汽车发动机缸体端面铣削加工技巧
2018-05-24 09:51:41· 来源:金属加工
缸体、缸盖是发动机的核心零部件,端面铣削在这两个零部件加工中占据重要位置,缸体、缸盖的顶底面和前后面都有较高的粗糙度和平面度要求,达不到要求会对发动机的性能、质量造成很大的影响。
摘要:缸体、缸盖是发动机的核心零部件,端面铣削在这两个零部件加工中占据重要位置,缸体、缸盖的顶底面和前后面都有较高的粗糙度和平面度要求,达不到要求会对发动机的性能、质量造成很大的影响。
2015年我厂在端面铣削过程中接连发生工件接刀痕严重、工件崩边的现象,工艺人员对此类现象了解的不够透彻,由此引发本文对端面铣削的深入研究与探讨,提出对端面铣削加工现象的优化解决方案。
加工现象技术分析
1. 加工现象
铣削是非常普通的加工方式。铣削属于断续切削,刀齿不断切入切出工件,切屑厚度和切削面积不断变化,冲击载荷较大,易发生振动,切削力在不断变化。切削力处于稳定状态时接刀痕并不明显,粗糙度、平面度都不会有太大变化。通常所指的接刀痕为痕迹明显、肉眼可辨,导致粗糙度、平面度超过工艺技术要求的刀痕。崩边一般发生在铸铁加工中,切削振动大,造成加工部位边缘的掉渣现象(见图1)。
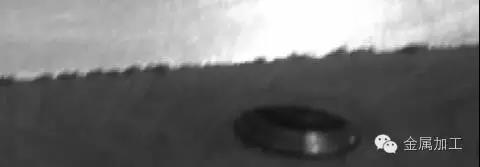
图 1
2. 接刀痕问题
(1)接刀痕产生的位置。切削力突变造成很大振动,就会产生明显的接刀痕。
接刀痕产生位置:①两次走刀的交接处会产生接刀痕。②刀具沿加工路径进给过程中,刀具再次经过已加工表面区域时,会产生微小的接刀痕迹,造成切削纹路发生些许变化,肉眼觉察不到,不影响加工质量,通常可忽略。③刀齿切入或切出工件的位置也会产生接刀痕。刀齿切入时,载荷突然急剧增大,产生较大振动;刀齿切出工件的瞬间,是一个卸载的过程,整个系统的弹性变形能瞬时释放,产生较大振动。故切入、切出过程均会产生较严重的刀痕,切出过程产生的刀痕比切入过程产生的刀痕严重。
(2)接刀痕产生的条件主要有以下几种:
切削参数:加工余量大、进给速度快,导致被加工表面挤压变形大,容易产生接刀痕。
刀具的安装误差:刀片安装误差较大,会产生接刀痕。由于我厂调刀人员,从未经过专业的调刀培训,专业素养及调刀经验参差不齐,调刀控制手段及标准不足,控制端面跳动的一致性有差别,不是每盘刀都能达到规定的换刀频次。例:新缸体OP210序,精铣前后面,Ra=3.2μm,平面度0.1mm,换刀频次800台,生产线反馈一盘新刀,有时加工1个班200台,接刀痕就很明显,而经验丰富的调刀人员调的端面铣刀确能达到规定的换刀频次,得到生产线工人的认可,既节约了换刀时间,又降低了成本。
主轴跳动很大:机床主轴与刀具系统连接刚性不足,高转速下,产生的巨大离心力会加速主轴轴承的磨损,同时引起机床加过过程中的急剧振动,切削表面会形成特别明显的刀痕。例:1.3缸体OP50序,后油封面加工,粗糙度3.2,平面度0.1,2015年设备改造前,主轴跳动大导致刀痕较深,平面度不符合工艺要求,严重影响了工件的质量。平面度不合格,会导致发动机后油封部位渗漏机油。当时主轴维修困难,我厂为了应对生产,重新匹配了两次走刀的加工余量,同时降低进给速度,暂时以牺牲刀具寿命为代价,完成了剩余的生产任务。
