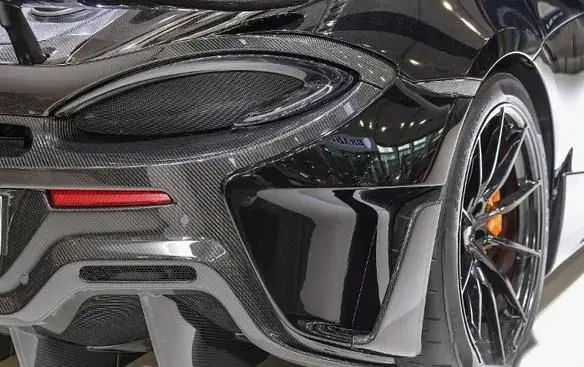
至少五十多年来,全球汽车复合材料供应链的重要工作都集中在努力使热塑性复合材料成为A级饰面水平车身面板的可行选择,包括发动机罩、车顶和舱盖(行李箱盖)。从20世纪50年代开始,热固性复合材料取代了半结构/垂直和全结构/水平车身面板上的金属。自20世纪80年代起,热塑性复合材料开始间歇性地应用于垂直车身面板,如保险杠面板和挡泥板;自20世纪90年代起,热塑性复合材料开始应用于门板和其他饰件;自21世纪初,热塑性复合材料开始应用于举升门。然而,事实证明,在水平面板上使用这一类材料很难满足汽车行业对性能、成本和美观的要求。
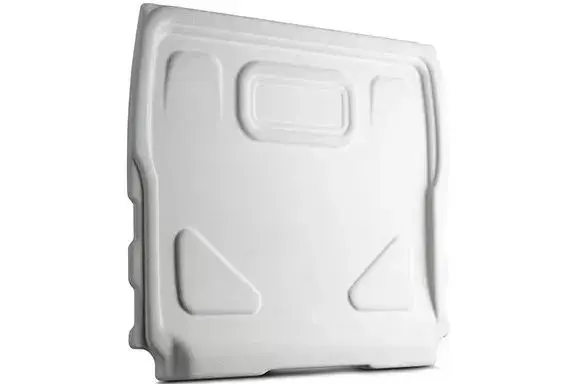
RLE国际开发了一种创新的低成本/低压压缩成型变体和热塑性夹芯板技术,该技术自2019年以来一直用于商用车的内部隔板(上图)。目前正在研究将该技术用于生产车顶外板和引擎盖。
这种情况可能正在发生变化,这要归功于英国的一种低压压缩成型和热塑性夹芯板技术。4年来,该技术一直在为一辆额定载重2吨的轻型商用车生产大型隔板。本文讨论的最新工作表明,该技术可将设计灵活性、机械性能、经济快速的加工和表面美学完美地结合在一起,最终可用于水平外板。
汽车复合车身板简史
热固性复合材料在乘用车上的应用历史悠久,可用于半结构垂直和全结构水平车身外板以及底盘/单体部件。玻璃纤维增强塑料(GFRP)于1953年首次出现在当时的通用汽车公司(现为通用汽车公司,GM,美国密歇根州底特律市)生产的新型雪佛兰克尔维特跑车的所有车身外板上。20世纪60年代,在科尔维特跑车上,手糊玻璃钢被循环速度更快、更稳定的压缩模塑片状模塑料(SMC)所取代。从那时起,SMC的使用范围已经超出了车身面板,包括结构拾取盒、底盘部件以及最近的电动汽车电池组的大型保护罩。此外,碳纤维/热固性基复合材料从20世纪90年代的一级方程式和二级方程式赛车的重要部件,过渡到车身面板,后来又从2000年代初开始过渡到街车(包括克尔维特)的整个整体车身。
注塑成型的短玻璃纤维增强热塑性塑料于20世纪80年代初首次应用于非结构性保险杠面板,到20世纪80年代中期,开始向挡泥板等其他垂直面板过渡。1990年,通用汽车的土星汽车首次亮相,所有垂直车身面板均采用注塑热塑性复合材料。不过,发动机罩、挡泥板和车顶仍采用冲压钢板,最终在2010年停产之前,整个车身外部都过渡到了钢板。
这十年间,通用汽车的其他几款车型也采用了热塑性垂直面板,例如德国慕尼黑宝马汽车公司(BMW AG)限量版(1989-1991年)Z1跑车,以及后来戴姆勒股份公司梅赛德斯-奔驰分部(现为德国斯图加特梅赛德斯-奔驰股份公司)于1997年推出的小巧的smart fortwo微型车。smart是第一款采用全热塑车身面板的汽车,尽管引擎盖和车顶面板确实非常小。2007年,smart成为第一款从玻璃纤维增强聚碳酸酯/聚对苯二甲酸丁二醇酯(GR/PC-PBT)转向滑石粉填充热塑性聚烯烃(TPO)的乘用车。
在过去的15年中,滑石粉填充热塑性聚烯烃在垂直车身面板上慢慢取代了 GR/PC-PBT和GR/改性聚苯醚-聚酰胺(GR/MPPE-PA)等工程热塑性塑料。2014年,日产Rogue跨界多功能车(CUV)首次采用全热塑性举升门(滑石粉/热塑性聚烯烃外板与长纤维热塑性聚丙烯(LFT-PP)内板粘合),这是另一个历时10年的重要里程碑。此后,其他越野车和CUV也纷纷效仿。
