客户:南南铝业股份有限公司
行业:新能源汽车
解决方案:康耐视DS1101 3D位移传感器
挑战:
▪ 人工抽检方式导致检测效率低,缺陷问题很难进行数据追溯
▪ 要求视觉产品不但视野大,而且精度要高
▪ 实现激光扫描产品的图像精准拼接,测量数据难以获取
效果:
▪ 实现检测自动化,替代人工,效率得到极大提升
▪ 检测精度达到了预期,满足产品最大视野的要求
▪ 解决图像拼接及测量难题,实现数据库轻松定制
南南铝业股份有限公司(简称南南铝)是汽车、新能源及装配式特种建筑铝合金组件及材料的专业制造商。经历“南南铝三次转型升级”,已形成铝合金材料、铝精加工、铝应用和研发的完整产业链,为汽车、电器、特种建筑等领域提供铝合金零组件、材料及工程的专业服务。南南铝拥有先进的汽车铝合金零组件智能制造生产线及种类齐全的铝合金连接工艺和设备,拥有铝合金材料及精深加工的熔体净化、材料热处理、铝合金表面处理加 工和涂装、铝合金白车身加工固装和铝合金再生等专利技术和专利设备。
目前,汽车行业的材料轻量化已经成为一种趋势。在不影响车身强度的情况下,采用高强度铝合金,通过激光焊接+榫卯结构设计,可形成一体化、轻量化的车身结构,有助于降低车身自重。南南铝拥有先进的汽车铝合金零组件智能制造生产线及种类齐全的铝合金连接工艺和设备,一直加快推进新能源汽车轻量化技术应用与产品研发。拥有行业领先的汽车轻量化、铝合金材料和智能制造的专家顾问团队,并与多家行业知名科研院所和企业紧密合作、建设开放研发平台,以领先的智能制造技术研发更先进的生产线,并努力推进“全铝轻量化车身机加产线项目”和“全铝轻量化车身焊接线项目”,将新型材料更大效率的转化为产能,实现多方互赢。
全铝轻量化车身制造中的PACK板检测难题
总所周知,铝合金工件在加工过程中避免不了发生变形的问题。因此,对全铝车身机件的外形检测尤为重要,这事关汽车质量安全水平。在南南铝的全铝轻量化车身自动化生产线中,PACK板和模组焊接是关键环节,其质量检测工作更是重中之重。
过去,该工序主要采用人工抽检的方式来进行质量检测,效率低,而且缺陷问题很难进行数据追溯,不利于质检体系的自动化建设。因此,南南铝准备用先进视觉技术实现自动化检测。
但是,由于PACK板和模组焊接的工艺特殊性,要实现视觉检测应用必须要解决几个技术挑战。如:视觉产品不但视野大,而且精度要高;实现激光扫描产品的图像拼接;定位校准板如何正确选型;降低拼接图片脚本处理的难度等问题。