刀具磨损:毛坯硬度的不均匀会造成刀具过早磨损,刀具一旦到达急剧磨损阶段(见图2),切削力必然急剧增大,造成振动,刀痕自然明显很多,影响工件质量及表面粗糙度。一般情况下,刀具磨损是产生接刀痕的主要原因。例:天内的铸铁粗加工(见图3),正态切削,刀具磨损到急剧磨损阶段后,振动噪声变大,刀痕纹路清晰,手摸较明显。
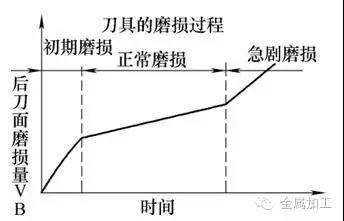
图 2
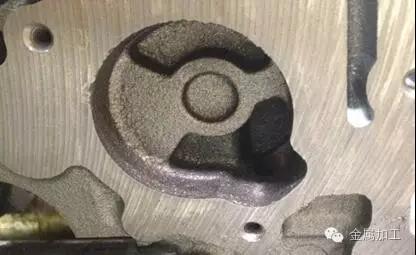
图 3
工件未夹紧:如果夹紧力不足,会导致工件松动,加工中产生震颤,产生接刀痕。
3. 崩边问题
新缸体OP50序,2015年2月设备厂家为保节拍、提高生产效率,对设备进行了维护,但在3月和4月刀片的换刀频次由100台降至40台,40台后继续加工,缸体左右凸台面发生崩边现象。刀具寿命偏低,刀具单台费用两个月居高不下。
伊斯卡样本表明,该刀片适用于铸铁加工,切削速度范围100~400m/min,而本工序切削速度为301m/min。铸铁加工,刀具磨损,导致横向切削力加大,造成铣刀盘即将切出工件的瞬间,将工件上留存的最后一点加工余量挤掉,工件表面发生崩边现象。刀具磨损越早,崩边现象发生的概率越大。解决办法如下:
(1)优化切削速度。
将切削速度由301m/min降至163m/min,为弥补节拍的不足,同时调整了进给速度。依据金属切削原理:合理速度内,切削速度降低20%,刀具寿命提高50%。降低切削速度后,该刀具单台费用由12元/台降至6元/台,按年产3万台缸体计算,年可节约资金18万元。此时换刀频次达到100后,崩边现象才会产生,保证了质量,同时也节约了频繁换刀的时间。
(2)刀盘结构优化。原刀盘(见图4)主偏角为90°,刀具在离开缸体边缘时的切削力全部为横向切削力,过大的拉力使工件边缘最后的加工余量剥落,造成表面崩边情况。
为了近一步降低成本,提高刀具寿命。我厂现地现物,利用现有资源,转序再利用开展降成本工作。原刀盘直径为Φ80mm,标准刀盘。利用曲轴OP10序刀盘(见图5)替换原刀盘。
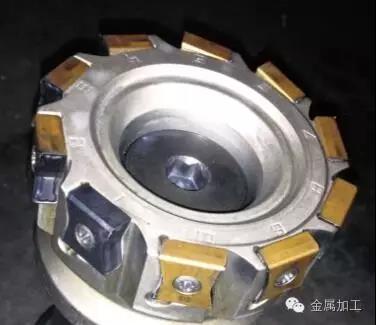
图 4
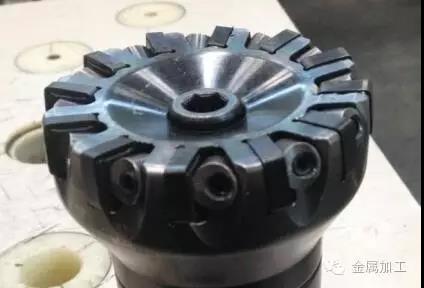
图 5
两刀盘基本参数如附表所示。
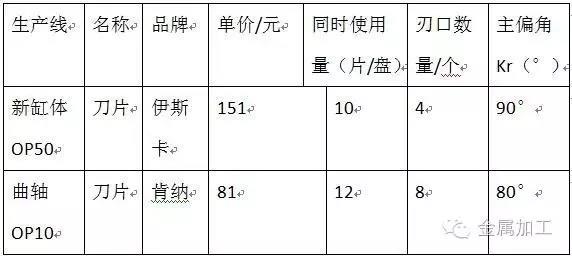
基本参数对比表
切削三要素不变的前提下,由于刀片同时使用量由10片变为12片,每个刀片的进给量相对变小,等同于每个刀刃产生的切屑厚度变薄,由粗糙度简化公式可知,小的进给量可适当的提高工件表面的粗糙度,小的进给量可以减小刀具离开缸体边缘时的切削力。同时 80°主偏角同90°主偏角比,可将切削力分解到两个方向,弱化了横向拉力对缸体边缘崩边现象的影响,增强了刀片寿命。
粗糙度简化公式Ra=f2/8R,式中,f为每转进给量(mm/min);R为刀尖圆弧半径(mm)。
走刀路线技术分析
