复合材料轻量化技术背景
在全球对于环境保护和不可再生能源可持续利用的认识不断提升的大背景下,各国纷纷制定了史无前例严格的燃油经济性和排放法规(见图1)。美国的CAFE标准(Corporate Average Fuel Economy,企业平均油耗标准)规定汽车企业油耗在2015年达到35.5mpg,2025年达到54.5mpg(合百公里油耗23.2升)。欧盟要求到2020年乘用车的二氧化碳排放从当前的130g/km降低到95g/km的水平。而我国的乘用车燃料消耗量第四阶段标准也在2016年开始生效。
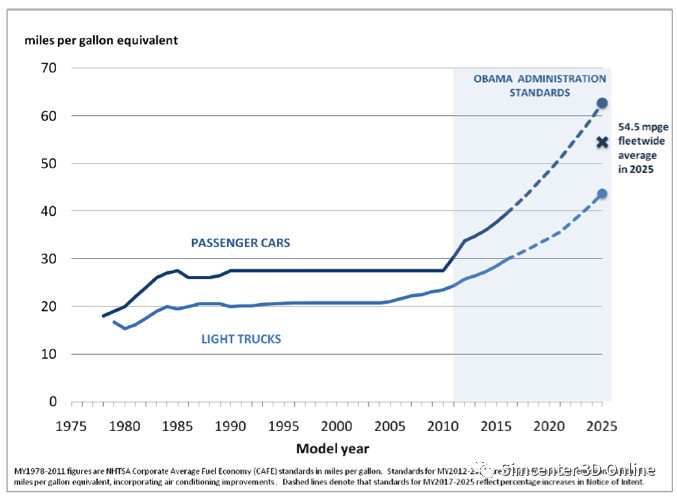
图1 美国政府大幅提升企业平均油耗标准(CAFE)[1]
面对这些异常严苛的政策,国内外车企纷纷从发动机、变速器、车轮/轮胎、整车等方面加力汽车节能减排技术的研发。根据美国Aberdeen集团的市场调研,48%的被调研企业认为轻量化是满足标准的首要手段也是最大难点,高达88%的车企则已经开始或即将开展新材料战略。
复合材料在汽车行业的应用与挑战
在各种候选材料中,复合材料由于其质量轻、强度高、可设计性好、便于整合零部件以及其耐冲击、腐蚀、疲劳耐久性能好,获得了很多车企的青睐。目前汽车上的很多零部件,比如保险杠、仪表板、前围、挡泥板、行李架、备胎舱等等已经是复合材料了。这些结构主要是基于GMT(GlassFiber Mat Reinforced Thermoplastics,玻璃纤维增强塑料)、LFT(LongFiber Reinforced Thermoplastics长纤维增强塑料)、NMT(Natural Fiber MatRefinforced Thermoplastics天然纤维增强塑料)等非连续纤维增强热塑性基体制成的非结构件。