汽车总装工艺技术应用趋势与研究
2018-05-14 13:17:51· 来源:汽车实用技术杂志社
随着汽车主机厂平台车型增加及多车型混线生产要求、人力成本攀升和生产交货期缩短的压力下,导致汽车总装厂对于先进装配技术和自动化设备的敏感性大大提高。各汽车厂都在提升总装工艺装备技术水平,采用更先进的装配设备提高产品质量,以应对满足新兴市场及提高产品市场竞争力的要求。汽车总装工艺作为汽车制造的最重要环节,在规模、质量、即时性、成本、产品先进性等方面都影响着市场竞争力。目前汽车总装工艺技术发展向着模块化、自动化、柔性化、人性化、智能数字化的趋势发展。随着市场的激烈竞争环境下,这些技术趋势正在从企业竞争的优势技术
引言:
随着汽车主机厂平台车型增加及多车型混线生产要求、人力成本攀升和生产交货期缩短的压力下,导致汽车总装厂对于先进装配技术和自动化设备的敏感性大大提高。各汽车厂都在提升总装工艺装备技术水平,采用更先进的装配设备提高产品质量,以应对满足新兴市场及提高产品市场竞争力的要求。汽车总装工艺作为汽车制造的最重要环节,在规模、质量、即时性、成本、产品先进性等方面都影响着市场竞争力。目前汽车总装工艺技术发展向着模块化、自动化、柔性化、人性化、智能数字化的趋势发展。随着市场的激烈竞争环境下,这些技术趋势正在从企业竞争的优势技术,向一种企业竞争的必备技术转变。
1 总装工艺技术
1.1模块化
汽车总装工艺采用模块化设计可以把不同级别车型的众多零部件进行通用标准化生产,同时又可以灵活的搭载其他的新技术。制造过程中,采用总装模块化可以减少总装工位线长度和主线装配工时,提高装配效率,扩展装配线的柔性化程度,缩短汽车生产周期。目前的模块化主要有电子控制系统模块化和产品结构模块化两种方向性的模块趋势。
1.1.1电子控制系统模块化
随着车联网的科技发展及信息娱乐需求下,出现以ECU(电子控制单元)集成和标准化趋势,ECU群的“标准件”功能成为各车型通用的模块,将各种功能细分的ECU整合起来,实现一个全车范围内的电子控制系统模块化。比如传动控制、车身控制、安全控制、驾驶辅助控制、动态底盘控制系统和多媒体移动互联网服务等标准系统为单位进行模块化大集成。
1.1.2产品结构模块化
通过将产品多功能结构与各种零部件相互关系的组合,把汽车各子系统产品结构与相互零部件组装集成为大总成模块。可以显著缩短产线长度及生产节拍,优化装配工艺和降低制造成本。目前总装工艺的模块化应用主要有前端块化、车门模块化、底盘模块化、顶棚集成化、油箱集成化、IP模块化、前后保模块化、车轮模块化等(如图1所示)。
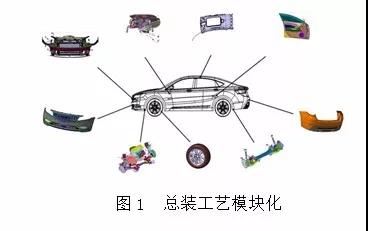
产品结构模块化中最具代表性的是底盘动力模块化,融合目前各种先进的装配工艺技术。以某汽车品牌的的MQB底盘动力模块为例,简要说明下底盘平台高度柔性化和集成化的模块化趋势。
