4.1 静力分析结果
如图5所示,其最大主应力发生在三缸上缘,大小为169.8Mpa。应力较大的地方有两处,第一处在缸体上表面,第三缸周围,主要由于此时第三刚爆发,有19Mpa压力作用在三缸上缘部分;第二处在第三、第四轴承座连接部分周围的缸体部分,由于三缸爆发,第三第四轴承座提供的支撑力十分大导致。
如图6所示,此时原方案缸体最大位移为0.054mm。缸体变形区域与缸体所受应力较大区域类似。
如图7所示,此时原方案缸套最大Mises应力为236.3Mpa。应力较大q区域为三缸套上缘及第二第四缸套靠近第三缸缸套的部分。三缸爆发时,其他缸内压力及活塞侧推力都较小,所以缸套应力主要受第三缸爆发影响。
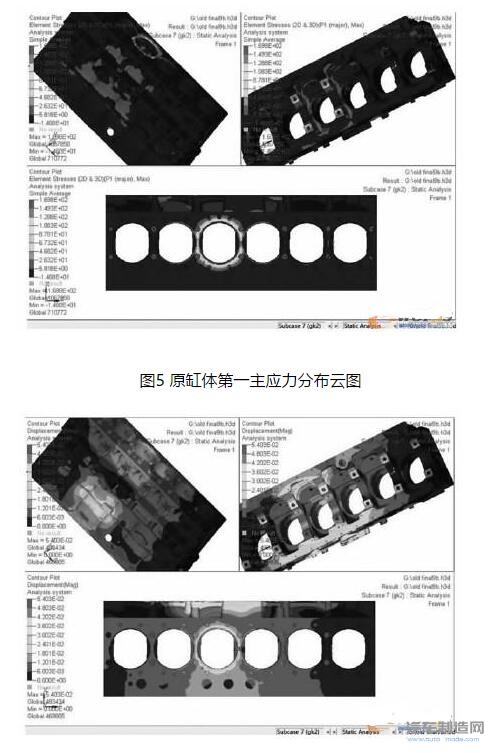
如图8所示,此时原方案缸套最大位移量为0.02777mm。位处第三缸上缘部分。整体位移分布十分具有规律性,以三缸套上缘为起点向下和向两侧逐步减小。
如图9所示,原方案轴承座最大Mises应力值为235.8Mpa,发生在螺栓预紧处。此处出现较大应力原因应该是施加螺栓预紧力时以集中力方式施加,出现应力集中所致。而除螺栓预紧处外,较大1、2、5、6、7号所受载荷较小的轴承座,应力从与缸体接触面其逐步向下和中间部分减小。而3、4号轴承座,应力值在载荷施加处较大向其他区域逐步减小。
如图10所示,此时原方案动机轴承座最大位移为0.09081mm。较大处为3、4号轴承座受载部分。
扩缸后发动机缸体静力分析模型的受载形式与原方案一致,仅是载荷大小略有变化,因此应力分布及位移情况类似,以下结果不再描述。
如图11所示,128mm缸径新方案的缸体最大平均第一主应力值为165Mpa。如图12所示,新方案缸体最大位移为0.07938mm。
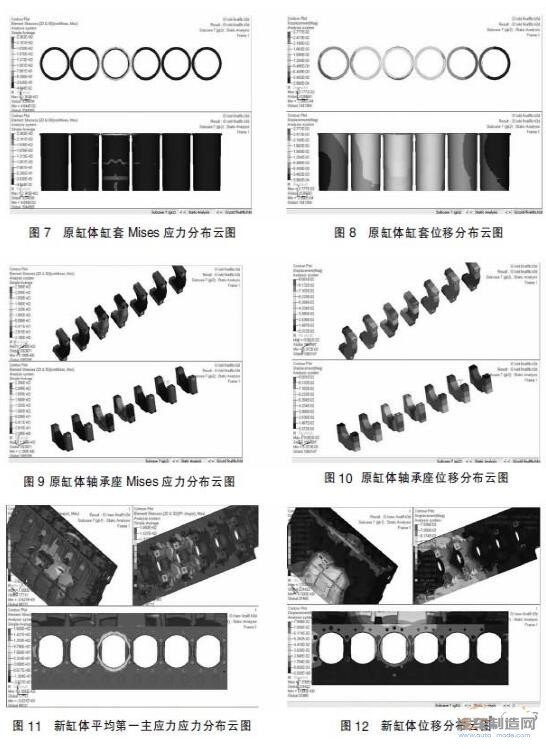
如图13所示,新方案缸套最大Mises应力值为215.9Mpa。如图14所示,新方案缸套最大位移为0.02477mm。
