总装工艺是整车四大工艺中最为复杂的工艺,它涉及动力总成,底盘、车身、内外饰和电子诸多系统,安装的工艺要求、技术规范在不同系统之间也有较大的差别。整车企业通常都非常注重建立完善的工艺开发流程,实施总装工艺同步工程(即SE 装配仿真分析),但对于总装工艺和成本之间的互相影响,没有进行透彻地分析,尚有很多改进的空间。
产品成本主要由零件成本( 来自于零部件供应商)、人工成本(体现在整车制造工厂操作者的操作工时)、物流运输成本以及工具、工装和设备的费用组成。本文结合实际工作,主要从零件的安装方式、零件的总成方式等几个方面,分析总装工艺与产品成本之间的关系,并通过一些具体的例子,给出成本优化的实践案例,供业界同仁参考。
总装工艺对零部件成本的影响
总装工艺对零部件成本有一定影响,通过分析研究可以适当优化,不仅可以降低零件成本,还可以改善总装工艺难度。以下介绍车顶天窗、后蒙皮线束及扭力梁后桥等几个零部件的总装工艺改善实例。
天窗的密封条可以由天窗供应商来料自带(图1),也可以在整车厂内安装(图2)。如果采用天窗密封条厂内安装的工艺(即图2 的方式),需要总装车间操作者进入车身安装,增加了操作者装配难度;但采用图2 的方式,天窗密封条可以直接安装在车身上,大大简化了天窗本身的零件结构,按图2 的方式开发零件,总成本(包含天窗零件成本和整车制造成本)比图1 的方式有明显降低。
后蒙皮线束可以集成在后蒙皮上(即由后蒙皮供应商安装),也可作为车身主线束的一个分支(图3)。采用图3 的工艺方案,将后蒙皮线束作为车身主线束分支,能减少一个车身主线束与蒙皮线束的中间过渡线束插接件,减少了线束零件成本。当然,采用图3 的工艺,也有不利之处。首先,它增加了操作难度。采用这种工艺设计,需要两名操作者一手插接3 个蒙皮线束,同时另外一只手还必须提着后蒙皮(若是蒙皮线束集成在后蒙皮上,就只需要插接这1 个线束插接件)。另外,采用图3 设计的车型,需要2 名操作工协同完成后蒙皮的安装,增加了整车厂厂内装配时间。但采用图3 的工艺设计,由于减少了中间过渡线束插头,总的成本还是有明显下降的。这个案例也给我们一个启示:某些零件的设计(如本案例中的后蒙皮中间过渡线束插接件),它们纯粹是为了满足某个工艺要求而设计的,这些零件本身不会给客户创造任何价值,因此,对于这一类零件,我们可以不断地优化生产工艺,降低这些零件的制造成本。
扭力梁后桥既可以使用工装定位安装,也可通过后桥自带定位支架(图4)来保证扭力后桥零件相对于车身的精确位置。采用工装定位后桥,可以大大简化后桥设计(采用工装定位的后桥零件时没有图4 的“后桥自带定位支架”),显著降低了后桥零件制造成本。采用工装定位后桥的工艺方案,虽然增加了工装的复杂程度(后桥定位工装需要更高的制造精度,并且后桥工装本身还需要滑动,工装制造难度大),但最终总的成本还是有显著下降的。这个案例给我们的启示是,随着工业技术水平的不断提升,我们可以采用更为先进的工具、设备来优化制造工艺,降低整车的制造成本。
总装工艺对整车物流成本的影响
整车的物流成本是整车成本的重要组成部分。总装车间所采用的装配工艺形式会影响到零件的存储、包装形式,进而影响到整车的物流成本。
比如,我们曾经设想优化底盘制动管组零件装配工艺,将整车后制动管分支集成在制动管组上(见图5,将制动管后部和制动管前部整合为一个零件),采用这种工艺可以减少2 个制动管接头(用于连接制动管后部和制动管前部),因而可以大幅降低制动管的零件制造成本;同时由于省去了2 个制动管中间接头,也不需要总装车间的操作者来装配制动管接头(不但可以节省装配时间,还可以节省装配工具费用),达到降低工厂制造成本的目的。但制动管接头被省去之后,整个的制动管零件变得非常庞大。与之前有制动管接头的制动管相比,图5 的制动管占用了非常大的物流包装面积,物流运输效率非常低下,显著增加了制动管零件的运输成本。通过综合计算零件成本、总装装配成本和物流运输成本,该方案最终未实施。
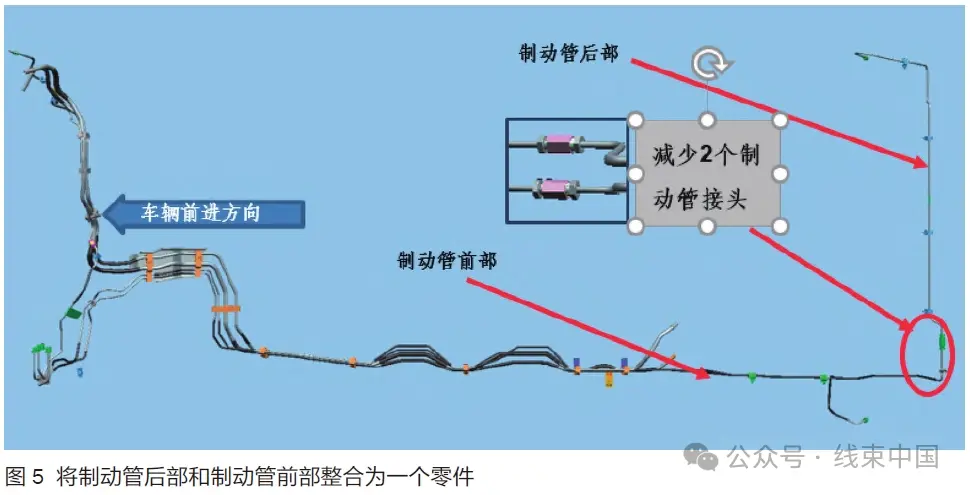
总装工艺对工具、工装、设备成本的影响
产品的总成本中也包含装配的工具、工装、设备的成本。由于这些工具、工装、设备需要满足一个车型生命周期几十万次的重复装配要求,同时还需要保证产品的高质量,这些工装、设备往往都造价不菲。为投产新车型,这些工具、工装及设备往往需要改造或者是再购买新的。如果在工艺规划设计中使用柔性的工装、设备,即采用同一套工装、设备,用于装配车间内投产的不同款式,不同配置的汽车,就可以大幅度降低工装、设备的制造或改造费用。以下以车门密封条柔性滚压工具和内饰电器零件装配的电测试设备举例说明。