受限于热塑性树脂自身的劣势,比如粘性小,难于铺贴模具;熔点高,熔融粘度大,加工成本高;力学性能低于类似热固性复合材料等,如果想进一步降低整车重量,满足能耗排放标准,则必须借鉴航空航天工业高性能连续纤维增强热固性复合材料的经验,将其运用到车身的主次承力构件上。实际上,市场上的先行者,比如宝马已经在其i3和i8等车型上实现了碳纤维增强复合材料作为主承力构件(如乘员舱)的批量生产(图2)。
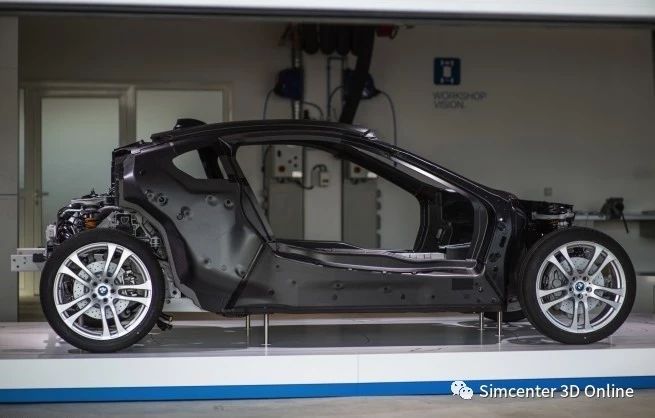
图2 BMW i8全CFRP碳纤维增强复合材料驾驶舱
常见承力复合材料的结构形式如图3。整体层合板由纤维增强的树脂铺层层叠而成,根据纤维丝/束在单个铺层中的排布主要分为单向和编织复合材料,考虑到层合板在垂直方向的力学性能,也会添加此方向的丝束形成非屈曲经编织物。可以直观的看到,相比均一各向同性的金属材料,复合材料的构造取决于其基体、纤维的材料,铺层的厚度,纤维朝向,编织方法等等,同时不同铺层的尺寸和连接方式又决定了整个构件的宏观尺寸构型和物理属性。
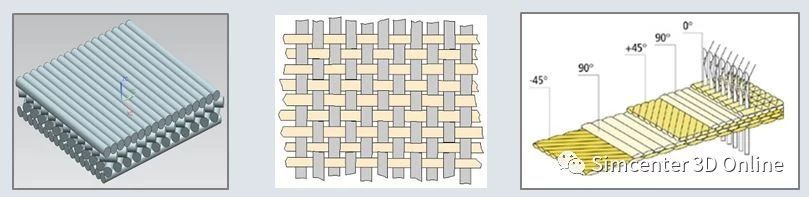
图3 常见铺层类复合材料构造,左起分别为单向复合材料、编织复合材料和非屈曲经编织物
这种复杂的细观结构一方面带来了复合材料强大的可设计性,另一方面从仿真的角度来讲是更多材料参数,更复杂的几何和有限元模型,不同的结构行为和性能表现。为了充分理解掌握并发挥复合材料的优势,复合材料结构的研发通常遵循搭积木式流程,亦称测试金字塔(图4)。具体到汽车行业,首先要对于样件进行材料和结构测试,获取基本的材料和结构性能,由此而上,试验分析不同结构形式的子部件,各级总成,最后进行整车测试。
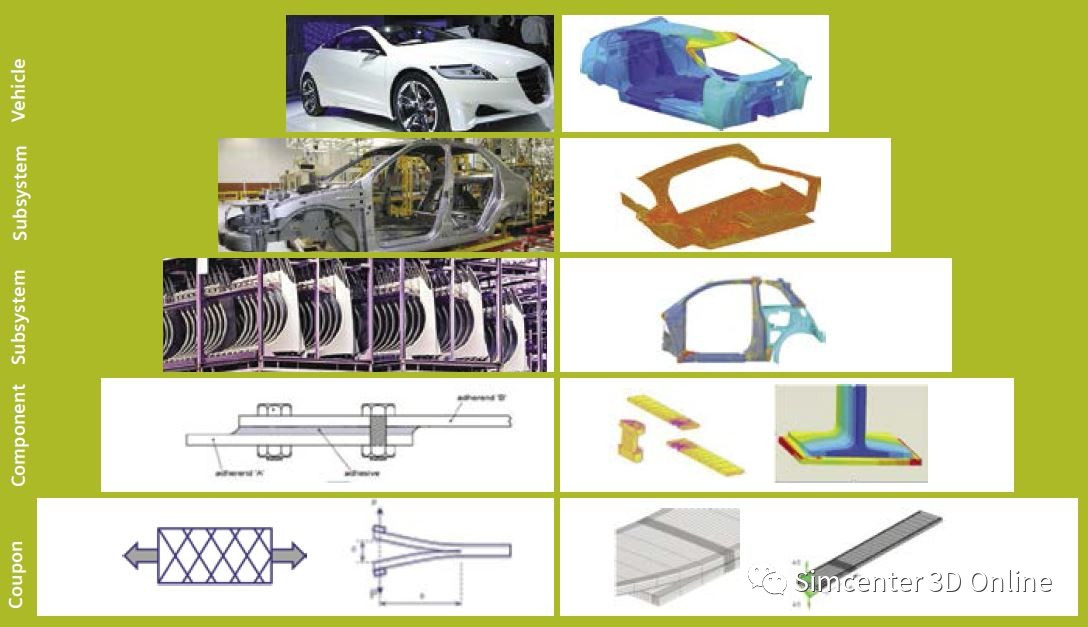
