结构优化在汽车天窗设计中的应用
2018-04-24 11:55:10· 来源:CAE技术资讯 作者:蒋振宇
目前汽车行业竞争非常激烈,国内外各大汽车和零部件厂商都在使用或关注结构优化技术,期望通过它能够帮助企业提高产品的质量、降低开发成本和缩短设计周期,从而提高产品的竞争力。结构优化通常分为拓扑优化、形貌优化、形状优化和尺寸优化,且所有优化类型都可以进行自由组合。
1概述
目前汽车行业竞争非常激烈,国内外各大汽车和零部件厂商都在使用或关注结构优化技术,期望通过它能够帮助企业提高产品的质量、降低开发成本和缩短设计周期,从而提高产品的竞争力。结构优化通常分为拓扑优化、形貌优化、形状优化和尺寸优化,且所有优化类型都可以进行自由组合。
现在世界上已有多个商用结构优化求解器,其中OptiStruct结构优化求解器以其成熟、全面的技术得到大家的认可,已被广泛应用于许多行业的产品设计实践中。下面将详细介绍伟巴斯特(Webasto)中国在去年(2016年)运用OptiStruct进行优化设计的两个案例。
2遮阳帘托盘形貌优化设计
汽车顶棚有些安装点需要固定在天窗遮阳帘托盘上,因此整车厂规定每个天窗遮阳帘安装点的最大安装变形应小于1.0mm。下面将以伟巴斯特(Webasto)某款天窗遮阳帘为研究对象,介绍利用形貌优化技术提高其刚度的案例。
2.1 遮阳帘托盘原始结构刚度分析
遮阳帘托盘是由板金冲压而成,因此可以采用壳单元对结构进行描述,托盘的材料为DC01,弹性模量:210Gpa,泊松比:0.33,密度为7800.0Kg/M3。约束托盘与天窗连接点的所有自由度如图1所示,把完成的有限元模型提交给OptiStruct进行静态求解,查看有限元结果,安装点的最大变形量为1.82mm如图2所示,原始结构不能满足整车厂的要求(<1.0mm),因此可以利用形貌优化技术对其加强筋重新布局设计,提高其刚度。
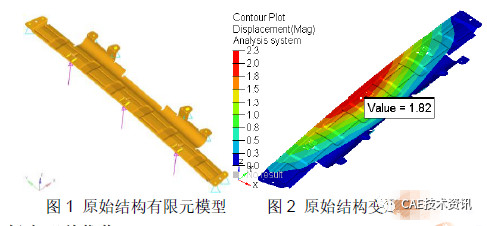
2.2 遮阳帘托盘形貌优化
形貌优化主要用于在薄壁结构中寻找最优的加强筋分布,在减轻结构重量的同时能够满足强度、频率等要求。形貌优化不删除材料,而是在可设计区域中根据节点扰动生成加强筋。将原有遮阳帘托盘模型中的起筋区域抹平并将它作为设计变量如图3中红色区域所示,考虑到设计空间的限制,加强筋参数与原有设计保持一致,把加载点位移最小作为优化目标,在完成其它设置后,提交给OptiStruct,经过30步迭代计算,最终得到新的加强筋分布如图 4所示,加强筋分布与原有设计明显不同。
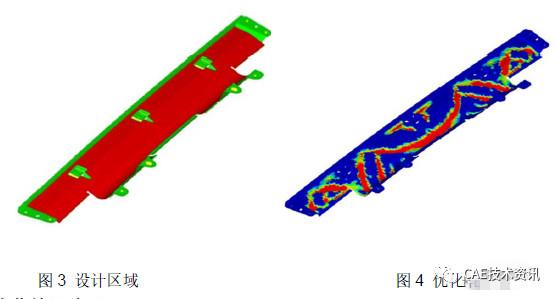
