冷、温锻造凹模传统的制造过程为:模坯粗加工→热处理→预应力环压装→精车/磨→放电加工→模腔研磨/抛光。以上制造过程中,放电加工是模腔成形的关键工序,也是整个模具制造过程中占用制造周期最长的一个工序。传统的冷、温锻造模具制造过程中,放电加工占有重要地位。几十年来,用于模具生产的各种放电加工设备也取得了巨大的进展,放电加工成形的精度、效率逐年提高。在全球推动绿色制造的形势下,冷、温锻造生产得到了快速发展,对冷、温锻造模具的制造精度和快速制模要求越来越迫切,传统的放电加工越来越不能满足需要。
模具的放电成形主要不足之处表现为:
(1)因电加工白层影响,在生产过程中,模具早期开裂现象较为普遍,模具寿命始终没有大的提升。
(2)电加工表面粗糙度达不到冷锻模具要求,同时为了尽可能消除白层的影响,在后续工序中还需大量人工研磨抛光,生产周期长且影响尺寸精度。
(3)加工尺寸精度不高,如汽车等速万向节星形套成形模具尺寸精度希望控制在0.015mm以内,当模腔采用放电加工-研磨-抛光成形时,模腔尺寸精度往往在0.05mm以上,难以满足客户对精密锻件不断提高的质量要求。
(4)放电加工需要预先制造电极,加工周期长,难以适应小批量、多品种的生产方式。一般情况下,电极准备和放电加工至少要2天的时间,整个模具制造周期在10天以上。成形冲头类模具因电加工余量较大,有时放电加工需要2天以上,整个模具制造周期长达15天以上。
(5)因电极损耗影响,模具加工一次合格率低。如汽车等速万向节星形套模具的一次加工合格率仅有70%,大量模具需要二次修复,加工成本也难以得到有效控制。放电加工的工业化应用已有几十年的历史,鉴于近期新的技术很难突破,我公司在2004年引进了瑞士MIKRON三轴高速铣床,2007年又引进了五轴高速铣床,由此模具的主要加工形式也发生了变化。
瑞士米克朗公司成立于1908年,现有两个集团:米克朗加工技术集团和米克朗装配技术集团,是世界著名的机床制造商。米克朗加工技术集团总部在瑞士Agno,在世界各地有子公司和众多销售服务机构。主要产品为多工位组合加工机床和CNC柔性加工系统,包括6个系列。Multistar、Multifactor、NRG-50、Namco系列为转台式多工位组合加工机床,Multistep、Ideo系列为多单元柔性加工系统。现有7000多台机床在世界各地使用。
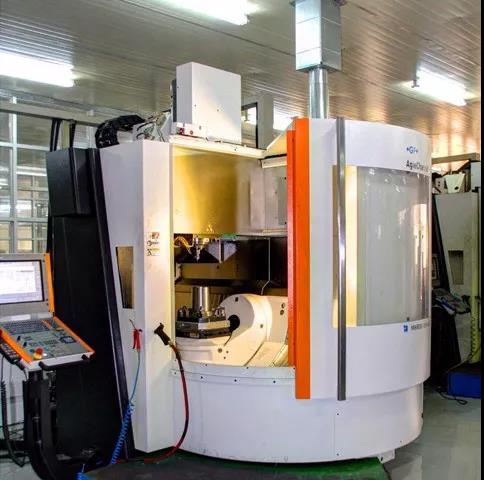
冷、温锻造凹模高速硬铣成形制造过程
冷、温锻造凹模高速硬铣成形制造过程为:模坯粗加工→模腔粗铣成形→热处理→预应力环压装→精车/磨→装配基准→模腔高速硬铣成形→模腔珩磨/抛光。数控高速切削加工作为模具制造中最重要的一项工艺,是集高效、优质、低耗于一身的先进制造技术。通过几年摸索与实践,我们基本掌握了高速铣加工的特点,与电加工方式相比,有以下几点优势:
(1)省略了电极加工,减少了生产准备时间。特别是高速铣削的高效率切除金属的特点,使模具制造周期大为缩短。以汽车等速万向节星形套成形凹模为例,重量1~2kg复杂零件的冷锻模具和6~10mm中厚复杂零件的精冲模具一个未经预铣加工的模腔,全部精密铣削(硬铣)成形可在2~3h内完成,模具加工周期缩短至3天以内。模块标准化后,可在计划下达的4h内将模具加工完并交付使用,这在以前是不可想象的。
