关于端面齿轮的相关技术研究
2018-05-08 20:58:22· 来源:齿轮传动 作者:麻俊方
本文针对端面齿轮的特点及应用场合做了相关介绍,并论述了端面齿轮的设计、制造以及加工工艺的相关问题。引言工业实际中,经常会遇到端面齿轮的设计与加工的相关问题,为此,笔者关于该方面问题搜集了部分资料,并进行整理,希望给相关从
本文针对端面齿轮的特点及应用场合做了相关介绍,并论述了端面齿轮的设计、制造以及加工工艺的相关问题。
引言
工业实际中,经常会遇到端面齿轮的设计与加工的相关问题,为此,笔者关于该方面问题搜集了部分资料,并进行整理,希望给相关从业者以启迪。
1.面齿轮传动的特点
面齿轮传动作为一种新型的齿轮传动副,其传动部件主要由一个圆锥齿轮和一个圆柱齿轮组合而成,如图1所示:
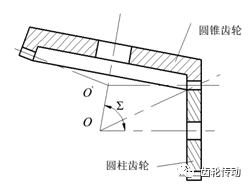
图1 面齿轮传动图
其圆锥齿轮是由齿轮刀具经范成运动加工得到,其齿轮刀具与锥齿轮啮合传动的圆柱齿轮是一样的。当圆锥齿轮与圆柱齿轮之间的轴线夹角为90度时,圆锥齿轮的所有轮齿将会分布在一个圆平面之内,这时的锥齿轮就是面齿轮,如图 2 所示:
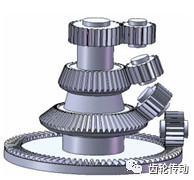
图2 面齿轮传动形成过程图
根据圆柱齿轮的种类不同,与之相啮合的面齿轮齿面节线可以为直齿、斜齿、圆弧齿、端面蜗轮等,如图3:
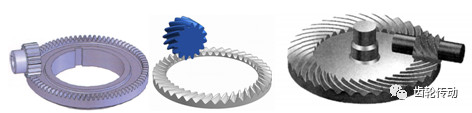
图3 直齿、斜齿、端面蜗轮传动
面齿轮可以被看作是锥齿轮传动的一种特例,它是在锥齿轮传动的基础上,进一步衍生而来的。然而与锥齿轮相比,面齿轮具有一些显著的优势,具体体现在以下几个方面:
(1)锥齿轮根据加工方法的不同,齿面的形状和齿轮的参数都会不一样,因此可以分为奥林康制、格里森制等几种齿制,这就给锥齿轮的加工制造、齿面检测和维修等带来了很多不便,而面齿轮却有着统一的理论齿面;
(2)与复杂的锥齿轮相比,与面齿轮传动的小齿轮只是普通的圆柱齿轮。锥齿轮的大小轮一般采用配对制造,由于小齿轮在传动过程中容易磨损,失效很快,在更换时需要对锥齿轮进行成对更换;而对于圆柱齿轮,其加工方法在国内外都比较成熟,而且互换性好,在磨损严重时只需对小齿轮进行更换,大大降低了使用成本;
(3)在面齿轮传动中,圆柱齿轮对轴向位置的误差不敏感,而在锥齿轮传动中,大小齿轮在装配过程中一定要保证锥顶的重合,轴向位置误差将会引起锥齿轮严重的偏载现象,特别是在一些要求精密传动的重要场合,还需要对锥齿轮进行防位错设计, 而面齿轮不需要, 这样也就大大减小了齿轮传动调整的工作量;
(4)在面齿轮传动中,圆柱齿轮的渐开线齿面具有等距性[2]。传动过程中的安装误差在面齿轮传动过程中不会产生传递误差,但在锥齿轮传动中会有,这种优势对传动过程中运动的准确传递是非常有利的。但是安装误差的存在,会引起接触轨迹线的偏移, 所以必须在面齿轮传动中采取将接触痕迹限制在局部的措施;面齿轮传动中将接触痕迹限制在局部后,可以实现大小齿轮齿面之间的点接触传动,这样的面齿轮传动仍可以在传动过程中保持传动比的恒定,传动过程中的噪声和振动都会大大降低;
