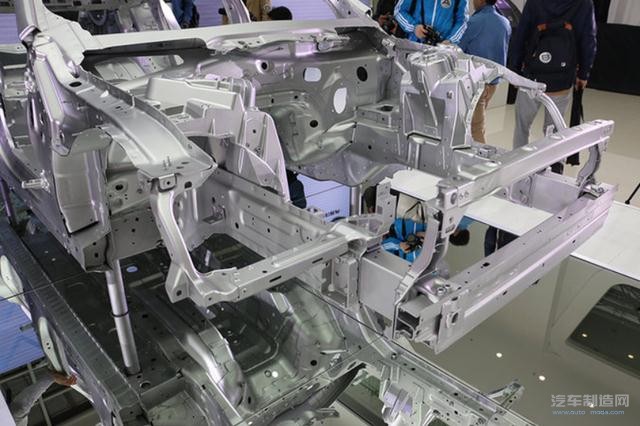
在全铝家族中,奥迪算是最早提倡全铝车身概念,像大家熟悉的奥迪A8,就是基于全铝结构打造的。不过,奥迪并没有坚持,新的奥迪A8明显变得更重了。奔驰的全铝车身设计与奥迪可谓是棋逢对手,不过随着国产新一代奔驰E级上市,细心消费者发现该车也变重了。实际上,大家猜测也没有错,奔驰E级的确将车门和引擎盖由铝材换成了钢材。特斯拉就不用说了,它是新人,目前也只是处于尝试全铝结构的阶段。
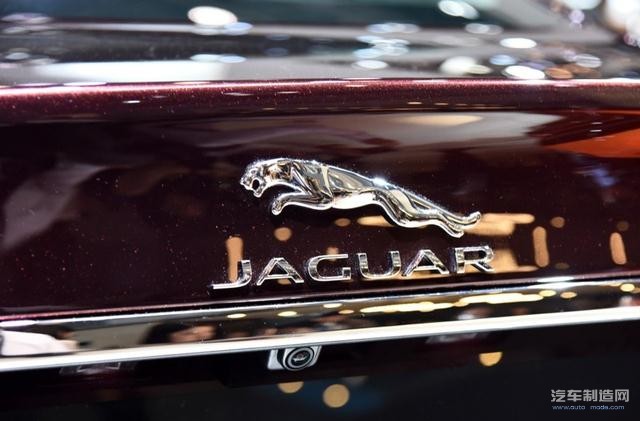
各大豪华品牌在钢与铝之间犹豫徘徊时,捷豹则舍近求远的坚持了全铝车身的传统,即便是国产的捷豹XFL价格门槛大幅降低,也没有放弃。是什么动力驱使捷豹这么做?看来很有必要进行一番追根溯源。
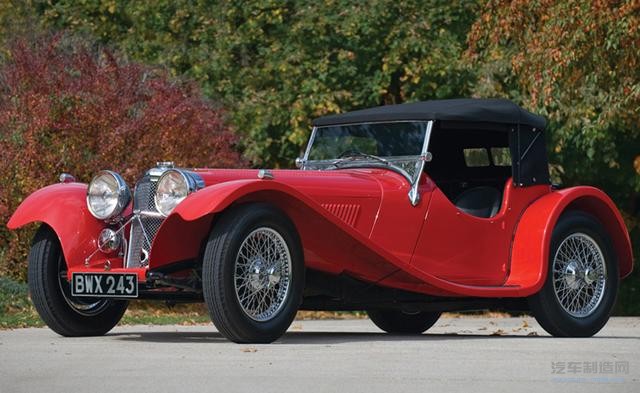
捷豹对铝材的青睐可以追溯到上世纪20年代。当人们还在汽车发展上探索的时候,捷豹就开始大胆采用铝材。到了1935年,捷豹在全世界率先推出了采用铝合金车身的SS100,其重量仅为1181kG,不但创造了世界记录,更开启了全铝车身的时代。
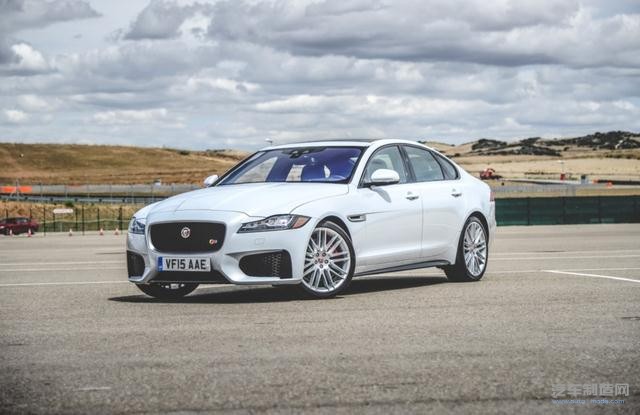
