直齿锥齿轮的Hypoflex制造技术
2018-04-19 18:43:46· 来源:齿轮传动
在机械传动系统中,直齿锥齿轮的应用十分广泛。它们除了在汽车差速器上的用途外,其他应用的例子还在电动工具和各种各样的农业机械和设备中有广泛应用。
在机械传动系统中,直齿锥齿轮的应用十分广泛。它们除了在汽车差速器上的用途外,其他应用的例子还在电动工具和各种各样的农业机械和设备中有广泛应用。
与弧齿锥齿轮相比,直齿锥齿轮承载能力较低,运行平稳。他们之所以应用广泛,是因为与螺旋锥齿轮相比,具有较低的轴向力,且轴向力的方向和大小与旋转方向无关,减少了对于轴承的设计任务量。这个特点与变速箱中无限制轴向安装的附加优势结合在一起,带来了较大的设计优势。
本文讨论了采用先进的设计和优化软件,以及与之相匹配的现代干式切削技术对直齿锥齿轮加工的制造工艺。
研究现状
直齿锥齿轮是通过预成形、成形或切削加工制造的。预成形的实例包括铸造和烧结。铸造被用来大规模生产直齿锥齿轮,当对齿轮要求精度和功率密度较高时,可以使用非金属材料或有色金属材料。烧结锥齿轮在手持电动工具中使用较多,例如,电动角磨机。与其它工艺方法比较,该工艺难以避免材料的不均匀性,由于不均匀的致密化。另外模具的制造和齿轮参数的修改会有较高的成本。
锻造和摆动挤压都被证明是批量生产差速器锥齿轮的有效方法。但是该工艺方法存在的缺点在于其齿轮的周节误差和齿的形貌误差精度水平较低,采用摆动挤压生产的齿轮精度等级一般大概为IT8。然而,切削加工工艺依然为认为是能够稳定获得大批量或者小批量高精度齿轮产品的重要加工工艺。
就软齿面加工而言,可以采用诸如刨削、滚削和拉削等切削加工手段。直齿锥齿轮的热后硬加工只能通过研齿或磨齿的方式在有限的范围内进行。磨削工艺也在航空工业齿轮制造中有一些应用。Heidenreich-Harbeck 制定的加工工艺依然应用在某些一次性和小批量的零部件制造中。
加工直伞齿轮的Revacycle的拉削工艺特别适用于差速器锥齿轮的生产。该工艺所利用的刀具是一种圆周拉刀,圆周上有大量不同齿廓的刀具。第一个圆周段由粗加工刀片组成,每个叶片之间有轻微的向外偏移,接着是带有精加工叶片的段,接着是留出工件在一个周节处转动的间隙,刀具的每一次旋转都产生一个齿隙,如图1所示。
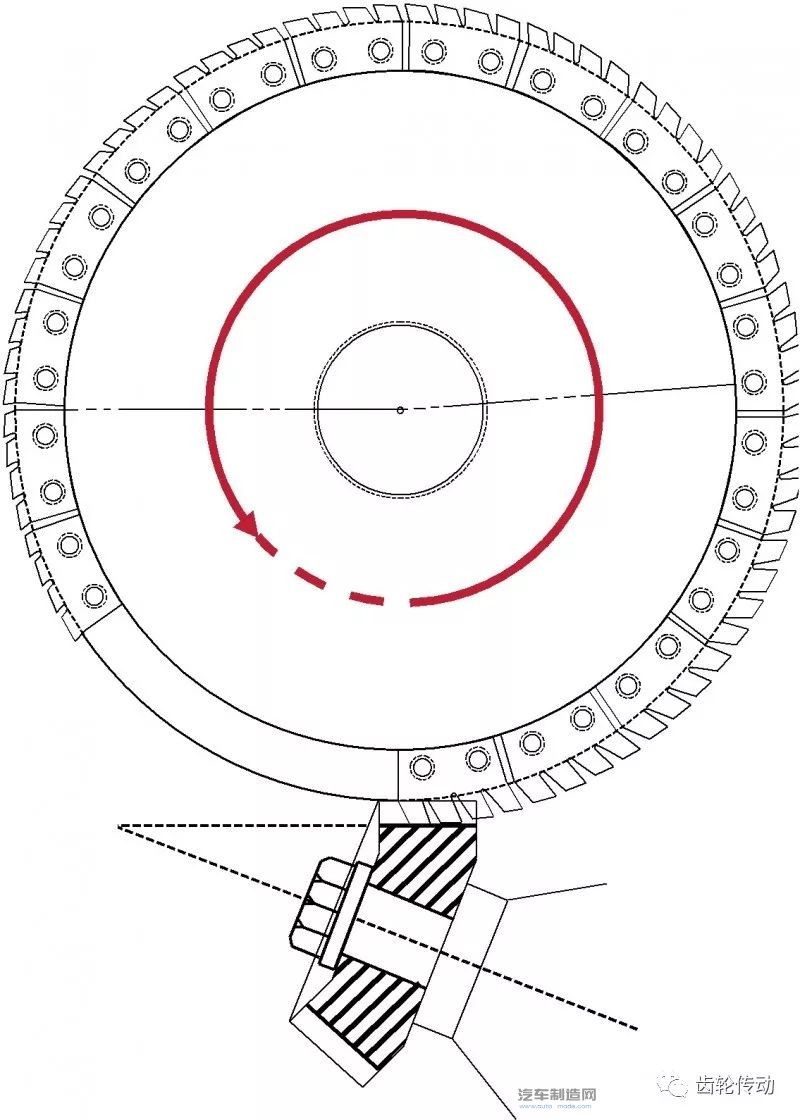
图1 Revacycle制造工艺
最后的叶片具有凹形,这个凹形将会被复制到工件,而刀具的中心点在一条直线上移动,就产生了直齿根。齿形沿端面宽度变化,纵向凸度是由单个切削刀片的形状和拉刀的切向运动产生的。Revacycle加工直伞齿轮的特征在于由其很高的生产效率,但仅仅可以用刀具来影响齿形。因此,这个工艺方法只适合大规模生产。
