轻量化白车身及多材料连接技术的发展
2018-01-11 13:06:28· 来源:AI制造
汽车轻量化是节能减排的一个有效途径,而汽车轻量化最有效的手段就是轻质合金材料的应用,目前国外已开发出多种多材料应用的轻量化白车身,但其连接问题成为瓶颈,目前通用的点焊连接技术已无法满足要求,各种新晋的连接技术层出不穷。
汽车轻量化
汽车轻量化是节能减排的一个有效途径,而汽车轻量化最有效的手段就是轻质合金材料的应用,目前国外已开发出多种多材料应用的轻量化白车身,但其连接问题成为瓶颈,目前通用的点焊连接技术已无法满足要求,各种新晋的连接技术层出不穷。
随着国外轻量化白车身的发展,白车身的用材由钢板应用阶段逐步发展到多材料混合应用阶段。本文以奥迪品牌的白车身发展进程为例,归纳了其白车身用材演化的四个阶段,分析了典型欧系、美系和日系车型白车身用材发展现状及用材趋势。
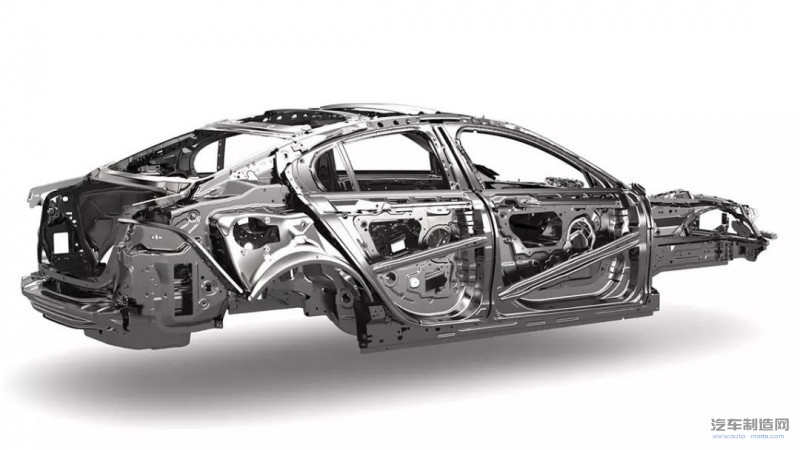
伴随着轻量化白车身的发展,其相应的多材料连接技术也随之发展迅速。针对四个白车身发展阶段,列举了目前9种常用的多材料连接技术,也对应规划为4个不同阶段,分析了每个阶段进程的多材料连接技术的适用范围与优劣势。
国外轻量化车身发展过程
纵观国外白车身的发展趋势,奥迪公司的白车身发展趋势极具代表性,到目前为止,其白车身的发展过程可分为四个阶段:
第一阶段:铝合金覆盖件开发阶段
这个阶段主要是为了增加材料强度级别,热成形钢逐步用于车身,还有少量铝合金覆盖件的应用。典型的车型代表为奥迪A3车型(见图1)。
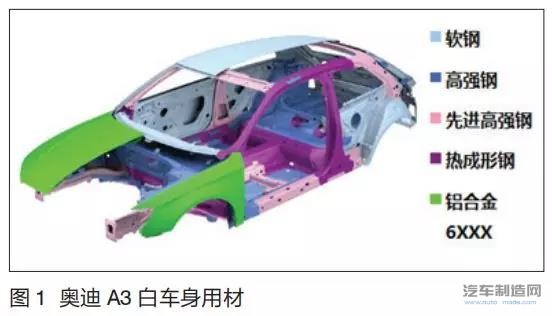
零部件用材方面,机盖、翼子板使用铝合金材质(3.2%),后座椅横梁、中通道、A柱、B柱、机舱纵梁后段、前围下板、后地板横梁和后地板纵梁等位置采用热成形钢(21.7%)。
第二阶段:铝合金外覆盖件成熟应用阶段
这一阶段,外覆盖件大量采用铝合金,铝合金覆盖件比重显著增加,热成形钢比重相对减少,典型的车型代表是奥迪A6车型(见图2)。