经过调研,南南铝的技术工程师发现,在视觉检测行业有众多的公司在分享整个市场。他们在比较很多视觉品牌提供的解决方案后,但是结果不尽如意。
“我们对精度要求比较高,比如定位销孔成型尺寸以及相对位置精度为±0.1mm,水嘴的成型尺寸精度要求为±0.5mm,螺纹孔的相对位置要求为±0.2mm,焊接成型从尺寸为±2mm,平面度精度要求为±1.5mm。”南南铝的技术工程师表示,“另外,PACK产品的尺寸都比较大,产品最大视野达到了2500*1400*130mm,所以视野小的视觉产品达不到我们的要求,而视野大的视觉产品精度却不行。”
面对这一棘手的问题,南南铝的系统集成商建议采用康耐视的视觉解决方案,来解决PACK板的检测挑战。于是,南南铝就邀请康耐视的工程师来现场进行沟通交流和产品演示。
面对南南铝的检测要求,并综合考虑现场工况,康耐视推荐了强大的三维机器视觉工具DS1101 3D位移传感器。
康耐视DS1101 3D位移传感器赢得信任
根据生产线的工艺要求和检测痛点,康耐视向南南铝提供了具体的检测解决方案和实现形式。首先将DS1101安装在2轴翻转机构上,以保证DS1101在翻转时线缆不会干扰设备的正常运行;然后整体搭载在1个3轴模组上面;3轴模组运行带动DS1101,完成产品的外形尺寸正面扫描;2轴翻转机构翻转DS1101,检测左右2个端面的厚度和加工成型尺寸,并同时检测出产品的平面度。
在设备测试时,南南铝的工程师惊讶地发现,在DS1101的高效运行下,不但精度达到了预期,满足了产品最大视野的要求,而且其他各项检测指标都相当出色。如检测速度大于80mm/s,检测宽度大于70mm,检测深度大于130mm。
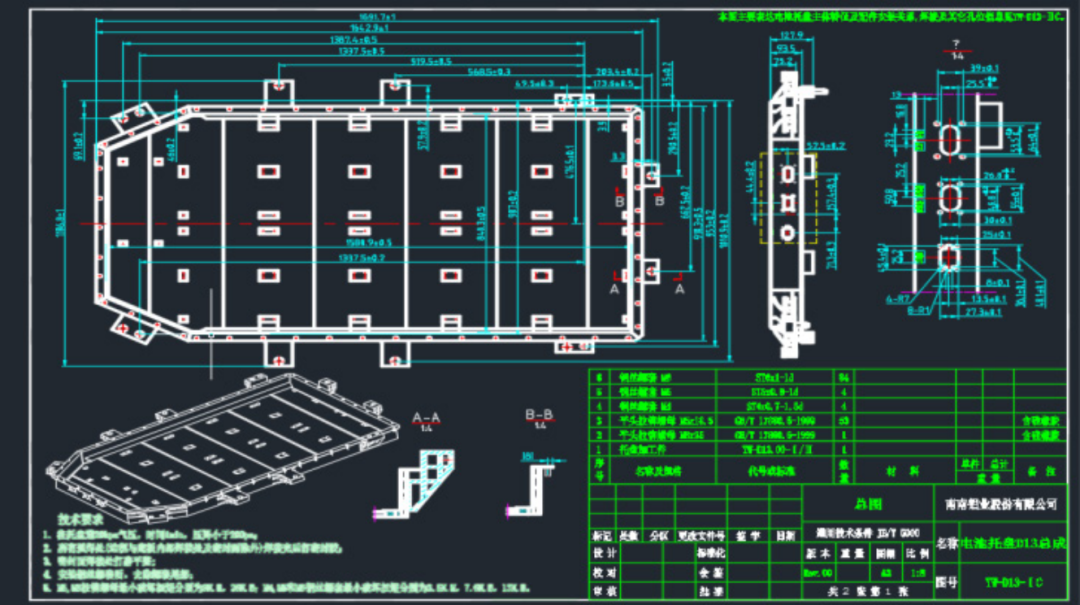
产品测量图片
而且,更让南南铝的工程师满意的是,DS1101一次扫描之后可以同时得出所有已扫描到的特征尺寸,包括销孔的外形尺寸、销孔的相对位置尺寸、台阶相对底面的高度尺寸、螺纹孔的相对位置尺寸和平面度尺寸等等。其输出图像可以拼接成产品的尺寸,并保证拼接精度符合图纸精度要求。
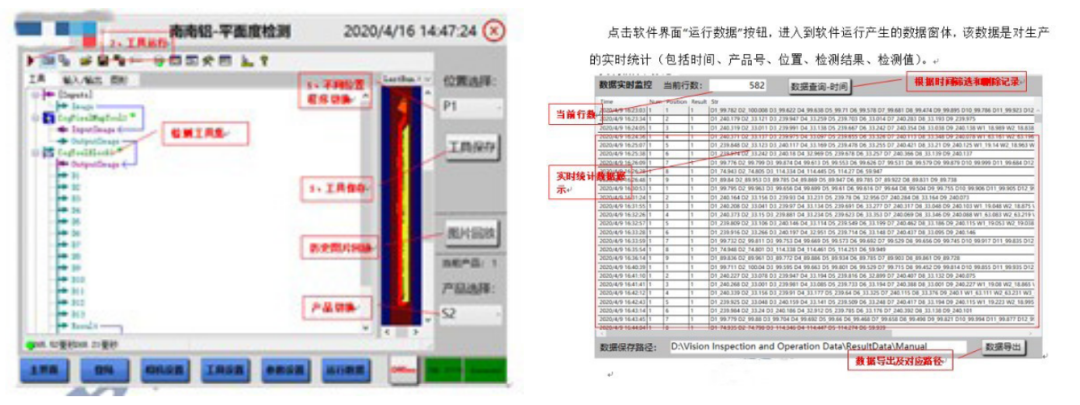
软件程序图片
“我们可以通过8块校准板标定拼接图片,并计算出成千上百个相对关系的产品对位尺寸,这极大提高了工作效率。”南南铝的工程师高兴地说,“康耐视提供的方案可以通过激光扫描测量出成千上万的数据,再通过软件算法和图像拼接,成功解决我们棘手难题!”
