传统磷化转锆系薄膜前处理的前期工艺试验分析
2018-01-23 17:45:07· 来源:《涂料工业》
新材料在汽车涂装行业中的应用有助于在汽车制造过程中实现降低能耗、增进环保,并达到提高生产效率和提升产品性能的目的,锆系薄膜前处理作为其中的一项新技术,在节能环保方面的表现尤为突出。
随着全球各国对环境保护的不断加强及技术的进步,汽车涂装的前处理材料也不断涌现出环保新产品,如低温脱脂、液体表调、薄膜前处理产品等。新材料在汽车涂装行业中的应用有助于在汽车制造过程中实现降低能耗、增进环保,并达到提高生产效率和提升产品性能的目的,锆系薄膜前处理作为其中的一项新技术,在节能环保方面的表现尤为突出。《涂装行业清洁生产评价指标体系》将薄膜型转化膜处理工艺归为I级的最高基准值。因此,对传统磷化转为薄膜前处理设计实验进行可行性研究,为老线转换薄膜前处理产品做前期准备的工作非常有意义。
锆系薄膜前处理技术
传统的汽车涂装磷化前处理工艺存在污染严重(含磷,并含有镍、锰等重金属离子)、沉渣多、能耗大等缺点,是需要淘汰的高污染高能耗的落后工艺。在推行环保和清洁生产的大趋势下,新型薄膜前处理产品应运而生,以PPG、汉高为代表的锆系薄膜前处理和凯密特为代表的硅烷薄膜前处理已在全球范围内得到推广运用。锆系薄膜的涂层非常致密,因此通常又被称为陶瓷涂层,可以为金属底材提供等同于传统磷化工艺的防腐、耐酸、耐碱等性能。
锆系薄膜前处理成膜利用的是金属表面微电池反应原理,阳极发生氧化反应,如式(1);阴极发生还原反应,如式(2)所示。

阴极附近金属表面局部pH升高,促进氟锆酸解离,析出氧化锆。同时,溶液中的氟离子捕捉剂与氟离子形成稳定的氟络合物,以降低氟锆酸分解出的氟离子,促进锆系薄膜的生成。
锆系薄膜前处理生产线,可省去原磷化前的表调和磷化后的水洗和钝化工艺,并且无磷无镍生成,可减少废水排放;转化槽可在室温下运行,降低能耗的同时,也可减少设备的刻蚀;沉渣量降低明显,可省去磷化除渣系统的使用,并减少槽体、管路、喷嘴等设备的清洗频次。
锆系薄膜对处理车身混合板材也具有优势,特别是铝车身零件占比20%以上时。传统磷化因铝离子析出产生大量冰晶石/钾冰晶石结晶沉渣,影响整车零件成膜,而锆系薄膜在铝或铝合金零件上沉积氧化锆成膜的同时,因槽液兼容性好,析出的铝离子也无大量结晶沉渣。但锆系薄膜由于膜厚非常薄,在车身使用的混合底材上呈现的颜色不同,所以很难遮盖底材的缺陷,容易产生条印等问题,所以对底材的表面状态要求较高。
