弧齿锥齿轮热后硬齿面刮削工艺试验
2018-04-10 08:50:42· 来源:齿轮传动
汽车驱动桥作为汽车的重要传动部件,对整车的承载能力和舒适性有很大影响,其中主被动锥齿轮是驱动桥中最重要的零件。传统的弧齿锥齿轮加工流程为制坯—软齿面切削(干切或湿切)—热处理—热后研齿或磨齿。
汽车驱动桥作为汽车的重要传动部件,对整车的承载能力和舒适性有很大影响,其中主被动锥齿轮是驱动桥中最重要的零件。传统的弧齿锥齿轮加工流程为制坯—软齿面切削(干切或湿切)—热处理—热后研齿或磨齿。
常规的加工工艺过程中,在热前将齿面接触区修正完成后,由于材料或其他方面的原因,热处理变形的存在,导致热处理后齿面接触区形状与位置发生很大变化。为此,热后对齿面接触区修正成为必不可少的工序,目前国内应用较普遍的是研齿或磨齿工艺。
磨齿工艺的开展需要花费巨资引进弧齿磨齿机,与弧齿铣齿机相比较,弧齿磨齿机工艺复杂,机床调整繁琐,修要经常对砂轮进行修正。并且由于磨削过程中切削液的存在,不可避免会对环境产生影响。研齿工艺的开展,也需要引进研齿设备,并且机床调整较为复杂,由于研齿工艺无法修正变形较大的齿面接触区,只能对其做小部分修正。因此,研齿后的齿轮副其本身几何精度并无太大提高。
基于以上原因,需求更经济、环保有效的热后加工工艺成为必然选择。随着刀具材料技术和淬硬切削技术的进步,淬硬工件的加工已得到大规模推广应用。为此,决定尝试在弧齿锥齿轮铣齿机上,利用新型切削刀具,进行硬切削试验。
1.热后硬切削应用的可行性分析
本次工艺试验决定使用PCBN复合焊接刀具进行试验。PCBN即聚晶立方氮化硼(Polycrystalline Cubic Boron Nitride)作为利用人工方法合成的硬度仅次于天然金刚石的新型刀具材料,是目前高速切削铁系金属最合适的刀具材料。
根据相关资料介绍,用PCBN刀具加工淬硬钢时,要求工件淬火硬度高于60~65HRC,加工硬铸铁时,只要硬度达到中等硬度水平(45HRC),就会取得良好的加工效果。目前公司内被动锥齿轮热后内孔精加工即使用CBN刀片,切削余量为0.3mm,使用效果良好。而目前我公司内锥齿轮副热处理后硬度范围为58~62HRC,完全满足该类型刀具的使用条件,对其进行工艺试验完全可行。
PCBN刀具的制造主要通过CBN粉末和结合剂经超高压高温烧结而成.大致步骤有;混合粉末--模压成型/与硬质合金底层组装成整体--超高压高温烧结--深加工。在CBN聚晶体中也可以不加粘结剂直接烧结而成聚晶立方氮化硼。CBN在烧结时发生再结晶和晶粒长大过程,烧结后的CBN多晶体的晶粒已不是原来的CBN单晶体颗粒。这种PCBN刀具耐磨性好,寿命长,但较脆且温度条件苛刻,难以制成高韧性及大尺寸的刀片。 故本次试验中采用焊接式结构,将刀齿做成三部分结构。
