一种重型商用车转向节机加工工艺方案与路线的制定
2018-02-08 15:50:38· 来源:锻造与冲压 作者:刘国伟
汽车转向节是汽车转向系统中的一个重要零件,是汽车前轮导向及承载部分的关键零件之一,它将方向盘转动的角度值有效地传递到汽车前轮上,适时控制汽车行进中的路线,从而保证汽车安全、准确无误地运行。
汽车转向节是汽车转向系统中的一个重要零件,是汽车前轮导向及承载部分的关键零件之一,它将方向盘转动的角度值有效地传递到汽车前轮上,适时控制汽车行进中的路线,从而保证汽车安全、准确无误地运行。其轴部与前轮相连;叉架部的主销孔,通过主销与汽车前轴相连;此外,叉架部还与左、右转向节臂相连,使汽车获得正常的灵活转向作用。转向节上主销孔的中心孔线与轴承颈中心线的垂线有一定的偏角,俗称主销内倾角,其主要作用是使汽车转向灵活方便,安全可靠。转向节承受的作用力较复杂,既受到变载荷的弯曲变应力的作用,又承受一定的冲击载荷和扭转力矩,因此转向节的材料需要有良好的机械强度和刚度。其几何形状比较复杂,需要加工的几何形体比较多,各几何表面之间位置精度要求较高,其加工精度的高低会影响到汽车运行中的转向精度。
零件的结构特点和工艺分析
我公司承接的一种重型商用车转向节,零件图如图1所示,材料为42CrMo,调质处理,硬度269~321HBW。
转向节的结构是支承轴、凸缘盘和支架等零件结构的空间组合。支承轴部分的结构形状为阶梯轴,由同轴的外圆柱面、圆锥面、螺纹面以及与轴心线垂直的轴肩、过渡圆角和端面组成的回转体;凸缘盘部分包括凸缘面、均布的连接螺栓孔和转向限位螺钉孔;支架部分是由转向节的上、下耳和凸缘面构成的支架形体。转向节由于其结构特征,决定了其特殊、复杂的加工工艺流程。
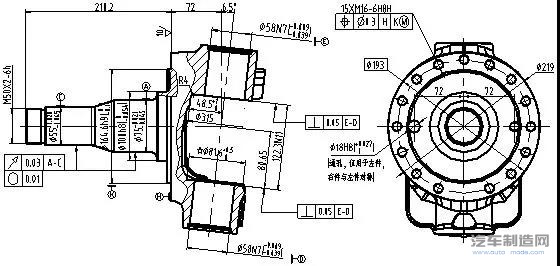
图1 重型商用车转向节零件图
经过我们认真分析后认为该零件的加工难点有以下几个方面:⑴15-M16螺纹孔的位置度φ0.3mm;⑵上、下两主销孔的跳动量0.05mm;⑶上、下耳环内端面相对主销孔中心的垂直度0.05mm;⑷上耳环内端面φ315/R4的加工;⑸下耳环φ81.6mm沉孔的加工;⑹法兰端面环形槽的加工;⑺两轴承颈的跳动量0.03mm及其圆度0.01mm。这几个难点也是我们在进行工艺设计时需要重点考虑的地方。
毛坯的制造形式
根据该零件的产品设计和结构形式,毛坯生产厂家确定采用立式锻造的方式生产该零件。对于转向节,采用立式锻造的优缺点如下:
优点:⑴锻件杆部直径方向的尺寸比较稳定,形状也规整,比较适合于第一序铣端面打中心孔工序的定位,杆部加工余量也比较均匀;⑵法兰面的叉架部位侧无需拔模,因此可以不用加工,故可以直接打中心孔。
