焊装工艺作为汽车行业四大工艺之一,其重要性不言而喻,其肩负着车身成型,为整车提供支撑框架的重要使命,除了要保证外观造型之外,还必须保证总装所有零部件安装点的精度,故其工艺远比其他三大工艺复杂,生产线的规划及布置不仅需从精度保证、生产效率、配送物流、仓储存放诸多方面权衡考虑,也受限于厂房面积及结构、涂装连廊等现有条件。没有十全十美的布置方案,只有当前最合适的布置方案。
作为四大工艺中最复杂的工艺,生产线规划及布置概括起来主要从几个步骤着手:
(1)产能计算及节拍确定;
(2)主线输送方式选择;
(3)工序拆分及工位数量确定;
(4)侧围总成配送方式;
(5)总拼工位结构方式;
(6)物流仓储规划;
(7)平面布置及仿真验证。
1.产能计算及节拍确定
规划第一步,必须有市场部及公司战略规划部门输入的年产能要求,根据产能要求计算出生产节拍及单工位作业时间,作为工序拆分及工位数量确定的主要数据,其计算方法如下:
生产节拍(JPH)——每小时生产台数。
生产天数——365个自然天数,扣除国家法定节假日及双休日,年生产天数大致按251天计算。
每天生产时间——单班生产时间8小时、双班16小时、三班22.5小时计算。
设备开动率——设备有效开动比例,焊装车间设备开动率规划时一般设定为90%。
2.主线输送方式选择
主线输送方式决定了输送时间及效率,决定了工位的有效作业时间,是工序拆分及工位数量确定的依据。主线输送方式目前常用的有往复杆输送、滚床滑撬输送、随行夹具输送3种方式,具体选用哪种方式需结合效率、节拍、成本综合考虑。
(1)往复杆输送
优点:价格低廉,输送可靠,占地面积小。
缺点:输送效率较低,一般往复杆的输送时间达到28s(含举升、输送、下降、回退动作),只能直线输送,如工位数较多是只能分段布置,输送精度较差,需配合定位夹具使用。
适用范围:一般用于低节拍、工位数量相对较少的生产线,如输送工位超过10个不建议选用。
(2)滚床滑撬输送
优点:价格适中,输送可靠,输送效率较高(输送时间可达到16s左右),输送不受距离限制,可任意转弯、布置灵活。
缺点:需考虑空滑撬的回转方式及布置,会占用较多布置空间,动力滚床成本较高,输送精度较差,需配合定位夹具使用。
适用范围:适用于节拍较高、工位数较多的生产线,目前汽车行业使用最为广泛。
(3)随行夹具输送
优点:输送效率最高,定位精度高,输送机构与定位夹具功能合一,不需要额外增加定位夹具,减少了升降时间,输送时间可达8s。
缺点:单个输送随行夹具成本高,同时仍需动力滚床定位精度要求高,需考虑空滑撬的回转方式及布置,占用较多布置空间。
适用范围:适用于50JPH以上超高节拍的焊装线布置。
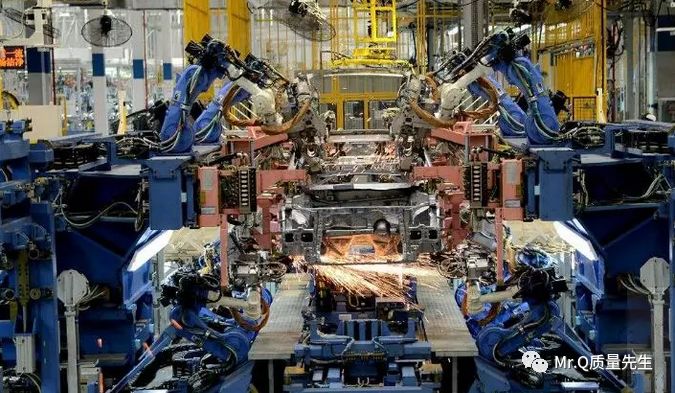
3.工序拆分及工位数确定
设计部门输入整体产品机构及图纸、工艺路线,界定焊装工艺内容,再拆分工艺到单个工位,需遵循以下原则:
(1)点焊一般按平均每个焊点3s作业时间进行综合测算;
(2)弧焊由于烟尘排放、工作效率较低,需尽量集中布置,避免分散;
(3)装件、取件、夹具夹紧与打开可根据过往经验设定作业时间;
(4)单工位有效工作时间+输送时间不得大于工位作业时间;
(5)需考虑输送布置中的工位损失。
4.侧围总成输送方式
侧围总成大部分属于A级外观面,对表面质量要求高,故其输送方式需综合考虑输送效率,是否需要库存、侧围线的布置区域等因素确定,可分为单侧围输送和双侧围配套输送两种。
