塑料在汽车领域的最新成功应用
2018-05-28 09:39:20· 来源:SAEInternational
近年来涌现出了一批新型工程塑料,凭借结构强、重量轻、外观美等多种优点,得以在新型汽车应用中大展拳脚。
近年来涌现出了一批新型工程塑料,凭借结构强、重量轻、外观美等多种优点,得以在新型汽车应用中大展拳脚。
- Lindsay Brooke
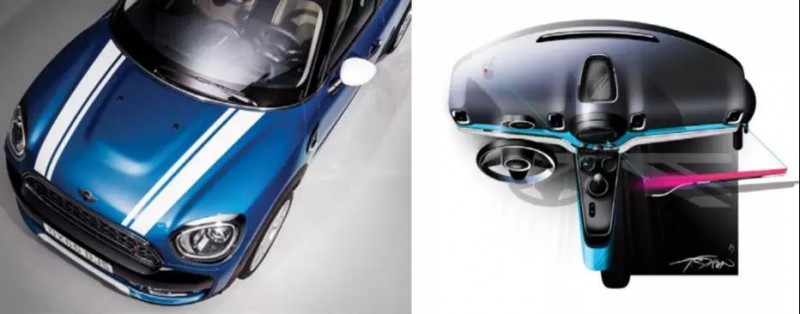
宝马最新款Mini Countryman采用了IAC的轻量化仪表板解决方案。
选钢还是选铝,这是一个全球汽车研发人员一直争论不下的问题。然而钢铝之争尚未尘埃落定,塑料和复合材料领域已取得了同样惊人的创新成果,无论是汽车还是卡车,无论是车内还是车外,都能见到这些新材料的身影。
宝马原本打算在总结i3和i8的宝贵装配经验后,建立一个从华盛顿摩西湖市到德国的“闭环式”碳纤维供应链,但最近这个雄心勃勃的项目被叫停了。不过,这并没有影响先进复合轻量化材料对以金属为核心的汽车行业的冲击。本文将着重介绍塑料在汽车领域的最新成功应用,并从CFRP(碳纤维增强塑料)的主要特性之一出发,探讨CFRP的未来。
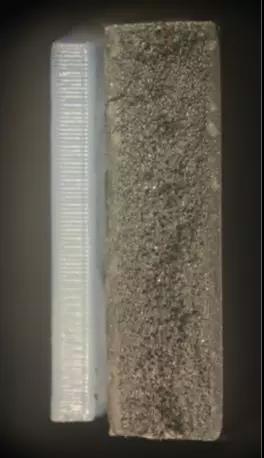
一个由Coreback工艺制成的零件的剖面图,整体厚度为2.8mm。白色物体是厚度为1mm的参照物。
宝马选择了Coreback
仪表板骨架和交叉结构,一直是材料创新的焦点,种类繁多的金属和金属复合材料与新型复合材料在该领域展开竞争。为了减轻2017版Mini Countryman的仪表板架构的重量,宝马工程师选择了IAC(国际汽车零部件集团)的Coreback全新注塑工艺。
据介绍,和“PP(聚丙烯)+ 滑石粉填料”的传统注塑件相比,长玻纤维增强聚丙烯轻量化塑料泡沫制成的Mini 仪表板骨架的重量减轻了15%,而且刚性重量比卓越。通过改进这样的传统工艺,宝马实现了4%-5%的车身减重。
“Coreback 工艺是先在全压下注入树脂和CFA(化学发泡剂),完全填满模腔。接着再开模。零件内部的泡沫会顺着开模拉伸的方向,均匀完美地膨胀,”IAC高级研发部总监Marc Hayes解释道。
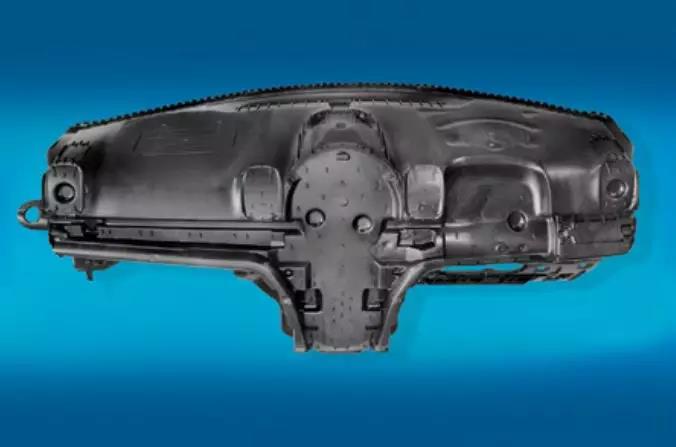
Mini的Coreback仪表板骨架展现了该工艺有助于整合零部件的优点。
Hayes表示,在使用Coreback工艺制造仪表板骨架或车门内饰板等大件时,注塑厚度为1.8mm,然后在开模时将制件拉伸到2.8mm。“模腔内的真实树脂注塑厚度是1.8mm,而不是2.8mm。这就是减重15-20%的秘密所在。横截面的其它部分都是气穴。”该工艺最多可将制件拉伸到4mm(0.157英寸)。
