摘要
为从材料成本控制角度降低冲压成本,从材料利用率提升、钣金制造新工艺应用、合理选材 3 个方面,结合具体的应用案例,探讨了汽车冲压材料成本的控制策略。首先,针对材料利用率可从产品协同开发、冲压工艺优化及冲压废料再利用 3 个方面进行提升。其次,钣金制造新工艺方面可采用辊压、集成式热成形等工艺代替单件冲压或多件单独冲压后点焊的工艺。最后,针对合理选材,给出了同强度钢材选择原则、烘烤硬化钢代替无间隙原子钢和高强度钢的应用建议。
关键词:材料成本 材料利用率 产品协同 工艺优化 合理选材
1 前言
随着全球汽车行业的快速发展和竞争的加剧,主机厂对降低成本、提高效率和保持竞争力的需求日益凸显[1]。材料成本控制作为汽车冲压制造的重要一环,成为汽车制造企业关注的焦点之一。有效的材料成本控制不仅可以直接降低生产成本,还可以提高资源利用效率,推动工艺技术的创新,提升产品质量,从而实现企业的可持续发展。
汽车冲压件的制造成本包括一次性成本和长期成本[2]。一次性成本主要包括设备成本与模具成本,长期成本包括设备部件的损耗成本、人员成本、能源成本、材料成本等。其中,材料成本随着产量增加呈线性增加,材料成本控制对于冲压降本非常重要[3-5]。
本文从产品协同开发、冲压工艺优化、废料的利用、新工艺应用、选材的原则等方面探讨汽车冲压材料成本控制的具体策略和方法。
综合来看,材料成本的控制措施主要包括 3 个方面:提升材料利用率、采用新的钣金制造工艺、合理选材。本文针对这 3 个方面,结合具体应用案例进行探讨。
2 材料利用率提升
材料利用率可从产品协同开发、冲压工艺优化以及冲压废料再利用 3 个维度提升[6]。
2.1 产品协同开发
在冲压件同步工程阶段,产品设计决定零件的材料利用率上限[7]。因此,需要以材料利用率为目标进行产品协同开发,对产品进行合理的合并、拆分、优化局部特征及公差定义。
2.1.1 零件合并设计
图 1 为某车型的后盖合并设计案例,原始方案设计分为后盖上部与后盖下部 2 个零件,材料均为厚度为 0.6 mm 的 CR210IF,将 2 个零件合并设计为一体式后盖,可以减少拉延补充面,材料利用率由43.9% 提升至 46.9%。
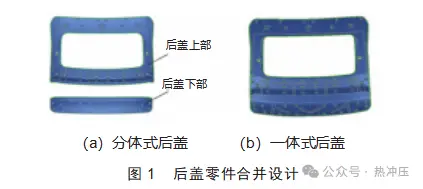
2.1.2 零件拆分设计
图2为某车型的侧围C柱内板拆分设计案例,将整体式零件拆为2个零件,并焊接。零件拆分后,冲压综合材料利用率由45.3%提升至50.4%。
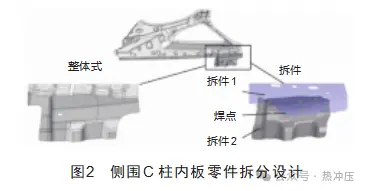
需要注意的是,拆件方案虽有利于零件材料利用率提升及成形性控制,但会增加焊接成本,对NVH 性能可能有不利影响,需要基于更全面的评价结果进行方案取舍。
2.1.3 零件局部优化
