汽车扭梁成形DYNAFORM仿真研究
2018-05-03 14:06:55· 来源:锻压世界
随着中国成为世界上第二大汽车生产国,对汽车模具行业进一步发展提出了新的挑战。整车中约60%~70%零部件属于冲压成形件,如驾驶室、车身、发动机和底盘的表面零部件,为提高成形效率保证成品率,对冲压工艺设计提出了更高要求。传统工艺设计方法采用“试错法”,该种方法容易造成巨大的资源浪费,较长的设计周期,已不能适合新时期的要求。
随着中国成为世界上第二大汽车生产国,对汽车模具行业进一步发展提出了新的挑战。整车中约60%~70%零部件属于冲压成形件,如驾驶室、车身、发动机和底盘的表面零部件,为提高成形效率保证成品率,对冲压工艺设计提出了更高要求。传统工艺设计方法采用“试错法”,该种方法容易造成巨大的资源浪费,较长的设计周期,已不能适合新时期的要求。
近年来,随着计算机技术、有限元仿真技术的不断发展,利用CAE技术进行冲压成形工艺设计的有限元数值分析,节约了大量资源,提高了工艺设计效率,对传统工艺设计方法起到了很好的补充效果。
汽车内支撑件后扭梁属于典型梁类冲压件,在成形过程中容易发生起皱、回弹、拉裂及较薄等表面缺陷,影响使用性能。为提高后扭梁冲压成形成品率,本文借助Dynaform软件对其冲压成形过程进行有限元数值分析,获得较为合理工艺设计参数,为企业生产提供指导作用。
后扭梁简介
如图1所示,为天津某模具公司的汽车底盘后扭梁模型,该模型包括后扭梁上部和下部零件,均为冲压件,并通过CO2气体保护焊将后扭梁上下部连接到一起。
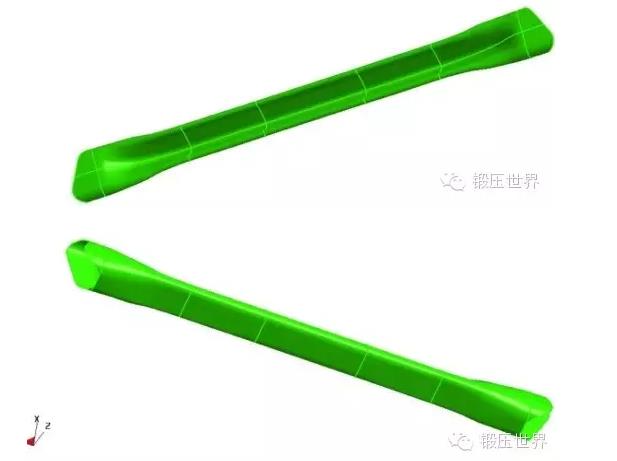
图1汽车后扭梁模型
汽车后扭梁是汽车的重要组成部分,需大批量生产,零件采用常用3mm厚B280VK钢板,该种材料冲压性能良好,适于冲压批量生产,这样不仅能提高生产效率,降低成本,还能够有效保证零件精度与互换性。本文有限元模拟采用Barlat’s-3 parameter Plasticity Model材料模型,该模型适用于任何薄板金属成形分析,相关输入参数如表1所示,应力应变曲线如图2所示,材料参数很大程度上决定有限元模拟精度,因在进行有限元仿真模拟前一般要进行相关实验或查询工程材料手册获得较为准确材料参数。