2.3 优化结果验证
完成形貌优化后,利用OSSmotth工具输出优化后的几何模型,这个不可以直接用于生产,需要再次导入专业的CAD软件,作为参照对初始设计进行修改得到适应生产和成本要求的设计方案如图5所示。
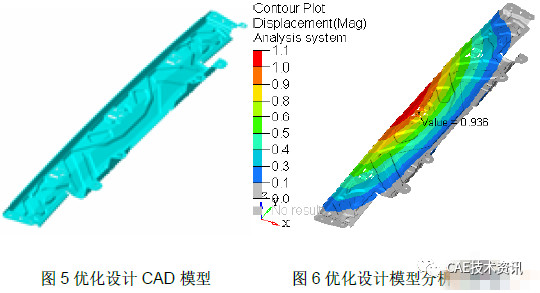
在完成对遮阳帘托盘加强筋修改设计后,需要再次进行结构分析,结果如图6所示,对比优化前后的变形结果可以发现优化后的结构变形明显减小到0.94mm,满足设计要求,优化效果显著。
3玻璃框架的支架自由形状优化设计
汽车天窗和整车一样需要经过道路试验,满足疲劳要求。为了减少试制和试验的次数,伟巴斯特(Webasto)根据以往道路试验数据定义了天窗在Z和Y方向CAE简化振动工况。下面将以伟巴斯特(Webasto)某款天窗为研究对象,介绍利用形状优化技术降低天窗玻璃框架局部应力的案例。
3.1 天窗总成疲劳分析
某天窗具体结构如下图7所示,经过简化振动CAE分析,发现天窗玻璃框架支架根部存在应力集中见图8和9。
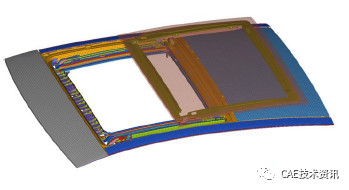
图7天窗结构
.jpg)
疲劳极限与结构形式,载荷类型,表面处理和机械加工粗糙度等等因素相关。对于钢材的疲劳问题,在缺乏实验数据的情况下,我们可以用下面的经验公式来初略的评估钢材疲劳极限:

据上面原始结构的强度分析结果,天窗玻璃框架的支架根部存在应力集中并远远大于疲劳极限,必须对其应力集中区域进行自由形状优化,降低其局部应力。
此天窗在实际台架疲劳测试过程中,也发生了疲劳断裂破坏,破坏形式与CAE结果一致。
3.2 自由形状优化
形状优化是一种用于详细设计阶段的技术,是将有限元模型网格节点移动到某个新的位置,相当于改变零件的CAD设计,从而提高零件的性能,如提高刚度、模态,降低集中力等。
根据形状优化的需要,必须在Hypermesh中对应力集中区域进行网格细化,并把应力集中的节点定义为可自由移动节点,并将其作为形状优化变量,如图10所示:
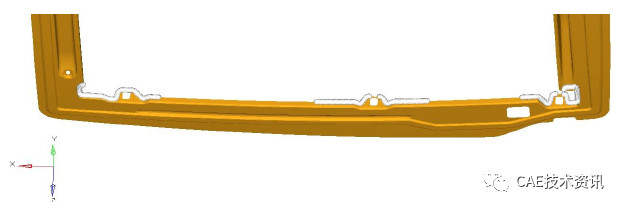
图10 形状优化变量
3.3 形状优化的结果
OptiStruct能够同时根据两个工况(Z和Y方向的简化振动)找到最佳形状,经过3轮形状优化分析,每个支架根部应力都有大幅度的降低,且结构应力分布更加趋于平缓见图11和12,比较优化前后各个支架的应力结果(见表1和2),发现其最大应力下降超过50%,优化效果非常明显,都满足了材料强度要求。
