刚性专机变速箱壳体生产线柔性改造
2018-04-26 17:11:21· 来源:金属加工
单品种、大批量生产线无法满足多品种、小批量的市场需求,企业怎么对现有的生产线进行改造?如果采用推倒重来,企业的生产成本会非常高。本文重点阐述刚性生产线的柔性改造,将粗加工的经济和精加工的高品质有效地结合在一起。
摘要:单品种、大批量生产线无法满足多品种、小批量的市场需求,企业怎么对现有的生产线进行改造?如果采用推倒重来,企业的生产成本会非常高。本文重点阐述刚性生产线的柔性改造,将粗加工的经济和精加工的高品质有效地结合在一起。
1. 项目背景
目前商用车变速箱壳体采用的生产线为多机细分工序生产线,虽然节拍短,效率高,但无法适应多品种、小批量市场的要求,经常要调整,尺寸的稳定性差,质量波动大;加工中心的产品质量好,但节拍长。企业的发展,迫切要求对目前壳体生产线进行柔性化改造。
2. 原工艺流程
原工艺流程如图1所示。
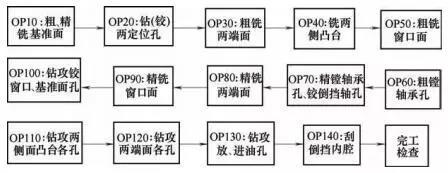
图 1
3. 原工艺存在的主要问题
(1)品种多。商用车变速器壳的品种多,生产线只能生产设定的产品,由于市场对各产品的需求不同,导致生产线的生产不均衡。
(2)开发周期长。每开发一个产品,小批量时都是在相近的生产线上更换工装,更换一个品种需要将近8h的时间,生产线品种的切换就必须增加各品种的库存。
(3)生产线的特点。由通用设备、专机组成的生产线能否达产,其关键点就在于专机的到位时间,专机的生产周期一般需要6个月;而专机线无法满足产品的改型,产品在各加工线之间也难于切换。
(4)生产线产能与配置(见表1)。
表1 生产线产能与配置
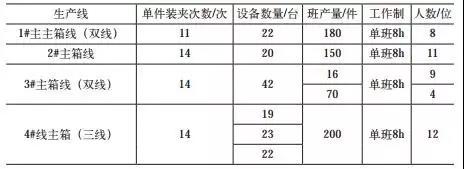
(5)专机线对产品的影响因素:①铸造应力和加工应力。②干切时铸件的热胀冷缩。③分序的定位精度。④转序引起的磕碰。
4. 改造方案的分析
(1)设计精度对加工工艺的要求,如图2所示,如果精铣两端面和精镗轴承孔(铰倒挡孔)在一次装夹下完成,就不存在分序加工的定位累计误差。
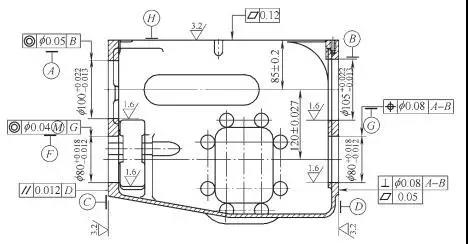
图 2
(2)我们选用了一款壳体加工的生产线,从使用设备、投资额、人员配置和工艺成本几个方面,对不同的方案进行分析(见表2)。
表2 方案对比
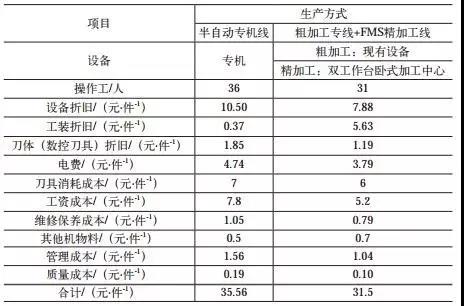
经过以上对比分析,采用粗加工专线+FMS精加工线方案的成本优于自动专机生产线。
5. 改进的措施
(1)要实现生产线对各产品加工的适应性,需要对现有的产品进行设计改进,在基准面的周边设置工艺凸台和工艺定位孔,如图3所示,将工艺定位孔的中心距离L和销孔的孔径设计成一致。
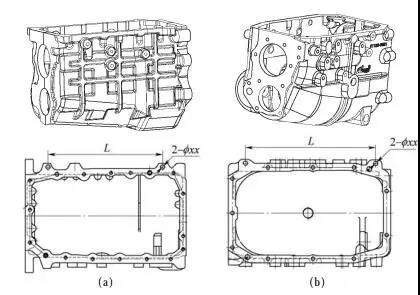
图 3
(2)为了消除铸造应力,加工应力及加工产生的热量对产品质量的影响,将壳体的粗精加工分开。