一种更为通用的切削方法是滚齿加工。在这里有三种不同的切削系统,其差别仅仅在于刀具的轻区别。最常用的是Coniflex®, Konvoid 和Sferoid Coniflex® 。
这组刀具包括两个圆周内啮合侧铣齿刀盘,它们代表了一个冠轮轮齿。这两个侧铣齿刀盘的轴线,一个在左侧,一个在右侧,被以一个相对确定的角度布置,因此这两个刀盘存在一定的相互内部啮合,这就引起它们产生一个梯形的轮廓。由于切削刃不在各自的旋转平面内,但位于一个轻微的内锥面内(如图2所示),齿廓就会存在一个固定的长度鼓形量,且齿根不是直线而是椭圆形,其最低点位于齿部中间。齿的长度鼓形变化量可以由刀具以及它的调整来决定。
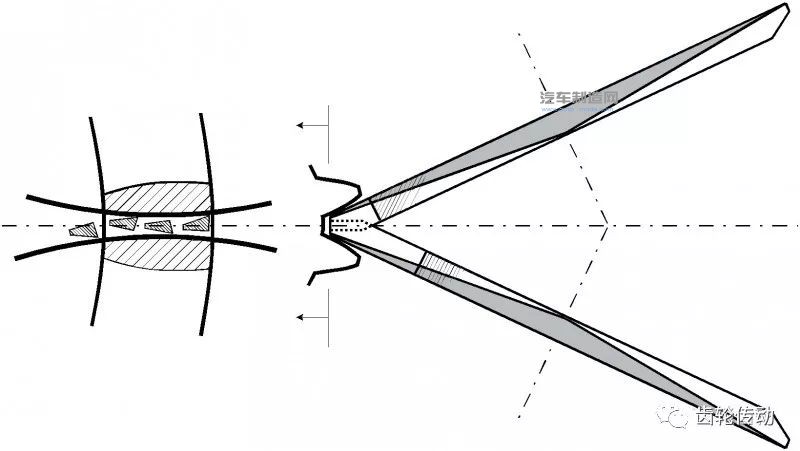
图2 内啮合侧铣齿刀盘
齿的长度鼓形量是由两个侧铣刀互相倾斜的角度和刀具直径决定的。这个角度的变化要求切削刃的侧面角发生变化,因为齿的压力角被改变了。
展成运动产生齿轮的齿高齿廓。这两个刀盘沿着它们的顶端摆动,而工件沿着自身的轴旋转。通过对机床的不同设定,可以利用相同刀具制造出不同的锥齿轮。
滚齿和拉齿工艺已经被创立好多年了,关于它们的历史可以追溯到19世纪60年代。这两种工艺均采用湿式切削,其工作效率和切削速度比较低。在生产率方面,它们已不能与现在所利用的干式切削方法相比较。
与螺旋锥齿轮相比,关于刀具的计算没有相应的软件。没有现代的尺寸计算和优化软件可以使用,同时也没有基于计算机的齿面形貌测量程序,同时缺乏3D名义数据。
理论基础
弧齿锥齿轮通常采用单齿分度和连续分度加工。单分度加工时,机床单独加工某一个齿面。刀具呈圆形排列,产生齿长方向鼓形。
当一个圆在另外一个圆上做滚动时,就产生了外摆线。滚动的圆通常称为滚圆,半径为EB,固定圆为基圆,半径为EY。如果外摆线的生成点位于内部,所得的曲线称为缩短外摆线;否则,它被称为一个延伸外摆线(图3)。
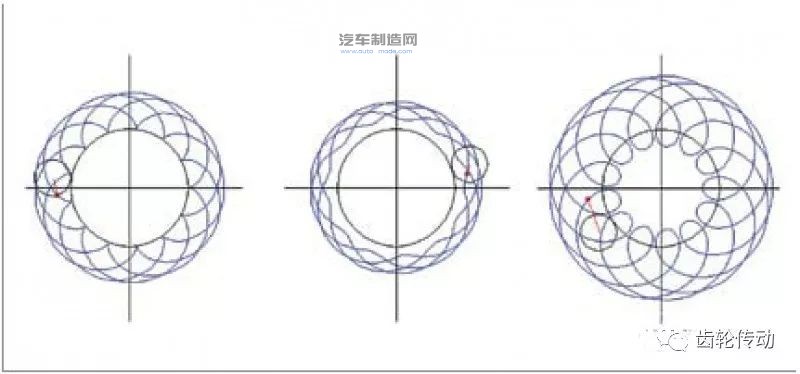
图3 摆线的形成方式
连续分度加工采用面铣刀刀头,其刀刃口由内、外刀片组成。每组刀头切削一个齿槽间隙。刀盘中刀齿的组数取决于刀盘的起始或者仅仅取决于其初始齿数Z0。在与工件相关时,一组刀齿沿着一个延伸外摆线运动。在连续切削的螺旋锥齿轮加工中,因此形成轮齿向的延伸外摆线部分。
当螺旋锥齿轮是在一个连续分度加工时,开始的数冠齿轮的齿数之比等于滚动圆半径与基圆半径的比值: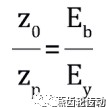