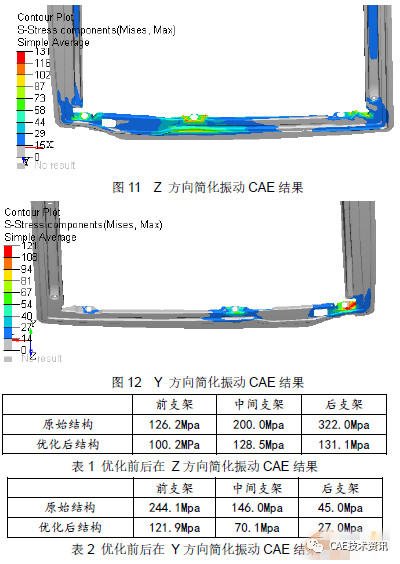
4结构优化在天窗设计中的其它研究
1:前框和后框优化设计(拓扑和尺寸优化)
2:挡风条加强筋优化(拓扑优化)
3:玻璃顶出力DOE研究(形状和尺寸优化)
4:天窗总成零件厚度优化(尺寸优化)
5:密封条截面形状优化(拓扑和形状优化)
5结论
1:本文成功的利用OptiStruct形貌优化功能实现了对遮阳帘托盘加强筋的重新布局,使遮阳帘托盘刚度提高了44.0%,分析结果表明形貌优化技术是提高薄壁件刚度最有效的方法,为以后汽车天窗上的薄壁件结构优化设计提供了借鉴思路。
2:另一个案例是利用OptiStruct自由形状优化功能快速的找到了降低零件局部应力的方法,使框架的结构应力大幅度降低且幅度超过50%,而且分布变化趋于平缓,为以后解决天窗零件局部应力集中的问题提供了解决方法。本轮优化使用一天时间,现有的经验已经证明,如果不采用形状优化技术,几个月的持续工作也没能找到大幅度降低局部应力的方案,由此可知,OptiStruct能够快速的解决问题和大幅度提高工作效率。
3:上面两个优化案例表明,在设计过程中采用结构优化的方法,能够帮助工程师快速的找到最佳设计方案,避免了反复CAE分析,设计修改及试验工作,减少研发的投入,节约了产品的开发时间。
目前汽车行业竞争非常激烈,国内外各大汽车和零部件厂商都在使用或关注结构优化技术,期望通过它能够帮助企业提高产品的质量、降低开发成本和缩短设计周期,从而提高产品的竞争力。结构优化通常分为拓扑优化、形貌优化、形状优化和尺寸优化,且所有优化类型都可以进行自由组合。
现在世界上已有多个商用结构优化求解器,其中OptiStruct结构优化求解器以其成熟、全面的技术得到大家的认可,已被广泛应用于许多行业的产品设计实践中。下面将详细介绍伟巴斯特(Webasto)中国在去年(2016年)运用OptiStruct进行优化设计的两个案例。
2遮阳帘托盘形貌优化设计
汽车顶棚有些安装点需要固定在天窗遮阳帘托盘上,因此整车厂规定每个天窗遮阳帘安装点的最大安装变形应小于1.0mm。下面将以伟巴斯特(Webasto)某款天窗遮阳帘为研究对象,介绍利用形貌优化技术提高其刚度的案例。
2.1 遮阳帘托盘原始结构刚度分析
遮阳帘托盘是由板金冲压而成,因此可以采用壳单元对结构进行描述,托盘的材料为DC01,弹性模量:210Gpa,泊松比:0.33,密度为7800.0Kg/M3。约束托盘与天窗连接点的所有自由度如图1所示,把完成的有限元模型提交给OptiStruct进行静态求解,查看有限元结果,安装点的最大变形量为1.82mm如图2所示,原始结构不能满足整车厂的要求(<1.0mm),因此可以利用形貌优化技术对其加强筋重新布局设计,提高其刚度。
