作为安徽省汽车行业的领军企业之一,安徽江淮汽车集团股份有限公司(以下简称“江淮汽车”)先后与德国大众、蔚来汽车签订战略合资合作协议,加速了其新能源汽车由“先进制造”向“高端智造”的跨越。近期,本刊记者有幸采访到江淮汽车工艺工程院冲压工艺部技术总监崔礼春先生,请他带领大家走进江淮汽车,揭开这家老牌车企神秘的面纱。
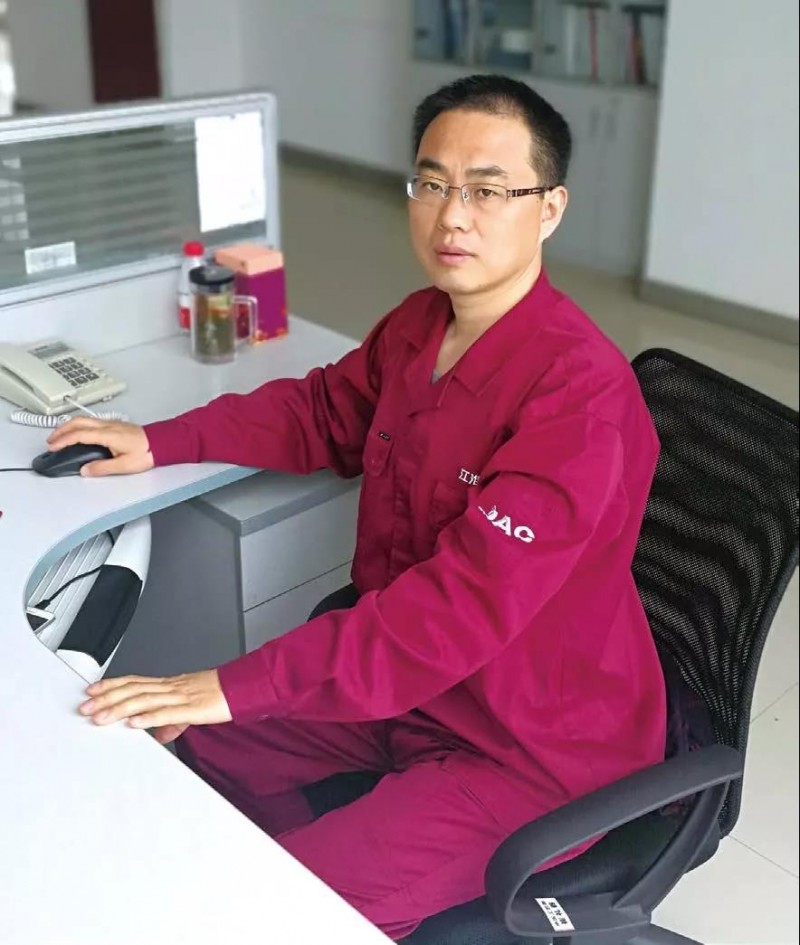
崔礼春,高级工程师,江淮汽车冲压技术总监,在冲压工厂规划、冲压零件的冲压工艺设计等领域都做出过突出成绩。
2017年度主要业绩:
1、完成“高档数控机床与基础装备”科技重大专项“汽车大型铝合金覆盖件充液成形技术与装备”的技术验收:主导课题的技术方案与实施,达成“课题完成质量高,产业化推广好,具有示范效应,同意通过技术终验收”的验收结论。
2、主导和参与国行标的制修订工作:行标《冲模 冲模用钢 技术条件》已发布;国标《冲模 矩形截面压缩弹簧 安装尺寸和颜色标识》已定稿报批;国标《冲模耐磨板 第2部分 B型》已定稿报批。
3、负责江淮汽车轻卡新基地、蔚来工厂的工艺规划设计和设备选型,目前已批产工艺验证中。
4、负责大梁压力机的设备改造及自动化方案制定,现已批产交验。
5、负责江淮汽车多款车型项目的冲压工艺方案制定与过程实现,按指标要求达到交付状态。
技术创新是发展根基
江淮汽车是集研发、试验、生产、销售于一体的综合性汽车集团,是国家火炬计划重点高新技术企业、国家级创新型企业,位居中国企业500强、中国百强工业企业之列。1990年,公司开发出的填补国内空白的客车专用底盘,改写了中国客车底盘由货车底盘改装的历史。自2009年起,公司共有9款自主研发的发动机荣获“中国心”十佳发动机称号。公司主持的国家863计划重点项目——6DCT自动变速箱,实现了TCU上层软件开发完全自主,打破国际垄断。在新能源汽车领域,江淮汽车在电池热管理技术、本质安全管理技术等方面实现重要突破,电池液冷技术世界领先,国内独一无二。
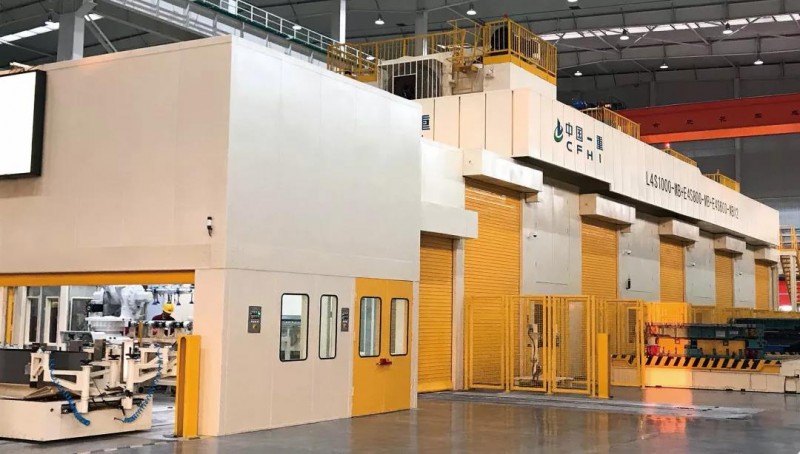
2500t伺服压力机自动线