当滚动圆在基圆的做滚动时,所产生的即为内摆线(图4)。这与切削外摆线时的刀具运动轨迹相同,但旋转方向相反。
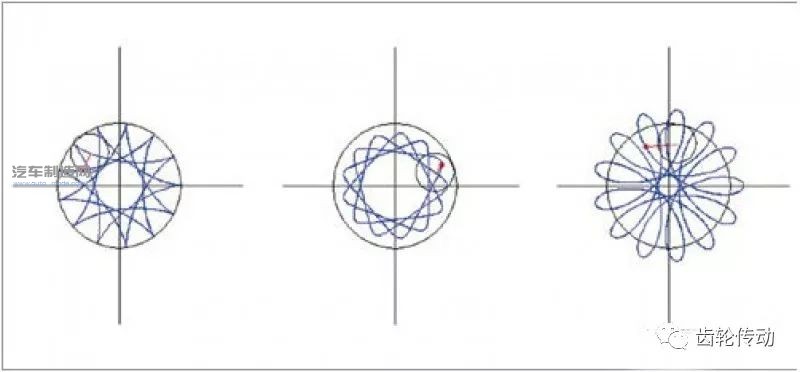
图4 内摆线以及缩短内摆线
在这个基础上,怎样才能产生直线,从而产生直齿呢?在滚圆半径等于基圆半径的一半的特殊情况下,滚动圆上某点产生的所有点都位于直线上。在这种情况下,缩短和延长的摆线就会变成椭圆。
Hypoflex制造工艺
Hypoflex制造工艺的动力学原理与上边所述的基本一致,即,在理论精确地基础上,开始的数与冠轮齿数的一半有关。
牙冠齿数通常不全是偶数,只有在极少数情况下才能完全满足要求。一般情况下,选择冠齿数的一半的整数作为起始数。齿长曲率(延长或缩短摆线)是由一个半径几米的曲率产生的在直线方向,存在2刀3μm的变化数值,这比在上面提到的滚削或滚削加工要小得多。
Hypoflex的连续分度加工工艺是一个精加工和半精加工的干式切削加工工艺。在精加工工艺过程中,一组刀具包括内刀和外刀,它们分别切削齿轮的左齿面和右齿面,它们是在同一台机床上设置的。在半精切加工工艺中,需要进行两台机床设置,其中分别加工齿轮的左齿面和右侧齿面,但是刀盘上只有一组刀齿,外刀或者内刀。后一种加工方式的特点是,它只用了一组刀齿。Klingelnberg发明了一种具有两个切削刃的刀具,称为TWIN刀具。当仅用一组刀齿加工时,半精切加工的特点在于适合大批量生产和较高的灵活性设计。
Hypoflex齿轮的齿全高时随着齿宽方向而变化的,其齿根和齿角可以在一个有意义的范围内选取,这使得在用不同工艺生产的直齿锥齿轮进行改进时保留相同类型的毛坯成为可能。
由于根锥角和节锥角的不同,在0°节锥平面上的螺旋角可以认为是由内刀刀齿和外刀刀齿的半径差异引起的。这个差异的大小有一半取决于压力角和齿根角。连续分度工艺中,同一类型的连续两刀之间的组角的大小是:
作为专家应当承认的是,当采用内刀齿和其它刀齿的排列角度与刀组数的一半相等时,就会发生齿槽的宽度与期望的数值相差太大的情况。因此有必要去调整刀齿序列角度。这意味着与采用连续分度法加工螺旋锥齿轮相比,刀齿之间距离会靠近。刀齿序列角度的数值取决于起始数量,齿根角、压力角以及滚动圆和基圆半径。一标准在设计齿轮和选择一个真正的刀盘时必须考虑到。
通常情况下,鼓形量是由各种修正方法来实现的。与切削其它锥齿轮工艺相,齿长鼓形是可以通过刀盘倾斜和特定的压力角来实现的。如果在长度鼓形方向采用空心锥的方法去实现,就会出现齿面接触区位于齿高方向的变化。另外一种生成齿廓鼓形的方法是采用修缘的刀具。更进一步的修正(接触区和失配)可以采用与螺旋锥齿轮的相同的方法来实现。