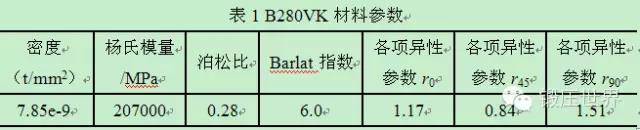
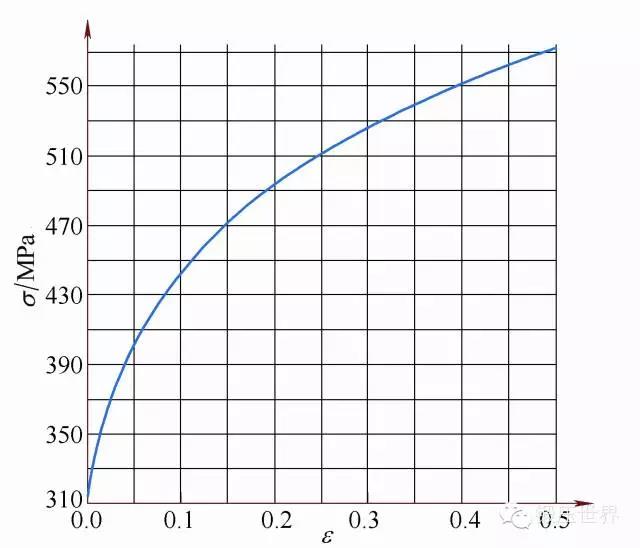
图2 B280VK材料应力应变曲线
后扭梁冲压成形仿真分析
(1)有限元模型 对零件冲压成形进行计算机仿真,主要包括两个步骤:第一,利用CAD软件建立零件几何模型。第二,将几何模型导入Dynaform有限元软件,建立有限元模型,进行有限元前处理、有限元求解和仿真结果分析。本文仅对后扭梁下部进行有限元分析。
扭转梁下部零件是利用CATIA软件建立几何模型,并通过IGES格式输出,导入到Dynaform中,将模型形面当做冲压模拟中的凹模,划分网格,然后通过网格偏移生成冲压凸模和压边圈模型,如图3所示。
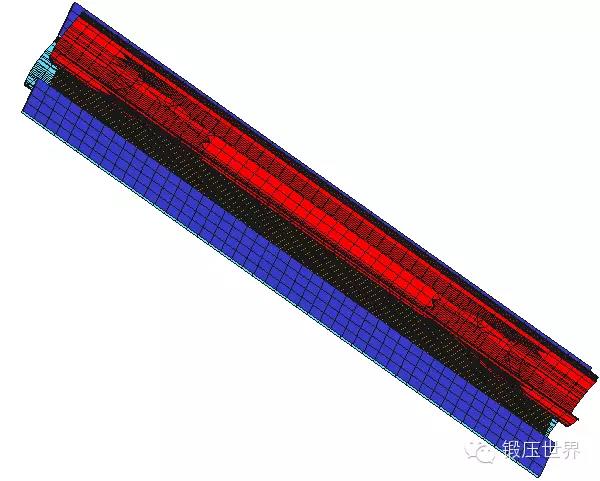
图3有限元模型
(2)边界条件 接触设置:毛坯和模具各个部分间静摩擦系数0.125,滑动摩擦系数取0.1,粘性阻尼系数取20。工艺参数设置:在成形分析过程中使用的工艺参数,有些需符合实际情况;有些为适应分析,需进行相应调整。对于冲压速度,如选择实际值,需较长计算时间,因此在显示求解有限元分析中,采用虚拟冲压速度,同时考虑到人工动态效应,通常冲压速度最大值2000~5000mm/s。本研究采用单动拉延成形,即压边阶段和冲压阶段。首先凹模和压边圈闭合,凹模速度2000mm/s;然后凹模带动压边圈完成拉延过程,凹模速度取5000mm/s,压边力200kN。
