超细长钛合金梁的数控加工工艺
2018-01-05 14:03:34· 来源:工具技术
图1为超细长钛合金梁类零件。其毛料为模锻件,材料牌号TA15M,毛料外廓尺寸3500mm×210mm×180mm,毛料重量220.5kg。零件外廓尺寸3450mm×160mm×151mm,最宽处为151mm,最窄处仅为34mm。零件外形为复杂双曲面,双面槽腔,缘条与腹板厚度最小处仅为2mm。尺寸精度及表面质量要求较高。
图1为超细长钛合金梁类零件。其毛料为模锻件,材料牌号TA15M,毛料外廓尺寸3500mm×210mm×180mm,毛料重量220.5kg。零件外廓尺寸3450mm×160mm×151mm,最宽处为151mm,最窄处仅为34mm。零件外形为复杂双曲面,双面槽腔,缘条与腹板厚度最小处仅为2mm。尺寸精度及表面质量要求较高。
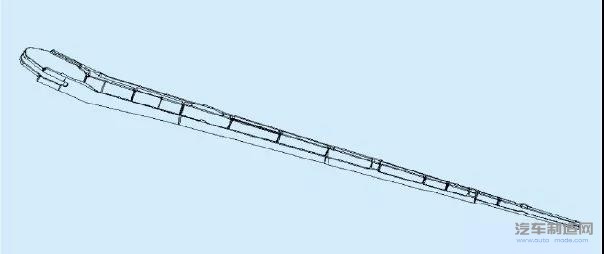
图1 零件模型
1 确定工艺方案
零件毛料为TA15M自由锻件,锻件残余应力导致了机加过程中零件的变形。零件超长且窄,长宽比范围22.8-101.5。零件结构面多为变角度曲面,所有缘条都为斜面,装夹定位不可靠。缘条和腹板厚度薄,最小处2mm,公差±0.2mm。缘条较高,角度大,最高处96mm。零件的装配关系复杂,在该梁每一个位置都有零件与之装配。表面质量要求高,所有转角及底角粗糙度1.6μm。该零件结构属于工艺性极差的结构类型。在加工中要解决的问题包括:机加过程中变形的控制、装夹定位方式的选择和缩短加工周期。
(1)零件定位方式
超细长钛合金梁在加工过程中,定位方式的选择至关重要。该梁长又细,且为两面槽结构,因此采用缘条定位。由于该零件采用斜缘条直接定位会大幅降低定位面的精度,对零件加工质量影响很大,所以在缘条上设置工艺凸台来进行定位,既可以保证定位基准精度,又可以避免在加工过程中频繁的倒压板工作。工艺凸台的距离应适当,如果太近会增加加工过程中的跳刀频率,加大工艺凸台的去除难度;工艺凸台太远会使定位不稳定,增加零件在机加过程中的变形几率,降低定位准确度。根据该梁的结构特点,采用阶梯工艺凸台,再在梁身上钻两工艺孔联合定位,孔径分别为25H9、12H9,定位稳定可靠。工艺凸台外形如图2所示。
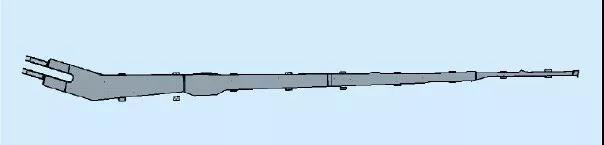
图2 工艺凸台外形
(2)机床设备及工装的选择
超细长钛合金梁长约3.5m,零件头部抬起,并且工装庞大,零件加上工装的高度已超过500mm,所以所用机床的Z向行程必须为700mm左右。通过对现场机床进行考察,选用机床工作台尺寸3500mm×1250mm,摆角范围A±30°、B±30°,机床精度较高,能满足零件加工要求。
