汽车高固含涂装工艺的研究与应用
2018-02-13 16:56:10· 作者:奇瑞汽车股份有限公司 和军强
1. 概述汽车产业作为现代化社会的标志性产业,随着中国经济的高速发展,已经成为国民经济中的支柱产业。然而,其对环境产生的负面影响也进一步凸显。现代汽车工业分为四大工艺环节:零件冲压工艺、车身焊装工艺、车身涂装工艺和总成装配
1. 概述
汽车产业作为现代化社会的标志性产业,随着中国经济的高速发展,已经成为国民经济中的支柱产业。然而,其对环境产生的负面影响也进一步凸显。现代汽车工业分为四大工艺环节:零件冲压工艺、车身焊装工艺、车身涂装工艺和总成装配工艺。车身涂装是污染排放最高的环节,汽车生产过程中,有 80%以上的VOCs排放来自于涂装环节。
2013年以前,国内汽车行业普遍使用低固体分溶剂型涂料。随着国内环保意识的日益提升及政府更为严格的环保要求,国内涂装专业提出了绿色涂装的概念,即涂装生产线的节能、降耗、减排。绿色涂装中,所选用的涂料、涂装工艺的环保特性起决定性作用。为了降低污染,汽车涂料逐步更新为环保型产品,包括粉末涂料、水性涂料以及高固体分涂料。高固体分涂装工艺在老线便于改造的突出优势已逐步显现,在可预见的未来其发展将会达到一个全新的高度。
2. 环保涂料的发展
作为汽车行业成熟的产品,传统中低固体分3C2B溶剂涂料具有很好的装饰性、使用性能和很宽的施工窗口。但其诟病之处在于VOCs排放高,对大气污染严重;且生产线长,设备多,占地面积大。为克服VOCs污染问题,逐渐研究出了新一代的环保涂料——水性涂料、粉末涂料以及高固体分涂料;并且为了减少生产线投资,降低生产过程中的能源消耗,衍生出了紧凑型工艺如3C1B、水性B1B2等。在颜色多、换色频繁的车身涂装过程中,粉末涂料由于其自身特点的限制而应用较少。目前常用的环保型涂料为水性涂料及高固体分涂料。
2.1 水性涂料及溶剂型涂料的VOCs排放对比
相比于传统溶剂型3C2B涂装工艺,新一代环保涂料在VOCs排放方面均有明显降低。水性涂料的VOCs排放优势最大,最高降幅可达80%以上;高固体分溶剂型涂料也能较大程度地减少有机溶剂的排放,最高降幅可达60%以上。采用两种工艺均可达到目前国内环保法规要求的VOCs限值,有效减轻大气污染。
2.2 工艺对比
目前常见于国内OEM制造商的涂装工艺因使用涂料类别不同相差较大。对于水性涂料而言,由于水的潜热大挥发慢,在烘烤成膜前需要增加强制闪干(烘烤)段,以保证涂层充分脱水。以3C2B(三涂层二烘烤)为例,水性涂料将比溶剂型涂料多出两个强制闪干段,增加了生产线的占地面积、厂房及设备投入,并大幅度增加了能源的消耗。见图1 工艺对比图:
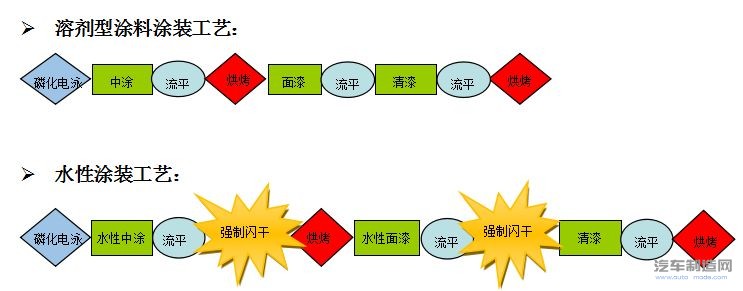
图1 工艺对比图