(5)面齿轮传动与锥齿轮传动相比,其重合度更大,在空载情况下一般可以达到 1.6~1.8, 甚至高达 2 以上, 在承载时会更高,这样有助于提高承载能力,提高传动的平稳性;特别是当面齿轮传动中的小齿轮齿面是连续的螺旋面时,在传动过程中, 小轮与面齿轮是逐渐进入啮合和脱离啮合的,所以传动会更加平稳、冲击和噪声也会进一步减小;
(6)将面齿轮传动与锥齿轮传动同时应用到减速器中时,前者的重量可减轻 35%左右;特别是面齿轮的小齿轮为直齿圆柱齿轮时,在传动过程中小齿轮没有受到轴向力的作用,这样就可以简化支撑,进一步减轻传动装置的质量。
虽然面齿轮传动副相对于锥齿轮传动副在传动过程中有着诸多的优势, 但面齿轮也存在以下两方面的缺点:
(1)在面齿轮加工过程中,其加工刀具是与圆柱齿轮一一对应的,那么从理论上来说加工面齿轮的刀具将会是无穷多的,这样就给面齿轮加工刀具的设计带来了一些麻烦;
(2)在面齿轮设计过程中,由于根切和齿顶变尖两个因素的影响,其齿宽受到限制而不能设计的太长,这样也就限制了面齿轮的传动强度和承载能力。
总体来说,面齿轮传动的优势还是很明显的。首先,在一些要求尺寸小、重量轻的机械传动产品中,面齿轮在齿宽上所受到的限制将会变成它的一种优势;其次,对于使用面齿轮传动的具体产品,比如汽车、航空产品等等,它的型号一般都是有限的几组, 从而面齿轮的齿面参数也会是固定的, 或者也是有限的几组;再者,有限元法、优化设计等现代设计方法的使用,可以对面齿轮进行非常精确的几何设计,从而也对面齿轮在齿宽上受到限制的这一劣势进行一定程度的弥补。
2.面齿轮参数计算
面齿轮的几何尺寸的计算主要确定两个参数:最小内半径和最大外半径。最小内半径根据齿根不发生根切条件确定, 最大外半径根据齿顶不变尖条件确定。
根据国内相关学者的技术资料,给出的最小内半径为
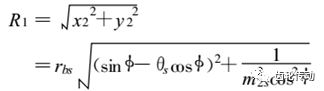
面齿轮齿顶不变尖的最大外半径为:

3.面齿轮加工工艺
从所查得的资料看,面齿轮的加工方法有很多种:插齿、滚齿和磨齿,有的场合甚至采用注塑模、粉末冶金和锻造等非传统齿轮加工方法来加工圆柱齿轮和面齿轮以实现面齿轮传动。
早在 1942 年,美国的 E.Miller 申请的专利文献《Hob for generation crown gears》中就提出了采用滚刀加工面齿轮的思想,该专利的主要思想是:滚刀螺旋面可由横截面为渐开线的刀具范成加工出来。但通过滚齿加工面齿轮,得到的面齿轮齿面形状与理论偏差至少有 40~50 微米,精度上达不到要求。由于没有提出正确的滚刀螺旋面的齿面形状,滚刀螺旋面的修正和加工等问题也没有很好的解决,因而导致了加工面齿轮的失败。