DS1101在测试中的强大表现赢得了南南铝的信任,“康耐视的产品及软件算法很符合我们的要求,比较智能,简单容易操作,并且还能在底层软件基础上开发出企业需要的数据库,还可以根据要求定制界面。”南南铝的生产负责人表示,“所以当看到康耐视的方案和测试结果后,我们就毫不犹豫选择了康耐视的3D位移传感器。”
实现检测自动化和智能化
目前,在康耐视先进视觉技术的帮助下,不但PACK板变形检测问题得到解决,南南铝的产线检测效率得到大大提高,而且成功实现了数据追溯,完善了车间现场的质检规范。
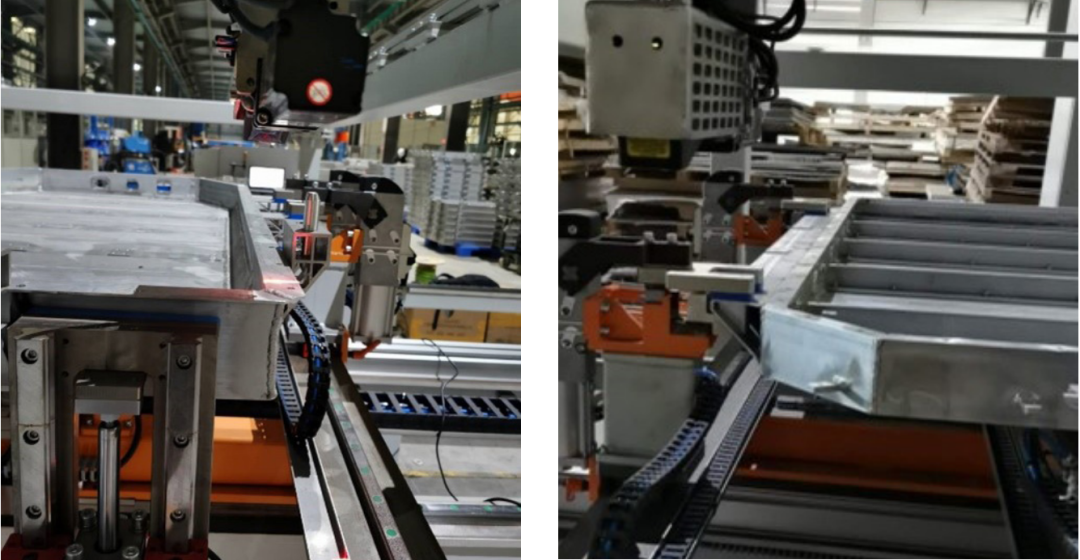
现场图片
“该工序本来需要4位质量操作工进行质量监控,每天两班一共需要8个人质检和复检,有了康耐视的视觉系统不但节约了人工成本,提高了检测自动化水平,而且检测的数据更精准正确,能够发现更多的不良问题,再也没有返工的情况发生。”南南铝的技术负责人表示,“目前产品合格率基本上在99.4%以上,而且效率比人工更快,之前一天人工只能检测几十个产品并且是抽检,现在换成视觉产品后改成全检,效率当然是高效提升了。”
“康耐视的视觉技术让我们的工厂更加自动化和智能化,现在汽车行业的客户来厂里参观考察时,对南南铝的产品质量相当认可,让公司得到了更多的订单。”南南铝的设备负责人最后评价说,“该视觉系统的成功应用,让企业只需半年不到的时间就能收回投资成本,等我们后续项目再建设的时候,一定会指定使用康耐视的产品,因为它让我们更放心、更省心!”
也正是因为有了诸如南南铝这样一个又一个复杂项目的经验与技术积累,康耐视才能始终保持视觉行业领导者的地位,并在全铝汽车轻量化的发展中提供重要的技术支持,为汽车工业的进步贡献自己的智慧和力量。
来源:汽车制造网