(2)高速加工可以一次将型腔和定位销孔加工完成。模具型腔尺寸精度可以达到0.015m m以内,等分度误差达到±1′。与电加工相比,提升了模具的加工精度,为精锻件质量水平的持续提高提供了坚实的保障。
(3)高速铣削使切削系统的工作频率远离机床的低阶固有频率,而工件的表面粗糙度对低阶频率最为敏感,由此降低了模具表面粗糙度。在模具的高淬硬钢件(58~63H R C)的加工过程中,采用高速切削成形的模具,后续只需挤压珩磨和抛光后即可交付使用,但电加工白层用挤压珩磨很难完全去除。
(4)高速铣削模具表面没有电加工产生的微裂纹,杜绝了表面早期开裂失效。原来星形套闭塞成形模具寿命只有4 000件左右,寿命很不稳定,现在已提高到了2万件以上,且寿命稳定。
(5)模具在使用过程中往往需要多次修复,过去靠电加工多次修复来完成,采用高速加工后可更快地完成该工作,且可以使用原NC程序,无需重新编制。在淬硬模块的高速硬铣成形过程中,根据各种模具复杂情况的不同,我们采用不同的加工方式:
其一,型腔较浅的模具(如星形套)采用三轴加工方法即可满足要求。
其二,对于有后隙的冲头类工件采用四轴联动的加工方法,可以一次装夹完成刃带、后隙及导向部分的加工。模具具有较低的表面粗糙度,后续只需直接抛光即可使用。
其三,对于形状复杂的冲头采用五轴联动加工,可以得到精确尺寸、优良的表面粗糙度。较深或形状复杂的凹模,采用热固式夹头五轴联动加工,对于很小的圆弧和拐角也能做到完美的处理。
其四,对于型腔较浅的模具,使用三轴加工就能够满足要求,但在冷、温锻造中多数为有后隙冲头和型腔较深的模具,采用三轴加工要么无法加工,要么加工出来的模具精度很差,表面粗糙度很高,这一类模具需采用四轴、五轴数控铣削加工完成。
五轴联动高速铣削成形应用
(1)五轴联动铣削的优势 可以优化切削过程与参数,有利于降低刀具磨损,减少后续加工,是汽车模具加工技术发展的潮流。适合于使用球头铣刀加工小曲率的凸表面和较浅的凹表面,也可用于使用铣刀侧面加工自由表面。采用五轴高速切削技术加工时,必须考虑尽可能用最短的切削刀具完成整个模具的加工,从而使加工模具精度高、表面质量好,避免返工,同时减少人工抛光时间,图1所示为五轴加工路径的情况。使用短的切削刀具是五轴加工的主要特征。短刀具会明显地降低刀具偏差,从而获得良好的表面质量。五轴联动铣削加工模具的目标是:尽可能用最短的切削工具完成整个工件的加工,也包括减少编程、装夹及加工时间来得到更加完美的表面质量。
(2)“3轴”和“3+2轴”加工 只要工件型腔不是很深,三轴刀具路径就足够了。如果工件型腔很深并有很窄的部位,使用纯粹的三轴刀具路径来完成整个精加工是不够的。这种情况下,差的表面质量和较长的加工时间随之而来。图2所示为三轴刀具路径的情况,这时,最短刀具的走刀长度必须很长,以期在垂直的方向上能够加工到工件的所有区域。
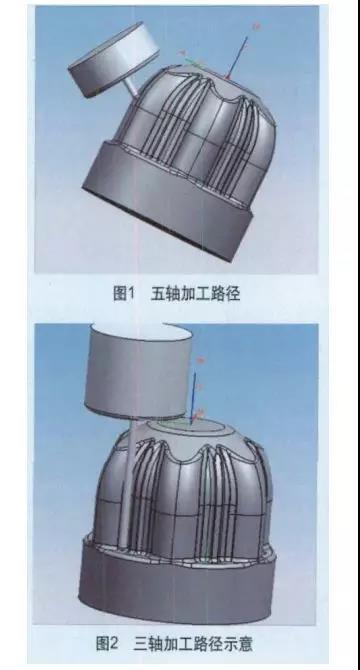