(3)结果分析 完成上述设置后,验证模型运动正确性后,即可利用LS-dyna求解器对当前任务进行求解计算。当计算完成后,进入ETA/Post-Processor后处理软件对仿真结果进行分析和评价。图4、图5分别为冲压模拟后板料的成形极限图、厚度分布图。由图4可知,冲压仿真结果不符合质量要求,不仅局部区域存在破裂危险,且大部分区域冲压不完全,存在起皱现象;由图5可知红色区域厚度约为2.078mm,表面此处减薄率为30.7%,蓝色区域厚度为4.969mm,增厚率约为65.6%,而一般认为在成形部分增厚不超过1%,减薄不超过30%,都是可以接受的。通过以上分析可知,该种工艺设计方案不能进行生产加工。
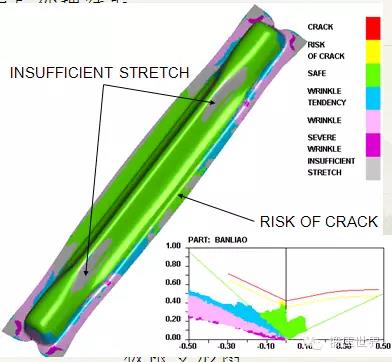
图4成形极限图
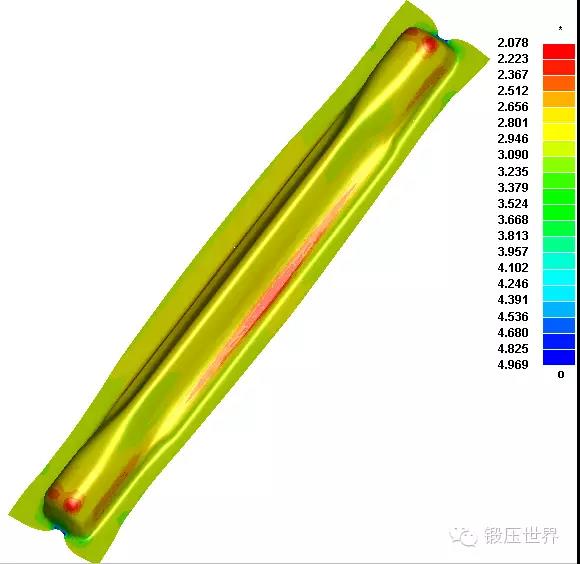
图5厚度分布
改进方案
为解决单工序冲压不能获得较为理想的冲压效果与经济效益,建议采取第二套方案进行分析,即采用2工序冲压成形,如图6所示。工序1将坯料拉伸成V形截面形状,工序2将工件拉延成最后零件形状。
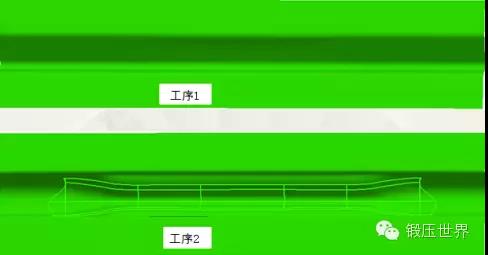
图6冲压工序
(1)边界条件 接触设置与上述参数相同。采用2工序单动拉延成形,即第1工序将坯料拉延成V形,第2工序将工件拉延成最终形状,每一工序均包含压边阶段和冲压阶段参数设置如表2所示,凹模运动方向为正。
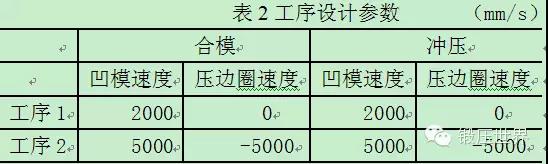
(2)结果分析 经LS-dyna求解后,进入ETA/Post-Processor后处理软件对仿真结果进行分析和评价。图7、8为工序1完成时的成形极限图、厚度分布图。由图7可知,当工序1完成时,工件没有发生折皱、拉裂等表面损伤;由图8可知,红色区域厚度约为2.570mm,表面此处减薄率为14.3%,蓝色区域厚度为3.006mm,增厚率约为0.2%。由此可知,经工序1拉延后,半成品工件没有发生损伤,可继续进行工序2拉延。
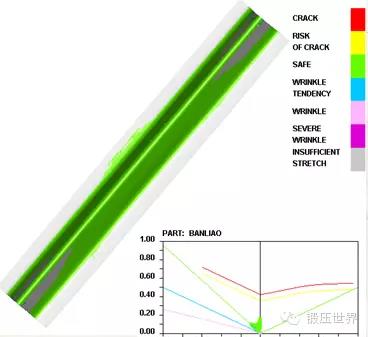
图7工序1成形极限
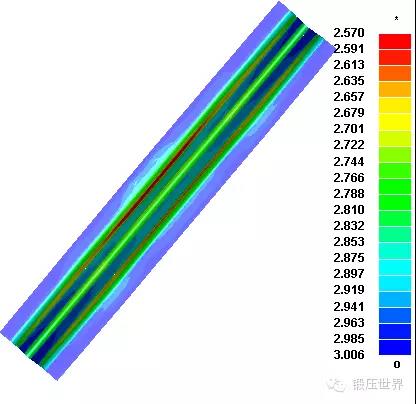