超细长钛合金梁加工采用缘条高工艺凸台及梁身基准孔定位方式。头部采用辅助可调支撑,用于头部变形量的校正以及加工中变形量的去除;压板选用Z字形压板,可以有效降低刀具长度,避免机床与工装的干涉,并且提高加工效率,保证零件加工后的表面粗糙度;工装增加校验块的使用,用于加工中程序的验证,以及避免工人由于用错刀具造成的零件超差及废品,提高了产品加工的一次就成功概率。正反面加工各需一套工装。
超细长钛合金梁缘条两侧的导孔接近300个,如采用传统方法,常规加工难度非常大,费时费力,产品质量也不易保证。使用数控机床钻导孔,既省时省力,又能保证产品质量。采用数控钻导孔需工装要求较高。缘条两侧各一套。
(3)确定加工流程
加工流程的合理安排是零件生产研制的重要环节,加工流程的合理与否是导致零件加工变形的重要原因。加工流程的顺序直接决定零件的去量方式、去量大小和去量先后顺序,这些都会影响零件材料的应力释放,以及零件的变形大小、变形方式。合理的加工流程可以大幅降低零件的变形几率。加工流程不仅要考虑零件的变形因素,还要保证零件尺寸精度。
根据超细长钛合金梁的零件特点,制定零件的加工流程:模锻件来料—铣基准面—镗基准孔—粗铣航后面(留7mm余量)—粗铣航前面(留7mm余量)—粗铣航前面(留3mm余量)—粗铣航后面(留3mm余量)—粗铣槽一侧(留3mm余量)—粗铣槽另一侧(留3mm余量)—测量外形及槽口—半精铣外形(留1mm余量)—半精铣航前面(留1mm余量)—半精铣航后面(留1mm余量)—测量外形及交点孔—精铣槽口—精铣外形—测量外形及槽口—精铣航前内形—精铣航后内形—测量孔位等—数控钻缘条导孔—铣工艺凸台—钳工钻筋条导孔—半检—清洗—荧光检验—吹砂—标识—成检—交付。通过多次不断的翻面加工以及去量的逐渐递减,有效消除零件变形,保证产品质量。
(4)刀具的选择及参数的确定
数控加工机床采用冷却液冷却,结合零件的钛合金材料,应以浅切刀具和整体合金直柄立铣刀为主,国产镶齿合金刀具为辅。由于钛合金属于难加工材料,对刀具的质量和性能要求都很高。
依据现有参数库及零件的实际加工情况来确定刀具加工参数。在切削中主要的切削参数有:主轴转速n、切削深度ap、切削宽度ae、每齿进给量fz、刀具齿数Z和进给速度vf,其中vf=nZfz。
钛合金加工刀具的齿数一般是多齿刀具,在加工该零件选用的刀具绝大多数都是4齿刀具。影响刀具加工效率的主要参数是主轴转数(n)和刀具每齿进给量(fz)。表1为参与加工的主要刀具的规格及加工参数。
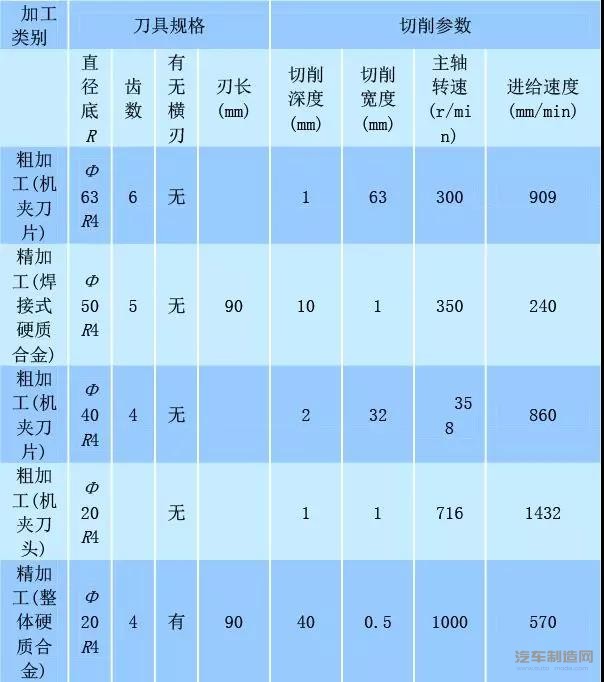
表1 加工刀具选择及切削参数数值
2 数控程序的编制