缺点:⑴杆部长度方向加工余量不稳定,公差累计后,存在杆部端面和法兰面端面加工余量大的问题;⑵叉架部位的上、下耳环端面,由于主销内倾角的存在,下端面为了便于拔模,拔模方向正好和加工后端面的倾斜方向相反,故加工余量大;⑶锻件的错差,直接影响到上、下耳环端面的加工余量的均匀性,严重的情况下会出现端面黑皮的现象。
工艺路线的制定
生产纲领和生产节拍
根据客户需求和市场预测情况,确定年纲领为9万件,三班制生产,工艺节拍为3.5min/件。
工序划分
通过对零件的认真分析,我们对工序进行了如下划分:铣端面打中心孔→粗车杆部外圆和法兰端面→精车杆部外圆和法兰端面→叉架部位铣凸台、钻孔、攻螺纹、铰孔→法兰部位钻孔、攻丝→粗铣上下耳环端面→粗钻主销孔→精镗主销孔,铣内端面→精磨杆部轴承颈→打刻标识、下线。
理由如下:⑴铣端面打中心孔是为后续杆部和法兰端面的加工提供基准;叉架部位铣凸台,钻孔、攻螺纹、铰孔是为了后续叉架部位其它尺寸的加工提供基准;⑵粗加工和精加工分开,如设置了粗车杆部外圆和法兰端面、粗铣上下耳环端面、粗钻主销孔三个粗加工工序;⑶法兰部位钻孔、攻丝安排在其它工序前面,主要是考虑需加工的孔高达15个,丝锥容易折断,产生废品;而且螺纹孔的位置度精度要求较高,易出现不良品。从而避免其它工序加工后的浪费;⑷铣内端面和精镗主销孔放在一个工序内,主要考虑内端面相对主销孔中心的端面垂直度要求较高,放在一个工序内,可以避免二次装夹误差,保证加工质量;⑸精磨杆部轴承颈,主要是考虑轴承颈精度要求很高,故将其排在后面,避免其它工序加工时对轴承颈产生磕碰伤。
定位基准的选择
针对该零件,由于既有杆部的加工,又有叉架部位孔和平面的加工,结构比较复杂,加工部位较多,因此,加工不同的部位,需要选择不同的基准:⑴在加工杆部时,不管是粗车、精车、精磨工序,我们均以杆部两端的中心孔作为加工的基准,即杆部加工的精基准;⑵在加工作为杆部精基准的中心孔时,选择杆部外圆作为粗基准,可以保证后续车、磨工序加工余量均匀;⑶加工叉架部位时,所有工序均选择φ100mm轴颈、φ18mm孔及法兰端面作为精基准,采用“一面双销”的定位方式。这样各工序的基准就实现了统一,确保加工质量。
工艺方案及路线
设备选型方面,粗加工和精加工设备分开,关键工序选用加工中心等数控设备,部分工序选择专机和通用设备,保证适当的柔性、生产效率及产品质量,同时也可以避免加工过程中因疏忽而造成加工尺寸遗漏。
根据前述一些原则,结合我们工艺调研情况,确定了:⑴零件的加工工序;⑵满足各工序要求的工艺设备(设备、夹具、刀具、量具等),对装用工艺装备提出工艺设计任务书;⑶各工序的技术要求和检验方法;⑷各工序的加工余量、计算工序尺寸和公差;⑸切削用量;⑺时间定额。形成的最终工艺方案和路线如表1所示。
表1 最终工艺方案和路线
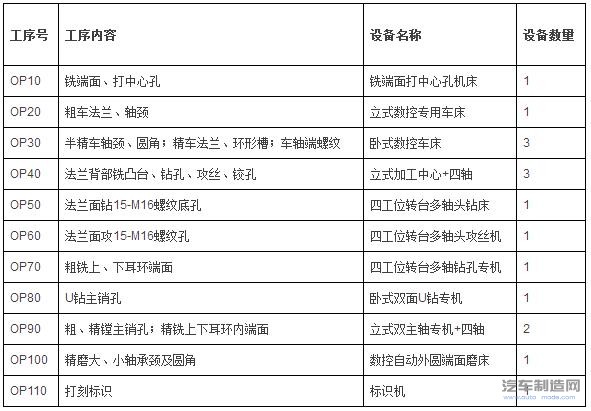