(1)采用多种柔性托盘(如图2所示)组合形成底盘合车工装(如图3所示),包含前托盘、中托盘、后托盘。多种柔性化的扳倒式、伸缩式、限位块式定位销运用可以满足多种组合动力模块的装配支撑。非常方便底盘的自动化装配,减少下车体装配人机性差的问题。
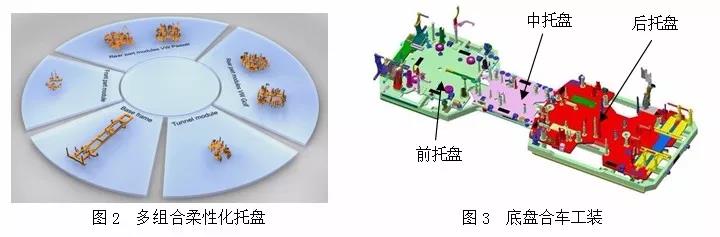
(2)底盘模块化集成程度非常高。如图4所示,除将常规的前悬模块、后悬模块外,还几乎将全部下车体附件如排气管总成、油箱总成、隔热垫、操纵机构及燃油管路集成在大托盘工装上。显著的减少底盘主线工位数和装配工时。
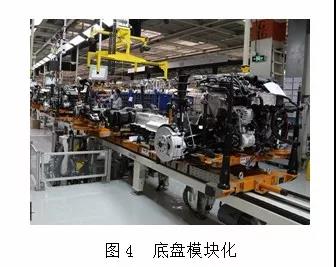
(3)底盘标准件自动拧紧技术应用。如图5所示,将紧固件及拧紧套筒集成在大托盘工装上,柔性化设置高精度电动拧紧工具,利用信息化网络系统完成标准件装配的力矩控制和质量监测。是网络化装配制造技术在汽车装配生产线上的典型工程应用。
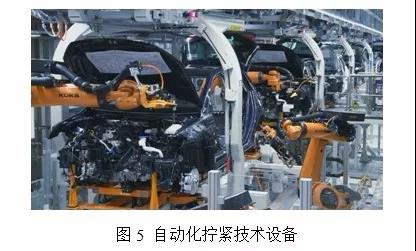
(4)底盘合车自动化。配合AGV自动导引小车,利用电磁或光学等自动导引装置,实现路径自动跟踪、转向同步行驶,并且具有障碍物识别、停车、自动调速和无线通讯等功能,实现底盘合车无人化、自动化装配(见图6)。
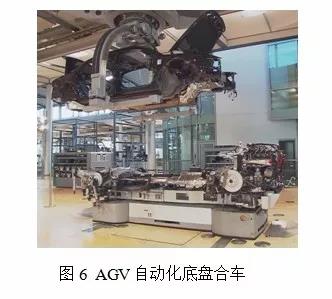
1.2 自动化
受到人力成本攀升及制造节拍的影响,并且自动化设备使用可以显著提高产品的质量和装配稳定性,汽车总装厂对于自动化的需求趋势日益明显。较为典型的采用自动化的工序内容有:
(1)前/后风挡和全景天窗的涂胶工序采用涂胶机器人设备,避免了人工打胶的断胶现象,同时胶型质量更可靠稳定(见图7),配合风挡装配机器人全自动化装配(见图8),提高车辆密封性。
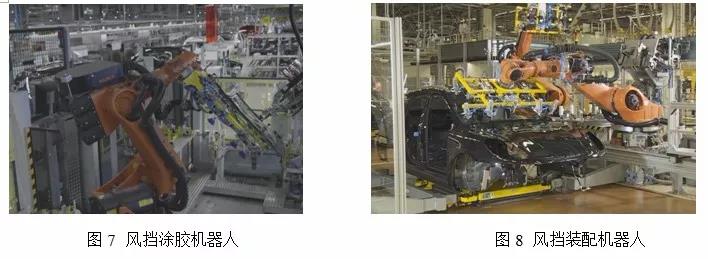
(2)车轮模块通过轮胎自动分装线完成分装,并通过自动输送线运输至装配工位。如图9所示,自动化分装系统能根据车辆配置自动识别不同规格的轮胎,自动完成轮胎装配和动平衡检测,有效的保证了轮胎分装的品质与生产的稳定性。采用机器人装配轮胎至车身及车轮螺母自动化拧紧技术(见图10),满足可变多轴拧紧及PCD变径的柔性化装配需求。提高产品质量的同时也减少人力成本。
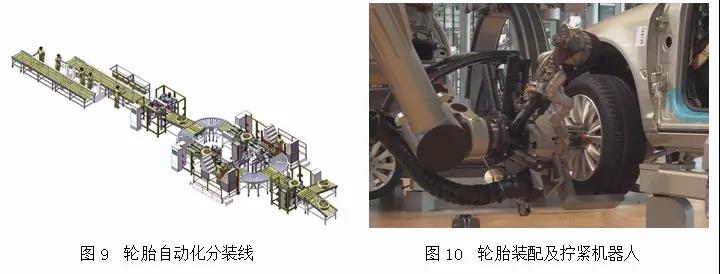
(3)各种需助力设备辅助装配的模块化工序。如IP模块采用自动化的机械手装配代替人工装配(如图11所示),可以保证高精度的定位装配,对于内饰外观质量的尺寸链控制,造型效果的感官质量有很大的提升;且自动化机械手可以集成拧紧设备紧固标准件(如图12所示),大大提高装配质量和节省人力成本。