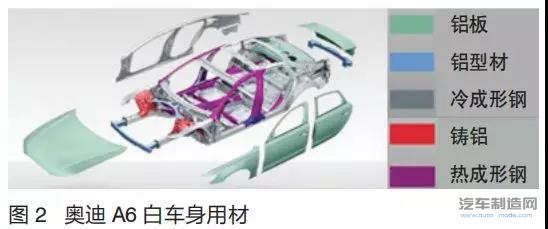
零部件用材方面,机盖、前后车门、翼子板、行李箱盖板、顶盖和前后防撞梁(铝型材)应用铝合金。铝合金用量较第一阶段增加至18%,中通道、座椅横梁、A柱和B柱等位置保留热成形钢,热成形钢的用量比例减少至11.3%。
第三阶段:全铝车身开发应用阶段
这个阶段,车身外覆盖件全部应用铝合金(铝板材)、铝型材和铸铝开始应用到车身结构件,轻量化效果显著,与此同时,高强钢和软钢板的用量急剧减少,典型的车型代表是奥迪TT车型(见图3)。
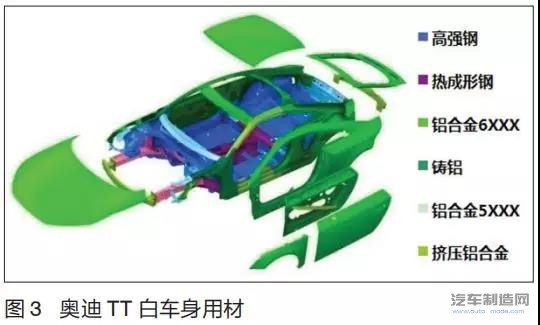
零部件用材方面,增加了A柱、C柱、侧围和顶盖横梁等位置的铝合金,铝合金用量由18%增加到35.8%,中通道、座椅横梁采用热成形钢,软钢应用量由35.2%下降到5.3%。
第四阶段:多材料混合应用阶段
这一阶段以铝合金为主要车身材料,铝型材和铸铝件大量应用到车身结构件。高强钢、软钢和碳纤维为辅助用材,典型的车型代表是奥迪Q7车型(见图4)。

零部件用材方面,地板、前纵梁等位置应用铝合金,铝合金用量较上一阶段由35.8%增加到49.9%,中通道采用的是铝板和热成形钢的混合结构,热成形钢的用量减少至9.2%。
车身用材比较及发展趋势
以上四款车型的白车身用材比例如表1所示。
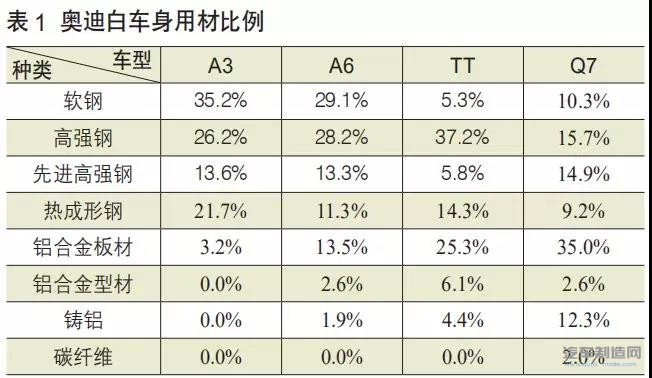
分析奥迪用材趋势如下:
铝合金用量上升趋势明显(3.2%→18.0%→35.8%→49.9%);
热成形钢整体用量呈下降趋势(21.7%→11.3%→14.3%→9.2%);
软钢用量下降趋势明显(35.2%→29.1%→5.3%→10.3%)。
除欧系的奥迪车型外,美系福特和日系车的用材比例如表2、表3所示。
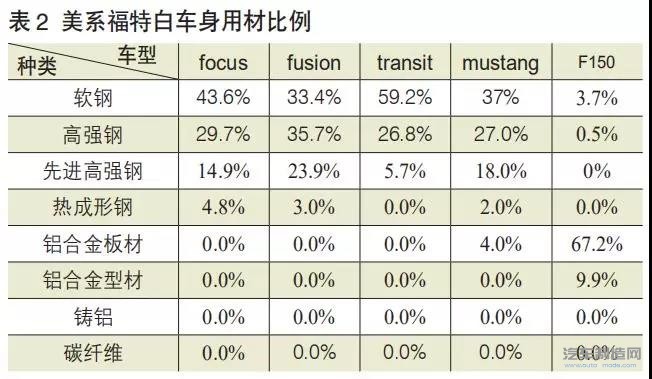
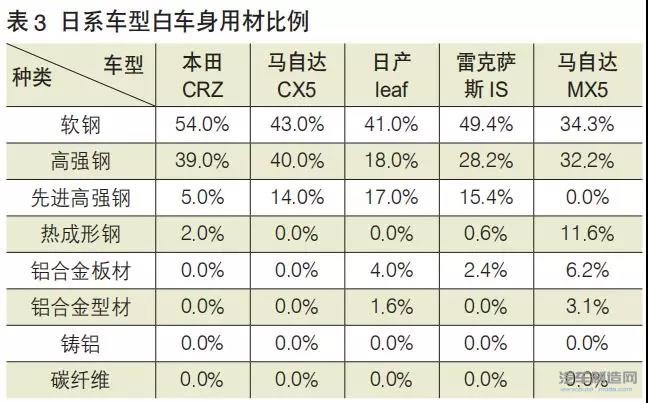