接下来的岁月里,尽管汽车技术日新月异,但没有哪个品牌像捷豹一直坚持在全铝车身上下功夫,捷豹E-Type、捷豹XJR-5、捷豹XJ220,都在人类汽车制造领域留下里程碑。进入21世纪之后,全球汽车市场逐步饱和,在大多数车企将成本控制摆在首位之时,捷豹又陆续推出采用全铝车身的捷豹XK、XF、XE以及XJ等车型。从这我们可以看得出来,捷豹很执着,尽管面临铝材上涨带来的成本威胁,但一直不忘初心。
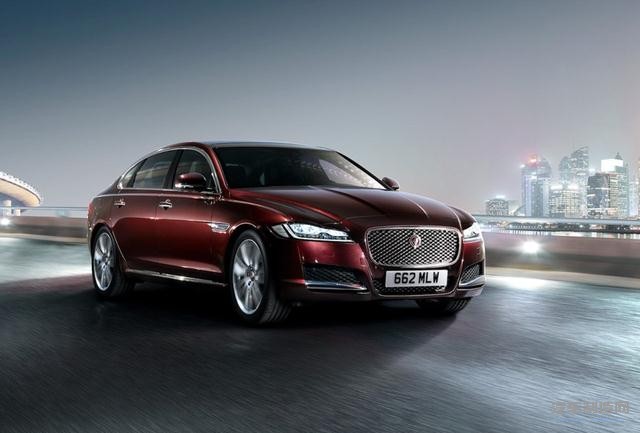
2016年,全新一代XFL发布,这是基于捷豹路虎最新模块化智能全铝车身结构研发的一款重磅级新车。捷豹XFL采用全铝车身结构之后的减重效果十分明显,1590KG的整备质量基本和更低一级的B级车相当。而竞争对手宝马5系(参配、图片、询价) 、奔驰E级以及奥迪A6L,车重都在1750-1760kG左右。毫无疑问,捷豹XFL要比这些车型轻了至少160KG。
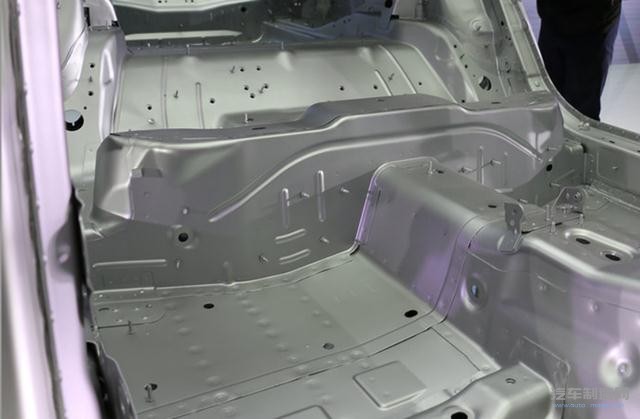
也许有人对160KG没有直接概念,这相当于国内两个成年男子的重量,还是比较壮硕的体格,绝不是弱不禁风的那种。大家可以比较一下,一个人开车与多搭载两人,车辆加速与灵活性会有比较明显的区别。
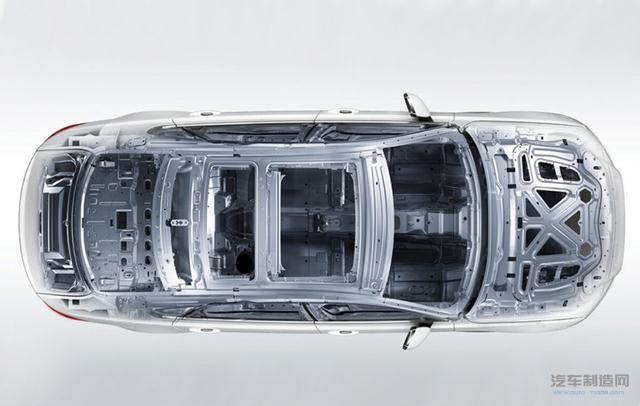
