国内汽车发动机缸体铸件铸造技术发展趋势
2018-05-24 09:43:09· 来源:铸造联盟
我国汽车产业近年来发展迅速,主要汽车企业(集团)2011年年底形成整车产能1 841万辆,相应发动机产能已达到年产1 671万台。随着社会经济快速发展和人民生活水平不断提高,我国汽车国产化进程不断加快,汽车消费需求旺盛,汽车保有量保持快速增长趋势。
1国内车用发动机市场需求
我国汽车产业近年来发展迅速,主要汽车企业(集团)2011年年底形成整车产能1 841万辆,相应发动机产能已达到年产1 671万台。随着社会经济快速发展和人民生活水平不断提高,我国汽车国产化进程不断加快,汽车消费需求旺盛,汽车保有量保持快速增长趋势。2006年至2010年,汽车保有量年均增加951万辆;据分析,目前中国的汽车保有量为7 000多万辆,到2020年将达到2亿辆,也就是每年将净增1 300万辆,考虑到汽车报废等因素,每年净增量将在2 000万辆左右。巨大的汽车市场保有量,必将促进汽车发动机缸体市场的大发展,表1为2007~2020年国内汽车发动机缸体铸件生产及预测情况。
2国内发动机缸体铸件铸造工艺及生产设备
2.1熔化工艺和设备
缸体铸造所用的熔炼设备大多为冲天炉—中频感应炉双联熔炼,也有采用中频感应炉—中频感应炉双联熔炼,而使用变频感应炉作为保温炉的企业亦在不断增加。为了节能和环保,部分企业的冲天炉采用水冷热风除尘方式,用具有高发热值的铸造焦取代冶金焦,以提高铁液温度,保证铁液质量,增强熔化效率。一汽铸造公司的冲天炉熔化过程控制采用微机等集散式控制系统,冲天炉熔炼铁液的检测采用测温仪、碳当量检测仪和化学成分直读光谱仪等。 从掌握的汽车行业铸造厂资料来看,哈尔滨东安机械厂、上汽通用和安徽奇瑞等许多车间的熔化设备多数以中频炉为主。当然,熔化设备的选择主要考虑当地的能源供应状况;但从熔炼质量看,这些熔炼设备都能满足供货需求,与世界先进水平基本接近。随着工业废钢的生产量增加,国内已经采用以废钢增碳的熔化工艺来生产缸体等薄壁高强度合金铸铁件,这为提高铸件质量和稳定生产提供了可靠的保证。一汽铸造公司使用国产10 t中频熔化炉,采用废钢增碳熔化技术生产高强度灰铸铁,铸件各项指标均达到国际同类水平,抗拉强度达230-320 MPa,硬度达180-220 HB,内腔清洁度要求小于3 000 mg。
总之,国内熔化设备的水平不断提高,不论是冲天炉还是电炉,均已接近世界先进水平。关键的电器控制元件引进后,电炉产品的总体水平已满足生产要求,熔化效率都有提高,但在运行过程中仍会出现小问题,有待设备生产厂家进一步降低设备故障率。
目前,大批量流水线生产的汽车铸造行业采用大吨位中(变)频炉熔化也是一种趋势。如安徽芜湖奇瑞60万台发动机缸体铸造及原一汽大宇发动机有限公司铸铁厂(现为上海通用烟台动力)熔炼炉和保温炉全部采用美国应达8 t容量的中频炉和20 t容量的保温炉。近10年来,随着静态变频装置的发展,其效率和安全性能不断提高而投资呈逐年下降的趋势,使得铸造厂采用中频感应电炉来代替工频感应电炉熔炼铁合金和非铁合金变得越来越普遍。 目前,国内几乎停止制造工频坩埚式感应电炉。另外,采用高功率密度的中频感应电炉的熔化时间较工频炉大大缩短,常见配置见表2。
表2中(变)频电源与电炉的配置方式
2.2造型工艺和设备
缸体是发动机上最关键、最复杂的铸件,其壁厚最薄处往往不到3 mm,缸体铸件生产应用最广的仍然是湿型粘土砂,具有成型性能好、能耗低、噪音小、污染少、效率高、运行可靠等优点的静压造型线及气冲造型线使用较为广泛。近年来,国内外造型线制造厂家对造型机的不断改进,先后已出现气冲加压实、气流增益气冲加压实、静压加压实、主动多触头压实、成型挤压等加砂方式,砂型硬度更加均匀化,成为缸体铸件生产首选的造型设备。另外,对于发动机缸体铸件年产量万台左右的厂家,如潍柴四川柴油机厂和康明斯四川五粮液等大中型柴油机缸体铸造企业,均采用pepset自硬砂工艺和三乙胺冷芯盒工艺,这也是节能低碳的最佳选择。
国内清华大学、济南铸锻所等早已研制静压造型线,苏州铸造机械厂和保定维尔的静压造型线以及无锡华佩线已有数条投入使用,但他们在整线性能和铸型质量一致性方面还显得不足。因此,国内汽车铸件生产所用造型线多以进口为主,济南铸造锻压机械研究所捷迈铸造工程公司为扬动股份有限公司提供了一条砂箱尺寸为1 000 mm×750 mm×320 mm的静压造型线,该线主机选用德国HWS公司的静压造型机,辅机由国内提供,是国内单主机布线生产率最高的造型线,代表了当今世界的最高造型技术水平。