采用较短刀具时,主轴应倾斜,以保证工件的特殊区域也能被加工到。“3+2轴”加工(见图3)通常设置一个相对主轴的常量角度。复杂工件可能要求更多的倾斜视图以覆盖整个工件,但这样会导致刀具路径重叠,从而增加加工时间。另外,所有的倾斜视图也很难准确结合,因而手工打磨的工作量会增加,同时还极大地增多了进出动作,常导致表面质量问题和更多的刀具运动。
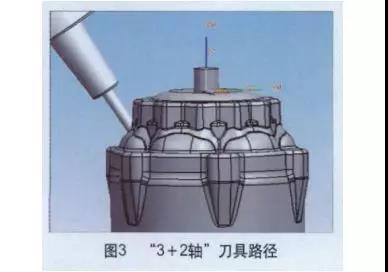
为了克服“3+2轴”加工的缺点,五轴联动加工可能是一个更好的选择,五轴联动加工能协调三个直线轴和两个旋转轴使它们同时动作,解决了“3轴”和“3+2轴”加工的所有问题。刀具可以非常短,且不会产生视图重叠现象,遗漏加工区域的可能性更小,加工可以连续进行而无需额外的导入、导出。
五轴铣削机床
五轴铣削机床(见图4)具有多种不同的配置。
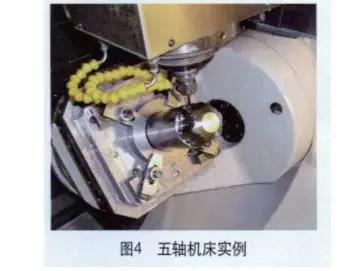
其一,通过旋转工作台可使工件在两个自由度上自由旋转,这种情况下主轴只能沿轴向移动。其二,主轴安装方式可提供两个自由度,使铣刀旋转,这种情况下工件不能移动。其三,系统可以是以上两种情况的组合,一个旋转轴是旋转工作台,另一个旋转轴由主轴充当。购买三轴铣床时需考虑几个不同的特征,如主轴功率、转速、轴向进给率、工作范围及重量极限等。评估五轴机床时,除了这些,还必须考虑如下几个方面:
(1)复定位精度 重复定位性是指五轴机床具有能返回同一点并保持矢量一致性的能力。对五轴机床的重复定位精度来说,不仅是轴向位置的精度,还要考虑角度定位精度。
(2)转速 其实也意味着刀具相对与工件的旋转速度,这个值越快,机床切削速度也越快。老式五轴机床的转速较慢,达不到高性能加工的生产要求。针对淬硬钢加工方面考虑,30 000r/min左右的最高转速已够用,不必花高价追求特别高速的配置。
(3)角度极限 角度极限是铣床铣头所允许的旋转角度的物理极限,这是以特殊机床设计为基础的。假如需要铣头倾斜50°来使用最短的刀具或切削倒角,只具备30°旋转极限的铣头,当然不能完成这次装夹工况下的加工任务。
(4)五轴联动铣削C A M软件 采用了五轴联动铣削加工后,“3+2轴”加工的问题并没有完全得到解决,编程问题转化成了C A M系统问题,振动控制也成了最重要的考虑事项。C A M系统仅发现工件、刀具及锥柄间的振动是不够的,必须还能自动消除这些振动,这样C A M 编程者就不需要手动调整上千万个或更多数据点的倾斜角度。另外,C A M系统的五轴自动编程可获得最优化的刀具应用。
自动刀柄振动消除对于深腔件的加工非常需要,尤其是高效加工,自动刀柄振动消除和较多形式的切削方式组合,使五轴模具加工具有更高的效率和柔性。当评估用于加工模具的C A M软件时,尤其是对于深腔模具加工,有许多因素需要考虑,如五轴功能的柔性,五轴切削路径的可靠性、易用性,以及五轴铣削机床的极限等。
结语
五轴联动高速加工在效率、精度及质量方面的优势,将使高速加工在冷、温锻模制造方面得到越来越广泛的应用。但推广应用最大的障碍是设备投资巨大,刀具价格昂贵。当前,国家将多轴联动高速数控加工中心列入高档数控机床与基础制造装备重大专项,一旦实现装备和刀具的国产化,将对高速加工在冷、温锻造模具制造中应用起到巨大的推动作用。
来源:《金属加工》杂志
作者:江苏森威精锻有限公司 张骏、徐祥龙,在此表示感谢!
来源:《金属加工》