简单分析铝合金物流车用水性聚氨酯涂料的应用性
2018-03-14 09:07:52· 来源:第15届环保车用涂料及涂装年会 作者:陈杰 郭鹏 来信 赵辉 刘正堂 刘宪文
铝合金车作为轻量化物流车的一个发展方向,近些年具有较大程度的增长,但是由于铝合金表面氧化膜的问题造成外观效果随着时间的延长而变差,然而随着车厢材质由钢铁转变为铝合金等的变化,为了更好的装饰和防止氧化腐蚀,涂料的种类和品质也发生很大的改变。
引言
铝合金车作为轻量化物流车的一个发展方向,近些年具有较大程度的增长,但是由于铝合金表面氧化膜的问题造成外观效果随着时间的延长而变差,然而随着车厢材质由钢铁转变为铝合金等的变化,为了更好的装饰和防止氧化腐蚀,涂料的种类和品质也发生很大的改变。通过水性聚氨酯涂料来进一步抑制其氧化膜的形成,并达到装饰美观的外观效果是近些年发展起来的一条便捷而更环保的解决方案。水性聚氨酯是用水作为溶剂,相较于传统的溶剂型聚氨酯具有无污染、安全可靠、机械性能优良等优点。随着国家对环境保护要求的进一步提高,尤其是控制有机挥发物(VOC)的排放,继北京市后,广州市、天津市、河北省等相关省市均出台了《工业企业挥发性有机物排放控制标准》等相应的控制VOC的管理办法,所以水性化涂料产品作为低VOC产品的发展方向的一个分支,具有更大的市场潜力,本实验旨在为某汽车公司开发的铝合金物流车上研发一支具有良好附着力和耐候性的环保型水性聚氨酯产品。
1 试验部分
1.1 原材料
本实验中应用的主要原材料,相关的指标、技术参数等见表1所示:
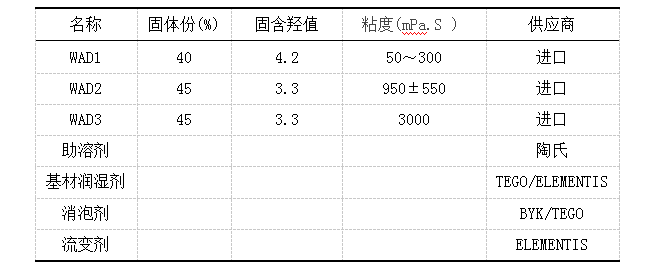
表1 制备水性聚氨酯的主要原材
1.2 涂料制备
涂料的制备方式为:将部分水加入烧杯中,在搅拌下将分散剂、消泡剂、胺中和剂、助溶剂等依次加入,低速分散5~10min,然后在搅拌下将颜填料加入,先低速搅拌均匀,再提高搅拌速度分散30min,使浆料达到控制的细度(≤20um),最后在低速搅拌下将分散体、流变剂和流平剂依次加入,用剩余的去离子水将搅拌杆进行冲洗后测试其浆料的pH值,合格后即得相应的涂料产品。
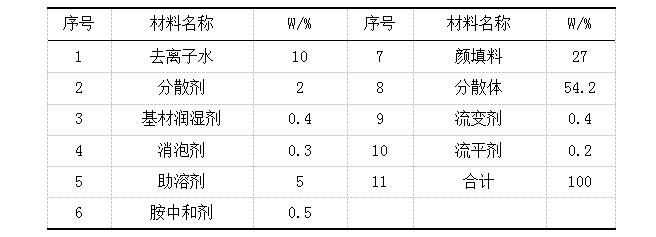
表2 涂料基础配方
1.3 涂装
本产品为双组份产品,添加固化剂时需要在搅拌下加入,将主剂在搅拌下加入固化剂,搅拌3~5min后,在搅拌下将去离子水按量加入,调整喷涂粘度到50s/-4/23℃,在湿度≤70%且通风良好的环境下喷涂测试板,涂装好后晾置30min,用80℃烘箱烘烤40min,即可成透明膜。