气冲造型问世几十年,其技术发展也在不断提高和进步,与其它现代化湿型砂造型方法一样,都是追求提高砂型紧实的均匀性,从而保证砂型表面光洁,尺寸精确,内部致密。为保证这一点,国外近几年又有了新发展。
2.3制芯工艺和设备
目前,国内汽车铸造厂缸体生产所用砂芯如水套砂芯、曲轴箱砂芯、缸筒与顶端砂芯、前后端面砂芯等依各厂条件不同,分别采用冷芯盒制芯、热芯盒制芯或覆膜壳芯制芯。冷芯盒工艺因其芯砂流动性、溃散性、生产率、节能和砂芯精度优于其它制芯工艺,在国内汽车发动机缸体铸造行业得到广泛应用。从今后趋势看,其应用范围将不断扩大。
另外,采用锁芯工艺,利用砂芯上开设的工艺孔,二次填砂固化,使多个砂芯组合为一个整体组合砂芯,然后整体涂料、烘干,这样铸件尺寸精度可大大提高,总体尺寸误差不超过0.3 mm。多数厂家采用计算机控制的“制芯中心”使全部制芯过程实现自动化。
制芯等设备主要有德国兰佩冷芯制芯机、西班牙洛拉门迪制芯中心、日本浪速等,国产热芯设备有单工位、两工位、四工位等,壳芯设备有K763/874壳芯机等,可满足复杂、薄壁、高精度铸件对砂芯质量的要求。
2.4砂处理工艺和设备
2.4.1粘土湿型砂处理
砂处理工艺对铸件产量和质量至关重要。在大批量流水线生产条件下,型砂周期循环使用,国内汽车行业都非常重视反复使用过程中型砂性能的变化规律,力求选择好的砂处理工艺流程,并采用逐级多点检测和自动控制。随着高压、气冲及静压造型工艺对型砂要求严格性的不断提高,相当多厂家进口了大容量高速混砂设备,如一汽二铸厂采用2套200t/h砂处理单元,分别都配有美国国家工程公司辛普森22G高效混砂机和连续双盘冷却器,整个系统配有各种检测仪器,通过中央控制室模拟控制;哈尔滨东安发动机公司和天津内燃机厂等引进日本新东公司SSD型砂处理系统,回砂采用测温加水(MIA)和测湿加水(MIC)装置以及型砂成型性控制仪,配以先进的检测系统,通过自动化监控向静压造型线提供合格的型砂;上海通用、烟台动力、安徽奇瑞等公司采用塔式结构的砂处理单元,使用国外公司的高效混砂机,旧砂冷却系统以及计算机控制系统,并将旧砂破碎、磁选、筛分、增湿冷却、辅料定量、混砂等工艺布置在24 m×24 m×25 m左右的空间内,这也是目前国外较先进的布置形式。
常州法迪尔克公司开发的MXC 30~120 t/h系列变频式冷却混砂机实现了混砂机创新性的突破,在沈阳华晨、常柴股份等20余家发动机铸造厂得到推广。其砂处理系统布置简单,减少了设备、厂房的基础投入;采用调速变频,降低能耗,型砂混制更均匀;充分发挥膨润土的效率,降低加入量,有效控制型砂温度。表4为部分铸造公司选用的砂处理设备参数。
2.4.2粘土湿型砂旧砂(混合型旧砂)热法再生处理线
国内一些汽车发动机铸造厂由于使用砂芯数量较多,落砂时有大量溃散砂芯(这些砂芯几乎都是树脂砂芯)流入到旧砂中,使旧砂量远远超过砂系统的容纳量,迫使必须抛弃大量的旧砂以保持砂处理系统平衡,在所抛弃的旧砂中,不仅有芯头、清理的废砂以及除尘细粉,还有许多落砂时不易破碎的型砂块,形成混合型旧砂。如果把这种混合型旧砂作为废砂(废弃物)抛弃,不仅造成了资源浪费,而且废弃旧砂堆放既占场地,又污染环境,还需大量的运输费用。为减少这类混合型旧砂的产生,有的发动机缸体铸造厂采用热法再生:如哈尔滨东安汽车发动机公司引进意大利的热法再生设备已在生产中应用;一汽铸造公司引进日本热法再生和机械再生结合技术,处理芯砂和型、芯砂混合砂已在生产中得到应用。粘土湿型旧砂再生技术的应用近年来有了突破,实践证明湿型粘土旧砂经热法再生后的LOI值、热膨胀率、发气量、角形系数及灰分含量等指标都优于新砂。但就目前国内铸造行业现状而言,粘土湿型砂热法再生技术的推广仍不如预期的那么广泛,仅有宜宾五粮液康明斯发动机缸体铸造厂以及东风、一拖等大型铸造厂、长三角地区的吴江、昆山等地建有热法焙烧炉用于旧砂再生。 最近国外流行一种集铸造与热处理于一体,即落砂、再生和热处理三合一的工艺,国内已陆续有一些采用自硬砂工艺生产铝缸体的铸造厂在落砂清理工序中推广这种工艺。在焙烧炉中,砂型和砂芯的树脂粘结剂所含有的许多能量在与炉中高温及富氧气氛接触燃烧后会被释放,而伴随着粘结剂的燃烧,砂型和砂芯中的型砂就会散落下来。炉顶安装的轴流风扇产生的高速气流向下吹向缸体铸件,将散落的型砂带向炉底。高速气流流过不规则形状的缸体铸件会产生压差,这种压差引起铸件内部和外部的气流扰动,从而将松动的型砂带走。与此同时,高速风扇也使炉内气流分布达到最佳状态,从而使炉内温差保持在很小的范围内。铸件从清洁铸造三合一系统出来后,在完成了固溶热处理的同时,型砂和芯砂都已去除干净。型(芯)砂在漏斗形炉底上被收集在一起。炉底装有流态床,用于对型(芯)砂进行最后清理。粘结剂残留的微粒被分离并被排放。型(芯)砂在炉内被完全再生,经过气力输送到造型、制芯工部。炉内废气集中排放,通过旋风分离器、灼烧器、换热器,最后经过袋式过滤除尘器,清洁后的气体才被排放到大气。
