案例背景
哈尔滨航天科技控股集团股份有限公司(以下简称哈尔滨航天公司)主要从事航天飞行器和汽车电子产品制造、航天微电机伺服系统研发,以及精密机械制造等。
案例解析
面临的挑战:
汽车仪表盘是哈尔滨航天公司的主力产品之一,这种反映车辆各系统工作状况的装置,由于上面集成了各种指示灯和仪表,需要在生产过程中进行大量复杂的检测工作。比如仪表盘检测包含了3级菜单7个页面30多处检测项,而且生产工位对节拍要求较高,要求检测速度一定要快。另外,检测项复杂,包含了字符识别、颜色识别、图案匹配等。
挑战:
“之前这些检测工作我们是使用人工方式,但是检测效率低,工件的误检率和漏检率居高不下。”哈尔滨航天公司仪表盘项目负责人李经理介绍说,“随着生产线自动化程度的提高,人工检测方式严重地限制了公司的生产效率,引入机器视觉检测势在必行。”
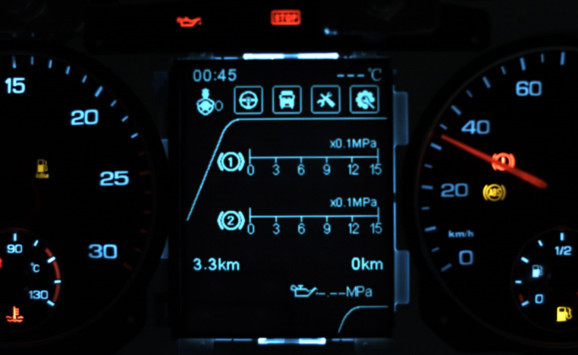
这时,哈尔滨航天公司的合作伙伴——沈阳新松机器人公司获悉了他们的技术难题。由于沈阳新松机器人公司一直大量使用康耐视公司的视觉设备,非常了解其技术和解决方案的能力。因此,沈阳新松机器人公司向李经理推荐了康耐视的视觉检测系统。

于是,哈尔滨航天公司联系上康耐视公司,并邀请他们的工程师来公司进行交流和评估。“由于汽车仪表盘检测项繁多且检测需求复杂,这就要求检测速度快、精度高、稳定性强,对于视觉检测来说着实是个不小的挑战。”康耐视的工程师表示,“因此,就选用了性能强劲、算法完备的In-Sight 7000 视觉系统。”
康耐视的解决方案:
解决方案:
在前期测试中,康耐视的工程师团队对仪表盘的各个界面检测需求进行初步评估,并根据评估结果为每个检测项选定了专门的检测工具,最后将整个检测程序分成了四大类:
1、各界面总体检测。在这个部分使用了康耐视快速强大的PatMax算法以及瑕疵检测工具。通过PatMax的高精度图案匹配,来检测仪表盘上各个区域的图案是否缺失/残缺/错位,并在极短的时间内输出结果。
2、各界面指定位置的字符检测,包括出厂日期、产品批号等。这个部分使用了康耐视成熟的OCR字符检测工具,用以读取出指定位置的字符,并将字串输出与标准字串对比,以判定日期、批次等是否合格。
3、各界面彩色图标检测,如ABS图标、油箱图标等。这个部分使用了康耐视强大的颜色识别工具,通过提取出各个图标的标准颜色来建立颜色库,然后每次检测都把指定图标的颜色与其在颜色库中的标准颜色对比,以判定图标颜色是否合格。
