简单分析配套企业智能冲压车间该如何规划
2018-01-24 09:10:47· 来源:锻造与冲压
随着冲压工艺的完善、材料的变革,企业对冲压车间智能制造的要求越来越高,工厂的智能化程度对企业利润的影响越来越大。
国内汽车行业以及配套企业面临的机遇和挑战
目前,我国是全球汽车产销第一大国,从2013 年以来汽车产销量一直维持在2000 万辆以上。近几年中国汽车生产基地也呈现爆炸式发展,90%的省份都有汽车企业的生产基地,而且企业新增基地数量在30% 以上,产能陆续释放。这其中一个比较重要的特点是:新增基地比较集中,车型较多,例如湖北地区除东风集团新建基地外,通用汽车、广汽集团、长丰汽车、众泰汽车等也都新建基地。以200 公里配套距离来计算,这就给所有的配套企业创造出新的发展机遇。
这种新的发展特点,对配套企业来说,变化是非常大的:
⑴生产车型较多,多家产品共线生产情况突出,对冲压生产线的兼容性要求增高;
⑵换模更加频繁,手工线、液压线越来越无法满足产能需求;
⑶企业相对集中也带来了用工难的问题,冲压工人流动性变大,配套企业面临人工成本增加的巨大压力。这些日益突出的矛盾是我们要进行冲压车间智能规划的动力所在。
智能冲压车间规划的原则和参考因素
在进行智能冲压车间规划时的原则和参考要素:
⑴产品种类导入;
⑵产能预期导入;
⑶投资及回收期导入(图1)。
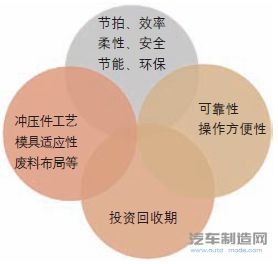
图1 参考要素叠加图
产品种类包括冲压件的工艺要求、模具适应性要求、冲压件的品种要求。产能预期要依据工厂产量测算,月产能(冲次)= 小时产量× 每日工作小时数× 每月工作日× 模具数量;月实际产能(冲次)=每分钟实际冲次×60× 每日工作时间小时数× 每月工作日× 模具数量。总投资预算包括冲压设备预算、模具预算、厂房预算、工装等辅助设备预算;年产量预估、原材料预估费用、人工成本预估费用、企业运行费用、承接产品的预期。
目前,现阶段冲压生产工艺已经日趋完善,冲压装备智能化发展迅速,可供选择的方案很多。以上三个要素综合叠加,就能找到一种最适合企业自身发展的整体规划方案。
智能冲压规划的案例浅析
新建冲压基地智能冲压规划
⑴大型覆盖件。压力机部分需要多连杆四点压力机(1 台)+ 偏心四点压力机(3 ~ 5 台);自动化部分需要机器人;整线节拍为8 ~ 12 次/ 分钟。
⑵中小型冲压件。双点快速自动化冲压线:双点压力机(4 ~ 5 台)+ 机械手,同步控制技术为15 次/ 分钟;800 ~ 3200t 多工位自动化冲压线25 ~ 30 次/ 分钟;400 ~ 1600t 级进模自动化冲压线30 ~ 60 次/ 分钟。
⑶板材备料。500 ~ 1250t 开卷落料线。
案例解析
⑴天津某汽配企业(天津一汽—大众的配套商)的大型冲压件解决方案(生产侧围、四门、两盖)。生产线采用整线湿式离合器+ 整线全防护,传输方式为机器人,六台压力机:1 台P4LS-2100+5 台P4S-1200, 中心距6500mm; 首台P4LS-2100 为八连杆、八点600t 数控液压垫、公称力行程25mm,后续P4S-1200 为偏心+ 上气垫。
