基于DEFORM的直齿锥齿轮复合锻造冷整成形
2018-02-08 15:41:28· 来源:锻造与冲压
齿轮是传动系统和转向系统的关键核心零件,如何改善优化齿轮性能得到越来越多研究学者的关注。传统的齿轮加工方法为切削加工和锻造,相比切削加工锻造可获得完整的金属流线、更优的材料组织和性能,获得更可靠更安全和使用寿命更长的齿轮产品。
齿轮是传动系统和转向系统的关键核心零件,如何改善优化齿轮性能得到越来越多研究学者的关注。传统的齿轮加工方法为切削加工和锻造,相比切削加工锻造可获得完整的金属流线、更优的材料组织和性能,获得更可靠更安全和使用寿命更长的齿轮产品。虽然热精锻加工精度高,但是加工时由于高温易发生氧化作用,影响工件的表面精度和表面质量。近年来,热锻冷整复合加工工艺不仅具备热锻工艺的优势,获得具备完整流线的工件,还可减小中间成形步,降低成形载荷,冷整工序可保证工件的尺寸精度和表面质量,提高齿轮的使用寿命,是齿轮复合锻造成形工艺中重要的一环。因此有必要对冷整成形工艺进行优化设计,以保证最佳成形质量。
随着计算机技术的不断发展,实际生产中,为优化产品工艺、减小生产周期、降低生产成本,数值模拟方法得到广泛应用。本文基于热锻冷整复合加工工艺,利用DEFORM软件对直齿锥齿轮复合锻造冷整工序进行数值模拟,提出优化方案并进行成形验证,对直齿锥齿轮复合锻造成形工艺设计具有指导意义。
有限元模型及模拟方案
有限元模型的建立
本文基于热锻冷整成形工艺,模拟工序为热锻后的冷整工序。选取两个不同齿高、齿厚的直齿锥齿轮热锻成形件,运用Pro/E建立直齿锥齿轮与上下模具的三维模型,并保存为stl文件导入DEFORM软件进行有限元数值模拟。图1为直齿锥齿轮热锻成形件示意图,图2为模具的有限元数值模拟模型。
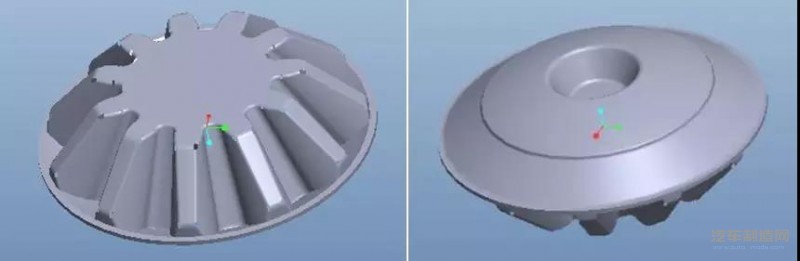
图1 直齿锥齿轮热锻件示意图
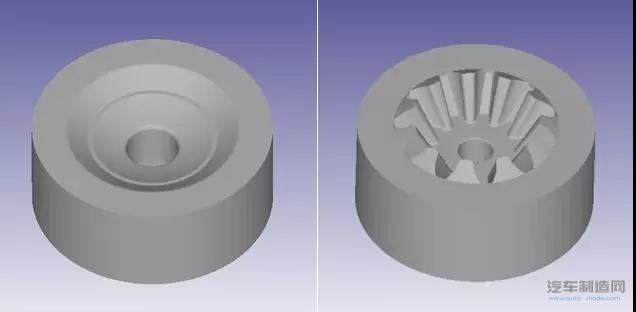
图2 模具有限元模拟模型
模拟参数设置
热锻件/冷整成形件尺寸对比和模拟参数设置如表1所示。