本文进行研究的薄膜材料由汉高公司提供,电泳涂料由BASF公司提供。
2 应用研究
2.1泳透力对比
泳透力是电泳的一项重要指标,由传统磷化转为锆系薄膜后,电泳的泳透力也可能随之发生改变。实验使用冷轧板泳透力条,分别对其进行磷化和锆系薄膜处理。再将其放置在目标工厂同一辆车中进行泳透力测试。结果如图1所示。
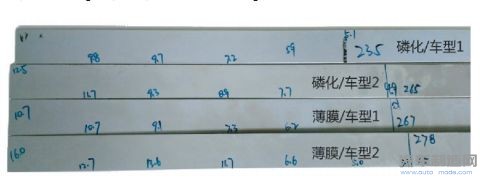
图1 磷化/锆系薄膜处理后的泳透力对比
从图1可以发现,使用锆系薄膜的泳透力条表现出了更好的泳透力,薄膜前处理工艺与高泳透力搭配下的泳透力能满足现场要求。磷化处理的2次泳透力结果为235mm和265mm,而使用锆系薄膜处理的泳透力结果为267mm和278mm。这可能是因为锆系薄膜在泳透力条上形成的膜更薄,对应的膜阻要比磷化膜小,因此泳透力条更容易上电泳,这对于提升车身内腔电泳膜厚是有帮助的。
2.2上电电压对比
从泳透力实验结果可以看出,锆系薄膜处理的板材在电泳上电方面和传统磷化处理的板材有较大不同。因此,实验对比了2种工艺处理板材的上电电压,结果如表1所示。

表1 2种工艺处理板材的上电电压对比
从表1可见,在相同电压相同电泳时间下,锆系薄膜处理的板材能获得更高的电泳膜厚。
2.3薄膜前处理停线模拟实验
锆系薄膜的反应机理与传统磷化反应机理不同,在停线后,其反应并不会快速自动中止。在镀锌板上,其反应速率在20min后才有所降低,如图2所示。
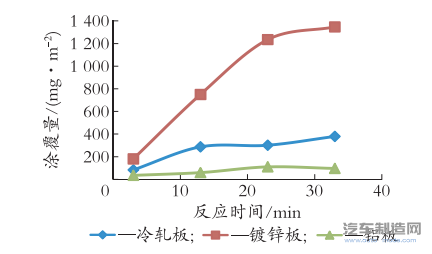
图2 不同反应时间锆系薄膜质量变化的影响
实验模拟了车身在出槽过程中发生停线的情形,先将整块板材全浸在锆系薄膜槽液中,在达到标准工艺时间后,提起板材,使其一半暴露在空气中,一半仍在槽液中继续反应。观察不同锆系薄膜停线时间对最终电泳性能的影响,结果如表2所示。其中,初始附着力参考标准GMW14829,使用Gardco或者BYKGardner划格仪以及3M公司的8981胶带进行测试,按失效面积大小进行评级。标准要求为0级或1级,即失效面积小于5%;240h湿热老化附着力的测试方法同初始附着力,但电泳板在测试附着力前需按GMW14729标准在(38±2)℃,湿度100%的环境下保养240 h。