如图15所示,新方案轴承座最大Mises应力为222.4Mpa。如图16所示,新方案轴承座最大位移为0.125mm。
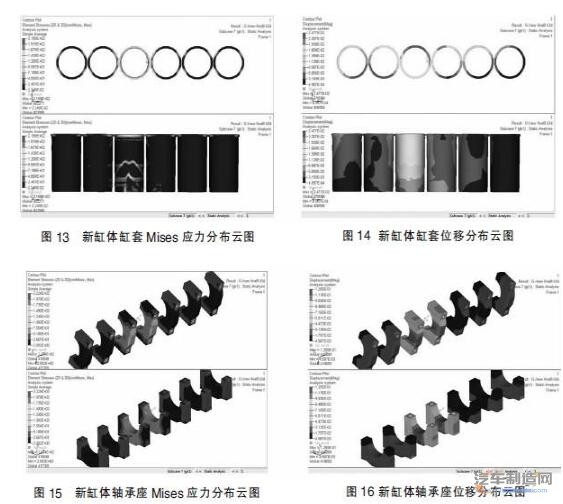
4.2 静力分析汇总与分析
上述对123mm缸径和128mm缸径两种发动机缸体进行了在第三缸爆发压力最大这一极限工况的静力分析求解。结果汇总如表5所示:
表5 静力分析结果汇总
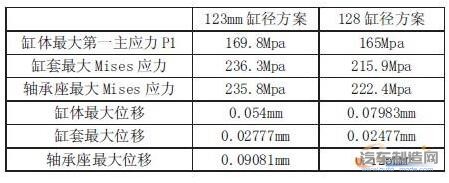
对于所关心的缸体最大第一主应力值,均为160Mpa以上。此值小于HT250的抗拉强度250Mpa,但引入安全系数的概念后,此值偏大。但考虑到新方案是在原缸体基础上改进得到的,且新方案最大主应力值变化不大,且略有减小。故说明新缸体静力分析强度符合要求。
从表中清晰可得,在同一发动机缸内压力变化曲线数据下,扩缸后发动机缸体、缸套最大应力值略微变小。缸体、轴承座最大位移略微变大。且最大应力均小于材料强度极限。但由于扩缸后,缸内压力曲线数据会发生变化,所以实际中略有差异。但是整体的分布形式应该变化不大,主要的危险区域,和较大位移区域不会发生改变。所得结果有一定参考价值。
在建立分析模型时,缸盖部分由4层2.5mm的三棱柱单元代替,其材料选用较大的弹性模量。通过多次尝试求解对比结果发现,此弹性模量大小会导致缸体最大第一主应力值。具体规律是缸盖部分单元弹性模量越大,缸体最大应力值越小。所以在缸体静力分析中,缸盖部分影响十分大。所以为得到更好结果,需要建立较为准确的缸盖模型。
5 缸体模态分析
5.1 缸体模态分析的有限元模型
缸体模态分析的有限元模型,与静力分析相比只选择缸体部分,去掉缸套、缸盖、等连接部分。
对于发动机缸体这种具有复杂几何的模型,在Hypermesh网格划分中,一般选用四面体单元。网格划分思路一般为先生成高质量2D网格单元,再向内填充生成3D网格单元模型。