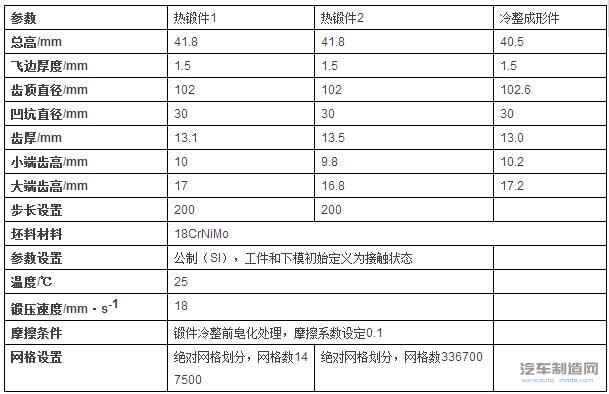
有限元数值模拟结果与分析
成形载荷分析
图3为不同热锻件尺寸冷整时上模对应的行程载荷,二者行程载荷相差较大。这是由于热锻件1齿厚较小、齿高较高,冷整时直齿锥齿轮齿顶和齿根区域先于齿面区域与上模发生并保持接触,材料流动所受阻力增加且材料变形范围小,齿顶、齿根区域承受的作用力大,齿面受力较小。热锻件2由于减小了齿高增大了齿厚,齿面先于齿顶与上模发生接触作用,直齿锥齿轮可自由流动材料增加且变形范围扩大,有效降低了成形载荷。
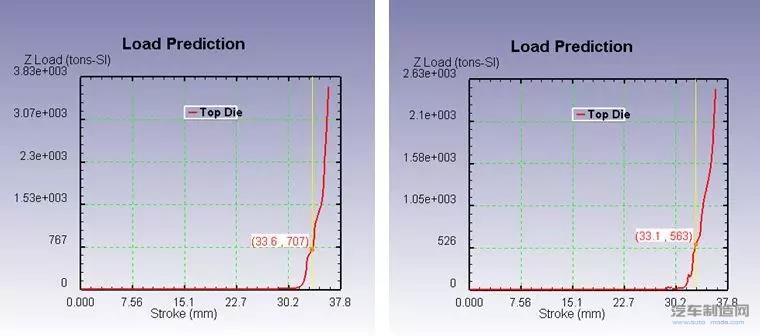
(a)热锻件1冷整成形载荷曲线 (b)热锻件2冷整成形载荷曲线
图3 上模载荷行程曲线
金属流动速度场分析
图4为不同齿高、齿厚热锻件冷整工序最终材料流动情况。图4(a)为高齿高薄齿厚的热锻件1,上模下行,与工件发生接触并发生挤压,从而使齿面材料向齿顶流动,因此齿顶存在一定的速度场;下模与工件始终处于接触阶段,在冷整过程中材料流动受到下模限制,其向飞边区域以及工件底部流动;最大流动速度在工件底部区域,为40mm/s。图4(b)为齿高减小0.2mm、齿厚增加0.4mm的热锻成形件,由于齿厚增加,工件受到上模的挤压作用,齿面材料向齿顶流动,因此齿顶存在材料流动速度场,且齿面平均流动速度比热锻件1增加了约1.5倍,齿面冷整效果良好;由于冷整过程中下模与工件始终接触,其材料流动受下模的限制作用,所以材料向飞边区域和工件底部流动;最大流动速度在工件底部区域。工件减小齿高、增加齿厚后最大材料流动速度减小,可能原因是上模与工件接触后,工件齿面发生的形变增大,齿顶面受到的挤压力变小,导致工件底部受到的挤压力减小,底部材料流动速度减小。
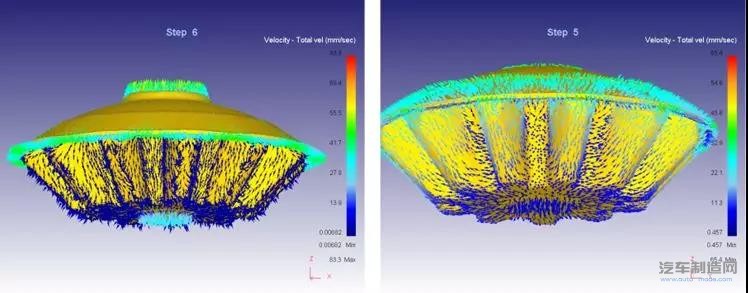
(a)热锻件1冷整工序材料流动速度场 (b)热锻件2材料流动速度场
图4 材料流动速度场
应力应变分析