在生产纲领一定的情况下,我们确定建设一条生产线,故在提出专用机床的设备技术任务书时,我们要求该工序必须用一台设备保证生产节拍的要求,这样相对于两条或多条生产线,可以大大减少设备的投入,节约了投资和成本。
此外,由于该零件毛坯重量为32kg,采用人工上下料劳动强度非常大,同时为了降低人工成本,我们提出了采用3台行走机器人组成的自动物流线代替人工实现上下料和工序间工件的转运。工艺设备平面布置如图2所示。
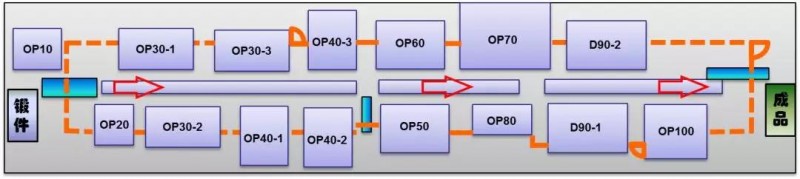
图2 工艺设备平面布置
工艺装备的要求
⑴对机床夹具的要求。一是稳定地保证工件的加工精度;二是提高机械加工的劳动生产率;三是结构件简单,有良好的结构工艺性和劳动条件;四是应能降低工件的制造成本。简而言之,设计夹具时必须保证加工质量、生产率、劳动条件和经济性等几方面达到辩证的统一。其中保证加工质量是最基本的要求。
⑵对设备的特殊要求。由于生产线全新建设,设备全部为新增,为了统一美观,对所有设备的外观颜色和积屑小车提出了统一的要求;由于计划采用机器人自动物流线进行上下料,对设备还提出了以下特殊要求:1)设备的控制系统须和自动上下料机械手或机器人的控制系统相互通讯,实现联动,确保装卸零部件和运行安全;2)配置可自动开、关的防护门,采用双开“┓”敞开式结构,方便机器人更换零件;防护门装有电气联锁保护装置及解除互锁控制开关,并采用光电保护,光电信号同时传输到机器人系统,以保证操作者和机器人的安全;3)机床可以实现自动和手动两种模式工作;4)机床的控制系统应能自动实现机床操作门的开关、工件的夹紧松开、夹具定位面的自动清理等动作。
⑶刀具。对于刀具的选择,尽量采用复合刀具,以提高加工效率,同时还要保证刀具消耗控制在目标范围内。
⑷量、检具。转向节轴颈磨削、主销孔孔径镗削和轴承颈精车时采用自动在线测量,以确保关键尺寸的加工质量;普通尺寸采用通用量具(卡规、塞规、卡尺、内径量表、外径千分尺等),形位公差采用CMM进行检查。
⑸配套的自动物流线。生产线采用3台行走机器人组成的自动物流线代替人工实现上下料和工序间工件的转运。自动物流线由上下料平台、中间转运平台、抽检平台、机器人导轨单元、机器人、机器人自动夹具单元、工件自动清理装置、工件打刻标识设备、安全隔离护栏、安全防护系统、润滑系统、各类控制柜和控制系统等组成。
⑹控制、信息系统。由中央控制台、机器人控制系统与所有设备进行通信的从站、网络及软件、自动统计、警示/报警/显示以及安全防护系统等组成。机器人中央控制系统采用S7-317-2DP系列PLC,与各台设备之间采用profibus总线通讯方式。
实施效果
生产线建成及投产后,经过验证,达到了工艺设计要求,产品质量符合技术要求,同时也为我公司自动化生产线建设积累了宝贵的经验。建成后的生产线如图3所示。