另外,水性涂料施工窗口窄,导致对施工环境要求高,需要稳定的温度和湿度控制:温度(25±2) ℃,湿度65%±5%。现场需要添加额外的空调制冷等设备保证应用环境。
除VOCs对大气的污染需严格控制外,能耗也是生产过程中需重点控制的因素之一。为了降低能耗,逐步衍生出了紧凑型工艺,减少一道中涂烘干工序。同时,将部分涂层厚度调整降低,也在一定程度上降低了VOCs的排放。由于水性涂料传统3C2B涂装工艺能耗高,在设计时更多考虑VOCs排放和紧凑型工艺,且水性涂料对设备的要求区别很大,不适宜在传统溶剂型涂装线上进行改造。
唯一例外的是高固体分溶剂型涂料,其自身与传统涂料体系一致,均为溶剂型涂料,施工与传统中低固溶剂型涂装工艺一致,基本无需改造。高固体分涂料提升了固体分含量,可以从源头上有效降低VOCs的产生及排放。对于有环保要求进行涂装线改造的企业来说,高固体分涂料涂装是一个可以达到降低VOCs目标、省时省力、节省投资的非常好的选择。
3. 高固体分涂料及其特性
根据市场上出现的高固体分产品定义为:较传统涂料施工固体分更高的涂料体系,一般高出10%~25%的质量固体分。本文选取美国某知名涂料企业高固体分金属漆产品,对比传统溶剂型汽车涂料如表1:

表1 施工固体分对比
注:此处为质量固体分。
在传统汽车涂装各工序溶剂挥发量中,电泳漆占1%,中涂漆占16%,底色漆占52%,罩光漆占13%、喷蜡占13%、其它占5%。高固体分底色漆的施工固体分可提高2倍以上,其在降低VOCs排放方面的贡献不容小觑。
高固体分涂料的核心问题是设法降低传统成膜物质的相对分子质量,降低黏度,提高溶解性,在成膜过程中靠有效的交联反应,保证完美的涂层质量达到热固性溶剂型涂料的水平或更高。因此成膜树脂必须具有合适相对分子质量及分布,这对涂料供应商的技术及成本控制能力都是巨大的挑战。另外,高固体分涂料体系必须辅之以溶解力强的溶剂,用更少的溶剂高效地降低黏度。
3.1 高雾化能量
高固体分涂料施工时固体分较传统涂料高出10-20%,这种特性带来的不利影响是:高固体分涂料雾化难,而且即便从雾化口喷出的漆滴大小一样,到达被涂件表面时传统中低固涂料因溶剂挥发颗粒变得更细腻(见图2)。而喷涂高固体分涂料时需要更高的能量促使漆滴充分雾化,才能保证最终漆膜的外观。这种特性对含有效果颜料(金属粉、珠光粉等)的产品的定向效果具有较大的影响。如下图中(1)部分,雾化不佳导致了效果颜料堆积,颜色难以调整;图中(2)部分左侧表示充分雾化,喷涂时漆滴达到要求才可满足右侧的涂着效果。现场使用经验表明,高固涂料施工时旋杯转速一般在50 K 转/分钟以上。
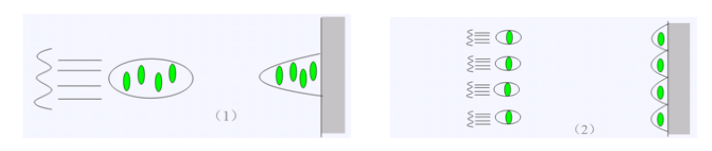
图2 涂料雾化效果图
3.2 电阻率