图 3 为拼焊板(Tailor-Welded-Blank,TWB)天窗加强件拼焊缝位置优化示例,该零件由厚度为2.4 mm 和 1.5 mm 的 CR3 拼焊而成,在保证车辆强度及冲压成形性能的前提下,将焊缝由中间位置向两侧移动,当移动距离为 70 mm 时,所需料片总质量由 20.3 kg 减少至 19.0 kg,单车约减少 1.3 kg材料。
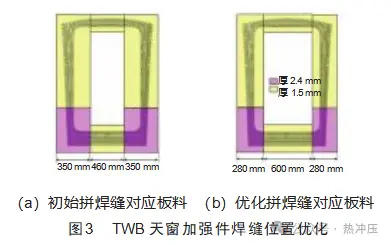
2.1.4 合理定义零件公差
常规产品边界公差要求为±0.5 mm,需要采用 拉延后精切边的工艺,一般工艺要求留有 5~ 10 mm 切边余量 。若将产品边界公差放大为±2 mm,则可在工艺上对零件边线使用预开法 ,对影响材料利用率的敏感区域进行板料边界精准预测 ,经过拉延或成形后即可满足边界公差要求 ,取消后序精切边 。 图 4为热成形加强件案例 ,图 4a 为常规公差定义下的冲压状态 ,料片尺寸较大且冲压后料片距离零件边界有较大余量,图 4b 为合理公差定义后的冲压状态 ,料片尺寸较小且冲压后料片距 离零件边界几乎没有余量,材料利用率由 85.3% 提升至 91.2%。
2.2 冲压工艺优化
冲压工艺方案对材料利用率具有显著影响,本质上是考虑如何减少工艺补充面造成的材料浪费,可以通过浅拉延及其衍生方法的应用、合并拉延、零件嵌套拉延以及合理的落料排样提升材料利用率。
2.2.1 浅拉延及其衍生方法的应用
在保证零件质量的前提下,尽可能减小补充面可提升材料利用率,浅拉延是最常用的方法,下面介绍浅拉延及其衍生方法。
a. 单纯浅拉延:零件的拉延深度直接决定工艺补充面的面积,浅拉延可以显著减小工艺补充面的面积,进而提升材料利用率。图 5 为某翼子板采用不同拉延深度的材料利用率对比,图 5a 为采用较深的压料面设计的深拉延状态,图 5b 为压料面抬升后的浅拉延状态,采用浅拉延后材料利用率由 33.6% 提升至 37.5%。
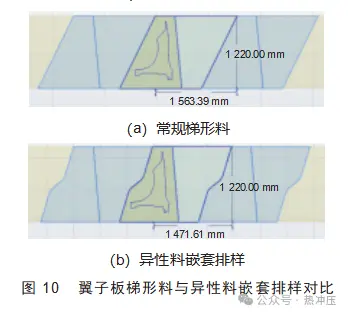
一般来说,门外板、牌照板等平坦零件可采用锁死筋与浅拉延配合的方式大幅提升材料利用率。但为保证材料被充分拉伸,零件通常有最小减薄率的要求,以利于回弹尺寸及表面质量控制,实际应用时应结合仿真结果确定最小拉延深度。
b. 开口拉延:当零件某个方向或某些局部的拉
延深度为 0 时即为开口拉延,属于浅拉延的衍生方法。图6为侧围内板采用开口拉延和闭口拉延的对比,在零件上、下两侧将图 6a 的封闭拉延设计改为图 6b 的开口拉延,可使卷料宽度由 1 300 mm 减小至 1 160 mm。
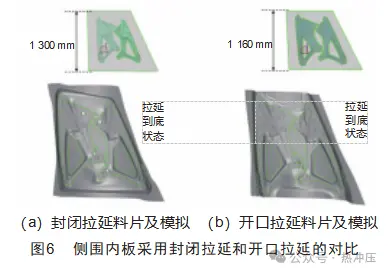
需要注意的是,开口拉延状态下零件的拉伸充分性低于封闭拉延,需要基于零件的拉伸状态以及回弹情况确定更合理的拉延方案。