根据零件的变形控制、来料状态、零件结构特点、机床特性、刀具特点等,编制数控加工程序。在编制程序时需有效避免一些常见的问题:①避免刀具路径冗余,减少不必要的跳刀;②尽量采取顺铣的走刀方式,保证零件尺寸精度;③针对不同的余量,采取径向以及轴向的分层加工,保证刀具切削余量均匀,降低机床及刀具的损耗;④避免刀具垂直与零件接触;⑤在转角要降低加工速度,普通转角降速值是正常切削的60%,特殊转角(例如工艺凸台内侧筋条转角)降速要达到20%。保证无人工干预的正常切削;⑥精加工前清转角,保证精铣的铣切量均匀;⑦正确计算R退缩值。
程序的走刀方式也可以影响零件的变形,比如浅切、顺铣等都可以大幅降低零件的变形量。浅切加工不仅可以大幅提高金属去除率,更重要的是可以降低切削力、减少加工应力,有利于减小零件加工中的变形,同时还可以降低机床负荷、保护数控机床。浅切使用的专用的加工刀具,该类型刀具加工效率较高,以D20R4刀具为例,进给速度可达1432mm/min,相比普通的刀具粗铣进给速度60mm/min,效率可以高出几倍甚至十几倍。浅切加工特别适合超细长钛合金梁的粗加工。
选用“roughing”命令编制浅切程序,在半精加工和精加工过程中采用径向分层的方式,每层进量0.5,在保证零件精度的前提下,可以大幅降低切削应力,减小零件的变形量。
小结
制定一套合理的工艺方案适用于超细长钛合金梁类零件,通过应力释放、优化切削方式与合理刀具参数等方法有效控制了零件变形,采用工艺凸台定位的方式也起到了很好的定位效果。该方案已通过加工验证,在实际加工中取得了非常好的效果,最终生产出了合格的零件,加工过程稳定,产品质量合格。
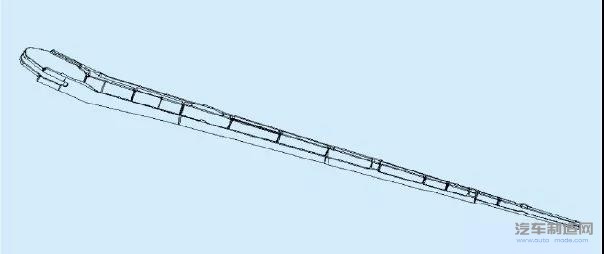
图1 零件模型
1 确定工艺方案
零件毛料为TA15M自由锻件,锻件残余应力导致了机加过程中零件的变形。零件超长且窄,长宽比范围22.8-101.5。零件结构面多为变角度曲面,所有缘条都为斜面,装夹定位不可靠。缘条和腹板厚度薄,最小处2mm,公差±0.2mm。缘条较高,角度大,最高处96mm。零件的装配关系复杂,在该梁每一个位置都有零件与之装配。表面质量要求高,所有转角及底角粗糙度1.6μm。该零件结构属于工艺性极差的结构类型。在加工中要解决的问题包括:机加过程中变形的控制、装夹定位方式的选择和缩短加工周期。
(1)零件定位方式
超细长钛合金梁在加工过程中,定位方式的选择至关重要。该梁长又细,且为两面槽结构,因此采用缘条定位。由于该零件采用斜缘条直接定位会大幅降低定位面的精度,对零件加工质量影响很大,所以在缘条上设置工艺凸台来进行定位,既可以保证定位基准精度,又可以避免在加工过程中频繁的倒压板工作。工艺凸台的距离应适当,如果太近会增加加工过程中的跳刀频率,加大工艺凸台的去除难度;工艺凸台太远会使定位不稳定,增加零件在机加过程中的变形几率,降低定位准确度。根据该梁的结构特点,采用阶梯工艺凸台,再在梁身上钻两工艺孔联合定位,孔径分别为25H9、12H9,定位稳定可靠。工艺凸台外形如图2所示。