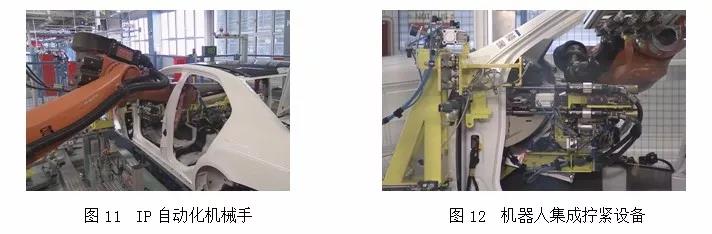
1.3 加注设备真空化及智能化
制动液、冷却液、动力转向液、空调冷媒等加注设备向着抽真空加注、自动检测、自动定量加注等功能集成设备趋势,以及出现油液二合一以上的集成加注设备的应用(如图13)。
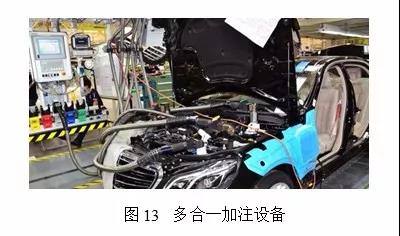
1.4力矩控制智能化
力矩拧紧设备广泛采用高精度电动拧紧设备。拧紧技术也从通常的扭矩法转向扭矩+转角法或屈服强度法应用;从控制力矩间接控制拧紧质量向着直接控制预紧力为目的,具备在线动态力矩控制与监测(见图14);工厂联网形成力矩数据化网络系统,实时监控拧紧质量、数据储存和追溯、数据信息分析处理等(见图15),进行智能统计过程控制(SPC),提高和稳定制造过程控制能力(CPK)。利用网络化通信模块与单片机控制器相结合,进行信息的交互,设计成一体式智能网络装配控制模块,完成力矩装配的控制。
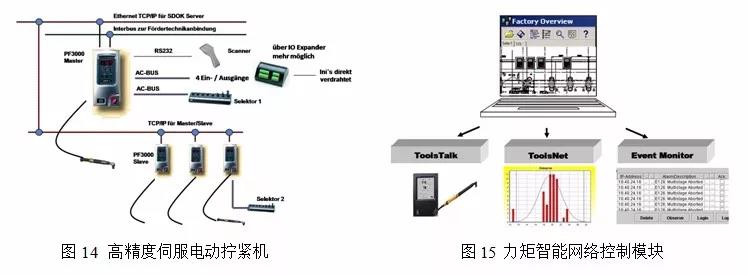
1.5 柔性化工装
总装整体工序中,部分装配工序由于装配空间狭小或零附件复杂等原因造成装配人员的非常规作业姿势,装配人机性很差。解决方法一方面通过采用自动化机器人代替人工装配外,另一方面需要在工装或作业手法上进行柔性化设计提高人机性。具体案例有:
(1)底盘线下车体附件的装配需要人员在车底下装配,出现人员下蹲及身体弯曲等不良作业动作。现在解决的方法是对车身吊具设备进行人机性设计,如图16所示使用高度可调及车身可旋转的C型钳吊具,确保人员可以站立式姿势或较佳的姿势进行正常装配。
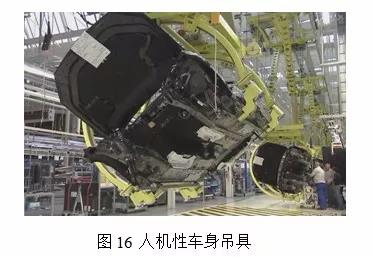
(2)内饰线如机舱内线束等工序出现人员装配位置和车身悬挂高度不吻合,出现人员下蹲或身体弯曲的姿势来完成装配作业。通过采用Z向高度柔性可调的车身托盘,可以保证在不同的工位将车身定位在合理的高度,方便人员站立式装配(如图17)。另外如车体内装配人员采用坐式机械手(见图18),使员工可以坐着完成作业,减少蹲着及躯干弯曲造成的身体机能劳损。
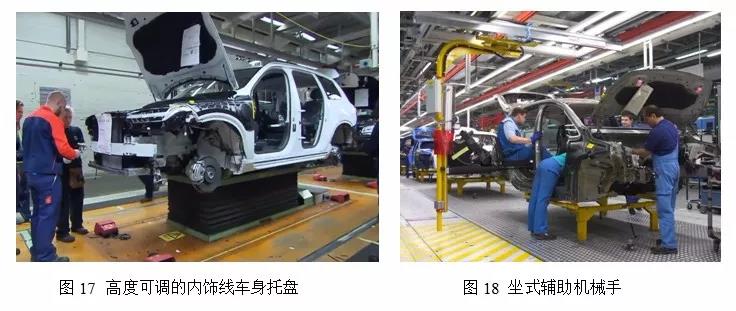
1.6 SPS物流
汽车总装厂在多车型混线生产的趋势下,线旁储料空间不足及物料种类繁多限制了产线的柔性化和物流效率。有效的解决方式是采用SPS物流形式——随行配料系统(SPS)。如图19所示,SPS是指一种单量份向生产线准时化配送的物流方式。该物流方式将拣料与装配分开,使各自作业更加专业化和模块化,有利于消除员工不必要的非增值操作,有效防止总装装配线的错、漏装问题,从而提高装配质量;同时配合随车物料投放形式可以减少线边物料摆放空间约束,且采用AGV小车运输代替人工物流(见图20),满足准时化的高要求及多车型混线物流配送要求,是一种普遍采用的物流趋势。