1.4 涂膜性能测试
涂膜性能测试的项目以及依据的标准如表3所示。
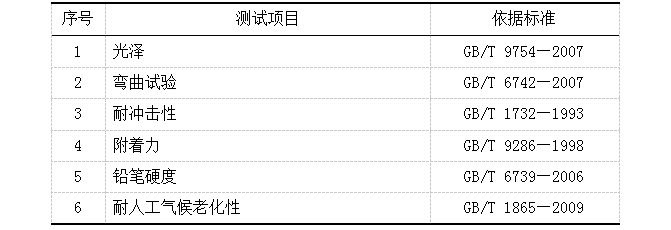
表3 测试项目及相关标准
2 结果与讨论
2.1 水性树脂的选择
由于本实验的基材为铝合金基材,客户要求附着力佳,耐候性良好,并且要求涂膜对光泽≥85%,所以在选择水性树脂时选择二次分散体作为其主体的成膜物,因为二级分散体具有粒径小、光泽高、流平性好、储存稳定等的特点,本实验选择了国外三家公司的水性羟基丙烯酸分散体,分别做成清漆,涂覆在铝合金上测试其附着力以及别的相关性能,其结果如表4。
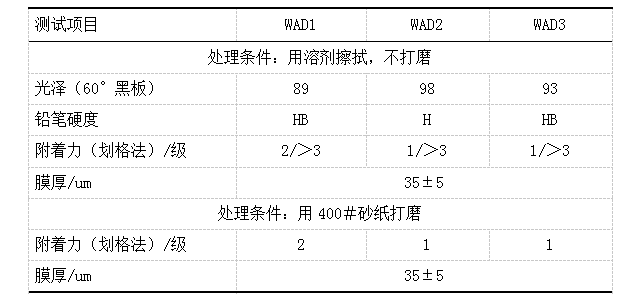
表4 水性聚氨酯清漆在铝合金板上的物理机械性能
在试验水性聚氨酯清漆的过程中发现,三支清漆在铝合金表面均可以良好的涂装,并且具有较高的光泽,符合客户要求的光泽(≥85%),但是在检测附着力时发现,在不同的位置测试出来的附着力有较大的差异,其中大部分是合格的,但是总有一些位置出现附着力非常差,甚至出现胶带将局部1~2cm2范围内的漆膜全撕掉,此现象在三支产品中均表现出来,通过用溶剂清洗铝合金表面,以及擦拭等方法均无法使全部表面的附着力做到一致,总会出现一两个检测点的附着力特别差的情况,经过分析了解到,铝合金表面存在一种氧化膜,一种是在大气中氧化形成的膜层,δ约为4~5nm,这层膜结构疏松;另外一种是采用化学氧化法或电化学氧化在铝合金表面形成的氧化膜,膜厚可达数百微米,具有高硬度,高耐磨,具有强吸附能力和耐腐蚀力。本实验所采用的铝合金板是采用阳极化成膜的,阳极氧化膜的横截面为六角形的蜂窝状结构,中间有一个圆形的空洞,其单元尺寸一般小于100nm,微孔孔径一般小于20nm,微孔的密度达到760 亿个/ 平方厘米。氧化膜单元的厚度一般以微米为单元。如果氧化膜的厚度为10 um,那么其高度约为孔径的500 倍以上。所以其表面积仍很大,容易造成不同程度的局部污染,即使用溶剂擦拭,仍然出现涂膜局部附着力不合格的问题。通过分析其具体的原因,最后选择用打磨的方法来解决其局部污染或后处理不干净造成附着力差异性的问题,整体打磨后重新喷涂,干燥后在不同位置测试,其附着力均一致。通过表4的检测结果可以看出WAD2和WAD3两支水性分散体在铝合金上的附着力较好,均达到了1级。
2.2 助剂的选择