表2中,福特focus、福特fusion、福特transit和福特mustang处于奥迪轻量化白车身第一阶段用材水平,且只有福特mustang的机盖、翼子板应用铝合金(4%),福特F150处于奥迪轻量化白车身第三阶段用材水平,车身结构件和覆盖件大量应用铝合金。
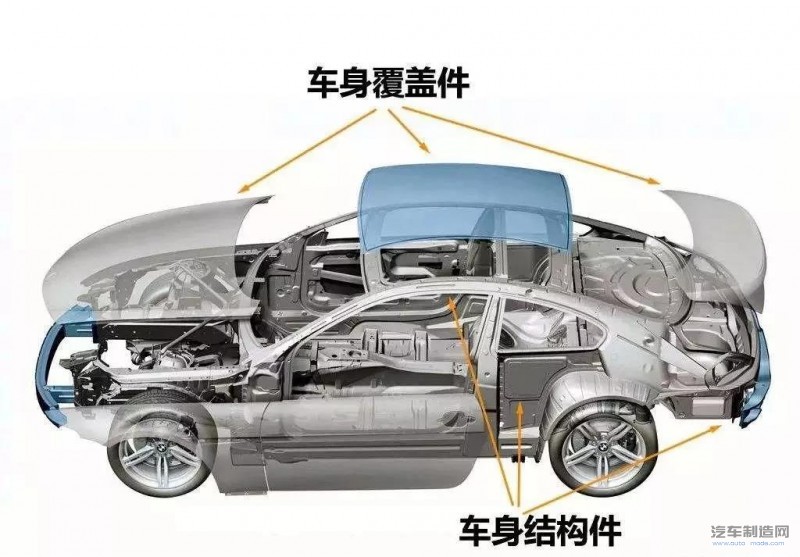
表3中的5款日系车型均处于奥迪轻量化白车身第一阶段用材水平。在日系车型中,只有对轻量化要求较高的跑车、电动车及部分高端车中少量应用铝合金(2%~10%),主要应用在防撞梁、机盖和翼子板三个部位。
车身多材料连接技术
四个白车身发展阶段,每个阶段都有与之相应的多材料连接技术,表4列举了不同的白车身发展阶段与之对应的多材料连接技术与主要应用部位。
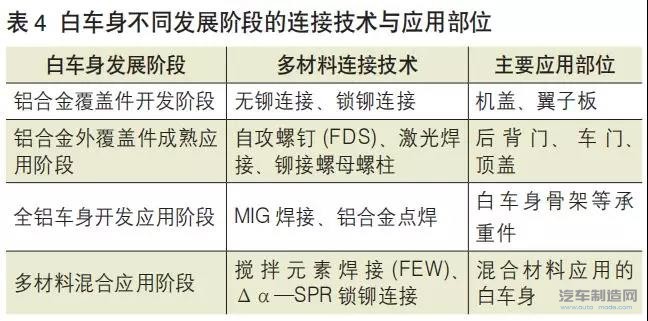
针对四个阶段轻量化白车身的用材,图5共归纳了目前最流行的9种白车身多材料连接技术。
根据奥迪车身发展的四个阶段,所对应的四个多材料连接技术发展阶段如下:
第一阶段应用的连接技术主要是无铆连接和锁铆连接(SPR)。无铆连接适合于不同金属材料及不同厚度连接,过程简单,一步完成且不需要预先打孔,能耗低,但连接强度略低。锁铆连接(SPR)具有很高的动态疲劳强度(约为焊点的2倍),碰撞吸收的能量较焊点高,铆接材料组合广泛,不过铆钉增加了车身自重。
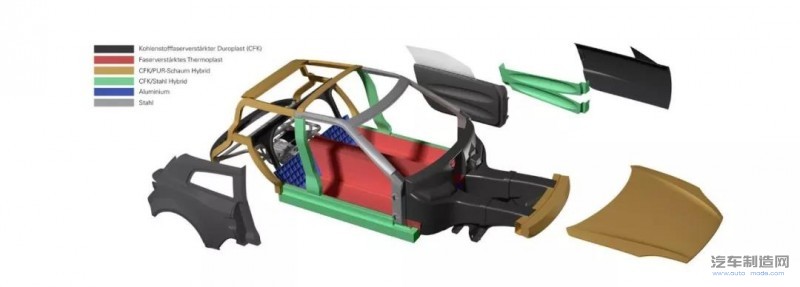
第二阶段应用的连接技术主要是自攻螺丝(FDS)、激光焊接和铆接螺母螺柱。自攻螺丝(FDS)机械强度高,动态连接强度高,单面连接,可与折边胶结合使用,拆卸更换螺丝方便;劣势是防腐蚀能力降低,增加了车身自重,可能会产生金属飞屑误伤工人。激光焊接速度快,焊点排布方式更灵活,焊点宽深比大,变形小;缺点是异种材料不可直接焊接,需焊部位务必非常精确,需在激光束的聚焦范围内。铆接螺母螺柱可集成在冲压模具中,减少工序,静态和动态载荷高,对涂层无损伤,适用板材范围广,铆点可以防液、防气,防止腐蚀,成品也容易检验;劣势是一次性投资大,连接高强度钢板时需预先开孔,工艺繁琐。