总之,新建铸造工厂必须考虑旧砂再生处理;对已建成投产的铸造工厂,可增加旧砂再生,或将旧砂集中到就近专业处理工厂再生后使用。这已经是一种发展趋势,是国家节能减排、可持续发展的需要。
2.5清理工艺和设备
目前,缸体铸件经去除浇冒口后,在清理线上打磨外表面,然后进入鼠笼式抛丸室清理,已是一种常规工艺。生产多品种缸体时,部分厂家采用夹持式高效抛丸清理机进行抛丸。普遍采用各种自动化和机械化专用清理线和高效缸体鼠笼抛丸机以及机械手对缸体进行整体清理,然后用手工对缸体逐个精整及吹净水套内腔残留物。经尺寸检查,气密性试验,铣加工定位点及终检后,进行涂漆或其它防锈处理,成为合格缸体铸件。
以钢丸代替铁丸进行抛丸清理,采用机器人分拣缸体铸件,采用浇冒口去除机去除浇冒口以及采用X射线和超声波探伤仪检验内部缺陷等方法已为越来越多的厂家采用。
天津丰田等铸造厂都对金属炉料进行抛丸、破碎、净化和称量,以提高熔化效率和铁液质量。表5为国内现有抛丸清理设备的主要技术参数。
2.6检测技术和装备
国内大批量生产发动机铸件的厂家都拥有先进的检测仪器和严格的质量保证体系。一般都采用先进的直读光谱仪和红外碳硫仪进行成分检测与控制,利用先进的电子金相显微镜进行精确的金相组织分析,先进的电子拉力试验机可以进行各种金属材料的拉伸、压缩、弯曲等试验,采用三坐标测量机对缸体铸件、模具、芯盒进行自动精确测量,检测水平一直在国内同行业中领先。表6为某铸造厂铸件检测设备及其主要技术参数。
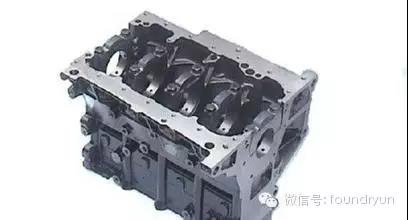
2.7压铸工艺和设备
2.7.1铝合金压铸件
随着人们对环保、轻量化的要求日益提高,汽车发动机缸体逐渐转向采用压铸生产。
目前,发展迅速的有广州东风本田发动机公司、重庆长安汽车集团、长安铃木汽车公司、上海乾通汽车附件公司(3 550 t/年)、乔治费歇尔(苏州)有限公司以及哈尔滨东安动力公司等;此外,长春一汽集团(2 700 t/年)、重庆渝江压铸集团、宜兴江旭铸造公司(3 200 t/年)、广东鸿图科技公司(3 000 t/年)、宁波合力模具科技公司、徐航压铸有限公司、重庆渝美合资公司、重庆蓝黛实业公司以及高要鸿泰精密压铸有限公司等均引进大型压铸机自动生产线生产发动机缸体等铝合金压铸件。由传统铸造方法转向压铸法生产铝合金汽车缸体已经成为一个发展趋势,仅2008一个年度,国内不同厂家从布勒公司引入了7条2 700 t级别的铝合金发动机缸体生产线。由此可见,我国汽车缸体压铸生产规模在逐步扩大,生产水平也在不断提高,预计在今后铝合金发动机缸体的比例将达到60%~75%。
铝合金缸体压铸工艺如下:熔化采用快速集中熔炼炉,熔化能力一般为1 500~2 000 kg/h,以洁净能源天然气作燃料,控温精度±5℃,炉衬寿命长。大型压铸机选用铝合金定量保温炉,可以在压铸过程中缩短定量循环时间,降低能耗、减少废品率,从而降低成本。压铸机采用压铸岛单元式布置,每台压铸机需要完成铝液精炼、浇注、压铸、取件、冷却、切边、铣浇口、初打磨、检验(在线检测)和装筐等工序,然后进行时效、抛丸、精打磨等后续工序,最后入库。
大型压铸机单元采用取件机械手和喷涂机械手。全自动压铸机采用计算机管理系统实现整个压铸过程检测、存储、计算和记录;强化和提高质量控制手段和检测水平,采用专用真空直读光谱仪对铝合金成分进行快速分析,采用进口仪器对铝液的含氢量、非金属夹杂物、熔渣和铝密度进行检测。
随着压铸工业中一些高新技术的不断出现,如两模板压铸机的应用;采用铝合金390的整套压铸技术压铸出全铝气缸体,摒弃了原来铝合金压铸气缸体中缸筒内铸入铸铁套的方法。近年来,铝合金压铸的柴油发动机壳体已经问世,这是压铸件进入柴油发动机领域的前奏。 另外,压铸充型过程理论水平将逐步提高,生产技术也将不断改进;压铸工艺参数的检测技术将不断普及和提高;压铸生产过程中自动化程度逐步完善,并日益普及;电子计算机技术的应用更加广泛和深入;大型压铸件的工艺技术逐步成熟。此外,已研究出各种消除气孔缺陷的工艺方法,如真空压铸、ACRAD压铸(精速密Accurate Rapid Dense)、充氧压铸、匀加速的慢压射技术、局部加压技术等;更有挤压铸造和半固态成型(含流变成型与触变成型)等技术。所有这些,无疑给压铸法注入了新的活力,进而使生产具有高强度、高致密度、可热处理、可焊接等特性的压铸零件成为可能。