减重方法
故事开始于2015年左右,一家汽车制造商的工程团队找到RLE国际公司(德国科隆)英国办事处,寻求帮助降低商用车的成本和质量。RLE因其汽车设计和工程工作而闻名全球,尤其是在主要车身结构和内饰方面。因此,该公司提供全面的CAE、工程设计、造型可行性和发布支持。RLE团队提出了几种金属到复合材料的转换方案,以降低成本和质量,其中包括全结构/水平式外部顶板和客舱与货舱之间的半结构/垂直式内部隔板。
联合小组首先解决了技术上较为容易的舱壁问题。在接下来的几年中,舱壁设计不断发展,最终使该技术通过了所有原始设备制造商的性能要求。为满足原始设备制造商的最大12千牛顿冲击力要求,最终的舱壁采用了单层轻质增强热塑性塑料 (LWRT) 面板,包括聚丙烯 (PP) 浸渍的可悬浮、短玻璃、低克/平方米 (GSM) 形式的玻璃毡热塑性塑料 (GMT) 复合材料,夹心为0°/90°单向 (UD) 玻璃纤维带(也可使用织物编织)。选择LWRT蒙皮材料是为了提供良好的未涂漆表面效果。
设计结果
◆与钢材和SMC相比,结构面板的质量减少了≥50%,半结构/美观面板的质量减少了≥60%,同时与碳纤维增强塑料 (CFRP) 外面板的质量相匹配。
◆单件成本降低10%,但零件数量减少,耐久性更强,模具成本大大降低,噪音/振动/震动(NVH)明显优于金属。◆成型周期短(90-120 秒),具有出色的低温抗冲击性,可选择模内着色和100%报废回收。
隔仓板是在室温下通过低成本/低压(3.4-4.5巴)“热压/凝固”变体在匹配的金属模具中压缩成型,成型时间小于90秒。模具既不加热也不冷却,但夹层结构中使用的材料在成型前要预热。由于模具没有剪切边缘,因此在脱模后需要进行水刀修整,以清理零件边缘并切割所需的孔洞。一体式面板取代了多件式钢/聚氨酯泡沫衬垫组件,重量减轻了5.2千克,降低了单件成本,模具投资减少了80%。此外,这种全玻璃纤维/烯烃夹层结构在部件寿命结束时可完全回收利用。该获奖舱壁自2019年起投入商业使用,年产量为60,000至70,000件,但据报道,该工艺的单个工具年产量可达90,000件。
独辟蹊径
RLE的团队(由内饰/外饰开发主管Mark Grix领导)相信同样的技术也适用于车顶外板,因此选择独自开发A级水平车顶板。Grix自20世纪90年代在通用电气塑料公司工作以来,一直从事热塑性车身外板的开发工作。
由于团队预算有限,因此需要采取巧妙的方法。其中一种方法是获得三块免费的钢制车顶外板--打算在装有隔板的商用车上用作焊接车顶板的外层/表层。这些钢板身兼两职。其中一块被扫描并用于创建模板,以快速设计面板的外表皮,从而大大缩短了CAE时间。由于车顶面板的内部(B面)不是概念验证的一部分,因此团队只关注外部(A面)的几何形状和表面光洁度。
另外两块钢板被用来制作低成本的成型工具,其中一块作为核心,另一块作为模腔,用于成型相对平整的复合屋面板的A面和B面。该车顶工具随后被用于在开发项目中成型复合材料面板,Grix称它从一开始就生产出了出色的部件。
从与商用舱壁类似的夹层结构开始,铺设、成型和评估了许多不同的表皮和芯材组合(总厚度从3毫米到5毫米不等),以开发车顶板概念。在对各种材料进行预热后(不同的层受热时间可能不同),在装有上述工具(保持室温)的压缩压力机中手动铺设,并通过热压成型。研究人员再次将有效循环时间设定为90秒。
