目前,汽车零部件呈现集成化、国产化、轻量化发展趋势。
集成化:降本增效是核心推动力
一体化压铸:掀起车身制造革命,国内厂商纷纷布局
一体化压铸是通过重新设计,将原本需要组装的多个独立零部件,利用大型压铸机进行一次成型。传统汽车车身制造包括冲压、焊装、涂装和总装四大环节,工序繁琐且耗时较长。例如,传统的焊接过程需要对数百种车身结构件进行数千次焊接,以完成车身组装。相比之下,一体化压铸将冲压和焊接步骤合二为一,显著简化了制造流程。这种创新技术不仅降低了整车厂的生产成本,同时提升了生产效率。
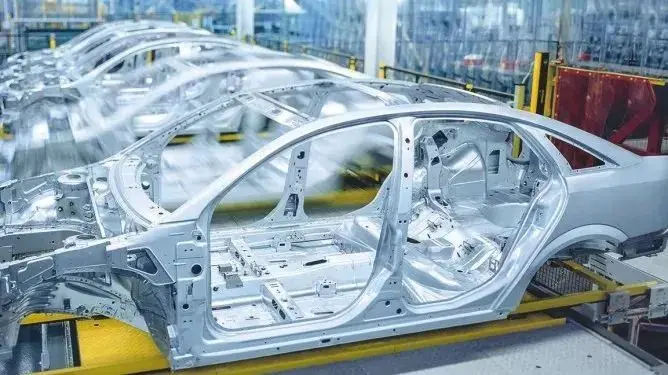
生产线成本:通过使用大型压铸机,工厂的占地面积减少了30%。时间成本方面,采用一体化压铸技术后,底板的加工时间约为80-90秒,显著提高了生产效率。在人力成本方面,传统焊装工厂通常需要200-300名生产线工人,而采用一体化压铸技术后,每台设备只需要2-3人操作,大幅降低了人力成本。
热管理:一体化集成热管理系统成为电动汽车的大势所趋
电动汽车热管理子系统包括电池热管理系统、电机热管理系统和热泵空调系统等。在电动汽车早期发展阶段,这些系统的热管理功能是相互独立的。例如,乘员舱制冷通常采用传统空调制冷系统,而采暖则使用高压PTC技术。至于电池包的冷却,则依赖空调制冷系统对冷却液进行二次换热并进行再冷却处理;电池包的加热则利用高压PTC技术。至于电机的冷却,通常采用前端散热器进行冷却。