对于螺旋锥齿轮的接触应力和齿面承载能力计算的相应最新计算方法,同时能够适用于Hypoflex制造工艺。第一次,采用计算机和享用计算程序,可以测量齿面数据,建立3D齿面模型,在这基础上进行机床参数的修正。这使得使用者能够采用闭环制造系统,作为Hypoflex的制造工艺,提高产品的质量水平。
采用这一个工艺过程,直齿锥齿轮副可以采用Oerlikon的锥齿轮切削机床进行加工,所需要做的仅仅是选取不同的计算软件。同样,刀具调整和磨削傻呗也可以通用,只需要在现有的ARCON刀具上匹配所需要的刀条以及起始数量即可。
Hypoflex制造工艺的优点
Hypoflex制造工艺是一种直齿锥齿轮的制造工艺方法,它采用的连续分度切削方法,采用带有条形刀条的铣齿刀盘。除了在直齿锥齿轮领域率先采用最新的干切削技术外,它还有更大的灵活性。采用硬质合金刀具,切削速度高,可获得较高的生产率。
Hypoflex制造工艺可以在现有的CNC螺旋锥齿轮制造机床上实现。,所需要做的唯一调整就是设计软件的升级。直齿锥齿轮的设计可以在现有的KIMOS软件上实现,KIMOS软件在螺旋锥齿轮制造领域已经成熟应用多年,它可以就按机床设置参数,刀具参数以及EASE OFF的优化,还可以做加载齿面分析和齿面轮廓数据设计。所有需要的数据均以名义数据的格式保存在KIMOS数据库中。
由于采用了较高的生产效率,Hypoflex制造工艺使得使用者能够利用现有的闭环制造系统来控制整个过程中的质量水平。这个闭环系统包括了制造过程中的检测以及与之相关的刀具和机床参数修正的KOMET和3D形貌轮廓扫描等,该系统已经在螺旋锥齿轮中得到了广泛应用。
应用实例
图5显示的是如表1所列的齿轮参数的齿轮实例,该齿轮为Hypoflex工艺制造而成。
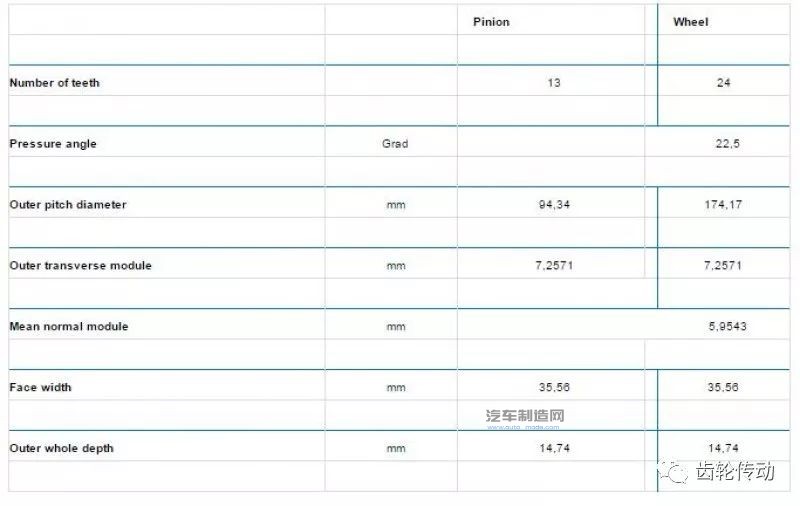
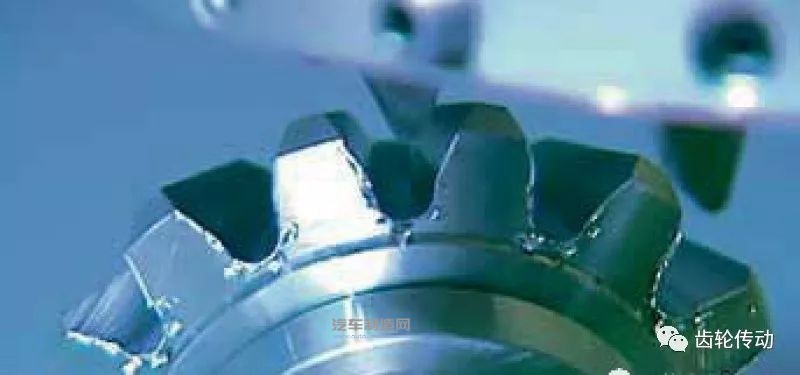
图5 采用Hypoflex工艺制造的锥齿轮
相关的齿面接触区分析结果如图6所示。齿面接触区位置和加载分析结果符合客户要求。
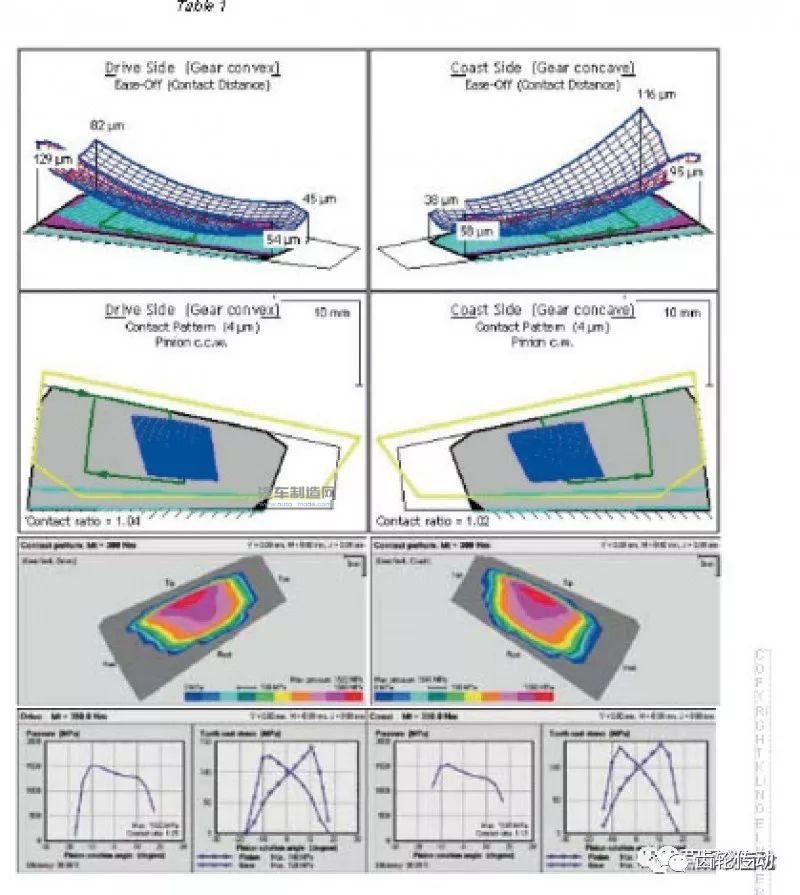
图7 KIMOS对hypoflex的计算
该齿轮是在C29铣齿机上采用半精切工艺所加工的,所用的是代用条形刀具的ARCON刀盘,14组刀条,且代用刀具涂层。主动轮加工时间为4.25分钟,被动轮加工时间为4.5分钟。齿轮副测量结果显示,主动轮周节误差精度达到DIN3965标准的3级,被动轮周节误差精度达到标准的2级。齿面形貌测量结果以及齿面粗糙度等级均满足生产质量要求。这意味着与以前的传统制造工艺相比,有了一个巨大的质量和效率的提升。