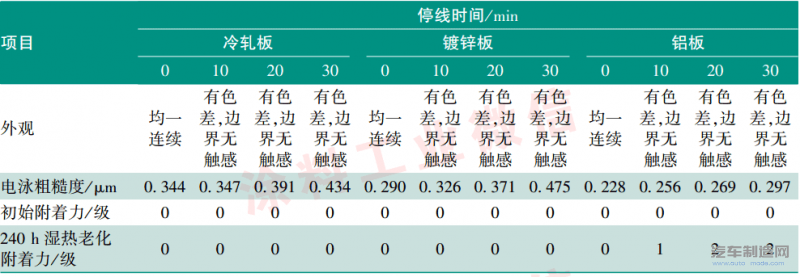
表2 锆系停线时间对电泳板外观及附着力的影响
从表2可以看出,半浸的停线会导致板材两部分有明显的色差,但是边界无触感,不需要打磨处理。停线时间的延长,会导致电泳粗糙度有所上升。各板材的电泳初始附着力结果均合格。但对电泳板材进行240h的湿热老化处理后,铝板在锆系薄膜停线20min以及30min的电泳附着出现不合格现象(见图3)。
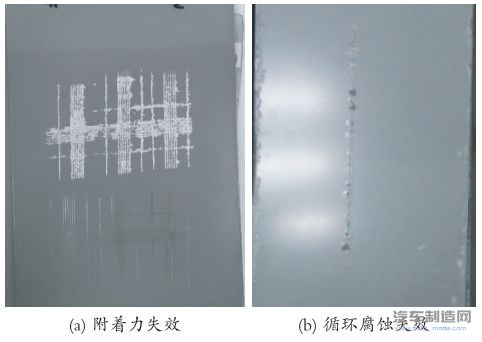
图3 停线实验中的失效样板
实验同时对各电泳后的板材进行了石击测试和循环腐蚀测试,测试结果如表3所示。其中,石击测试按标准GMW14700规定使用SAEJ400注明的砾石投掷测试设备和8~16mm的砾石在室温以及-18℃2个温度下进行,一般要求评价要高于8级,即电泳破损宽度不大于1.5mm;循环腐蚀测试则参考GMW14282进行26个盐雾循环,观察扩蚀宽度,标准要求冷轧板扩蚀宽度小于6mm,镀锌板、铝板扩蚀宽度小于4mm。室温以及-18℃条件下的石击测试结果均合格(≥8)。而循环腐蚀中,冷轧板停线20min、30min以及镀锌板停线20min的测试结果均勉强达标,镀锌板停线30min的循环腐蚀测试结果不达标。
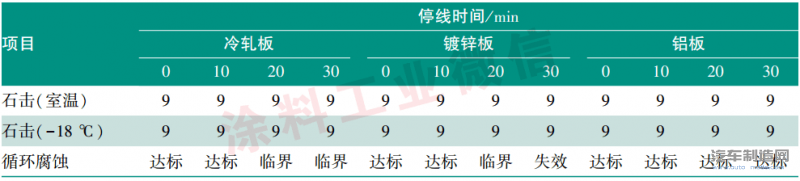
表3 不同锆系反应时间的电泳板耐石击和耐腐蚀性能
从以上测试结果可以看出,锆系薄膜前处理停线10min对车身板材不会有负面影响,停线车可以直接放行;停线20min部分性能会有下降,需要针对实际情况综合评估决定放行与否;停线30min,由于板材防腐蚀性能有所下降,建议进行报废处理。
2.4电泳入槽方式模拟实验
传统磷化车身在进电泳槽前,有全湿入槽或半干半湿入槽等方式。转换成锆系薄膜后,有必要研究其对入槽方式是否有特殊需求。实验模拟了5种入槽方式,分别是:半干半纯水、半干半超滤液、纯水喷淋全湿、超滤液喷淋全湿以及全干入槽,实验结果如图4所示。由图4可以看出,5种入槽方式的电泳板都没有明显边界,喷涂面漆后,表面无缺陷。
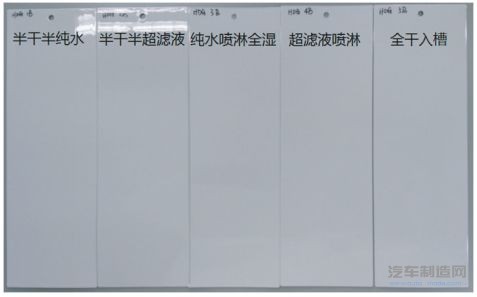
图4 不同电泳入槽方式的面漆外观
2.5打磨印遮盖模拟实验
鉴于锆系薄膜前处理在板材上形成转换膜厚度只有10~200nm,远比传统2~3μm的磷化膜要薄。因此其对板材打磨印的遮盖能力也是需要关注的性能之一。