图8 工序1厚度分布
图9、图10为工序2完成时成形极限图、厚度分布图。由图9可知,当工序2完成时,工件没有发生折皱、拉裂等表面损伤;由图10可知,红色区域厚度约为2.505mm,表面此处减薄率为16.5%,蓝色区域厚度为3.010mm,增厚率约为0.3%。由此可知,经工序2拉延后,后扭梁成品表面质量好,可用于后扭梁批量冲压生产活动。
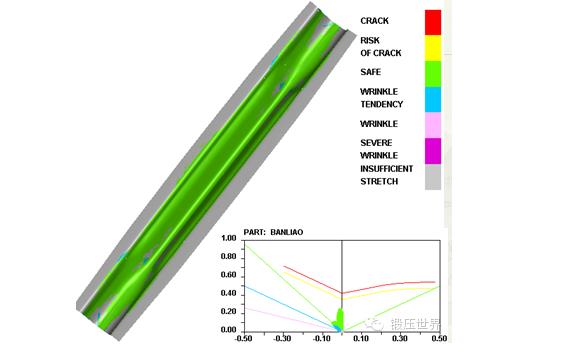
图9 工序2成形极限图
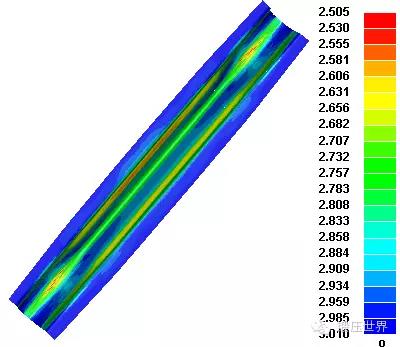
图10工序2厚度分布
文中提出的后扭梁冲压成形改进方案,虽增加了一个工序,但冲压成形效果明显高于改进前,说明可以通过有限元分析可快速探寻较为合理的工艺设计方案,为企业节约资源、提高效率,迅速响应市场需求。
结语
(1)利用Dynaform软件模拟后扭梁的冲压成形过程,能够直观了解成形过程,观察冲压过程工件折皱、拉裂等表面缺陷,缩短模具设计周期。
(2)通过有限元分析,汽车后扭梁冲压需采用2工序较为合理,可避免冲压过程出现折皱、拉裂等缺陷。
阅读 4666 投诉
近年来,随着计算机技术、有限元仿真技术的不断发展,利用CAE技术进行冲压成形工艺设计的有限元数值分析,节约了大量资源,提高了工艺设计效率,对传统工艺设计方法起到了很好的补充效果。
汽车内支撑件后扭梁属于典型梁类冲压件,在成形过程中容易发生起皱、回弹、拉裂及较薄等表面缺陷,影响使用性能。为提高后扭梁冲压成形成品率,本文借助Dynaform软件对其冲压成形过程进行有限元数值分析,获得较为合理工艺设计参数,为企业生产提供指导作用。
后扭梁简介
如图1所示,为天津某模具公司的汽车底盘后扭梁模型,该模型包括后扭梁上部和下部零件,均为冲压件,并通过CO2气体保护焊将后扭梁上下部连接到一起。
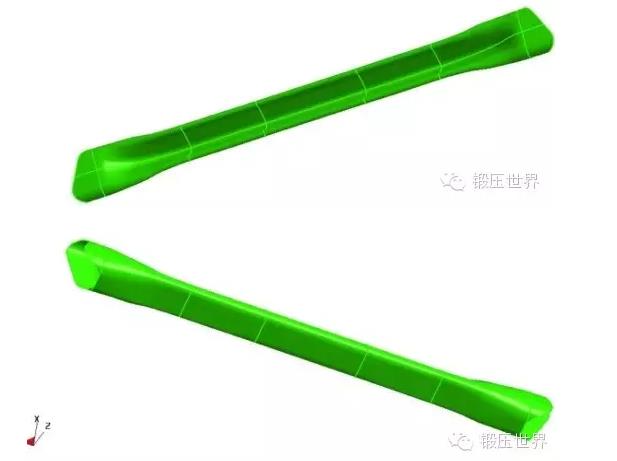
图1汽车后扭梁模型