c. 三动拉延:三动拉延为浅拉延的另一种衍生方法。一般而言,拉延工艺的压料面均设置于零件的同一侧,以保证压料闭合状态良好。例如,单动拉延时压料面均位于零件下方,双动拉延时压料面均位于零件上方。对于深度较大的零件,该设计往往需要较大的工艺补充面,而采用三动拉延可大幅降低工艺补充面,即外部的压料面设计成上部和下部均为运动部件。
以后盖内板为例,图 7 为采用三动拉延和传统拉延的工艺面对比,三动拉延工艺面可以使工艺面的线长显著小于传统拉延工艺面,特别是在零件的缓冲块安装面和锁安装面附近,线长减少量可达 70~80 mm,从而显著提升材料利用率。
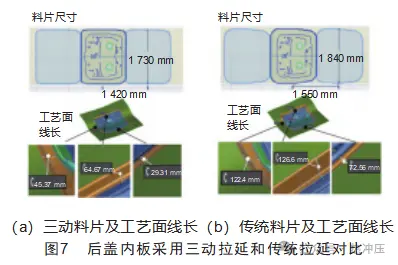
2.2.2 合并成形
对于门外板、无框门内板、部分后盖等常见的覆盖件,采用合并成形能够显著提高材料利用率。图 8 为典型零件采用合并成形方式的案例,门外板材料利用率由图 8a 单独拉延的 73.2% 提升至图 8b合并拉延的 77.3%。
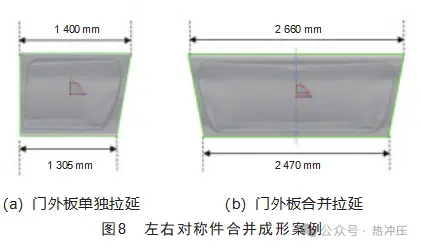
合并成形不仅局限于左右对称零件,只要 2 个或多个零件使用的材料相同且零件尺寸和型面走势满足合并成形工艺要求即可进行合并成形设计。需要注意的是,该设计需在同步工程阶段进行模拟验证。
2.2.3 套件生产
还有一种特殊的合并成形是在较大零件的非产品区域嵌套较小的零件。例如,前盖内板减轻孔、门内板窗孔、后盖窗孔、天窗加强件窗孔等区域均可以考虑嵌套具有相同材料属性的小尺寸简单零件。图 9 为后盖嵌套前盖锁加强件,综合材料利用率由嵌套前的 53.5% 提升至嵌套后 56.4%。
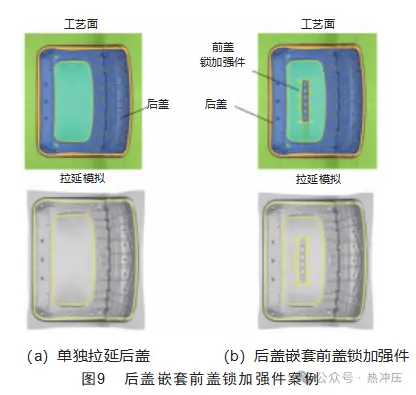
2.2.4 落料排样
对料片尺寸的优化也是常用的材料降本手段,本质上是减少工艺补充面的材料消耗。将常规的方料、梯形料等规则形状料片改为不规则的形状,进行落料嵌套,可在一定程度上提升利用率。
图 10 为翼子板排样优化案例,从图 10a 的常规梯形料优化为图 10b 的异性料嵌套排样后,单个零件可节省约 0.3 kg 材料。需要注意的是,异形料增加了落料模具成本,因此,需要结合预期产量等指标综合考虑总成本的影响。
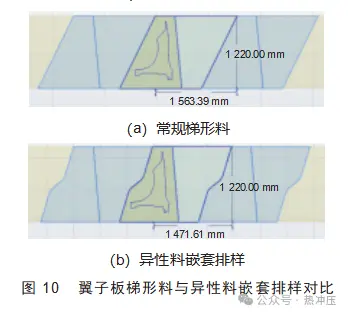
上述案例是针对一个零件的料片进行优化与嵌套排样。此外,还可以对不同的零件在同一个卷料上进行嵌套排样,从而达到更高的综合材料利用率。
对料片进行嵌套同样存在风险,例如,开模后如果发生零件设计变更,嵌套方案的调整灵活性比方料或梯形料等常规方案要差,某些情况下可能会牺牲材料利用率,因此,需要结合零件的更改可能性进行合理选择。
2.3 废料再利用
将冲压废料再利用于其他零件能够大幅降低材料成本。以冷冲钢材 CR3 为例,冲压废料销售费用比冲压前的原材料采购费用低约 5 元/kg。冲压废料分为拉延前和拉延后 2 种。拉延前废料是在开卷落料阶段产生的,废料与母材性能一致。拉延后废料是拉延后切割获得的,相比母材已经有一定的减薄和塑性变形强化。
