汽车变速器那些零件的加工工艺
2018-01-25 09:26:28· 来源:金属加工
根据不同结构要求,齿轮零件加工主要工艺流程采用的是锻造制坯→正火→精车加工→插齿→倒尖角→滚齿→剃齿→(焊接)→热处理→磨加工→对啮修整。
第一部分:齿轮、轴类零件
1. 齿轮加工工艺流程
根据不同结构要求,齿轮零件加工主要工艺流程采用的是锻造制坯→正火→精车加工→插齿→倒尖角→滚齿→剃齿→(焊接)→热处理→磨加工→对啮修整。
热后齿部一般不再加工,除了主减从齿或顾客要求磨齿的零件。
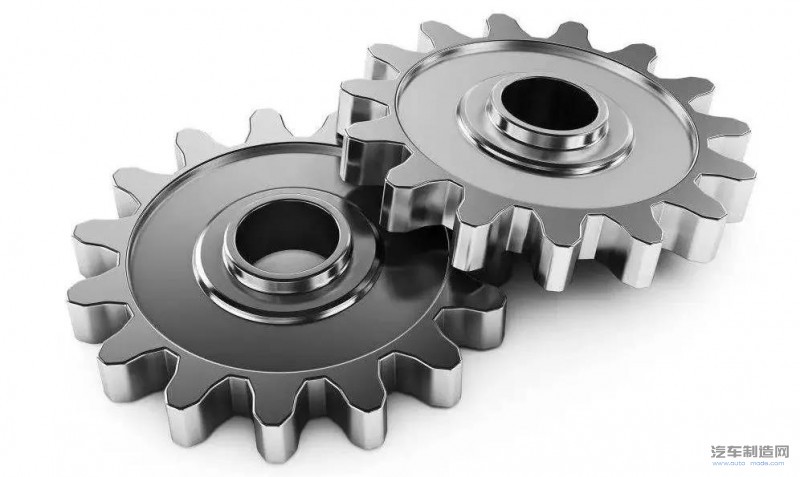
2. 轴类工艺流程
输入轴:锻造制坯→正火→精车加工→搓齿→钻孔→插齿→倒尖角→滚齿→剃齿→热处理→磨加工→对啮修整。
输出轴:锻造制坯→正火→精车加工→搓齿滚齿→剃齿→热处理→磨加工→对啮修整。
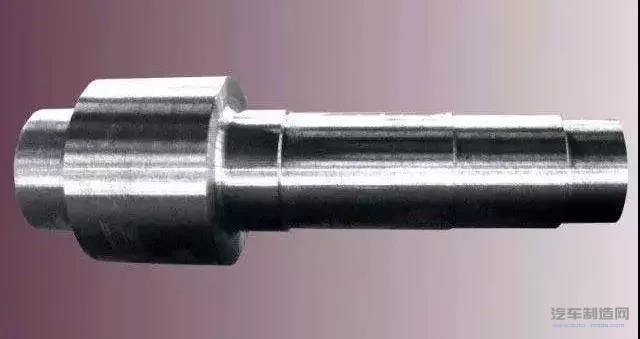
3. 具体工艺流程
(1)锻造制坯
热模锻是汽车齿轮件广泛使用的毛坯锻造工艺。以前较广泛采用的是热锻和冷挤压的毛坯,近年来,楔横轧技术在轴类加工上得到了大量推广。这项技术特别适合为比较复杂的阶梯轴类制坯,它不仅精度较高、后序加工余量小而且生产效率高。
(2)正火
这一工艺的目的是获得适合后序齿轮切削加工的硬度和为最终热处理做组织准备,以有效地减少热处理变形。一般的正火由于受人员、设备和环境的影响比较大,使得工件冷却速度和冷却的均匀性难以控制,造成硬度散差大,金相组织不均匀,直接影响机加工和最终热处理。
(3)精车加工
为了满足高精度齿轮加工的定位要求.齿坯的精车加工全部采用数控车床。齿轮先进行内孔和定位端面的加工,然后另一端面及外径加工同步完成。既保证了内孔与定位端面的垂直度要求,又保证了大批量齿坯生产的尺寸离散小。从而提高了齿坯精度,确保了后序齿轮的加工质量。
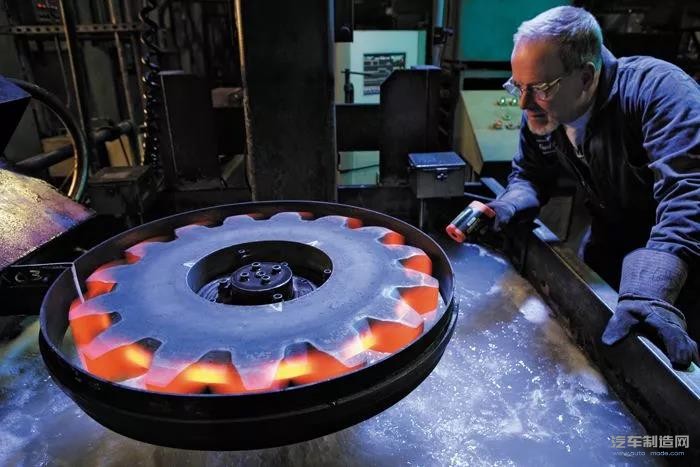
