1 前言
随着我国经济的飞速发展以及人民对于高质量生活的追求,汽车逐渐在人们的生活中变得不可或缺。21世纪以来,国内汽车工业得到迅猛发展,汽车产量及保有量不断增加,2019年,汽车产销量均升至全球第一。汽车工业的发展给经济带来增长、人民带来便利的同时,给能源及环境带来的问题日益凸显。2021年,《中共中央、国务院关于完整准确全面贯彻新发展理念做好碳达峰碳中和工作的意见》提出要将节约能源放在首位,实行全面节约战略,持续降低能源消耗和碳排放,力争2030年前二氧化碳排放达到峰值,2060年前实现碳中和,这使得汽车工业不得不聚焦如何提升能源利用效率、减少二氧化碳排放,而汽车轻量化设计是节能减排的有效措施。
汽车轻量化可以通过3个方面综合应用来实现,分别是材料轻量化、结构轻量化和工艺轻量化。随着设计方法和制造工艺的不断改进与成熟,汽车轻量化正重点向着提高材料轻量化的使用方向发展。本文通过对铝合金在汽车轻量化应用中的优势及应用方向进行研究,提出目前铝合金在汽车轻量化应用中所面临的技术挑战,为未来汽车铝合金轻量化的研究提供参考。
2 铝合金在汽车轻量化中的应用优势
铝在地壳中储量非常丰富,因其质量轻,比强度高,良好的焊接性、耐蚀性、优异的加工成形性能及可回收再利用等优点,在汽车轻量化的生产制造中有着良好的应用前景。目前,中国单车用铝量与欧美相比差距较大,但随着汽车轻量化的发展,未来国内汽车用铝合金市场前景广阔。
2.1 有效减重、节能减排
根据美国铝业学会的报告,汽车中每使用1 kg铝,可以获得2.2 kg的减重效果,且服役期内将减少20 kg尾气排放;铝合金在汽车中的使用带来轻量化效果外,又使得制动器等零部件实现减重,即产生二次轻量化,据美国铝业公司的研究,汽车典型零件用铝的一次轻量化效果可达30%~40%,二次轻量化效果可提高至50%。此外,汽车的油耗与整车质量有着很大关系,而二氧化碳排放量与油耗呈正相关。大量数据表明,汽车质量每减轻1%,可节省燃料消耗0.6%~1.0%;自重每降低100 kg,每行驶100 km 可节约0.7 L的汽油消耗,二氧化碳排放可减少约5 g/km;若整车质量降低10%,燃油效率可提高6%~8%,尾气排放将减少5%~6%;当汽车质量减轻50%,二氧化碳排放减少13%的同时,硫化物、氮化物等其他有害物质的排放也会相应减少。
2.2 行驶性能、安全性能提高
在汽车上使用铝合金能够减轻汽车质量,且其安全性能和行驶性能可以得到提高。据美国铝业协会研究,铝合金在汽车中实现25%的轻量化效果,那么汽车加速到96.56 km/h的时间就能够缩短4 s。同时,铝合金的轻量化效果使得汽车动力传动系统负荷降低,因此在较低的牵引负荷状态下,汽车就能得到同样甚至更好的行驶性能。此外,在同样设计要求条件下,铝合金不仅能有效减轻汽车自身质量,而且吸收碰撞的性能比钢材优异。当汽车发生碰撞时,与钢材相比,铝合金材料更容易形成褶皱和变形,会多吸收50%~70%的冲击力,从而在实现车身轻量化的同时提高了汽车安全性。另外,铝合金在汽车上使用通常会使得汽车整体重心降低,汽车驾驶的舒适性及稳定性相应得到提高。
2.3 装配效率高、易回收
铝合金整体车身只有部分需要点焊,焊点少,加工工序缩短,且不需要做防锈处理,因此可显著提高汽车的装配效率 。此外,铝合金熔点低,在使用期间腐蚀率低且程度轻微,因此便于回收利用。由于生产零件采用再生铝耗能远低于原生铝所用能量,因此再生铝材料在未来汽车上的应用将得到提高。
3 铝合金在汽车轻量化中的应用
汽车用铝合金可以分为变形铝合金和铸造铝合金两部分,铸造铝合金在汽车发动机、轮毂、变速器等部位广泛使用,变形铝合金主要应用在发动机罩、翼子板、顶盖、车门、后备箱盖、覆盖件等汽车车身上(图1)。研究发现,汽车车身质量约占总质量的40%,因此降低汽车车身质量是整车轻量化的关键。
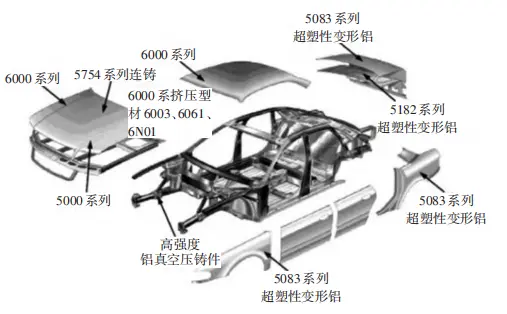
图1 铝合金在汽车上的使用