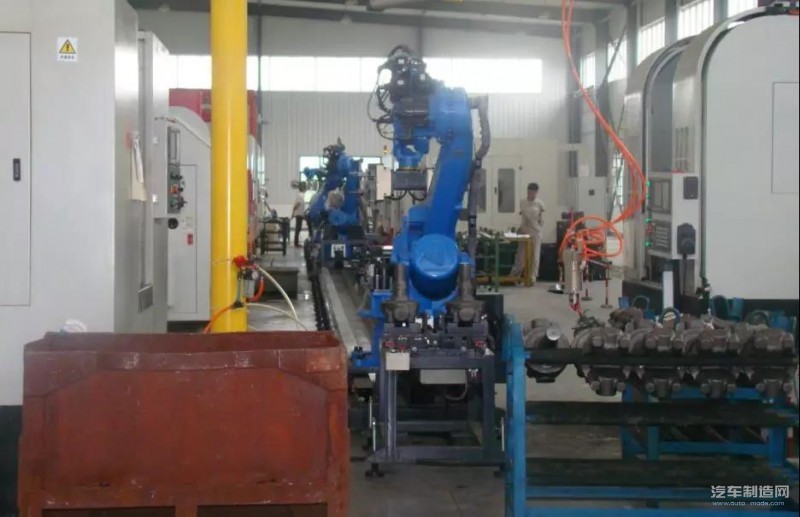
图3 建成后的生产线
在加工生产的过程中,采用立式锻造方式生产的锻件的优缺点也得到了验证。通过锻造控制和加工时的调整,锻件就能很好的满足机加工要求。
零件的结构特点和工艺分析
我公司承接的一种重型商用车转向节,零件图如图1所示,材料为42CrMo,调质处理,硬度269~321HBW。
转向节的结构是支承轴、凸缘盘和支架等零件结构的空间组合。支承轴部分的结构形状为阶梯轴,由同轴的外圆柱面、圆锥面、螺纹面以及与轴心线垂直的轴肩、过渡圆角和端面组成的回转体;凸缘盘部分包括凸缘面、均布的连接螺栓孔和转向限位螺钉孔;支架部分是由转向节的上、下耳和凸缘面构成的支架形体。转向节由于其结构特征,决定了其特殊、复杂的加工工艺流程。
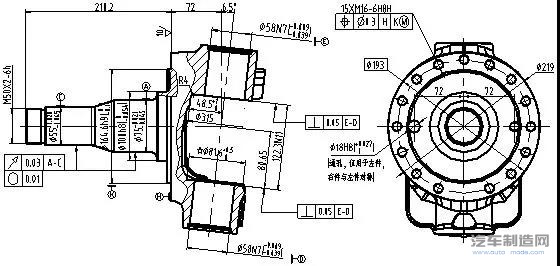
图1 重型商用车转向节零件图
经过我们认真分析后认为该零件的加工难点有以下几个方面:⑴15-M16螺纹孔的位置度φ0.3mm;⑵上、下两主销孔的跳动量0.05mm;⑶上、下耳环内端面相对主销孔中心的垂直度0.05mm;⑷上耳环内端面φ315/R4的加工;⑸下耳环φ81.6mm沉孔的加工;⑹法兰端面环形槽的加工;⑺两轴承颈的跳动量0.03mm及其圆度0.01mm。这几个难点也是我们在进行工艺设计时需要重点考虑的地方。
毛坯的制造形式
根据该零件的产品设计和结构形式,毛坯生产厂家确定采用立式锻造的方式生产该零件。对于转向节,采用立式锻造的优缺点如下:
优点:⑴锻件杆部直径方向的尺寸比较稳定,形状也规整,比较适合于第一序铣端面打中心孔工序的定位,杆部加工余量也比较均匀;⑵法兰面的叉架部位侧无需拔模,因此可以不用加工,故可以直接打中心孔。
缺点:⑴杆部长度方向加工余量不稳定,公差累计后,存在杆部端面和法兰面端面加工余量大的问题;⑵叉架部位的上、下耳环端面,由于主销内倾角的存在,下端面为了便于拔模,拔模方向正好和加工后端面的倾斜方向相反,故加工余量大;⑶锻件的错差,直接影响到上、下耳环端面的加工余量的均匀性,严重的情况下会出现端面黑皮的现象。
工艺路线的制定
生产纲领和生产节拍
根据客户需求和市场预测情况,确定年纲领为9万件,三班制生产,工艺节拍为3.5min/件。
工序划分
通过对零件的认真分析,我们对工序进行了如下划分:铣端面打中心孔→粗车杆部外圆和法兰端面→精车杆部外圆和法兰端面→叉架部位铣凸台、钻孔、攻螺纹、铰孔→法兰部位钻孔、攻丝→粗铣上下耳环端面→粗钻主销孔→精镗主销孔,铣内端面→精磨杆部轴承颈→打刻标识、下线。