轴类零件加工的定位基准和装夹主要有以下三种方式:
1.以工件的中心孔定位:在轴的加工中,零件各外圆表面、端面的同轴度,端面对旋转轴线的垂直度是其相互位置精度的主要项目,这些表面的设计基准一般都是轴的中心线,若用两中心孔定位,符合基准重合的原则。
2.以外圆和中心孔作为定位基准(一夹一顶):用两中心孔定位虽然定心精度高,但刚性差,尤其是加工较重的工件时不够稳固,切削用量也不能太大。粗加工时,为了提高零件的刚度,可采用轴的外圆表面和一中心孔作为定位基准来加工。这种定位方法能承受较大的切削力矩,是轴类零件最常见的一种定位方法。
3.以两外圆表面作为定位基准:在加工空心轴的内孔时,(例如:机床上莫氏锥度的内孔加工),不能采用中心孔作为定位基准,可用轴的两外圆表面作为定位基准。当工件是机床主轴时,常以两支撑轴颈(装配基准)为定位基准,可保证锥孔相对支撑轴颈的同轴度要求,消除基准不重合而引起的误差。
第二部分:壳体类零件
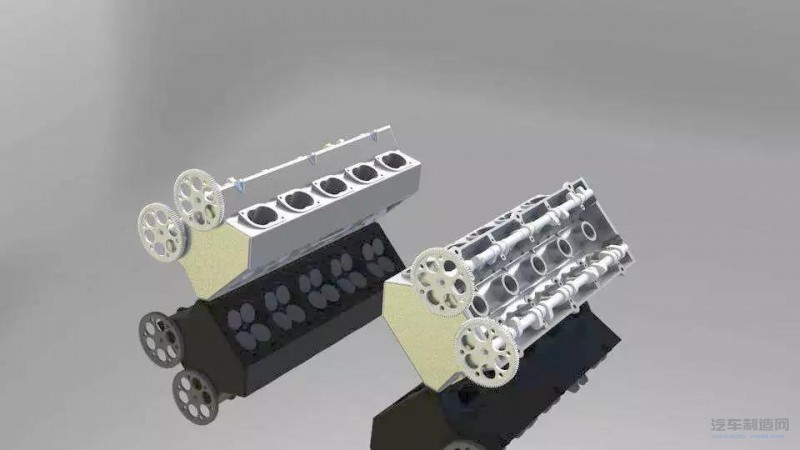
1. 工艺流程
一般工艺流程是铣结合面→加工工艺孔和连接孔→粗镗轴承孔→精镗轴承孔和定位销孔→清洗→泄漏试验检测。
2. 控制方法
(1)夹具方面
变速器壳体的加工工序以采用“立式加工中心加工。10#工序+立式式加工中心加工 20#工序+卧式加工中心加工 30#工序”为例,需要三套加工中心夹具,避免工件的夹紧变形,还要考虑刀具干涉、操作灵活、多件一夹、快速切换等因素。
(2)刀具方面
在汽车零部件制造成本中,刀具成本占总成本的3%~5%。模块式结构的复合刀具具有精度较高,刀柄可重复使用,库存量少等特点,被广泛采用,它可以大幅度缩短加工时间,提高劳动效率。因此,在精度要求不高、标准刀具能够达到比较好的加工效果时尽量采用标准刀具,降低库存,提高互换性。同时,对于大批量生产的零件,精度要求又高的零件采用先进的非非标复合刀具更能提高加工精度和生产效率。
1. 齿轮加工工艺流程