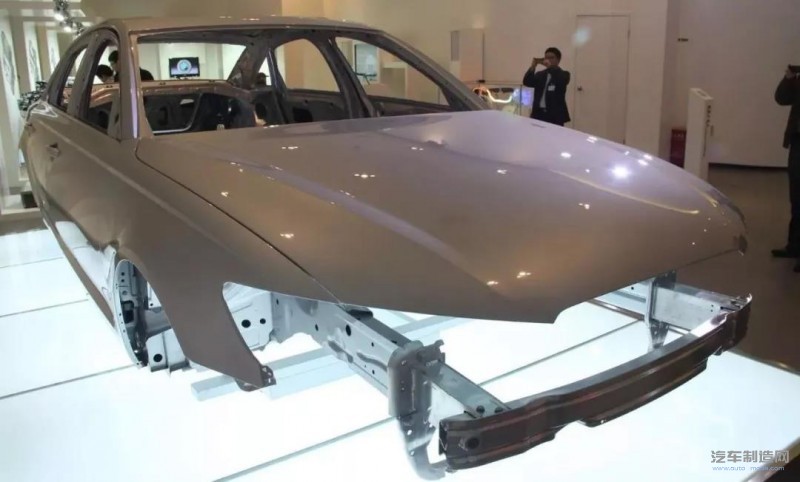
第三阶段应用的连接技术主要是MIG焊和铝合金点焊。MIG焊主要应用在A柱、B柱、顶盖横梁、消声器和减振塔等部位,优点是拥有更优的保护气氛、焊丝无焊渣,可焊接铝合金,但成本较高,操作难度大,细微缺陷都会造成严重的不良率。铝合金点焊主要应用于白车身及外覆盖件,优势是生产一致性高,表面质量高,变形小;缺点是需对原有钢产线进行大幅度改造,设备投入高,因此目前主机厂应用少,借鉴点少。
第四阶段应用的连接技术主要有摩擦塞铆焊(Friction Elment Welding FEW)和Δα—SPR锁铆连接。摩擦塞铆焊可以解决铝合金与高强钢、热成形钢之间的连接,且不需预先开孔,可以和胶混合使用,缺点是需要额外的紧固件,增加了自重,另外头部凸起2.5 mm需预防干涉,潮湿环境还需要在头部一侧增加PVC密封胶。Δα—SPR锁铆连接解决了碳纤维和铝合金膨胀系数不同在涂装过程中导致的铆点损坏问题,不过仅适用于膨胀率相差较大的材料连接。
结论
轻量化白车身方面,以奥迪为代表的白车身的发展与用材可归纳为四个阶段:铝合金覆盖件开发阶段、铝合金外覆盖件成熟应用阶段、全铝车身开发应用阶段和多材料混合应用阶段,总体趋势为铝合金应用量上升,软钢及热成形钢的应用量相应下降,材料应用趋于多样化,白车身重量逐步下降。国外白车身技术发展的进程中,德系车身用材较为激进,美系车身用材略显中庸,日系车型用材较为滞后。
车身多材料连接技术方面,针对轻量化白车身的四个发展阶段,多材料连接技术可对应规划为四个应用阶段,以适应不同阶段轻量化白车身的研发与生产;根据不同主机厂其白车身的用材发展现状,可对应规划并投入其对应阶段的多材料连接技术。多材料连接技术的应用阶段越高,其工艺应用越不成熟,尚需探索和改进。