理由如下:⑴铣端面打中心孔是为后续杆部和法兰端面的加工提供基准;叉架部位铣凸台,钻孔、攻螺纹、铰孔是为了后续叉架部位其它尺寸的加工提供基准;⑵粗加工和精加工分开,如设置了粗车杆部外圆和法兰端面、粗铣上下耳环端面、粗钻主销孔三个粗加工工序;⑶法兰部位钻孔、攻丝安排在其它工序前面,主要是考虑需加工的孔高达15个,丝锥容易折断,产生废品;而且螺纹孔的位置度精度要求较高,易出现不良品。从而避免其它工序加工后的浪费;⑷铣内端面和精镗主销孔放在一个工序内,主要考虑内端面相对主销孔中心的端面垂直度要求较高,放在一个工序内,可以避免二次装夹误差,保证加工质量;⑸精磨杆部轴承颈,主要是考虑轴承颈精度要求很高,故将其排在后面,避免其它工序加工时对轴承颈产生磕碰伤。
定位基准的选择
针对该零件,由于既有杆部的加工,又有叉架部位孔和平面的加工,结构比较复杂,加工部位较多,因此,加工不同的部位,需要选择不同的基准:⑴在加工杆部时,不管是粗车、精车、精磨工序,我们均以杆部两端的中心孔作为加工的基准,即杆部加工的精基准;⑵在加工作为杆部精基准的中心孔时,选择杆部外圆作为粗基准,可以保证后续车、磨工序加工余量均匀;⑶加工叉架部位时,所有工序均选择φ100mm轴颈、φ18mm孔及法兰端面作为精基准,采用“一面双销”的定位方式。这样各工序的基准就实现了统一,确保加工质量。
工艺方案及路线
设备选型方面,粗加工和精加工设备分开,关键工序选用加工中心等数控设备,部分工序选择专机和通用设备,保证适当的柔性、生产效率及产品质量,同时也可以避免加工过程中因疏忽而造成加工尺寸遗漏。
根据前述一些原则,结合我们工艺调研情况,确定了:⑴零件的加工工序;⑵满足各工序要求的工艺设备(设备、夹具、刀具、量具等),对装用工艺装备提出工艺设计任务书;⑶各工序的技术要求和检验方法;⑷各工序的加工余量、计算工序尺寸和公差;⑸切削用量;⑺时间定额。形成的最终工艺方案和路线如表1所示。
表1 最终工艺方案和路线
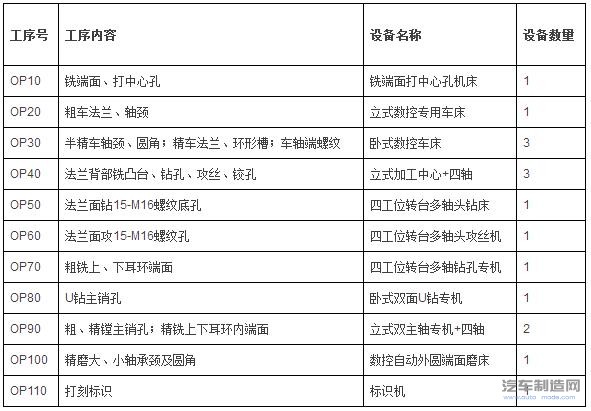
在生产纲领一定的情况下,我们确定建设一条生产线,故在提出专用机床的设备技术任务书时,我们要求该工序必须用一台设备保证生产节拍的要求,这样相对于两条或多条生产线,可以大大减少设备的投入,节约了投资和成本。
此外,由于该零件毛坯重量为32kg,采用人工上下料劳动强度非常大,同时为了降低人工成本,我们提出了采用3台行走机器人组成的自动物流线代替人工实现上下料和工序间工件的转运。工艺设备平面布置如图2所示。
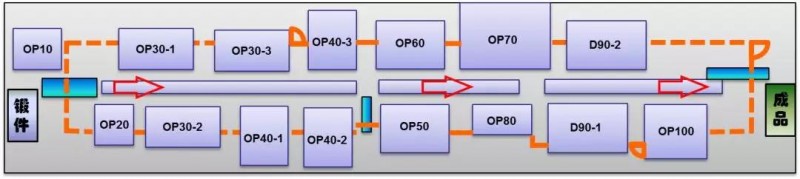
图2 工艺设备平面布置
工艺装备的要求
⑴对机床夹具的要求。一是稳定地保证工件的加工精度;二是提高机械加工的劳动生产率;三是结构件简单,有良好的结构工艺性和劳动条件;四是应能降低工件的制造成本。简而言之,设计夹具时必须保证加工质量、生产率、劳动条件和经济性等几方面达到辩证的统一。其中保证加工质量是最基本的要求。