(3)粗加工工序利用现有的设备资源,组成粗加工单元,发挥专机生产线生产节拍短的优势。
(4)OP10粗铣基准面工序,圆台铣工装的柔性设计:采用三顶针顶入轴承预留孔中,通过伸缩上端两顶针来适应不同长度的箱体,通过弹簧顶针的偏心来适应不同中心距的壳体加工,如图4所示。
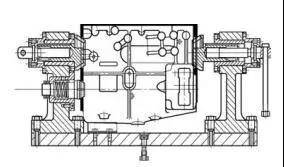
图 4
(5)OP20工序通过调整箱体长度的定位,对不同的箱体进行定位孔的加工,实现工艺定位的统一,这样就可以在OP30、OP40和OP50的铣削工序中实现工装底板的统一,只要调整铣削头的轴向距离就可以适应不同长度箱体铣面的要求;对于OP60粗镗工序,只要更换镗削头就可以适应不同中心距产品的切换。
(6)精加工采用交换工作台卧式加工中心组成的FMS柔性加工生产单元,确保关键尺寸的加工在一次装夹下完成。
6. 改后的工艺流程
改进后粗加工工艺流程如图5所示。
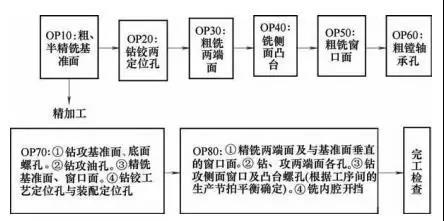
图 5
7. 设备布局
设备布局如图6所示。
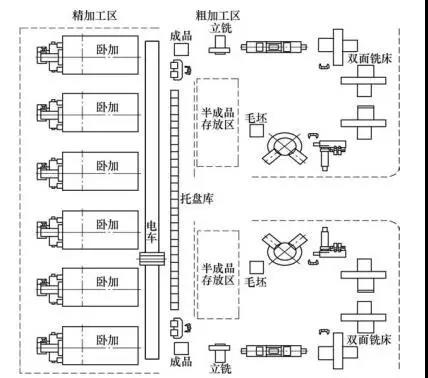
图 6
8. 精加工的夹具的设计
(1)精加工OP70夹具如图7所示,工件推入夹具体后,通过工装底部圆柱锥体导入一轴轴承孔和中间轴孔削边销的顶出,限制了箱体的两个自由度,通过顶部导向压板使得箱体在长度方向进行定位,再经过薄型缸压紧,这样,夹紧力就可以很小,防止箱体的夹持变形,如图7所示。
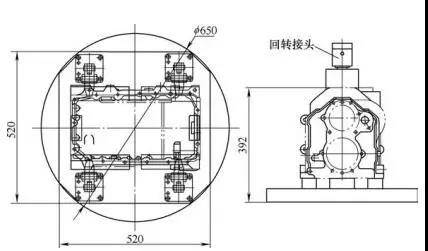
图 7
(2)在OP70工序中,对粗定位孔进行扩孔和铰孔加工,这样便于精加工OP80的夹具底板的统一,如图8所示。
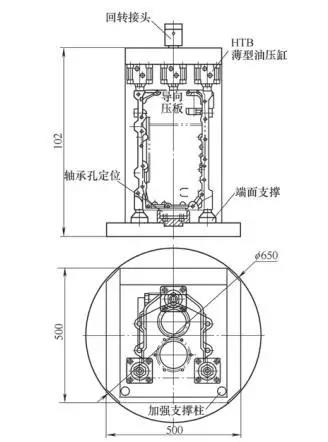
图 8
(3)OP70、OP80分别进行防错设计,做到产品与托盘的对应,托盘与加工程序的对应。
9. 生产线改造实施后达到的效果
(1)生产线的操作人员由原来的44人降至31人,人员降幅为42%。
(2)由于实现了工艺定位的统一和可调试夹具,提升了粗加工生产线对产品的适应性。
(3)采用柔性制造系统的精加工单元,可以实现多品种的同时生产。
(4)物流合理:该生产模式,可以粗精加工连线布局,也可以粗精生产线的异地布局,如将粗加工扩展到毛坯的生产厂家。
(5)由于生产线的柔性化强,可同时生产多个品种,减少在制品的数量,加速资金的周转。
(6)粗精加工分开,使粗加工和铸造的应力得到释放,保证产品尺寸的稳定性。
(7)精加工单元采用了先进的卧式加工中心,并采用湿式加工,避免零件因受热变形对尺寸精度的影响。
10. 结语
通过产品增设工艺定位孔,并使之标准统一,通过夹具和设备的适当调整,就能实现产品在各粗加工单元的及时切换,与自动柔性加工单元(FMS)配套,来满足多品种、小批量的生产要求,并对市场的变化作出快速反应;采用粗精加工分开,消除了应力和热变形对零件精度的影响;统一的工艺定位孔同样也满足了精加工单元的产品切换,使用快速夹紧的液压夹具,提高加工中心的生产效益。