汽车轻量化是节能减排的一个有效途径,而汽车轻量化最有效的手段就是轻质合金材料的应用,目前国外已开发出多种多材料应用的轻量化白车身,但其连接问题成为瓶颈,目前通用的点焊连接技术已无法满足要求,各种新晋的连接技术层出不穷。
随着国外轻量化白车身的发展,白车身的用材由钢板应用阶段逐步发展到多材料混合应用阶段。本文以奥迪品牌的白车身发展进程为例,归纳了其白车身用材演化的四个阶段,分析了典型欧系、美系和日系车型白车身用材发展现状及用材趋势。
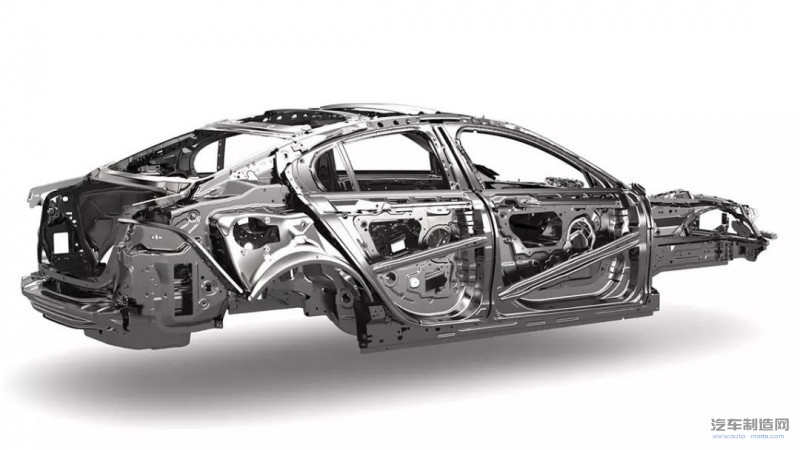
伴随着轻量化白车身的发展,其相应的多材料连接技术也随之发展迅速。针对四个白车身发展阶段,列举了目前9种常用的多材料连接技术,也对应规划为4个不同阶段,分析了每个阶段进程的多材料连接技术的适用范围与优劣势。
国外轻量化车身发展过程
纵观国外白车身的发展趋势,奥迪公司的白车身发展趋势极具代表性,到目前为止,其白车身的发展过程可分为四个阶段:
第一阶段:铝合金覆盖件开发阶段
这个阶段主要是为了增加材料强度级别,热成形钢逐步用于车身,还有少量铝合金覆盖件的应用。典型的车型代表为奥迪A3车型(见图1)。
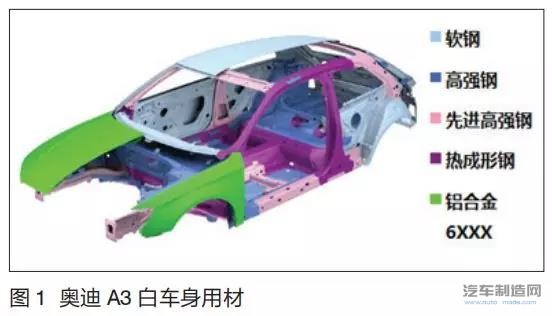
零部件用材方面,机盖、翼子板使用铝合金材质(3.2%),后座椅横梁、中通道、A柱、B柱、机舱纵梁后段、前围下板、后地板横梁和后地板纵梁等位置采用热成形钢(21.7%)。
第二阶段:铝合金外覆盖件成熟应用阶段
这一阶段,外覆盖件大量采用铝合金,铝合金覆盖件比重显著增加,热成形钢比重相对减少,典型的车型代表是奥迪A6车型(见图2)。
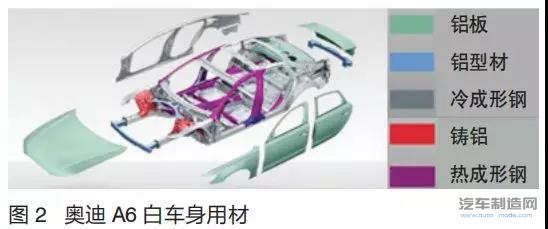
零部件用材方面,机盖、前后车门、翼子板、行李箱盖板、顶盖和前后防撞梁(铝型材)应用铝合金。铝合金用量较第一阶段增加至18%,中通道、座椅横梁、A柱和B柱等位置保留热成形钢,热成形钢的用量比例减少至11.3%。
第三阶段:全铝车身开发应用阶段