压力机参数、性能和要求同天津一汽—大众冲压线相同,整线节拍低于主车厂。生产线特点:整线投资相比主车厂可降低30% ~ 50%,可实现大型冲压件的承制。
⑵宁波某汽车零部件制造(长安福特、吉利汽车等企业配套商)的中小型冲压件解决方案,如图2所示。线首部分有垛料小车+ 拆垛机械手+ 对中台+ 上料机械手;压力机部分为1 台P2S-1600+1 台P2S-1000+2 台P2S-800+1 台P2S-1000 五台双点偏心结构的机械压力机;传输部分为4 套机械手,整线节拍为15spm;线尾部分为下料机械手+ 传输皮带;整线同步功能;压力机间距为5500 ~ 6500mm。

图2 双点快速自动化冲压线
生产线特点:可实现两种生产模式,实现更多冲压产品工艺要求,既可以满足4 序生产,也可以满足5 序生产,如图3 所示。
生产模式⑴:五台压力机自动化生产;
生产模式⑵:前四台压力机自动化生产,最后一台压力机多工位生产。
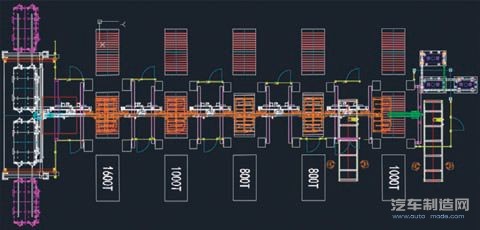
图3 冲压线布局图
机械手采用同步生产模式,效率相比手工线提高40% ~ 60%,最快节拍可达每分钟15 次;离合制动器不需要频繁动作,寿命长,维护费用低,噪声低;工件质量高,废品率低;用电量节省20% 左右,对工厂电网冲击小;对模具冲击小,模具寿命长。
⑶无锡某模具制造企业(奔驰、宝马、麦格纳等企业的配套商)多工位冲压件及模具解决方案,如图4 所示。压力机选择四点多连杆2500t;偏载设计进料端公称力占60%,出料端公称力占40%;行程为800mm;工作台左右尺寸为2500mm×6200mm;采用六连杆传动形式;最高节拍为30spm;采取连续工作模式;气垫放在第一工位。
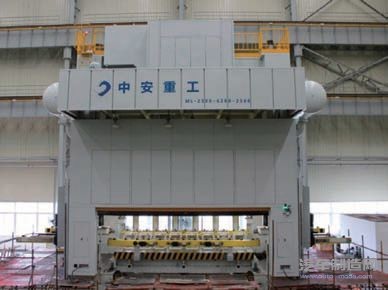
图4 2500t 多工位冲压线
生产线特点:可适用至少25 组对称型冲压件的多工位生产,产品覆盖面广,效率最高可达30spm;厂房占地面积小;设备自动化程度高,人工成本低,尤其适用于生产大批量产品。
⑷武汉某汽车零部件企业(武汉通用、神龙汽车等企业的配套商)板材落料项目解决方案,如图5所示。压力机选择四点800t 机械式压力机;行程为300mm;台面尺寸为2500mm×4600mm;生产节拍为10 ~ 60spm;自动化设备有开卷、校平、清洗涂油、伺服送料、摆剪模、电磁码垛等。
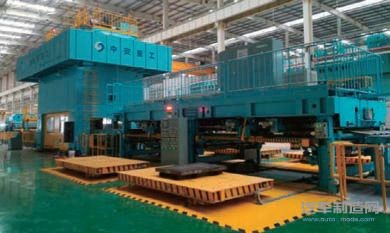
图5 四点800t 开卷落料线
生产线特点:可实现各种板材、异形料片的加工,既可以满足外板件的高标准要求,也可实现内板件的快速落料;可满足一个生产基地料片的用料需求。
原有冲压车间智能化升级改造
原有冲压车间智能化升级改造原则:旧设备的自动化改造升级,由于受到压力机本身、场地、投资等条件的限制,不同的方案,效果差异很大;方案实用性更重要。原有冲压车间智能化升级改造分以下5 种