由于水的表面张力随着温度的升高而降低,在常温下(以20℃来计)的表面张力为72.7mN/m,而常规溶剂的表面张力一般在20~30 mN/m,水的表面张力高的多,所以在金属基材上不易更好的铺展,同时还容易形成厚边、流平不好,以及起泡等问题,所以本研究主要对针对水性聚氨酯中应用的消泡剂和基材润湿剂进行了筛选,筛选办法为,取10g分散体,按每种消泡剂推荐量的最大值加入,然后在玻璃板上涂膜查看其是否有发白、缩孔等问题,其中涂膜出现缩孔等问题的消泡剂排除掉不再评价其消泡能力,具体如表5所示。涂料对基材的润湿性及铺展性是通过筛选基材润湿剂来评估的,具体如表6所示。从表5和表6可以看出,单从混溶性来看BYK-1711、Foamex 7447、Foamex K3是比较适合WAD2分散体的,而Foamex 825和Airex 902w是比较适合WAD3分散体,但是再考虑消泡能力来分析,可以看出BYK-1711更适合WAD1,而Foamex 825更加适合WAD3。
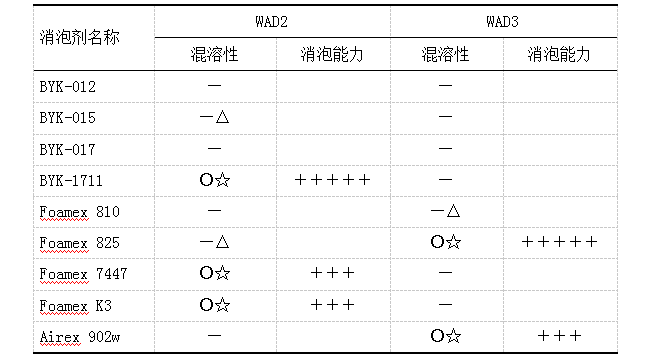
表5 消泡剂的筛选
注:表格中符号的含义,缩孔符号:—;无缩孔符号:○;混溶发白符号:△;透明:☆;消泡能力用“+”表示,其中最强为“+++++”;“++”以下不合格。
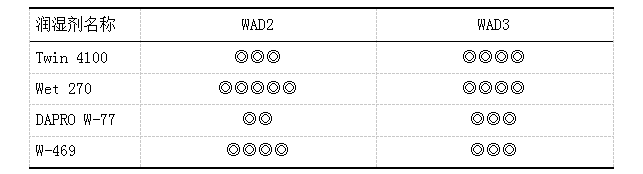
表6 基材润湿性的筛选
注:基材的润湿性用“◎”表示,其中“◎◎◎◎◎”为基材润湿良好,流平性最佳;“◎◎”以下不合格,“◎”为流平性不良,缩边严重。
2.3 助溶剂的选择
助溶剂在水性聚氨酯中起的主要作用是更好的搭接水相/油相,同时还可以更好的调节体系的粘度、流变性,并降低体系的最低成膜温度,在一定程度上还可以提高涂膜的光泽和流平性,降低分散体的Tg,使得聚氨酯树脂有足够时间来相互聚结,形成分子链段相互渗透的涂膜,使漆膜具有更好的密闭性。本实验对比了不同助溶剂对水性聚氨酯涂膜的光泽,涂装厚度,以及外观的影响,具体如表7所示,从表7可以看出,DPnB和DB添加相同量时均可使水性聚氨酯涂膜的膜厚达到60 um,同时流平性性较好,而DPM要稍差一些。
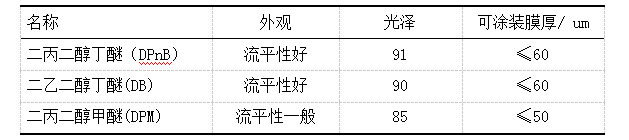
表7 助溶剂对涂膜的性能影响
2.4 n(-NCO)/n(-OH)比例对涂层性能的影响
由于异氰酸酯(-NCO)和水也可以发生反应放出CO2,尤其在固化剂刚加入水性聚氨酯主漆中时,初期较快的反应会促使漆浆粘度提升比较明显,而且在涂装后对涂层的光泽、硬度等性能的影响也较为明显,本实验测试了n(-NCO)/n(-OH)不同比例时,漆膜的性能如表8所示,从表8可以看出当n(-NCO)/n(-OH)的比例控制在1.5或1.7时,涂膜的相关物理机械性能均达到较佳的效果。