热锻件1和热锻件2最终成形对应的应力、应变图如图5、图6所示。通过对比可知,随着变形的完成,热锻件1最大应力为834MPa,热锻件2最大应力为827MPa,热锻件1齿根处出现了应力集中区域,可能会导致成形件在工作中更容易失效减小其使用寿命。由图6可知,热锻件2的平均应变比热锻件1小,热锻件1齿根齿顶区域应变大,说明热锻件2的材料流动更为合理。热锻件1的应变分布差值较大,应变分布不均可能会导致附加应力和残余应力的产生,影响成形件精度,影响传动过程中的平稳性。
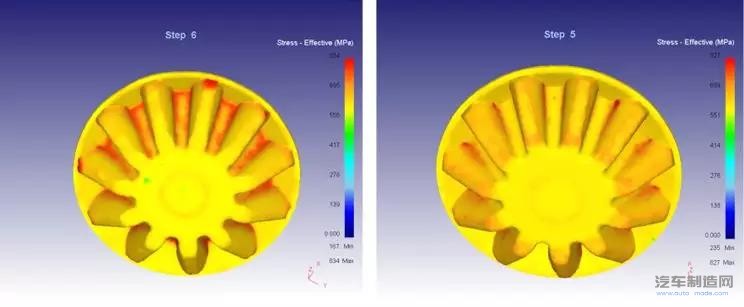
(a)热锻件1应力分布图 (b)热锻件2应力分布图
图5 应力分布图
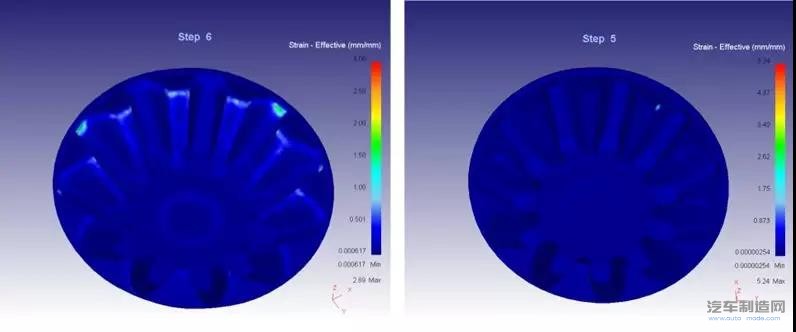
(a)热锻件1应变分布图 (b)热锻件2应变分布图
图6 应变分布图
成形对比试验
传统单一的热/温模锻造或者冷精锻工艺无法满足产品要求,本文基于复合锻造(热锻冷整)工艺进行成形实验对比,将前文中数值模拟的方案1和方案2进行实际锻造加工,在冷整上一工序,即热锻工序修整直齿锥齿轮齿高、齿厚,图7为方案1和方案2成形件对比图。图中灰白色部分属于未精整部分,图7(a)中大面积灰白色区域分布在齿面上,可能的原因是热锻工序温度较高,冷却时成形件收缩较大,导致冷整时由于齿厚偏小导致冷整不到位;图7(b)为优化后的冷整件,即增加热锻件齿厚减小齿高,增加齿厚充分考虑到热锻坯冷收缩量及模具弹性变形,确保齿面被精整达到加工要求,减小齿高是为了增加材料流动空间,减小模具的承载力提高模具使用寿命,从图中可以看出灰白色区域分布于成形件的齿顶和齿高部分,齿面被完全精整,符合加工要求。成形试验结果验证了数值模拟结果的可靠性,说明了方案2可以有效优化复合锻造工艺,显著提高成形质量。
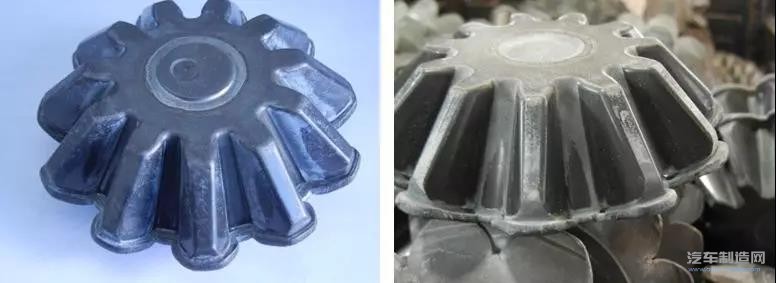
(a)方案1冷整直齿锥齿轮 (b)方案2冷整直齿锥齿轮
图7 直齿锥齿轮冷整成形件对比图
结论
