随着节能减排要求的提升,全球汽车制造商在设计制造汽车时都在追求车身重量的减轻。同时,这也对汽车的安全性能提出了越来越高的要求。为了达到这一目的,汽车制造商往往会在车身的结构设计中使用多达60%以上的高强钢和超高强钢材料。
而这对各种高强钢的点焊工艺技术提出了新的挑战:这些新型高强钢材料焊接规范特性参数窗口非常窄,焊接电流的规范参数窗口甚至小于500A 的规范窗口,为了得到合格焊点熔核直径要求,制造商往往只能使用较大的焊接电流规范,这样就会引起焊点极大的飞溅和毛刺的出现。而借助我们的中频自适应点焊技术产品,可以完美地对各种热成型钢板进行无飞溅,无毛刺的焊接。
什么是热成型钢板?
热型形钢板是指将硼钢钢板高温加热后,快速转移到模具中高速冲压成形,在保证一定压力的情况下,制件在模具本体中以大于27℃/s的冷却速度进行淬火处理,保压淬火一段时间,所获得的超高强钢零件。
为何要使用热成型钢板?
优势一:
极高的材料强度及延展性
一般的高强度钢板的抗拉强度在400-450MPa左右,而热成形钢材加热前抗拉强度就已达到500-800 MPa,加热成形后则提高至1300-1600 MPa,为普通钢材的3-4倍,其硬度仅次于陶瓷,同时又具备钢材的韧性。因此由热成型钢板制成的车身极大的提高了车身的抭碰撞能力和整体安全性,在碰撞中对车内人员能起到很好的保护作用。
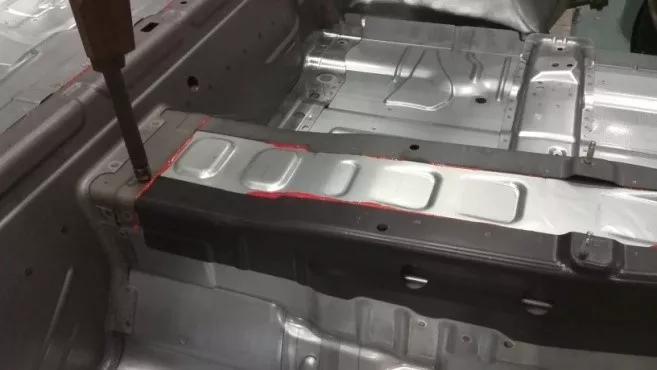