2.7.2镁合金压铸件
发动机缸体采用镁合金压铸件以实现汽车轻量化也呈不断扩大势态,2010年全国汽车达到1 806万辆时镁合金使用量为6.13万t(仅限于汽车变速箱壳体、制动壳体和方向盘等),这标志着中国镁合金压铸工艺技术正在向国际水平推进。
目前,镁合金的应用已引起我国科研部门的高度重视,早在国家“十五”科技攻关计划中,镁合金项目已被列为重大专项。国内部分企业,如吉利在2007年已经实现了汽车减重10%~14%的初期目标。其轻量化目标是在发动机上全面实施铝镁合金化。
乔治费歇尔(苏州)在供应奇瑞和长城等铝合金发动机缸体基础上,正在考虑镁合金发动机缸体压铸项目投产。
汽车镁合金压铸件“入门”要求很高,必须取得一系列的质量体系认证以及生产环境认证,通常包括:ISO9002、QS9000、TS16949等质量体系认证。大型镁合金压铸件生产具有一定的技术难度,这也是需要投入大量人力财力的。由于以上多种因素,向镁合金压铸领域投资应持积极审慎态度,并采取正确的投资策略。
2.8发动机缸体凝固模拟软件的应用
目前,国内部分汽车铸造厂家采用凝固模拟软件对发动机缸体铸造过程进行仿真模拟,使整个铸造过程清晰明了地表现出来,以提高铸件的质量及降低成本。
例如,亚新科国际铸造(山西)有限公司的缸体、缸盖铸件在现实生产中经常出现在缩松、渗漏缺陷,如TC6112缸体的渗漏比率高达30%~50%,造成巨大损失。通过使用国内外最先进的模拟凝固软件对产品的浇注状况进行分析;通过UG建立各种设计方案的三维模型,再利用Patran建立它们的有限元模型,然后对各种方案充型过程和凝固过程进行数值模拟。主要模拟了发动机缸体充型过程的速度场与温度场、凝固过程的温度场,以及对可能产生缩孔、缩松等缺陷的区域进行预测。完成模拟后,对各种浇注系统设计方案的充型、凝固过程及缩孔、缩松等缺陷的预测进行了对比分析,从模拟结果中得出最佳的工艺方案。
目前ProCAST、Anycasting、HYCAST,华铸CAE铸造模拟凝固软件、
等相继开发,模拟软件在发动机缸体铸造方面的开发应用呈不断扩大趋势。
2.9快速成形制造技术的应用
快速成形制造技术又称为快速原型制造技术,它包括立体光刻技术、分层实体制造技术、选择性激光烧结技术、熔融沉积技术、三维印刷技术、热塑性材料选择性喷洒和无模型树脂砂型快速制造工艺等成型方法,集成了CAD技术、数控技术、激光技术和材料技术等现代科技成果,是先进制造技术的重要组成部分。
与传统制造方法不同,快速成型从零件的CAD几何模型出发,通过软件分层离散和数控成型系统,用激光束或其它方法将材料堆积而形成实体零件,所以又称为材料添加制造法。由于它把复杂的三维制造转化为一系列二维制造的叠加,因而可以在不用模具和工具的条件下几乎能够生成任意复杂形状的零部件,极大地提高了生产效率。与数控加工、铸造、金属冷喷涂、硅胶模等制造手段一起,快速自动成型已成为现代模型、模具和零件制造的强有力手段,是目前适合我国国情的实现金属零件的单件或小批量敏捷制造的有效方法,尤其在汽车发动机缸体铸件等领域已得到了应用。
例如,选区激光烧结与铸造技术结合,可有效地应用于发动机设计开发阶段中样机的快速制造,保证产品开发速度,提高产品的开发质量,大大降低开发成本,推动产品早日进入市场。国内已经开发出V8发动机的缸体熔模,利用选区激光烧结成型技术直接制作蜡模,无需开模具,因而大大节省了制造周期和费用,其成型时间为42 h,铸造周期20天。如果按传统制作方法开模具制造,至少需要6个月的时间,费用上百万。此项技术为客户节省大量的时间和开发成本。
汽车发动机缸体的铸造生产中,模板、芯盒、压铸模的制造往往采用机加工的方法完成,此过程不仅周期长、耗资大,而且从模具设计到加工制造是一个多环节的复杂过程,其模具的制造过程极其复杂,开发周期长,研发成本大。不能适用于当前迅速响应市场的需求,而快速成型技术恰好满足了汽车发动机快速制造的要求。采用该技术与传统铸造相结合的方法能够非常迅速地实现从设计到产品的过程,减少中间环节,加快产品投放市场的速度,节省开发成本。