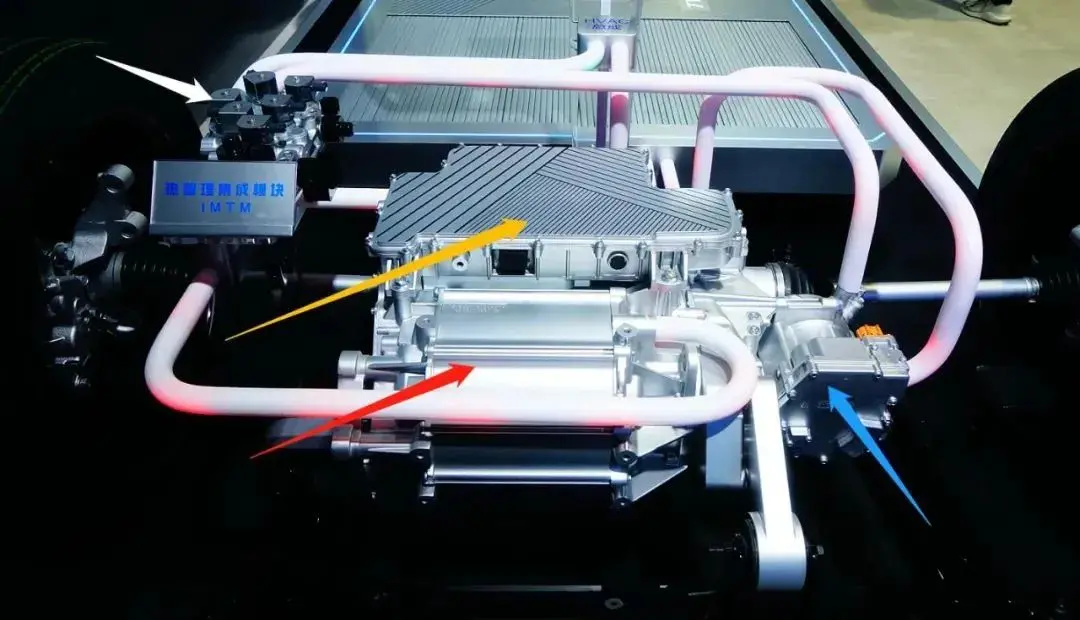
分散式热管理系统由于部件众多、体积大、质量重、能耗高,导致系统成本昂贵。在电动汽车需要解决续航里程和整车能效的压力下,随着电动汽车技术的发展,一体化集成热管理系统以其低能耗、广泛适应性、低成本和紧凑结构成为不可避免的趋势。一体化热管理系统的优势在于:成本更低;占用空间更小;提高了主机厂的装配效率;能够高效地管理热量分布。
电驱动系统:向集成化趋势发展
电动驱动产品系统正朝着集成化发展的趋势迈进。过去,电动汽车的三电系统通常由单独的零部件采购,并根据电气和机械结构进行集成和组装。近年来,这些系统逐渐演变为二合一、三合一甚至多合一的集成产品。
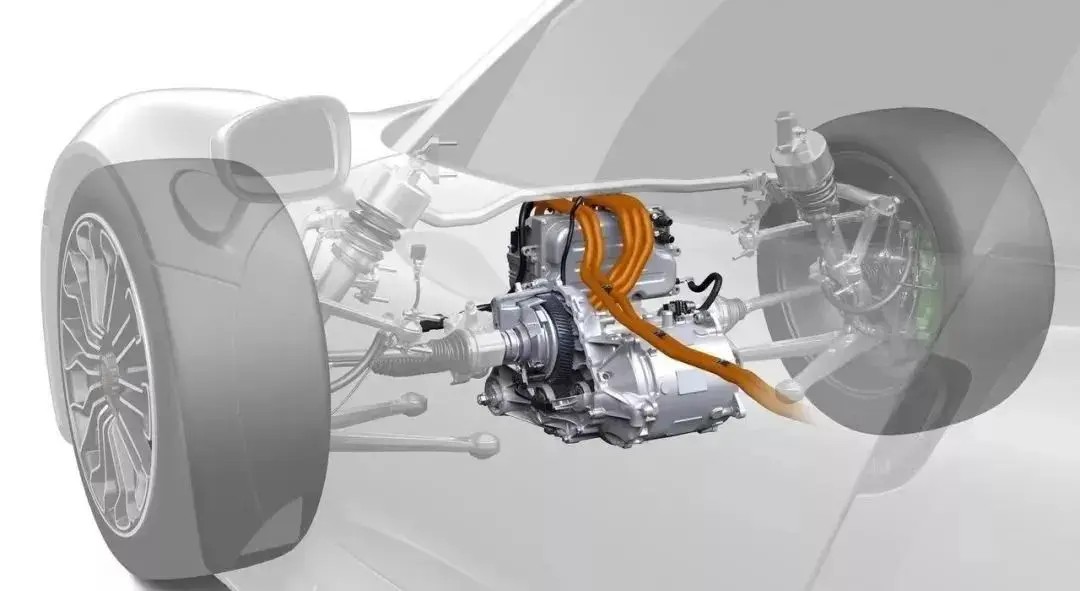
驱动系统集成化的优势在于体积小、布局灵活,重量轻,可增加续航里程,并降低主机厂的采购和配套成本。随着电动驱动产品向集成化发展的趋势,产品的价值显著提升。截至2022年9月,国内乘用车市场中,三合一及多合一驱动总成占比超过六成。NE时代的数据显示,2022年9月,新能源乘用车搭载的三合一及多合一电驱动系统达到37.97万套,同比增长81.7%。这些系统占总配套量的63.4%,比例较2020年全年的37%提高了26个百分点,并且显示出持续增长的趋势。
零部件国产浪潮不可阻挡
线控制动:One-box方案占比有望持续提升