Mini 仪表板骨架项目是IAC Coreback工艺的首例量产应用。该项目由IAC、宝马、模具制造商Siebenwust、化学品供应商SABIC(沙特基础工业公司)共同合作完成。
Hayes 表示,“为了确保凹坑或升降杆的运动,标准的筋与壁厚之比通常为60%,而通过使用Coreback,我们可以打破这个局限。发泡剂也有助于增加这一比例。”
IAC和SABIC的工程师使用CAE(计算机辅助工程技术)探索出了如何在现有的注塑机中使用特制的CFA,并预测泡沫塑件的翘曲。这一全面的分析法使工程师得以提前修改工具,避免可能出现的生产问题,确保生产顺利展开。
数十年来,结构性泡沫已经成为了船只仪表板、建筑外饰和门板的主体材料。福特早在上世纪80年代就尝试过使用结构性泡沫制造仪表板。
继Mini仪表板项目大获成功后,IAC将继续在外部内饰件和内部结构件上应用Coreback工艺。Hayes表示,未来需要进一步改进CFA。
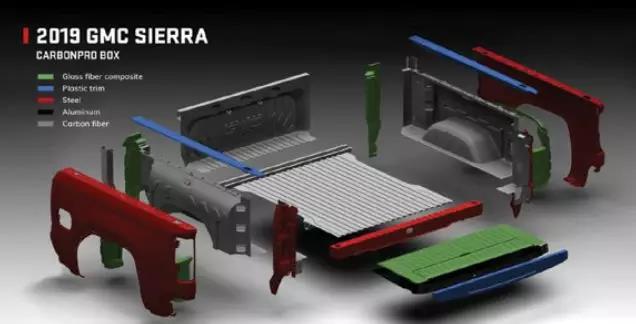
2019GMC Sierra Denali的全新碳纤维复合型车厢采用了多种材料,上图是各类材料的分解图。
Denali的碳纤维车厢
通用汽车的2019版Sierra Denali是业内首次采用碳复合材车厢的皮卡,这也标志着包括连续纤维增强材料在内的轻量化材料离主流应用更近了一步,且其在车内的应用比例也在提升。
值得一提的是,通用对复合材料的应用最早可追溯到1953版Corvette的车身。随后,通用又在1955年和1958年的雪佛兰Cameo Carrier上率先使用了片状模压部分复合材料车厢。这次由通用、CSP(大陆结构塑料公司)和CSP母公司帝人公司共同研发的Denali碳复合车身正是这一技术沿革的最新成果。
Sierra首席工程师Tim Herrick在接受《汽车工程》杂志的采访时表示,全新Sierra车厢抗凹陷、抗刮痕、抗腐蚀,这让通用的工程师很满意。Sierra碳纤维热塑性尼龙6车厢比标准铁制的减轻了62磅(28kg)。
新材料选用了短切纤维,而非编织纤维。短切纤维可塑性强,使得设计师可以拓宽车厢,车厢容积增加了一立方英尺。Herrick表示,为防止剥落,双层粘接工艺一开始就使用了结构性粘合剂和一个机械紧固件。
Herrick还告诉《汽车工程》杂志,新款Sierra车厢的两个部分—左前和右前插槽加强件—采用了100%后处理可再生材料。碳纤维车厢将先在位于印第安纳州惠灵顿市的CSP工厂注塑成型,然后在通用的韦恩堡装配工厂修平。
