耐世特专注于全方位整合制造与设计 推出数字追踪制造系统
2018-01-16 11:00:39· 来源:耐世特汽车系统
随心操控的引领者、世界领先的转向及动力传动系统供应商耐世特汽车系统于今日宣布,推出数字追踪™制造系统(Digital Trace™ Manufacturing),成为目前汽车行业中最先进、最全面、最集成的设计与制造系统之一。
随心操控的引领者、世界领先的转向及动力传动系统供应商耐世特汽车系统于今日宣布,推出数字追踪™制造系统(Digital Trace™ Manufacturing),成为目前汽车行业中最先进、最全面、最集成的设计与制造系统之一。
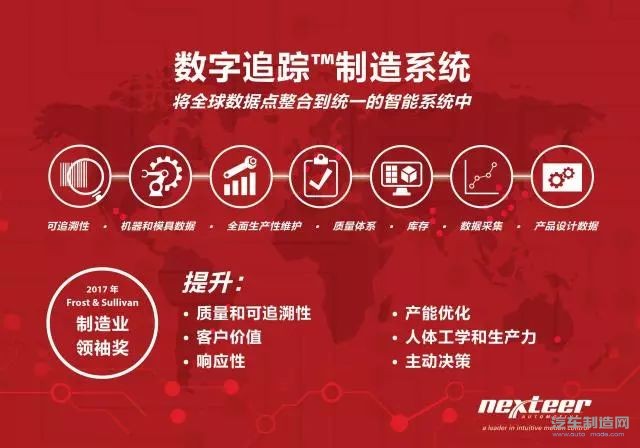
耐世特数字追踪™制造系统在统一的全球架构中运用最新的技术和数据分析。对客户而言,这不仅有助于实现产品的高质量和高性能,还能够在耐世特遍布全世界的24个制造工厂中推动价值和全球产能的优化。
在2018年1月13日至28日期间举行的2018年北美国际车展上,耐世特展示了这套行业领先的制造流程自动化系统。通过虚拟现实的呈现方式,参观者可以亲身体验数字追踪™制造系统是如何从工作站的整合优化开始,改善整个制造流程的。
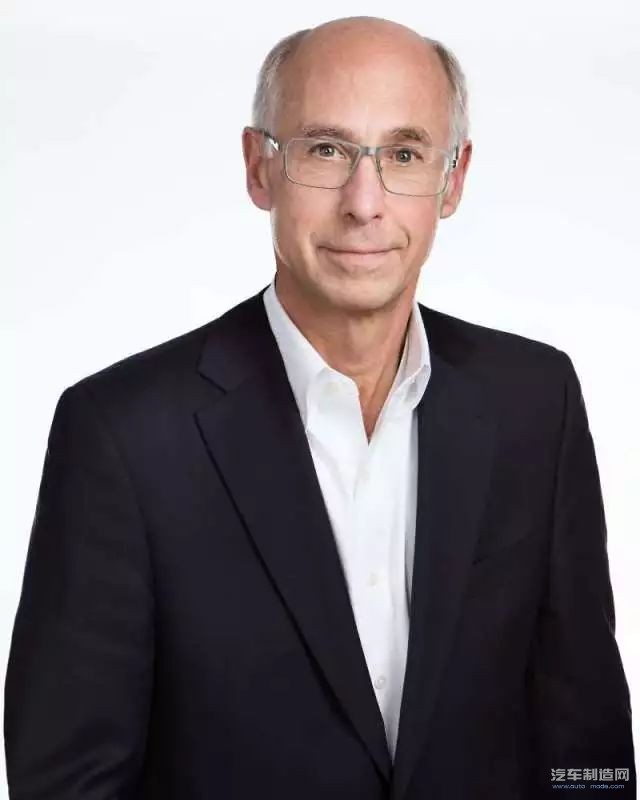
Dennis Hoeg
耐世特全球副总裁兼北美区首席运营官
“为了实现数字追踪™制造系统,我们采用了‘连点成线’的方法,对全球范围内数以千计的数据点进行标准化处理,使其始终能够交互通信。每个数据点都代表着一台设备、一套流程、一个数据库、一个文件、一个工作场所机器人等等。通过连接这些数据点,我们打造了一个统一的全球架构。数字追踪™制造系统让耐世特能够对其制造运营进行实时、动态的全局掌控,使我们的客户、员工以及利益相关方受益匪浅。”
从根本上来看,数字追踪™制造系统能够使耐世特深入地了解任一时刻的全球运营状况。此外,通过该系统,在某一工厂中进行的设计或生产改进即可快速地复制到全球范围。
大数据、行业趋势及耐世特之道
据Hoeg表示,与业界常说的“数字线程”或“制造自动化”有所不同,耐世特的数字追踪™制造系统覆盖的范围更广阔。Hoeg解释道,由于整合范围更广、整合层级更复杂,完全实施整个系统需要分阶段推进。不过,Hoeg表示他已经在实施初期阶段看到了该系统在客户响应和产品质量方面带来的积极影响。
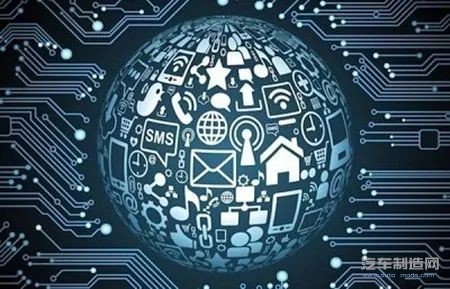