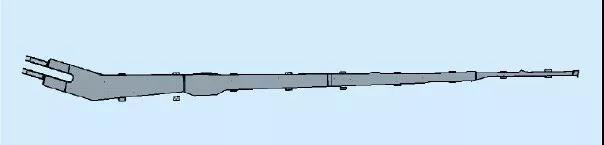
图2 工艺凸台外形
(2)机床设备及工装的选择
超细长钛合金梁长约3.5m,零件头部抬起,并且工装庞大,零件加上工装的高度已超过500mm,所以所用机床的Z向行程必须为700mm左右。通过对现场机床进行考察,选用机床工作台尺寸3500mm×1250mm,摆角范围A±30°、B±30°,机床精度较高,能满足零件加工要求。
超细长钛合金梁加工采用缘条高工艺凸台及梁身基准孔定位方式。头部采用辅助可调支撑,用于头部变形量的校正以及加工中变形量的去除;压板选用Z字形压板,可以有效降低刀具长度,避免机床与工装的干涉,并且提高加工效率,保证零件加工后的表面粗糙度;工装增加校验块的使用,用于加工中程序的验证,以及避免工人由于用错刀具造成的零件超差及废品,提高了产品加工的一次就成功概率。正反面加工各需一套工装。
超细长钛合金梁缘条两侧的导孔接近300个,如采用传统方法,常规加工难度非常大,费时费力,产品质量也不易保证。使用数控机床钻导孔,既省时省力,又能保证产品质量。采用数控钻导孔需工装要求较高。缘条两侧各一套。
(3)确定加工流程
加工流程的合理安排是零件生产研制的重要环节,加工流程的合理与否是导致零件加工变形的重要原因。加工流程的顺序直接决定零件的去量方式、去量大小和去量先后顺序,这些都会影响零件材料的应力释放,以及零件的变形大小、变形方式。合理的加工流程可以大幅降低零件的变形几率。加工流程不仅要考虑零件的变形因素,还要保证零件尺寸精度。
根据超细长钛合金梁的零件特点,制定零件的加工流程:模锻件来料—铣基准面—镗基准孔—粗铣航后面(留7mm余量)—粗铣航前面(留7mm余量)—粗铣航前面(留3mm余量)—粗铣航后面(留3mm余量)—粗铣槽一侧(留3mm余量)—粗铣槽另一侧(留3mm余量)—测量外形及槽口—半精铣外形(留1mm余量)—半精铣航前面(留1mm余量)—半精铣航后面(留1mm余量)—测量外形及交点孔—精铣槽口—精铣外形—测量外形及槽口—精铣航前内形—精铣航后内形—测量孔位等—数控钻缘条导孔—铣工艺凸台—钳工钻筋条导孔—半检—清洗—荧光检验—吹砂—标识—成检—交付。通过多次不断的翻面加工以及去量的逐渐递减,有效消除零件变形,保证产品质量。
(4)刀具的选择及参数的确定
数控加工机床采用冷却液冷却,结合零件的钛合金材料,应以浅切刀具和整体合金直柄立铣刀为主,国产镶齿合金刀具为辅。由于钛合金属于难加工材料,对刀具的质量和性能要求都很高。