高固体分涂料中以少量溶剂快速降低粘度,故所用溶剂大部分为溶解力强的极性溶剂,如酮类、醇类等。因此,高固体分涂料电阻率比传统溶剂低:传统溶剂施工电阻率范围为0.8-2.0 MΩ,高固体分体系为0.5-0.8 MΩ。低电阻率对喷涂设备提出较高要求,需要更低的报警阀值。
3.3 温度敏感性
温度对涂料中成膜树脂的流变行为有较大的影响,而高固体分涂料(特别是高固体分清漆)中树脂含量非常高,温度变化通常会对涂料粘度产生更大的影响。例如图3 ,展示了某高固清漆典型的粘度温度曲线:
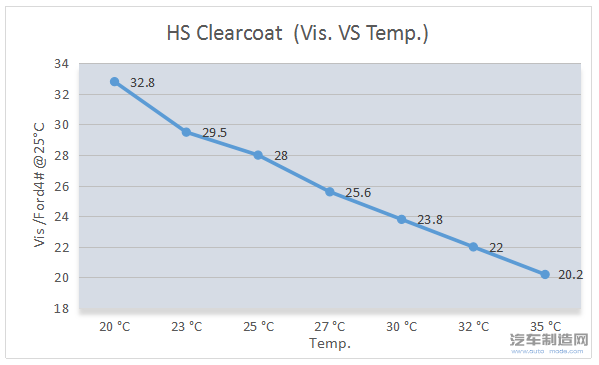
图3 某高固清漆粘度温度曲线
实际情况是国内已有的溶剂型涂装线对温度的控制并不严格,因此需要特别注意随着季节及气温变动调整涂料施工粘度,避免出现流挂外观等缺陷。
4. 高固体分涂层性能与外观
4.1 干膜性能表现
通过严格的原材料挑选和恰当的配方设计,目前高固体分涂料在性能方面已经达到与传统溶剂型涂料相同的水平,能够满足多数汽车生产商的要求。仍选取美国某知名涂料企业高固体分产品与传统产品对比,如表2:

表2 高固体份涂料干膜性能测试结果
4.2 漆膜外观表现
高固体分涂料的两种主要成膜树脂的选择都有别于传统中低固溶剂体系:所用丙烯酸树脂分子量偏低以满足粘度;同时高固体分的氨基树脂醚化度高,聚合度低,交联反应活性低。这种特性将导致高固体系交联反应不如低固体系平顺,最终影响到漆膜外观,尤其是短波表现。选列如表3:
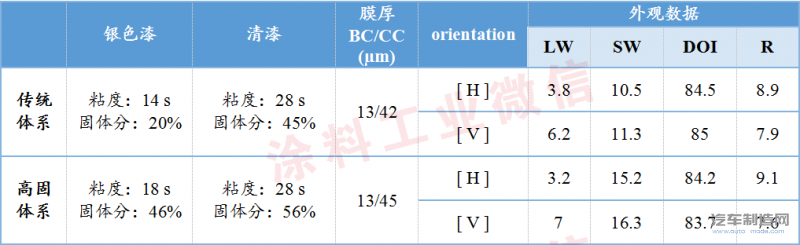
表3 高固体系与传统体系外观对比
注:粘度使用Ford 4# 粘度杯,25°C测量(施工状态下);外观使用BYK wavescan测量。
5. 高固体分涂料施工参数及注意事项
鉴于高固体分涂料具备上述特点,其在喷涂方面具备自己的特点:要求整形空气流量高、涂料流量低、喷涂电压高、旋杯转速高等;对现场环境、烘烤参数的要求与中低固溶剂涂料一致。具体如表4所示:
表4:中低固体分与高固体分涂料施工对比
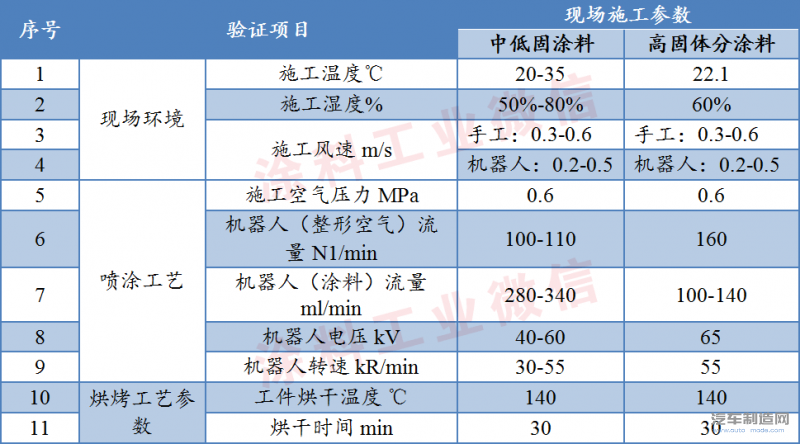
在已有的传统中低固溶剂涂装线上进行高固体份涂装工艺改造时,仅需对参数改变的部分做稍微调整,再考虑部分必要的涂料开发、系统清洗,即可实现高固涂装工艺的切换。此环保改造方案,成本最低,耗时最短,基本不会造成原生产线的停产。
6. 结语
随着国内环保要求的日益提升,环保涂料的推广也将加快,并且呈现出多元化的发展路径。高固体分涂料能在原有生产线上使用,在尊重其材料特性的条件下正确应用,能达到与传统溶剂型涂料同等的水平;同时还能显著降低VOCs排放。高固体分涂料的这种独特优势是其它环保涂料所不具备的。因此,在一些有环保诉求但又不是非常严苛的汽车生产商以及其它工业涂装场合,高固体分涂料有很大的发展潜力,必将以其自身独特的优势在未来汽车涂装环保应用中争得一席之地。