2.3.1 拉延前的废料利用
侧围等零件通常有较大落料废料,可用于较小零件的冲压。图 11 为某侧围废料再利用案例,其门洞及车顶区域的 3 块废料可分别用于 2 个隔板、2 个行礼箱封板及 1 个尾灯支架盖板零件冲压,单个侧围可重复利用的废料约为 0.75 kg。
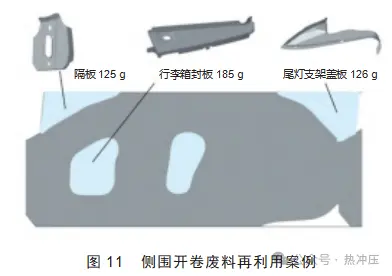
常规落料线无专门收集废料的装置,需按照废料收集的需要进行改造,一般采用废料小车。
2.3.2 拉延后的废料利用
由于拉延后的废料性能发生变化,需进行试验得到拉延后材料的参数,基于更新的模拟材料卡进行零件可制造性分析,才可应用于其他零件的制造。
表 1 为厚度为 0.8 mm 的 CR3 用于某车顶拉伸前后的材料参数对比,拉伸后选取天窗区域材料进行性能检测,材料拉伸后的成形性能相关指标均有不同程度的降低。
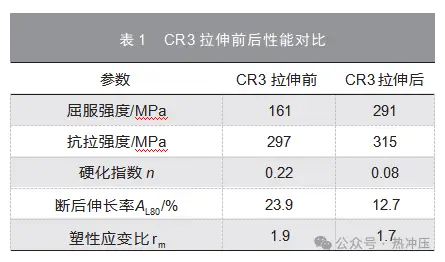
图 12 为基于 2 种不同的材料参数对相同拉延工艺下的尾灯封板进行成形模拟的结果,使用拉伸后的 CR3成形性明显恶化。因此,对拉延后的废料利用务必要基于合理的材料性能作为分析前提。
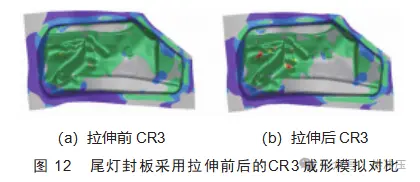
图 13 为车顶拉延后天窗区域废料利用案例。图 13a 方案 1 是将废料用于 4 个相同的车顶后横梁,图 13b 方案 2 是将废料用于 3 个不同零件,包括1 对左右对称件 D 柱加强板和 1 个非对称件车顶后横梁。该车型所有车顶都有天窗,从零件数量配比的角度看,更推荐方案 2,因为车顶与废料再生产的零件数量配比是 1∶1,更经济。
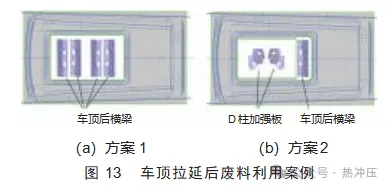
3 应用钣金制造替代工艺
某些特定的产品可采用替代工艺,相比常规单件冷冲压工艺或者多个单件冲压后再焊接为总成的工艺具有更大的材料成本优势。常用的替代工艺包括辊压和集成式热成形。
3.1 辊压
导轨、门槛、梁类件可采用辊压工艺代替冲压,典型零件有前后防撞梁、座椅滑轨、座椅横梁、门槛加强件、车窗玻璃导轨等[8],目前已有部分量产车型使用辊压制造出厚度为 2.0 mm、抗拉强度为 1 700 MPa 的梁类件。
图 14 为某车窗玻璃导轨结构及辊压成形模拟结果,相比冲压可提升材料利用率及生产效率。
3.2 集成式热成形
集成式热成形可以代替“多个单件冲压后再 焊接”,热成形需要的补充面相较冷冲压要小 ,同 时节省了 2 个冲压件用于焊接的搭接区域。
图 15 为该方案的典型应用案例 ,用于一体式(a)拉伸前 CR3 (b)拉伸后 CR3门环制造 。
图 15a 为常规方案,需要将多个件单独 冲压成形后再焊接为整体门环 。 图 15b 为集成式 热成形方案,将料片拼焊为环形料片后,再整体热成形 。零件质量由 23. 1 kg 减轻至 19.2 kg,原材料 由 41.3 kg 减轻至 32. 1 kg。