依据现有参数库及零件的实际加工情况来确定刀具加工参数。在切削中主要的切削参数有:主轴转速n、切削深度ap、切削宽度ae、每齿进给量fz、刀具齿数Z和进给速度vf,其中vf=nZfz。
钛合金加工刀具的齿数一般是多齿刀具,在加工该零件选用的刀具绝大多数都是4齿刀具。影响刀具加工效率的主要参数是主轴转数(n)和刀具每齿进给量(fz)。表1为参与加工的主要刀具的规格及加工参数。
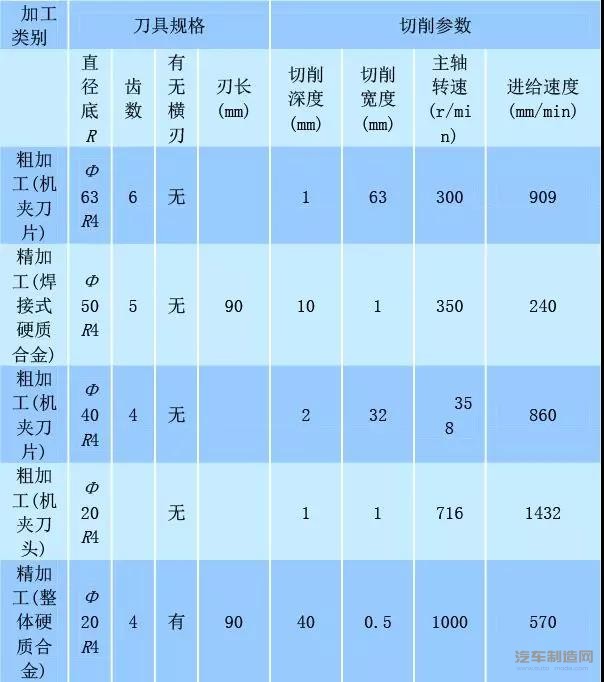
表1 加工刀具选择及切削参数数值
2 数控程序的编制
根据零件的变形控制、来料状态、零件结构特点、机床特性、刀具特点等,编制数控加工程序。在编制程序时需有效避免一些常见的问题:①避免刀具路径冗余,减少不必要的跳刀;②尽量采取顺铣的走刀方式,保证零件尺寸精度;③针对不同的余量,采取径向以及轴向的分层加工,保证刀具切削余量均匀,降低机床及刀具的损耗;④避免刀具垂直与零件接触;⑤在转角要降低加工速度,普通转角降速值是正常切削的60%,特殊转角(例如工艺凸台内侧筋条转角)降速要达到20%。保证无人工干预的正常切削;⑥精加工前清转角,保证精铣的铣切量均匀;⑦正确计算R退缩值。
程序的走刀方式也可以影响零件的变形,比如浅切、顺铣等都可以大幅降低零件的变形量。浅切加工不仅可以大幅提高金属去除率,更重要的是可以降低切削力、减少加工应力,有利于减小零件加工中的变形,同时还可以降低机床负荷、保护数控机床。浅切使用的专用的加工刀具,该类型刀具加工效率较高,以D20R4刀具为例,进给速度可达1432mm/min,相比普通的刀具粗铣进给速度60mm/min,效率可以高出几倍甚至十几倍。浅切加工特别适合超细长钛合金梁的粗加工。
选用“roughing”命令编制浅切程序,在半精加工和精加工过程中采用径向分层的方式,每层进量0.5,在保证零件精度的前提下,可以大幅降低切削应力,减小零件的变形量。
小结
制定一套合理的工艺方案适用于超细长钛合金梁类零件,通过应力释放、优化切削方式与合理刀具参数等方法有效控制了零件变形,采用工艺凸台定位的方式也起到了很好的定位效果。该方案已通过加工验证,在实际加工中取得了非常好的效果,最终生产出了合格的零件,加工过程稳定,产品质量合格。
编辑推荐
最新资讯
-
全球产业链聚沪 共探双碳新路径 SNEC
2025-04-18 18:05
-
柯马签订具有约束力的协议收购 Autom
2025-04-17 13:01
-
高效协同新范式:比亚迪叉车领创智能
2025-04-17 10:04
-
埃马克德国总部迎来中国社科院工业经
2025-04-15 09:40
-
埃马克这项全新应用即将在CIMT惊艳首
2025-04-15 09:37