与弧齿锥齿轮相比,直齿锥齿轮承载能力较低,运行平稳。他们之所以应用广泛,是因为与螺旋锥齿轮相比,具有较低的轴向力,且轴向力的方向和大小与旋转方向无关,减少了对于轴承的设计任务量。这个特点与变速箱中无限制轴向安装的附加优势结合在一起,带来了较大的设计优势。
本文讨论了采用先进的设计和优化软件,以及与之相匹配的现代干式切削技术对直齿锥齿轮加工的制造工艺。
研究现状
直齿锥齿轮是通过预成形、成形或切削加工制造的。预成形的实例包括铸造和烧结。铸造被用来大规模生产直齿锥齿轮,当对齿轮要求精度和功率密度较高时,可以使用非金属材料或有色金属材料。烧结锥齿轮在手持电动工具中使用较多,例如,电动角磨机。与其它工艺方法比较,该工艺难以避免材料的不均匀性,由于不均匀的致密化。另外模具的制造和齿轮参数的修改会有较高的成本。
锻造和摆动挤压都被证明是批量生产差速器锥齿轮的有效方法。但是该工艺方法存在的缺点在于其齿轮的周节误差和齿的形貌误差精度水平较低,采用摆动挤压生产的齿轮精度等级一般大概为IT8。然而,切削加工工艺依然为认为是能够稳定获得大批量或者小批量高精度齿轮产品的重要加工工艺。
就软齿面加工而言,可以采用诸如刨削、滚削和拉削等切削加工手段。直齿锥齿轮的热后硬加工只能通过研齿或磨齿的方式在有限的范围内进行。磨削工艺也在航空工业齿轮制造中有一些应用。Heidenreich-Harbeck 制定的加工工艺依然应用在某些一次性和小批量的零部件制造中。
加工直伞齿轮的Revacycle的拉削工艺特别适用于差速器锥齿轮的生产。该工艺所利用的刀具是一种圆周拉刀,圆周上有大量不同齿廓的刀具。第一个圆周段由粗加工刀片组成,每个叶片之间有轻微的向外偏移,接着是带有精加工叶片的段,接着是留出工件在一个周节处转动的间隙,刀具的每一次旋转都产生一个齿隙,如图1所示。
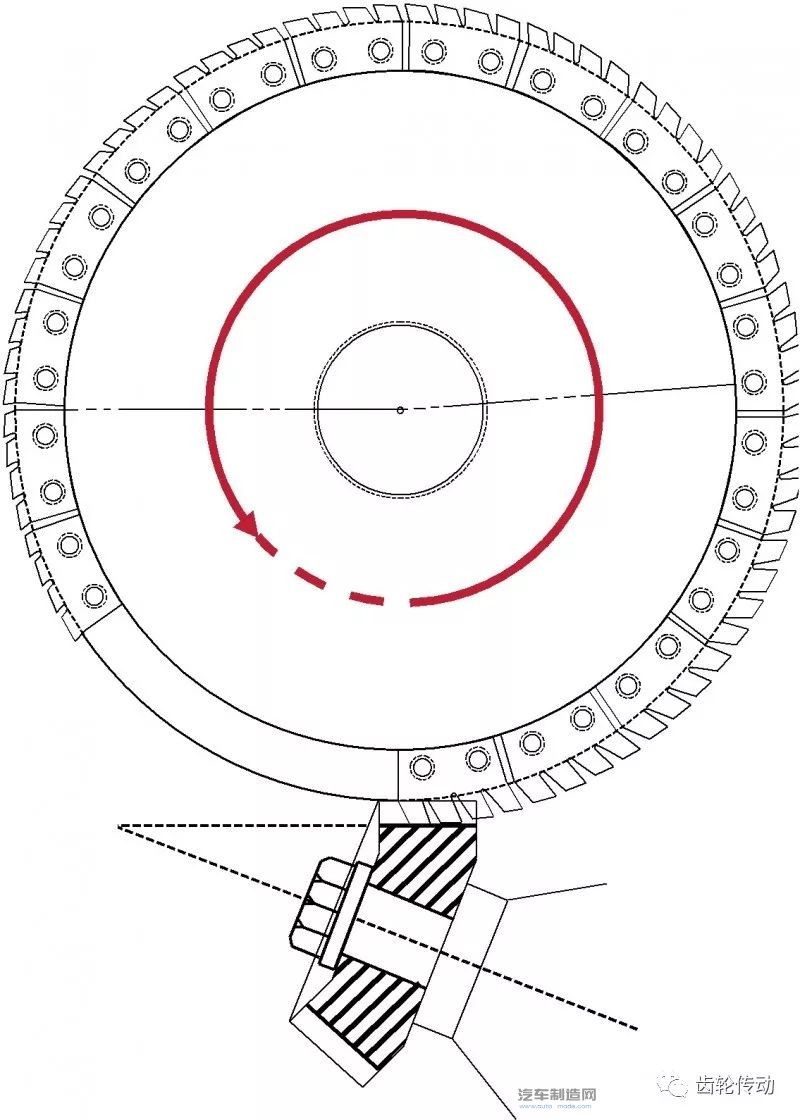
图1 Revacycle制造工艺
最后的叶片具有凹形,这个凹形将会被复制到工件,而刀具的中心点在一条直线上移动,就产生了直齿根。齿形沿端面宽度变化,纵向凸度是由单个切削刀片的形状和拉刀的切向运动产生的。Revacycle加工直伞齿轮的特征在于由其很高的生产效率,但仅仅可以用刀具来影响齿形。因此,这个工艺方法只适合大规模生产。
一种更为通用的切削方法是滚齿加工。在这里有三种不同的切削系统,其差别仅仅在于刀具的轻区别。最常用的是Coniflex®, Konvoid 和Sferoid Coniflex® 。