我国汽车产业近年来发展迅速,主要汽车企业(集团)2011年年底形成整车产能1 841万辆,相应发动机产能已达到年产1 671万台。随着社会经济快速发展和人民生活水平不断提高,我国汽车国产化进程不断加快,汽车消费需求旺盛,汽车保有量保持快速增长趋势。2006年至2010年,汽车保有量年均增加951万辆;据分析,目前中国的汽车保有量为7 000多万辆,到2020年将达到2亿辆,也就是每年将净增1 300万辆,考虑到汽车报废等因素,每年净增量将在2 000万辆左右。巨大的汽车市场保有量,必将促进汽车发动机缸体市场的大发展,表1为2007~2020年国内汽车发动机缸体铸件生产及预测情况。
2国内发动机缸体铸件铸造工艺及生产设备
2.1熔化工艺和设备
缸体铸造所用的熔炼设备大多为冲天炉—中频感应炉双联熔炼,也有采用中频感应炉—中频感应炉双联熔炼,而使用变频感应炉作为保温炉的企业亦在不断增加。为了节能和环保,部分企业的冲天炉采用水冷热风除尘方式,用具有高发热值的铸造焦取代冶金焦,以提高铁液温度,保证铁液质量,增强熔化效率。一汽铸造公司的冲天炉熔化过程控制采用微机等集散式控制系统,冲天炉熔炼铁液的检测采用测温仪、碳当量检测仪和化学成分直读光谱仪等。 从掌握的汽车行业铸造厂资料来看,哈尔滨东安机械厂、上汽通用和安徽奇瑞等许多车间的熔化设备多数以中频炉为主。当然,熔化设备的选择主要考虑当地的能源供应状况;但从熔炼质量看,这些熔炼设备都能满足供货需求,与世界先进水平基本接近。随着工业废钢的生产量增加,国内已经采用以废钢增碳的熔化工艺来生产缸体等薄壁高强度合金铸铁件,这为提高铸件质量和稳定生产提供了可靠的保证。一汽铸造公司使用国产10 t中频熔化炉,采用废钢增碳熔化技术生产高强度灰铸铁,铸件各项指标均达到国际同类水平,抗拉强度达230-320 MPa,硬度达180-220 HB,内腔清洁度要求小于3 000 mg。
总之,国内熔化设备的水平不断提高,不论是冲天炉还是电炉,均已接近世界先进水平。关键的电器控制元件引进后,电炉产品的总体水平已满足生产要求,熔化效率都有提高,但在运行过程中仍会出现小问题,有待设备生产厂家进一步降低设备故障率。
目前,大批量流水线生产的汽车铸造行业采用大吨位中(变)频炉熔化也是一种趋势。如安徽芜湖奇瑞60万台发动机缸体铸造及原一汽大宇发动机有限公司铸铁厂(现为上海通用烟台动力)熔炼炉和保温炉全部采用美国应达8 t容量的中频炉和20 t容量的保温炉。近10年来,随着静态变频装置的发展,其效率和安全性能不断提高而投资呈逐年下降的趋势,使得铸造厂采用中频感应电炉来代替工频感应电炉熔炼铁合金和非铁合金变得越来越普遍。 目前,国内几乎停止制造工频坩埚式感应电炉。另外,采用高功率密度的中频感应电炉的熔化时间较工频炉大大缩短,常见配置见表2。
表2中(变)频电源与电炉的配置方式
2.2造型工艺和设备
缸体是发动机上最关键、最复杂的铸件,其壁厚最薄处往往不到3 mm,缸体铸件生产应用最广的仍然是湿型粘土砂,具有成型性能好、能耗低、噪音小、污染少、效率高、运行可靠等优点的静压造型线及气冲造型线使用较为广泛。近年来,国内外造型线制造厂家对造型机的不断改进,先后已出现气冲加压实、气流增益气冲加压实、静压加压实、主动多触头压实、成型挤压等加砂方式,砂型硬度更加均匀化,成为缸体铸件生产首选的造型设备。另外,对于发动机缸体铸件年产量万台左右的厂家,如潍柴四川柴油机厂和康明斯四川五粮液等大中型柴油机缸体铸造企业,均采用pepset自硬砂工艺和三乙胺冷芯盒工艺,这也是节能低碳的最佳选择。
国内清华大学、济南铸锻所等早已研制静压造型线,苏州铸造机械厂和保定维尔的静压造型线以及无锡华佩线已有数条投入使用,但他们在整线性能和铸型质量一致性方面还显得不足。因此,国内汽车铸件生产所用造型线多以进口为主,济南铸造锻压机械研究所捷迈铸造工程公司为扬动股份有限公司提供了一条砂箱尺寸为1 000 mm×750 mm×320 mm的静压造型线,该线主机选用德国HWS公司的静压造型机,辅机由国内提供,是国内单主机布线生产率最高的造型线,代表了当今世界的最高造型技术水平。
气冲造型问世几十年,其技术发展也在不断提高和进步,与其它现代化湿型砂造型方法一样,都是追求提高砂型紧实的均匀性,从而保证砂型表面光洁,尺寸精确,内部致密。为保证这一点,国外近几年又有了新发展。
2.3制芯工艺和设备
目前,国内汽车铸造厂缸体生产所用砂芯如水套砂芯、曲轴箱砂芯、缸筒与顶端砂芯、前后端面砂芯等依各厂条件不同,分别采用冷芯盒制芯、热芯盒制芯或覆膜壳芯制芯。冷芯盒工艺因其芯砂流动性、溃散性、生产率、节能和砂芯精度优于其它制芯工艺,在国内汽车发动机缸体铸造行业得到广泛应用。从今后趋势看,其应用范围将不断扩大。