(1)单侧围输送
优点:成本低,抓具与输送一体,无需单独设置吊具及抓手;
缺点:1:只能一个总成输送工作完成后才能返回输送下一个总成,节拍较低;2:无缓冲库存,当侧围线出现异常时会直接影响整条生产线停线,无缓冲余地;3:侧围输送后需配合翻转夹具使用。
适用范围:适用与节拍相对较低的焊装线,且侧围线需布置在主线两侧,总拼工位必须配合翻转夹具使用。
(2)双侧围配套输送
优点:输送效率高,可灵活制定缓冲库存,且不受输送距离限制,可总拼工位夹具方式可灵活选用。
缺点:需配合自动抓手或抓件机器人使用,成本高。
适用范围:适用于高节拍生产线,针对车间面积大,侧围线距离主线较远时。
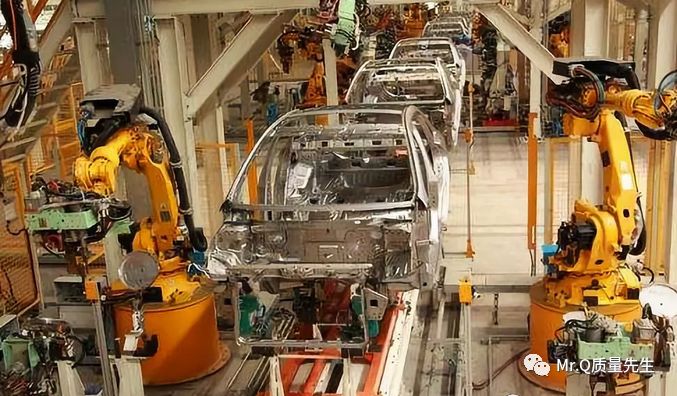
5.总拼工位结构方式
总拼工位机构方式需结合侧围输送方式考虑,其主要受场地、生产车型种类限制,常用的有翻转滑台和可切换柔性滑台、背扣式3种。
(1)翻转滑台
通过翻转夹具将侧围从水平翻转90°,利用滑台拼装侧围,该方式可与侧围输送方式配合单侧侧围输送方式使用,不用预装侧围,直接拼焊,但效率偏低,不适合高节拍生产线。
(2)可切换柔性滑台
可切换柔性滑台主要由滑台基座、可切换夹具两部分组成,夹具可以整体切换,通过切换生产不同平台车型,生产效率较高,但由于两侧滑台庞大,无法预装侧围,需额外增加预装工位。
(3)背扣式
背扣式在顶部设置转动铰链机构连接两侧夹具,往下旋转后扣在侧围上定位焊接,其主要的优势是生产效率高,但柔性差,只能生产单一车型,且必须增加预装工位,如果单一车型产量高的情况下采用较多。
总拼工位的形式多样,不限于以上3种形式,可根据实际情况因地制宜,选择总拼方案,只要保证车身精度与效率兼顾,适合当前形式需求即可。但不管哪一种方案,都必须制定合适长宽高三维尺寸要求,为同步工程及平面布置提供数据输入。
6.物流仓储规划
物流仓储规划应结合工艺布置、生产节拍综合考虑,大致应遵循以下原则:
(1)仓储区域大小应满足基本库存要求。基本库存一般不少于2小时消耗量,应根据零件总数,零件工位器具尺寸、装框数量计算仓储区域面积,确保面积不小于2小时库存需求面积。
(2)仓储区域应靠近在车间物流门及厂区物流通道。
(3)结合物流效率与场地节约性考虑,焊装线之间的物流通道宽度一般3m左右。
(4)所有需要装件的工位均需预留物流通道,保证配送空间。
(5)物流方向不能与车身整体流向相反。
7.平面布置及仿真验证
平面布置应结合厂房结构以及前面确定的工位数量、侧围输送方式、总拼工位三维尺寸数据等进行布置及仿真模拟,以验证厂房结构及工艺规划的可行性。具体过程中应注意以下事项:
(1)所有需要装配零件的工位两侧均需布置物流通道及配送空间;
(2)根据侧围配送方式,单侧围配送需保证侧围线布置在主线两侧,否则无法实现侧围配送;
(3)应避开厂房钢结构,避免钢结构立柱在工位中间或者物流通道中间;
(4)所有夹具、设备、工位器具、厂房结构等均按1∶1实际尺寸布置;
(5)受厂房结构限制,需要转弯时,需充分考虑因此损失的作业工位,因为旋转滚床工位是无法作业的;
(6)线体宽度应结合作业空间、工位器具摆放空间、夹具及设备尺寸综合考虑;
(7)前舱、地板、门总成等分件焊接的区域,应尽量靠近其总成上线的位置;
(8)所有布置完成后,应充分检查是否存在干涉区域,如存在即时调整布置。
声明:本平台只提供分享和交流不作商业用途,如侵权请及时联系我们删除!
来源:Mr.Q质量先生