图4 复合材料“积木式”研发流程
考虑到物理样机的成本,每个层级都要尽量采用仿真的方法来减少测试数目,加速研发流程,降低成本。西门子根据其在欧洲三十多年的航空航天和汽车复合材料成功应用的经验上,提供了一整套复合材料整体解决方案,包括专注于复合材料设计制造的Fibersim软件和Simcenter 3D复合材料结构和成型工艺仿真软件(图5)。目前,业内领先的车企正在利用这套方案来帮助来理解和分析复合材料,解决同传统金属材料完全不同的新的挑战。
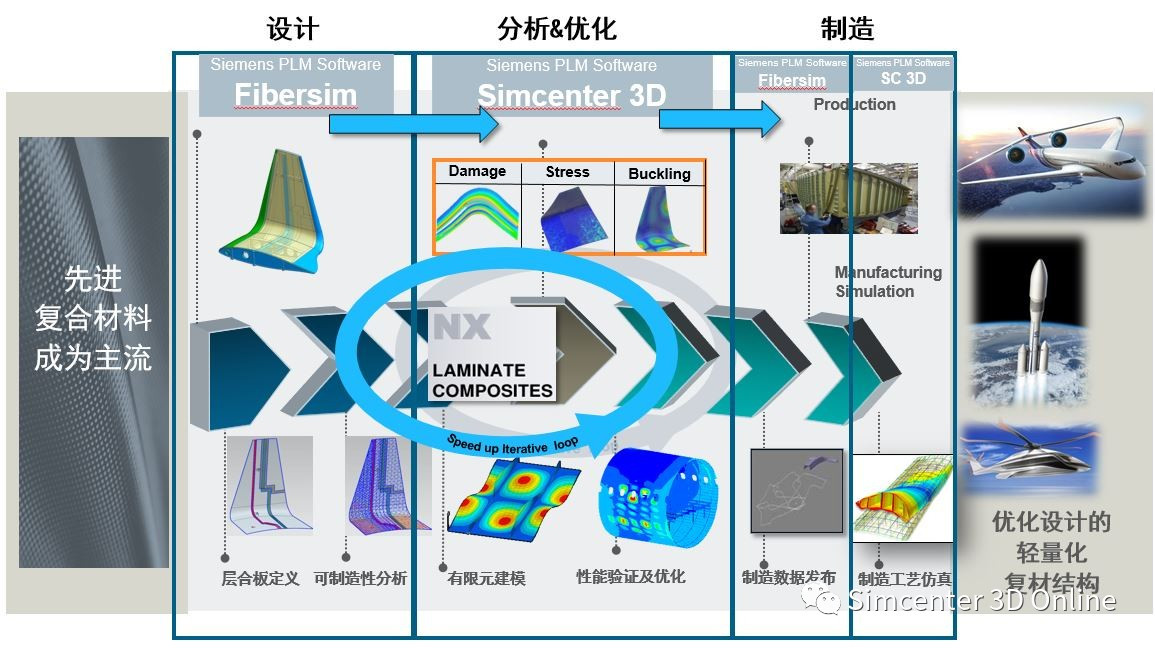
图5 西门子复合材料整体解决方案
复合材料损伤分析
先进结构复合材料在生产和使用过程中,常会面临同金属材料完全不同的失效模式。金属的断裂通常是单个或多个裂纹在静态和交变载荷下的形核和扩展,但是复合材料的破坏取决于多种不同的机理:基体开裂、纤维断裂、基体与界面的脱粘和分层,以及它们之间的耦合作用(图6)。
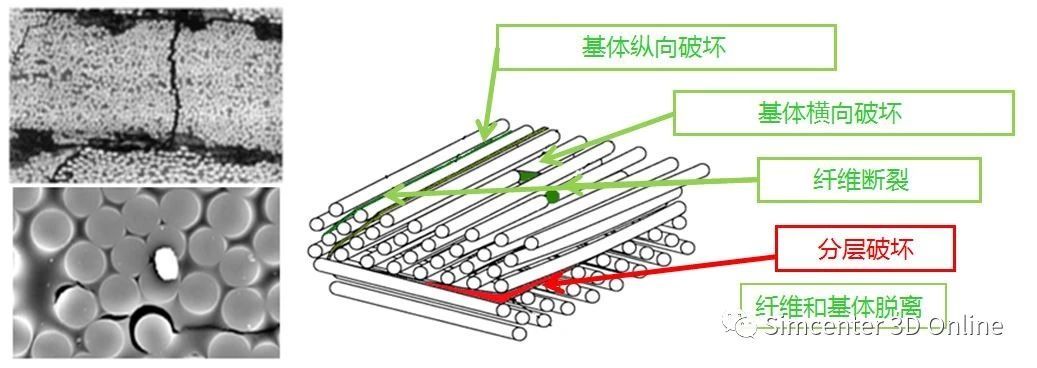
图6 复合材料不同类型的损伤机理
如何有效的描述这些损伤行为对于结构强度的破坏并最终预测结构的整体性能呢? 西门子通过与欧洲领先的航空航天企业和研究所合作,成功的开发了多个针对复合材料结构仿真的材料法则与失效模型,并将其植入到了Simcenter 3D软件中。通过与大量实验的对比证明了这些模型的准确性。
目前,日本本田汽车已在西门子的帮助下进行相关的预研工作[3]。项目初期的目标是调研不同候选材料的材料参数,包括传统工程力学参数和影响损伤行为的参数,然后建立材料损伤模型。在这个过程中,西门子帮助开发了材料测试方案、进行了虚拟仿真测试和搭建了最终的材料模型(图7)。
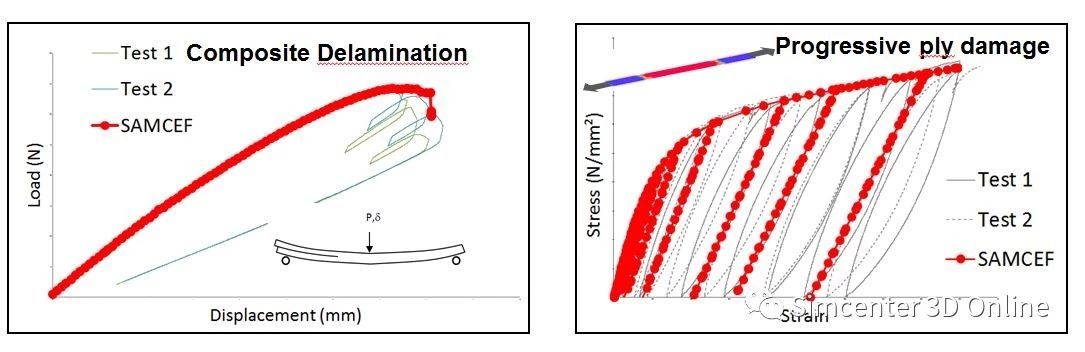