这个阶段,车身外覆盖件全部应用铝合金(铝板材)、铝型材和铸铝开始应用到车身结构件,轻量化效果显著,与此同时,高强钢和软钢板的用量急剧减少,典型的车型代表是奥迪TT车型(见图3)。
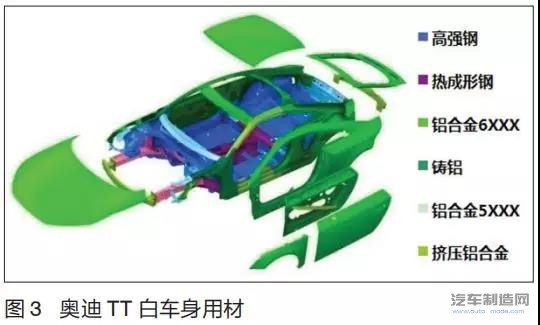
零部件用材方面,增加了A柱、C柱、侧围和顶盖横梁等位置的铝合金,铝合金用量由18%增加到35.8%,中通道、座椅横梁采用热成形钢,软钢应用量由35.2%下降到5.3%。
第四阶段:多材料混合应用阶段
这一阶段以铝合金为主要车身材料,铝型材和铸铝件大量应用到车身结构件。高强钢、软钢和碳纤维为辅助用材,典型的车型代表是奥迪Q7车型(见图4)。

零部件用材方面,地板、前纵梁等位置应用铝合金,铝合金用量较上一阶段由35.8%增加到49.9%,中通道采用的是铝板和热成形钢的混合结构,热成形钢的用量减少至9.2%。
车身用材比较及发展趋势
以上四款车型的白车身用材比例如表1所示。
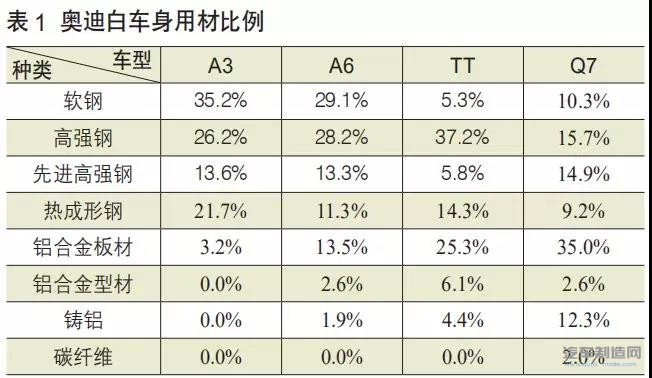
分析奥迪用材趋势如下:
铝合金用量上升趋势明显(3.2%→18.0%→35.8%→49.9%);
热成形钢整体用量呈下降趋势(21.7%→11.3%→14.3%→9.2%);
软钢用量下降趋势明显(35.2%→29.1%→5.3%→10.3%)。
除欧系的奥迪车型外,美系福特和日系车的用材比例如表2、表3所示。
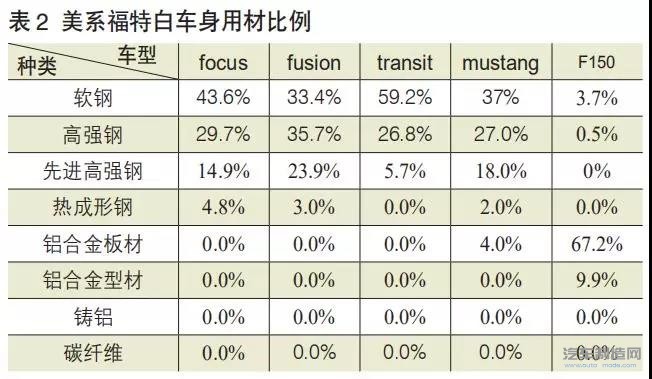
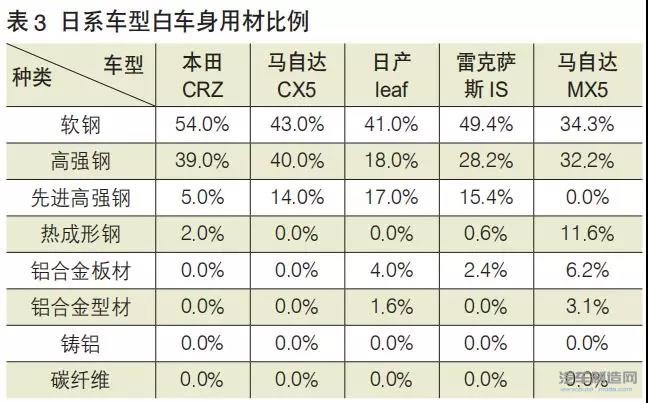
表2中,福特focus、福特fusion、福特transit和福特mustang处于奥迪轻量化白车身第一阶段用材水平,且只有福特mustang的机盖、翼子板应用铝合金(4%),福特F150处于奥迪轻量化白车身第三阶段用材水平,车身结构件和覆盖件大量应用铝合金。
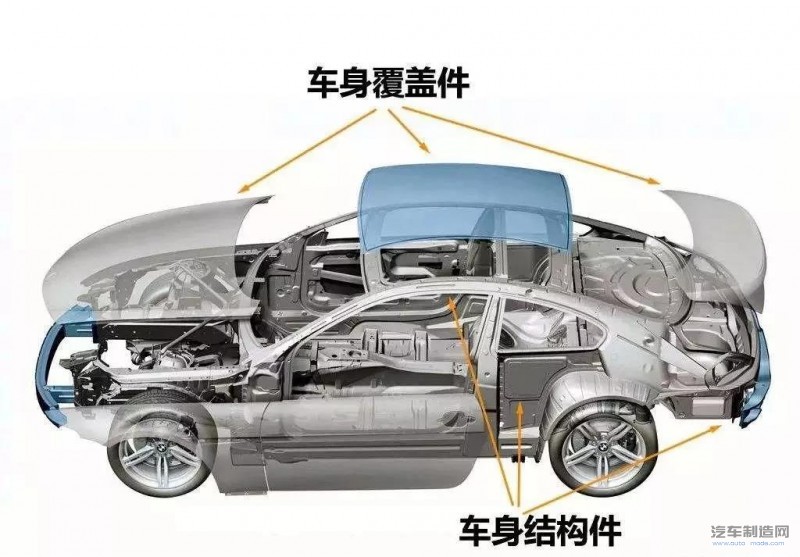