汽车产业作为现代化社会的标志性产业,随着中国经济的高速发展,已经成为国民经济中的支柱产业。然而,其对环境产生的负面影响也进一步凸显。现代汽车工业分为四大工艺环节:零件冲压工艺、车身焊装工艺、车身涂装工艺和总成装配工艺。车身涂装是污染排放最高的环节,汽车生产过程中,有 80%以上的VOCs排放来自于涂装环节。
2013年以前,国内汽车行业普遍使用低固体分溶剂型涂料。随着国内环保意识的日益提升及政府更为严格的环保要求,国内涂装专业提出了绿色涂装的概念,即涂装生产线的节能、降耗、减排。绿色涂装中,所选用的涂料、涂装工艺的环保特性起决定性作用。为了降低污染,汽车涂料逐步更新为环保型产品,包括粉末涂料、水性涂料以及高固体分涂料。高固体分涂装工艺在老线便于改造的突出优势已逐步显现,在可预见的未来其发展将会达到一个全新的高度。
2. 环保涂料的发展
作为汽车行业成熟的产品,传统中低固体分3C2B溶剂涂料具有很好的装饰性、使用性能和很宽的施工窗口。但其诟病之处在于VOCs排放高,对大气污染严重;且生产线长,设备多,占地面积大。为克服VOCs污染问题,逐渐研究出了新一代的环保涂料——水性涂料、粉末涂料以及高固体分涂料;并且为了减少生产线投资,降低生产过程中的能源消耗,衍生出了紧凑型工艺如3C1B、水性B1B2等。在颜色多、换色频繁的车身涂装过程中,粉末涂料由于其自身特点的限制而应用较少。目前常用的环保型涂料为水性涂料及高固体分涂料。
2.1 水性涂料及溶剂型涂料的VOCs排放对比
相比于传统溶剂型3C2B涂装工艺,新一代环保涂料在VOCs排放方面均有明显降低。水性涂料的VOCs排放优势最大,最高降幅可达80%以上;高固体分溶剂型涂料也能较大程度地减少有机溶剂的排放,最高降幅可达60%以上。采用两种工艺均可达到目前国内环保法规要求的VOCs限值,有效减轻大气污染。
2.2 工艺对比
目前常见于国内OEM制造商的涂装工艺因使用涂料类别不同相差较大。对于水性涂料而言,由于水的潜热大挥发慢,在烘烤成膜前需要增加强制闪干(烘烤)段,以保证涂层充分脱水。以3C2B(三涂层二烘烤)为例,水性涂料将比溶剂型涂料多出两个强制闪干段,增加了生产线的占地面积、厂房及设备投入,并大幅度增加了能源的消耗。见图1 工艺对比图:
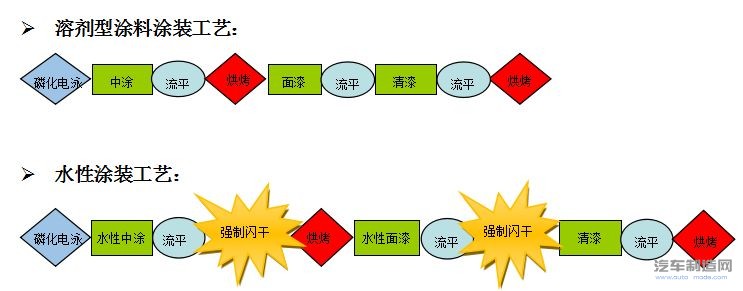
图1 工艺对比图
另外,水性涂料施工窗口窄,导致对施工环境要求高,需要稳定的温度和湿度控制:温度(25±2) ℃,湿度65%±5%。现场需要添加额外的空调制冷等设备保证应用环境。
除VOCs对大气的污染需严格控制外,能耗也是生产过程中需重点控制的因素之一。为了降低能耗,逐步衍生出了紧凑型工艺,减少一道中涂烘干工序。同时,将部分涂层厚度调整降低,也在一定程度上降低了VOCs的排放。由于水性涂料传统3C2B涂装工艺能耗高,在设计时更多考虑VOCs排放和紧凑型工艺,且水性涂料对设备的要求区别很大,不适宜在传统溶剂型涂装线上进行改造。