屋面板是在Airborne公司(荷兰海牙)在英国拥有的一家工厂进行模压成型的,目的是进一步发展这一概念,并为夹芯板结构实现表皮和芯材的正确组合。Airborne公司的设备非常理想,因为它配备了一个可以加热整个1.75×2.0米顶板的超大烤箱,可以将材料加热到240°C。具有讽刺意味的是,这个烤箱实际上对面板来说太大了,因此我们将烤箱的一部分隔开,这样材料的停留时间就不会太长,而且材料可以从烤箱的侧面而不是末端送入。
随后,对各种面板材料组合进行了小规模的实验室测试。最终,最有希望的候选材料通过西卡股份公司(瑞士巴尔)生产的1K结构聚氨酯粘合剂粘合到了测试车辆的车顶环/弓上,并接受了额外的车辆级测试。
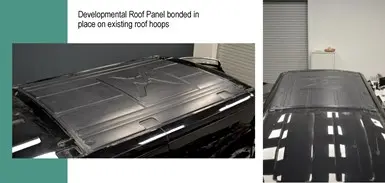
RLE在没有原始设备制造商关于开发车顶面板规格的情况下,将工作重点放在外部表皮上,目的是将车顶箍/弓保持在原位,并将复合材料解决方案粘接到当前金属车顶使用的现有焊接法兰上。之所以能做到这一点,是因为复合材料结构的线性热膨胀系数(CLTE)较低。随后的测试表明,目标热塑板的线性热膨胀系数接近铝的线性热膨胀系数。
由于最终的复合材料是在加固和成型之前在压力机中组装的,因此根据应用所需的性能和表面处理要求,RLE的技术在材料类型方面具有极大的通用性,可以组合成最终面板的表皮、内核和外表面处理。几乎可以使用任何类型的片状热塑性复合材料(如胶带、GMT、有机片、LWRT)。唯一的要求是聚合物基体必须具有化学相容性(以实现良好的材料流动性,确保成分均匀),并且具有相似的玻璃化转变温度(Tg),以便在同一烘箱中加热,而不必担心温度较高的材料会在固结/成型完成之前熔化温度较低的材料。
Grix解释说:“每个应用的要求都是不同的,所以我们可以灵活地使用纤维体积分数从20%到50%不等的材料,尽管我们通常喜欢在30-40%左右。测试表明,使用更高的FVFs并没有任何好处。事实上,如果我们有太多的树脂,那么冲击强度和层之间的附着力就会受到影响。为了获得良好的表面,有足够的树脂是绝对必要的”。
对于控制表面光洁度的最上层美观层,候选材料包括哑光或亮光热塑性薄膜、纺织品、无纺布/织物组合,甚至是抗划痕/抗紫外线硬涂层或柔软触感热塑性聚氨酯(TPU)涂层。同样,这项技术的优点在于它可以很容易地进行即时修改,以满足许多行业的应用需求。
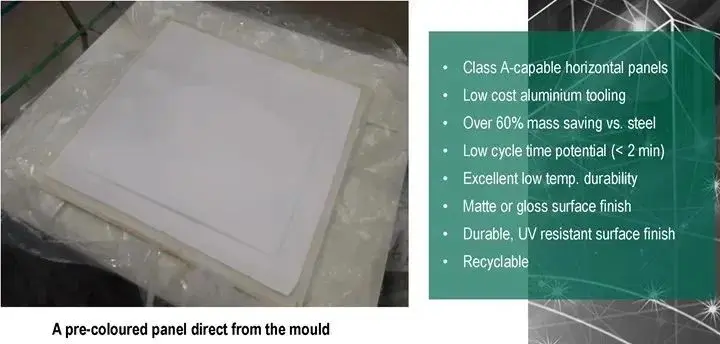
迄今为止,RLE已经使用预着色薄膜和低成本铝制工具直接从模具中生产出具有耐用且抗紫外线光泽或哑光表面的汽车A级面板,周期时间为<2分钟。与钢板相比,复合材料为结构板提供了50%的潜在质量节省,为外部/半结构板提供了60%的潜在质量节省。即使在低温下,它们也具有出色的冲击强度和完全的报废可回收性。这种热塑性夹芯板技术不仅引起了汽车行业参与者的兴趣,也引起了其他地面运输领域参与者的兴趣。
该团队研究了热塑性树脂系统(主要在烯烃和聚酰胺系列中)和增强材料(包括短切、UD和机织织物)的不同组合,用于屋顶夹芯板的表皮和芯材。由于其较高的位置,开发中的屋顶板不需要A级饰面。最初,使用预着色的黑色材料,并尝试了哑光白色面板。最近,Grix和他的团队通过在工具中涂上一层薄膜以及尝试硬涂层,提高了紫外线稳定性和耐刮擦性。面板可以使用对比色,也可以与身体的其余部分相匹配。开发中的车顶板或商用舱壁都不需要金属加固。如果将整个钢屋顶(而不仅仅是一块面板)转换为热塑性夹层技术,Grix估计可以节省24.5公斤的重量。
准备好迎接黄金时段了吗?