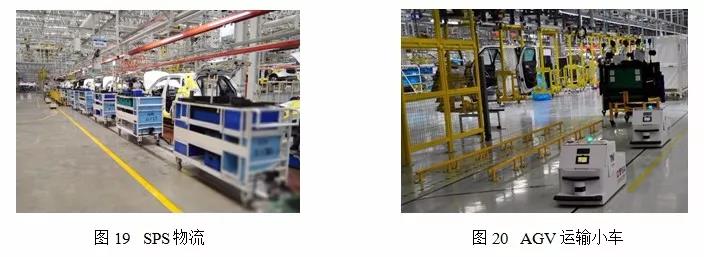
2 同步工程
汽车总装工艺技术开发过程中,同步工程技术的作用越来越明显。产品项目开发中已经减少了样车试制及验证的数量和时间,提高了虚拟仿真在产品设计过程的比重。更多在要求在产品前期虚拟仿真中发现制造问题并提前解决,减少工厂技改及产品设变费用。
2.1装配仿真分析
汽车总装的同步工程在新车产品开发之初,就开始介入对产品结构装配性、设备操作性进行虚拟仿真分析(见图21、22),提前在设计阶段发现和解决装配工艺问题。
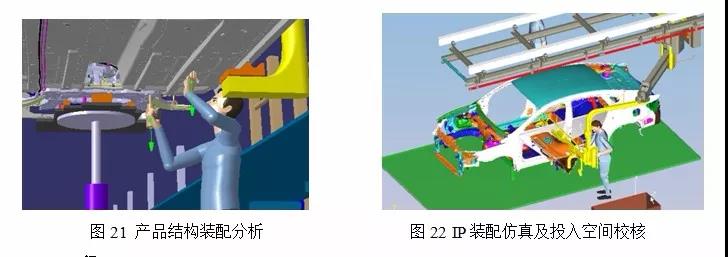
2.2 IE工程
产品数据设计至冻结前后, 利用3D仿真分析软件中的工时分析模块,综合主机厂生产线实际的相关信息,对装配工人的操作工时和作业强度进行分析,优化工序流程和作业内容,减小工位劳动强度(如图23所示)。同时进行产线工时线平衡分析,提前发现和解决工时均衡及瓶颈工位等问题(如图24所示)。

2.3数字化工厂
合理、经济科学的生产工艺流程设计对于降低汽车生产主线长度、制造能耗,提高产线柔性化有很大帮助。在工厂规划之初利用虚拟仿真技术对工艺流程(见图25)进行设定和虚拟验证,及进行数字工厂规划和仿真(见图26)。提前发现生产隐患问题和减少不必要的工厂技改费用。
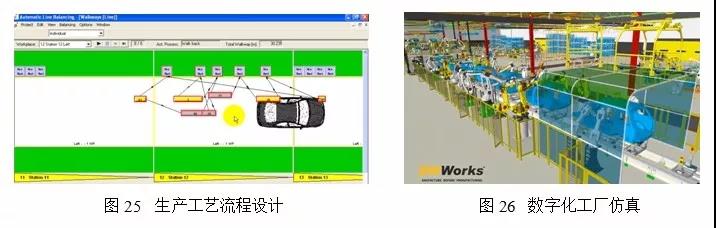
3 结语
汽车装配的新工艺和新技术,随着市场、技术及政策导向等多方面因素的推动而不断进步,缩短生产周期、提高整车质量、降低制造成本、提高市场竞争力等方面都是汽车制造商追求的共同目标,在经历平台化、整车模块化开发与设计后,现代汽车制造业出现了如下较为明显的发展趋势。
1)产品结构通用化、模块化技术简化了装配关系,逐步改变了传统汽车制造商的装配策略与工艺设计的理念,实现零部件全球采购和全球供货。该技术势必革新汽车制造业中的供应链关系和零部件配套模式。
2)模块化、柔性化等制造工艺的普及逐步形成了新的制造形态,一些高级汽车制造商完成从平台化到模块化生产方式的过渡,甚至达到了可扩展整车平台模块化生产方式高度。具备在数个模块化扩展性开发基础上,垂直形成“多种汽车平台”和“高低端多层级模块群”,同步设计出全系品牌下功能用途以及风格不同的高低端多级车型产品,实现更高效率和规模的设计和生产。
3)数字化、自动化、智能化等优势技术的应用虽然在开发前期需要较大成本投入,但随着优势技术不断转化为实际效益,新车型开发和制造的成本大幅度减少,投资回报率具有明显优势,已逐步形成了新的制造形态。随着“工业4.0”的引领,这些优势技术必将爆炸式地发展,推进汽车制造业的新一轮技术革命。
4)随着科技的发展、产品思路和技术层面的进化、移动互联技术对消费结构的影响,汽车制造商的角色正在逐渐转化为移动出行和产品服务的提供商,这必将推动整车制造工艺技术的革新。
