三维激光切割汽车模具生产中的应用
2018-05-28 14:52:30· 来源:激光谷
三维激光切割是将激光切割技术应用于立体工件的非接触切割加工,激光头的运动轨迹是一个空间的曲线。在正常情况下一套模具只能针对一种工件一道工序,而三维激光切割能针对任意工件的任意工序。
三维激光切割是将激光切割技术应用于立体工件的非接触切割加工,激光头的运动轨迹是一个空间的曲线。在正常情况下一套模具只能针对一种工件一道工序,而三维激光切割能针对任意工件的任意工序。
三维激光切割的优点
首先,三维激光切割柔性化程度高,在工件产品发生变动时,例如曲面,修边和孔等的变化更改,只需对激光切割的脱机程序进行更改,因其使用的工装夹具相对简单一些,所以工装夹具改动也方便。其次,三维激光切割相对其他切割方式,效率高、精度好、污染小、劳动强度低以及节约成本。
由于三维激光切割具有上述优点,其广泛应用于汽车行业中,它能够方便快捷的实现汽车覆盖件的三维修边和冲孔,也可以在一些小批量的试制中取代修边和冲孔模具,甚至在一些量产车型的部分制件的修边冲孔工序中完全由三维激光切割取代。
三维激光切割机的应用
我厂是国内汽车覆盖件模具生产的龙头企业,目前使用的三维激光切割设备是德国Arnold公司19044ZXB龙门式激光加工系统(见图1)。虽然该三维激光切割系统对生产效率提升不少,但是也存在一些影响生产效率和质量的不足之处。
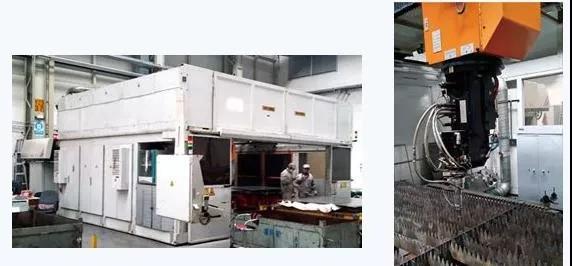
(图一)
(1)编程三维激光切割有示教和离线两种。对于示教编程:首先,示教编程占用机床时间长。例如一个轿车侧围的修边切孔编程大约需要两天时间,此类程序编制的工作量大,劳动强度大(见图2),且在采点编缉过程中容易出错。其次,程序的可交换性差。对称件(如左右翼子板)程序需重复编制。但示教编程的准确性高,因为其是一步一步通过大量的点数据采集构成的程序,所以此类程序后期改动量小,并且节约了购买编程软件的成本,对于占用机床时间对生产任务不忙的企业是合适的。
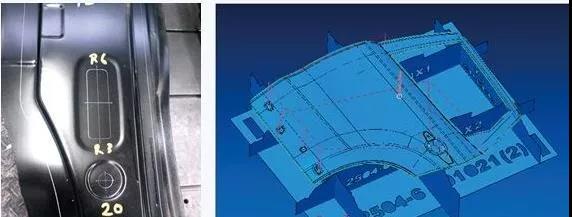
图2三维切割前刻线件手工标示图3插板式支架切割车门外板
对于离线编程:使用编程软件利用工件的数控模型编程。这种方式的优点很多,首先,效率高,编程速度快;其次,不占用机床,可以提前编制多个程序,方便安排生产;并且此类程序方便更改,对称工件无需要重复编程。相比示教编程,不需要全尺寸的刻线件,只需要几个刻线点(三个以上)即可。但这种编程方式准确度低,后期改动大。因为离线编写的程序在机床加工时对程序坐标系的定位是通过实际采集刻线点的机床坐标值与数据模型中的理论坐标值进行比对,通过某种算法拟合程序。也就是说,它会对实际工件的偏差做出相对应的调整,使程序的轨迹更贴近于实际工件。但是这种策略几乎可以肯定,实际加工出来的工件会有所偏差。而数据点的采集一般设在较容易采集区域,只是根据这三个点间偏差来回移动坐标系,难免无法顾及全部。因此,在实际生产中,必须对程序进行调整。
(2)工装支架工装支架通常有两种制作方式。一种是插板式的,即通过切割出对应产品形状的钢板,彼此拼搭而成。这种方法速度快,效率高,是一种粗定位。另一种是用钢筋(管)焊在底座上和产品搭接部分或使用旧件的一部分(手工切割下来),或使用树脂块和产品贴附。这种方法更贴近实际工件。三维激光切割主要面对的是拉延件,无法用销子等孔来定位,只能靠工件的形状来定位,而薄板件的变形量又比较大,所以生产中在支架上辅以磁铁等加强定位。