在 1992 年的国际动力传输和齿轮会议上, Ishii 等人也提出了采用数控滚齿机来加工面齿轮,该方法中采用了“飞刀”来代替专用滚刀,减小了切削力,提高了齿面精度。日本的 Hagiwara 等人在 1995 年提出了基于“虚位移原理”的面齿轮滚齿方法,其齿接触试验显示,滚切得到的面齿轮经抛光后接触平滑。荷兰的 Crown Gear 公司也提出了数控滚齿和数控磨齿来加工面齿轮的方法。经磨齿后其加工精度可达 AGMA11~12 级,甚至更高。
在国外,目前最重要的进展是美国Boeing公司与加拿大的North Star公司协作研制的面齿轮5轴磨床。该磨齿机能够磨削不同锥角、尺寸范围较大、满足航空使用要求的面齿轮,可生产出精度达AGMA12级的面齿轮和小齿轮,面齿轮的外半径尺寸从200mm到500mm,2828马力的分流传动验证机也已经研制成功。
从加工精度来看,插齿和滚齿属于粗加工,磨齿属于精加工;从加工材料看,前两者属于软齿面加工,后者属于硬齿面加工。当然,这些加工方法中,最简单的还是插齿加工,这种加工运动形式比较简单,加工过程也就是模拟刀具和面齿轮之间的范成运动。
面齿轮加工中如果希望对面齿轮修形 , 可通过选用不同插齿刀齿数来进行。这样可实现圆柱齿轮与面齿轮接触的局部化。具体地来说, 就是使插刀的齿数zs 比与面齿轮相啮合圆柱齿轮的齿数Z1多若干个齿。例如 ,渐开线圆柱齿轮为22个齿,插齿刀可选用25个齿。这样能使插齿加工出来的面齿轮的齿廓曲率变大。
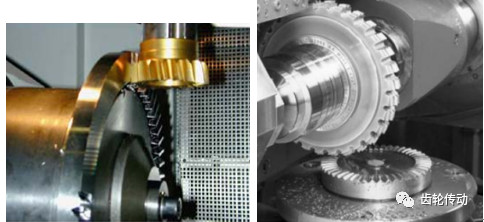
图4 面齿轮的插齿加工(左)与滚齿加工(右)
磨削面齿轮的原理是采用连续范成运动的原理, 图 4中所示为磨轮 (砂轮)、面齿轮和假想的圆柱齿轮刀具相啮合的情况。磨轮与面齿轮之间的运动和面齿轮传动中啮合运动相同,即为范成运动,从而能加工出与配对小齿轮相对应的共轭齿廓。从理论上讲,砂轮的几何形状可以根据啮合原理,从与之共轭的面齿轮齿面方程推导出来。
齿轮刀具和小齿轮之间的啮合为虚拟的内啮合,它们之间的啮合关系为线接触,齿轮刀具与面齿轮的啮合关系也是线接触,最后得到实际啮合中小齿轮与面齿轮的啮合关系为点接触。
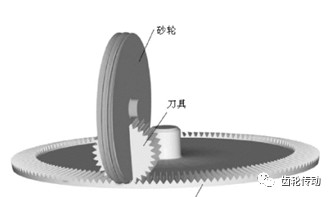
图5 砂轮、面齿轮、刀具之间的啮合关系
另外,有相关文献介绍了弧线齿面齿轮传动的加工工艺。弧线齿面齿轮传动是一种全新的齿轮传动结构,大小轮在传动中凸凹两啮合面为点接触,除了在强度、啮合平稳性方面具有优势外,最为重要的是加工方便 ,可用现有机床设备和刀盘加工。
弧线齿面齿轮传动是由弧线齿面齿轮( 大轮)和弧线齿圆柱齿轮(小轮) 组成的, 大小轮加工均采用格里森刀盘;大轮齿数较多,采用成形加工可提高加工效率, 小轮用展成加工。
为避免加工大轮时,切削刀盘和已加工完成的轮齿产生干涉, 必须将刀盘倾斜一定角度;小轮有一定刀倾角之后,可改善齿面曲率特性。对成形法加工的弧线齿面齿轮齿面沿齿廓方向修形,可减小传动误差幅值和获得开口向下抛物线形传动误差曲线。
引言
工业实际中,经常会遇到端面齿轮的设计与加工的相关问题,为此,笔者关于该方面问题搜集了部分资料,并进行整理,希望给相关从业者以启迪。