随着汽车主机厂平台车型增加及多车型混线生产要求、人力成本攀升和生产交货期缩短的压力下,导致汽车总装厂对于先进装配技术和自动化设备的敏感性大大提高。各汽车厂都在提升总装工艺装备技术水平,采用更先进的装配设备提高产品质量,以应对满足新兴市场及提高产品市场竞争力的要求。汽车总装工艺作为汽车制造的最重要环节,在规模、质量、即时性、成本、产品先进性等方面都影响着市场竞争力。目前汽车总装工艺技术发展向着模块化、自动化、柔性化、人性化、智能数字化的趋势发展。随着市场的激烈竞争环境下,这些技术趋势正在从企业竞争的优势技术,向一种企业竞争的必备技术转变。
1 总装工艺技术
1.1模块化
汽车总装工艺采用模块化设计可以把不同级别车型的众多零部件进行通用标准化生产,同时又可以灵活的搭载其他的新技术。制造过程中,采用总装模块化可以减少总装工位线长度和主线装配工时,提高装配效率,扩展装配线的柔性化程度,缩短汽车生产周期。目前的模块化主要有电子控制系统模块化和产品结构模块化两种方向性的模块趋势。
1.1.1电子控制系统模块化
随着车联网的科技发展及信息娱乐需求下,出现以ECU(电子控制单元)集成和标准化趋势,ECU群的“标准件”功能成为各车型通用的模块,将各种功能细分的ECU整合起来,实现一个全车范围内的电子控制系统模块化。比如传动控制、车身控制、安全控制、驾驶辅助控制、动态底盘控制系统和多媒体移动互联网服务等标准系统为单位进行模块化大集成。
1.1.2产品结构模块化
通过将产品多功能结构与各种零部件相互关系的组合,把汽车各子系统产品结构与相互零部件组装集成为大总成模块。可以显著缩短产线长度及生产节拍,优化装配工艺和降低制造成本。目前总装工艺的模块化应用主要有前端块化、车门模块化、底盘模块化、顶棚集成化、油箱集成化、IP模块化、前后保模块化、车轮模块化等(如图1所示)。
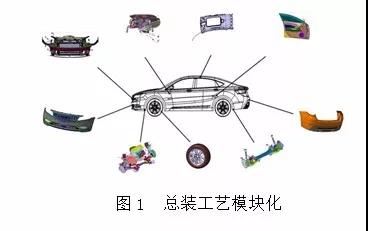
产品结构模块化中最具代表性的是底盘动力模块化,融合目前各种先进的装配工艺技术。以某汽车品牌的的MQB底盘动力模块为例,简要说明下底盘平台高度柔性化和集成化的模块化趋势。
(1)采用多种柔性托盘(如图2所示)组合形成底盘合车工装(如图3所示),包含前托盘、中托盘、后托盘。多种柔性化的扳倒式、伸缩式、限位块式定位销运用可以满足多种组合动力模块的装配支撑。非常方便底盘的自动化装配,减少下车体装配人机性差的问题。
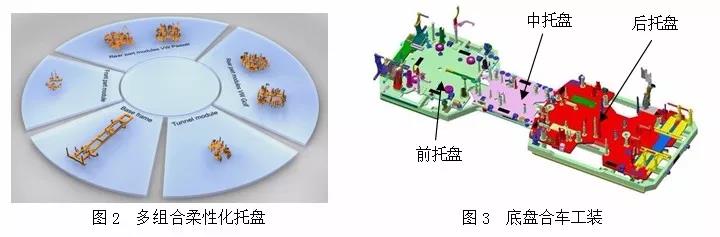
(2)底盘模块化集成程度非常高。如图4所示,除将常规的前悬模块、后悬模块外,还几乎将全部下车体附件如排气管总成、油箱总成、隔热垫、操纵机构及燃油管路集成在大托盘工装上。显著的减少底盘主线工位数和装配工时。