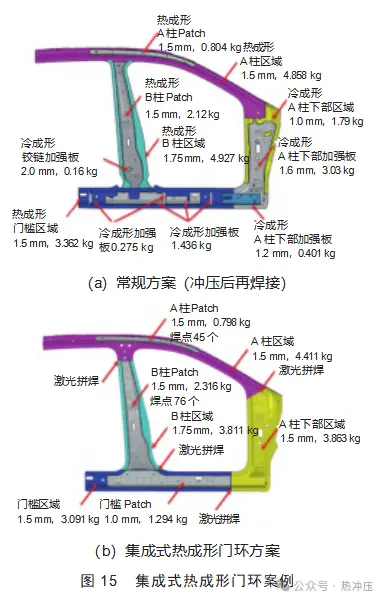
2 种方案的经济性对比如表 2 所示 。 目前热成形门环最成熟的方案是铝硅镀层板加镀层剥离拼焊,由于专利保护原因,其单片坯料成本较高。近年来 ,针对原材料的薄镀层 、镀锌 、无镀层等低成本材料方案以及针对拼焊工艺的无剥离镀层或半剥离镀层填丝焊已有大量研究 。随着这些低成本方案的逐步成熟 ,集成式热成形技术的成本优势会更加明显。
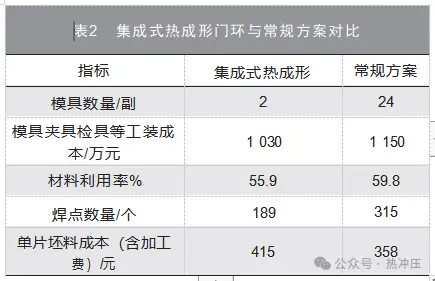
需要注意的是,集成式热成形门环相比常规门环方案有一定的技术难度,包括:拼焊板质量的控制、大尺寸热成形件的生产稳定性、焊缝位置的成形性控制、采用低成本裸板需要进行喷丸处理难以保证生产稳定性等。
4 合理选材
材料的牌号、厚度、镀层等对材料价格均有影响,进行产品定义时,在满足车辆性能要求的前提下合理选材可显著降低成本。下面针对外覆盖件常用材料说明低成本选材的原则。
4.1 同强度钢材选择原则
相同强度的钢材,其价格一般与零件的成形性正相关,即成形性越好的材料价格越高,因此,尽可能通过优化零件结构,使性能一般的材料满足成形性要求。
例 如 ,相 同 厚 度 的 CR3 相 比 CR4 成 本 约 低350 元/t。图 16为针对 CR3门内板的成形性优化案例,原始产品拔模角度较小,采用 CR4 成形性符合要求,采用CR3成形开裂。将产品拔模角放大,采用CR3也能够满足成形性要求,从而降低材料成本。
4.2 烘烤硬化钢代替无间隙原子钢
在设计翼子板、门外板、前盖外板等覆盖件时,有 2 种钢经常被选用:一是无间隙原子钢,在超低碳钢中加入适量的钛或铌,使钢中的碳、氮间隙原子完全被固定成碳、氮化物,钢中没有间隙原子存在;二是烘烤硬化钢,在低碳钢或超低碳钢中保留一定量的固溶碳原子,必要时通过添加磷等固溶强化元素提高强度[9],钢板成形后经涂漆烘烤处理,强度及抗凹性会进一步提高[10]。
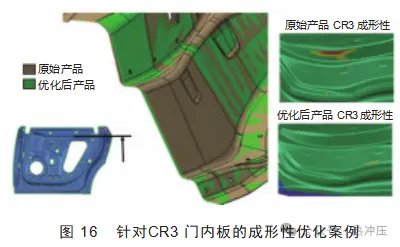
为降低成本,充分利用烘烤硬化钢的成本优势与烘烤后性能提升的特点替代无间隙原子钢。表3为无间隙原子钢 CR210IF 与烘烤硬化钢 CR180BH的对比,油漆烘房烘烤前二者成形性均可满足零件成形要求,烘烤后二者强度指标较为接近,后者价格比前者低约 150 元/t,因此,可在保证成形性及零件强度与抗凹形的前提下显著降低成本。
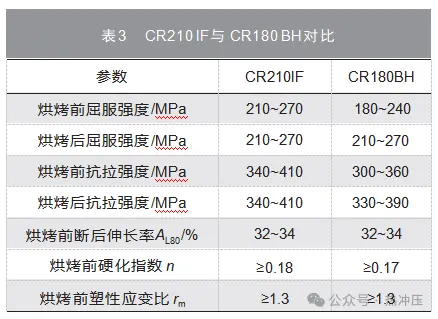
需要注意的是,烘烤硬化钢具有时效性,通常需要在生产后 3~6 个月内使用完毕。
4.3 选用高强度钢材
采用厚度更薄的高强钢替代低强度钢可降低材料成本,该方案常见于结构件,也可用于部分外覆盖件。