数控加工过程中,刀具相对于工件的运动轨迹称为走刀路线。走刀路线反应了工件的加工过程,确定合理的走刀路线是保证铣削加工精度和表面质量的重要工艺措施之一,走刀路线的合理关系到加工的生产效率及刀具寿命,因此每道工序的走刀路线都非常重要。保证产品质量的前提下,走刀路线尽量最短,保持刀具一直吃刀。前期的工艺设计多考虑刀盘直径、刀盘结构、刀盘位置、铣削方式和刀具切入切出过程等因素,刀具全生命周期的70%取决于前期的工艺设计,工艺设计一旦设计完成,刀具成本也就固定了,后续改善优化只是一些辅助措施。
1. 端面铣削方式—顺铣和逆铣
如图6所示,顺铣可以理解为铣刀切入时切屑的厚度大于切出时切屑的厚度;逆铣可以理解为铣刀切入时切屑的厚度小于切出时切屑的厚度。刀片切入工件时承受压应力,切出时承受拉应力;拉应力更容易导致刀片产生裂纹、蹦刃,若要提高刀片寿命,就得减小刀片切出时的拉应力。顺铣,切出时切屑薄拉应力小;逆铣,切出时切屑厚拉应力大。对刀具寿命而言,顺铣方式要好于逆铣方式。
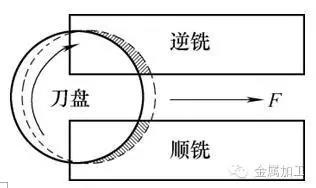
图 6
逆铣过程,端面铣刀刚刚切入时,刀片本身存在极细小的刀刃倒棱,加工余量很薄,刀片挤压、摩擦产生大量的切削热,造成工件表面硬化现象,切屑存在于刀片前刀面,再次切削造成工件质量变差。现大多数机床采用顺铣方式,优点:顺铣时,切屑由厚变薄,当端面铣刀前刀面切出工件的一瞬间,载荷突然释放,容易产生振动,但此时切屑很薄,切削力很小,载荷波动不会太大,故刀具寿命增加。
2. 铣削过程分析
铣削过程分为四个阶段:非切入阶段、切入阶段、切削阶段和切出阶段。
(1)端面铣刀切入策略:圆弧切入好于直接切入,斜着切入好于直接切入。切入策略原因分析:
直接切入方式(见图7)。未满刀切削与满刀切削相比,未满刀切出处产生厚的切屑,导致刀具加工过程中振动较大,刀具刃口容易失效、刀具寿命变差。若要采用此种方式直接切入,则在满刀切之前,为降低刀痕的影响,可将每转进给降为正常进给的50%。我厂的缸体、缸盖顶底面及前后面加工,都是采用直接切入方式,并且每转进给没有降低,这是需要注意的。
圆弧切入方式(见图8)。切出处切屑很薄,降低了切削力,振动降低,提高了刀具寿命。
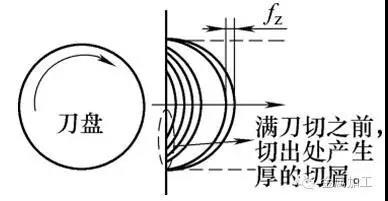
图 7
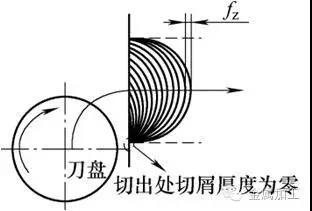
图 8
斜切方式。刀盘与工件成一定角度切入,目的是对刀盘切出处切屑厚度进行控制,间接提高铣刀片寿命。平滑切入工件是必要的,刚切入时进给应该降至50%,满刀切时恢复到正常的每转进给。
(2)端面铣刀切出策略。定义:切出角=铣刀切出点和刀盘中心点的连线与铣刀盘中心线的夹角。
经过世界第一刀具集团公司试验验证,切出角在(30°~90°与-90°~-30°)之间时刀片寿命较高,切出角范围在±30°时,刀片寿命偏低(见图9),故刀盘与工件位置关系影响刀片寿命。刀盘宽度为工件宽度2倍时,采用对称铣削方式(见图10),此时切出角为30°,刀盘布置是否合理,以此位置为基准,透彻全面的了解刀盘布置原理,迅速解决刀盘布置不合理,引发的刀片寿命偏低问题。
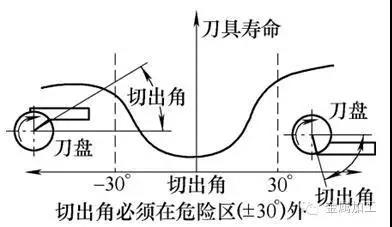
图 9
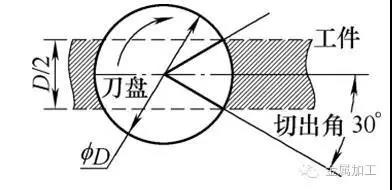
图 10
3. 刀盘直径与走刀路线