应用于地板加强板的热成型钢板
优势二:
有效的减轻整车重量,节约能耗
由于热成型钢板极高的材料强度,因此在设计时一个热成形零件可以代替多个普通钢板的零件。这种零件具有厚度薄、重量轻、强度高的特点,相比冷冲压回弹性小,适合制造汽车A/B柱加强板,地板部件,前端等部件。可以为汽车提高安全性,减轻重量。
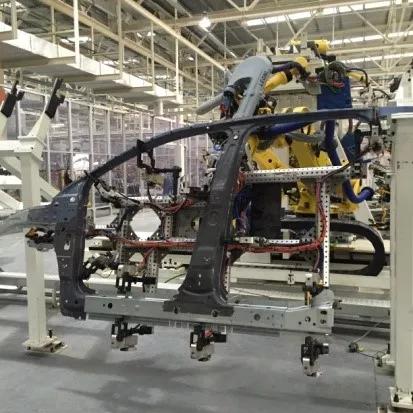
应用于侧围A/B 立柱加强板的热成型钢板
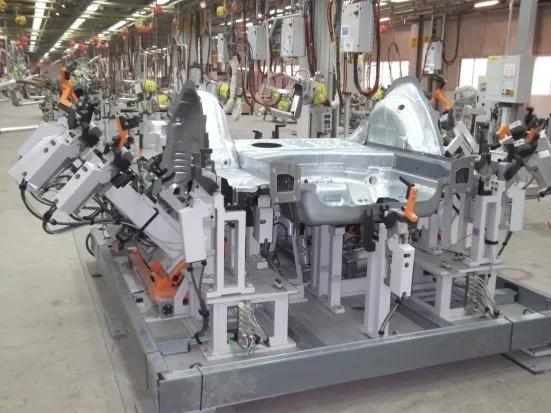
应用于地板前端的热成型钢板
例如速腾车型前后门中间的B柱,由于采用了热成型钢板则不再需要加强梁,在保证强度的情况下,减少5个零件,减重约4.5公斤,从而减少了汽车的油耗,对缩减车主的使用成本也起到了辅助作用。
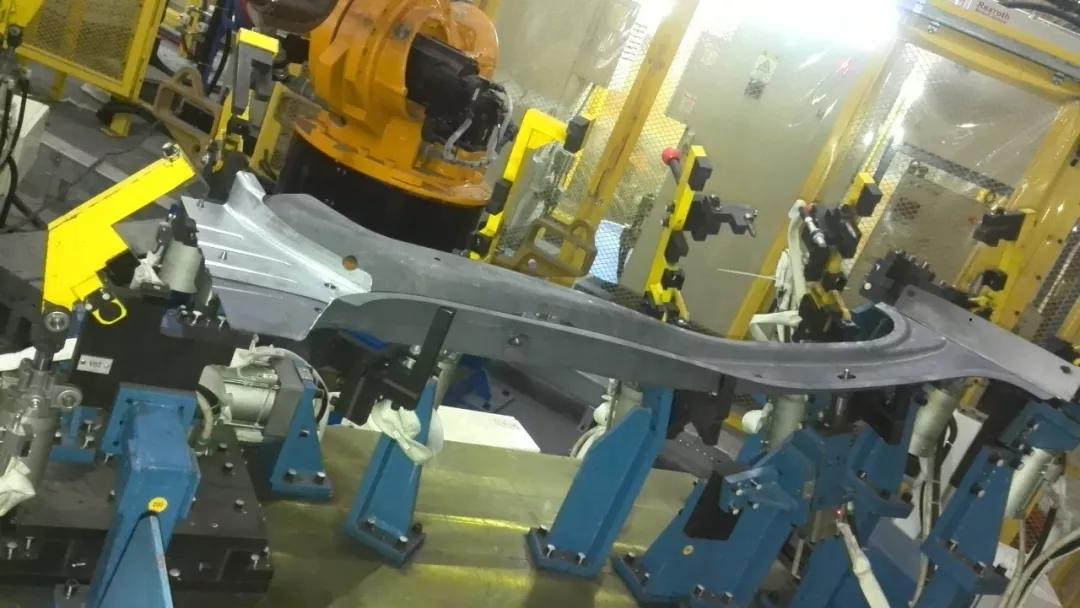
应用于车身B 柱的热成型钢板
热成型钢板的焊接难点
凭借自身的诸多优势,热成型钢板在汽车厂获得了越来越普遍的应用。同时,由于热成型钢板的电阻点焊的焊接性能非常特别,焊接参数带非常窄,不同的厂家提供的热成型钢板的焊接电阻也差别大,进口与国产的热成型钢板的电阻焊接性能也相差较大,这些都给汽车厂的零件的点焊工艺提出了严重的挑战。
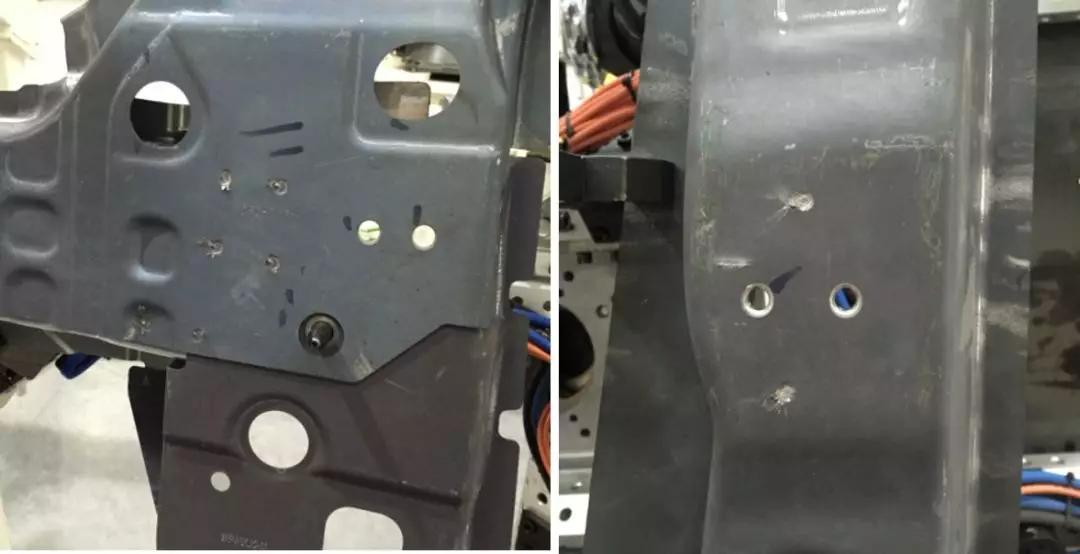
热成型钢板点焊时出现了严重的毛刺