唯一例外的是高固体分溶剂型涂料,其自身与传统涂料体系一致,均为溶剂型涂料,施工与传统中低固溶剂型涂装工艺一致,基本无需改造。高固体分涂料提升了固体分含量,可以从源头上有效降低VOCs的产生及排放。对于有环保要求进行涂装线改造的企业来说,高固体分涂料涂装是一个可以达到降低VOCs目标、省时省力、节省投资的非常好的选择。
3. 高固体分涂料及其特性
根据市场上出现的高固体分产品定义为:较传统涂料施工固体分更高的涂料体系,一般高出10%~25%的质量固体分。本文选取美国某知名涂料企业高固体分金属漆产品,对比传统溶剂型汽车涂料如表1:

表1 施工固体分对比
注:此处为质量固体分。
在传统汽车涂装各工序溶剂挥发量中,电泳漆占1%,中涂漆占16%,底色漆占52%,罩光漆占13%、喷蜡占13%、其它占5%。高固体分底色漆的施工固体分可提高2倍以上,其在降低VOCs排放方面的贡献不容小觑。
高固体分涂料的核心问题是设法降低传统成膜物质的相对分子质量,降低黏度,提高溶解性,在成膜过程中靠有效的交联反应,保证完美的涂层质量达到热固性溶剂型涂料的水平或更高。因此成膜树脂必须具有合适相对分子质量及分布,这对涂料供应商的技术及成本控制能力都是巨大的挑战。另外,高固体分涂料体系必须辅之以溶解力强的溶剂,用更少的溶剂高效地降低黏度。
3.1 高雾化能量
高固体分涂料施工时固体分较传统涂料高出10-20%,这种特性带来的不利影响是:高固体分涂料雾化难,而且即便从雾化口喷出的漆滴大小一样,到达被涂件表面时传统中低固涂料因溶剂挥发颗粒变得更细腻(见图2)。而喷涂高固体分涂料时需要更高的能量促使漆滴充分雾化,才能保证最终漆膜的外观。这种特性对含有效果颜料(金属粉、珠光粉等)的产品的定向效果具有较大的影响。如下图中(1)部分,雾化不佳导致了效果颜料堆积,颜色难以调整;图中(2)部分左侧表示充分雾化,喷涂时漆滴达到要求才可满足右侧的涂着效果。现场使用经验表明,高固涂料施工时旋杯转速一般在50 K 转/分钟以上。
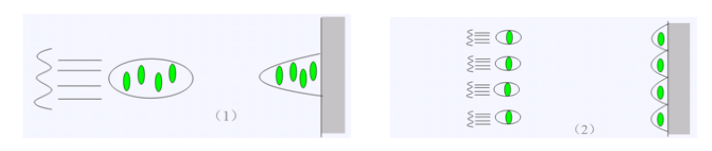
图2 涂料雾化效果图
3.2 电阻率
高固体分涂料中以少量溶剂快速降低粘度,故所用溶剂大部分为溶解力强的极性溶剂,如酮类、醇类等。因此,高固体分涂料电阻率比传统溶剂低:传统溶剂施工电阻率范围为0.8-2.0 MΩ,高固体分体系为0.5-0.8 MΩ。低电阻率对喷涂设备提出较高要求,需要更低的报警阀值。
3.3 温度敏感性
温度对涂料中成膜树脂的流变行为有较大的影响,而高固体分涂料(特别是高固体分清漆)中树脂含量非常高,温度变化通常会对涂料粘度产生更大的影响。例如图3 ,展示了某高固清漆典型的粘度温度曲线:
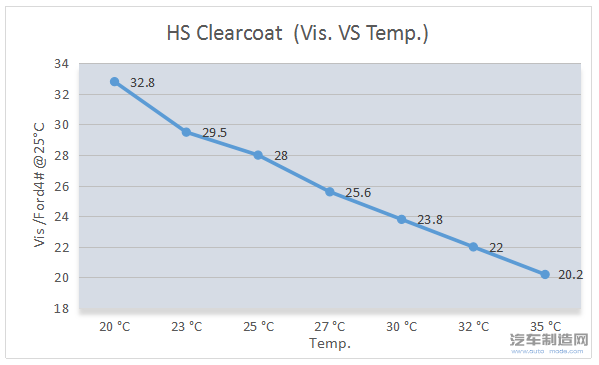
图3 某高固清漆粘度温度曲线
实际情况是国内已有的溶剂型涂装线对温度的控制并不严格,因此需要特别注意随着季节及气温变动调整涂料施工粘度,避免出现流挂外观等缺陷。
4. 高固体分涂层性能与外观
4.1 干膜性能表现
通过严格的原材料挑选和恰当的配方设计,目前高固体分涂料在性能方面已经达到与传统溶剂型涂料相同的水平,能够满足多数汽车生产商的要求。仍选取美国某知名涂料企业高固体分产品与传统产品对比,如表2:

表2 高固体份涂料干膜性能测试结果
4.2 漆膜外观表现
高固体分涂料的两种主要成膜树脂的选择都有别于传统中低固溶剂体系:所用丙烯酸树脂分子量偏低以满足粘度;同时高固体分的氨基树脂醚化度高,聚合度低,交联反应活性低。这种特性将导致高固体系交联反应不如低固体系平顺,最终影响到漆膜外观,尤其是短波表现。选列如表3:
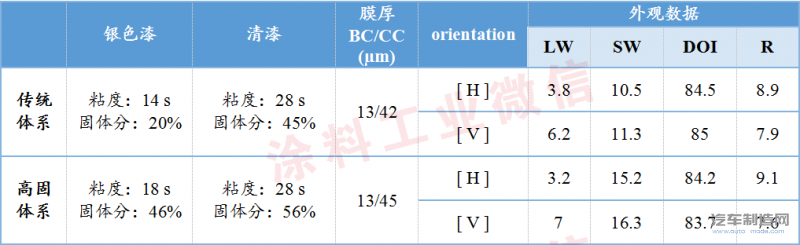
表3 高固体系与传统体系外观对比
注:粘度使用Ford 4# 粘度杯,25°C测量(施工状态下);外观使用BYK wavescan测量。
5. 高固体分涂料施工参数及注意事项
鉴于高固体分涂料具备上述特点,其在喷涂方面具备自己的特点:要求整形空气流量高、涂料流量低、喷涂电压高、旋杯转速高等;对现场环境、烘烤参数的要求与中低固溶剂涂料一致。具体如表4所示:
表4:中低固体分与高固体分涂料施工对比
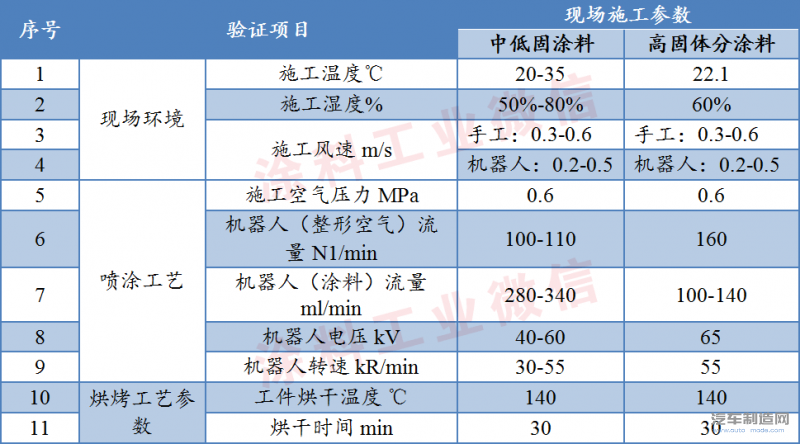
在已有的传统中低固溶剂涂装线上进行高固体份涂装工艺改造时,仅需对参数改变的部分做稍微调整,再考虑部分必要的涂料开发、系统清洗,即可实现高固涂装工艺的切换。此环保改造方案,成本最低,耗时最短,基本不会造成原生产线的停产。
6. 结语
随着国内环保要求的日益提升,环保涂料的推广也将加快,并且呈现出多元化的发展路径。高固体分涂料能在原有生产线上使用,在尊重其材料特性的条件下正确应用,能达到与传统溶剂型涂料同等的水平;同时还能显著降低VOCs排放。高固体分涂料的这种独特优势是其它环保涂料所不具备的。因此,在一些有环保诉求但又不是非常严苛的汽车生产商以及其它工业涂装场合,高固体分涂料有很大的发展潜力,必将以其自身独特的优势在未来汽车涂装环保应用中争得一席之地。
编辑推荐
最新资讯
-
思看科技受邀出席第三届联合国教科文
2025-04-27 13:29
-
聚势谋远,智领新程——五菱柳机以硬
2025-04-27 13:22
-
聚势求新、智驱未来——五菱工业底盘
2025-04-27 13:22
-
向轻量化、智能化迈进,助力建设国家
2025-04-27 13:21
-
五菱工业:以“中国智造”领跑绿色未
2025-04-27 13:21