这组刀具包括两个圆周内啮合侧铣齿刀盘,它们代表了一个冠轮轮齿。这两个侧铣齿刀盘的轴线,一个在左侧,一个在右侧,被以一个相对确定的角度布置,因此这两个刀盘存在一定的相互内部啮合,这就引起它们产生一个梯形的轮廓。由于切削刃不在各自的旋转平面内,但位于一个轻微的内锥面内(如图2所示),齿廓就会存在一个固定的长度鼓形量,且齿根不是直线而是椭圆形,其最低点位于齿部中间。齿的长度鼓形变化量可以由刀具以及它的调整来决定。
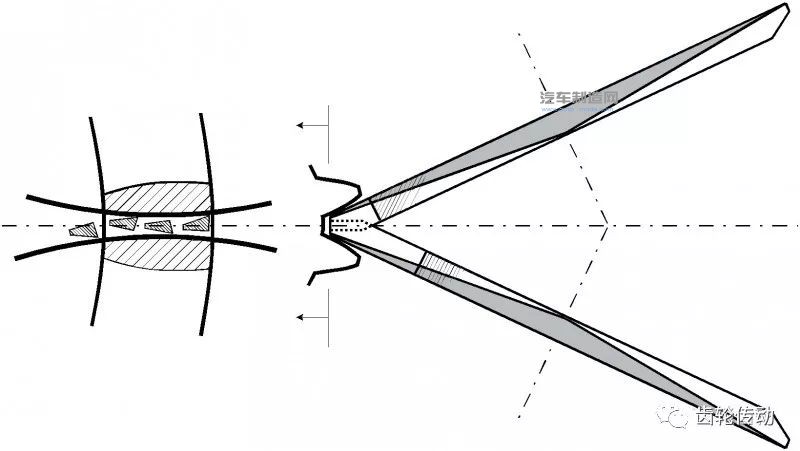
图2 内啮合侧铣齿刀盘
齿的长度鼓形量是由两个侧铣刀互相倾斜的角度和刀具直径决定的。这个角度的变化要求切削刃的侧面角发生变化,因为齿的压力角被改变了。
展成运动产生齿轮的齿高齿廓。这两个刀盘沿着它们的顶端摆动,而工件沿着自身的轴旋转。通过对机床的不同设定,可以利用相同刀具制造出不同的锥齿轮。
滚齿和拉齿工艺已经被创立好多年了,关于它们的历史可以追溯到19世纪60年代。这两种工艺均采用湿式切削,其工作效率和切削速度比较低。在生产率方面,它们已不能与现在所利用的干式切削方法相比较。
与螺旋锥齿轮相比,关于刀具的计算没有相应的软件。没有现代的尺寸计算和优化软件可以使用,同时也没有基于计算机的齿面形貌测量程序,同时缺乏3D名义数据。
理论基础
弧齿锥齿轮通常采用单齿分度和连续分度加工。单分度加工时,机床单独加工某一个齿面。刀具呈圆形排列,产生齿长方向鼓形。
当一个圆在另外一个圆上做滚动时,就产生了外摆线。滚动的圆通常称为滚圆,半径为EB,固定圆为基圆,半径为EY。如果外摆线的生成点位于内部,所得的曲线称为缩短外摆线;否则,它被称为一个延伸外摆线(图3)。
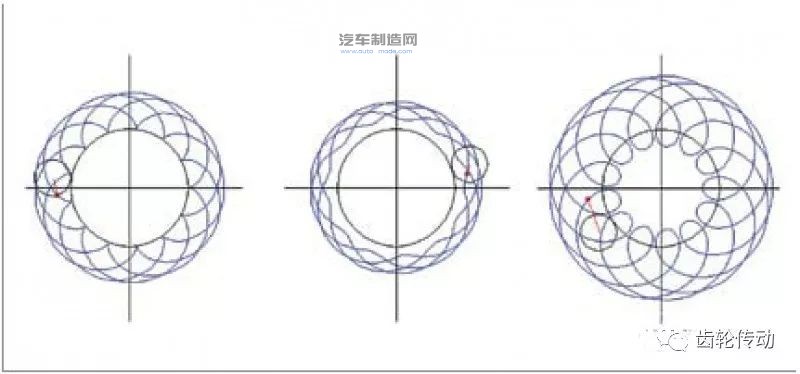
图3 摆线的形成方式
连续分度加工采用面铣刀刀头,其刀刃口由内、外刀片组成。每组刀头切削一个齿槽间隙。刀盘中刀齿的组数取决于刀盘的起始或者仅仅取决于其初始齿数Z0。在与工件相关时,一组刀齿沿着一个延伸外摆线运动。在连续切削的螺旋锥齿轮加工中,因此形成轮齿向的延伸外摆线部分。
当螺旋锥齿轮是在一个连续分度加工时,开始的数冠齿轮的齿数之比等于滚动圆半径与基圆半径的比值:
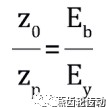
当滚动圆在基圆的做滚动时,所产生的即为内摆线(图4)。这与切削外摆线时的刀具运动轨迹相同,但旋转方向相反。
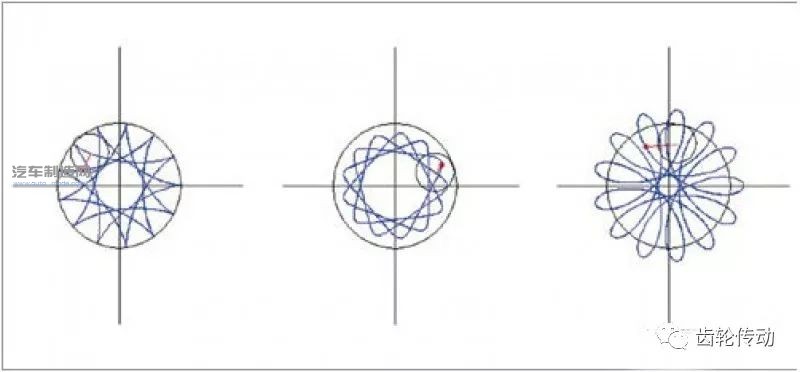
图4 内摆线以及缩短内摆线