Hoeg强调:“随着系统的分阶段推进,我们预计其带来的效益将不断提升。耐世特作为行业的技术领导者,不仅仅为客户提供先进的转向及传动系统产品,我们的技术领先性更体现在制造方法上。”
带来真实可见的好处
在实施数字追踪™制造系统的过程中,耐世特将多项尖端科技和流程引入到制造运营中。数字追踪™制造系统能够帮助质量工程师在早期阶段主动、前瞻性地确认产品质量,从而避免了潜在的成本高昂的下线测试。这些技术和流程包括:
使用热图以可视化的方式实时识别高风险托盘,使现场服务工程师能够在出现问题之前进行主动维护。
追踪和存储序列号专有数据,并在制造过程中对性能进行测量。
建立虚拟“指挥中心”,对拒收部件的缺陷根源进行分析,快速采取改进措施。
对采集产品信息的数据库进行整合,从而进行完整的分析和快速的问题解决。
实施制造执行系统(MES),在车间对制造过程进行实时监测和管理。
精简并提升制造工艺
耐世特数字追踪™制造系统能够将公司所有的制造数据点全方位整合,从而:
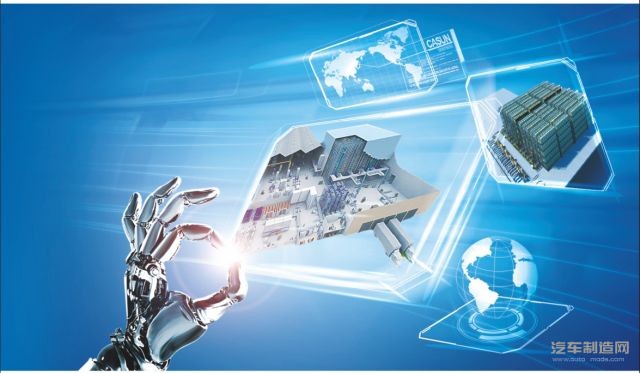
对全球制造活动进行清晰实时的掌控
对潜在的制造问题进行预测,在问题出现之前主动解决
通过“智造”系统收集经验教训并依此对决策做出微调,从而加速和扩大持续改进
在耐世特各个地区以及制造和产品工程部门之间进行更好的全球协作,从而缩短从设计到生产的周期
优化产能、车间物流、产品库存及计划
提高组件可追溯性,实现先进的质量管控、追踪及报告
运用大数据和人体工学的理念设计工作台,优化产线员工的工作环境
访问虚拟“指挥中心”,随时随地获取全球制造洞察,从而改善决策和问题解决能力
荣获Frost & Sullivan制造业领袖奖
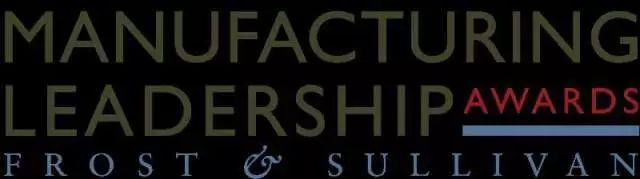
作为对制造卓越领导力的表彰,耐世特于去年凭借在全球范围内实施的先进制造和分析技术荣获著名市场分析咨询公司Frost & Sullivan授予的制造业领导力大奖(The Manufacturing Leadership Awards)。这些技术能够实现产品仓储、追溯以及质量管理过程的精简和互联。
Frost & Sullivan公司制造业领导力委员会全球副总裁、主编兼联合创始人David R. Brousell认为:“制造业领导力大奖的获奖企业向业界表明,制造业并不缺少远见卓识和技术创新。这些领导企业大力推进‘制造业4.0’的技术驱动型转型,不断创新商业模式,全面调动敬业的员工队伍,为制造业生产力提升的新时代打下基础。”