根据不同结构要求,齿轮零件加工主要工艺流程采用的是锻造制坯→正火→精车加工→插齿→倒尖角→滚齿→剃齿→(焊接)→热处理→磨加工→对啮修整。
热后齿部一般不再加工,除了主减从齿或顾客要求磨齿的零件。
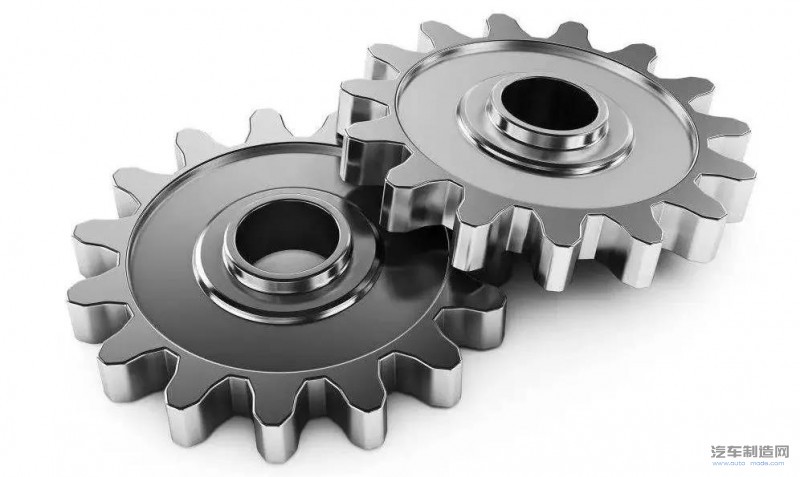
2. 轴类工艺流程
输入轴:锻造制坯→正火→精车加工→搓齿→钻孔→插齿→倒尖角→滚齿→剃齿→热处理→磨加工→对啮修整。
输出轴:锻造制坯→正火→精车加工→搓齿滚齿→剃齿→热处理→磨加工→对啮修整。
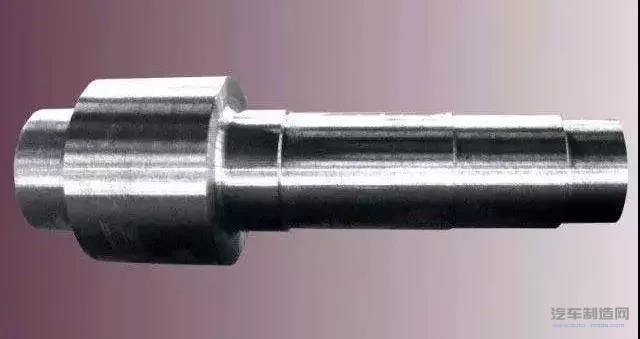
3. 具体工艺流程
(1)锻造制坯
热模锻是汽车齿轮件广泛使用的毛坯锻造工艺。以前较广泛采用的是热锻和冷挤压的毛坯,近年来,楔横轧技术在轴类加工上得到了大量推广。这项技术特别适合为比较复杂的阶梯轴类制坯,它不仅精度较高、后序加工余量小而且生产效率高。
(2)正火
这一工艺的目的是获得适合后序齿轮切削加工的硬度和为最终热处理做组织准备,以有效地减少热处理变形。一般的正火由于受人员、设备和环境的影响比较大,使得工件冷却速度和冷却的均匀性难以控制,造成硬度散差大,金相组织不均匀,直接影响机加工和最终热处理。
(3)精车加工
为了满足高精度齿轮加工的定位要求.齿坯的精车加工全部采用数控车床。齿轮先进行内孔和定位端面的加工,然后另一端面及外径加工同步完成。既保证了内孔与定位端面的垂直度要求,又保证了大批量齿坯生产的尺寸离散小。从而提高了齿坯精度,确保了后序齿轮的加工质量。
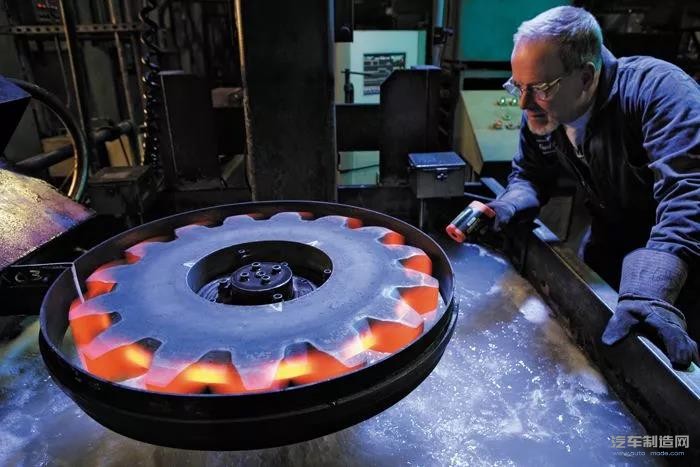
轴类零件加工的定位基准和装夹主要有以下三种方式:
1.以工件的中心孔定位:在轴的加工中,零件各外圆表面、端面的同轴度,端面对旋转轴线的垂直度是其相互位置精度的主要项目,这些表面的设计基准一般都是轴的中心线,若用两中心孔定位,符合基准重合的原则。