汽车制造商喜欢问的一个大问题是,概念车目前处于什么技术准备水平(TRL),而Grix的回答是,车顶板概念还很遥远。
他解释道:“你仍然需要做一些特定于OEM的测试,例如环境稳定性、NVH等等,但出于所有意图和目的,车顶板使用与隔板相同的材料系列和相同加工方法的变体,隔板在过去四年中一直在进行相当大的商业生产,这项技术的灵活性意味着,如果您需要提高紫外线性能或耐刮擦性,甚至使面板更厚、更薄或更坚硬,那么我们可以做到这一点。我们花了很多时间来真正了解这项技术,以及用工具制作漂亮的面板需要什么”。
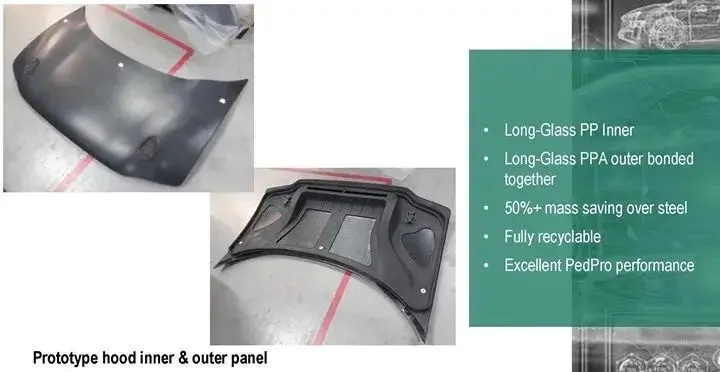
据报道,RLE正在与汽车一级供应商和农业设备和高尔夫球车等其他地面运输领域的OEM进行讨论,以实现内部和外部应用的商业化。
这项技术的下一步是什么?Grix说:“没有理由(使用正确的配方)这项技术也不能用于符合PedPro(行人保护)标准的引擎盖,我们已经生产了开发罩,小规模测试表明,我们比热固性塑料或钢具有更好的能量吸收和消散能力。此外,我们还探索了将这项技术不仅用于相对简单的面板,还用于几何复杂度明显更高的汽车内饰的高拉伸面板。结合工具的A级预着色饰面,与钢相比节省50-60%的质量,以及使用寿命结束时完全可回收的部件,我们认为这对在多个行业寻求轻质面板技术的OEM来说是一个成功的组合。我们很乐意与任何有兴趣进一步探索的人合作”。
热塑性复合材料车身面板:优势和挑战
与热固性复合材料或金属相比,热塑性复合材料是车身外板的理想材料,原因有很多。首先,它们往往更轻(比重更低),具有更好的耐损伤性(抗冲击强度)--这是满足PedPro要求的一个优势,而且它们能提供更好的出模表面,减少模后加工。
与热固性材料不同,热塑性复合材料可回收(可熔融再加工),因此更容易重复使用废料,并从报废零件中回收可用材料--这对于向欧盟销售汽车的企业来说是一个重要的特点,而且热塑性复合材料在供货时已完全聚合,这意味着成型周期更短,可重复性和再现性(R&R)更好,因此更适合大批量生产,并有助于抵消通常较高的原材料和模具成本。与金属相比,热塑性塑料还提供了更大的设计自由度,并为零件集成(减少零件数量)、插入硬件(便于连接)和简化模后装配提供了大量机会。
尽管热塑性复合材料具有诸多优点,但与所有材料一样,它们也面临着必须克服的挑战。例如,与钢或铝相比,早期的整体式热塑性复合材料车身面板具有更高的热膨胀系数(CLTE),不连续的纤维加固要求复合材料与金属面板之间留有大于理想的间隙,以适应温度循环过程中的尺寸变化。如果没有这种美学上的权衡,车门等可移动面板有时就无法打开或关闭。这一问题在很大程度上是通过以下方法解决的:将整体面板改成成对的粘合内/外面板--带或不带芯--以及在片状复合材料(如GMT/organosheet)和热塑性塑料带中使用较长的短切/非连续纤维增强材料以及连续纤维无纺布、单向和编织增强材料。