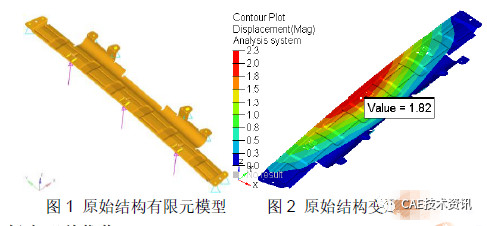
2.2 遮阳帘托盘形貌优化
形貌优化主要用于在薄壁结构中寻找最优的加强筋分布,在减轻结构重量的同时能够满足强度、频率等要求。形貌优化不删除材料,而是在可设计区域中根据节点扰动生成加强筋。将原有遮阳帘托盘模型中的起筋区域抹平并将它作为设计变量如图3中红色区域所示,考虑到设计空间的限制,加强筋参数与原有设计保持一致,把加载点位移最小作为优化目标,在完成其它设置后,提交给OptiStruct,经过30步迭代计算,最终得到新的加强筋分布如图 4所示,加强筋分布与原有设计明显不同。
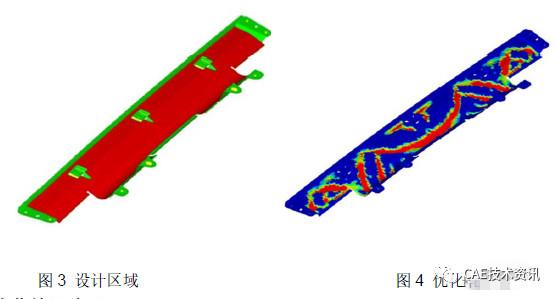
2.3 优化结果验证
完成形貌优化后,利用OSSmotth工具输出优化后的几何模型,这个不可以直接用于生产,需要再次导入专业的CAD软件,作为参照对初始设计进行修改得到适应生产和成本要求的设计方案如图5所示。
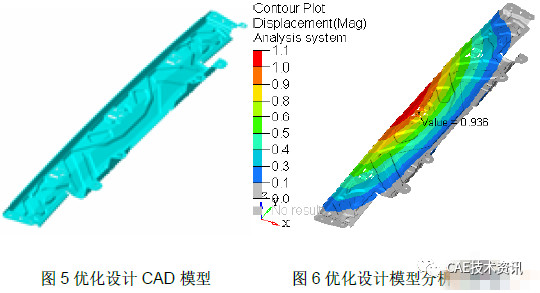
在完成对遮阳帘托盘加强筋修改设计后,需要再次进行结构分析,结果如图6所示,对比优化前后的变形结果可以发现优化后的结构变形明显减小到0.94mm,满足设计要求,优化效果显著。
3玻璃框架的支架自由形状优化设计
汽车天窗和整车一样需要经过道路试验,满足疲劳要求。为了减少试制和试验的次数,伟巴斯特(Webasto)根据以往道路试验数据定义了天窗在Z和Y方向CAE简化振动工况。下面将以伟巴斯特(Webasto)某款天窗为研究对象,介绍利用形状优化技术降低天窗玻璃框架局部应力的案例。
3.1 天窗总成疲劳分析
某天窗具体结构如下图7所示,经过简化振动CAE分析,发现天窗玻璃框架支架根部存在应力集中见图8和9。
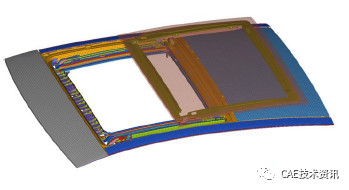
图7天窗结构
.jpg)
疲劳极限与结构形式,载荷类型,表面处理和机械加工粗糙度等等因素相关。对于钢材的疲劳问题,在缺乏实验数据的情况下,我们可以用下面的经验公式来初略的评估钢材疲劳极限:

据上面原始结构的强度分析结果,天窗玻璃框架的支架根部存在应力集中并远远大于疲劳极限,必须对其应力集中区域进行自由形状优化,降低其局部应力。
此天窗在实际台架疲劳测试过程中,也发生了疲劳断裂破坏,破坏形式与CAE结果一致。
3.2 自由形状优化