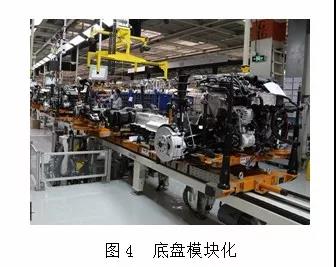
(3)底盘标准件自动拧紧技术应用。如图5所示,将紧固件及拧紧套筒集成在大托盘工装上,柔性化设置高精度电动拧紧工具,利用信息化网络系统完成标准件装配的力矩控制和质量监测。是网络化装配制造技术在汽车装配生产线上的典型工程应用。
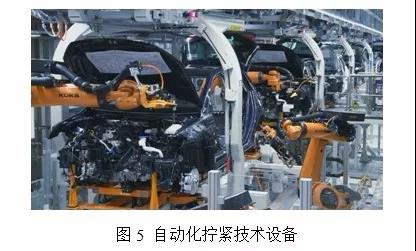
(4)底盘合车自动化。配合AGV自动导引小车,利用电磁或光学等自动导引装置,实现路径自动跟踪、转向同步行驶,并且具有障碍物识别、停车、自动调速和无线通讯等功能,实现底盘合车无人化、自动化装配(见图6)。
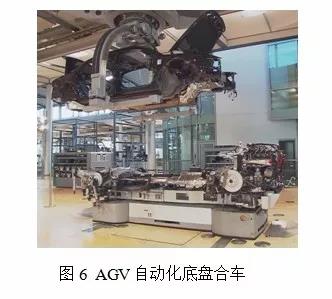
1.2 自动化
受到人力成本攀升及制造节拍的影响,并且自动化设备使用可以显著提高产品的质量和装配稳定性,汽车总装厂对于自动化的需求趋势日益明显。较为典型的采用自动化的工序内容有:
(1)前/后风挡和全景天窗的涂胶工序采用涂胶机器人设备,避免了人工打胶的断胶现象,同时胶型质量更可靠稳定(见图7),配合风挡装配机器人全自动化装配(见图8),提高车辆密封性。
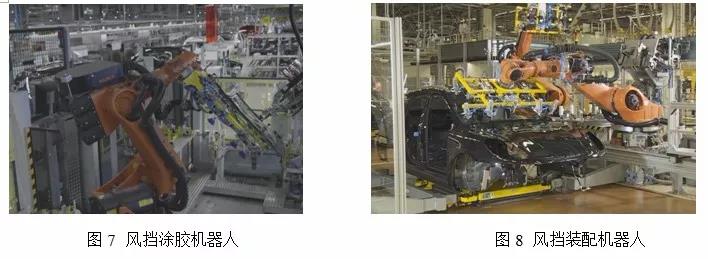
(2)车轮模块通过轮胎自动分装线完成分装,并通过自动输送线运输至装配工位。如图9所示,自动化分装系统能根据车辆配置自动识别不同规格的轮胎,自动完成轮胎装配和动平衡检测,有效的保证了轮胎分装的品质与生产的稳定性。采用机器人装配轮胎至车身及车轮螺母自动化拧紧技术(见图10),满足可变多轴拧紧及PCD变径的柔性化装配需求。提高产品质量的同时也减少人力成本。
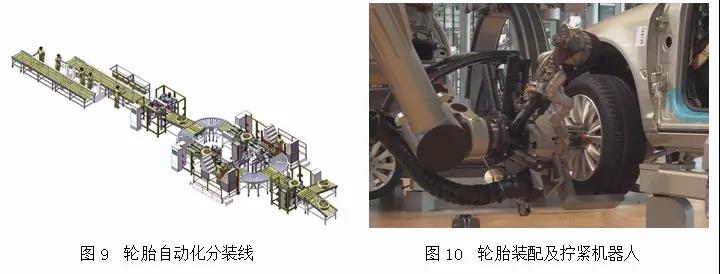
(3)各种需助力设备辅助装配的模块化工序。如IP模块采用自动化的机械手装配代替人工装配(如图11所示),可以保证高精度的定位装配,对于内饰外观质量的尺寸链控制,造型效果的感官质量有很大的提升;且自动化机械手可以集成拧紧设备紧固标准件(如图12所示),大大提高装配质量和节省人力成本。
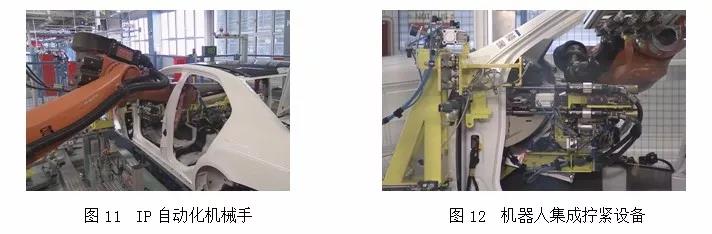
1.3 加注设备真空化及智能化
制动液、冷却液、动力转向液、空调冷媒等加注设备向着抽真空加注、自动检测、自动定量加注等功能集成设备趋势,以及出现油液二合一以上的集成加注设备的应用(如图13)。
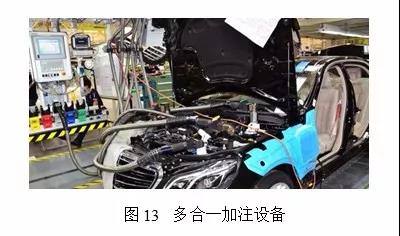
1.4力矩控制智能化