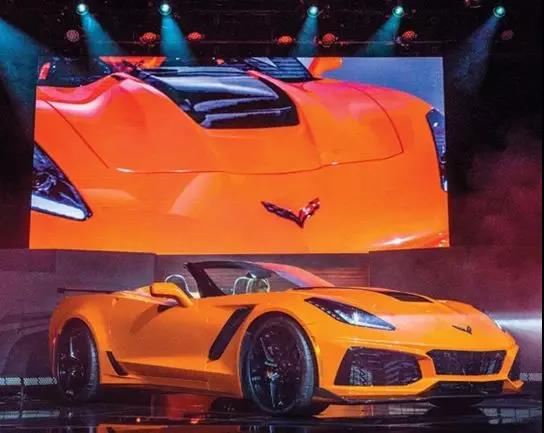
图上展示的是2019款ZR1 两门跑车。现有Corvette系列所采用的PCC创新型材料展现了顶级奢华感和一流质量水准。C8会有新的突破吗?
Plasan带来CFRP先进分析技术
2019款Sierra Denali将于2018年秋季亮相,但是让工程师们更翘首以盼的,是通用C8 Corvette。通用此前在2014款Corvette上大胆采用了以PCC(Plasan复合材料公司)的非高压釜(out-of-autoclave)冲压技术制作而成的A级车身板,在定于2019年年初发布的下一代Corvette上,不知道通用是否会增加CFRP的比例。
“无可奉告,这个问题我们无法回答!”,PCC工程副总裁Dan Hartzler和PCC总工程师Robert Murch这样说道。两人在最近接受《汽车工程》杂志的采访时表示,目前CFRP材料和工艺技术的研发目标是加快加工周期、扩大生产量,同时大大缩短注塑后的抛光环节。
“十年前我们的工艺就已经在赶超那些预浸料化工巨头了,”Murch解释道,“但是所有主要的树脂供应商都意识到了市场需求。过去3年,预浸料工艺取得了令人惊叹的进步。像Solvay、Toray这样的公司还在航空航天领域一争高下。但是他们缺乏像我们这样的先进工艺。我们的预浸料工艺只需要2分钟,甚至更短。”
Hartzler表示,PCC也在研发冲压模具。“我们正在努力将生产周期从15到17分钟缩短到10到12分钟。现在的关键是攻破瓶颈,但是瓶颈总在变化。我们的模具能否达到新型树脂的生产周期标准?”他还表示,为了缩短生产周期,PCC可能会探索其它成型工艺。
“现在,整车企业终于准备好要研究怎么样才能在新领域发挥新材料和成型工艺的最大价值,”Hartzler说道。下一波技术将助力CFRP在结构件上得到更大规模的应用。
PCC已经宣布将在汽车技术上投资4000万美元,以支持结构性碳纤维在车门防撞梁、保险杆等零部件上的应用,并缩短生产周期,降低制造成本。
Murch表示,“我们越来越多地使用了动态建模,这将帮助我们将材料的应用范围拓展到B柱和发动机机舱内的零部件。PPC正在将母公司(Plasan Sasa)的弹道技术转移到汽车领域,这不是我在说大话。我们可以为整车企业提供分析在内的完整解决方案。”
展望2020年,随着自动驾驶汽车的兴起和完全自动驾驶的到来,Hartzler和Murch相信CFRP将会有更多的发展机遇。
Hartzler说,“整车企业已经达成了新的共识:新型复合材料不是金属板的替代件,而是综合性的零部件解决方案。”