图7 本田基于西门子复合材料仿真解决方案的材料参数识别流程
在第二阶段,运用已获取的材料参数和损伤模型,利用Simcenter 3D预测了部件级复合材料结构的损伤行为(图8)和低能量冲击行为(图9)[4]。
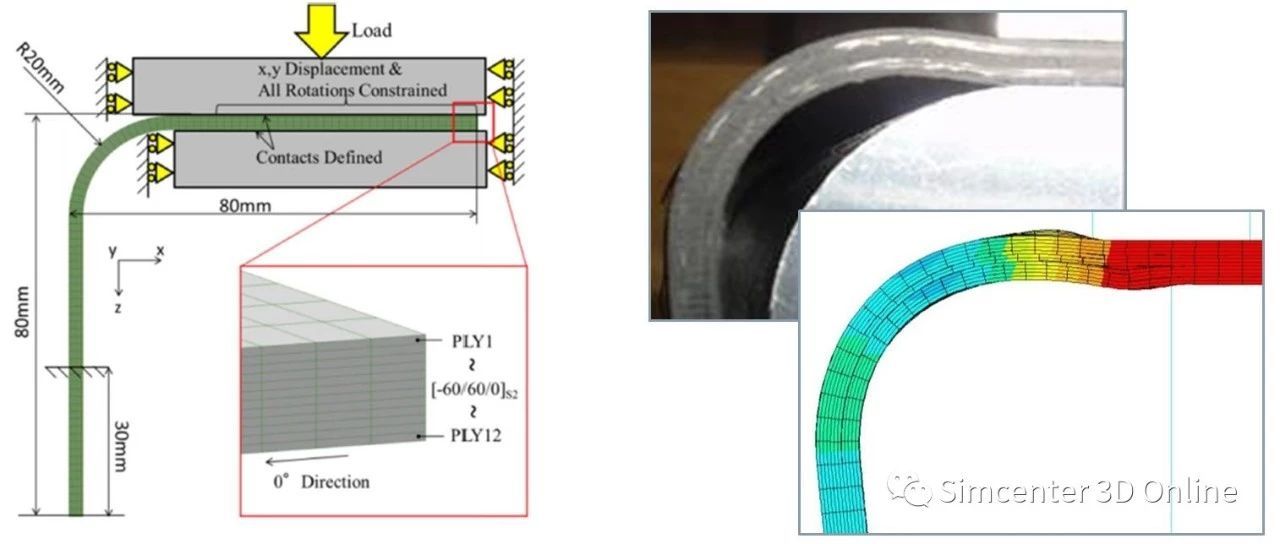
图8 本田基于西门子Simcenter3D平台的损伤分析
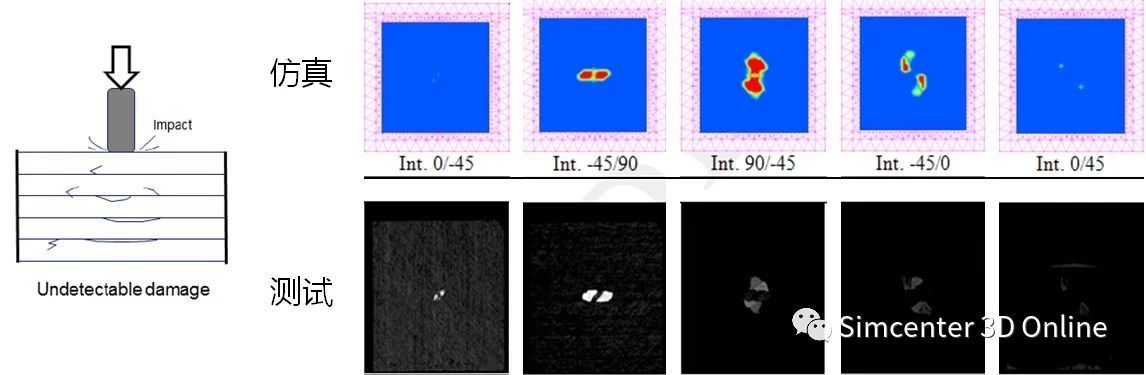
图9 本田基于西门子Simcenter3D平台的低能量冲击仿真同试验的对比
复合材料疲劳分析
同金属材料不同,复合材料的疲劳行为并不总是由一个宏观裂纹的生成和扩展导致的,由于其物理属性是非均匀和各向异性的,它通常是以整体的方式累积损伤。对于目前在汽车上应用的非连续纤维复合材料,它依然可以沿用对于金属材料分析的常用方法(例如S-N曲线法),它的计算效率比较高且可用于复杂的载荷工况,但是这种方法并不能考虑复合材料由于渐进损伤行为带来的刚度衰减和以及铺层破坏之后的应力重分布,且不能考虑疲劳损伤的相互影响和多轴问题,最后,由于S-N曲线的测量取决予铺层结构,如果我们有多种候选材料方案,则必须进行多次测量获取多条曲线,这样会大大增加试验的成本和研发的进度。
如果将来我们需要将连续纤维复合材料大量应用到车身上去,则必须提出一种新的疲劳分析方法。西门子同比利时根特大学的科研人员合作,共同在Simcenter 3D平台中开发了一套基于周期跳变法的疲劳分析算法,其结合了基于有限元的损伤分析和传统疲劳分析的优势,兼顾了效率同精度,能够真实的反应复合材料结构的刚度衰减和应力重分布(图10)。目前,日本本田正在采用此套方案进行结构疲劳方面的研发。
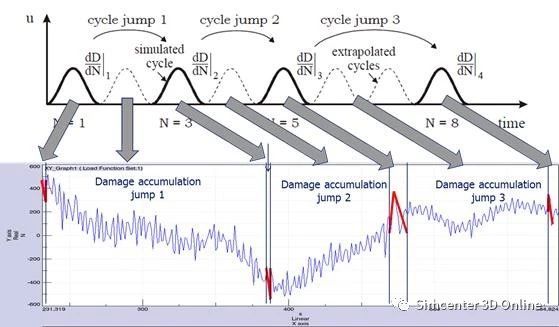