本次工艺试验采用AC16被动锥齿轮进行,使用12英寸铣刀盘,其刀齿参数主要借鉴目前所使用的热前精切刀齿参数。刀齿由三部分组成:高速钢刀具基体、硬质合金基体、PCBN切削刃。各部分间焊接成型。
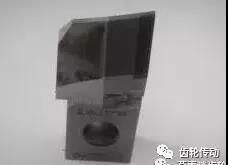
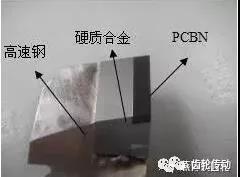
图1 复合式焊接刀具
2.热后硬切削切削参数的确定
根据相关资料介绍,PCBN刀具适合的切削速度为80-120m/min,结合刀具直径,算出的刀具转速应为:
n=1000*V/(3.14*d)=104r/min-125r/min
本次试验在格里森NO.26机床上进行,所选取的速度挂轮为:20/70*28/62,刀具主轴转速为114r/min。
PCBN刀具的吃刀量范围为0.15-0.25mm,本次切削试验中所采用的切削余量为0.2mm左右。进给量选择在0.03r/min。
3.热后硬切削工装设计
由于热处理前后的重复装夹,不可避免会在热后加工时出现乱齿现象,为此,对切齿工装更改了设计,增加一套对齿机构。此外,将定位碟簧尺寸进行了更改,使用了热后研配用碟簧,提高了工装整体的刚性。
4.热后硬切削加工情况
在本次工艺试验中,采用大轮双精刀盘进行加工,通过对齿机构的调整,实现了凹面与凸面的单独切削。切削过程中,机床无明显震动,刀具无损坏,加工中出现明显火花。由于切削热大部分被切屑带走,切屑颜色为微蓝色,因此,切削后工件仅有微热感。
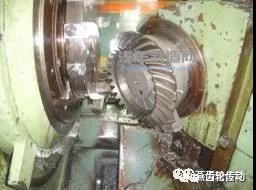
图2 切削情况
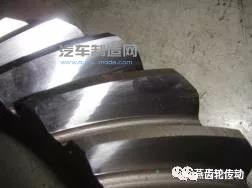
图3 切削后齿轮齿面
切削后工件表面发亮,粗糙度达到Ra0.5左右,高于外圆磨粗糙度。
5.热后硬加工质量情况
经过热后硬加工的零部件进行检测,齿圈跳动可达0.05,远低于产品图纸成品要求。与小轮研配后的齿面接触区如下:

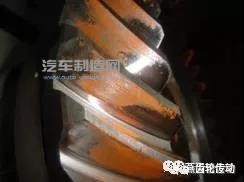
图4 成品接触区图片
距离啮合点0.5米时,检测噪音结果如下:
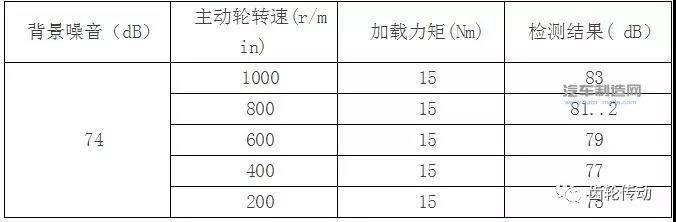
按常规工艺加工的齿轮副检测结果为:
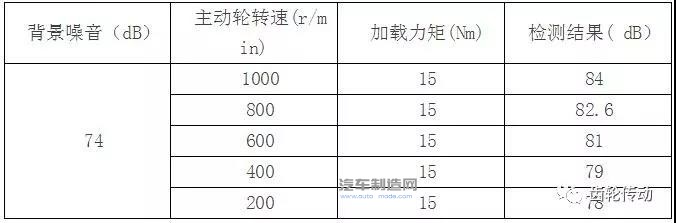
由此可以看出,热后切削加工的齿轮副其质量水平较正常加工零件质量要高。
6.结论
1.目前在国内,对于硬度超过HRC50的锥齿轮产品,大部分采取的为热后磨削工艺或者研齿工艺,热后硬切削加工方法和装备在中国重卡制造领域属于空白。对于我公司,此次为首次引进热后硬切削技术,属于公司内首创,且在国内重卡行业处于领先地位。
2.通过进行工艺试验,验证了热后弧齿锥齿轮硬齿面刮削工艺的可行性,为以后生产高精度齿轮副奠定了基础,加工后的齿轮副质量状况完全满足要求,从根本上消除了热处理变形对接触区的影响。