1.面齿轮传动的特点
面齿轮传动作为一种新型的齿轮传动副,其传动部件主要由一个圆锥齿轮和一个圆柱齿轮组合而成,如图1所示:
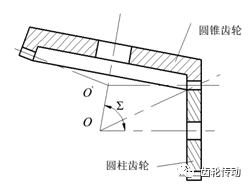
图1 面齿轮传动图
其圆锥齿轮是由齿轮刀具经范成运动加工得到,其齿轮刀具与锥齿轮啮合传动的圆柱齿轮是一样的。当圆锥齿轮与圆柱齿轮之间的轴线夹角为90度时,圆锥齿轮的所有轮齿将会分布在一个圆平面之内,这时的锥齿轮就是面齿轮,如图 2 所示:
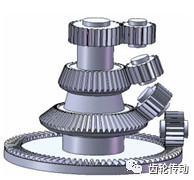
图2 面齿轮传动形成过程图
根据圆柱齿轮的种类不同,与之相啮合的面齿轮齿面节线可以为直齿、斜齿、圆弧齿、端面蜗轮等,如图3:
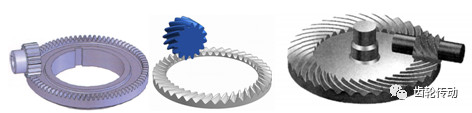
图3 直齿、斜齿、端面蜗轮传动
面齿轮可以被看作是锥齿轮传动的一种特例,它是在锥齿轮传动的基础上,进一步衍生而来的。然而与锥齿轮相比,面齿轮具有一些显著的优势,具体体现在以下几个方面:
(1)锥齿轮根据加工方法的不同,齿面的形状和齿轮的参数都会不一样,因此可以分为奥林康制、格里森制等几种齿制,这就给锥齿轮的加工制造、齿面检测和维修等带来了很多不便,而面齿轮却有着统一的理论齿面;
(2)与复杂的锥齿轮相比,与面齿轮传动的小齿轮只是普通的圆柱齿轮。锥齿轮的大小轮一般采用配对制造,由于小齿轮在传动过程中容易磨损,失效很快,在更换时需要对锥齿轮进行成对更换;而对于圆柱齿轮,其加工方法在国内外都比较成熟,而且互换性好,在磨损严重时只需对小齿轮进行更换,大大降低了使用成本;
(3)在面齿轮传动中,圆柱齿轮对轴向位置的误差不敏感,而在锥齿轮传动中,大小齿轮在装配过程中一定要保证锥顶的重合,轴向位置误差将会引起锥齿轮严重的偏载现象,特别是在一些要求精密传动的重要场合,还需要对锥齿轮进行防位错设计, 而面齿轮不需要, 这样也就大大减小了齿轮传动调整的工作量;
(4)在面齿轮传动中,圆柱齿轮的渐开线齿面具有等距性[2]。传动过程中的安装误差在面齿轮传动过程中不会产生传递误差,但在锥齿轮传动中会有,这种优势对传动过程中运动的准确传递是非常有利的。但是安装误差的存在,会引起接触轨迹线的偏移, 所以必须在面齿轮传动中采取将接触痕迹限制在局部的措施;面齿轮传动中将接触痕迹限制在局部后,可以实现大小齿轮齿面之间的点接触传动,这样的面齿轮传动仍可以在传动过程中保持传动比的恒定,传动过程中的噪声和振动都会大大降低;
(5)面齿轮传动与锥齿轮传动相比,其重合度更大,在空载情况下一般可以达到 1.6~1.8, 甚至高达 2 以上, 在承载时会更高,这样有助于提高承载能力,提高传动的平稳性;特别是当面齿轮传动中的小齿轮齿面是连续的螺旋面时,在传动过程中, 小轮与面齿轮是逐渐进入啮合和脱离啮合的,所以传动会更加平稳、冲击和噪声也会进一步减小;
(6)将面齿轮传动与锥齿轮传动同时应用到减速器中时,前者的重量可减轻 35%左右;特别是面齿轮的小齿轮为直齿圆柱齿轮时,在传动过程中小齿轮没有受到轴向力的作用,这样就可以简化支撑,进一步减轻传动装置的质量。