- Lindsay Brooke
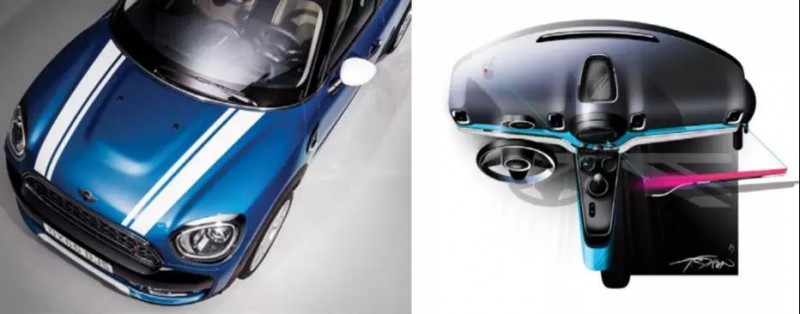
宝马最新款Mini Countryman采用了IAC的轻量化仪表板解决方案。
选钢还是选铝,这是一个全球汽车研发人员一直争论不下的问题。然而钢铝之争尚未尘埃落定,塑料和复合材料领域已取得了同样惊人的创新成果,无论是汽车还是卡车,无论是车内还是车外,都能见到这些新材料的身影。
宝马原本打算在总结i3和i8的宝贵装配经验后,建立一个从华盛顿摩西湖市到德国的“闭环式”碳纤维供应链,但最近这个雄心勃勃的项目被叫停了。不过,这并没有影响先进复合轻量化材料对以金属为核心的汽车行业的冲击。本文将着重介绍塑料在汽车领域的最新成功应用,并从CFRP(碳纤维增强塑料)的主要特性之一出发,探讨CFRP的未来。
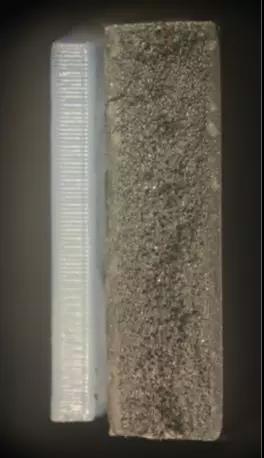
一个由Coreback工艺制成的零件的剖面图,整体厚度为2.8mm。白色物体是厚度为1mm的参照物。
宝马选择了Coreback
仪表板骨架和交叉结构,一直是材料创新的焦点,种类繁多的金属和金属复合材料与新型复合材料在该领域展开竞争。为了减轻2017版Mini Countryman的仪表板架构的重量,宝马工程师选择了IAC(国际汽车零部件集团)的Coreback全新注塑工艺。
据介绍,和“PP(聚丙烯)+ 滑石粉填料”的传统注塑件相比,长玻纤维增强聚丙烯轻量化塑料泡沫制成的Mini 仪表板骨架的重量减轻了15%,而且刚性重量比卓越。通过改进这样的传统工艺,宝马实现了4%-5%的车身减重。
“Coreback 工艺是先在全压下注入树脂和CFA(化学发泡剂),完全填满模腔。接着再开模。零件内部的泡沫会顺着开模拉伸的方向,均匀完美地膨胀,”IAC高级研发部总监Marc Hayes解释道。
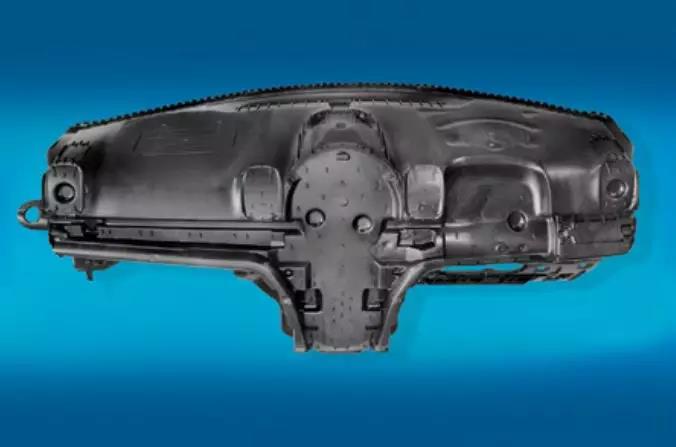
Mini的Coreback仪表板骨架展现了该工艺有助于整合零部件的优点。
Hayes表示,在使用Coreback工艺制造仪表板骨架或车门内饰板等大件时,注塑厚度为1.8mm,然后在开模时将制件拉伸到2.8mm。“模腔内的真实树脂注塑厚度是1.8mm,而不是2.8mm。这就是减重15-20%的秘密所在。横截面的其它部分都是气穴。”该工艺最多可将制件拉伸到4mm(0.157英寸)。
Mini 仪表板骨架项目是IAC Coreback工艺的首例量产应用。该项目由IAC、宝马、模具制造商Siebenwust、化学品供应商SABIC(沙特基础工业公司)共同合作完成。