汽车后扭梁是汽车的重要组成部分,需大批量生产,零件采用常用3mm厚B280VK钢板,该种材料冲压性能良好,适于冲压批量生产,这样不仅能提高生产效率,降低成本,还能够有效保证零件精度与互换性。本文有限元模拟采用Barlat’s-3 parameter Plasticity Model材料模型,该模型适用于任何薄板金属成形分析,相关输入参数如表1所示,应力应变曲线如图2所示,材料参数很大程度上决定有限元模拟精度,因在进行有限元仿真模拟前一般要进行相关实验或查询工程材料手册获得较为准确材料参数。
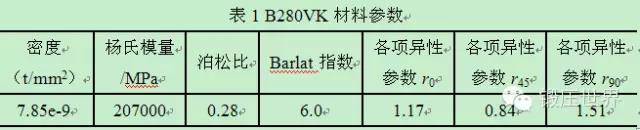
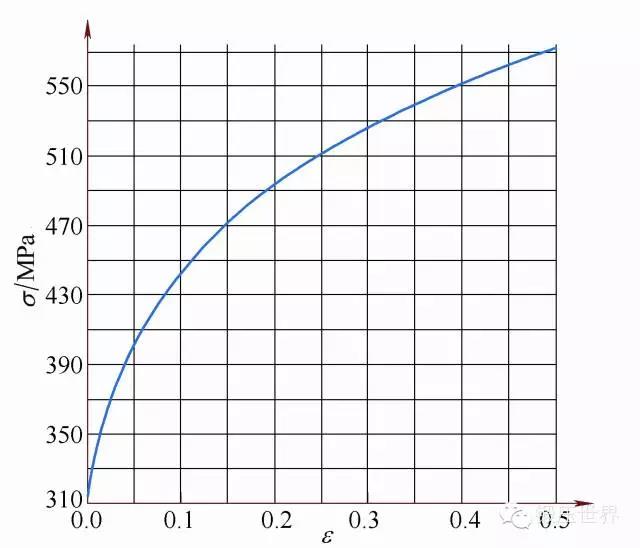
图2 B280VK材料应力应变曲线
后扭梁冲压成形仿真分析
(1)有限元模型 对零件冲压成形进行计算机仿真,主要包括两个步骤:第一,利用CAD软件建立零件几何模型。第二,将几何模型导入Dynaform有限元软件,建立有限元模型,进行有限元前处理、有限元求解和仿真结果分析。本文仅对后扭梁下部进行有限元分析。
扭转梁下部零件是利用CATIA软件建立几何模型,并通过IGES格式输出,导入到Dynaform中,将模型形面当做冲压模拟中的凹模,划分网格,然后通过网格偏移生成冲压凸模和压边圈模型,如图3所示。
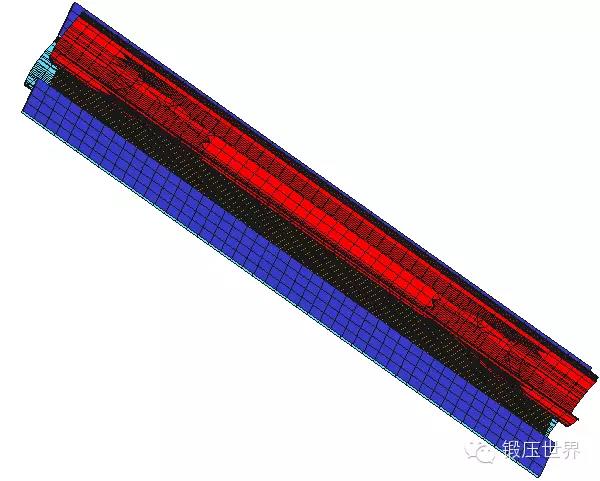
图3有限元模型
(2)边界条件 接触设置:毛坯和模具各个部分间静摩擦系数0.125,滑动摩擦系数取0.1,粘性阻尼系数取20。工艺参数设置:在成形分析过程中使用的工艺参数,有些需符合实际情况;有些为适应分析,需进行相应调整。对于冲压速度,如选择实际值,需较长计算时间,因此在显示求解有限元分析中,采用虚拟冲压速度,同时考虑到人工动态效应,通常冲压速度最大值2000~5000mm/s。本研究采用单动拉延成形,即压边阶段和冲压阶段。首先凹模和压边圈闭合,凹模速度2000mm/s;然后凹模带动压边圈完成拉延过程,凹模速度取5000mm/s,压边力200kN。