在电动智能化的趋势下,电子液压制动系统(EHB)的优势显著,特别体现在高能量回收效率和短制动距离等方面。随着新能源汽车市场的快速扩展,EHB系统的应用率也在迅速增加。根据高工智能汽车的数据,2022年1至9月,国内EHB线控制动系统(包括Two-box和One-box)的搭载率达到23.45%,比2021年全年提升了14.85个百分点。
汽车座椅:行业规模大,自主供应商加速渗透
目前,全球和中国的汽车座椅市场主要由外资企业主导。2020年数据显示,安道拓、李尔与佛吉亚等外资品牌在全球汽车座椅市场占据了64%的份额,而在中国市场,延锋安道拓、中国李尔与佛吉亚三家公司占据了70%的份额。这显示出国内市场对于国产替代有着巨大的潜力。
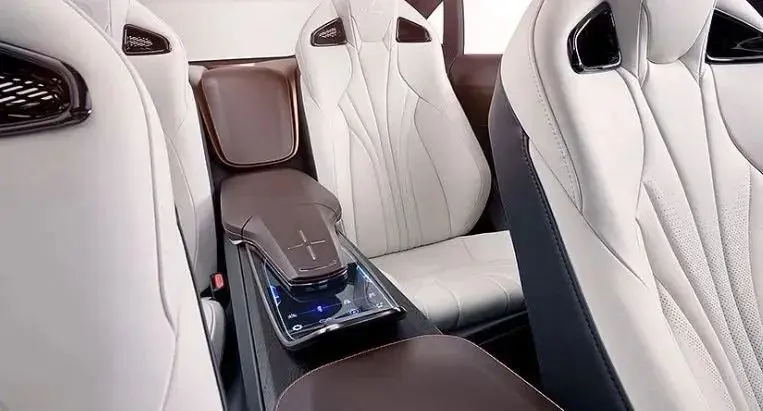
汽车座椅的核心零部件是座椅骨架,其成本占比为15%。座椅由座椅骨架、滑轨、调角器、升降器及面套等组成,据华经产业研究院的数据,座椅骨架、滑轨和调角器的成本占比分别为15%、4%、4%。作为汽车安全系统的重要组成部分,座椅的安全性要求极高,主要通过座椅骨架及相关零部件来实现,因此座椅骨架的技术门槛较高。考虑到新能源车辆续航里程的关注,座椅骨架正朝着轻量化方向发展,对技术和材料提出了更高的要求。由于前排座椅骨架在安全性和配置方面要求更高,因此其价值量也更加显著。