另一个问题是,汽车行业青睐的热塑性塑料牌号(主要是聚丙烯、聚酰胺6或6/6,以及聚酰胺或热塑性聚酯与PC或MPPE的混合物)缺乏热稳定性,无法在白车身(BIW)电泳涂装(e-coat)和喷漆后承受烘烤炉的温度。这增加了装配的复杂性和成本,因为面板必须离线喷涂,并在汽车装配流程的后期阶段添加。虽然热塑性塑料板的喷漆仍需离线完成,但在改善模塑着色(MIC)板的紫外线稳定性、色彩深度和金属特效方面已做了大量工作,之后只需清漆即可完成。此外,薄膜技术也取得了长足进步,它提供了比油漆更耐用的表面,符合汽车制造商降低油漆成本和环境负担的努力。
另一个配方问题是在刚度和冲击力之间取得适当的平衡,以避免使用大型金属支架将垂直面板悬挂在车辆上。与此相关的一个问题是,由于刚度和强度通常低于金属的数值,因此通常需要采用几何形状(如肋条)来实现面板的可比机械性能。然而,这往往会导致名义壁较厚,从而引起包装问题。面对必须重新设计现有车辆的车身结构以适应更厚的复合材料面板的前景,大多数原始设备制造商都会选择放弃。对于热塑性烯烃(TPO)材料来说,将非连续纤维增强材料与矿物填料相结合的精心配方工作,已使这些材料在外部垂直面板的表皮上占据了主导地位。此外,通过从整体面板设计转变为粘合内/外面板,无法满足 A级要求的结构性内面板与无法单独满足机械要求的A级外皮相辅相成。
数十年来,热塑性水平面板之所以无法使用,最大的挑战可能就是在高温下的下垂和长期蠕变问题。这有几个原因。首先,热塑性塑料在接近其Tg的温度范围内会软化,从而导致机械性能的逐渐丧失,包括承载负荷和自支撑的能力。这种特性使热塑性塑料更容易回收利用,但也会损害其在高温下的长期机械完整性。在某种程度上,从短纤维/非连续纤维加固改成连续纤维加固,以及从整体板材改成带或不带芯材的粘合板材,都有助于解决这一问题。
与此相关的一个问题是如何获得足够高的FVF或 FWF,以改善高温期间的机械性能。热塑性聚合物在供应时已预聚(成型前分子链很长),这意味着即使在熔融温度下,它们与许多液态热固性体系相比也相当粘稠。这就很难实现高水平的纤维浸润和浸渍。因此,即使在今天,FWF值超过40%的注塑成型产品也很有限,而许多热固性技术允许达到高达70%的FVF值。在某种程度上,解决这一问题的方法包括:谨慎选择树脂(例如,使用支链型聚丙烯而非线型聚丙烯,后者的粘度较低),修改热塑性胶带和GMT/organosheet生产的层压工艺,以及最近使用低粘度己内酰胺单体进行浸渍,然后反应聚合成PA6。其代价是较长的循环时间(更像热固性塑料)和专业设备。不过,随着时间的推移,在热塑性复合材料中加入更多纤维,特别是更长的连续纤维的能力不断提高,这极大地促进了热塑性复合材料在越来越多的结构性应用中的使用。这里需要权衡的一点是,对于外观美观的表面来说,较高的FVF/FWF可能会导致纤维穿透。解决这一问题的部分方法是使用薄膜、对面板进行喷漆或纹理处理,或在夹芯板组合的最外层美观层中使用较低的纤维增强层。
最后但并非最不重要的一点是,在高产量/低利润的汽车行业中,直接和间接成本始终是一个敏感点。当复合材料行业致力于改进材料和工艺以应对一个又一个车身面板挑战时,铝和钢铁行业的同行们也在不断改进他们的材料和工艺。即使在今天,除非改用复合材料能使汽车减轻大量重量、带来重要的制造优势或使安全性或功能性达到新的水平,否则大多数汽车制造商都会拒绝使用复合材料,除非使用复合材料的成本至少与传统材料持平或更低。
来源:中欧SENIA