(3)结果分析 完成上述设置后,验证模型运动正确性后,即可利用LS-dyna求解器对当前任务进行求解计算。当计算完成后,进入ETA/Post-Processor后处理软件对仿真结果进行分析和评价。图4、图5分别为冲压模拟后板料的成形极限图、厚度分布图。由图4可知,冲压仿真结果不符合质量要求,不仅局部区域存在破裂危险,且大部分区域冲压不完全,存在起皱现象;由图5可知红色区域厚度约为2.078mm,表面此处减薄率为30.7%,蓝色区域厚度为4.969mm,增厚率约为65.6%,而一般认为在成形部分增厚不超过1%,减薄不超过30%,都是可以接受的。通过以上分析可知,该种工艺设计方案不能进行生产加工。
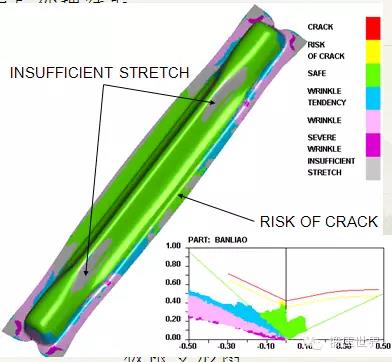
图4成形极限图
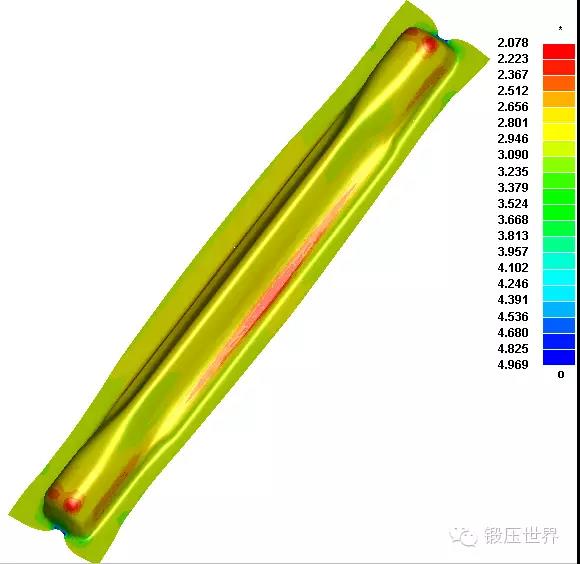
图5厚度分布
改进方案
为解决单工序冲压不能获得较为理想的冲压效果与经济效益,建议采取第二套方案进行分析,即采用2工序冲压成形,如图6所示。工序1将坯料拉伸成V形截面形状,工序2将工件拉延成最后零件形状。
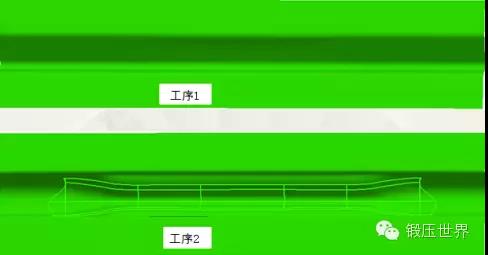
图6冲压工序
(1)边界条件 接触设置与上述参数相同。采用2工序单动拉延成形,即第1工序将坯料拉延成V形,第2工序将工件拉延成最终形状,每一工序均包含压边阶段和冲压阶段参数设置如表2所示,凹模运动方向为正。
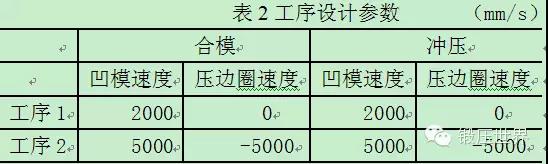
(2)结果分析 经LS-dyna求解后,进入ETA/Post-Processor后处理软件对仿真结果进行分析和评价。图7、8为工序1完成时的成形极限图、厚度分布图。由图7可知,当工序1完成时,工件没有发生折皱、拉裂等表面损伤;由图8可知,红色区域厚度约为2.570mm,表面此处减薄率为14.3%,蓝色区域厚度为3.006mm,增厚率约为0.2%。由此可知,经工序1拉延后,半成品工件没有发生损伤,可继续进行工序2拉延。