在汽车座椅总成领域,继峰股份、天成自控等自主供应商在技术积累、成本及响应速度等方面均具备一定优势,有望以自主整车厂为客户开拓突破口提升市场份额,实现国产替代。上海沿浦的座椅骨架产品性价比优势突出,通过深度绑定东风李尔实现快速客户开拓,业绩增长可期。
内饰:自主汽车内饰供应商成本管控能力优秀,看好汽车内饰行业国产化替代全球传统燃油车内饰件市场目前由外资和合资企业主导,市场格局相对稳定。与汽车座椅和汽车玻璃等其他汽车零部件领域相比,全球汽车内饰市场的集中度较低。目前,延锋国际、安通林、佛吉亚等国际巨头仍然主导着全球汽车内饰市场,这三家公司在市场上的地位非常稳固。
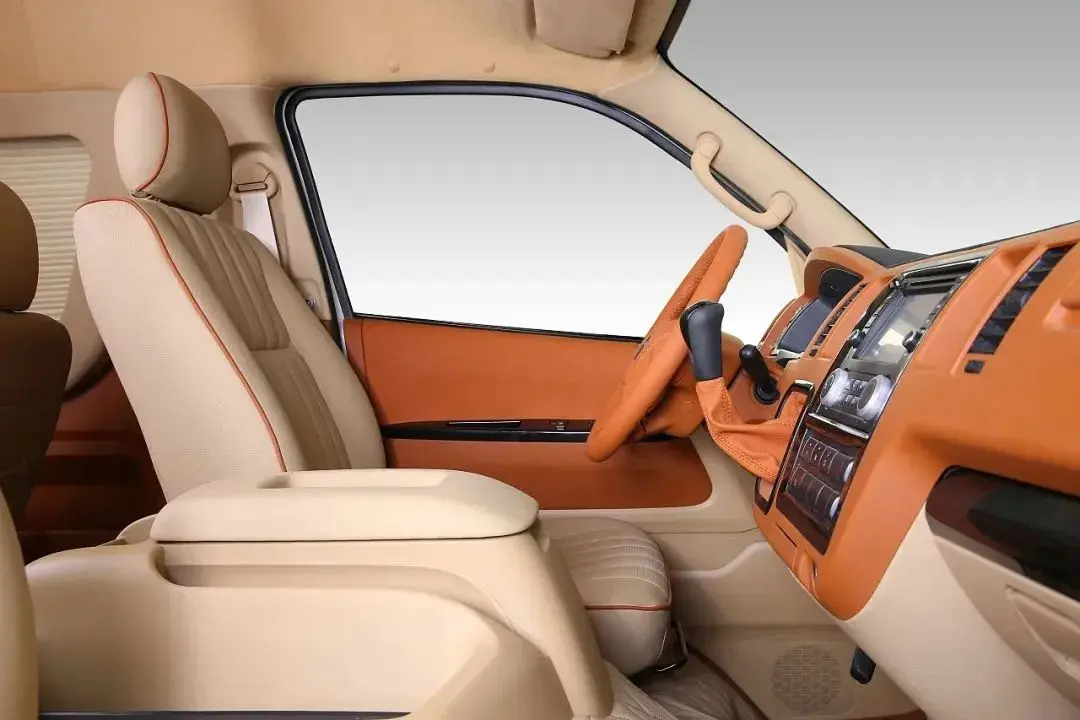
国内自主汽车内饰供应商在成本管控方面表现出色,看好国产化替代在汽车内饰行业的发展前景。作为传统市场中壁垒较低的领域,内饰件行业的核心竞争力主要集中在成本控制能力上。近年来,国内自主内饰件供应商凭借强大的成本管控能力和本地化优势,加速了客户群的扩展。尤其是在国产替代和新能源车型兴起的大背景下,这些趋势为传统内饰件供应商带来了新的发展机遇。
轻量化零部件渗透率提升
铝合金结构件:“政策”+“续航里程”推动渗透率快速提升
汽车轻量化是关乎节能减排和解决续航焦虑的重要技术方向,其中铝合金是最为优势的轻量化材料之一。据中国汽车工程协会发布的技术路线图,预计到2020年、2025年和2030年,单车铝合金使用量将分别达到190kg、250kg和350kg,显示出其在未来的重要性。