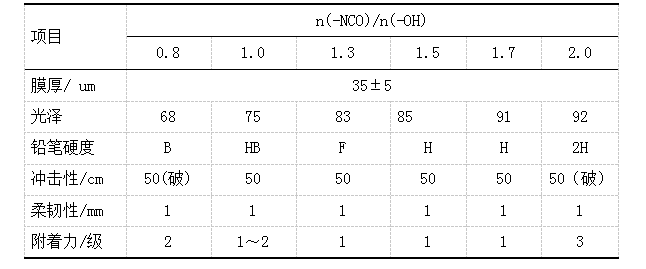
表8 不同n(-NCO)/n(-OH)对涂膜性能的影响
2.5 施工条件对涂层外观的影响
水在一个大气压(0.1MPa)下,100℃时的气化潜热为40.63KJ/mol,而溶剂型涂料所用的烷烃类溶剂的蒸发潜热一般在20~30KJ/mol的范围[10],水的蒸发潜热高的多,所以水分难以在低温时挥发出来,这也造成水性漆对涂装环境,干燥环境的温湿度,以及通风情况的要求比较高,一般建议湿度小于70%,温度高于10℃,具有良好的通风情况,温度低时需要循环热风,这样可以更好的促进水分挥发,本实验研究在喷涂厚度为60±5 um时,表干不同时间后在80℃的烘烤条件下,对涂膜外观的影响,具体如表9所示。由表9可以看出,60±5 um厚度的干膜,需要的干燥时间条件为:表干20min,80℃烘烤40min,在铝合金板上的附着力为1级。由此也可看出,要获得良好的外观,烘烤前需要一定的晾干,促使部分水份提前挥发,同时更好的流平。
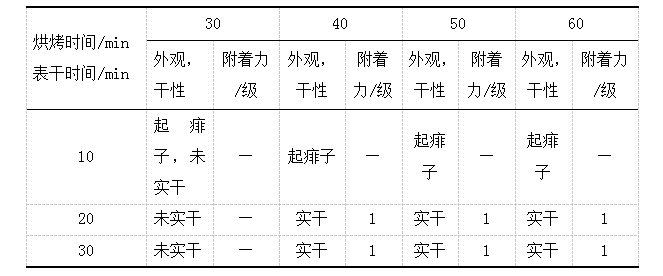
表9 不同表干和烘烤时间对涂膜外观的影响
2.6 涂层的性能结果
根据客户的需求,在铝合金板上试验不同的水性羟基丙烯酸分散体,其中WAD2和WAD3均可达到客户的需求,但是通过表10可以看出,WAD2和WAD3两支分散体的各项物理化学指标均相似,但是WAD2在耐酸性和耐人工老化性方面比WAD3具有更优越的性能,但是两支产品均可达到客户在铝合金车辆上的要求,按较高的要求选择WAD2作为最终的定型产品。
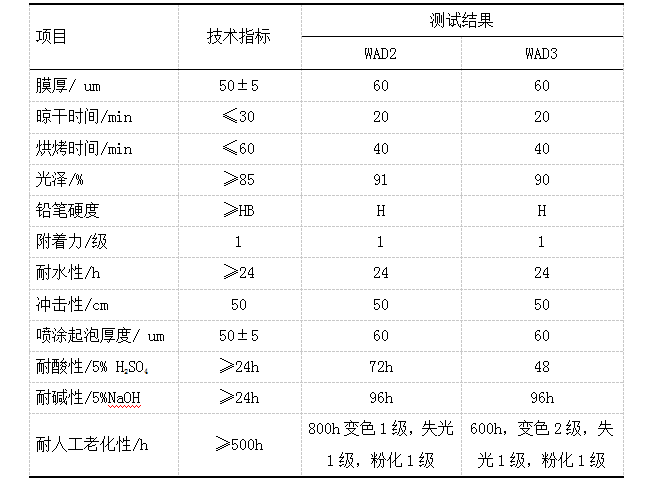
表10 涂层的性能结果
总结
本研究试验了不同的水性分散体固化后在阳极化处理的铝合金基材上的各项性能,通过对涂料所用的分散体、助剂、助溶剂、n(-NCO)/n(-OH)比例、施工条件的试验得出以下结论:1.阳极化的铝合金基材上不容易处理干净,正常涂膜存在附着力差异性,通过打磨处理可以更好的解决此问题;2.DPnB和DB在本体系中均使涂膜的干膜厚度达到60 um,同时涂膜的流平性和光泽均较佳;3.当n(-NCO)/n(-OH)的比例控制在1.5或1.7时,涂膜的相关物理机械性能均达到较佳的效果;4.烘烤工艺来干燥水性聚氨酯需要足够的时间来进行初步的水份挥发和涂膜流平。