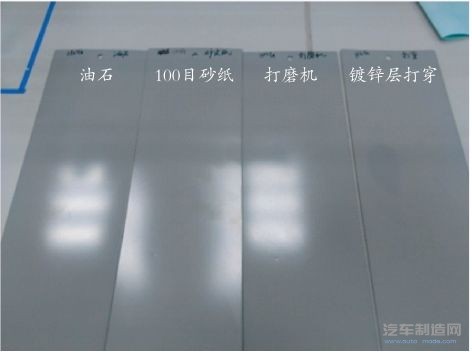
图5 镀锌板4种打磨状态后的电泳板
实验选取车身板材采用的冷轧板、镀锌板和铝板,对各样板进行打磨。打磨方式分别为100目砂纸手工打磨、100目砂纸打磨机打磨、油石打磨。其中镀锌板额外增加镀锌层打穿的遮盖考察。打磨完成后,将各板材按正常工艺进行薄膜以及电泳处理,观察打磨印状态,如图5所示。由图5可以看出,冷轧板和铝板打磨后电泳外观良好,只有镀锌板在被打穿之后,打磨区域与其他区域有色差。而在粗糙度、外观以及附着力方面,打磨区域的粗糙度比未打磨区域基本持平或略偏高,附着力均合格,结果见表4。
以上数据表明,目前的车身打磨状态能被锆系薄膜以及电泳良好覆盖,常规打磨印不会对外观造成不良影响。对以上板材喷涂面漆后,其外观无明显缺陷。
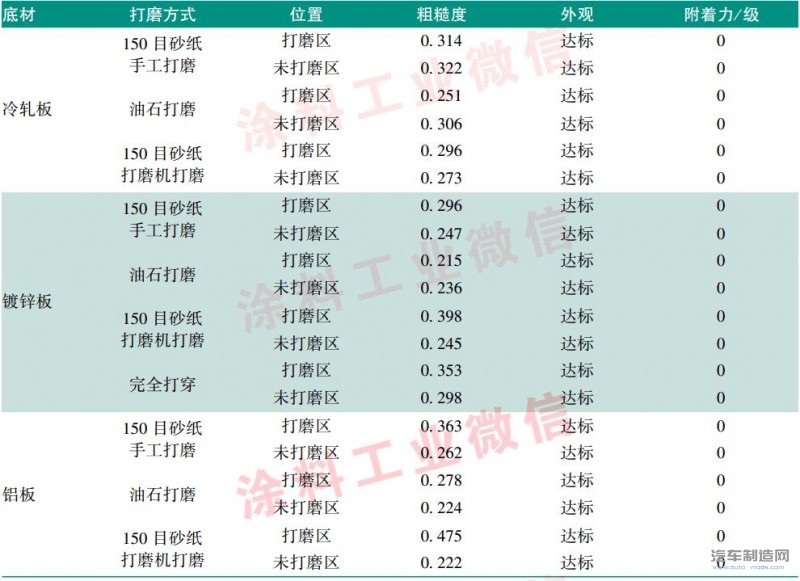
表4 不同打磨状态的性能评估
3 总结
薄膜前处理工艺是绿色涂装工艺,节能减排优势突出。但是很多主机厂出于对新工艺稳定性的担忧,导致其在国内应用进展缓慢。通过以上各方面性能的研究,我们认为薄膜前处理工艺在各方面均能达到目前的质量要求。通过对其工艺特性的进一步熟悉,在未来完全有可能全面替代传统磷化工艺。
锆系薄膜前处理技术
传统的汽车涂装磷化前处理工艺存在污染严重(含磷,并含有镍、锰等重金属离子)、沉渣多、能耗大等缺点,是需要淘汰的高污染高能耗的落后工艺。在推行环保和清洁生产的大趋势下,新型薄膜前处理产品应运而生,以PPG、汉高为代表的锆系薄膜前处理和凯密特为代表的硅烷薄膜前处理已在全球范围内得到推广运用。锆系薄膜的涂层非常致密,因此通常又被称为陶瓷涂层,可以为金属底材提供等同于传统磷化工艺的防腐、耐酸、耐碱等性能。
锆系薄膜前处理成膜利用的是金属表面微电池反应原理,阳极发生氧化反应,如式(1);阴极发生还原反应,如式(2)所示。

阴极附近金属表面局部pH升高,促进氟锆酸解离,析出氧化锆。同时,溶液中的氟离子捕捉剂与氟离子形成稳定的氟络合物,以降低氟锆酸分解出的氟离子,促进锆系薄膜的生成。
锆系薄膜前处理生产线,可省去原磷化前的表调和磷化后的水洗和钝化工艺,并且无磷无镍生成,可减少废水排放;转化槽可在室温下运行,降低能耗的同时,也可减少设备的刻蚀;沉渣量降低明显,可省去磷化除渣系统的使用,并减少槽体、管路、喷嘴等设备的清洗频次。
