简单分析汽车用钢板电阻点焊工艺参数优化选择
2018-01-26 17:32:24· 来源:焊接技术
电阻点焊是汽车制造行业中最普遍的连接方式。微型汽车车身共有5000多个焊点,分布在车身地板、顶盖、前车体等部位,在发生碰撞时不同区域承担了吸能、连接、承托等功能。
摘要:焊装车间多采用多层板搭接进行电阻电焊,而电阻电焊过程的不确定因素较多。为了用较少的试验次数得到满足生产要求的试验结果,以板厚0.8mm+1.4mm+1.8mm的三层低碳钢板搭接为研究对象,分析各因素对多层板材搭接焊点熔核质量的影响,获得了最优焊接工艺参数。试验结果表明:板厚为0.8mm+1.4mm+1.8mm的三层低碳钢板搭接最佳焊接工艺参数为多脉冲软规范焊接参数,即三周波,焊接电流8.8/11.1/9.6kA、焊接时间5/19/5cyc、电极压力3kN,得到各层搭接板之间熔核直径大于等于Φ6mm.
前言
电阻点焊是汽车制造行业中最普遍的连接方式。微型汽车车身共有5000多个焊点,分布在车身地板、顶盖、前车体等部位,在发生碰撞时不同区域承担了吸能、连接、承托等功能。
实际应用中需要将不同厚度、材料的钢板进行点焊连接,同一工位会出现不同强度、厚度的两层板或三层板搭接,目前的电阻点焊工艺参数很难适用于不同厚度的两层/三层钢板的连接.
在此以五菱宏光S生产线前车体区域 1 # 工位(该工位焊接左前大梁焊合件与前围板焊合总成搭接)为研究对象,为五菱宏光S车型的不同搭接方式电阻点焊工艺参数优化选择提供新的思路和方法。
1试验材料和方法
采用小原品牌一体式电阻点焊机(型号ST21)额定功率180kV A,配套X型手工焊枪 (型号UXH-C9625) 进行焊接,如图1所示。
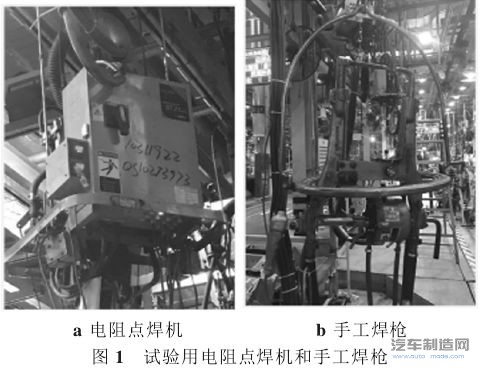
左前大梁和前围板零件材料均为宝钢牌号BLD低碳钢板,试验用钢板的化学成分如表1所示。
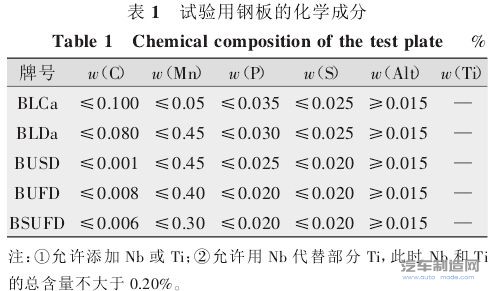
前大梁与前围板搭接共11个焊点,其中:两层板搭接焊点10个,板厚0.8mm+1.2mm;三层板搭接焊点1个,板厚0.8mm+1.4mm+1.8mm。