铝合金车作为轻量化物流车的一个发展方向,近些年具有较大程度的增长,但是由于铝合金表面氧化膜的问题造成外观效果随着时间的延长而变差,然而随着车厢材质由钢铁转变为铝合金等的变化,为了更好的装饰和防止氧化腐蚀,涂料的种类和品质也发生很大的改变。通过水性聚氨酯涂料来进一步抑制其氧化膜的形成,并达到装饰美观的外观效果是近些年发展起来的一条便捷而更环保的解决方案。水性聚氨酯是用水作为溶剂,相较于传统的溶剂型聚氨酯具有无污染、安全可靠、机械性能优良等优点。随着国家对环境保护要求的进一步提高,尤其是控制有机挥发物(VOC)的排放,继北京市后,广州市、天津市、河北省等相关省市均出台了《工业企业挥发性有机物排放控制标准》等相应的控制VOC的管理办法,所以水性化涂料产品作为低VOC产品的发展方向的一个分支,具有更大的市场潜力,本实验旨在为某汽车公司开发的铝合金物流车上研发一支具有良好附着力和耐候性的环保型水性聚氨酯产品。
1 试验部分
1.1 原材料
本实验中应用的主要原材料,相关的指标、技术参数等见表1所示:
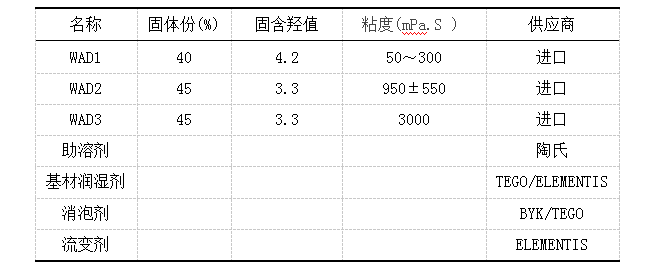
表1 制备水性聚氨酯的主要原材
1.2 涂料制备
涂料的制备方式为:将部分水加入烧杯中,在搅拌下将分散剂、消泡剂、胺中和剂、助溶剂等依次加入,低速分散5~10min,然后在搅拌下将颜填料加入,先低速搅拌均匀,再提高搅拌速度分散30min,使浆料达到控制的细度(≤20um),最后在低速搅拌下将分散体、流变剂和流平剂依次加入,用剩余的去离子水将搅拌杆进行冲洗后测试其浆料的pH值,合格后即得相应的涂料产品。
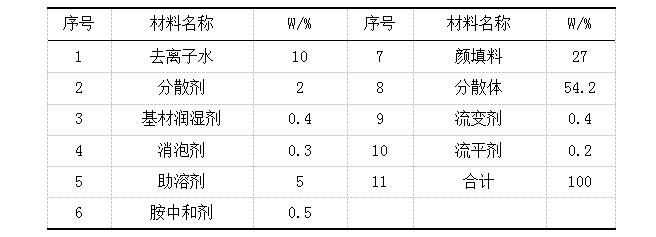
表2 涂料基础配方
1.3 涂装
本产品为双组份产品,添加固化剂时需要在搅拌下加入,将主剂在搅拌下加入固化剂,搅拌3~5min后,在搅拌下将去离子水按量加入,调整喷涂粘度到50s/-4/23℃,在湿度≤70%且通风良好的环境下喷涂测试板,涂装好后晾置30min,用80℃烘箱烘烤40min,即可成透明膜。
1.4 涂膜性能测试
涂膜性能测试的项目以及依据的标准如表3所示。
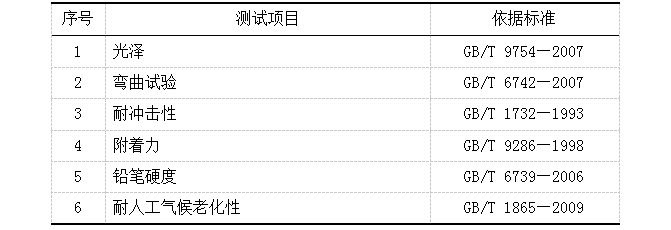
表3 测试项目及相关标准
2 结果与讨论
2.1 水性树脂的选择