形状优化是一种用于详细设计阶段的技术,是将有限元模型网格节点移动到某个新的位置,相当于改变零件的CAD设计,从而提高零件的性能,如提高刚度、模态,降低集中力等。
根据形状优化的需要,必须在Hypermesh中对应力集中区域进行网格细化,并把应力集中的节点定义为可自由移动节点,并将其作为形状优化变量,如图10所示:
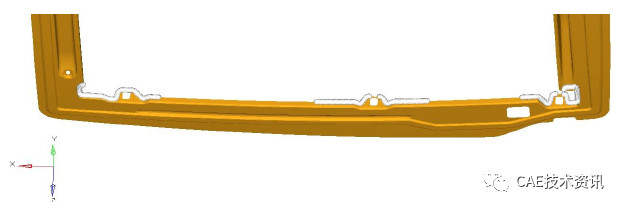
图10 形状优化变量
3.3 形状优化的结果
OptiStruct能够同时根据两个工况(Z和Y方向的简化振动)找到最佳形状,经过3轮形状优化分析,每个支架根部应力都有大幅度的降低,且结构应力分布更加趋于平缓见图11和12,比较优化前后各个支架的应力结果(见表1和2),发现其最大应力下降超过50%,优化效果非常明显,都满足了材料强度要求。
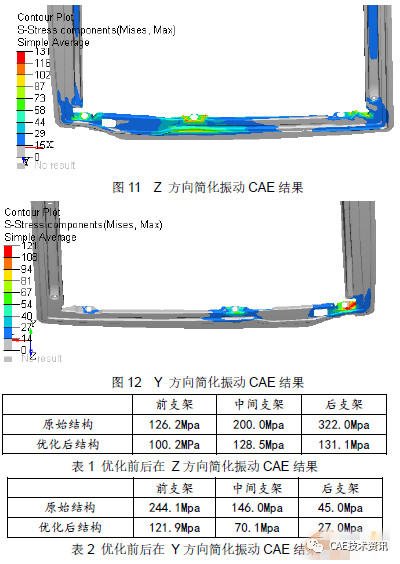
4结构优化在天窗设计中的其它研究
1:前框和后框优化设计(拓扑和尺寸优化)
2:挡风条加强筋优化(拓扑优化)
3:玻璃顶出力DOE研究(形状和尺寸优化)
4:天窗总成零件厚度优化(尺寸优化)
5:密封条截面形状优化(拓扑和形状优化)
5结论
1:本文成功的利用OptiStruct形貌优化功能实现了对遮阳帘托盘加强筋的重新布局,使遮阳帘托盘刚度提高了44.0%,分析结果表明形貌优化技术是提高薄壁件刚度最有效的方法,为以后汽车天窗上的薄壁件结构优化设计提供了借鉴思路。
2:另一个案例是利用OptiStruct自由形状优化功能快速的找到了降低零件局部应力的方法,使框架的结构应力大幅度降低且幅度超过50%,而且分布变化趋于平缓,为以后解决天窗零件局部应力集中的问题提供了解决方法。本轮优化使用一天时间,现有的经验已经证明,如果不采用形状优化技术,几个月的持续工作也没能找到大幅度降低局部应力的方案,由此可知,OptiStruct能够快速的解决问题和大幅度提高工作效率。
3:上面两个优化案例表明,在设计过程中采用结构优化的方法,能够帮助工程师快速的找到最佳设计方案,避免了反复CAE分析,设计修改及试验工作,减少研发的投入,节约了产品的开发时间。
编辑推荐
最新资讯
-
旭化成微电子开始批量生产用于环保发
2025-04-24 16:00
-
华为、地平线、大众、东风、起亚等引
2025-04-24 08:27
-
全球产业链聚沪 共探双碳新路径 SNEC
2025-04-18 18:05
-
柯马签订具有约束力的协议收购 Autom
2025-04-17 13:01
-
高效协同新范式:比亚迪叉车领创智能
2025-04-17 10:04