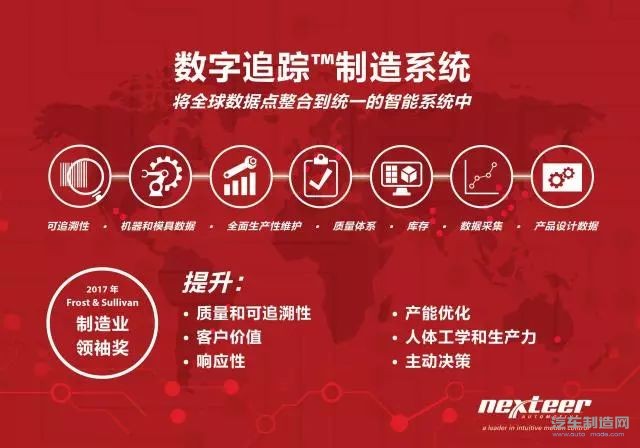
耐世特数字追踪™制造系统在统一的全球架构中运用最新的技术和数据分析。对客户而言,这不仅有助于实现产品的高质量和高性能,还能够在耐世特遍布全世界的24个制造工厂中推动价值和全球产能的优化。
在2018年1月13日至28日期间举行的2018年北美国际车展上,耐世特展示了这套行业领先的制造流程自动化系统。通过虚拟现实的呈现方式,参观者可以亲身体验数字追踪™制造系统是如何从工作站的整合优化开始,改善整个制造流程的。
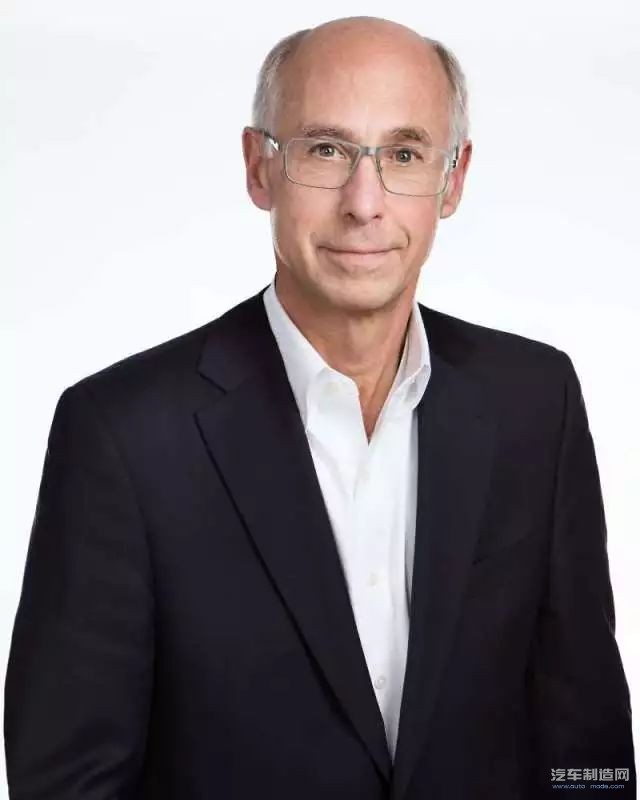
Dennis Hoeg
耐世特全球副总裁兼北美区首席运营官
“为了实现数字追踪™制造系统,我们采用了‘连点成线’的方法,对全球范围内数以千计的数据点进行标准化处理,使其始终能够交互通信。每个数据点都代表着一台设备、一套流程、一个数据库、一个文件、一个工作场所机器人等等。通过连接这些数据点,我们打造了一个统一的全球架构。数字追踪™制造系统让耐世特能够对其制造运营进行实时、动态的全局掌控,使我们的客户、员工以及利益相关方受益匪浅。”
从根本上来看,数字追踪™制造系统能够使耐世特深入地了解任一时刻的全球运营状况。此外,通过该系统,在某一工厂中进行的设计或生产改进即可快速地复制到全球范围。
大数据、行业趋势及耐世特之道
据Hoeg表示,与业界常说的“数字线程”或“制造自动化”有所不同,耐世特的数字追踪™制造系统覆盖的范围更广阔。Hoeg解释道,由于整合范围更广、整合层级更复杂,完全实施整个系统需要分阶段推进。不过,Hoeg表示他已经在实施初期阶段看到了该系统在客户响应和产品质量方面带来的积极影响。
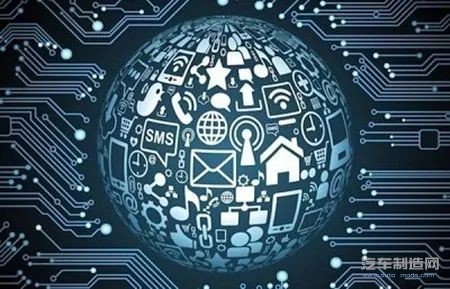
Hoeg强调:“随着系统的分阶段推进,我们预计其带来的效益将不断提升。耐世特作为行业的技术领导者,不仅仅为客户提供先进的转向及传动系统产品,我们的技术领先性更体现在制造方法上。”
带来真实可见的好处
在实施数字追踪™制造系统的过程中,耐世特将多项尖端科技和流程引入到制造运营中。数字追踪™制造系统能够帮助质量工程师在早期阶段主动、前瞻性地确认产品质量,从而避免了潜在的成本高昂的下线测试。这些技术和流程包括:
使用热图以可视化的方式实时识别高风险托盘,使现场服务工程师能够在出现问题之前进行主动维护。
追踪和存储序列号专有数据,并在制造过程中对性能进行测量。
建立虚拟“指挥中心”,对拒收部件的缺陷根源进行分析,快速采取改进措施。
对采集产品信息的数据库进行整合,从而进行完整的分析和快速的问题解决。
实施制造执行系统(MES),在车间对制造过程进行实时监测和管理。
精简并提升制造工艺
耐世特数字追踪™制造系统能够将公司所有的制造数据点全方位整合,从而:
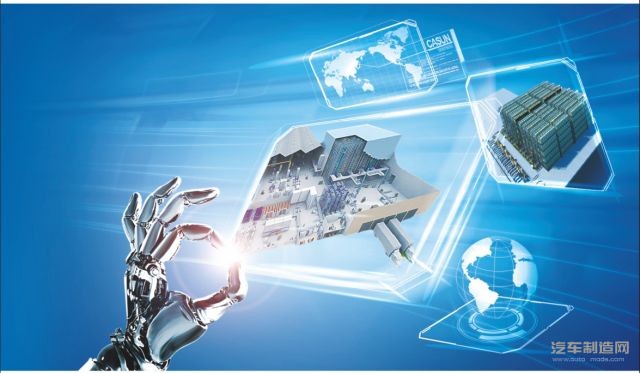
对全球制造活动进行清晰实时的掌控
对潜在的制造问题进行预测,在问题出现之前主动解决
通过“智造”系统收集经验教训并依此对决策做出微调,从而加速和扩大持续改进
在耐世特各个地区以及制造和产品工程部门之间进行更好的全球协作,从而缩短从设计到生产的周期
优化产能、车间物流、产品库存及计划
提高组件可追溯性,实现先进的质量管控、追踪及报告
运用大数据和人体工学的理念设计工作台,优化产线员工的工作环境
访问虚拟“指挥中心”,随时随地获取全球制造洞察,从而改善决策和问题解决能力
荣获Frost & Sullivan制造业领袖奖
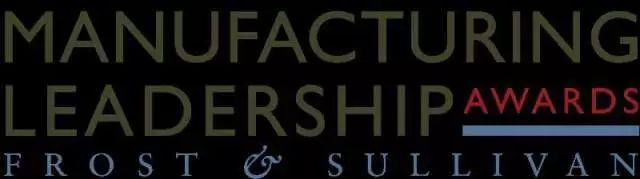
作为对制造卓越领导力的表彰,耐世特于去年凭借在全球范围内实施的先进制造和分析技术荣获著名市场分析咨询公司Frost & Sullivan授予的制造业领导力大奖(The Manufacturing Leadership Awards)。这些技术能够实现产品仓储、追溯以及质量管理过程的精简和互联。
Frost & Sullivan公司制造业领导力委员会全球副总裁、主编兼联合创始人David R. Brousell认为:“制造业领导力大奖的获奖企业向业界表明,制造业并不缺少远见卓识和技术创新。这些领导企业大力推进‘制造业4.0’的技术驱动型转型,不断创新商业模式,全面调动敬业的员工队伍,为制造业生产力提升的新时代打下基础。”
编辑推荐
最新资讯
-
“锂”想万家——比亚迪叉车在家电行
2025-04-28 10:02
-
全球工业数字化领袖齐聚申城,共绘智
2025-04-28 08:28
-
思看科技受邀出席第三届联合国教科文
2025-04-27 13:29
-
聚势谋远,智领新程——五菱柳机以硬
2025-04-27 13:22
-
聚势求新、智驱未来——五菱工业底盘
2025-04-27 13:22