锆系薄膜对处理车身混合板材也具有优势,特别是铝车身零件占比20%以上时。传统磷化因铝离子析出产生大量冰晶石/钾冰晶石结晶沉渣,影响整车零件成膜,而锆系薄膜在铝或铝合金零件上沉积氧化锆成膜的同时,因槽液兼容性好,析出的铝离子也无大量结晶沉渣。但锆系薄膜由于膜厚非常薄,在车身使用的混合底材上呈现的颜色不同,所以很难遮盖底材的缺陷,容易产生条印等问题,所以对底材的表面状态要求较高。
本文进行研究的薄膜材料由汉高公司提供,电泳涂料由BASF公司提供。
2 应用研究
2.1泳透力对比
泳透力是电泳的一项重要指标,由传统磷化转为锆系薄膜后,电泳的泳透力也可能随之发生改变。实验使用冷轧板泳透力条,分别对其进行磷化和锆系薄膜处理。再将其放置在目标工厂同一辆车中进行泳透力测试。结果如图1所示。
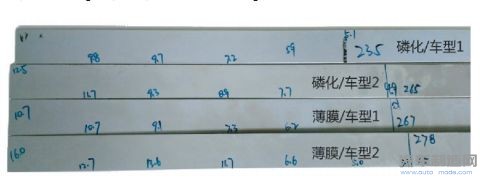
图1 磷化/锆系薄膜处理后的泳透力对比
从图1可以发现,使用锆系薄膜的泳透力条表现出了更好的泳透力,薄膜前处理工艺与高泳透力搭配下的泳透力能满足现场要求。磷化处理的2次泳透力结果为235mm和265mm,而使用锆系薄膜处理的泳透力结果为267mm和278mm。这可能是因为锆系薄膜在泳透力条上形成的膜更薄,对应的膜阻要比磷化膜小,因此泳透力条更容易上电泳,这对于提升车身内腔电泳膜厚是有帮助的。
2.2上电电压对比
从泳透力实验结果可以看出,锆系薄膜处理的板材在电泳上电方面和传统磷化处理的板材有较大不同。因此,实验对比了2种工艺处理板材的上电电压,结果如表1所示。

表1 2种工艺处理板材的上电电压对比
从表1可见,在相同电压相同电泳时间下,锆系薄膜处理的板材能获得更高的电泳膜厚。
2.3薄膜前处理停线模拟实验
锆系薄膜的反应机理与传统磷化反应机理不同,在停线后,其反应并不会快速自动中止。在镀锌板上,其反应速率在20min后才有所降低,如图2所示。
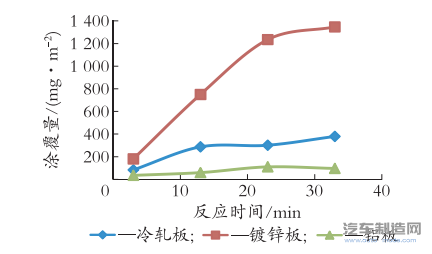
图2 不同反应时间锆系薄膜质量变化的影响