江淮汽车拥有一支近5000人的高水平研发团队,已形成整车、核心动力总成、自动变速箱及软件系统等关键零部件研发、试验验证和标定开发等完整的正向研发体系。截至2017年底,江淮汽车累计拥有授权专利10881件,其中发明专利授权1205件,成为国内首家专利过万的车企。江淮汽车技术中心是国家级研发设计中心,研发成果位于行业前列,其中1.5TGDI发动机、6DCT自动变速箱获得安徽省科技进步一等奖。
车型丰富 销量领先
公司生产的车型包括乘用车、轻型商用车、重型商用车、新能源汽车、客车以及工程车辆,轻卡销量多年来一直稳居国内第二,出口量连续十几年稳居行业第一。格尔发重卡在载货车细分市场多年来一直稳居前三甲。瑞风MPV连续多年荣获“年度最佳MPV”称号,在公商务车MPV细分市场保持领先。瑞风S3蝉联2015年、2016年小型SUV销量冠军。中高端技术座驾瑞风A60、高端商务车MPV瑞风M6、旗舰SUV瑞风S7上市开启江淮汽车品牌向上之道。
乘用车目前处于发展阶段,重点工作是夯实品质、塑造品牌,轻型商用车处于行业第二位置,重型商用车处于行业第六位置,发展势头良好,2017年销售各类车辆51万辆,销售收入近500亿元,2018年全年销售目标为68万辆。轻卡连续多年行业出口第一,乘用车出口位列行业前三。江淮汽车国际市场涵盖南美、欧洲、非洲、中东、东南亚等130多个国家和地区。在“一带一路”沿线60多个国家中,已出口30多个国家。2014年与委内瑞拉成功签订6159辆重卡出口订单,创下近年来中国重卡出口第一大单。
作为我国新能源汽车产业的先行者,新能源汽车业务涵盖乘用车、轻型商用车、多功能商用车、客车等产品,江淮汽车历经七代迭代研发,累计应用推广新能源汽车近8万辆,累计行驶里程超过15亿公里。
冲压工艺部的主要职责
江淮汽车工艺工程院承担车身设计实现,冲压工艺部是其下属部门,共有五个科室组成,分别是材料技术室、工艺策划室、工艺设计室、轻量化工艺室、品质培育室。冲压工艺部的工作内容包括工艺规划、金属材料、工艺设计、品质培育和CAE五个专业模块,涵盖工厂设备规划、冲压零件工艺设计两大部分。其中,工艺规划专业模块承担工厂设备规划,其他四个专业模块均与冲压零件相关,如CAE模拟、工艺设计、品标设计与培育、冲压零件的板材应用研究及模检具的主要材料应用研究。