Hayes 表示,“为了确保凹坑或升降杆的运动,标准的筋与壁厚之比通常为60%,而通过使用Coreback,我们可以打破这个局限。发泡剂也有助于增加这一比例。”
IAC和SABIC的工程师使用CAE(计算机辅助工程技术)探索出了如何在现有的注塑机中使用特制的CFA,并预测泡沫塑件的翘曲。这一全面的分析法使工程师得以提前修改工具,避免可能出现的生产问题,确保生产顺利展开。
数十年来,结构性泡沫已经成为了船只仪表板、建筑外饰和门板的主体材料。福特早在上世纪80年代就尝试过使用结构性泡沫制造仪表板。
继Mini仪表板项目大获成功后,IAC将继续在外部内饰件和内部结构件上应用Coreback工艺。Hayes表示,未来需要进一步改进CFA。
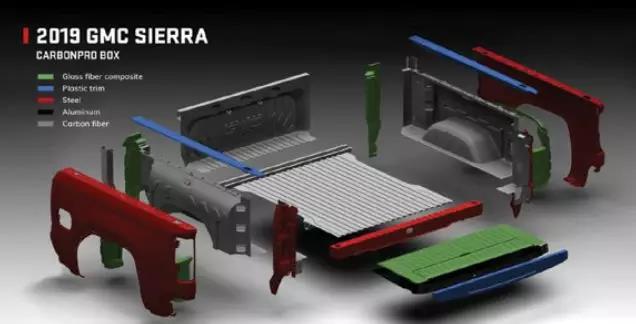
2019GMC Sierra Denali的全新碳纤维复合型车厢采用了多种材料,上图是各类材料的分解图。
Denali的碳纤维车厢
通用汽车的2019版Sierra Denali是业内首次采用碳复合材车厢的皮卡,这也标志着包括连续纤维增强材料在内的轻量化材料离主流应用更近了一步,且其在车内的应用比例也在提升。
值得一提的是,通用对复合材料的应用最早可追溯到1953版Corvette的车身。随后,通用又在1955年和1958年的雪佛兰Cameo Carrier上率先使用了片状模压部分复合材料车厢。这次由通用、CSP(大陆结构塑料公司)和CSP母公司帝人公司共同研发的Denali碳复合车身正是这一技术沿革的最新成果。
Sierra首席工程师Tim Herrick在接受《汽车工程》杂志的采访时表示,全新Sierra车厢抗凹陷、抗刮痕、抗腐蚀,这让通用的工程师很满意。Sierra碳纤维热塑性尼龙6车厢比标准铁制的减轻了62磅(28kg)。
新材料选用了短切纤维,而非编织纤维。短切纤维可塑性强,使得设计师可以拓宽车厢,车厢容积增加了一立方英尺。Herrick表示,为防止剥落,双层粘接工艺一开始就使用了结构性粘合剂和一个机械紧固件。
Herrick还告诉《汽车工程》杂志,新款Sierra车厢的两个部分—左前和右前插槽加强件—采用了100%后处理可再生材料。碳纤维车厢将先在位于印第安纳州惠灵顿市的CSP工厂注塑成型,然后在通用的韦恩堡装配工厂修平。
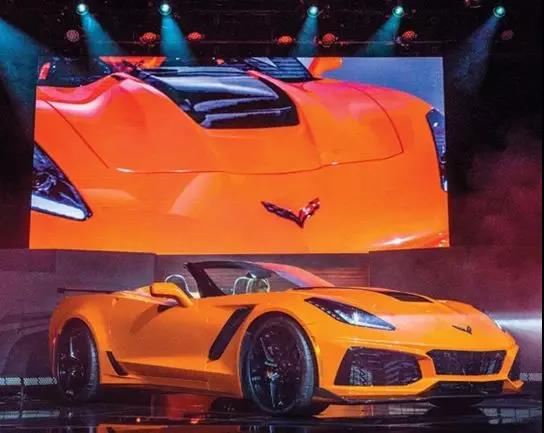
图上展示的是2019款ZR1 两门跑车。现有Corvette系列所采用的PCC创新型材料展现了顶级奢华感和一流质量水准。C8会有新的突破吗?