⑵对设备的特殊要求。由于生产线全新建设,设备全部为新增,为了统一美观,对所有设备的外观颜色和积屑小车提出了统一的要求;由于计划采用机器人自动物流线进行上下料,对设备还提出了以下特殊要求:1)设备的控制系统须和自动上下料机械手或机器人的控制系统相互通讯,实现联动,确保装卸零部件和运行安全;2)配置可自动开、关的防护门,采用双开“┓”敞开式结构,方便机器人更换零件;防护门装有电气联锁保护装置及解除互锁控制开关,并采用光电保护,光电信号同时传输到机器人系统,以保证操作者和机器人的安全;3)机床可以实现自动和手动两种模式工作;4)机床的控制系统应能自动实现机床操作门的开关、工件的夹紧松开、夹具定位面的自动清理等动作。
⑶刀具。对于刀具的选择,尽量采用复合刀具,以提高加工效率,同时还要保证刀具消耗控制在目标范围内。
⑷量、检具。转向节轴颈磨削、主销孔孔径镗削和轴承颈精车时采用自动在线测量,以确保关键尺寸的加工质量;普通尺寸采用通用量具(卡规、塞规、卡尺、内径量表、外径千分尺等),形位公差采用CMM进行检查。
⑸配套的自动物流线。生产线采用3台行走机器人组成的自动物流线代替人工实现上下料和工序间工件的转运。自动物流线由上下料平台、中间转运平台、抽检平台、机器人导轨单元、机器人、机器人自动夹具单元、工件自动清理装置、工件打刻标识设备、安全隔离护栏、安全防护系统、润滑系统、各类控制柜和控制系统等组成。
⑹控制、信息系统。由中央控制台、机器人控制系统与所有设备进行通信的从站、网络及软件、自动统计、警示/报警/显示以及安全防护系统等组成。机器人中央控制系统采用S7-317-2DP系列PLC,与各台设备之间采用profibus总线通讯方式。
实施效果
生产线建成及投产后,经过验证,达到了工艺设计要求,产品质量符合技术要求,同时也为我公司自动化生产线建设积累了宝贵的经验。建成后的生产线如图3所示。
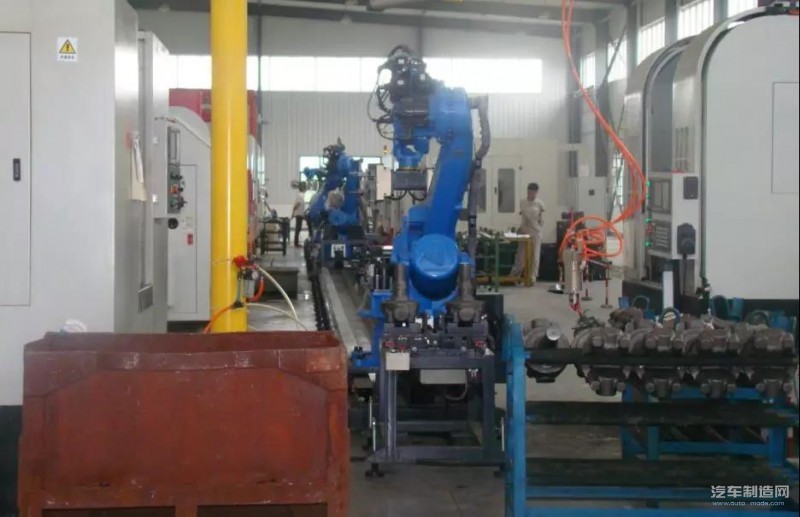
图3 建成后的生产线
在加工生产的过程中,采用立式锻造方式生产的锻件的优缺点也得到了验证。通过锻造控制和加工时的调整,锻件就能很好的满足机加工要求。
最新资讯
-
全球产业链聚沪 共探双碳新路径 SNEC
2025-04-18 18:05
-
柯马签订具有约束力的协议收购 Autom
2025-04-17 13:01
-
高效协同新范式:比亚迪叉车领创智能
2025-04-17 10:04
-
埃马克德国总部迎来中国社科院工业经
2025-04-15 09:40
-
埃马克这项全新应用即将在CIMT惊艳首
2025-04-15 09:37