另外,采用锁芯工艺,利用砂芯上开设的工艺孔,二次填砂固化,使多个砂芯组合为一个整体组合砂芯,然后整体涂料、烘干,这样铸件尺寸精度可大大提高,总体尺寸误差不超过0.3 mm。多数厂家采用计算机控制的“制芯中心”使全部制芯过程实现自动化。
制芯等设备主要有德国兰佩冷芯制芯机、西班牙洛拉门迪制芯中心、日本浪速等,国产热芯设备有单工位、两工位、四工位等,壳芯设备有K763/874壳芯机等,可满足复杂、薄壁、高精度铸件对砂芯质量的要求。
2.4砂处理工艺和设备
2.4.1粘土湿型砂处理
砂处理工艺对铸件产量和质量至关重要。在大批量流水线生产条件下,型砂周期循环使用,国内汽车行业都非常重视反复使用过程中型砂性能的变化规律,力求选择好的砂处理工艺流程,并采用逐级多点检测和自动控制。随着高压、气冲及静压造型工艺对型砂要求严格性的不断提高,相当多厂家进口了大容量高速混砂设备,如一汽二铸厂采用2套200t/h砂处理单元,分别都配有美国国家工程公司辛普森22G高效混砂机和连续双盘冷却器,整个系统配有各种检测仪器,通过中央控制室模拟控制;哈尔滨东安发动机公司和天津内燃机厂等引进日本新东公司SSD型砂处理系统,回砂采用测温加水(MIA)和测湿加水(MIC)装置以及型砂成型性控制仪,配以先进的检测系统,通过自动化监控向静压造型线提供合格的型砂;上海通用、烟台动力、安徽奇瑞等公司采用塔式结构的砂处理单元,使用国外公司的高效混砂机,旧砂冷却系统以及计算机控制系统,并将旧砂破碎、磁选、筛分、增湿冷却、辅料定量、混砂等工艺布置在24 m×24 m×25 m左右的空间内,这也是目前国外较先进的布置形式。
常州法迪尔克公司开发的MXC 30~120 t/h系列变频式冷却混砂机实现了混砂机创新性的突破,在沈阳华晨、常柴股份等20余家发动机铸造厂得到推广。其砂处理系统布置简单,减少了设备、厂房的基础投入;采用调速变频,降低能耗,型砂混制更均匀;充分发挥膨润土的效率,降低加入量,有效控制型砂温度。表4为部分铸造公司选用的砂处理设备参数。
2.4.2粘土湿型砂旧砂(混合型旧砂)热法再生处理线
国内一些汽车发动机铸造厂由于使用砂芯数量较多,落砂时有大量溃散砂芯(这些砂芯几乎都是树脂砂芯)流入到旧砂中,使旧砂量远远超过砂系统的容纳量,迫使必须抛弃大量的旧砂以保持砂处理系统平衡,在所抛弃的旧砂中,不仅有芯头、清理的废砂以及除尘细粉,还有许多落砂时不易破碎的型砂块,形成混合型旧砂。如果把这种混合型旧砂作为废砂(废弃物)抛弃,不仅造成了资源浪费,而且废弃旧砂堆放既占场地,又污染环境,还需大量的运输费用。为减少这类混合型旧砂的产生,有的发动机缸体铸造厂采用热法再生:如哈尔滨东安汽车发动机公司引进意大利的热法再生设备已在生产中应用;一汽铸造公司引进日本热法再生和机械再生结合技术,处理芯砂和型、芯砂混合砂已在生产中得到应用。粘土湿型旧砂再生技术的应用近年来有了突破,实践证明湿型粘土旧砂经热法再生后的LOI值、热膨胀率、发气量、角形系数及灰分含量等指标都优于新砂。但就目前国内铸造行业现状而言,粘土湿型砂热法再生技术的推广仍不如预期的那么广泛,仅有宜宾五粮液康明斯发动机缸体铸造厂以及东风、一拖等大型铸造厂、长三角地区的吴江、昆山等地建有热法焙烧炉用于旧砂再生。 最近国外流行一种集铸造与热处理于一体,即落砂、再生和热处理三合一的工艺,国内已陆续有一些采用自硬砂工艺生产铝缸体的铸造厂在落砂清理工序中推广这种工艺。在焙烧炉中,砂型和砂芯的树脂粘结剂所含有的许多能量在与炉中高温及富氧气氛接触燃烧后会被释放,而伴随着粘结剂的燃烧,砂型和砂芯中的型砂就会散落下来。炉顶安装的轴流风扇产生的高速气流向下吹向缸体铸件,将散落的型砂带向炉底。高速气流流过不规则形状的缸体铸件会产生压差,这种压差引起铸件内部和外部的气流扰动,从而将松动的型砂带走。与此同时,高速风扇也使炉内气流分布达到最佳状态,从而使炉内温差保持在很小的范围内。铸件从清洁铸造三合一系统出来后,在完成了固溶热处理的同时,型砂和芯砂都已去除干净。型(芯)砂在漏斗形炉底上被收集在一起。炉底装有流态床,用于对型(芯)砂进行最后清理。粘结剂残留的微粒被分离并被排放。型(芯)砂在炉内被完全再生,经过气力输送到造型、制芯工部。炉内废气集中排放,通过旋风分离器、灼烧器、换热器,最后经过袋式过滤除尘器,清洁后的气体才被排放到大气。