虽然面齿轮传动副相对于锥齿轮传动副在传动过程中有着诸多的优势, 但面齿轮也存在以下两方面的缺点:
(1)在面齿轮加工过程中,其加工刀具是与圆柱齿轮一一对应的,那么从理论上来说加工面齿轮的刀具将会是无穷多的,这样就给面齿轮加工刀具的设计带来了一些麻烦;
(2)在面齿轮设计过程中,由于根切和齿顶变尖两个因素的影响,其齿宽受到限制而不能设计的太长,这样也就限制了面齿轮的传动强度和承载能力。
总体来说,面齿轮传动的优势还是很明显的。首先,在一些要求尺寸小、重量轻的机械传动产品中,面齿轮在齿宽上所受到的限制将会变成它的一种优势;其次,对于使用面齿轮传动的具体产品,比如汽车、航空产品等等,它的型号一般都是有限的几组, 从而面齿轮的齿面参数也会是固定的, 或者也是有限的几组;再者,有限元法、优化设计等现代设计方法的使用,可以对面齿轮进行非常精确的几何设计,从而也对面齿轮在齿宽上受到限制的这一劣势进行一定程度的弥补。
2.面齿轮参数计算
面齿轮的几何尺寸的计算主要确定两个参数:最小内半径和最大外半径。最小内半径根据齿根不发生根切条件确定, 最大外半径根据齿顶不变尖条件确定。
根据国内相关学者的技术资料,给出的最小内半径为
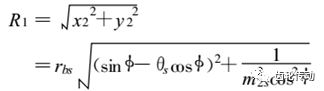
面齿轮齿顶不变尖的最大外半径为:

3.面齿轮加工工艺
从所查得的资料看,面齿轮的加工方法有很多种:插齿、滚齿和磨齿,有的场合甚至采用注塑模、粉末冶金和锻造等非传统齿轮加工方法来加工圆柱齿轮和面齿轮以实现面齿轮传动。
早在 1942 年,美国的 E.Miller 申请的专利文献《Hob for generation crown gears》中就提出了采用滚刀加工面齿轮的思想,该专利的主要思想是:滚刀螺旋面可由横截面为渐开线的刀具范成加工出来。但通过滚齿加工面齿轮,得到的面齿轮齿面形状与理论偏差至少有 40~50 微米,精度上达不到要求。由于没有提出正确的滚刀螺旋面的齿面形状,滚刀螺旋面的修正和加工等问题也没有很好的解决,因而导致了加工面齿轮的失败。
在 1992 年的国际动力传输和齿轮会议上, Ishii 等人也提出了采用数控滚齿机来加工面齿轮,该方法中采用了“飞刀”来代替专用滚刀,减小了切削力,提高了齿面精度。日本的 Hagiwara 等人在 1995 年提出了基于“虚位移原理”的面齿轮滚齿方法,其齿接触试验显示,滚切得到的面齿轮经抛光后接触平滑。荷兰的 Crown Gear 公司也提出了数控滚齿和数控磨齿来加工面齿轮的方法。经磨齿后其加工精度可达 AGMA11~12 级,甚至更高。
在国外,目前最重要的进展是美国Boeing公司与加拿大的North Star公司协作研制的面齿轮5轴磨床。该磨齿机能够磨削不同锥角、尺寸范围较大、满足航空使用要求的面齿轮,可生产出精度达AGMA12级的面齿轮和小齿轮,面齿轮的外半径尺寸从200mm到500mm,2828马力的分流传动验证机也已经研制成功。