本文针对热锻冷整复合锻造工艺中的冷整工序,对直齿锥齿轮冷整成形进行有限元数值模拟。通过对不同齿厚、齿高的直齿锥齿轮冷整成形过程中的成形载荷、流动速度场、应力应变的分析,对直齿锥齿轮齿厚、齿高进行了修正和优化。通过成形实验结果对比分析发现,适当的增加齿厚、减小齿高可有效提高冷整工序的产品合格率,降低模具成形载荷,提高模具使用寿命,对实际的锻造生产加工具有指导意义。
随着计算机技术的不断发展,实际生产中,为优化产品工艺、减小生产周期、降低生产成本,数值模拟方法得到广泛应用。本文基于热锻冷整复合加工工艺,利用DEFORM软件对直齿锥齿轮复合锻造冷整工序进行数值模拟,提出优化方案并进行成形验证,对直齿锥齿轮复合锻造成形工艺设计具有指导意义。
有限元模型及模拟方案
有限元模型的建立
本文基于热锻冷整成形工艺,模拟工序为热锻后的冷整工序。选取两个不同齿高、齿厚的直齿锥齿轮热锻成形件,运用Pro/E建立直齿锥齿轮与上下模具的三维模型,并保存为stl文件导入DEFORM软件进行有限元数值模拟。图1为直齿锥齿轮热锻成形件示意图,图2为模具的有限元数值模拟模型。
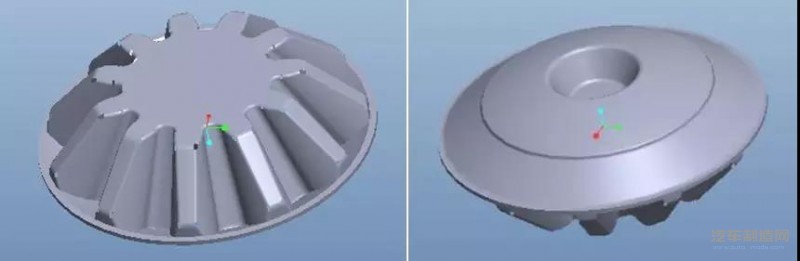
图1 直齿锥齿轮热锻件示意图
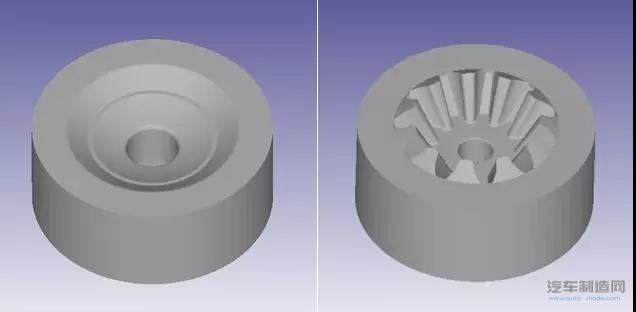
图2 模具有限元模拟模型
模拟参数设置
热锻件/冷整成形件尺寸对比和模拟参数设置如表1所示。
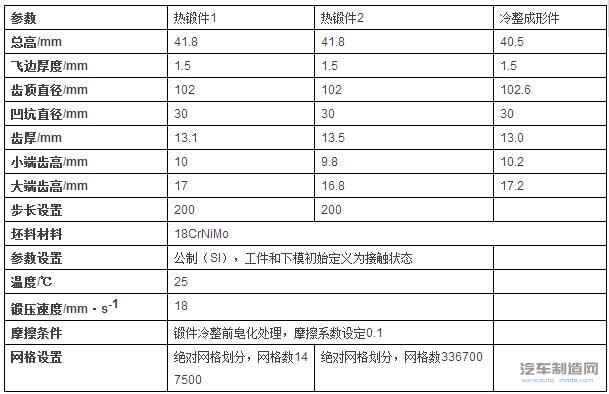
有限元数值模拟结果与分析
成形载荷分析
图3为不同热锻件尺寸冷整时上模对应的行程载荷,二者行程载荷相差较大。这是由于热锻件1齿厚较小、齿高较高,冷整时直齿锥齿轮齿顶和齿根区域先于齿面区域与上模发生并保持接触,材料流动所受阻力增加且材料变形范围小,齿顶、齿根区域承受的作用力大,齿面受力较小。热锻件2由于减小了齿高增大了齿厚,齿面先于齿顶与上模发生接触作用,直齿锥齿轮可自由流动材料增加且变形范围扩大,有效降低了成形载荷。
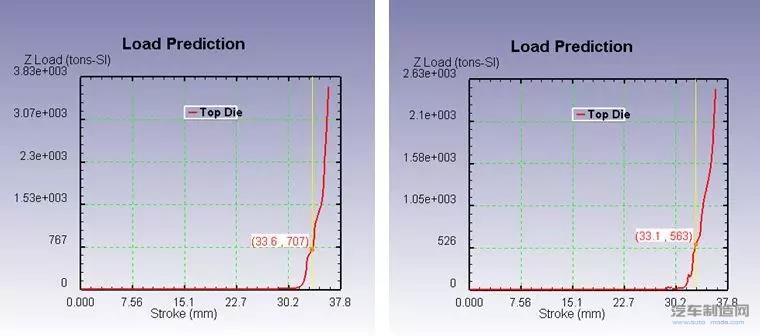
(a)热锻件1冷整成形载荷曲线 (b)热锻件2冷整成形载荷曲线