实验模拟了车身在出槽过程中发生停线的情形,先将整块板材全浸在锆系薄膜槽液中,在达到标准工艺时间后,提起板材,使其一半暴露在空气中,一半仍在槽液中继续反应。观察不同锆系薄膜停线时间对最终电泳性能的影响,结果如表2所示。其中,初始附着力参考标准GMW14829,使用Gardco或者BYKGardner划格仪以及3M公司的8981胶带进行测试,按失效面积大小进行评级。标准要求为0级或1级,即失效面积小于5%;240h湿热老化附着力的测试方法同初始附着力,但电泳板在测试附着力前需按GMW14729标准在(38±2)℃,湿度100%的环境下保养240 h。
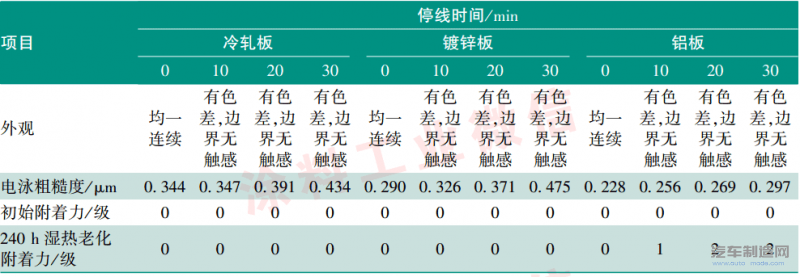
表2 锆系停线时间对电泳板外观及附着力的影响
从表2可以看出,半浸的停线会导致板材两部分有明显的色差,但是边界无触感,不需要打磨处理。停线时间的延长,会导致电泳粗糙度有所上升。各板材的电泳初始附着力结果均合格。但对电泳板材进行240h的湿热老化处理后,铝板在锆系薄膜停线20min以及30min的电泳附着出现不合格现象(见图3)。
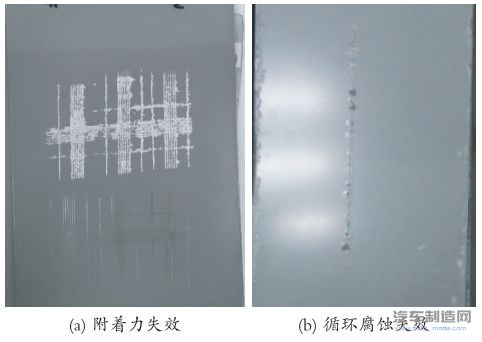
图3 停线实验中的失效样板
实验同时对各电泳后的板材进行了石击测试和循环腐蚀测试,测试结果如表3所示。其中,石击测试按标准GMW14700规定使用SAEJ400注明的砾石投掷测试设备和8~16mm的砾石在室温以及-18℃2个温度下进行,一般要求评价要高于8级,即电泳破损宽度不大于1.5mm;循环腐蚀测试则参考GMW14282进行26个盐雾循环,观察扩蚀宽度,标准要求冷轧板扩蚀宽度小于6mm,镀锌板、铝板扩蚀宽度小于4mm。室温以及-18℃条件下的石击测试结果均合格(≥8)。而循环腐蚀中,冷轧板停线20min、30min以及镀锌板停线20min的测试结果均勉强达标,镀锌板停线30min的循环腐蚀测试结果不达标。
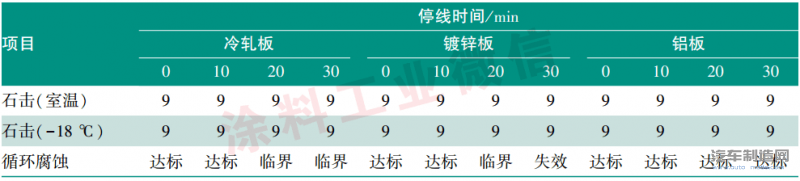
表3 不同锆系反应时间的电泳板耐石击和耐腐蚀性能
从以上测试结果可以看出,锆系薄膜前处理停线10min对车身板材不会有负面影响,停线车可以直接放行;停线20min部分性能会有下降,需要针对实际情况综合评估决定放行与否;停线30min,由于板材防腐蚀性能有所下降,建议进行报废处理。
2.4电泳入槽方式模拟实验
传统磷化车身在进电泳槽前,有全湿入槽或半干半湿入槽等方式。转换成锆系薄膜后,有必要研究其对入槽方式是否有特殊需求。实验模拟了5种入槽方式,分别是:半干半纯水、半干半超滤液、纯水喷淋全湿、超滤液喷淋全湿以及全干入槽,实验结果如图4所示。由图4可以看出,5种入槽方式的电泳板都没有明显边界,喷涂面漆后,表面无缺陷。