从加工精度来看,插齿和滚齿属于粗加工,磨齿属于精加工;从加工材料看,前两者属于软齿面加工,后者属于硬齿面加工。当然,这些加工方法中,最简单的还是插齿加工,这种加工运动形式比较简单,加工过程也就是模拟刀具和面齿轮之间的范成运动。
面齿轮加工中如果希望对面齿轮修形 , 可通过选用不同插齿刀齿数来进行。这样可实现圆柱齿轮与面齿轮接触的局部化。具体地来说, 就是使插刀的齿数zs 比与面齿轮相啮合圆柱齿轮的齿数Z1多若干个齿。例如 ,渐开线圆柱齿轮为22个齿,插齿刀可选用25个齿。这样能使插齿加工出来的面齿轮的齿廓曲率变大。
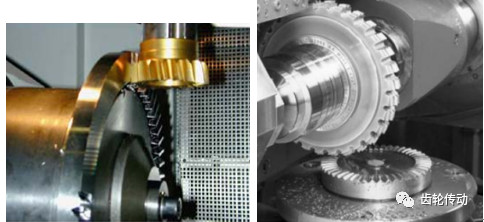
图4 面齿轮的插齿加工(左)与滚齿加工(右)
磨削面齿轮的原理是采用连续范成运动的原理, 图 4中所示为磨轮 (砂轮)、面齿轮和假想的圆柱齿轮刀具相啮合的情况。磨轮与面齿轮之间的运动和面齿轮传动中啮合运动相同,即为范成运动,从而能加工出与配对小齿轮相对应的共轭齿廓。从理论上讲,砂轮的几何形状可以根据啮合原理,从与之共轭的面齿轮齿面方程推导出来。
齿轮刀具和小齿轮之间的啮合为虚拟的内啮合,它们之间的啮合关系为线接触,齿轮刀具与面齿轮的啮合关系也是线接触,最后得到实际啮合中小齿轮与面齿轮的啮合关系为点接触。
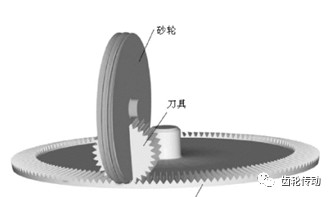
图5 砂轮、面齿轮、刀具之间的啮合关系
另外,有相关文献介绍了弧线齿面齿轮传动的加工工艺。弧线齿面齿轮传动是一种全新的齿轮传动结构,大小轮在传动中凸凹两啮合面为点接触,除了在强度、啮合平稳性方面具有优势外,最为重要的是加工方便 ,可用现有机床设备和刀盘加工。
弧线齿面齿轮传动是由弧线齿面齿轮( 大轮)和弧线齿圆柱齿轮(小轮) 组成的, 大小轮加工均采用格里森刀盘;大轮齿数较多,采用成形加工可提高加工效率, 小轮用展成加工。
为避免加工大轮时,切削刀盘和已加工完成的轮齿产生干涉, 必须将刀盘倾斜一定角度;小轮有一定刀倾角之后,可改善齿面曲率特性。对成形法加工的弧线齿面齿轮齿面沿齿廓方向修形,可减小传动误差幅值和获得开口向下抛物线形传动误差曲线。
举报 0
收藏 0
分享 110
-
埃马克德国总部迎来中国社科院工业经济研究所代
2025-04-15 -
埃马克这项全新应用即将在CIMT惊艳首秀!
2025-04-15 -
[转载] 机床巨头埃马克:百年跌宕再出发
2025-03-31 -
赋能电动未来,埃马克重庆技术日展示尖端制造技
2025-03-03
编辑推荐
最新资讯
-
全球产业链聚沪 共探双碳新路径 SNEC
2025-04-18 18:05
-
柯马签订具有约束力的协议收购 Autom
2025-04-17 13:01
-
高效协同新范式:比亚迪叉车领创智能
2025-04-17 10:04
-
埃马克德国总部迎来中国社科院工业经
2025-04-15 09:40
-
埃马克这项全新应用即将在CIMT惊艳首
2025-04-15 09:37