方案。
⑴手工机械压力机线→机器人自动上下料生产模式。
⑵液压机串联生产线→机械手自动上下料生产模式。
⑶机械压力机→外挂式多工位自动生产模式。
⑷单台机械压力机→机械手自动上下料生产模式。
⑸单台液压机→机械手自动上下料生产模式。
案例分析
一汽大众成都供应商液压线自动化改造项目如图6 所示。⑴该车间生产后地板、前纵梁典型件,原设备为5 台液压机组成的生产线,工件靠手工搬运,生产效率3 次/ 分钟,改造后机械手搬运5 件/ 分钟,生产效率提高了66.7%。⑵改造前,每班15 人,⑶减少了人工搬运工件时对其表面造成的磕碰,冲压件合格率明显提高;无人工错误操作,液压机运行平稳。
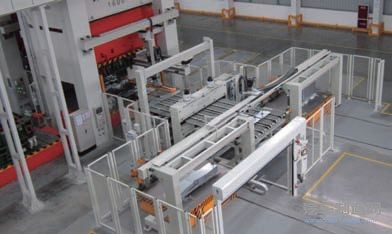
图6 液压线自动化改造项目
总结
随着冲压工艺的完善、材料的变革,企业对冲压车间智能制造的要求越来越高,工厂的智能化程度对企业利润的影响越来越大。我们在做规划时不仅要考虑现有产品的情况,也要考虑未来3 到5 年企业的发展需求。以上几种情况解析并不能涵盖所有方面,每改造后,每班3人,每年节省人工费用约180万元。一个规划还都需要根据企业自身的情况量体裁衣。
目前,我国是全球汽车产销第一大国,从2013 年以来汽车产销量一直维持在2000 万辆以上。近几年中国汽车生产基地也呈现爆炸式发展,90%的省份都有汽车企业的生产基地,而且企业新增基地数量在30% 以上,产能陆续释放。这其中一个比较重要的特点是:新增基地比较集中,车型较多,例如湖北地区除东风集团新建基地外,通用汽车、广汽集团、长丰汽车、众泰汽车等也都新建基地。以200 公里配套距离来计算,这就给所有的配套企业创造出新的发展机遇。
这种新的发展特点,对配套企业来说,变化是非常大的:
⑴生产车型较多,多家产品共线生产情况突出,对冲压生产线的兼容性要求增高;
⑵换模更加频繁,手工线、液压线越来越无法满足产能需求;
⑶企业相对集中也带来了用工难的问题,冲压工人流动性变大,配套企业面临人工成本增加的巨大压力。这些日益突出的矛盾是我们要进行冲压车间智能规划的动力所在。
智能冲压车间规划的原则和参考因素
在进行智能冲压车间规划时的原则和参考要素:
⑴产品种类导入;
⑵产能预期导入;
⑶投资及回收期导入(图1)。
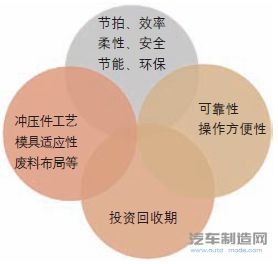
图1 参考要素叠加图
产品种类包括冲压件的工艺要求、模具适应性要求、冲压件的品种要求。产能预期要依据工厂产量测算,月产能(冲次)= 小时产量× 每日工作小时数× 每月工作日× 模具数量;月实际产能(冲次)=每分钟实际冲次×60× 每日工作时间小时数× 每月工作日× 模具数量。总投资预算包括冲压设备预算、模具预算、厂房预算、工装等辅助设备预算;年产量预估、原材料预估费用、人工成本预估费用、企业运行费用、承接产品的预期。
目前,现阶段冲压生产工艺已经日趋完善,冲压装备智能化发展迅速,可供选择的方案很多。以上三个要素综合叠加,就能找到一种最适合企业自身发展的整体规划方案。