(1)刀盘直径。刀盘直径的选择主要由加工工件宽度决定。当加工平面面积不大时,刀盘直径一般为切削宽度的(1.3~1.6)倍,可有效保证切屑的形成和排出。精铣加工条件允许的情况下,可采用较大面铣刀一次走刀加工完成。
选择刀盘直径时尽量选择通用的标准刀盘。目前行业内标准刀盘直径已经固化,刀盘直径大致为Ф50mm、Ф63 mm、Ф80 mm、Ф100 mm、Ф125 mm、Ф160 mm、Ф200 mm、Ф250 mm和Ф315 mm等。标准刀盘通用性强,价格便宜,可替换。
刀盘直径的确定。刀盘直径D的大小与切入角A、切出角B及工件宽度E有关系,不管刀盘相对于工件如何布置,采用什么样的铣削方式,确定刀盘直径的原理是相同的。例:按如图11方式布置刀盘。
E=(D/2)sinB-(D/2)sinA
D=2E/(sinB-sinA)
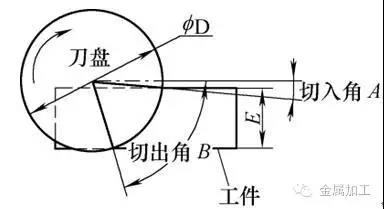
图 11
由上述公式可看出,只要选定刀盘径向切入深度、切入角和切出角,则铣刀盘直径就已确定。
(2)走刀路线。当加工平面面积较大时,可选择刀盘直径合适的铣刀,分多次走刀。多次走刀必然面临切削方向改变的情况,切削方向改变时产生的加工现象可理解为直接切入工件的情况。加工过程中,铣刀换向时,应变为圆角路线加工(见图12),可保证铣刀切出时铁屑厚度较薄,降低切削力,降低振动,增强刀具寿命,推迟了接刀痕产生的时间,提高了工件质量;图12切入时,采用的是斜切切入方式有助于刀片寿命的提高。我厂所有的面铣加工,走刀路线有切削方向变化的,都采用如图13所示方式。
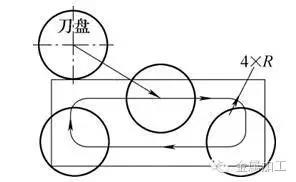
图 12
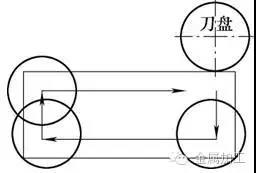
图 13
例如。我厂缸体加工两条生产线,后油封面加工两种不同的走刀路线。图14为1.3缸体线后油封面加工走刀路线。刀盘为非标刀盘,价格昂贵;切入方式为直接切入方式,现状:刚切入时每转进给没有优化,容易产生振纹;一次走刀完成加工,但刀盘布置方式为对称方式布置,对称铣削,加工过程中顺铣和逆铣同时存在,虽不是最佳方案,但也算合理。
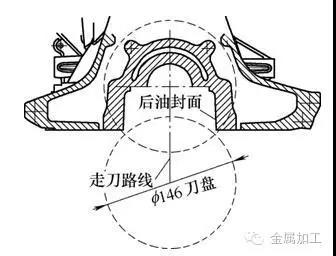
图 14
图15为1.5缸体线后油封面加工走刀路线。刀盘为标准刀盘,价格便宜;铣削方式为不对称顺铣方式,刀盘换向时采用圆弧加工路线过渡,非常合理,刀片寿命比图14的铣削方式高。加工过程需重点关注后油封面中间部位的粗糙度,两刀盘交接处容易产生刀痕。
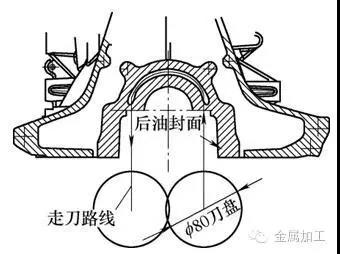
图 15
结语
本文在理论与实践的基础上,对加工过程中产生的接刀痕与崩边现象进行了大量的阐述,并提出了一系列的具体优化方案,多方位全角度的拓展了工作思路,可指引工艺人员迅速解决、消除生产中遇到的不良加工现象。本文对提升产品质量,提高工作效率,降本增效有一定的借鉴意义,值得引起重视与推广。
本文发表于《金属加工(冷加工)》2016年第19期8-11页
作者:天津一汽夏利汽车股份有限公司内燃机制造分公司刘崇泉
2015年我厂在端面铣削过程中接连发生工件接刀痕严重、工件崩边的现象,工艺人员对此类现象了解的不够透彻,由此引发本文对端面铣削的深入研究与探讨,提出对端面铣削加工现象的优化解决方案。