首先选择同样汽车用钢、厚度的试片模拟三层板搭接,使用不同的焊接工艺参数在三层板试片上进行测试,获取不同板厚下的工艺参数,以确定符合技术要求的焊接工艺参数。
然后在左前大梁和前围板连接区域进行验证,获得最终的工艺参数。根据搭接零件的主导板厚,参照《上汽通用五菱电阻点焊焊接参数推荐值》选择试验用电阻点焊工艺参数。电阻点焊初始工艺参数如表2所示。
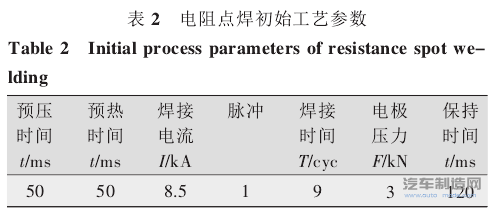
2 试验结果分析
2.1初始焊接工艺参数对焊接的影响
使用板材、厚度、工艺一致的3块试片(0.8mm+1.4mm+1.8mm),根据表2的焊接工艺参数,选择电流8.5kA、电极压力3kN、焊接时间9cyc进行电阻点焊测试。焊点熔核尺寸如图2所示。
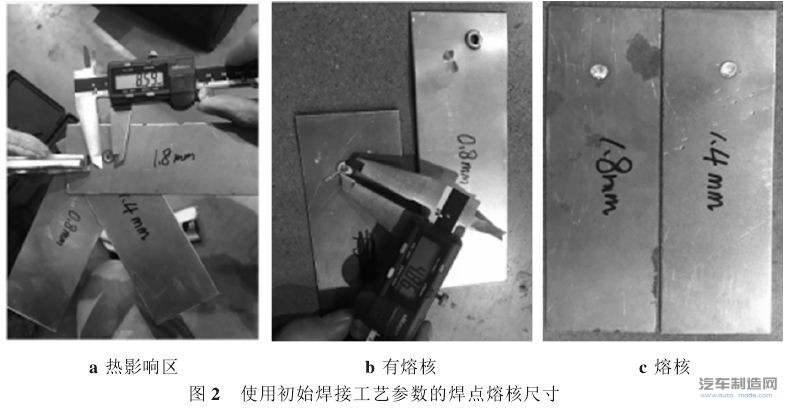
用游标卡尺测量焊点热影响区大小为8.59mm(见图2a);将焊接试片撕裂后,0.8mm+1.4mm板材搭接处存在焊接熔核,熔核尺寸为4.86mm(见图2b);但1.4mm+1.8mm板材搭接处未形成熔核,撕裂后焊点脆断表面呈颗粒状态(见图2c).
试验结果表明,初始焊接工艺参数不适用于现场实际搭接状态,需要逐一调整焊接工艺参数,使三层板材焊接均有符合要求的焊点熔核。
2.2左前大梁和前围板连接区域点焊试验
影响试片焊点熔核尺寸的主要因素有焊接电流、焊接时间、电极压力和脉冲,其他参数保持不变。本试验电极采用球形电极帽,端面尺寸Φ7mm,采取逐一对比方式进行试验,焊接工艺参数见表3.
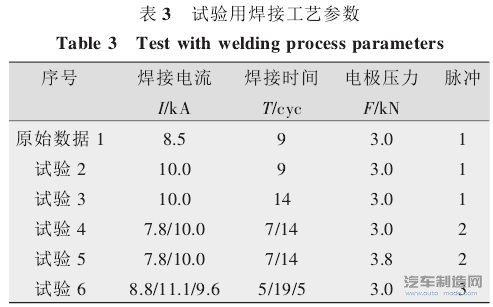
(1) 试验2。保持焊接时间和电极压力不变,增加焊接电流至10.0kA(见表3)。试验2的熔核尺寸如图3所示,将焊接试片撕裂后,0.8mm+1.4mm板材搭接处存在焊接熔核,尺寸Φ5.69mm,如图3a所示;但1.4mm+1.8mm板材搭接处未形成熔核,撕裂后焊点脆断表面呈颗粒状态如图3b所示。
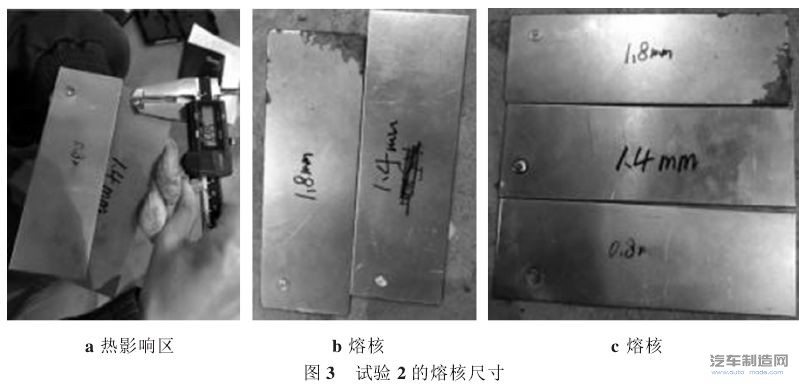