表 4 为门外板采用常规材料 CR180BH 与替代材料 DP500 的对比,由于后者强度更高,抗凹性更好,可将零件厚度由 0.65 mm 减小至 0.6 mm,甚至更低。以某 A 级 SUV 为例,相比 CR180BH,采用DP500 可降低整车 4 个门外板材料约 1.25 kg,在材料单价少量增加的情况下,显著降低材料成本。
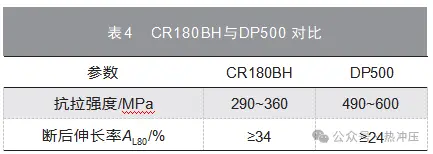
需要注意的是,采用 DP500 进行外覆盖件设计需要针对高强钢回弹进行合理的尺寸补偿控制。
5 结束语
本文从材料利用率提升、钣金制造新工艺应用、合理选材 3 个方面探讨了汽车冲压材料成本的控制策略,得到以下结论:
a 提升材料利用率本质上是要尽可能减少工艺补充面的面积。具体实现途径包括:对产品进行合理的划分和公差定义,采用尽可能小的成形深度和补充面设计冲压工艺,对无法避免的工艺废料进行再利用。
b 采用特殊工艺并设计相应的零件。采用辊压、集成式热成形等工艺代替传统工艺,可一定程度上降低材料成本。
c 在不影响零件功能及成形质量的前提下,应选用综合成本更低的材料。如基于同强度钢材选择原则,采用烘烤硬化钢代替无间隙原子钢;用更薄的高强度钢替代厚的低强度钢等。
如何更好地兼顾材料成本、产品功能要求及制造质量稳定性,是上述策略实施过程中需要重点关注的问题,也是需要进一步研究的课题。
参考文献:
[1] 刘晓林. 成本定生死,车企开启技术和材料降本新竞赛[N].经济观察报, 2024-01-29(14).
[2] 刘可伟 . 汽车行业冲压成本的控制方法[J]. 模具制造,2021, 21(10): 6-9.
[3] 吕良, 段英慧, 韩振强, 等. 整车厂冲压件完全成本构成简析[J]. 锻造与冲压, 2020(10): 56-60.
[4] 曹亚东, 罗亮 . 汽车冲压件成本核算方法研究[J]. 汽车实用技术, 2018(24): 283-285.
[5] 徐明琦, 王彦, 闫丽红, 等. 材料技术在商用车冲压成本控制中的应用[J]. 汽车工艺与材料, 2018(11): 53-56.
[6] 王文华 . 汽车冲压件成本模型研究[J]. 汽车工艺师,2023(4): 60-64.
[7] 蒋磊, 陈天铎, 王龙, 等. 提升白车身覆盖件材料利用率的冲压工艺方案[J]. 汽车工程师, 2020(9): 13-16.
[8] 谢贵山, 黄宗斌, 赵肖斌, 等. 汽车车身的轻量化设计探讨[J]. 汽车零部件, 2023(2): 80-84.
[9] 胡吟萍, 李国彬, 段小平, 等. 汽车覆盖件用热镀锌烘烤硬化钢 H180BD的开发[C]// 2009年汽车用钢生产及应用技术国际研讨会, 2024.
[10] 叶仲超, 段小平. 烘烤硬化钢的硬化特性及机理[J]. 钢
铁研究, 2011, 39(1): 35-37.
来源:热冲压