在这个基础上,怎样才能产生直线,从而产生直齿呢?在滚圆半径等于基圆半径的一半的特殊情况下,滚动圆上某点产生的所有点都位于直线上。在这种情况下,缩短和延长的摆线就会变成椭圆。
Hypoflex制造工艺
Hypoflex制造工艺的动力学原理与上边所述的基本一致,即,在理论精确地基础上,开始的数与冠轮齿数的一半有关。
牙冠齿数通常不全是偶数,只有在极少数情况下才能完全满足要求。一般情况下,选择冠齿数的一半的整数作为起始数。齿长曲率(延长或缩短摆线)是由一个半径几米的曲率产生的在直线方向,存在2刀3μm的变化数值,这比在上面提到的滚削或滚削加工要小得多。
Hypoflex的连续分度加工工艺是一个精加工和半精加工的干式切削加工工艺。在精加工工艺过程中,一组刀具包括内刀和外刀,它们分别切削齿轮的左齿面和右齿面,它们是在同一台机床上设置的。在半精切加工工艺中,需要进行两台机床设置,其中分别加工齿轮的左齿面和右侧齿面,但是刀盘上只有一组刀齿,外刀或者内刀。后一种加工方式的特点是,它只用了一组刀齿。Klingelnberg发明了一种具有两个切削刃的刀具,称为TWIN刀具。当仅用一组刀齿加工时,半精切加工的特点在于适合大批量生产和较高的灵活性设计。
Hypoflex齿轮的齿全高时随着齿宽方向而变化的,其齿根和齿角可以在一个有意义的范围内选取,这使得在用不同工艺生产的直齿锥齿轮进行改进时保留相同类型的毛坯成为可能。
由于根锥角和节锥角的不同,在0°节锥平面上的螺旋角可以认为是由内刀刀齿和外刀刀齿的半径差异引起的。这个差异的大小有一半取决于压力角和齿根角。连续分度工艺中,同一类型的连续两刀之间的组角的大小是:
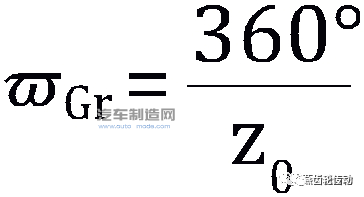
通常情况下,鼓形量是由各种修正方法来实现的。与切削其它锥齿轮工艺相,齿长鼓形是可以通过刀盘倾斜和特定的压力角来实现的。如果在长度鼓形方向采用空心锥的方法去实现,就会出现齿面接触区位于齿高方向的变化。另外一种生成齿廓鼓形的方法是采用修缘的刀具。更进一步的修正(接触区和失配)可以采用与螺旋锥齿轮的相同的方法来实现。
对于螺旋锥齿轮的接触应力和齿面承载能力计算的相应最新计算方法,同时能够适用于Hypoflex制造工艺。第一次,采用计算机和享用计算程序,可以测量齿面数据,建立3D齿面模型,在这基础上进行机床参数的修正。这使得使用者能够采用闭环制造系统,作为Hypoflex的制造工艺,提高产品的质量水平。
采用这一个工艺过程,直齿锥齿轮副可以采用Oerlikon的锥齿轮切削机床进行加工,所需要做的仅仅是选取不同的计算软件。同样,刀具调整和磨削傻呗也可以通用,只需要在现有的ARCON刀具上匹配所需要的刀条以及起始数量即可。