(2) 试验3。保持焊接电流为10.0kA,增加焊接时间到14cyc,电极压力保持3.0kN(见表3)。试验3的熔核尺寸如图4所示,将焊接试片撕裂后,0.8mm+1.4mm板材搭接处存在熔核,但1.4mm+1.8mm板材搭接处仍未形成熔核,且焊点脆断表明呈颗粒状态,如图4c所示。由于该板材三层板材厚度差异较大,焊接参数单项逐步增加已无法得到符合标准的焊点熔核,考虑选用2个焊接脉冲来增加焊接前的预热焊接。
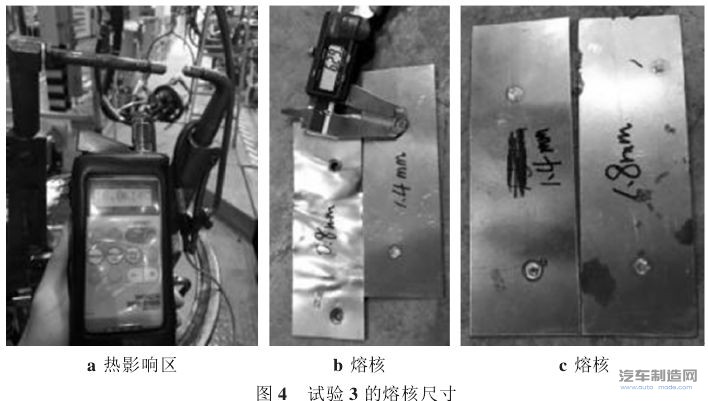
(3) 试验4。在前3个试验验证结果的基础上,选用双脉冲进行试验。第一脉冲:焊接电流7.8kA焊接时间7cyc;第二脉冲:焊接电流10.0kA,焊接时间14cyc,电极压力3.0kN保持不变(见表3)。焊接完成后,焊点热影响区明显变大,直径为Φ9.6mm,如图Sa所示;将焊接试片撕裂后,0.8mm+1.4mm板材搭接处存在焊接熔核,熔核尺寸为6.05mm,如图5b所示;1.4mm+1.8mm板材搭接处未形成熔核,焊点脆断表明呈颗粒状态,但承受剪切应力明显大
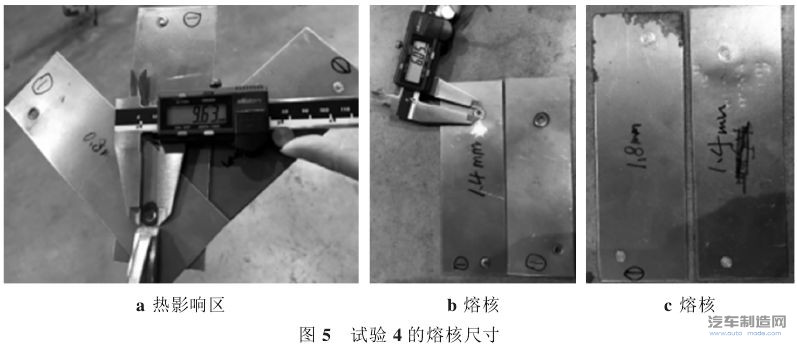
(4) 试验5。在试验4的基础上,焊接电流、焊接时间保持不变,增加电极压力至3.8kN进行焊接试片验证(见表3)。焊点热影响区尺寸Φ10.75mm已达到标准上限值,如图6a所示;撕裂焊点后,0.8mm+1.4mm板材搭接处存在熔核且增大至Φ6.13mm,如图5b所示;但1.4mm+1.8mm板材搭接处仍未形成明显熔核,如图5b所示;如果再单独增加焊接电流、焊接时间或电极压力,很难再产生明显效果,且焊点热影响区存在过烧风险。

(5)试验6。在试验5的基础上,考虑到本工位焊点数量及生产节拍要求,选择焊接参数中常用的软规范,增大为三脉冲焊接参数,增加了主焊接前的预热过程和主焊接后的熔核保持过程(见表3)第1脉冲:焊接电流8.8kA,焊接时间5cyc;第2脉冲:焊接电流11.1kA,焊接时间19cyc;第3脉冲:焊接电流9.6kA,焊接时间5cyc;电极压力保持为3.0kN。撕裂焊点后,0.8mm+1.4mm板材搭接存在焊接熔核,测量熔核尺寸为Φ6.19mm,如图7a所示;