表3中的5款日系车型均处于奥迪轻量化白车身第一阶段用材水平。在日系车型中,只有对轻量化要求较高的跑车、电动车及部分高端车中少量应用铝合金(2%~10%),主要应用在防撞梁、机盖和翼子板三个部位。
车身多材料连接技术
四个白车身发展阶段,每个阶段都有与之相应的多材料连接技术,表4列举了不同的白车身发展阶段与之对应的多材料连接技术与主要应用部位。
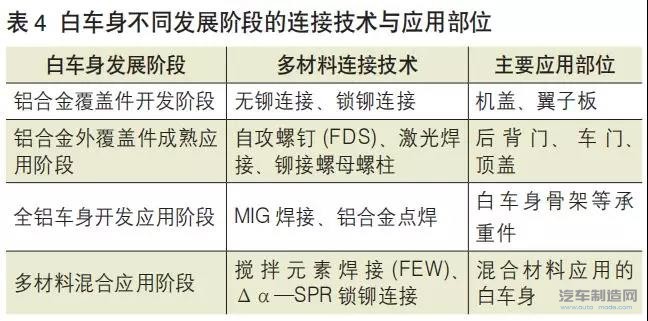
针对四个阶段轻量化白车身的用材,图5共归纳了目前最流行的9种白车身多材料连接技术。
根据奥迪车身发展的四个阶段,所对应的四个多材料连接技术发展阶段如下:
第一阶段应用的连接技术主要是无铆连接和锁铆连接(SPR)。无铆连接适合于不同金属材料及不同厚度连接,过程简单,一步完成且不需要预先打孔,能耗低,但连接强度略低。锁铆连接(SPR)具有很高的动态疲劳强度(约为焊点的2倍),碰撞吸收的能量较焊点高,铆接材料组合广泛,不过铆钉增加了车身自重。
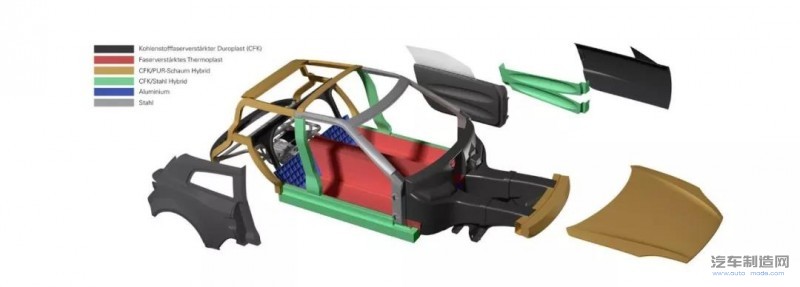
第二阶段应用的连接技术主要是自攻螺丝(FDS)、激光焊接和铆接螺母螺柱。自攻螺丝(FDS)机械强度高,动态连接强度高,单面连接,可与折边胶结合使用,拆卸更换螺丝方便;劣势是防腐蚀能力降低,增加了车身自重,可能会产生金属飞屑误伤工人。激光焊接速度快,焊点排布方式更灵活,焊点宽深比大,变形小;缺点是异种材料不可直接焊接,需焊部位务必非常精确,需在激光束的聚焦范围内。铆接螺母螺柱可集成在冲压模具中,减少工序,静态和动态载荷高,对涂层无损伤,适用板材范围广,铆点可以防液、防气,防止腐蚀,成品也容易检验;劣势是一次性投资大,连接高强度钢板时需预先开孔,工艺繁琐。
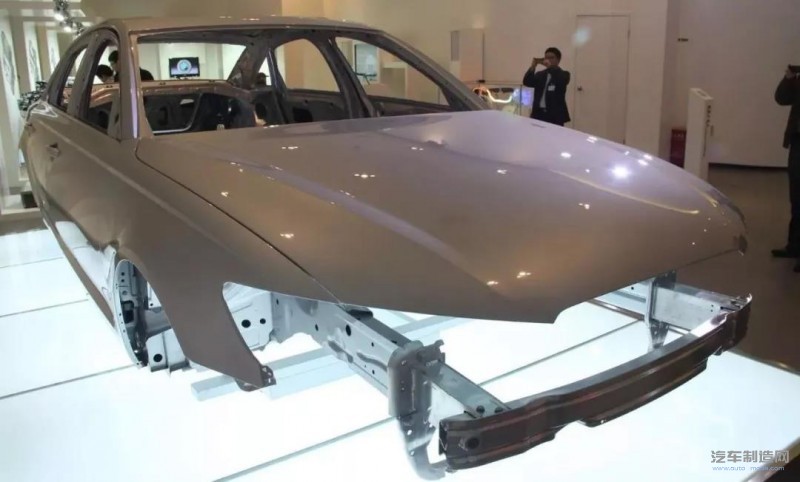