图3 上模载荷行程曲线
金属流动速度场分析
图4为不同齿高、齿厚热锻件冷整工序最终材料流动情况。图4(a)为高齿高薄齿厚的热锻件1,上模下行,与工件发生接触并发生挤压,从而使齿面材料向齿顶流动,因此齿顶存在一定的速度场;下模与工件始终处于接触阶段,在冷整过程中材料流动受到下模限制,其向飞边区域以及工件底部流动;最大流动速度在工件底部区域,为40mm/s。图4(b)为齿高减小0.2mm、齿厚增加0.4mm的热锻成形件,由于齿厚增加,工件受到上模的挤压作用,齿面材料向齿顶流动,因此齿顶存在材料流动速度场,且齿面平均流动速度比热锻件1增加了约1.5倍,齿面冷整效果良好;由于冷整过程中下模与工件始终接触,其材料流动受下模的限制作用,所以材料向飞边区域和工件底部流动;最大流动速度在工件底部区域。工件减小齿高、增加齿厚后最大材料流动速度减小,可能原因是上模与工件接触后,工件齿面发生的形变增大,齿顶面受到的挤压力变小,导致工件底部受到的挤压力减小,底部材料流动速度减小。
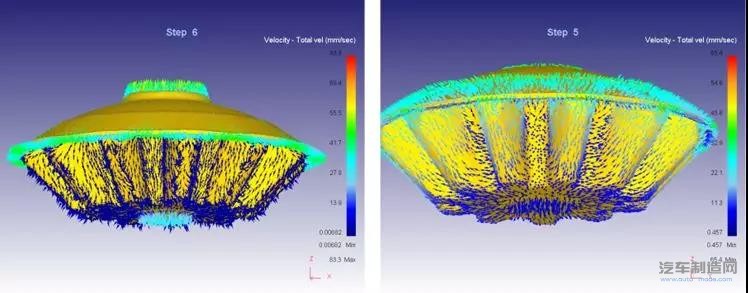
(a)热锻件1冷整工序材料流动速度场 (b)热锻件2材料流动速度场
图4 材料流动速度场
应力应变分析
热锻件1和热锻件2最终成形对应的应力、应变图如图5、图6所示。通过对比可知,随着变形的完成,热锻件1最大应力为834MPa,热锻件2最大应力为827MPa,热锻件1齿根处出现了应力集中区域,可能会导致成形件在工作中更容易失效减小其使用寿命。由图6可知,热锻件2的平均应变比热锻件1小,热锻件1齿根齿顶区域应变大,说明热锻件2的材料流动更为合理。热锻件1的应变分布差值较大,应变分布不均可能会导致附加应力和残余应力的产生,影响成形件精度,影响传动过程中的平稳性。
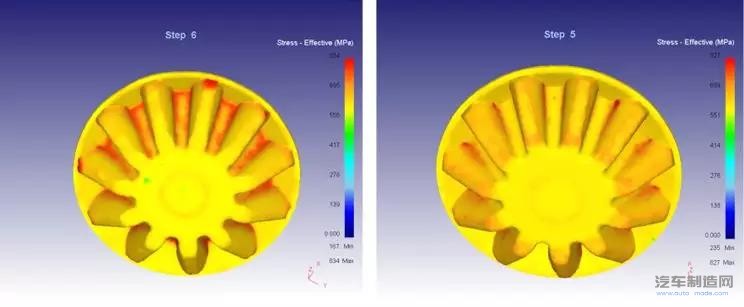
(a)热锻件1应力分布图 (b)热锻件2应力分布图
图5 应力分布图
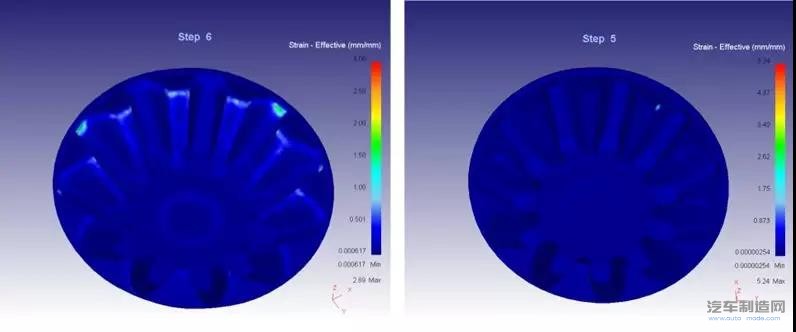