尽管全铝车身对车辆减重起到了关键作用,但这并不是捷豹坚持全铝车身的唯一理由。大家都知道,更为合理的分配车身前后重量一直是困扰各大车企的一个难题,这关乎到操纵上的灵活以及车辆运动表现。通过前置后驱的方式,车辆的前后重量比例可以做到接近50:50的比重分配,但要想进一步平衡,车身结构重量成为关键。相比更重的钢材,铝材无疑更容易实现50:50的前后比重设计,从而让整车具有更强操纵性和性能优势。
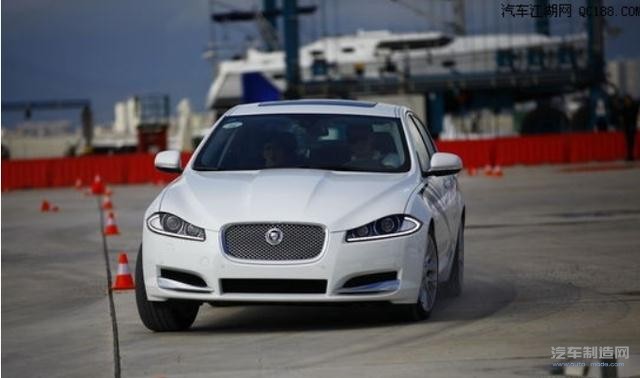
这么多年来,无论捷豹怎样变化,都一直将驾驶乐趣和运动基因摆在重要的位置。就拿捷豹XFL举例,后排空间虽然比竞争对手更为宽敞,但在全铝车身结构以及出色的前后车身比重的帮助下,驾驶该车的感受依然是非常运动的,足够让你在市内驾驶游刃有余,并不会受到庞大车身与轴距的影响。
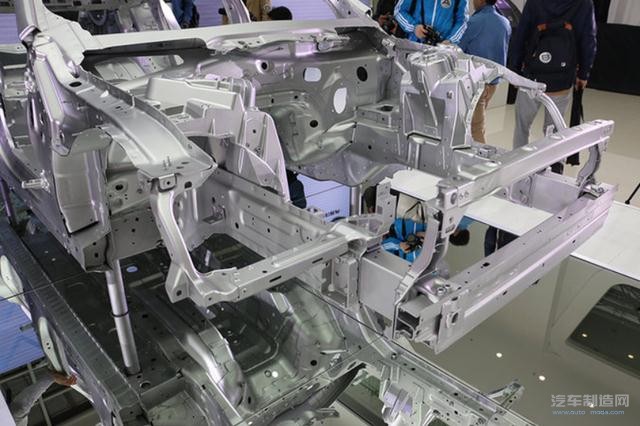
既然全铝车身有着明显的减重与提升操控的表现,那么为何采用全铝车身的车型又很少见?这个问题其实也不难回答,大家都知道铝材价格要比钢材高许多,因而采用全铝车身就意味着制造成本的大幅度攀升。
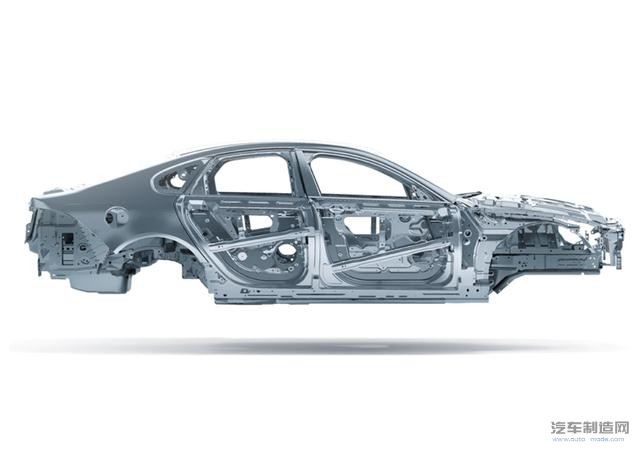
另外,全铝车身并不是简单的用铝材替代钢材,还涉及到车身强度和结构方面的技术难题。如果在全铝车身设计上缺乏足够的经验,即便是像劳斯莱斯也不得不采取更为谨慎的态度。