加工现象技术分析
1. 加工现象
铣削是非常普通的加工方式。铣削属于断续切削,刀齿不断切入切出工件,切屑厚度和切削面积不断变化,冲击载荷较大,易发生振动,切削力在不断变化。切削力处于稳定状态时接刀痕并不明显,粗糙度、平面度都不会有太大变化。通常所指的接刀痕为痕迹明显、肉眼可辨,导致粗糙度、平面度超过工艺技术要求的刀痕。崩边一般发生在铸铁加工中,切削振动大,造成加工部位边缘的掉渣现象(见图1)。
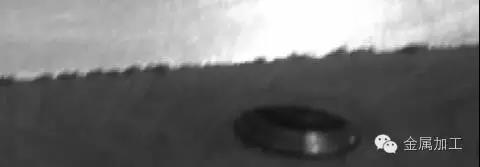
图 1
2. 接刀痕问题
(1)接刀痕产生的位置。切削力突变造成很大振动,就会产生明显的接刀痕。
接刀痕产生位置:①两次走刀的交接处会产生接刀痕。②刀具沿加工路径进给过程中,刀具再次经过已加工表面区域时,会产生微小的接刀痕迹,造成切削纹路发生些许变化,肉眼觉察不到,不影响加工质量,通常可忽略。③刀齿切入或切出工件的位置也会产生接刀痕。刀齿切入时,载荷突然急剧增大,产生较大振动;刀齿切出工件的瞬间,是一个卸载的过程,整个系统的弹性变形能瞬时释放,产生较大振动。故切入、切出过程均会产生较严重的刀痕,切出过程产生的刀痕比切入过程产生的刀痕严重。
(2)接刀痕产生的条件主要有以下几种:
切削参数:加工余量大、进给速度快,导致被加工表面挤压变形大,容易产生接刀痕。
刀具的安装误差:刀片安装误差较大,会产生接刀痕。由于我厂调刀人员,从未经过专业的调刀培训,专业素养及调刀经验参差不齐,调刀控制手段及标准不足,控制端面跳动的一致性有差别,不是每盘刀都能达到规定的换刀频次。例:新缸体OP210序,精铣前后面,Ra=3.2μm,平面度0.1mm,换刀频次800台,生产线反馈一盘新刀,有时加工1个班200台,接刀痕就很明显,而经验丰富的调刀人员调的端面铣刀确能达到规定的换刀频次,得到生产线工人的认可,既节约了换刀时间,又降低了成本。
主轴跳动很大:机床主轴与刀具系统连接刚性不足,高转速下,产生的巨大离心力会加速主轴轴承的磨损,同时引起机床加过过程中的急剧振动,切削表面会形成特别明显的刀痕。例:1.3缸体OP50序,后油封面加工,粗糙度3.2,平面度0.1,2015年设备改造前,主轴跳动大导致刀痕较深,平面度不符合工艺要求,严重影响了工件的质量。平面度不合格,会导致发动机后油封部位渗漏机油。当时主轴维修困难,我厂为了应对生产,重新匹配了两次走刀的加工余量,同时降低进给速度,暂时以牺牲刀具寿命为代价,完成了剩余的生产任务。
刀具磨损:毛坯硬度的不均匀会造成刀具过早磨损,刀具一旦到达急剧磨损阶段(见图2),切削力必然急剧增大,造成振动,刀痕自然明显很多,影响工件质量及表面粗糙度。一般情况下,刀具磨损是产生接刀痕的主要原因。例:天内的铸铁粗加工(见图3),正态切削,刀具磨损到急剧磨损阶段后,振动噪声变大,刀痕纹路清晰,手摸较明显。
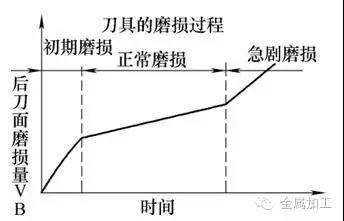
图 2
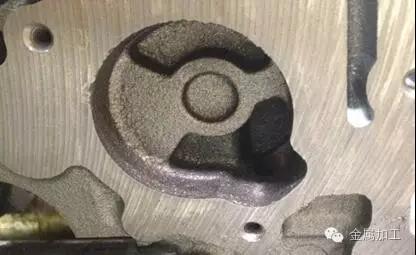
图 3
工件未夹紧:如果夹紧力不足,会导致工件松动,加工中产生震颤,产生接刀痕。
3. 崩边问题