总之,新建铸造工厂必须考虑旧砂再生处理;对已建成投产的铸造工厂,可增加旧砂再生,或将旧砂集中到就近专业处理工厂再生后使用。这已经是一种发展趋势,是国家节能减排、可持续发展的需要。
2.5清理工艺和设备
目前,缸体铸件经去除浇冒口后,在清理线上打磨外表面,然后进入鼠笼式抛丸室清理,已是一种常规工艺。生产多品种缸体时,部分厂家采用夹持式高效抛丸清理机进行抛丸。普遍采用各种自动化和机械化专用清理线和高效缸体鼠笼抛丸机以及机械手对缸体进行整体清理,然后用手工对缸体逐个精整及吹净水套内腔残留物。经尺寸检查,气密性试验,铣加工定位点及终检后,进行涂漆或其它防锈处理,成为合格缸体铸件。
以钢丸代替铁丸进行抛丸清理,采用机器人分拣缸体铸件,采用浇冒口去除机去除浇冒口以及采用X射线和超声波探伤仪检验内部缺陷等方法已为越来越多的厂家采用。
天津丰田等铸造厂都对金属炉料进行抛丸、破碎、净化和称量,以提高熔化效率和铁液质量。表5为国内现有抛丸清理设备的主要技术参数。
2.6检测技术和装备
国内大批量生产发动机铸件的厂家都拥有先进的检测仪器和严格的质量保证体系。一般都采用先进的直读光谱仪和红外碳硫仪进行成分检测与控制,利用先进的电子金相显微镜进行精确的金相组织分析,先进的电子拉力试验机可以进行各种金属材料的拉伸、压缩、弯曲等试验,采用三坐标测量机对缸体铸件、模具、芯盒进行自动精确测量,检测水平一直在国内同行业中领先。表6为某铸造厂铸件检测设备及其主要技术参数。
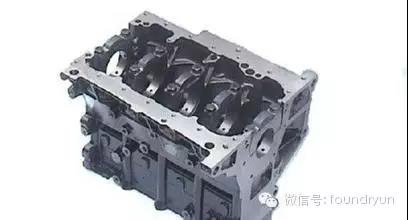
2.7压铸工艺和设备
2.7.1铝合金压铸件
随着人们对环保、轻量化的要求日益提高,汽车发动机缸体逐渐转向采用压铸生产。
目前,发展迅速的有广州东风本田发动机公司、重庆长安汽车集团、长安铃木汽车公司、上海乾通汽车附件公司(3 550 t/年)、乔治费歇尔(苏州)有限公司以及哈尔滨东安动力公司等;此外,长春一汽集团(2 700 t/年)、重庆渝江压铸集团、宜兴江旭铸造公司(3 200 t/年)、广东鸿图科技公司(3 000 t/年)、宁波合力模具科技公司、徐航压铸有限公司、重庆渝美合资公司、重庆蓝黛实业公司以及高要鸿泰精密压铸有限公司等均引进大型压铸机自动生产线生产发动机缸体等铝合金压铸件。由传统铸造方法转向压铸法生产铝合金汽车缸体已经成为一个发展趋势,仅2008一个年度,国内不同厂家从布勒公司引入了7条2 700 t级别的铝合金发动机缸体生产线。由此可见,我国汽车缸体压铸生产规模在逐步扩大,生产水平也在不断提高,预计在今后铝合金发动机缸体的比例将达到60%~75%。
铝合金缸体压铸工艺如下:熔化采用快速集中熔炼炉,熔化能力一般为1 500~2 000 kg/h,以洁净能源天然气作燃料,控温精度±5℃,炉衬寿命长。大型压铸机选用铝合金定量保温炉,可以在压铸过程中缩短定量循环时间,降低能耗、减少废品率,从而降低成本。压铸机采用压铸岛单元式布置,每台压铸机需要完成铝液精炼、浇注、压铸、取件、冷却、切边、铣浇口、初打磨、检验(在线检测)和装筐等工序,然后进行时效、抛丸、精打磨等后续工序,最后入库。
大型压铸机单元采用取件机械手和喷涂机械手。全自动压铸机采用计算机管理系统实现整个压铸过程检测、存储、计算和记录;强化和提高质量控制手段和检测水平,采用专用真空直读光谱仪对铝合金成分进行快速分析,采用进口仪器对铝液的含氢量、非金属夹杂物、熔渣和铝密度进行检测。
随着压铸工业中一些高新技术的不断出现,如两模板压铸机的应用;采用铝合金390的整套压铸技术压铸出全铝气缸体,摒弃了原来铝合金压铸气缸体中缸筒内铸入铸铁套的方法。近年来,铝合金压铸的柴油发动机壳体已经问世,这是压铸件进入柴油发动机领域的前奏。 另外,压铸充型过程理论水平将逐步提高,生产技术也将不断改进;压铸工艺参数的检测技术将不断普及和提高;压铸生产过程中自动化程度逐步完善,并日益普及;电子计算机技术的应用更加广泛和深入;大型压铸件的工艺技术逐步成熟。此外,已研究出各种消除气孔缺陷的工艺方法,如真空压铸、ACRAD压铸(精速密Accurate Rapid Dense)、充氧压铸、匀加速的慢压射技术、局部加压技术等;更有挤压铸造和半固态成型(含流变成型与触变成型)等技术。所有这些,无疑给压铸法注入了新的活力,进而使生产具有高强度、高致密度、可热处理、可焊接等特性的压铸零件成为可能。
2.7.2镁合金压铸件
