简单分析宝沃是如何打造出混线生产8车型生产体系
2018-03-01 13:30:48· 来源:车云 作者:Stylish
在宝沃工厂的对外介绍上,都提到工厂内「可以实现8车型混线生产」的生产系统,在二期建设完成后,可以实现年产量36万台。当然,当前宝沃只有BX5和BX7两款车型。而且对于一个复活时间尚且不长的汽车品牌来说,短期内推出8款完全不同的车型也是不太可能的。
对于汽车制造商来说,「制造」是根基。而在通往工业4.0的过程中,每一家制造商其实都选择了不同的发展路线。昨天,车云菌前往参观了宝沃汽车在北京密云郊区的工厂。单从自动化率这个数字去比较,这家工厂的自动化率并不是很高。不过从整体工厂的设计来看,宝沃的目标也是明确:能够柔性化生产多车型。而且从当前来看,宝沃的目标从某种程度上说也是实现了。
在宝沃工厂的对外介绍上,都提到工厂内「可以实现8车型混线生产」的生产系统,在二期建设完成后,可以实现年产量36万台。当然,当前宝沃只有BX5和BX7两款车型。而且对于一个复活时间尚且不长的汽车品牌来说,短期内推出8款完全不同的车型也是不太可能的。不过此前有消息提到,宝沃可能将会在北京车展上推出BX7的纯电动版本BXi7。因而这8款车型或许是当前两款车型及后续新车的不同动力总成版本。
从这个概念也可以看出,宝沃对工厂的期望是,在后续新产品跟上时,能够尽快地投入生产并下线,避免产品在生产阶段出现乏力过程。
众所周知,从智能化程度来说,要想混线生产8款不同产品,要求是很高的。不仅是生产线本身的智能化程度,车辆零部件的通用性、车身底盘的平台化设计都是必须的。那么,宝沃工厂是怎么实现的呢?
我们先看两个关键部分。
首先是柔性化针对的内容。根据工厂经理的介绍,工厂生产线可以生产轿车与SUV,所有可生产的车型,最大尺寸在5300ⅹ2000ⅹ1850mm以内,最大质量在2300公斤以下,轴距范围在2300-3200mm之间。因而,宝沃工厂是在工装设备与生产线的选择设计时考虑到,其能够满足不同尺寸、重量与轴距的车型需求。
然后是自动化设备与管理体系。
根据宝沃官方介绍资料,目前宝沃工厂的自动化机器人有547台:其中冲压22台,包括运输机器人与自动装箱机器人;车身443台,主要完成点焊、弧焊、螺柱焊、车顶激光钎焊,涂胶、滚边以及打磨等连接工艺的自动化;油漆车间76台,主要完成内外表面自动化喷涂以及车身底部涂胶的自动化;总装车间6台,主要完成玻璃涂胶和安装的自动化。
在制造的供应管理系统中,据介绍,宝沃也设有订单管理与物流管理体系,能够根据具体订单进行生产,实现某种程度上的定制化设计,订单交付周期最短是23天。这里的定制化设计当然是有条件的。生产线具备多车型混线生产能力,如果是具体到特定车型,则会是在选装配置与车身颜色等的区别。
从自动化设备的设置中可以看到,为了让工厂具备多车型混线生产的能力,除了冲压车间之外,宝沃是在重点工艺,即是涉及到大部件的连接、拼装等地,进行了自动化的设计来提高生产效率。具体到不同的工艺中,自动化的设计也有所不同。
在冲压车间,当前的生产过程基本实现了100%自动化。根据冲压车间负责人的介绍,冲压车间同时保持在工作状态的工厂是18名,主要是用在监控设备的运行、模具更换、下线后的产品检测环节。