新缸体OP50序,2015年2月设备厂家为保节拍、提高生产效率,对设备进行了维护,但在3月和4月刀片的换刀频次由100台降至40台,40台后继续加工,缸体左右凸台面发生崩边现象。刀具寿命偏低,刀具单台费用两个月居高不下。
伊斯卡样本表明,该刀片适用于铸铁加工,切削速度范围100~400m/min,而本工序切削速度为301m/min。铸铁加工,刀具磨损,导致横向切削力加大,造成铣刀盘即将切出工件的瞬间,将工件上留存的最后一点加工余量挤掉,工件表面发生崩边现象。刀具磨损越早,崩边现象发生的概率越大。解决办法如下:
(1)优化切削速度。
将切削速度由301m/min降至163m/min,为弥补节拍的不足,同时调整了进给速度。依据金属切削原理:合理速度内,切削速度降低20%,刀具寿命提高50%。降低切削速度后,该刀具单台费用由12元/台降至6元/台,按年产3万台缸体计算,年可节约资金18万元。此时换刀频次达到100后,崩边现象才会产生,保证了质量,同时也节约了频繁换刀的时间。
(2)刀盘结构优化。原刀盘(见图4)主偏角为90°,刀具在离开缸体边缘时的切削力全部为横向切削力,过大的拉力使工件边缘最后的加工余量剥落,造成表面崩边情况。
为了近一步降低成本,提高刀具寿命。我厂现地现物,利用现有资源,转序再利用开展降成本工作。原刀盘直径为Φ80mm,标准刀盘。利用曲轴OP10序刀盘(见图5)替换原刀盘。
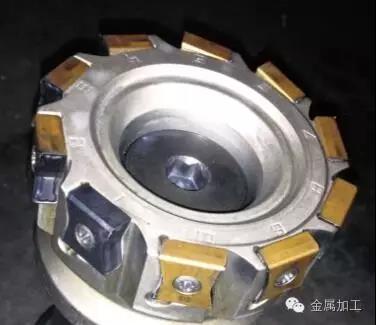
图 4
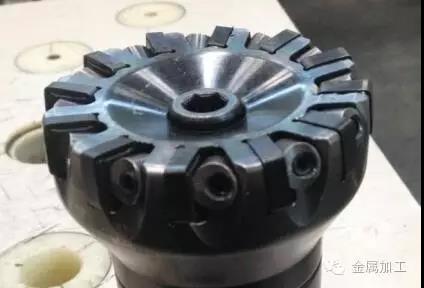
图 5
两刀盘基本参数如附表所示。
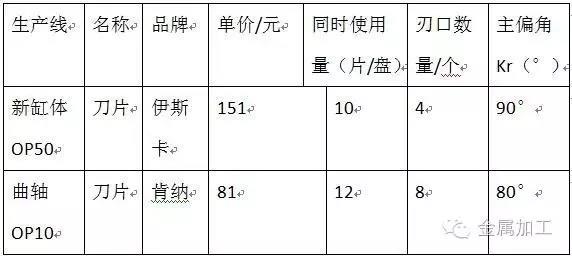
基本参数对比表
切削三要素不变的前提下,由于刀片同时使用量由10片变为12片,每个刀片的进给量相对变小,等同于每个刀刃产生的切屑厚度变薄,由粗糙度简化公式可知,小的进给量可适当的提高工件表面的粗糙度,小的进给量可以减小刀具离开缸体边缘时的切削力。同时 80°主偏角同90°主偏角比,可将切削力分解到两个方向,弱化了横向拉力对缸体边缘崩边现象的影响,增强了刀片寿命。
粗糙度简化公式Ra=f2/8R,式中,f为每转进给量(mm/min);R为刀尖圆弧半径(mm)。
走刀路线技术分析
数控加工过程中,刀具相对于工件的运动轨迹称为走刀路线。走刀路线反应了工件的加工过程,确定合理的走刀路线是保证铣削加工精度和表面质量的重要工艺措施之一,走刀路线的合理关系到加工的生产效率及刀具寿命,因此每道工序的走刀路线都非常重要。保证产品质量的前提下,走刀路线尽量最短,保持刀具一直吃刀。前期的工艺设计多考虑刀盘直径、刀盘结构、刀盘位置、铣削方式和刀具切入切出过程等因素,刀具全生命周期的70%取决于前期的工艺设计,工艺设计一旦设计完成,刀具成本也就固定了,后续改善优化只是一些辅助措施。
1. 端面铣削方式—顺铣和逆铣
如图6所示,顺铣可以理解为铣刀切入时切屑的厚度大于切出时切屑的厚度;逆铣可以理解为铣刀切入时切屑的厚度小于切出时切屑的厚度。刀片切入工件时承受压应力,切出时承受拉应力;拉应力更容易导致刀片产生裂纹、蹦刃,若要提高刀片寿命,就得减小刀片切出时的拉应力。顺铣,切出时切屑薄拉应力小;逆铣,切出时切屑厚拉应力大。对刀具寿命而言,顺铣方式要好于逆铣方式。