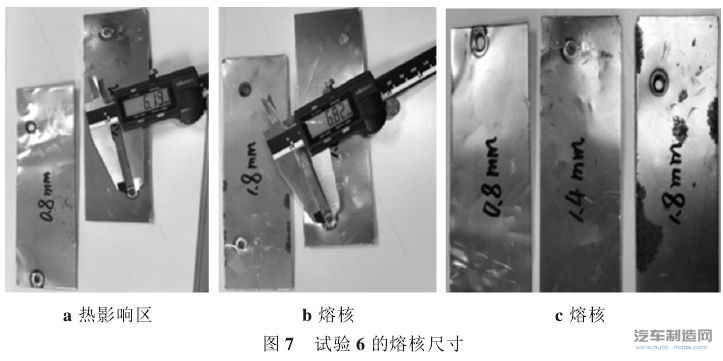
1.4mm+1.8mm板材搭接处存在明显焊接熔核,熔核尺寸为Φ6.82mm,如图7b,所示;在中间Φ侧板材(1.4mm厚度)两侧均有明显熔核,两侧板材(0.8mm和1.8mm厚度)存在明显焊点撕裂的孔洞,如图7c所示。板材焊点熔核质量合格。
所有零件搭接实际工况均比焊接试片情况复杂,采取试验6数据在实车上进行焊接实验,用铁锤和凿子在三层板焊点处(0.8mm+1.4mm+1.8mm)进行非破坏实验,上下扳动凿子30°,焊点位置未发现虚焊,饭金表面无毛刺和裂纹,实车非破坏焊点质量合格,如图8所示。
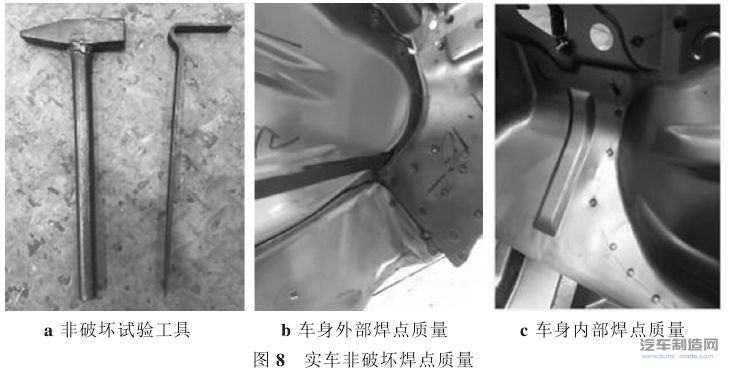
根据上汽通用五菱公司电阻点焊质量要求,定期对该车型前车体区域焊点进行全破坏实验,大梁焊点两侧均有焊点熔核,两侧板材出现拉裂孔洞,焊点质量合格,如图9所示。
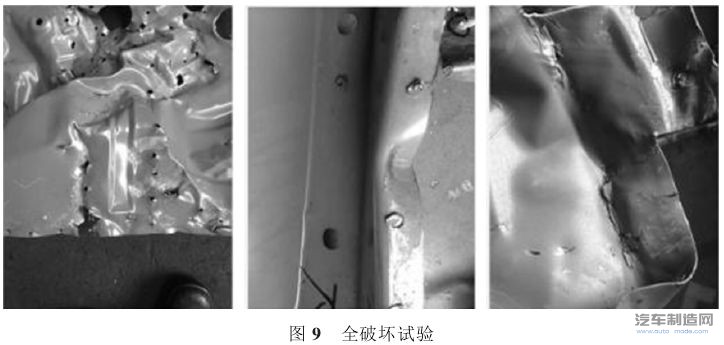
总 结
(1)获得脉冲为1,2,3的电阻点焊熔核尺寸情况,综合考虑三脉冲焊接参数为:焊接电流8.8/11.1/9.6kA、焊接时间5/19/5cyc、电极压力3kN,获得的各层搭接板之间熔核直径大于等于6mm,适用于0.8mm+1.4mm+1.8mm厚度差异大的板材搭接点焊。
(二)以左前大梁和前围板搭接为例,阐述了在两层板与三层板搭接时,应优先选择适用于三层板搭接的焊接工艺参数,解决了板材搭接的焊点熔核问题,为其他汽车生产企业提供一种新的思路及方法。
前言
电阻点焊是汽车制造行业中最普遍的连接方式。微型汽车车身共有5000多个焊点,分布在车身地板、顶盖、前车体等部位,在发生碰撞时不同区域承担了吸能、连接、承托等功能。
实际应用中需要将不同厚度、材料的钢板进行点焊连接,同一工位会出现不同强度、厚度的两层板或三层板搭接,目前的电阻点焊工艺参数很难适用于不同厚度的两层/三层钢板的连接.