汽车厂很难解决热成型钢板点焊时出现的大飞溅和大毛刺, 所以只能采用后续的毛刺打磨工序来解决这个问题。而设定打磨工序不但污染环境,浪费人力物力,也整体降低了汽车零部件的生产效率。
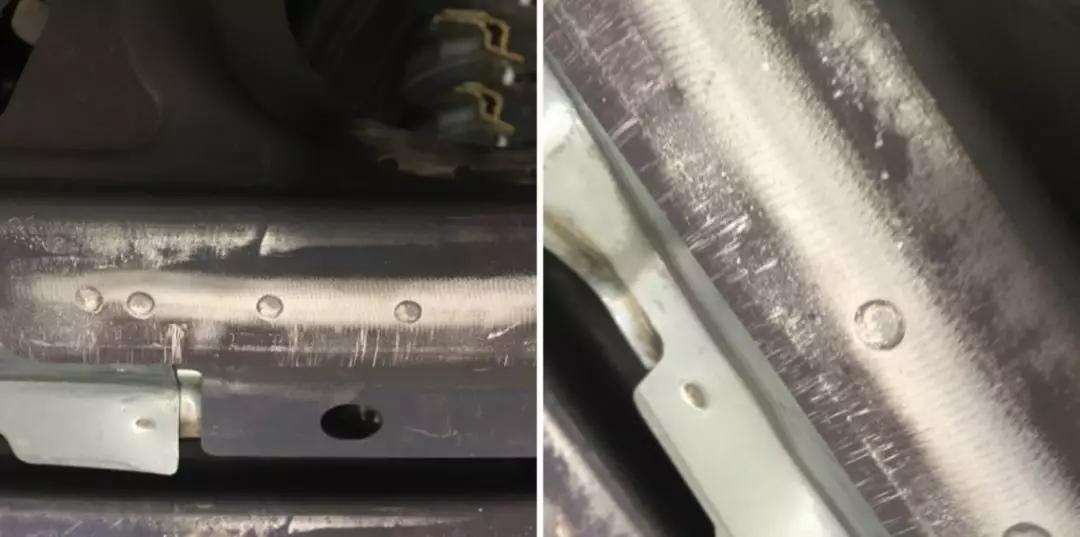
采用后续的打磨工序去掉焊点毛刺,才能达到焊点质量合格
无飞溅,无毛刺的热成型钢板点焊 :
中频自适应点焊技术
我们的中频自适应电阻点焊使用了动态电阻样本曲线的可视化方式,可以轻松地得出各种热成型钢板的动态电阻特性曲线,并详细分析出不同类型,不同厂家提供的热成型钢板的动态电阻特性曲线,从而快速地得出各种热成型钢板合格的焊接规范及其动态电阻样本曲线。
热成型钢板的动态电阻曲线,几乎都是单调下降的曲线,在准确得到焊接热成型钢板合格的焊点之后, 立即将该动态电阻样本曲线下载到博世力士乐的焊接控制器里,再打开自适应调节功能, 这样热成型钢板的焊点质量,就能得到完美控制,而且没有飞溅和毛刺, 轻松彻底解决长期困扰汽车厂的焊接工艺难题。
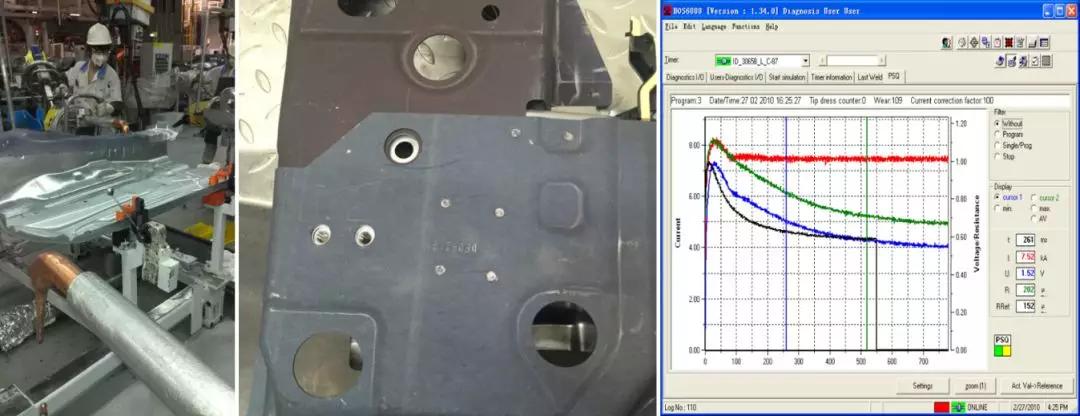
手工工位的热成型钢板点焊
无论是在手工焊接工位,还是机器人焊接工位, 博世力士乐的中频电阻点焊技术都能完美适应。
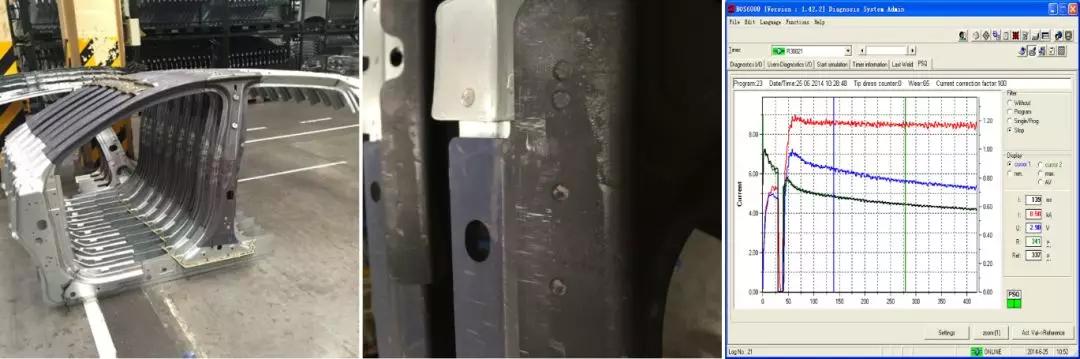
机器人焊接工位的热成型钢板的点焊
来源:博世力士乐