近两年来,冲压工艺部取得的工作成就主要包括:完成“高档数控机床与基础装备”科技重大专项“汽车大型铝合金覆盖件充液成形技术与装备”的技术验收;主导并参与多项国行标的制修订工作;参加多个行业论坛及学术会议并发表多篇技术报告;完成公司两个全新生产基地的冲压工艺规划设计和设备选型工作;完成公司多条生产线的压力机自动化改造工作;不断优化并完善产品&工程NAM流程体系标准;完成多款车型的关键大中型冲压零件的品标/CAE/工艺的自主设计等。
冲压工艺的优化与革新

3000t车架冲压线
崔礼春表示,冲压工艺应在助力企业发展方面,不断致力于使员工操作得心应手、制造过程行云流水,研究和应用安全、环保和制造节约型的制造技术,从而确保生产过程精益高效。冲压工艺部建立健全的各类专业指标及其过程方法,在项目实战中不断完善流程体系标准,丰富工程资源库,植入到产品开发流程和日常的员工工作中,交付质量稳定、安全可靠及成本周期合理的产品技术和服务。例如,公司乘用车二代车型的材料利用率相比一代车型提高了5%,工序比下降到2.3。在契合车身轻量化技术进步方面,工艺部着重研究高强钢、特高强钢、铝合金覆盖件及管梁件的成形特性,培育行业领先的新技术并应用到工程实际当中。相比一代车型,二代车型的车身减重达到10%,但安全级别更高。
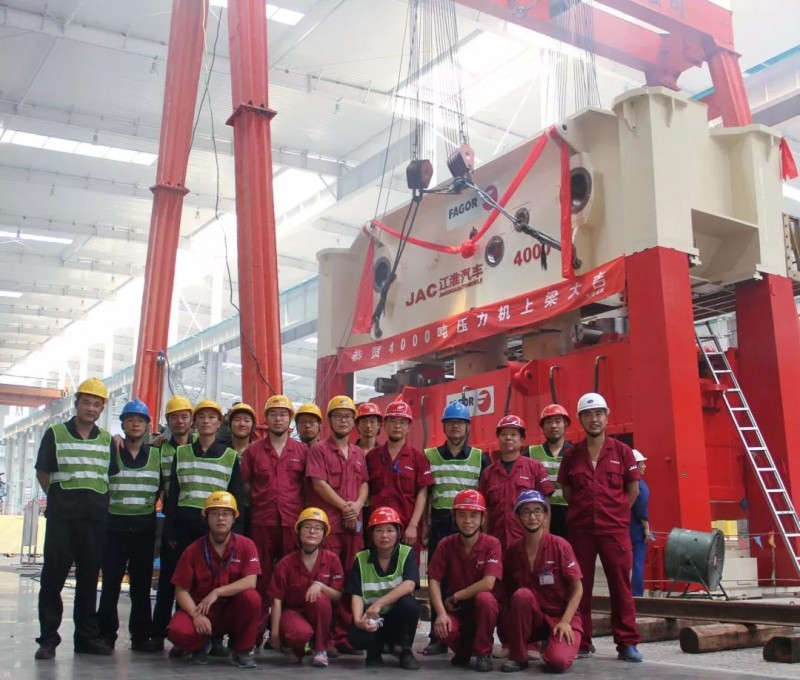
团队在4000t车架自动冲压线前的合影
冲压工艺部通过对高速压力机、伺服压力机与输送装置的系统集成,整线生产节拍超过10SPM,同时更安全、环保和节能。此外,以保障产品实现过程的一致性为目标,以资源节约、环境友好为基础,以保障职业卫生健康为前提,以提高劳动生产率为重点,工艺部不断提高工艺工程规划和建设水平。
技术和质量是制胜法宝
江淮汽车掌握的冲压先进技术主要包括:先进伺服成形技术、铝合金液压成形技术、热冲压成形技术、滚压成形技术等,对模具的选购要求国内一流的供应商,对模具的材料、结构设计、工艺设计、生产制造方面具有严格技术要求。
公司始终将质量视为企业生存发展之本,先后通过ISO9001质量管理体系,环境管理体系、职业健康管理体系、ISO/TS 16949质量管理体系认证。因在质量管理领域的卓越成就,2010年公司荣膺中国质量管理领域最高奖项——全国质量奖,成为唯一获得此奖项的中国品牌车企。2012年荣获出口免验企业资格,成功树立国际知名品牌形象。