在此以五菱宏光S生产线前车体区域 1 # 工位(该工位焊接左前大梁焊合件与前围板焊合总成搭接)为研究对象,为五菱宏光S车型的不同搭接方式电阻点焊工艺参数优化选择提供新的思路和方法。
1试验材料和方法
采用小原品牌一体式电阻点焊机(型号ST21)额定功率180kV A,配套X型手工焊枪 (型号UXH-C9625) 进行焊接,如图1所示。
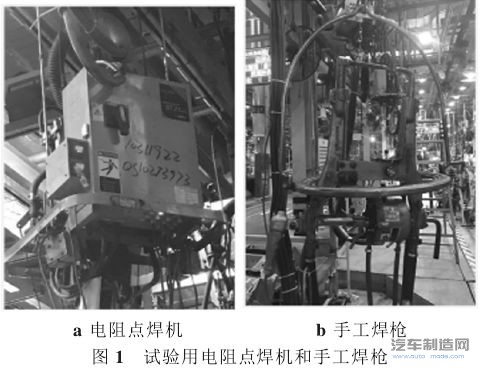
左前大梁和前围板零件材料均为宝钢牌号BLD低碳钢板,试验用钢板的化学成分如表1所示。
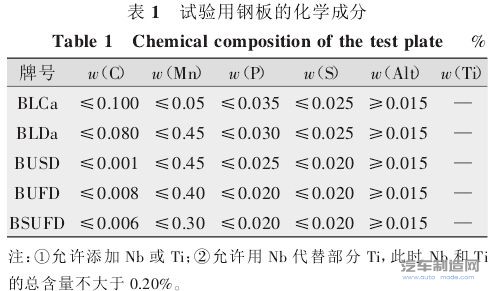
前大梁与前围板搭接共11个焊点,其中:两层板搭接焊点10个,板厚0.8mm+1.2mm;三层板搭接焊点1个,板厚0.8mm+1.4mm+1.8mm。
首先选择同样汽车用钢、厚度的试片模拟三层板搭接,使用不同的焊接工艺参数在三层板试片上进行测试,获取不同板厚下的工艺参数,以确定符合技术要求的焊接工艺参数。
然后在左前大梁和前围板连接区域进行验证,获得最终的工艺参数。根据搭接零件的主导板厚,参照《上汽通用五菱电阻点焊焊接参数推荐值》选择试验用电阻点焊工艺参数。电阻点焊初始工艺参数如表2所示。
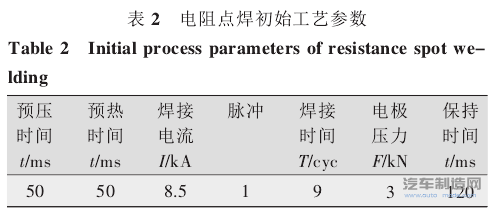
2 试验结果分析
2.1初始焊接工艺参数对焊接的影响
使用板材、厚度、工艺一致的3块试片(0.8mm+1.4mm+1.8mm),根据表2的焊接工艺参数,选择电流8.5kA、电极压力3kN、焊接时间9cyc进行电阻点焊测试。焊点熔核尺寸如图2所示。
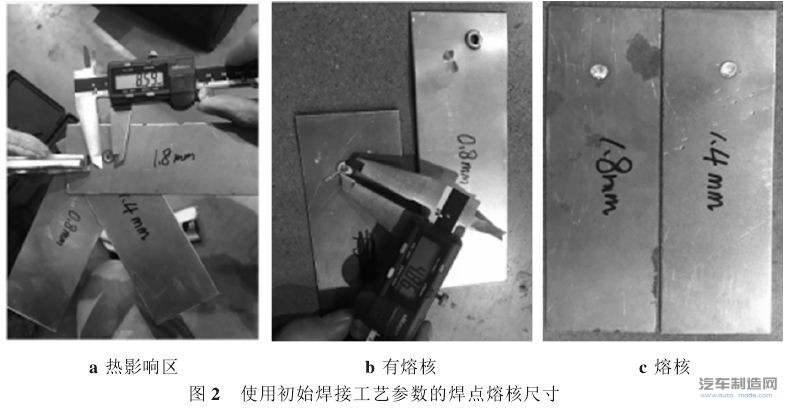
用游标卡尺测量焊点热影响区大小为8.59mm(见图2a);将焊接试片撕裂后,0.8mm+1.4mm板材搭接处存在焊接熔核,熔核尺寸为4.86mm(见图2b);但1.4mm+1.8mm板材搭接处未形成熔核,撕裂后焊点脆断表面呈颗粒状态(见图2c).