发动机缸体采用镁合金压铸件以实现汽车轻量化也呈不断扩大势态,2010年全国汽车达到1 806万辆时镁合金使用量为6.13万t(仅限于汽车变速箱壳体、制动壳体和方向盘等),这标志着中国镁合金压铸工艺技术正在向国际水平推进。
目前,镁合金的应用已引起我国科研部门的高度重视,早在国家“十五”科技攻关计划中,镁合金项目已被列为重大专项。国内部分企业,如吉利在2007年已经实现了汽车减重10%~14%的初期目标。其轻量化目标是在发动机上全面实施铝镁合金化。
乔治费歇尔(苏州)在供应奇瑞和长城等铝合金发动机缸体基础上,正在考虑镁合金发动机缸体压铸项目投产。
汽车镁合金压铸件“入门”要求很高,必须取得一系列的质量体系认证以及生产环境认证,通常包括:ISO9002、QS9000、TS16949等质量体系认证。大型镁合金压铸件生产具有一定的技术难度,这也是需要投入大量人力财力的。由于以上多种因素,向镁合金压铸领域投资应持积极审慎态度,并采取正确的投资策略。
2.8发动机缸体凝固模拟软件的应用
目前,国内部分汽车铸造厂家采用凝固模拟软件对发动机缸体铸造过程进行仿真模拟,使整个铸造过程清晰明了地表现出来,以提高铸件的质量及降低成本。
例如,亚新科国际铸造(山西)有限公司的缸体、缸盖铸件在现实生产中经常出现在缩松、渗漏缺陷,如TC6112缸体的渗漏比率高达30%~50%,造成巨大损失。通过使用国内外最先进的模拟凝固软件对产品的浇注状况进行分析;通过UG建立各种设计方案的三维模型,再利用Patran建立它们的有限元模型,然后对各种方案充型过程和凝固过程进行数值模拟。主要模拟了发动机缸体充型过程的速度场与温度场、凝固过程的温度场,以及对可能产生缩孔、缩松等缺陷的区域进行预测。完成模拟后,对各种浇注系统设计方案的充型、凝固过程及缩孔、缩松等缺陷的预测进行了对比分析,从模拟结果中得出最佳的工艺方案。
目前ProCAST、Anycasting、HYCAST,华铸CAE铸造模拟凝固软件、
等相继开发,模拟软件在发动机缸体铸造方面的开发应用呈不断扩大趋势。
2.9快速成形制造技术的应用
快速成形制造技术又称为快速原型制造技术,它包括立体光刻技术、分层实体制造技术、选择性激光烧结技术、熔融沉积技术、三维印刷技术、热塑性材料选择性喷洒和无模型树脂砂型快速制造工艺等成型方法,集成了CAD技术、数控技术、激光技术和材料技术等现代科技成果,是先进制造技术的重要组成部分。
与传统制造方法不同,快速成型从零件的CAD几何模型出发,通过软件分层离散和数控成型系统,用激光束或其它方法将材料堆积而形成实体零件,所以又称为材料添加制造法。由于它把复杂的三维制造转化为一系列二维制造的叠加,因而可以在不用模具和工具的条件下几乎能够生成任意复杂形状的零部件,极大地提高了生产效率。与数控加工、铸造、金属冷喷涂、硅胶模等制造手段一起,快速自动成型已成为现代模型、模具和零件制造的强有力手段,是目前适合我国国情的实现金属零件的单件或小批量敏捷制造的有效方法,尤其在汽车发动机缸体铸件等领域已得到了应用。
例如,选区激光烧结与铸造技术结合,可有效地应用于发动机设计开发阶段中样机的快速制造,保证产品开发速度,提高产品的开发质量,大大降低开发成本,推动产品早日进入市场。国内已经开发出V8发动机的缸体熔模,利用选区激光烧结成型技术直接制作蜡模,无需开模具,因而大大节省了制造周期和费用,其成型时间为42 h,铸造周期20天。如果按传统制作方法开模具制造,至少需要6个月的时间,费用上百万。此项技术为客户节省大量的时间和开发成本。
汽车发动机缸体的铸造生产中,模板、芯盒、压铸模的制造往往采用机加工的方法完成,此过程不仅周期长、耗资大,而且从模具设计到加工制造是一个多环节的复杂过程,其模具的制造过程极其复杂,开发周期长,研发成本大。不能适用于当前迅速响应市场的需求,而快速成型技术恰好满足了汽车发动机快速制造的要求。采用该技术与传统铸造相结合的方法能够非常迅速地实现从设计到产品的过程,减少中间环节,加快产品投放市场的速度,节省开发成本。
- 下一篇:汽车发动机缸体端面铣削加工技巧
- 上一篇:客车涂装原材料开发建议之电泳漆
最新资讯
-
旭化成微电子开始批量生产用于环保发
2025-04-24 16:00
-
华为、地平线、大众、东风、起亚等引
2025-04-24 08:27
-
全球产业链聚沪 共探双碳新路径 SNEC
2025-04-18 18:05
-
柯马签订具有约束力的协议收购 Autom
2025-04-17 13:01
-
高效协同新范式:比亚迪叉车领创智能
2025-04-17 10:04