智能冲压规划的案例浅析
新建冲压基地智能冲压规划
⑴大型覆盖件。压力机部分需要多连杆四点压力机(1 台)+ 偏心四点压力机(3 ~ 5 台);自动化部分需要机器人;整线节拍为8 ~ 12 次/ 分钟。
⑵中小型冲压件。双点快速自动化冲压线:双点压力机(4 ~ 5 台)+ 机械手,同步控制技术为15 次/ 分钟;800 ~ 3200t 多工位自动化冲压线25 ~ 30 次/ 分钟;400 ~ 1600t 级进模自动化冲压线30 ~ 60 次/ 分钟。
⑶板材备料。500 ~ 1250t 开卷落料线。
案例解析
⑴天津某汽配企业(天津一汽—大众的配套商)的大型冲压件解决方案(生产侧围、四门、两盖)。生产线采用整线湿式离合器+ 整线全防护,传输方式为机器人,六台压力机:1 台P4LS-2100+5 台P4S-1200, 中心距6500mm; 首台P4LS-2100 为八连杆、八点600t 数控液压垫、公称力行程25mm,后续P4S-1200 为偏心+ 上气垫。
压力机参数、性能和要求同天津一汽—大众冲压线相同,整线节拍低于主车厂。生产线特点:整线投资相比主车厂可降低30% ~ 50%,可实现大型冲压件的承制。
⑵宁波某汽车零部件制造(长安福特、吉利汽车等企业配套商)的中小型冲压件解决方案,如图2所示。线首部分有垛料小车+ 拆垛机械手+ 对中台+ 上料机械手;压力机部分为1 台P2S-1600+1 台P2S-1000+2 台P2S-800+1 台P2S-1000 五台双点偏心结构的机械压力机;传输部分为4 套机械手,整线节拍为15spm;线尾部分为下料机械手+ 传输皮带;整线同步功能;压力机间距为5500 ~ 6500mm。

图2 双点快速自动化冲压线
生产线特点:可实现两种生产模式,实现更多冲压产品工艺要求,既可以满足4 序生产,也可以满足5 序生产,如图3 所示。
生产模式⑴:五台压力机自动化生产;
生产模式⑵:前四台压力机自动化生产,最后一台压力机多工位生产。
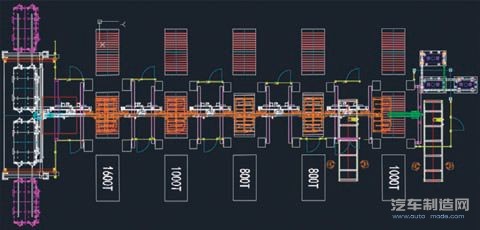
图3 冲压线布局图
机械手采用同步生产模式,效率相比手工线提高40% ~ 60%,最快节拍可达每分钟15 次;离合制动器不需要频繁动作,寿命长,维护费用低,噪声低;工件质量高,废品率低;用电量节省20% 左右,对工厂电网冲击小;对模具冲击小,模具寿命长。
⑶无锡某模具制造企业(奔驰、宝马、麦格纳等企业的配套商)多工位冲压件及模具解决方案,如图4 所示。压力机选择四点多连杆2500t;偏载设计进料端公称力占60%,出料端公称力占40%;行程为800mm;工作台左右尺寸为2500mm×6200mm;采用六连杆传动形式;最高节拍为30spm;采取连续工作模式;气垫放在第一工位。
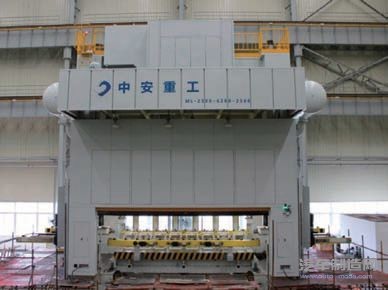
图4 2500t 多工位冲压线
生产线特点:可适用至少25 组对称型冲压件的多工位生产,产品覆盖面广,效率最高可达30spm;厂房占地面积小;设备自动化程度高,人工成本低,尤其适用于生产大批量产品。