与焊装、总装等工艺不同,冲压并非是混线生产的方式,而是一个冲压模具对应一个零件。冲压车间会根据工厂的整体产量、库存量设置每一个零件的生产数量,一次性生产完成后,再更换成下一个零件的模具进行生产,生产以3天为一周期,模具更换的时间为3分钟。从生产效率来说,某个零件生产得越多当然效率越高,因为省去了更换模具与原材料的时间。但是同样的,如果不能与产能想匹配,那么库存也会越多。
在生产过程中,每一个生产零件都有编号,模具会与管理系统连接,查看当前零件编号是否属于与模具相对应,以免出现误加工。
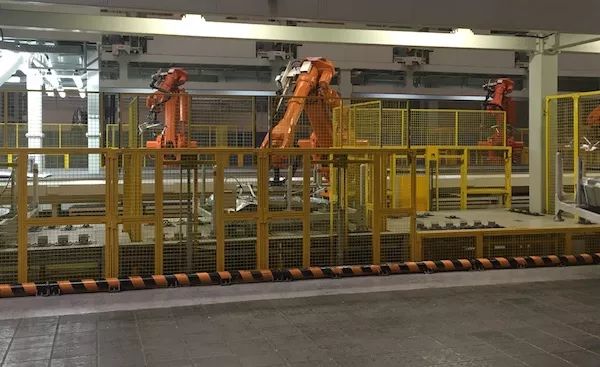
▲冲压车间自动装箱机器人
而为了实现冲压件的自动装箱,在产品下线处设有一个照相设备。照相设备拍照后会检测出冲压件在产线上的定位并将其发给装箱机器人,装箱机器人会根据定位调整吸附的角度,以便于冲压件能够装入对应的容器中。在容器存满后的转运过程则是由人工运输完成。
一般来说车身的焊装车间是相对容易实现90%以上的高自动化率车身,而宝沃的车身车间目前是60%。在参观时,车云菌发现,大部分的分装线焊接均是人工完成,而在车身总拼的工位则是自动化设备完成,为了满足8车型需求,设有可以满足8种不同车身总拼的工装设备。与冲压不同,因为需要完成混线生产,因而车间的生产管理系统的内容会更加复杂。
相比之下,总装车身的自动化率要更低。前面提到,总装车间的自动化率是在玻璃的涂胶与安装工位上,设有6台机器人,可以实现前后风挡玻璃的自动涂胶与安装,包括监测定位、涂胶与安装三类机器人。
另外,在总装车间,还设有AVG车辆。我们知道,AVG可以根据预先设好的路线(铺在路面的磁条)自动运行,一般用来进行车间内的物流运送。宝沃总装车间中,AVG用在部分生产线中运输大型部件,比如将底盘运送到“结婚”工位。
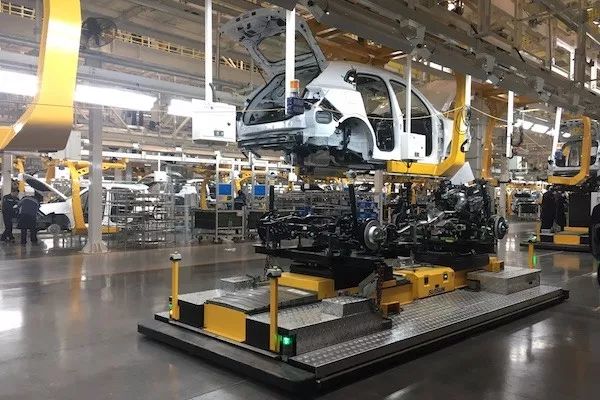
▲AVG车辆运送底盘到结婚工位
可以说,宝沃工厂是在柔性化与自动化之间进行了平衡。前面提到,要完成实现8车型的柔性化生产,如果又同时要求高自动化率,那么也就意味着工厂内智能化设备的量级式增加,随之而来的,是整个生产管理系统在管理控制上的复杂化。而这,都是需要时间来逐步提升的。在有限的时间中,优先解决最关键的需求,再逐步升级,或许也不失为一条路线。
在宝沃工厂的对外介绍上,都提到工厂内「可以实现8车型混线生产」的生产系统,在二期建设完成后,可以实现年产量36万台。当然,当前宝沃只有BX5和BX7两款车型。而且对于一个复活时间尚且不长的汽车品牌来说,短期内推出8款完全不同的车型也是不太可能的。不过此前有消息提到,宝沃可能将会在北京车展上推出BX7的纯电动版本BXi7。因而这8款车型或许是当前两款车型及后续新车的不同动力总成版本。
从这个概念也可以看出,宝沃对工厂的期望是,在后续新产品跟上时,能够尽快地投入生产并下线,避免产品在生产阶段出现乏力过程。
众所周知,从智能化程度来说,要想混线生产8款不同产品,要求是很高的。不仅是生产线本身的智能化程度,车辆零部件的通用性、车身底盘的平台化设计都是必须的。那么,宝沃工厂是怎么实现的呢?