试验结果表明,初始焊接工艺参数不适用于现场实际搭接状态,需要逐一调整焊接工艺参数,使三层板材焊接均有符合要求的焊点熔核。
2.2左前大梁和前围板连接区域点焊试验
影响试片焊点熔核尺寸的主要因素有焊接电流、焊接时间、电极压力和脉冲,其他参数保持不变。本试验电极采用球形电极帽,端面尺寸Φ7mm,采取逐一对比方式进行试验,焊接工艺参数见表3.
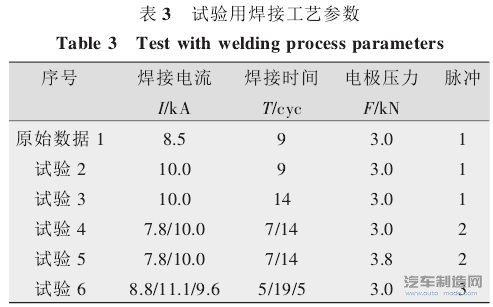
(1) 试验2。保持焊接时间和电极压力不变,增加焊接电流至10.0kA(见表3)。试验2的熔核尺寸如图3所示,将焊接试片撕裂后,0.8mm+1.4mm板材搭接处存在焊接熔核,尺寸Φ5.69mm,如图3a所示;但1.4mm+1.8mm板材搭接处未形成熔核,撕裂后焊点脆断表面呈颗粒状态如图3b所示。
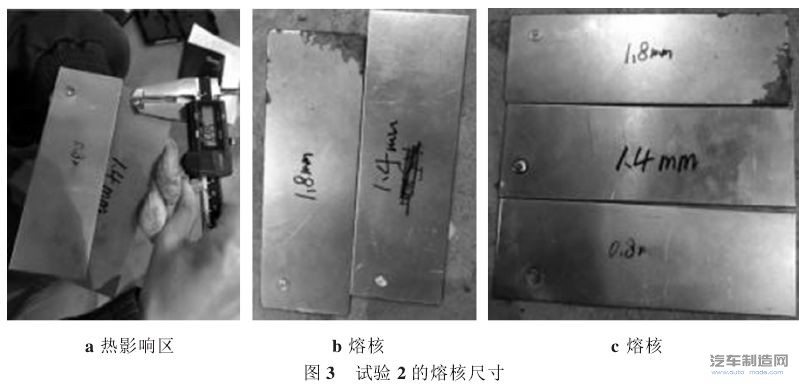
(2) 试验3。保持焊接电流为10.0kA,增加焊接时间到14cyc,电极压力保持3.0kN(见表3)。试验3的熔核尺寸如图4所示,将焊接试片撕裂后,0.8mm+1.4mm板材搭接处存在熔核,但1.4mm+1.8mm板材搭接处仍未形成熔核,且焊点脆断表明呈颗粒状态,如图4c所示。由于该板材三层板材厚度差异较大,焊接参数单项逐步增加已无法得到符合标准的焊点熔核,考虑选用2个焊接脉冲来增加焊接前的预热焊接。
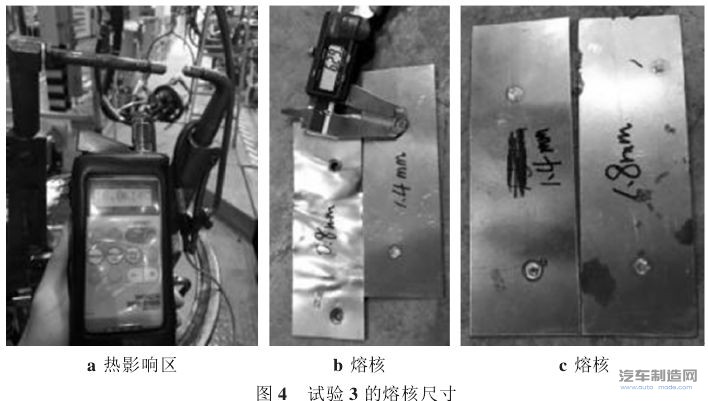