变形铝合金可分为轧制材、挤压材及锻压材,主要牌号为:2xxx系、5xxx系和6xxx系,其中2xxx系和6xxx系为可热处理合金。5xxx系Al-Mg合金在Mg元素的作用下,板材晶粒尺寸越大其成形表面质量越差,因此通常用于汽车内板;6xxx系 Al-Mg-Si合金不仅具有良好的冲压性能,而且在烤漆处理后能将强度提高,多用于汽车外覆盖件;2xxx系Al-Cu合金在汽车车身上的应用较少,因为其耐蚀性差,且自然时效与烤漆强化效果难以协同。近年来,我国汽车企业关于铝合金车身板的研究和应用逐渐增多(表 1)。东北轻合金有限公司首次采用5754铝合金薄板批量冲压制成了车门内衬,且其成形率高、质量良好;长安汽车公司利用冲压成形技术将6xxx系铝合金板材制成了发动机覆盖件,并实现量产;西南铝建成了我国第一条汽车铝合金板材生产线,并成功供应其生产的5182-O态铝合金板材;奇瑞打造的全铝车身新SUV纯电汽车,续驶里程超过500 km;蔚来ES8开发并量产了铝合金使用率高达96.4%的全铝车身;东风汽车开发的全铝车身公交车较同类客车实现了15.2%的轻量化;大众Golf电动车车身使用了全铝合金材料,整车质量成功减轻187 kg;江淮汽车在发盖内、外板上分别使用了1.0 mm厚的5180铝合金、1.2 mm厚的6016铝合金。
4 铝合金在汽车轻量化中应用的挑战
4.1 材料参数积累不足
当前,部分汽车制造类企业已经对铝合金材料相关知识和应用展开了研究,但研究不够全面、应用范围较小,加之汽车用铝合金材料的生产技术及加工工艺不成熟、生产经验相对较少,导致汽车用铝合金数据库不完整、不系统,特别是对铝合金零部件的设计、结构计算、加工工艺及使用性能方面的知识、技术严重欠缺。此外,对于铝合金的轻量化表征及测试方法也没有标准规范。
4.2 连接技术
乘用车车身大部分的工件都是通过焊接连接而成,而铝材的焊接技术难度远大于钢材,因此如何改善汽车铝合金覆盖件的焊接性能,提高焊接质量成为了扩大铝合金在汽车覆盖件上应用的难点。此外,未来汽车发展朝着多材料结构方向,这就要求对不同种类的材料进行连接(如钢-铝、镁-铝、碳纤维材料-铝等)。虽然Yan和Badu等分别通过冷金属过渡焊接和激光焊接技术在一定程度上实现了异种金属连接,但都没有得到广泛地应用,因为冷金属过渡焊接时,熔滴一旦接触到熔池将会发生短路,导致焊接过程不稳定;而激光焊接在焊接时焊缝内气体不易溢出,焊缝质量不理想。此外,传统的焊接技术不能满足异种材料连接时存在的变形和应力、界面硬脆相、电化学腐蚀评价检测问题,因此探究连接新技术尤为重要。
4.3 涂装性能
铝合金材料的涂装前处理工艺与钢材基本相同,但传统的钢板磷化处理时,磷化液中游离的氟离子含量较低,不能对铝板进行腐蚀,导致铝板生成的磷化膜质量不高。正常情况下,板材涂装后的耐蚀性及附着性与磷化膜质量息息相关,磷化膜质量过厚,板材涂装后的耐水二次附着力会显著下降;而磷化膜质量过低,则板材耐蚀性下降。有学者研究发现,铜和镁的添加能够改善铝材的磷化膜质量, 但是添加后铝材的耐腐蚀性能都会变差。此外,铝合金种类不同时,其磷化膜的大小、质量和附着状态、电泳漆膜及面漆的外观、附着力、硬度、光泽、耐水、耐腐蚀、耐冲击性能都有所区别,需要对其全面测试才能满足汽车涂装的性能要求。可见,铝合金材料涂装前处理工艺的多样化和复杂化将成为铝合金在汽车上应用的一大挑战。
4.4 冲压成形技术
汽车车身构件的主要成形方式为冲压成形,相较于已广泛研究应用的钢,铝合金板材的冲压成形技术还不成熟,存在着大量问题。铝板塑性及延伸率较钢板差,弹性模量也只为钢的三分之一,在冲压成形时会因为倒角和间隙偏小使得金属流动困难,因而板材各处受力不均匀,极易产生裂纹和起皱缺陷,且成形后出现回弹现象,将导致板材成形精度出现偏差。另外,铝板表面氧化膜较钢板塑性差、易破碎,在成形过程中不具有润滑作用,并且铝合金修边时料屑难以控制。此外,2系、6系及 7系可热处理合金在室温放置时不可避免地存在自然时效现象,这将影响板材的成形性能且使得人工时效效果降低。因此,未来应当综合考虑影响铝合金板材冲压成形性能的主要因素,比如工艺参数、圆角大小、材料属性、压边力、摩擦系数、润滑情况等因素;同时重视对铝合金先进加工制造工艺的研究,改善并解决铝合金的成形缺陷,提高成形铝的合格率。
5 结束语
随着国家对能源及环境问题的日益重视,轻量化已成为汽车工业节能减排的重要举措,而铝合金以其独特的优势成为汽车轻量化的首选材料。目前,我国已在汽车铝合金轻量化上取得一定的成果,但在材料参数、连接技术、涂装性能及冲压成形技术方面存在挑战,因此需要汽车类企业加大对汽车铝合金轻量化的研究。
来源:AEE汽车技术平台