1. 项目背景
目前商用车变速箱壳体采用的生产线为多机细分工序生产线,虽然节拍短,效率高,但无法适应多品种、小批量市场的要求,经常要调整,尺寸的稳定性差,质量波动大;加工中心的产品质量好,但节拍长。企业的发展,迫切要求对目前壳体生产线进行柔性化改造。
2. 原工艺流程
原工艺流程如图1所示。
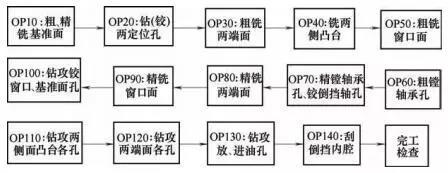
图 1
3. 原工艺存在的主要问题
(1)品种多。商用车变速器壳的品种多,生产线只能生产设定的产品,由于市场对各产品的需求不同,导致生产线的生产不均衡。
(2)开发周期长。每开发一个产品,小批量时都是在相近的生产线上更换工装,更换一个品种需要将近8h的时间,生产线品种的切换就必须增加各品种的库存。
(3)生产线的特点。由通用设备、专机组成的生产线能否达产,其关键点就在于专机的到位时间,专机的生产周期一般需要6个月;而专机线无法满足产品的改型,产品在各加工线之间也难于切换。
(4)生产线产能与配置(见表1)。
表1 生产线产能与配置
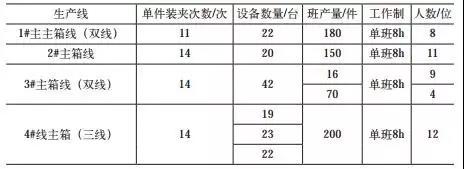
(5)专机线对产品的影响因素:①铸造应力和加工应力。②干切时铸件的热胀冷缩。③分序的定位精度。④转序引起的磕碰。
4. 改造方案的分析
(1)设计精度对加工工艺的要求,如图2所示,如果精铣两端面和精镗轴承孔(铰倒挡孔)在一次装夹下完成,就不存在分序加工的定位累计误差。
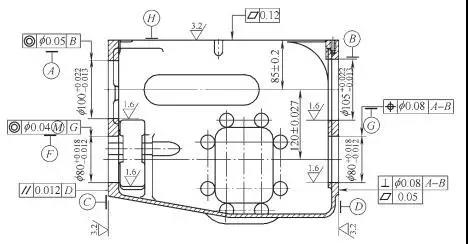
图 2
(2)我们选用了一款壳体加工的生产线,从使用设备、投资额、人员配置和工艺成本几个方面,对不同的方案进行分析(见表2)。
表2 方案对比
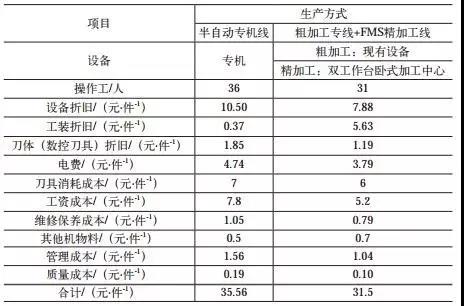
经过以上对比分析,采用粗加工专线+FMS精加工线方案的成本优于自动专机生产线。
5. 改进的措施
(1)要实现生产线对各产品加工的适应性,需要对现有的产品进行设计改进,在基准面的周边设置工艺凸台和工艺定位孔,如图3所示,将工艺定位孔的中心距离L和销孔的孔径设计成一致。
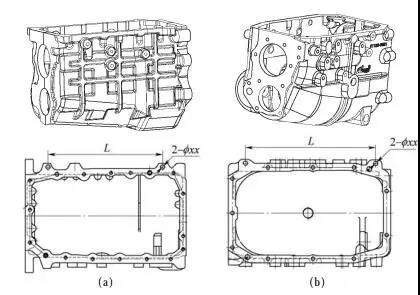
图 3
(2)为了消除铸造应力,加工应力及加工产生的热量对产品质量的影响,将壳体的粗精加工分开。
(3)粗加工工序利用现有的设备资源,组成粗加工单元,发挥专机生产线生产节拍短的优势。
(4)OP10粗铣基准面工序,圆台铣工装的柔性设计:采用三顶针顶入轴承预留孔中,通过伸缩上端两顶针来适应不同长度的箱体,通过弹簧顶针的偏心来适应不同中心距的壳体加工,如图4所示。
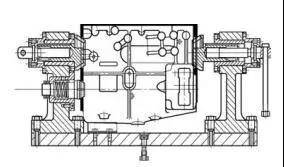
图 4