图10 西门子Simcenter 3D连续纤维复合材料结构的疲劳分析方案
总结与展望
相对于先进复合材料在航空行业的成功应用,汽车行业的复合材料才刚刚起步,也面临着很多困难。首先为了满足每年10万辆汽车和高达上百万件复合材料构件的产能,我们似乎还没有寻找到成熟的材料和工艺手段。其次,高性能复合材料的成本通常不菲,其原材料,包括碳纤维、芳纶和高性能树脂,价格居高不下,生产设备的投入和使用费用也很高昂,最后如何回收快速高效低成本的回收高性能复合材料也是一个悬而未决的问题。
虽然如此,轻量化是未来大势所趋,西门子将同各方面的专家和汽车制造商一起努力,提供更好的复合材料解决方案,引领行业前进。
参考:
[1] http://www.whitehouse.gov/sites/default/files/fuel_economy_report.pdf
[2] 贺光玉,向宇先进复合材料在汽车工业中的应用[期刊论文]-2013
[3] “Validation of material models for interand intra-laminar damage in laminated composites”, Bruyneel et al., ASC 29thTechnical Conference, USA, 2014.
[4]“Strength Calculation of Composite Materialconsidering multiple progress of failure by Ladaveze model”, Y.Urushiyama, T.Naito, JSAE Spring Conference, 2014 52 05
来源:Simcenter 3D Online
作者:西门剑客之SC3Der