随着企业规模和产量的扩大,采用机器视觉系统替代人来完成产质量检测工作具备极大的应用优势。在此背景下,IBM针对企业的这一应用需求推出了一系列面向不同行业应用的认知视觉检测技术解决方案。
相对于人工质检来说,机器视觉检测能够更加精准的把关产品质量、降低生产成本,同时还可以24小时不间断的工作,甚至可以在各种不适合人类工作的恶劣生产环境下实现高速在线检测,检测的准确度可以接近100%。因此,随着企业规模和产量的扩大,采用机器视觉系统替代人来完成产质量检测工作具备极大的应用优势。在此背景下,IBM针对企业的这一应用需求推出了一系列面向不同行业应用的认知视觉检测技术解决方案。
面向电子制造行业
近年来,由于电子组装的小型化,产品生产工艺要求更高,产量却不断增加,使得在电路板装配和电子产品组装过程中仅仅依靠人眼进行检测操作已经不能保证生产线的质量和效率,机器视觉技术正在代替人进行全自动的产品检测、工艺验证,甚至实现生产工艺的自动控制。
在电子制造业,为保证电子产品组装生产线装配出的产品质量,检测和监控几乎分布在生产线的每一个工序中。如果向电子制造的上游看,在晶圆制造、器件封装、甚至电子连接器等零配件产品的生产中,也都大量使用了视觉检测技术进行测量、检测和控制。
IBM认知视觉检测技术的优势是显而易见的。与人眼相比,机器不仅不会疲劳,具有人所不具有的一致性和重复性,而且IBM认知视觉检测技术能够通过高精度的摄像头放大产品表面细节,在细微层面进行拍照和分析,能检测人眼不能发现的质量问题,如PCB板缺陷、手机部件缺陷、液晶缺陷、晶片缺陷、光学镜片缺陷等。
面向汽车制造行业
随着汽车行业自动化水平的不断提高,一些传统的检测方式已不能适应高节拍、柔性化的生产需求,具有实时监控功能的机器视觉在线检测技术逐渐在主流生产厂家得到应用,并取得了良好的效果。
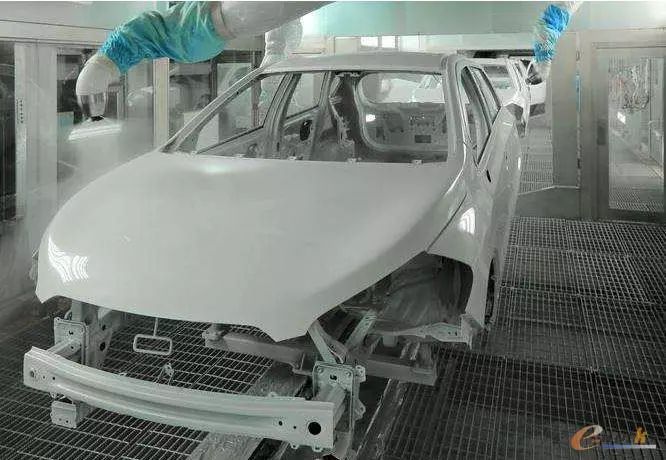
在自动化汽车生产线中,视觉系统必要时需要同机器人匹配应用,并与生产线的PLC控制系统建立联接,以实现测量、检测、定位和识别的功能。视觉检测系统具有如下特点:采用非接触式检测方式,提高了响应速度,对生产线影响小;具有长时间的稳定、可靠地重复工作的性能,适用于汽车连续化的流水线作业;适合在安全风险高、人机工程恶劣和环境差的区域工作。
目前,IBM认知视觉检测技术已经在汽车行业得到了应用实践,帮助领先的汽车工厂实现对汽车零部件、焊接、喷漆等工艺过程的高精度检测。IBM认知视觉检测系统可以根据车型的3D数据制定出机器人手臂的行动路径,配合矩阵式工业相机和辅助光源,完成全车360度高清尺寸的拍照,然后实时数据分析系统通过部署在产线边的缺陷识别系统对所拍摄的照片进行实时分析,识别出照片中缺陷位置和缺陷类型。
此外,在汽车零部件检测中,IBM认知视觉检测系统可以对汽车棘爪、铰链、托架、条形销等进行检测。在汽车棘爪缺陷识别应用方面,可以实现平整度、长度、厚度和高度的检测,而且准确率大大的提高,提升了企业的产品的合格率。
面向装备制造行业
在航空航天、重工船舶、工程机械、工业机器人等装备制造行业,由于设备体量较大,零部件较多,设备都处于长时间高负荷运行状态,任何由质量问题导致的事故都会造成重大的经济损失和人员伤害。因此,企业在关键零部件生产过程中对质量检测的要求都非常高。
随着智能制造的推进,装备制造业作为产业中最具竞争力的行业正在引领整个制造业的智能化转型。装备制造企业中以往采用人工检测和机器视觉结合为主的方式正在被更为高效和智能的机器视觉检测系统替代。IBM认知视觉检测系统能在充分满足装备制造业对产品质量检测高标准和高要求的基础上,还赋予了质量检测系统更高的智能。IBM认知视觉检测系统能实现自主化的缺陷标记和反馈,不断优化质量检测分析模型,提高质检过程的效率和产品合格率。
面向精密仪器行业
机器视觉以其检测精度和速度高并且有效的避免人工检测带来的主观性和个体差异的优势受到了企业的广泛关注。在精密制造行业,已经被应用于对精密加工零件表面划痕、凹陷进行检测,是实现优质产品生产以及降低成本的理想选择。
精密零部件对零件表面的质量要求都比普通零件要高,更加光滑的零件表面能提升精密仪器的耐磨性和腐蚀性以及抗疲劳能力。对于精密零部件的检测,一般是由人员用手通过放大镜来观察零件表面,以此来判断零部件表面的粗糙程度。由于这一过程人员的主观性比较强,很容易造成较大的误差。现在普遍采用的是非接触型检测,即用光电信号进行检测,物体表面所反映出来的就是图像特征,通过对图像特征的提取来进行分析和判断,这就是通常说的机器视觉检测。但由于有非常高精度检测要求的行业,如医疗器械、精密检测仪器等精密制造领域,很多非常细微的细节无法通过检测出来,也会导致检测结果的不准确。
针对高精密检测要求的行业,IBM认知视觉检测系统通过高精度的工业相机和基于神经网络的智能分析技术,通过不断放大零部件表面特征,给零部件表面的细节进行拍照,通过实时的数据分析能力来检测任何传统检测手段无法发现的缺陷。
来源:e-works 熊东旭