由于本实验的基材为铝合金基材,客户要求附着力佳,耐候性良好,并且要求涂膜对光泽≥85%,所以在选择水性树脂时选择二次分散体作为其主体的成膜物,因为二级分散体具有粒径小、光泽高、流平性好、储存稳定等的特点,本实验选择了国外三家公司的水性羟基丙烯酸分散体,分别做成清漆,涂覆在铝合金上测试其附着力以及别的相关性能,其结果如表4。
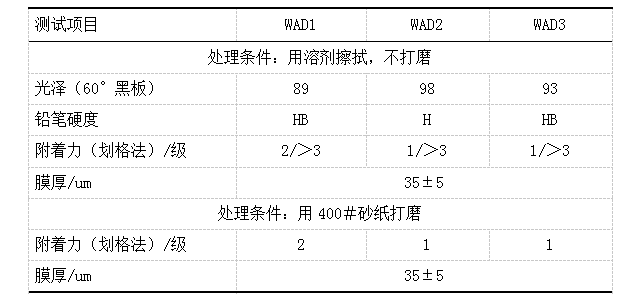
表4 水性聚氨酯清漆在铝合金板上的物理机械性能
在试验水性聚氨酯清漆的过程中发现,三支清漆在铝合金表面均可以良好的涂装,并且具有较高的光泽,符合客户要求的光泽(≥85%),但是在检测附着力时发现,在不同的位置测试出来的附着力有较大的差异,其中大部分是合格的,但是总有一些位置出现附着力非常差,甚至出现胶带将局部1~2cm2范围内的漆膜全撕掉,此现象在三支产品中均表现出来,通过用溶剂清洗铝合金表面,以及擦拭等方法均无法使全部表面的附着力做到一致,总会出现一两个检测点的附着力特别差的情况,经过分析了解到,铝合金表面存在一种氧化膜,一种是在大气中氧化形成的膜层,δ约为4~5nm,这层膜结构疏松;另外一种是采用化学氧化法或电化学氧化在铝合金表面形成的氧化膜,膜厚可达数百微米,具有高硬度,高耐磨,具有强吸附能力和耐腐蚀力。本实验所采用的铝合金板是采用阳极化成膜的,阳极氧化膜的横截面为六角形的蜂窝状结构,中间有一个圆形的空洞,其单元尺寸一般小于100nm,微孔孔径一般小于20nm,微孔的密度达到760 亿个/ 平方厘米。氧化膜单元的厚度一般以微米为单元。如果氧化膜的厚度为10 um,那么其高度约为孔径的500 倍以上。所以其表面积仍很大,容易造成不同程度的局部污染,即使用溶剂擦拭,仍然出现涂膜局部附着力不合格的问题。通过分析其具体的原因,最后选择用打磨的方法来解决其局部污染或后处理不干净造成附着力差异性的问题,整体打磨后重新喷涂,干燥后在不同位置测试,其附着力均一致。通过表4的检测结果可以看出WAD2和WAD3两支水性分散体在铝合金上的附着力较好,均达到了1级。
2.2 助剂的选择
由于水的表面张力随着温度的升高而降低,在常温下(以20℃来计)的表面张力为72.7mN/m,而常规溶剂的表面张力一般在20~30 mN/m,水的表面张力高的多,所以在金属基材上不易更好的铺展,同时还容易形成厚边、流平不好,以及起泡等问题,所以本研究主要对针对水性聚氨酯中应用的消泡剂和基材润湿剂进行了筛选,筛选办法为,取10g分散体,按每种消泡剂推荐量的最大值加入,然后在玻璃板上涂膜查看其是否有发白、缩孔等问题,其中涂膜出现缩孔等问题的消泡剂排除掉不再评价其消泡能力,具体如表5所示。