力矩拧紧设备广泛采用高精度电动拧紧设备。拧紧技术也从通常的扭矩法转向扭矩+转角法或屈服强度法应用;从控制力矩间接控制拧紧质量向着直接控制预紧力为目的,具备在线动态力矩控制与监测(见图14);工厂联网形成力矩数据化网络系统,实时监控拧紧质量、数据储存和追溯、数据信息分析处理等(见图15),进行智能统计过程控制(SPC),提高和稳定制造过程控制能力(CPK)。利用网络化通信模块与单片机控制器相结合,进行信息的交互,设计成一体式智能网络装配控制模块,完成力矩装配的控制。
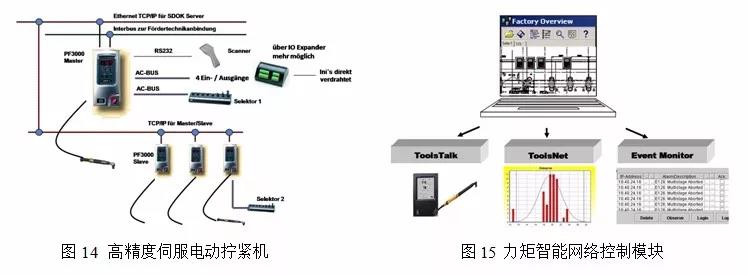
1.5 柔性化工装
总装整体工序中,部分装配工序由于装配空间狭小或零附件复杂等原因造成装配人员的非常规作业姿势,装配人机性很差。解决方法一方面通过采用自动化机器人代替人工装配外,另一方面需要在工装或作业手法上进行柔性化设计提高人机性。具体案例有:
(1)底盘线下车体附件的装配需要人员在车底下装配,出现人员下蹲及身体弯曲等不良作业动作。现在解决的方法是对车身吊具设备进行人机性设计,如图16所示使用高度可调及车身可旋转的C型钳吊具,确保人员可以站立式姿势或较佳的姿势进行正常装配。
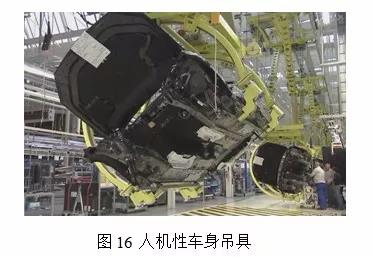
(2)内饰线如机舱内线束等工序出现人员装配位置和车身悬挂高度不吻合,出现人员下蹲或身体弯曲的姿势来完成装配作业。通过采用Z向高度柔性可调的车身托盘,可以保证在不同的工位将车身定位在合理的高度,方便人员站立式装配(如图17)。另外如车体内装配人员采用坐式机械手(见图18),使员工可以坐着完成作业,减少蹲着及躯干弯曲造成的身体机能劳损。
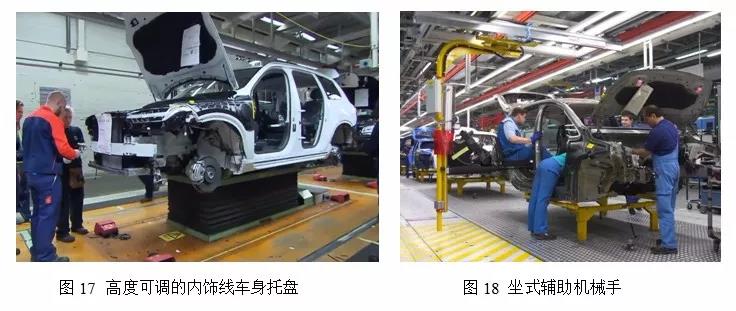
1.6 SPS物流
汽车总装厂在多车型混线生产的趋势下,线旁储料空间不足及物料种类繁多限制了产线的柔性化和物流效率。有效的解决方式是采用SPS物流形式——随行配料系统(SPS)。如图19所示,SPS是指一种单量份向生产线准时化配送的物流方式。该物流方式将拣料与装配分开,使各自作业更加专业化和模块化,有利于消除员工不必要的非增值操作,有效防止总装装配线的错、漏装问题,从而提高装配质量;同时配合随车物料投放形式可以减少线边物料摆放空间约束,且采用AGV小车运输代替人工物流(见图20),满足准时化的高要求及多车型混线物流配送要求,是一种普遍采用的物流趋势。
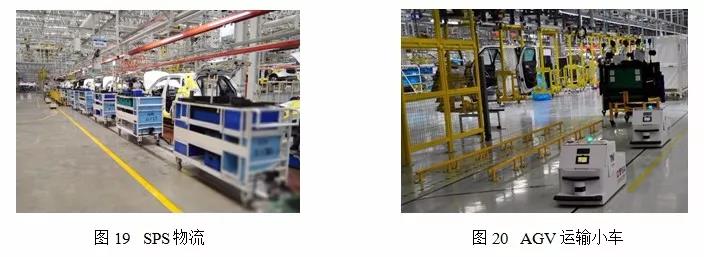
2 同步工程
汽车总装工艺技术开发过程中,同步工程技术的作用越来越明显。产品项目开发中已经减少了样车试制及验证的数量和时间,提高了虚拟仿真在产品设计过程的比重。更多在要求在产品前期虚拟仿真中发现制造问题并提前解决,减少工厂技改及产品设变费用。
2.1装配仿真分析
汽车总装的同步工程在新车产品开发之初,就开始介入对产品结构装配性、设备操作性进行虚拟仿真分析(见图21、22),提前在设计阶段发现和解决装配工艺问题。