Hypoflex制造工艺的优点
Hypoflex制造工艺是一种直齿锥齿轮的制造工艺方法,它采用的连续分度切削方法,采用带有条形刀条的铣齿刀盘。除了在直齿锥齿轮领域率先采用最新的干切削技术外,它还有更大的灵活性。采用硬质合金刀具,切削速度高,可获得较高的生产率。
Hypoflex制造工艺可以在现有的CNC螺旋锥齿轮制造机床上实现。,所需要做的唯一调整就是设计软件的升级。直齿锥齿轮的设计可以在现有的KIMOS软件上实现,KIMOS软件在螺旋锥齿轮制造领域已经成熟应用多年,它可以就按机床设置参数,刀具参数以及EASE OFF的优化,还可以做加载齿面分析和齿面轮廓数据设计。所有需要的数据均以名义数据的格式保存在KIMOS数据库中。
由于采用了较高的生产效率,Hypoflex制造工艺使得使用者能够利用现有的闭环制造系统来控制整个过程中的质量水平。这个闭环系统包括了制造过程中的检测以及与之相关的刀具和机床参数修正的KOMET和3D形貌轮廓扫描等,该系统已经在螺旋锥齿轮中得到了广泛应用。
应用实例
图5显示的是如表1所列的齿轮参数的齿轮实例,该齿轮为Hypoflex工艺制造而成。
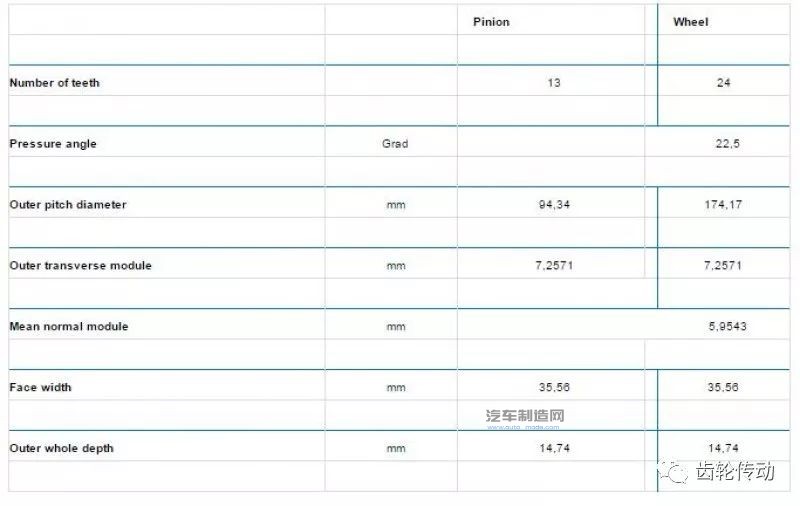
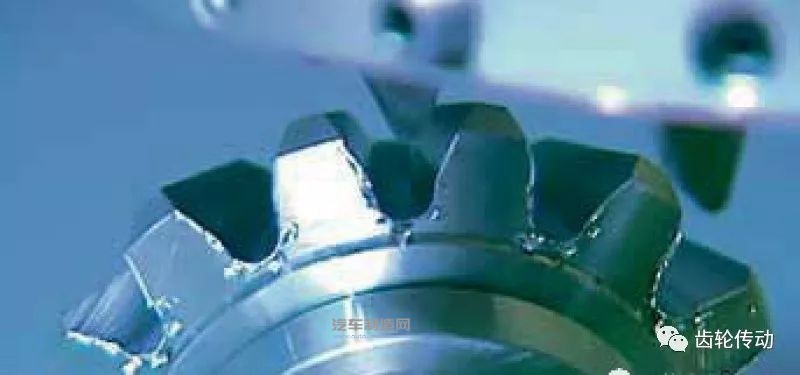
图5 采用Hypoflex工艺制造的锥齿轮
相关的齿面接触区分析结果如图6所示。齿面接触区位置和加载分析结果符合客户要求。
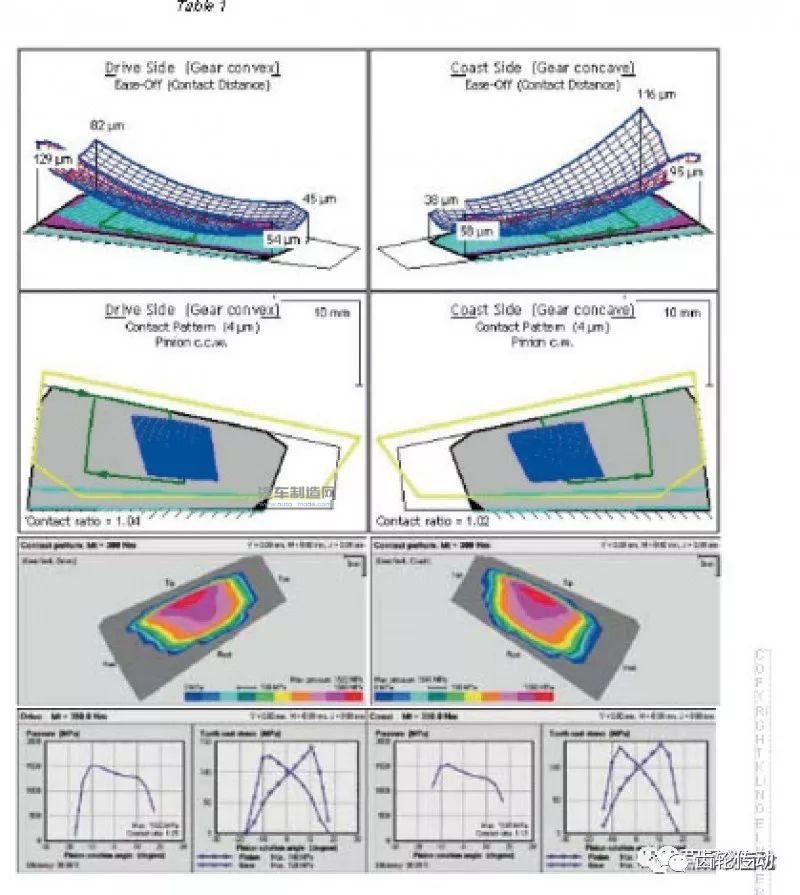
图7 KIMOS对hypoflex的计算
该齿轮是在C29铣齿机上采用半精切工艺所加工的,所用的是代用条形刀具的ARCON刀盘,14组刀条,且代用刀具涂层。主动轮加工时间为4.25分钟,被动轮加工时间为4.5分钟。齿轮副测量结果显示,主动轮周节误差精度达到DIN3965标准的3级,被动轮周节误差精度达到标准的2级。齿面形貌测量结果以及齿面粗糙度等级均满足生产质量要求。这意味着与以前的传统制造工艺相比,有了一个巨大的质量和效率的提升。
编辑推荐
最新资讯
-
全球产业链聚沪 共探双碳新路径 SNEC
2025-04-18 18:05
-
柯马签订具有约束力的协议收购 Autom
2025-04-17 13:01
-
高效协同新范式:比亚迪叉车领创智能
2025-04-17 10:04
-
埃马克德国总部迎来中国社科院工业经
2025-04-15 09:40
-
埃马克这项全新应用即将在CIMT惊艳首
2025-04-15 09:37