4、不合格工件图片的存储。由于仪表盘界面较多,不合格仪表盘的错误可能出现在某个界面的某个区域,不能只检测表盘是否合格,还需要存储不合格界面的图片以供日后追溯。在这里使用了FTP存图方式,将不合格的图片按日期存储到公共硬盘中,完美地解决了这个棘手问题。
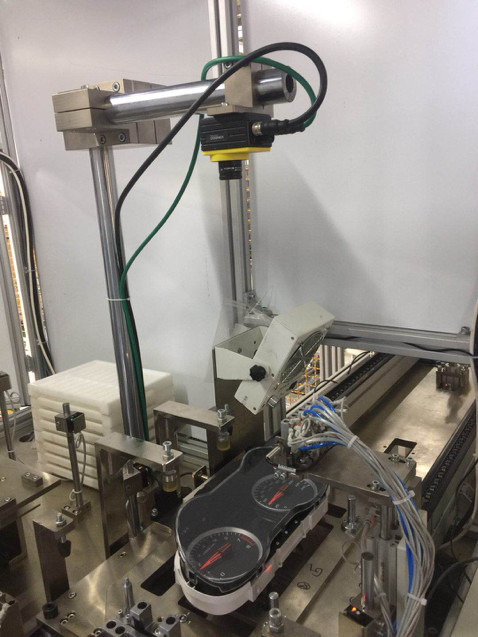
现场图片
另外,由于In-Sight 7000 视觉系统提供了多种通讯协议,这使得相机与现场PLC的通讯也十分方便,现场采用了稳定快速的Profinet通讯协议。
这样,在In-Sight 7000 视觉系统的帮助下,工程师们很快就定制了用来检测仪表盘的检测程序。程序内包含对于仪表盘的3级菜单、7个界面包含30多个检测项的检测,解决了图案匹配、图案缺失/错位、字符识别/读取、颜色识别、指示灯暗/亮显示错误、不合格界面图片的存储等问题。
优化后效果:
优化后的检测流程如下:当托盘上的仪表盘由传送带传送到检测位置时,自动化装置点亮仪表盘,由PLC给相机发送触发信号和作业切换信号,接收到PLC信号的相机开始采集图片并执行各界面的检测程序,以确保仪表盘各个显示功能准确无误;相机再将各界面的检测结果传回PLC;检测合格的仪表盘由机器人分拣到合格区,不合格的仪表盘则被分拣到不合格区,并将不合格界面的图片存储到公共机中,以便日后检查。
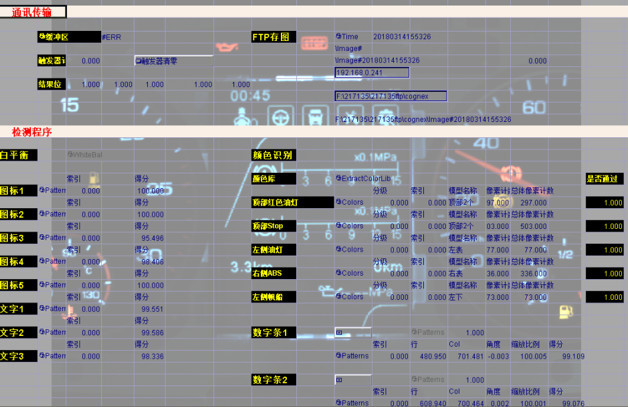
整个流程快速智能,完全不需要人工的参与,极大的提高了汽车仪表盘的检测准确率和生产效率。
客户评价:
对此,李经理评价说,“以前我们使用人工检测方式的时候,工人们都抱怨眼睛酸的不行,检测效率低下不说,产品检测的准确率更是得不到保障,良品误判、次品漏判比例高的可怕。现在好了,用上In-Sight 7000 视觉系统后,不仅检测速度提了好几个档次,检测准确率高达99.8%,还省下了人工检测专员的成本,真是一举多得。”
目前仪表盘检测项目的视觉检测工位已经投入到流水线的生产中,In-Sight 7000 视觉系统的出色表现让哈尔滨航天公司十分满意。李经理最后表示,“在车间生产逐步向自动化升级的过程中,视觉检测代替人工乃大势所趋。以后希望我们能够继续与康耐视合作共赢,创造更多的效益。”
来源:康耐视