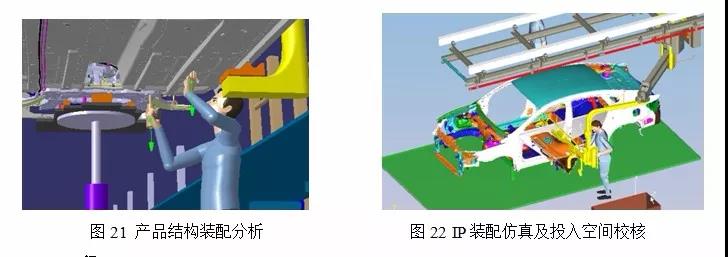
2.2 IE工程
产品数据设计至冻结前后, 利用3D仿真分析软件中的工时分析模块,综合主机厂生产线实际的相关信息,对装配工人的操作工时和作业强度进行分析,优化工序流程和作业内容,减小工位劳动强度(如图23所示)。同时进行产线工时线平衡分析,提前发现和解决工时均衡及瓶颈工位等问题(如图24所示)。

2.3数字化工厂
合理、经济科学的生产工艺流程设计对于降低汽车生产主线长度、制造能耗,提高产线柔性化有很大帮助。在工厂规划之初利用虚拟仿真技术对工艺流程(见图25)进行设定和虚拟验证,及进行数字工厂规划和仿真(见图26)。提前发现生产隐患问题和减少不必要的工厂技改费用。
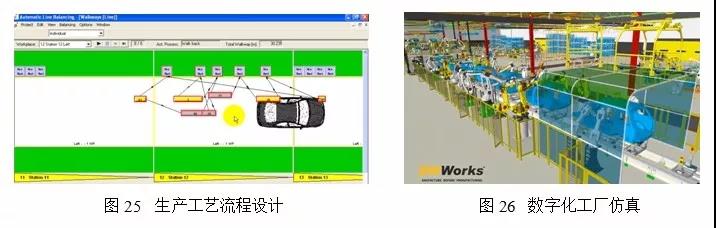
3 结语
汽车装配的新工艺和新技术,随着市场、技术及政策导向等多方面因素的推动而不断进步,缩短生产周期、提高整车质量、降低制造成本、提高市场竞争力等方面都是汽车制造商追求的共同目标,在经历平台化、整车模块化开发与设计后,现代汽车制造业出现了如下较为明显的发展趋势。
1)产品结构通用化、模块化技术简化了装配关系,逐步改变了传统汽车制造商的装配策略与工艺设计的理念,实现零部件全球采购和全球供货。该技术势必革新汽车制造业中的供应链关系和零部件配套模式。
2)模块化、柔性化等制造工艺的普及逐步形成了新的制造形态,一些高级汽车制造商完成从平台化到模块化生产方式的过渡,甚至达到了可扩展整车平台模块化生产方式高度。具备在数个模块化扩展性开发基础上,垂直形成“多种汽车平台”和“高低端多层级模块群”,同步设计出全系品牌下功能用途以及风格不同的高低端多级车型产品,实现更高效率和规模的设计和生产。
3)数字化、自动化、智能化等优势技术的应用虽然在开发前期需要较大成本投入,但随着优势技术不断转化为实际效益,新车型开发和制造的成本大幅度减少,投资回报率具有明显优势,已逐步形成了新的制造形态。随着“工业4.0”的引领,这些优势技术必将爆炸式地发展,推进汽车制造业的新一轮技术革命。
4)随着科技的发展、产品思路和技术层面的进化、移动互联技术对消费结构的影响,汽车制造商的角色正在逐渐转化为移动出行和产品服务的提供商,这必将推动整车制造工艺技术的革新。
- 下一篇:揭秘蔚来ES8全铝车身生产线
- 上一篇:车间流水线布局的7种原则与7种方式
编辑推荐
最新资讯
-
“锂”想万家——比亚迪叉车在家电行
2025-04-28 10:02
-
全球工业数字化领袖齐聚申城,共绘智
2025-04-28 08:28
-
思看科技受邀出席第三届联合国教科文
2025-04-27 13:29
-
聚势谋远,智领新程——五菱柳机以硬
2025-04-27 13:22
-
聚势求新、智驱未来——五菱工业底盘
2025-04-27 13:22