同时,车用铝合金零部件的市场渗透率预计将持续上升。根据DriveAluminum的数据,2015年车用铝合金的市场渗透率仅为6.6%,到2025年预计将增至26.6%。
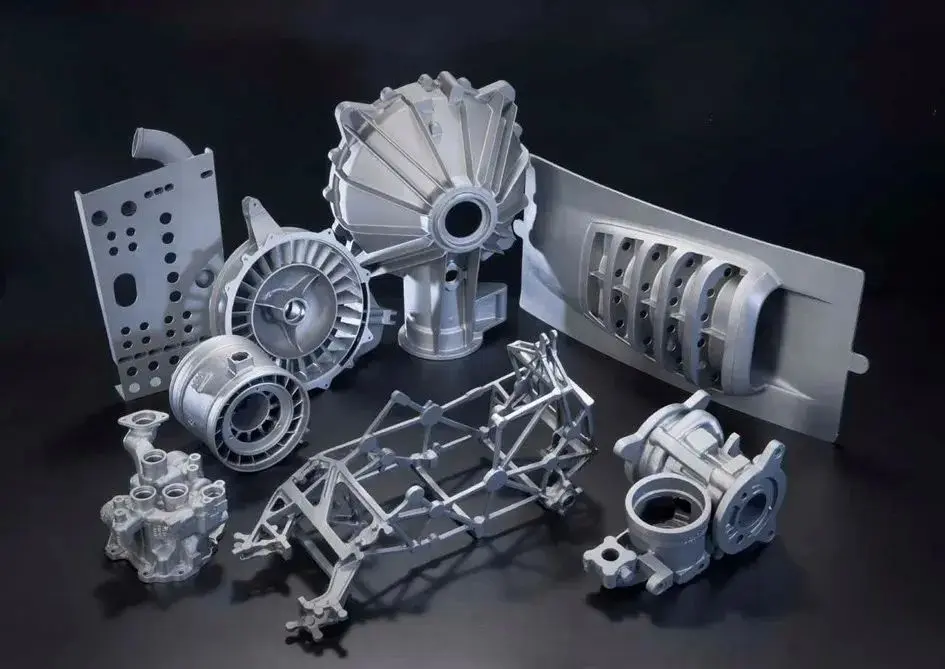
车用铝压铸行业市场竞争现状相对分散。据中国铸造协会数据显示,中国拥有超过3000家压铸企业,其中70%的产量用于汽车压铸件生产。在这些汽车压铸件中,铝合金占比超过80%,但规模较大的企业仅有数十家。铝压铸行业面临激烈的市场竞争,企业数量众多,竞争格局较为分散。
铝合金空气悬架:仍处于放量前的蓄力阶段
铝合金空气悬架系统已经成为高端新能源汽车平台的主流配置。随着新能源汽车市场的繁荣,空气悬架系统正处于黄金发展期。该系统在空气悬架结构基础上增加了高度传感器、加速传感器、控制线路和电子控制单元。
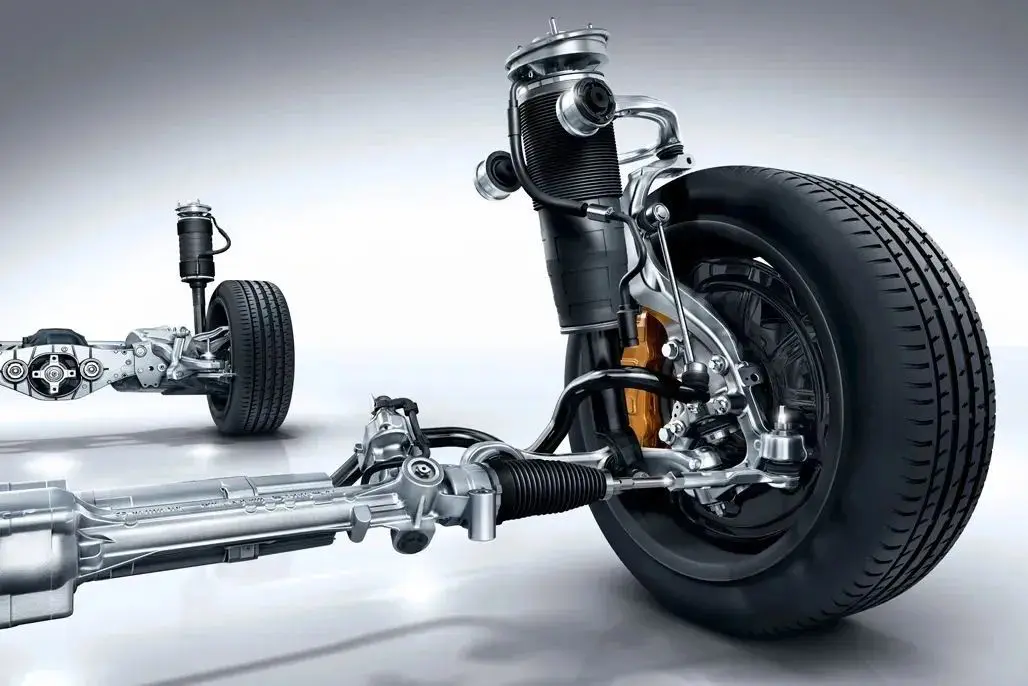
与传统的钢制汽车悬挂系统相比,铝合金空气悬挂系统能根据不同的路况和距离传感器的信号调整车身高度,通过控制空气压缩机和排气阀门,调节气室以提高或降低底盘与地面的间隙,从而增强行车稳定性并优化驾驶体验。铝合金空气悬架系统确保底盘与地面保持适当的间隙高度,有效保护电动车电池,已成为高端新能源车的主流配置之一。目前,铝合金空气悬挂市场正处于增长前夕,准备迎接未来的大规模需求。
来源:AEE汽车技术平台