2.以外圆和中心孔作为定位基准(一夹一顶):用两中心孔定位虽然定心精度高,但刚性差,尤其是加工较重的工件时不够稳固,切削用量也不能太大。粗加工时,为了提高零件的刚度,可采用轴的外圆表面和一中心孔作为定位基准来加工。这种定位方法能承受较大的切削力矩,是轴类零件最常见的一种定位方法。
3.以两外圆表面作为定位基准:在加工空心轴的内孔时,(例如:机床上莫氏锥度的内孔加工),不能采用中心孔作为定位基准,可用轴的两外圆表面作为定位基准。当工件是机床主轴时,常以两支撑轴颈(装配基准)为定位基准,可保证锥孔相对支撑轴颈的同轴度要求,消除基准不重合而引起的误差。
第二部分:壳体类零件
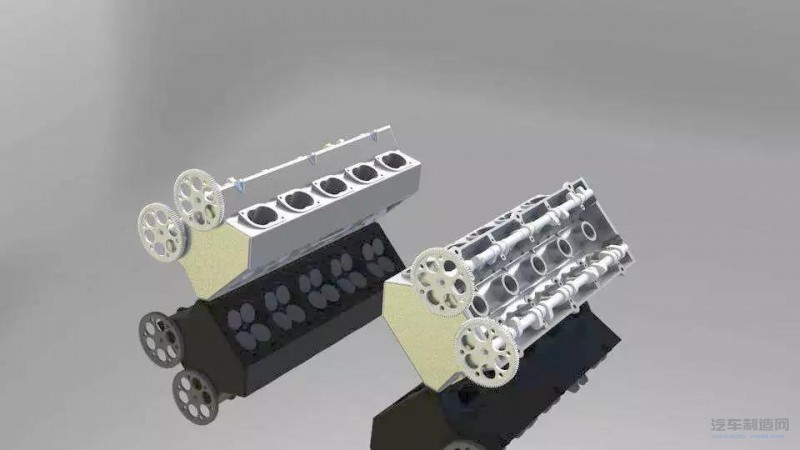
1. 工艺流程
一般工艺流程是铣结合面→加工工艺孔和连接孔→粗镗轴承孔→精镗轴承孔和定位销孔→清洗→泄漏试验检测。
2. 控制方法
(1)夹具方面
变速器壳体的加工工序以采用“立式加工中心加工。10#工序+立式式加工中心加工 20#工序+卧式加工中心加工 30#工序”为例,需要三套加工中心夹具,避免工件的夹紧变形,还要考虑刀具干涉、操作灵活、多件一夹、快速切换等因素。
(2)刀具方面
在汽车零部件制造成本中,刀具成本占总成本的3%~5%。模块式结构的复合刀具具有精度较高,刀柄可重复使用,库存量少等特点,被广泛采用,它可以大幅度缩短加工时间,提高劳动效率。因此,在精度要求不高、标准刀具能够达到比较好的加工效果时尽量采用标准刀具,降低库存,提高互换性。同时,对于大批量生产的零件,精度要求又高的零件采用先进的非非标复合刀具更能提高加工精度和生产效率。
编辑推荐
最新资讯
-
“锂”想万家——比亚迪叉车在家电行
2025-04-28 10:02
-
全球工业数字化领袖齐聚申城,共绘智
2025-04-28 08:28
-
思看科技受邀出席第三届联合国教科文
2025-04-27 13:29
-
聚势谋远,智领新程——五菱柳机以硬
2025-04-27 13:22
-
聚势求新、智驱未来——五菱工业底盘
2025-04-27 13:22