可划分为标杆车对比、共线分析、前处理和电泳的工艺性、注胶操作性、喷漆作业性,以及注蜡、贴膜等的作业性分析。随着汽车市场需求的多样化,新车型开发数量也逐渐增加,新开发车型大多会与现有车型共线生产,所以对新开发车型的共线分析就成为涂装SE分析一项重要工作内容。通过以某新车型涂装SE中的设备共线分析为例,对相关内容进行探讨。
1 生产线基本限制要求
根据现有生产线的基本限制要求,对比新车型的白车身最大外形尺寸、白车身重量、最大电泳面积、最大喷涂面积、底部焊缝密封胶最大长度、PVC喷涂最大面积、RPP喷涂要求、门框贴黑膜要求。若无法满足新车型的需求,则需要对生产线的设备或工艺进行改进。某车型设计阶段的生产线限制要求见表1所列。

关于白车身尺寸,除了各室体限制的长宽高的要求以外,还需满足前处理、电泳输送设备和槽体共同要求的最大边框线要求。结合涂装定位点的设定,同时需要满足车身在滑橇上的总体位置,在机盖、行李箱盖(或背门)开启一定角度后,白车身的任何部位均不能超出设备要求的最大边框线,且需要保留合理的余量。避免出现车身在槽体中因运动摆动造成的干涉,导致车身或槽体内部设备被破坏。
2 输送设备共用化分析
对于国内汽车涂装线来说,往往属于多车型混线生产,那么车型的定位点应尽量一致。如果确实因为产品本身原因不能做到一致时,可以通过改变吊具和滑橇的定位点来完成。输送设备的共用化分析主要从滑橇、吊具、转挂系统、升降机等几个方面进行分析。
2.1 滑橇共用化分析
本次共线分析新车型的生产线前处理、电泳采用RoDip的输送方式,且WBS和PBS滑橇定位点与涂装车间滑橇定位点相同。在车身设计初期,需将新车型的定位点坐标、孔径大小和定位孔的翻边高度与滑橇支撑进行匹配。可将新车型的数据和滑橇3D数据组合进行模拟分析,可同时观察车身与滑橇的横梁、支腿等是否存在干涉问题,结果更直观。如果不能匹配现有滑橇支撑,需要增加新的滑橇支撑,或对车身定位孔进行调整。一般优先考虑调整车身定位孔,因新增支撑前需要评估新支撑与现有车型是否干涉、布置新支撑需要的空间能否在滑橇增加该支撑,并且改造滑橇的费用巨大。
将分析的新车型下车体数据与滑橇匹配(图1所示)后发现:用现有后定位孔为基准,后定位孔的翻边高度不满足要求,无适合的前定位孔,前后定位孔的高度差为82.26mm,而滑橇要求的高度差为67mm,不满足共线要求。
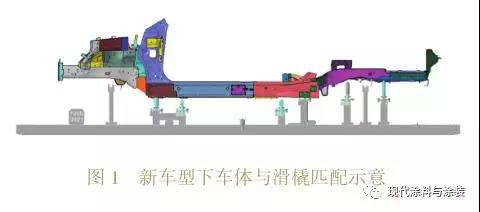
经过与产品设计人员和设备工程师进行讨论,若滑橇改造增加新的支撑,共585个滑橇,需要投资近300万,且改造周期长,影响正常生产,新增支撑也存在对现有产品带来生产安全隐患;若产品变更,需要对现有数据的20多个工件进行变更,数据周期也会受到影响。通过反复沟通、分析讨论,终于达成一致的解决方案:
1)在现有前定位点沿X向80mm处增加一个翻边高度为5-6mm的Φ40的定位孔,同时在内部增加加强板,经CAE强度校核分析,满足要求;