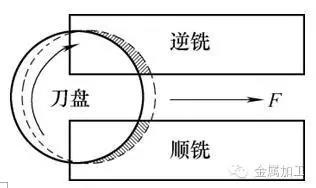
图 6
逆铣过程,端面铣刀刚刚切入时,刀片本身存在极细小的刀刃倒棱,加工余量很薄,刀片挤压、摩擦产生大量的切削热,造成工件表面硬化现象,切屑存在于刀片前刀面,再次切削造成工件质量变差。现大多数机床采用顺铣方式,优点:顺铣时,切屑由厚变薄,当端面铣刀前刀面切出工件的一瞬间,载荷突然释放,容易产生振动,但此时切屑很薄,切削力很小,载荷波动不会太大,故刀具寿命增加。
2. 铣削过程分析
铣削过程分为四个阶段:非切入阶段、切入阶段、切削阶段和切出阶段。
(1)端面铣刀切入策略:圆弧切入好于直接切入,斜着切入好于直接切入。切入策略原因分析:
直接切入方式(见图7)。未满刀切削与满刀切削相比,未满刀切出处产生厚的切屑,导致刀具加工过程中振动较大,刀具刃口容易失效、刀具寿命变差。若要采用此种方式直接切入,则在满刀切之前,为降低刀痕的影响,可将每转进给降为正常进给的50%。我厂的缸体、缸盖顶底面及前后面加工,都是采用直接切入方式,并且每转进给没有降低,这是需要注意的。
圆弧切入方式(见图8)。切出处切屑很薄,降低了切削力,振动降低,提高了刀具寿命。
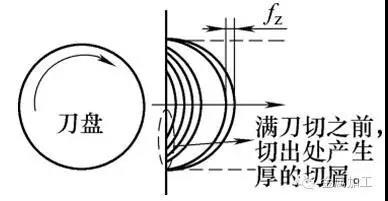
图 7
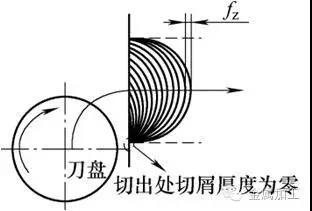
图 8
斜切方式。刀盘与工件成一定角度切入,目的是对刀盘切出处切屑厚度进行控制,间接提高铣刀片寿命。平滑切入工件是必要的,刚切入时进给应该降至50%,满刀切时恢复到正常的每转进给。
(2)端面铣刀切出策略。定义:切出角=铣刀切出点和刀盘中心点的连线与铣刀盘中心线的夹角。
经过世界第一刀具集团公司试验验证,切出角在(30°~90°与-90°~-30°)之间时刀片寿命较高,切出角范围在±30°时,刀片寿命偏低(见图9),故刀盘与工件位置关系影响刀片寿命。刀盘宽度为工件宽度2倍时,采用对称铣削方式(见图10),此时切出角为30°,刀盘布置是否合理,以此位置为基准,透彻全面的了解刀盘布置原理,迅速解决刀盘布置不合理,引发的刀片寿命偏低问题。
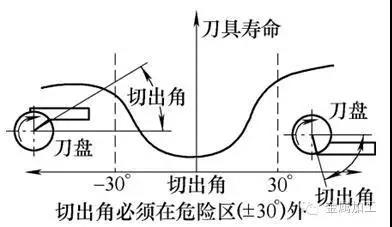
图 9
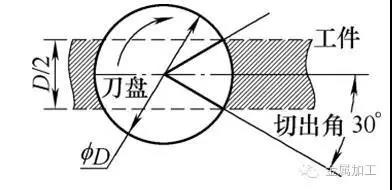
图 10
3. 刀盘直径与走刀路线
(1)刀盘直径。刀盘直径的选择主要由加工工件宽度决定。当加工平面面积不大时,刀盘直径一般为切削宽度的(1.3~1.6)倍,可有效保证切屑的形成和排出。精铣加工条件允许的情况下,可采用较大面铣刀一次走刀加工完成。
选择刀盘直径时尽量选择通用的标准刀盘。目前行业内标准刀盘直径已经固化,刀盘直径大致为Ф50mm、Ф63 mm、Ф80 mm、Ф100 mm、Ф125 mm、Ф160 mm、Ф200 mm、Ф250 mm和Ф315 mm等。标准刀盘通用性强,价格便宜,可替换。
刀盘直径的确定。刀盘直径D的大小与切入角A、切出角B及工件宽度E有关系,不管刀盘相对于工件如何布置,采用什么样的铣削方式,确定刀盘直径的原理是相同的。例:按如图11方式布置刀盘。