冲压件配套商体系是按公司准入管理办法经审核专家评审合格的方式构建,零部件的质量采用考核机制,期望供应商按产品开发时间节点保质保量提供合格冲压件。
十一大冲压生产基地
目前,江淮汽车拥有乘用车一工厂、乘用车二工厂、乘用车三工厂(蔚来工厂)、商务车一工厂、商务车二工厂、青州工厂、扬州工厂、蒙城工厂、安庆工厂、遂宁工厂、新港工厂共十一大冲压生产基地。乘用车一工厂冲压车间共有8条生产线,其中开卷落料生产线为1条,自动化生产线为5条,这些自动化生产线中有1条为国内首台2500t伺服压力机自动化应用生产线;商务车一工厂冲压车间共有5条生产线,其中1条为自动化生产线;商务车二工厂拥有1条手工油压机生产线;青州工厂拥有1条手工压力机生产线;扬州工厂拥有2条油压机生产线和1条自动化生产线;蒙城工厂拥有1条油压机生产线;安庆工厂拥有1条手工压力机生产线;遂宁工厂拥有1条手工压力机生产线;新港工厂拥有2条机械压力机自动化生产线;新港工厂拥有3台大型纵梁压力机。
目前,在公司拥有的若干先进生产线中,伺服生产线可以实现高质量、快节拍、低噪声、绿色环保的冲压成形。大型纵梁压力机全自动化生产线处于国内先进水平,具有高品质、低劳动强度、高效率等特点。
挑战与机遇并存
公司与蔚来汽车的合作基于全铝车身,带来的机遇是全铝车身冲压成形技术的应用,挑战是公司首次进行全铝车身技术的应用,应对的措施是派专家进行现场技术问题的指导;公司与大众的合作基于冲压工艺技术优化,车身设计流线型,造型更完美,冲压工艺更精湛。
在环保方面,江淮汽车大梁钢BMD技术的成功应用,为卡车大梁钢板取代传统酸洗板技术参数提供了有力支持,不仅提升了卡车车架性能,也实现了取代酸洗板所带来的成本和环保等方面的优势。
结束语
在汽车自主品牌产业的发展过程中,无论是久负盛名的老牌子,还是初临市场的新品牌,都是靠技术含量说话,靠质量赢得市场。未来市场竞争的规则一定是:谁抢占了科技制高点,谁就高人一筹;谁把握住企业发展的主动权,谁就能领先一步抢到金饭碗。
江淮汽车优异的成绩,非常好地证明了这一点。未来几年,江淮汽车将着重开展冲压新工艺、新材料、新技术的研究应用,实现汽车智能制造技术,公司也将持续坚持“创新驱动、质量为先、绿色发展、结构优化、人才为本”的基本方针,以实现中国汽车智能制造的目标。
来源:锻造与冲压