2)现有后定位孔翻边高度不满足滑橇锁紧高度9-10mm的要求,且该锁紧高度要求下,车身设计时采用的普通冷轧板翻边高度达不到要求,需要底部增加一块加强板来增加高度,导致车体重量增加,且板材贴合部位无法形成电泳漆膜,会导致锈蚀问题发生。若更换材质会导致整车成本上升,不建议采用。考虑到定位孔翻边与滑橇锁紧结构接触部位必须保证锁紧高度要求,而其余部位翻边高度对锁紧无影响,故可用渐变的翻边结构(图2所示),保证锁紧部位的高度要求。经过与冲压工程师确认分析,这种方案可行。对比设备图纸和现场测量,确认滑橇的锁紧机构锁紧后与定位孔翻边的接触范围,在保证满足工件强度要求和冲压工艺能实现的前提下,尽量增大最大高度翻边的范围。经过EP样车验证,此定位孔翻边形式锁紧可靠,无变形。
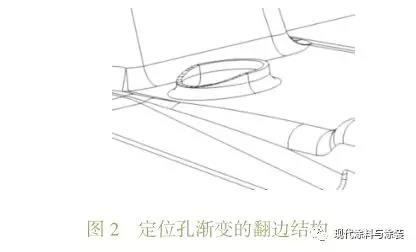
3)在满足冲压、焊接工艺以及整车布置要求下,通过调整前后定位孔所在工件的Z向高度来满足滑橇前后定位孔高度差的要求。且前后定位孔更改后,保证X向距离为1720mm,Z向高度差为67mm。
通过上述新车型产品数据的变更,最终实现直接共用滑橇,节省了设备改造的费用。
2.2 PVC吊具共用性分析
车身底部焊缝密封胶和PVC喷涂作业需要将车身吊起,高工位作业。吊具为拖块托举,分为前后拖块,托举部位为车身裙边部位,要确保裙边平齐,且能承受白车身的托举重量。通过性分析是重点关注的是新车型的裙边部位的X和Y向范围是否满足拖块托举限制要求。仍需将车身数据和生产线吊具的三位数据组合,校核是否存在干涉部位。
本次分析的新车型的数据能满足吊具的托举范围要求(表2所示),但是从3D数据查看可见前拖块托举处与车身地板下纵梁干涉,拖块不能与裙边部位垂直接触,会导致托举不到位、吊具前后承重不均匀,拖块发生形变。经与设计人员沟通确认,此纵梁位置涉及线束卡子的布置问题,更改困难;与设备工程师现场确认拖块的更改方案,可以更改且改造周期短,费用不高,最终确定更改吊具前拖块。吊具共用的问题顺利解决。
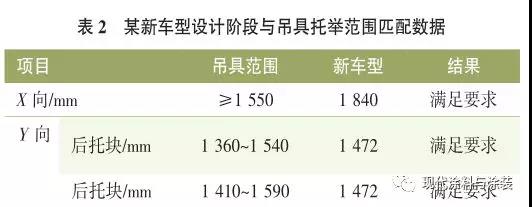
2.3 其他转接设备
涂装车间与焊装、总装车间的转接,以及车间内部各线体之间的转接基本都是通过升降机和移栽机完成的。做升降和移载设备共线分析的时候,须重点关注托举范围和重心位置,确保新车型的裙边部位在拖块的托举范围之内,且不存在干涉位置;需重点关注重心位置在前后拖块之间,且X向不可过度偏向某一拖块,以免出现车体前倾或后倾的问题。另外,车身在烘干炉爬坡段的重心位置也需重点关注,重心必须落在滑橇滚轮之间,否则会出现翻车的风险。
本次分析的新车型为汽油车改款电动车,由于电池布置的原因,相比汽油车纵梁的位置有变化,且纵梁的Z向高度比裙边低。在做锁紧检测设备分析时发现,检测拖块托举的部位为纵梁,前后拖块托举部位的Z向存在15mm高度差,经过与产品工程师讨论确认,最终通过产品变更消除了现有高度差,从而实现了锁紧检测设备直接共用。因锁紧检测设备包含车型识别系统,故改造难度大,同时增加车间生产管理难度,一般共线分析时考虑产品变更满足,而不建议设备改造。
3 结语
涂装共线分析是整个SE分析工作中极为重要的一部分,对新增车型的生产线后期的柔性化生产、产能的实现、生产管理的难易、制造成本控制都起到关键性的作用。若新车型投产时能考虑将同一平台车型策划在同一生产基地,且SE分析阶段把通过性分析做好,100%的共线性问题均能在产品设计阶段得出解决措施,从而避免投产后,发生产品设变或生产线因增加新车型而进行大量改造。
来源:现代涂料与涂装