E=(D/2)sinB-(D/2)sinA
D=2E/(sinB-sinA)
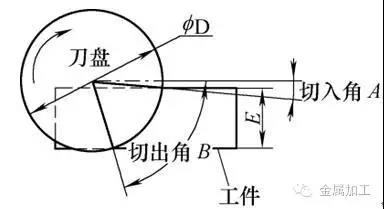
图 11
由上述公式可看出,只要选定刀盘径向切入深度、切入角和切出角,则铣刀盘直径就已确定。
(2)走刀路线。当加工平面面积较大时,可选择刀盘直径合适的铣刀,分多次走刀。多次走刀必然面临切削方向改变的情况,切削方向改变时产生的加工现象可理解为直接切入工件的情况。加工过程中,铣刀换向时,应变为圆角路线加工(见图12),可保证铣刀切出时铁屑厚度较薄,降低切削力,降低振动,增强刀具寿命,推迟了接刀痕产生的时间,提高了工件质量;图12切入时,采用的是斜切切入方式有助于刀片寿命的提高。我厂所有的面铣加工,走刀路线有切削方向变化的,都采用如图13所示方式。
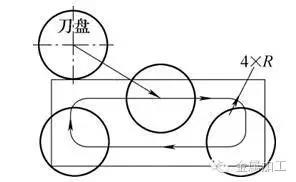
图 12
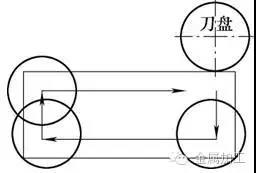
图 13
例如。我厂缸体加工两条生产线,后油封面加工两种不同的走刀路线。图14为1.3缸体线后油封面加工走刀路线。刀盘为非标刀盘,价格昂贵;切入方式为直接切入方式,现状:刚切入时每转进给没有优化,容易产生振纹;一次走刀完成加工,但刀盘布置方式为对称方式布置,对称铣削,加工过程中顺铣和逆铣同时存在,虽不是最佳方案,但也算合理。
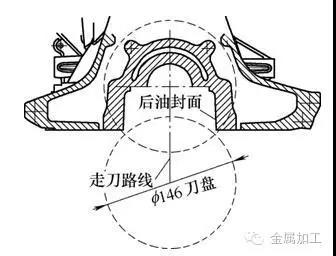
图 14
图15为1.5缸体线后油封面加工走刀路线。刀盘为标准刀盘,价格便宜;铣削方式为不对称顺铣方式,刀盘换向时采用圆弧加工路线过渡,非常合理,刀片寿命比图14的铣削方式高。加工过程需重点关注后油封面中间部位的粗糙度,两刀盘交接处容易产生刀痕。
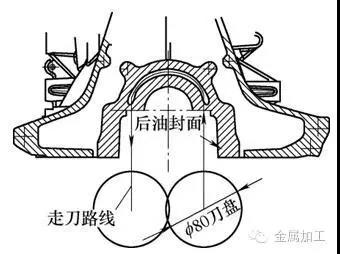
图 15
结语
本文在理论与实践的基础上,对加工过程中产生的接刀痕与崩边现象进行了大量的阐述,并提出了一系列的具体优化方案,多方位全角度的拓展了工作思路,可指引工艺人员迅速解决、消除生产中遇到的不良加工现象。本文对提升产品质量,提高工作效率,降本增效有一定的借鉴意义,值得引起重视与推广。
本文发表于《金属加工(冷加工)》2016年第19期8-11页
作者:天津一汽夏利汽车股份有限公司内燃机制造分公司刘崇泉
举报 0
收藏 0
分享 114
-
康耐视3D视觉软件:实现机器人对汽车发动机缸体
-
克服双金属发动机缸体面铣加工挑战
2018-07-23 发动机缸体 -
山特维克刀具解决方案 克服双金属发动机缸体面
-
国内汽车发动机缸体铸件铸造技术发展趋势
2018-05-24 发动机缸体铸件铸造技术
编辑推荐
最新资讯
-
展会预告 | 2025CIMT中国国际机床展
2025-04-11 14:44
-
航空发动机维修工装精准建模,3D扫描
2025-04-11 14:43
-
高歌猛进,奔赴“双碳”——比亚迪叉
2025-04-10 10:09
-
旭化成旗下旭塑洁螺杆清洗剂即将推出
2025-04-08 10:25
-
果栗智造磁悬浮技术赋能汽车制造:破
2025-04-03 19:27