(3) 试验4。在前3个试验验证结果的基础上,选用双脉冲进行试验。第一脉冲:焊接电流7.8kA焊接时间7cyc;第二脉冲:焊接电流10.0kA,焊接时间14cyc,电极压力3.0kN保持不变(见表3)。焊接完成后,焊点热影响区明显变大,直径为Φ9.6mm,如图Sa所示;将焊接试片撕裂后,0.8mm+1.4mm板材搭接处存在焊接熔核,熔核尺寸为6.05mm,如图5b所示;1.4mm+1.8mm板材搭接处未形成熔核,焊点脆断表明呈颗粒状态,但承受剪切应力明显大
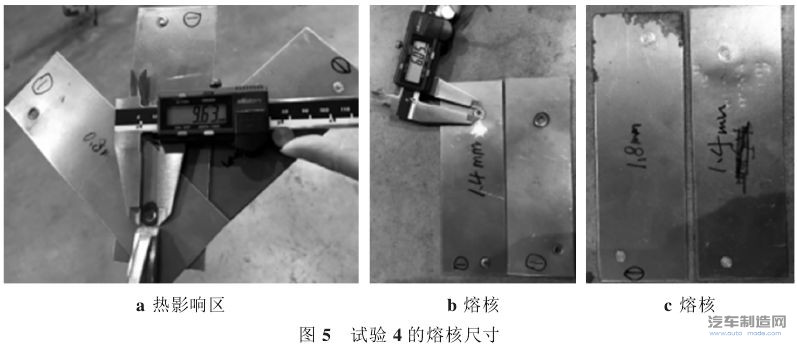
(4) 试验5。在试验4的基础上,焊接电流、焊接时间保持不变,增加电极压力至3.8kN进行焊接试片验证(见表3)。焊点热影响区尺寸Φ10.75mm已达到标准上限值,如图6a所示;撕裂焊点后,0.8mm+1.4mm板材搭接处存在熔核且增大至Φ6.13mm,如图5b所示;但1.4mm+1.8mm板材搭接处仍未形成明显熔核,如图5b所示;如果再单独增加焊接电流、焊接时间或电极压力,很难再产生明显效果,且焊点热影响区存在过烧风险。

(5)试验6。在试验5的基础上,考虑到本工位焊点数量及生产节拍要求,选择焊接参数中常用的软规范,增大为三脉冲焊接参数,增加了主焊接前的预热过程和主焊接后的熔核保持过程(见表3)第1脉冲:焊接电流8.8kA,焊接时间5cyc;第2脉冲:焊接电流11.1kA,焊接时间19cyc;第3脉冲:焊接电流9.6kA,焊接时间5cyc;电极压力保持为3.0kN。撕裂焊点后,0.8mm+1.4mm板材搭接存在焊接熔核,测量熔核尺寸为Φ6.19mm,如图7a所示;
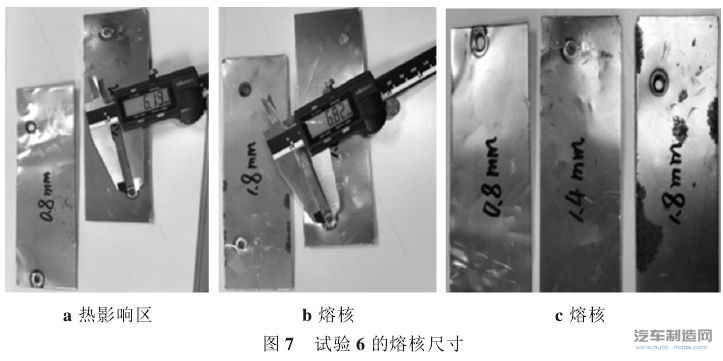
1.4mm+1.8mm板材搭接处存在明显焊接熔核,熔核尺寸为Φ6.82mm,如图7b,所示;在中间Φ侧板材(1.4mm厚度)两侧均有明显熔核,两侧板材(0.8mm和1.8mm厚度)存在明显焊点撕裂的孔洞,如图7c所示。板材焊点熔核质量合格。