第三阶段应用的连接技术主要是MIG焊和铝合金点焊。MIG焊主要应用在A柱、B柱、顶盖横梁、消声器和减振塔等部位,优点是拥有更优的保护气氛、焊丝无焊渣,可焊接铝合金,但成本较高,操作难度大,细微缺陷都会造成严重的不良率。铝合金点焊主要应用于白车身及外覆盖件,优势是生产一致性高,表面质量高,变形小;缺点是需对原有钢产线进行大幅度改造,设备投入高,因此目前主机厂应用少,借鉴点少。
第四阶段应用的连接技术主要有摩擦塞铆焊(Friction Elment Welding FEW)和Δα—SPR锁铆连接。摩擦塞铆焊可以解决铝合金与高强钢、热成形钢之间的连接,且不需预先开孔,可以和胶混合使用,缺点是需要额外的紧固件,增加了自重,另外头部凸起2.5 mm需预防干涉,潮湿环境还需要在头部一侧增加PVC密封胶。Δα—SPR锁铆连接解决了碳纤维和铝合金膨胀系数不同在涂装过程中导致的铆点损坏问题,不过仅适用于膨胀率相差较大的材料连接。
结论
轻量化白车身方面,以奥迪为代表的白车身的发展与用材可归纳为四个阶段:铝合金覆盖件开发阶段、铝合金外覆盖件成熟应用阶段、全铝车身开发应用阶段和多材料混合应用阶段,总体趋势为铝合金应用量上升,软钢及热成形钢的应用量相应下降,材料应用趋于多样化,白车身重量逐步下降。国外白车身技术发展的进程中,德系车身用材较为激进,美系车身用材略显中庸,日系车型用材较为滞后。
车身多材料连接技术方面,针对轻量化白车身的四个发展阶段,多材料连接技术可对应规划为四个应用阶段,以适应不同阶段轻量化白车身的研发与生产;根据不同主机厂其白车身的用材发展现状,可对应规划并投入其对应阶段的多材料连接技术。多材料连接技术的应用阶段越高,其工艺应用越不成熟,尚需探索和改进。
编辑推荐
最新资讯
-
全球产业链聚沪 共探双碳新路径 SNEC
2025-04-18 18:05
-
柯马签订具有约束力的协议收购 Autom
2025-04-17 13:01
-
高效协同新范式:比亚迪叉车领创智能
2025-04-17 10:04
-
埃马克德国总部迎来中国社科院工业经
2025-04-15 09:40
-
埃马克这项全新应用即将在CIMT惊艳首
2025-04-15 09:37