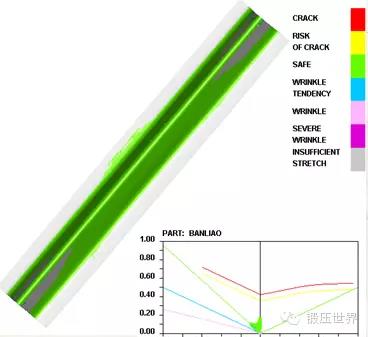
图7工序1成形极限
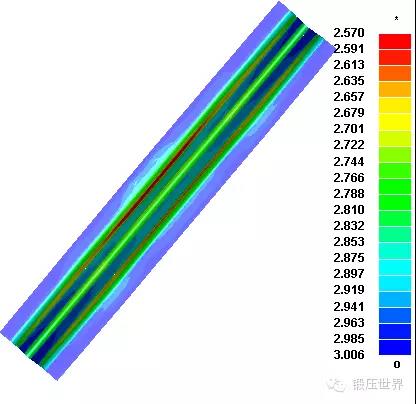
图8 工序1厚度分布
图9、图10为工序2完成时成形极限图、厚度分布图。由图9可知,当工序2完成时,工件没有发生折皱、拉裂等表面损伤;由图10可知,红色区域厚度约为2.505mm,表面此处减薄率为16.5%,蓝色区域厚度为3.010mm,增厚率约为0.3%。由此可知,经工序2拉延后,后扭梁成品表面质量好,可用于后扭梁批量冲压生产活动。
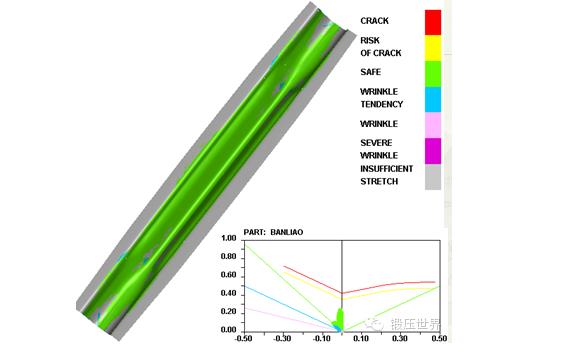
图9 工序2成形极限图
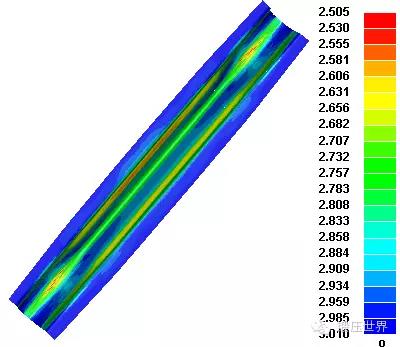
图10工序2厚度分布
文中提出的后扭梁冲压成形改进方案,虽增加了一个工序,但冲压成形效果明显高于改进前,说明可以通过有限元分析可快速探寻较为合理的工艺设计方案,为企业节约资源、提高效率,迅速响应市场需求。
结语
(1)利用Dynaform软件模拟后扭梁的冲压成形过程,能够直观了解成形过程,观察冲压过程工件折皱、拉裂等表面缺陷,缩短模具设计周期。
(2)通过有限元分析,汽车后扭梁冲压需采用2工序较为合理,可避免冲压过程出现折皱、拉裂等缺陷。
阅读 4666 投诉
编辑推荐
最新资讯
-
旭化成微电子开始批量生产用于环保发
2025-04-24 16:00
-
华为、地平线、大众、东风、起亚等引
2025-04-24 08:27
-
全球产业链聚沪 共探双碳新路径 SNEC
2025-04-18 18:05
-
柯马签订具有约束力的协议收购 Autom
2025-04-17 13:01
-
高效协同新范式:比亚迪叉车领创智能
2025-04-17 10:04