涂料对基材的润湿性及铺展性是通过筛选基材润湿剂来评估的,具体如表6所示。从表5和表6可以看出,单从混溶性来看BYK-1711、Foamex 7447、Foamex K3是比较适合WAD2分散体的,而Foamex 825和Airex 902w是比较适合WAD3分散体,但是再考虑消泡能力来分析,可以看出BYK-1711更适合WAD1,而Foamex 825更加适合WAD3。
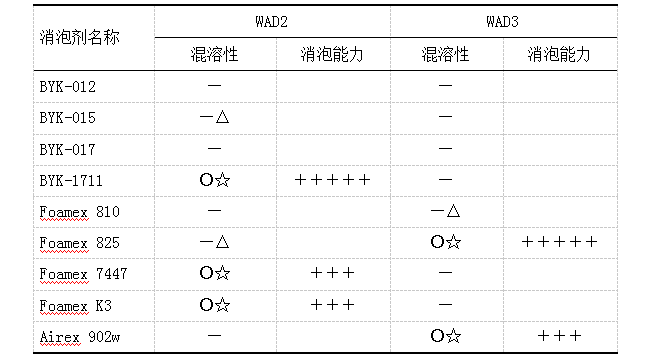
表5 消泡剂的筛选
注:表格中符号的含义,缩孔符号:—;无缩孔符号:○;混溶发白符号:△;透明:☆;消泡能力用“+”表示,其中最强为“+++++”;“++”以下不合格。
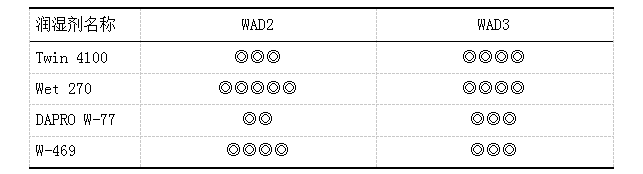
表6 基材润湿性的筛选
注:基材的润湿性用“◎”表示,其中“◎◎◎◎◎”为基材润湿良好,流平性最佳;“◎◎”以下不合格,“◎”为流平性不良,缩边严重。
2.3 助溶剂的选择
助溶剂在水性聚氨酯中起的主要作用是更好的搭接水相/油相,同时还可以更好的调节体系的粘度、流变性,并降低体系的最低成膜温度,在一定程度上还可以提高涂膜的光泽和流平性,降低分散体的Tg,使得聚氨酯树脂有足够时间来相互聚结,形成分子链段相互渗透的涂膜,使漆膜具有更好的密闭性。本实验对比了不同助溶剂对水性聚氨酯涂膜的光泽,涂装厚度,以及外观的影响,具体如表7所示,从表7可以看出,DPnB和DB添加相同量时均可使水性聚氨酯涂膜的膜厚达到60 um,同时流平性性较好,而DPM要稍差一些。
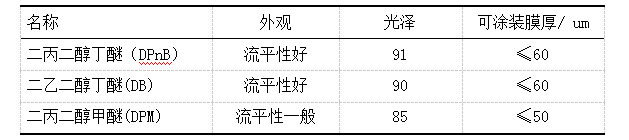
表7 助溶剂对涂膜的性能影响
2.4 n(-NCO)/n(-OH)比例对涂层性能的影响
由于异氰酸酯(-NCO)和水也可以发生反应放出CO2,尤其在固化剂刚加入水性聚氨酯主漆中时,初期较快的反应会促使漆浆粘度提升比较明显,而且在涂装后对涂层的光泽、硬度等性能的影响也较为明显,本实验测试了n(-NCO)/n(-OH)不同比例时,漆膜的性能如表8所示,从表8可以看出当n(-NCO)/n(-OH)的比例控制在1.5或1.7时,涂膜的相关物理机械性能均达到较佳的效果。
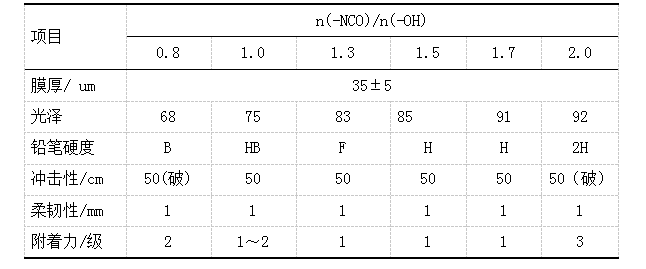
表8 不同n(-NCO)/n(-OH)对涂膜性能的影响
2.5 施工条件对涂层外观的影响