⑷武汉某汽车零部件企业(武汉通用、神龙汽车等企业的配套商)板材落料项目解决方案,如图5所示。压力机选择四点800t 机械式压力机;行程为300mm;台面尺寸为2500mm×4600mm;生产节拍为10 ~ 60spm;自动化设备有开卷、校平、清洗涂油、伺服送料、摆剪模、电磁码垛等。
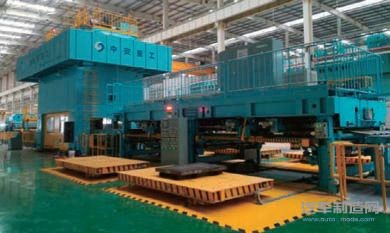
图5 四点800t 开卷落料线
生产线特点:可实现各种板材、异形料片的加工,既可以满足外板件的高标准要求,也可实现内板件的快速落料;可满足一个生产基地料片的用料需求。
原有冲压车间智能化升级改造
原有冲压车间智能化升级改造原则:旧设备的自动化改造升级,由于受到压力机本身、场地、投资等条件的限制,不同的方案,效果差异很大;方案实用性更重要。原有冲压车间智能化升级改造分以下5 种
方案。
⑴手工机械压力机线→机器人自动上下料生产模式。
⑵液压机串联生产线→机械手自动上下料生产模式。
⑶机械压力机→外挂式多工位自动生产模式。
⑷单台机械压力机→机械手自动上下料生产模式。
⑸单台液压机→机械手自动上下料生产模式。
案例分析
一汽大众成都供应商液压线自动化改造项目如图6 所示。⑴该车间生产后地板、前纵梁典型件,原设备为5 台液压机组成的生产线,工件靠手工搬运,生产效率3 次/ 分钟,改造后机械手搬运5 件/ 分钟,生产效率提高了66.7%。⑵改造前,每班15 人,⑶减少了人工搬运工件时对其表面造成的磕碰,冲压件合格率明显提高;无人工错误操作,液压机运行平稳。
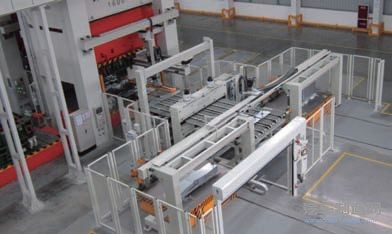
图6 液压线自动化改造项目
总结
随着冲压工艺的完善、材料的变革,企业对冲压车间智能制造的要求越来越高,工厂的智能化程度对企业利润的影响越来越大。我们在做规划时不仅要考虑现有产品的情况,也要考虑未来3 到5 年企业的发展需求。以上几种情况解析并不能涵盖所有方面,每改造后,每班3人,每年节省人工费用约180万元。一个规划还都需要根据企业自身的情况量体裁衣。
- 下一篇:汽车装配工厂更需要人而不是机器人
- 上一篇:ABB电动交通解决方案
举报 0
收藏 0
分享 116
-
舒勒与保时捷的合资智能冲压车间建设进展顺利
-
舒勒与保时捷的合资智能冲压车间将落户萨勒河畔
-
柔性化制造技术在智能冲压流水线中的应用
2018-07-18 柔性制造 -
荣成锻压承建国内最大吨位汽车整车智能冲压装备
2017-12-22 智能冲压
最新资讯
-
全球产业链聚沪 共探双碳新路径 SNEC
2025-04-18 18:05
-
柯马签订具有约束力的协议收购 Autom
2025-04-17 13:01
-
高效协同新范式:比亚迪叉车领创智能
2025-04-17 10:04
-
埃马克德国总部迎来中国社科院工业经
2025-04-15 09:40
-
埃马克这项全新应用即将在CIMT惊艳首
2025-04-15 09:37