(a)热锻件1应变分布图 (b)热锻件2应变分布图
图6 应变分布图
成形对比试验
传统单一的热/温模锻造或者冷精锻工艺无法满足产品要求,本文基于复合锻造(热锻冷整)工艺进行成形实验对比,将前文中数值模拟的方案1和方案2进行实际锻造加工,在冷整上一工序,即热锻工序修整直齿锥齿轮齿高、齿厚,图7为方案1和方案2成形件对比图。图中灰白色部分属于未精整部分,图7(a)中大面积灰白色区域分布在齿面上,可能的原因是热锻工序温度较高,冷却时成形件收缩较大,导致冷整时由于齿厚偏小导致冷整不到位;图7(b)为优化后的冷整件,即增加热锻件齿厚减小齿高,增加齿厚充分考虑到热锻坯冷收缩量及模具弹性变形,确保齿面被精整达到加工要求,减小齿高是为了增加材料流动空间,减小模具的承载力提高模具使用寿命,从图中可以看出灰白色区域分布于成形件的齿顶和齿高部分,齿面被完全精整,符合加工要求。成形试验结果验证了数值模拟结果的可靠性,说明了方案2可以有效优化复合锻造工艺,显著提高成形质量。
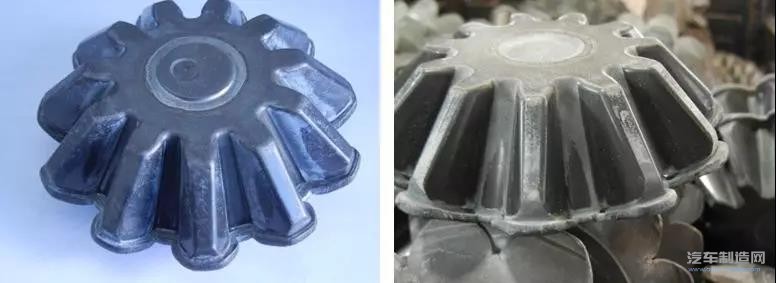
(a)方案1冷整直齿锥齿轮 (b)方案2冷整直齿锥齿轮
图7 直齿锥齿轮冷整成形件对比图
结论
本文针对热锻冷整复合锻造工艺中的冷整工序,对直齿锥齿轮冷整成形进行有限元数值模拟。通过对不同齿厚、齿高的直齿锥齿轮冷整成形过程中的成形载荷、流动速度场、应力应变的分析,对直齿锥齿轮齿厚、齿高进行了修正和优化。通过成形实验结果对比分析发现,适当的增加齿厚、减小齿高可有效提高冷整工序的产品合格率,降低模具成形载荷,提高模具使用寿命,对实际的锻造生产加工具有指导意义。
最新资讯
-
全球产业链聚沪 共探双碳新路径 SNEC
2025-04-18 18:05
-
柯马签订具有约束力的协议收购 Autom
2025-04-17 13:01
-
高效协同新范式:比亚迪叉车领创智能
2025-04-17 10:04
-
埃马克德国总部迎来中国社科院工业经
2025-04-15 09:40
-
埃马克这项全新应用即将在CIMT惊艳首
2025-04-15 09:37