水在一个大气压(0.1MPa)下,100℃时的气化潜热为40.63KJ/mol,而溶剂型涂料所用的烷烃类溶剂的蒸发潜热一般在20~30KJ/mol的范围[10],水的蒸发潜热高的多,所以水分难以在低温时挥发出来,这也造成水性漆对涂装环境,干燥环境的温湿度,以及通风情况的要求比较高,一般建议湿度小于70%,温度高于10℃,具有良好的通风情况,温度低时需要循环热风,这样可以更好的促进水分挥发,本实验研究在喷涂厚度为60±5 um时,表干不同时间后在80℃的烘烤条件下,对涂膜外观的影响,具体如表9所示。由表9可以看出,60±5 um厚度的干膜,需要的干燥时间条件为:表干20min,80℃烘烤40min,在铝合金板上的附着力为1级。由此也可看出,要获得良好的外观,烘烤前需要一定的晾干,促使部分水份提前挥发,同时更好的流平。
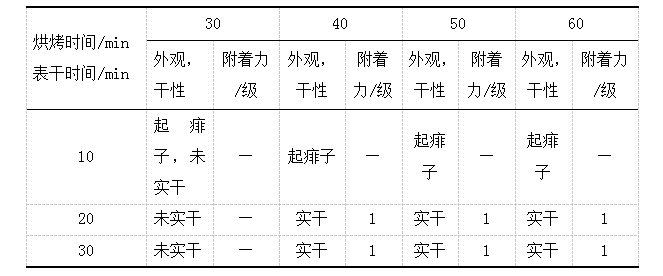
表9 不同表干和烘烤时间对涂膜外观的影响
2.6 涂层的性能结果
根据客户的需求,在铝合金板上试验不同的水性羟基丙烯酸分散体,其中WAD2和WAD3均可达到客户的需求,但是通过表10可以看出,WAD2和WAD3两支分散体的各项物理化学指标均相似,但是WAD2在耐酸性和耐人工老化性方面比WAD3具有更优越的性能,但是两支产品均可达到客户在铝合金车辆上的要求,按较高的要求选择WAD2作为最终的定型产品。
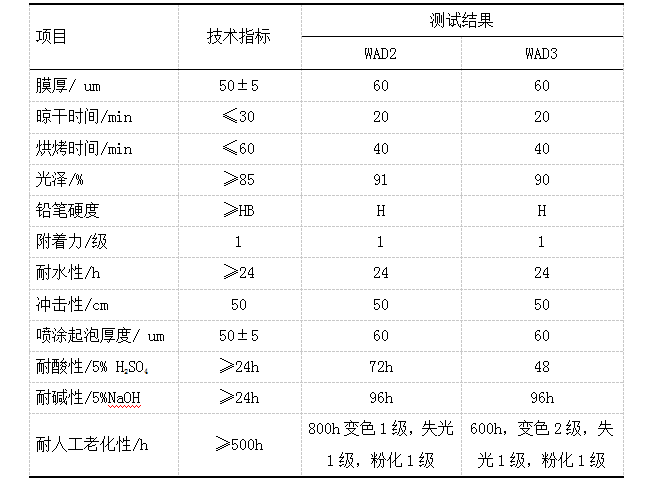
表10 涂层的性能结果
总结
本研究试验了不同的水性分散体固化后在阳极化处理的铝合金基材上的各项性能,通过对涂料所用的分散体、助剂、助溶剂、n(-NCO)/n(-OH)比例、施工条件的试验得出以下结论:1.阳极化的铝合金基材上不容易处理干净,正常涂膜存在附着力差异性,通过打磨处理可以更好的解决此问题;2.DPnB和DB在本体系中均使涂膜的干膜厚度达到60 um,同时涂膜的流平性和光泽均较佳;3.当n(-NCO)/n(-OH)的比例控制在1.5或1.7时,涂膜的相关物理机械性能均达到较佳的效果;4.烘烤工艺来干燥水性聚氨酯需要足够的时间来进行初步的水份挥发和涂膜流平。
编辑推荐
最新资讯
-
思看科技受邀出席第三届联合国教科文
2025-04-27 13:29
-
聚势谋远,智领新程——五菱柳机以硬
2025-04-27 13:22
-
聚势求新、智驱未来——五菱工业底盘
2025-04-27 13:22
-
向轻量化、智能化迈进,助力建设国家
2025-04-27 13:21
-
五菱工业:以“中国智造”领跑绿色未
2025-04-27 13:21