所有零件搭接实际工况均比焊接试片情况复杂,采取试验6数据在实车上进行焊接实验,用铁锤和凿子在三层板焊点处(0.8mm+1.4mm+1.8mm)进行非破坏实验,上下扳动凿子30°,焊点位置未发现虚焊,饭金表面无毛刺和裂纹,实车非破坏焊点质量合格,如图8所示。
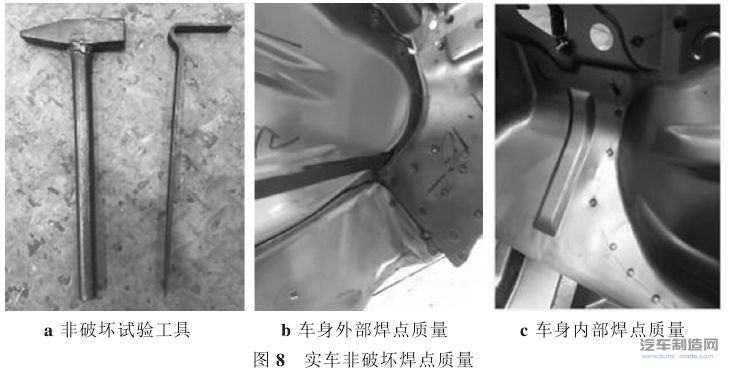
根据上汽通用五菱公司电阻点焊质量要求,定期对该车型前车体区域焊点进行全破坏实验,大梁焊点两侧均有焊点熔核,两侧板材出现拉裂孔洞,焊点质量合格,如图9所示。
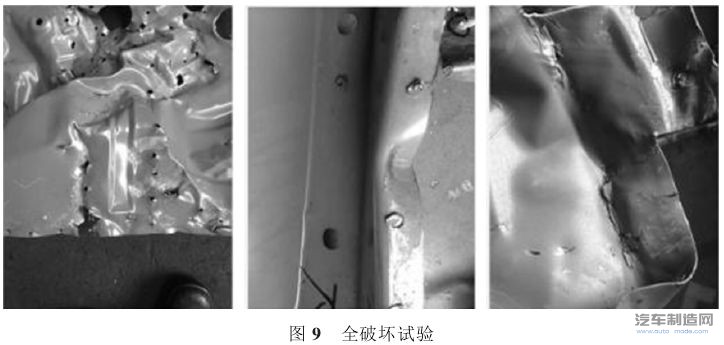
总 结
(1)获得脉冲为1,2,3的电阻点焊熔核尺寸情况,综合考虑三脉冲焊接参数为:焊接电流8.8/11.1/9.6kA、焊接时间5/19/5cyc、电极压力3kN,获得的各层搭接板之间熔核直径大于等于6mm,适用于0.8mm+1.4mm+1.8mm厚度差异大的板材搭接点焊。
(二)以左前大梁和前围板搭接为例,阐述了在两层板与三层板搭接时,应优先选择适用于三层板搭接的焊接工艺参数,解决了板材搭接的焊点熔核问题,为其他汽车生产企业提供一种新的思路及方法。
编辑推荐
最新资讯
-
全球产业链聚沪 共探双碳新路径 SNEC
2025-04-18 18:05
-
柯马签订具有约束力的协议收购 Autom
2025-04-17 13:01
-
高效协同新范式:比亚迪叉车领创智能
2025-04-17 10:04
-
埃马克德国总部迎来中国社科院工业经
2025-04-15 09:40
-
埃马克这项全新应用即将在CIMT惊艳首
2025-04-15 09:37