车门密封条安装时,需要使用密封条滚压工具。以往,由于不同车型的设计差异,对于新车型,我们需要新购置密封条滚压工具。我们目前普遍采用车门密封条柔性滚压工具(图6 滚压工具可以按不同车型自适应滚压力的大小),可适用不同车型,减少项目工具费用。
总装车间在装配车辆过程中,也会使用一些检测设备,这些设备虽然有助于提高制造质量,但另一方面却也增加了制造成本,存在优化检测工艺、降低检测设备成本的机会。
笔者非常认同“产品质量是制造出来的,而不是检验出来的”的质量理念。我们之前的总装工艺,要求在内饰零件安装完毕之后(即仪表板总成、天窗、座椅、车顶内饰等安装完毕),进行整车电子零件的电测试,以确保电器零件安装的正确性。目前,我们已经通过改进电器零件的设计和装配,取消了内饰电器零件装配的电测试设备。
柔性化生产工艺对制造成本的影响
为降低制造成本,提升生产效率,我们首先要实现能使用同一套设备来装配多种车型。比如可以采用柔性化的仪表板安装机械手,装配总装线上的所有车型的仪表板。对于这类柔性化的生产设备,我们在设备选型时,就应考虑设备能力(如电动机的负载以及机械手的行程),需要满足多车型的要求。当然,这些对设备能力提出的柔性化要求可能会增加设备的初始费用,但是当我们将未来投产新车型时节省的设备改造费用或是新增一套设备的费用计算在内时,采用柔性化的设备还是能给企业创造不小的收益。
为降低柔性化生产设备的初始费用,另外一个可行的方法是,将设备的柔性制造能力在设备初始制造时进行预留,待未来新车型投产时,再逐步增加设备的柔性化制造能力。我们以制动液加注设备举例说明。
在制动液加注设备向整车制动系统加注制动液时,加注设备需要与车辆建立通信关系,命令整车上的制动控制器EBCM 打开控制器内的电子阀门,实现加注制动液的目的。由于不同制动器厂家的通信接口的差异,制动液加注设备需针对每一种EBCM配置一路通信接口。我们在制动液设备初始制造时,仅配置在产车型的制动控制器通信管路,同时预留1 路或2 路未来新车型制动控制器通信管路。当未来新投产车型的制动控制器和现有车型制动控制器不同,需要对制动液加注设备新增通信管路时,我们只要在加液设备通信管路预留的接口处,加装新的通信管路即可。
采用这种方式就可以实现,“一次设计,分步实施”,降低设备的初始费用。采用柔性化生产模式,另一个需要关注的点是,实施统一的总装主零件的装配顺序(图7)。
当采用柔性的生产模式时,不同车型是在同一条总装线上连续生产的。具体落实到总装生产线上的每一名操作者,其装配的上一辆车和下一辆车,可能是产品结构和性能完全不同的车型。假设上一辆车和下一辆车的同一种零件(譬如车前照灯),由于整车的工艺设计不同,导致它们的安装工艺不同,或者甚至是安装工位不同,这会对总装车间的操作者带来比较大的混乱,因为操作者需要在不同车型的不相同装配工艺之间切换,并且可能由于同一种零件不同车型的安装工位不同,导致总装流水线上的操作者装配工作量不足的情况。
如何解决这一问题呢?我们可以在柔性的总装装配线上,实施统一的总装主零件装配顺序, 并采用统一的装配方法。譬如,我们目前已经实现了由同一名操作者在同一个工位用同一把工具安装同样数量的紧固件,将不同车型的仪表板总成安装到不同车型上。通过这种柔性化的工艺模式,不但显著提升了生产效率,也大大降低了制造成本。
为实现这种柔性化生产模式,需要我们工艺开发工程师在项目前期,就预先设定好每个新车型零件的安装顺序(这一工艺顺序符合统一的总装主零件装配顺序),并将这一工艺顺序在新车型零件设计开发前就传递到新车型产品开发部门。同时,在新车型SE 装配仿真分析时,也始终将实施统一的总装主零件装配顺序放在工艺开发的首位。如果工艺开发工程师发现新产品的工艺顺序与预先设定的工艺顺序不一致,就需要和产品开发工程师研究,适当改进产品设计,以满足预先设定的“总装主零件装配顺序”。
结 束 语
通过以上几个案例,我们可以看出,总装工艺与整车的成本有着密切的关系。我们在工艺开发时,不但需要关注工艺的可制造性,也需要关注不同工艺对整车成本的影响。在新车型前期工艺开发过程中,如果我们能发挥创造性的思维,不断总结工艺案例,挖掘改进点,并结合新的制造装配技术,就可以将现有的工艺持续优化,制造出更具竞争力的产品。
来源:线束中国