Plasan带来CFRP先进分析技术
2019款Sierra Denali将于2018年秋季亮相,但是让工程师们更翘首以盼的,是通用C8 Corvette。通用此前在2014款Corvette上大胆采用了以PCC(Plasan复合材料公司)的非高压釜(out-of-autoclave)冲压技术制作而成的A级车身板,在定于2019年年初发布的下一代Corvette上,不知道通用是否会增加CFRP的比例。
“无可奉告,这个问题我们无法回答!”,PCC工程副总裁Dan Hartzler和PCC总工程师Robert Murch这样说道。两人在最近接受《汽车工程》杂志的采访时表示,目前CFRP材料和工艺技术的研发目标是加快加工周期、扩大生产量,同时大大缩短注塑后的抛光环节。
“十年前我们的工艺就已经在赶超那些预浸料化工巨头了,”Murch解释道,“但是所有主要的树脂供应商都意识到了市场需求。过去3年,预浸料工艺取得了令人惊叹的进步。像Solvay、Toray这样的公司还在航空航天领域一争高下。但是他们缺乏像我们这样的先进工艺。我们的预浸料工艺只需要2分钟,甚至更短。”
Hartzler表示,PCC也在研发冲压模具。“我们正在努力将生产周期从15到17分钟缩短到10到12分钟。现在的关键是攻破瓶颈,但是瓶颈总在变化。我们的模具能否达到新型树脂的生产周期标准?”他还表示,为了缩短生产周期,PCC可能会探索其它成型工艺。
“现在,整车企业终于准备好要研究怎么样才能在新领域发挥新材料和成型工艺的最大价值,”Hartzler说道。下一波技术将助力CFRP在结构件上得到更大规模的应用。
PCC已经宣布将在汽车技术上投资4000万美元,以支持结构性碳纤维在车门防撞梁、保险杆等零部件上的应用,并缩短生产周期,降低制造成本。
Murch表示,“我们越来越多地使用了动态建模,这将帮助我们将材料的应用范围拓展到B柱和发动机机舱内的零部件。PPC正在将母公司(Plasan Sasa)的弹道技术转移到汽车领域,这不是我在说大话。我们可以为整车企业提供分析在内的完整解决方案。”
展望2020年,随着自动驾驶汽车的兴起和完全自动驾驶的到来,Hartzler和Murch相信CFRP将会有更多的发展机遇。
Hartzler说,“整车企业已经达成了新的共识:新型复合材料不是金属板的替代件,而是综合性的零部件解决方案。”
编辑推荐
最新资讯
-
全球产业链聚沪 共探双碳新路径 SNEC
2025-04-18 18:05
-
柯马签订具有约束力的协议收购 Autom
2025-04-17 13:01
-
高效协同新范式:比亚迪叉车领创智能
2025-04-17 10:04
-
埃马克德国总部迎来中国社科院工业经
2025-04-15 09:40
-
埃马克这项全新应用即将在CIMT惊艳首
2025-04-15 09:37