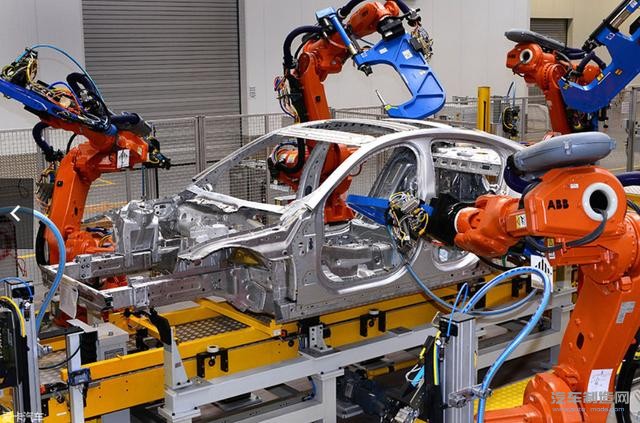
最关键的一点是,全铝车身不但要采用高强度的铝合金用于结构件和板件来提升车辆的安全性能,还得从传统的点焊工艺中走出来,寻找出一条最适合的工艺办法。如果是单纯的铆接,车身强度和密封性肯定不如点焊,这也是全铝车身制造的一个难点。
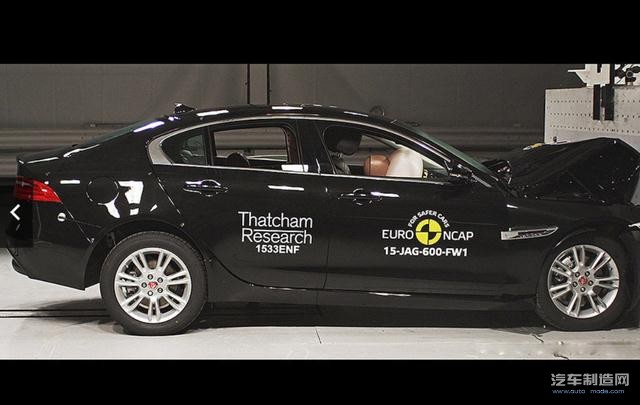
捷豹在安全碰撞测试方面一直领先,除了长时间采用全铝车身设计具备丰富的经验,更在严格的欧洲碰撞测试中屡次获得好成绩。
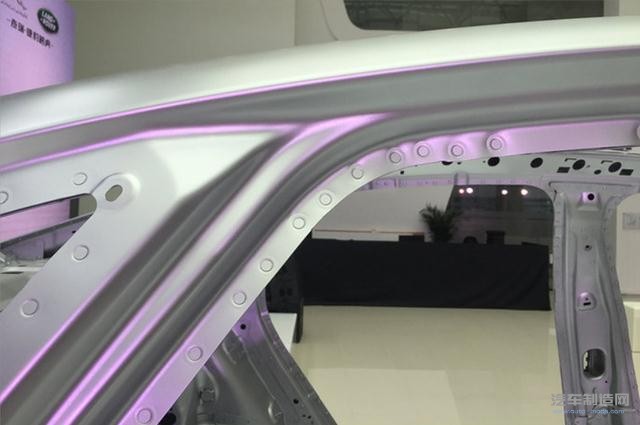
捷豹运用的是来自于航空领域的铆接方式来代替点焊,并且以胶合工艺来提高各部件的连接强度,同时胶合工艺还有助于提升车体的密封性。像战斗机、民航飞机都大量采用了自冲铆接和胶合粘接技术,因而运用到汽车上完全可以令人放心。
结语:随着国内首家全铝车身车间投产,捷豹将最领先、智能、环保的高端铝材技术引入了中国,不但为消费者提供了全铝车身的高端享受,更在节能、减排以及驾驶性能发挥了十分积极的示范作用。虽然全球采用全铝车身的车企并不仅仅是捷豹一家,但能从开始一直坚持到现在,这份敢执着的精神无疑更为让人感佩。