我们先看两个关键部分。
首先是柔性化针对的内容。根据工厂经理的介绍,工厂生产线可以生产轿车与SUV,所有可生产的车型,最大尺寸在5300ⅹ2000ⅹ1850mm以内,最大质量在2300公斤以下,轴距范围在2300-3200mm之间。因而,宝沃工厂是在工装设备与生产线的选择设计时考虑到,其能够满足不同尺寸、重量与轴距的车型需求。
然后是自动化设备与管理体系。
根据宝沃官方介绍资料,目前宝沃工厂的自动化机器人有547台:其中冲压22台,包括运输机器人与自动装箱机器人;车身443台,主要完成点焊、弧焊、螺柱焊、车顶激光钎焊,涂胶、滚边以及打磨等连接工艺的自动化;油漆车间76台,主要完成内外表面自动化喷涂以及车身底部涂胶的自动化;总装车间6台,主要完成玻璃涂胶和安装的自动化。
在制造的供应管理系统中,据介绍,宝沃也设有订单管理与物流管理体系,能够根据具体订单进行生产,实现某种程度上的定制化设计,订单交付周期最短是23天。这里的定制化设计当然是有条件的。生产线具备多车型混线生产能力,如果是具体到特定车型,则会是在选装配置与车身颜色等的区别。
从自动化设备的设置中可以看到,为了让工厂具备多车型混线生产的能力,除了冲压车间之外,宝沃是在重点工艺,即是涉及到大部件的连接、拼装等地,进行了自动化的设计来提高生产效率。具体到不同的工艺中,自动化的设计也有所不同。
在冲压车间,当前的生产过程基本实现了100%自动化。根据冲压车间负责人的介绍,冲压车间同时保持在工作状态的工厂是18名,主要是用在监控设备的运行、模具更换、下线后的产品检测环节。
与焊装、总装等工艺不同,冲压并非是混线生产的方式,而是一个冲压模具对应一个零件。冲压车间会根据工厂的整体产量、库存量设置每一个零件的生产数量,一次性生产完成后,再更换成下一个零件的模具进行生产,生产以3天为一周期,模具更换的时间为3分钟。从生产效率来说,某个零件生产得越多当然效率越高,因为省去了更换模具与原材料的时间。但是同样的,如果不能与产能想匹配,那么库存也会越多。
在生产过程中,每一个生产零件都有编号,模具会与管理系统连接,查看当前零件编号是否属于与模具相对应,以免出现误加工。
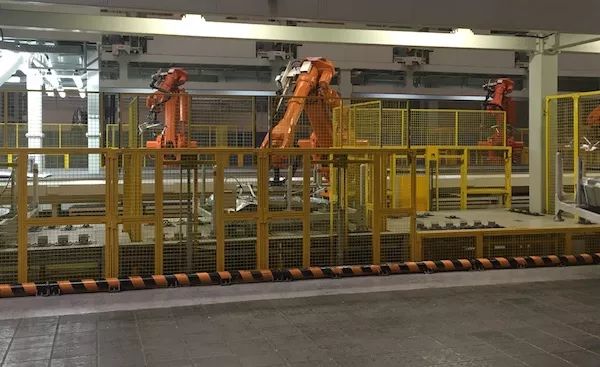
▲冲压车间自动装箱机器人
而为了实现冲压件的自动装箱,在产品下线处设有一个照相设备。照相设备拍照后会检测出冲压件在产线上的定位并将其发给装箱机器人,装箱机器人会根据定位调整吸附的角度,以便于冲压件能够装入对应的容器中。在容器存满后的转运过程则是由人工运输完成。
一般来说车身的焊装车间是相对容易实现90%以上的高自动化率车身,而宝沃的车身车间目前是60%。在参观时,车云菌发现,大部分的分装线焊接均是人工完成,而在车身总拼的工位则是自动化设备完成,为了满足8车型需求,设有可以满足8种不同车身总拼的工装设备。与冲压不同,因为需要完成混线生产,因而车间的生产管理系统的内容会更加复杂。
相比之下,总装车身的自动化率要更低。前面提到,总装车间的自动化率是在玻璃的涂胶与安装工位上,设有6台机器人,可以实现前后风挡玻璃的自动涂胶与安装,包括监测定位、涂胶与安装三类机器人。
另外,在总装车间,还设有AVG车辆。我们知道,AVG可以根据预先设好的路线(铺在路面的磁条)自动运行,一般用来进行车间内的物流运送。宝沃总装车间中,AVG用在部分生产线中运输大型部件,比如将底盘运送到“结婚”工位。
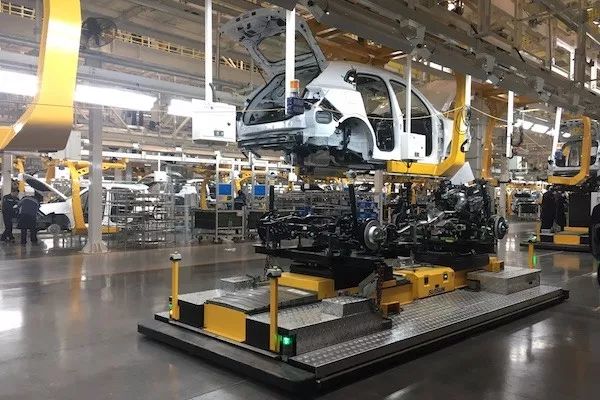
▲AVG车辆运送底盘到结婚工位
可以说,宝沃工厂是在柔性化与自动化之间进行了平衡。前面提到,要完成实现8车型的柔性化生产,如果又同时要求高自动化率,那么也就意味着工厂内智能化设备的量级式增加,随之而来的,是整个生产管理系统在管理控制上的复杂化。而这,都是需要时间来逐步提升的。在有限的时间中,优先解决最关键的需求,再逐步升级,或许也不失为一条路线。
编辑推荐
最新资讯
-
2025上海国际汽车成形制造产业对话会
2025-04-26 19:14
-
旭化成微电子开始批量生产用于环保发
2025-04-24 16:00
-
华为、地平线、大众、东风、起亚等引
2025-04-24 08:27
-
全球产业链聚沪 共探双碳新路径 SNEC
2025-04-18 18:05
-
柯马签订具有约束力的协议收购 Autom
2025-04-17 13:01