常规的加工工艺过程中,在热前将齿面接触区修正完成后,由于材料或其他方面的原因,热处理变形的存在,导致热处理后齿面接触区形状与位置发生很大变化。为此,热后对齿面接触区修正成为必不可少的工序,目前国内应用较普遍的是研齿或磨齿工艺。
磨齿工艺的开展需要花费巨资引进弧齿磨齿机,与弧齿铣齿机相比较,弧齿磨齿机工艺复杂,机床调整繁琐,修要经常对砂轮进行修正。并且由于磨削过程中切削液的存在,不可避免会对环境产生影响。研齿工艺的开展,也需要引进研齿设备,并且机床调整较为复杂,由于研齿工艺无法修正变形较大的齿面接触区,只能对其做小部分修正。因此,研齿后的齿轮副其本身几何精度并无太大提高。
基于以上原因,需求更经济、环保有效的热后加工工艺成为必然选择。随着刀具材料技术和淬硬切削技术的进步,淬硬工件的加工已得到大规模推广应用。为此,决定尝试在弧齿锥齿轮铣齿机上,利用新型切削刀具,进行硬切削试验。
1.热后硬切削应用的可行性分析
本次工艺试验决定使用PCBN复合焊接刀具进行试验。PCBN即聚晶立方氮化硼(Polycrystalline Cubic Boron Nitride)作为利用人工方法合成的硬度仅次于天然金刚石的新型刀具材料,是目前高速切削铁系金属最合适的刀具材料。
根据相关资料介绍,用PCBN刀具加工淬硬钢时,要求工件淬火硬度高于60~65HRC,加工硬铸铁时,只要硬度达到中等硬度水平(45HRC),就会取得良好的加工效果。目前公司内被动锥齿轮热后内孔精加工即使用CBN刀片,切削余量为0.3mm,使用效果良好。而目前我公司内锥齿轮副热处理后硬度范围为58~62HRC,完全满足该类型刀具的使用条件,对其进行工艺试验完全可行。
PCBN刀具的制造主要通过CBN粉末和结合剂经超高压高温烧结而成.大致步骤有;混合粉末--模压成型/与硬质合金底层组装成整体--超高压高温烧结--深加工。在CBN聚晶体中也可以不加粘结剂直接烧结而成聚晶立方氮化硼。CBN在烧结时发生再结晶和晶粒长大过程,烧结后的CBN多晶体的晶粒已不是原来的CBN单晶体颗粒。这种PCBN刀具耐磨性好,寿命长,但较脆且温度条件苛刻,难以制成高韧性及大尺寸的刀片。 故本次试验中采用焊接式结构,将刀齿做成三部分结构。
本次工艺试验采用AC16被动锥齿轮进行,使用12英寸铣刀盘,其刀齿参数主要借鉴目前所使用的热前精切刀齿参数。刀齿由三部分组成:高速钢刀具基体、硬质合金基体、PCBN切削刃。各部分间焊接成型。
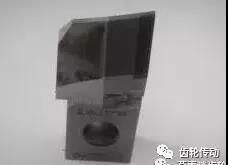
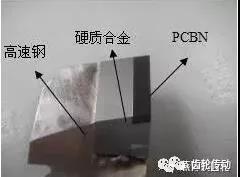
图1 复合式焊接刀具
2.热后硬切削切削参数的确定
根据相关资料介绍,PCBN刀具适合的切削速度为80-120m/min,结合刀具直径,算出的刀具转速应为:
n=1000*V/(3.14*d)=104r/min-125r/min
本次试验在格里森NO.26机床上进行,所选取的速度挂轮为:20/70*28/62,刀具主轴转速为114r/min。
PCBN刀具的吃刀量范围为0.15-0.25mm,本次切削试验中所采用的切削余量为0.2mm左右。进给量选择在0.03r/min。
3.热后硬切削工装设计
由于热处理前后的重复装夹,不可避免会在热后加工时出现乱齿现象,为此,对切齿工装更改了设计,增加一套对齿机构。此外,将定位碟簧尺寸进行了更改,使用了热后研配用碟簧,提高了工装整体的刚性。
4.热后硬切削加工情况
在本次工艺试验中,采用大轮双精刀盘进行加工,通过对齿机构的调整,实现了凹面与凸面的单独切削。切削过程中,机床无明显震动,刀具无损坏,加工中出现明显火花。由于切削热大部分被切屑带走,切屑颜色为微蓝色,因此,切削后工件仅有微热感。
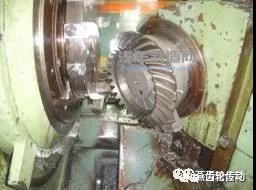
图2 切削情况
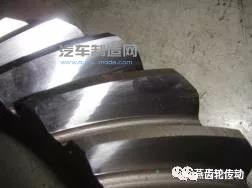
图3 切削后齿轮齿面
切削后工件表面发亮,粗糙度达到Ra0.5左右,高于外圆磨粗糙度。
5.热后硬加工质量情况
经过热后硬加工的零部件进行检测,齿圈跳动可达0.05,远低于产品图纸成品要求。与小轮研配后的齿面接触区如下:

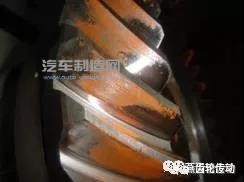
图4 成品接触区图片
距离啮合点0.5米时,检测噪音结果如下:
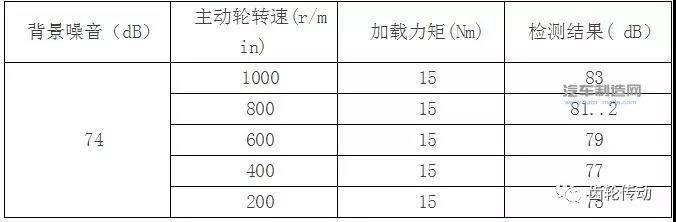
按常规工艺加工的齿轮副检测结果为:
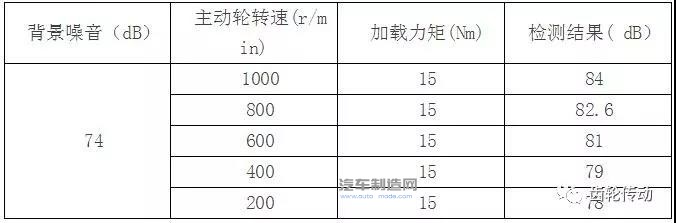
由此可以看出,热后切削加工的齿轮副其质量水平较正常加工零件质量要高。
6.结论
1.目前在国内,对于硬度超过HRC50的锥齿轮产品,大部分采取的为热后磨削工艺或者研齿工艺,热后硬切削加工方法和装备在中国重卡制造领域属于空白。对于我公司,此次为首次引进热后硬切削技术,属于公司内首创,且在国内重卡行业处于领先地位。
2.通过进行工艺试验,验证了热后弧齿锥齿轮硬齿面刮削工艺的可行性,为以后生产高精度齿轮副奠定了基础,加工后的齿轮副质量状况完全满足要求,从根本上消除了热处理变形对接触区的影响。
编辑推荐
最新资讯
-
全球产业链聚沪 共探双碳新路径 SNEC
2025-04-18 18:05
-
柯马签订具有约束力的协议收购 Autom
2025-04-17 13:01
-
高效协同新范式:比亚迪叉车领创智能
2025-04-17 10:04
-
埃马克德国总部迎来中国社科院工业经
2025-04-15 09:40
-
埃马克这项全新应用即将在CIMT惊艳首
2025-04-15 09:37