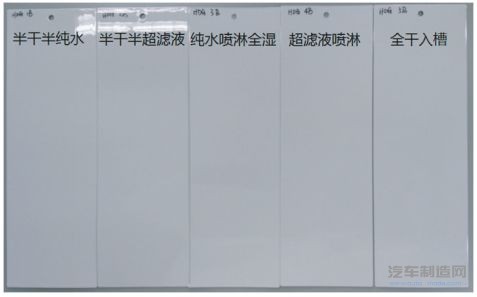
图4 不同电泳入槽方式的面漆外观
2.5打磨印遮盖模拟实验
鉴于锆系薄膜前处理在板材上形成转换膜厚度只有10~200nm,远比传统2~3μm的磷化膜要薄。因此其对板材打磨印的遮盖能力也是需要关注的性能之一。
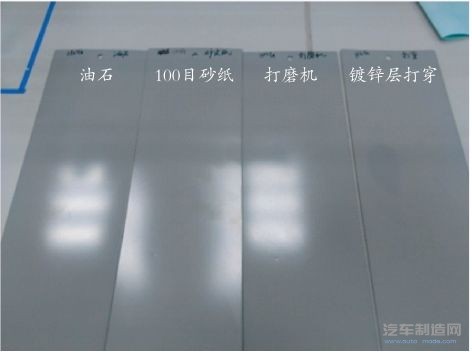
图5 镀锌板4种打磨状态后的电泳板
实验选取车身板材采用的冷轧板、镀锌板和铝板,对各样板进行打磨。打磨方式分别为100目砂纸手工打磨、100目砂纸打磨机打磨、油石打磨。其中镀锌板额外增加镀锌层打穿的遮盖考察。打磨完成后,将各板材按正常工艺进行薄膜以及电泳处理,观察打磨印状态,如图5所示。由图5可以看出,冷轧板和铝板打磨后电泳外观良好,只有镀锌板在被打穿之后,打磨区域与其他区域有色差。而在粗糙度、外观以及附着力方面,打磨区域的粗糙度比未打磨区域基本持平或略偏高,附着力均合格,结果见表4。
以上数据表明,目前的车身打磨状态能被锆系薄膜以及电泳良好覆盖,常规打磨印不会对外观造成不良影响。对以上板材喷涂面漆后,其外观无明显缺陷。
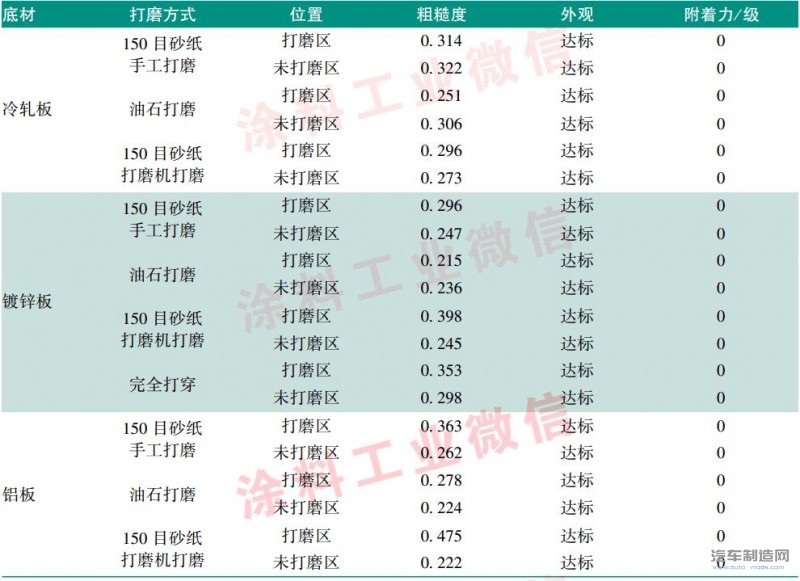
表4 不同打磨状态的性能评估
3 总结
薄膜前处理工艺是绿色涂装工艺,节能减排优势突出。但是很多主机厂出于对新工艺稳定性的担忧,导致其在国内应用进展缓慢。通过以上各方面性能的研究,我们认为薄膜前处理工艺在各方面均能达到目前的质量要求。通过对其工艺特性的进一步熟悉,在未来完全有可能全面替代传统磷化工艺。
- 下一篇:简单分析汽车涂装生产线技术改造
- 上一篇:简单分析继电器类型以及相关应用
编辑推荐
最新资讯
-
全球产业链聚沪 共探双碳新路径 SNEC
2025-04-18 18:05
-
柯马签订具有约束力的协议收购 Autom
2025-04-17 13:01
-
高效协同新范式:比亚迪叉车领创智能
2025-04-17 10:04
-
埃马克德国总部迎来中国社科院工业经
2025-04-15 09:40
-
埃马克这项全新应用即将在CIMT惊艳首
2025-04-15 09:37