(5)OP20工序通过调整箱体长度的定位,对不同的箱体进行定位孔的加工,实现工艺定位的统一,这样就可以在OP30、OP40和OP50的铣削工序中实现工装底板的统一,只要调整铣削头的轴向距离就可以适应不同长度箱体铣面的要求;对于OP60粗镗工序,只要更换镗削头就可以适应不同中心距产品的切换。
(6)精加工采用交换工作台卧式加工中心组成的FMS柔性加工生产单元,确保关键尺寸的加工在一次装夹下完成。
6. 改后的工艺流程
改进后粗加工工艺流程如图5所示。
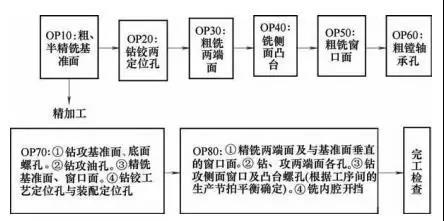
图 5
7. 设备布局
设备布局如图6所示。
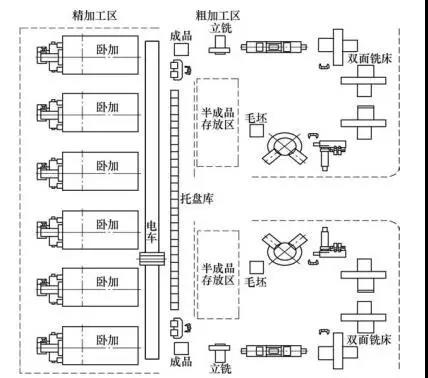
图 6
8. 精加工的夹具的设计
(1)精加工OP70夹具如图7所示,工件推入夹具体后,通过工装底部圆柱锥体导入一轴轴承孔和中间轴孔削边销的顶出,限制了箱体的两个自由度,通过顶部导向压板使得箱体在长度方向进行定位,再经过薄型缸压紧,这样,夹紧力就可以很小,防止箱体的夹持变形,如图7所示。
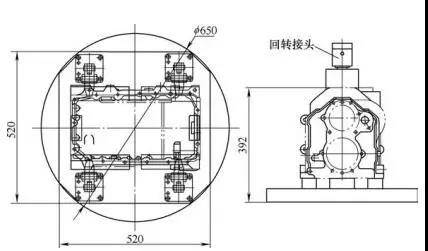
图 7
(2)在OP70工序中,对粗定位孔进行扩孔和铰孔加工,这样便于精加工OP80的夹具底板的统一,如图8所示。
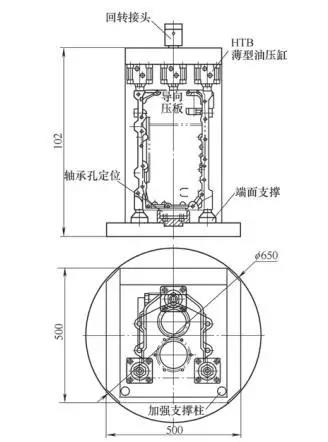
图 8
(3)OP70、OP80分别进行防错设计,做到产品与托盘的对应,托盘与加工程序的对应。
9. 生产线改造实施后达到的效果
(1)生产线的操作人员由原来的44人降至31人,人员降幅为42%。
(2)由于实现了工艺定位的统一和可调试夹具,提升了粗加工生产线对产品的适应性。
(3)采用柔性制造系统的精加工单元,可以实现多品种的同时生产。
(4)物流合理:该生产模式,可以粗精加工连线布局,也可以粗精生产线的异地布局,如将粗加工扩展到毛坯的生产厂家。
(5)由于生产线的柔性化强,可同时生产多个品种,减少在制品的数量,加速资金的周转。
(6)粗精加工分开,使粗加工和铸造的应力得到释放,保证产品尺寸的稳定性。
(7)精加工单元采用了先进的卧式加工中心,并采用湿式加工,避免零件因受热变形对尺寸精度的影响。
10. 结语
通过产品增设工艺定位孔,并使之标准统一,通过夹具和设备的适当调整,就能实现产品在各粗加工单元的及时切换,与自动柔性加工单元(FMS)配套,来满足多品种、小批量的生产要求,并对市场的变化作出快速反应;采用粗精加工分开,消除了应力和热变形对零件精度的影响;统一的工艺定位孔同样也满足了精加工单元的产品切换,使用快速夹紧的液压夹具,提高加工中心的生产效益。
编辑推荐
最新资讯
-
全球产业链聚沪 共探双碳新路径 SNEC
2025-04-18 18:05
-
柯马签订具有约束力的协议收购 Autom
2025-04-17 13:01
-
高效协同新范式:比亚迪叉车领创智能
2025-04-17 10:04
-
埃马克德国总部迎来中国社科院工业经
2025-04-15 09:40
-
埃马克这项全新应用即将在CIMT惊艳首
2025-04-15 09:37