(3)激光切割系统我厂的三维激光切割机床使用的是二氧化碳板条式激光器,激光发生器发出的激光需要经过由设在机床各自轴上的反射镜片组成的光路系统(所谓飞行光路)传到激光切割头的聚焦镜上,再通过聚焦使平行光束变成光点照射在工件上,通过烧熔、吹屑等动作完成切割工作。
影响激光切割质量的因素很多,激光的功率,模态频率,整个光路系统的传输效率,稳定性等,还有加工材料的光反射率,切割用气体种类,气体压力,切割喷嘴的口径大小,喷嘴的形状,切割时的焦点位置,打孔的焦点位置,切割功率与速度的对应等。这些是激光切割要考虑的因素,三维激光切割还需面对切割喷嘴与工件不垂直时加工状态。这是由产品形状与切割头干涉所造成的,有时这种干涉使得加工无法顺利完成,不得不更改工艺流程。三维激光切割对光路的准确性要求高,即使机床的A轴(B轴)和C轴转了很大的角度时,光斑也要保证出现在喷嘴的中间位置,不能有大的偏差。
3.结语
通过三维激光切割设备的生产实践,三维激光切割对加工效率的提升是非常显著的。对于二氧化碳板条式激光切割系统,激光器的各种性能光束的纯度,能量的密度,高负荷时输出的稳定性,激光气体的寿命与经济性,对电压变化的适应性等都将极大地提高三维激光切割的能力、质量与效率。机床方面光路系统的传输效率,激光头的灵活性,程序的易改与方便化,智能化都是用户期待的,也是厂家应该努力的方向。
三维激光切割的优点
首先,三维激光切割柔性化程度高,在工件产品发生变动时,例如曲面,修边和孔等的变化更改,只需对激光切割的脱机程序进行更改,因其使用的工装夹具相对简单一些,所以工装夹具改动也方便。其次,三维激光切割相对其他切割方式,效率高、精度好、污染小、劳动强度低以及节约成本。
由于三维激光切割具有上述优点,其广泛应用于汽车行业中,它能够方便快捷的实现汽车覆盖件的三维修边和冲孔,也可以在一些小批量的试制中取代修边和冲孔模具,甚至在一些量产车型的部分制件的修边冲孔工序中完全由三维激光切割取代。
三维激光切割机的应用
我厂是国内汽车覆盖件模具生产的龙头企业,目前使用的三维激光切割设备是德国Arnold公司19044ZXB龙门式激光加工系统(见图1)。虽然该三维激光切割系统对生产效率提升不少,但是也存在一些影响生产效率和质量的不足之处。
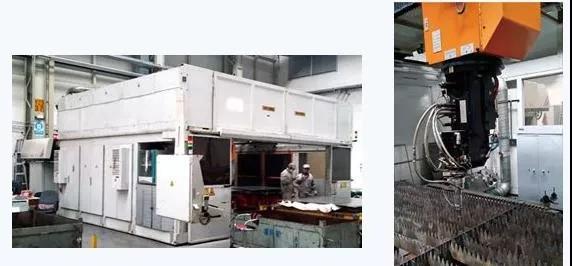
(图一)
(1)编程三维激光切割有示教和离线两种。对于示教编程:首先,示教编程占用机床时间长。例如一个轿车侧围的修边切孔编程大约需要两天时间,此类程序编制的工作量大,劳动强度大(见图2),且在采点编缉过程中容易出错。其次,程序的可交换性差。对称件(如左右翼子板)程序需重复编制。但示教编程的准确性高,因为其是一步一步通过大量的点数据采集构成的程序,所以此类程序后期改动量小,并且节约了购买编程软件的成本,对于占用机床时间对生产任务不忙的企业是合适的。
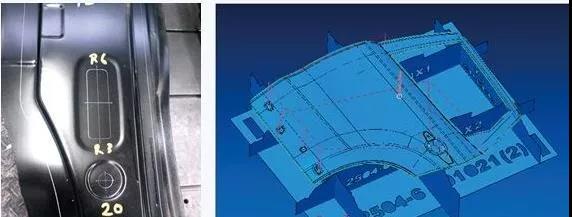
图2三维切割前刻线件手工标示图3插板式支架切割车门外板
对于离线编程:使用编程软件利用工件的数控模型编程。这种方式的优点很多,首先,效率高,编程速度快;其次,不占用机床,可以提前编制多个程序,方便安排生产;并且此类程序方便更改,对称工件无需要重复编程。相比示教编程,不需要全尺寸的刻线件,只需要几个刻线点(三个以上)即可。但这种编程方式准确度低,后期改动大。因为离线编写的程序在机床加工时对程序坐标系的定位是通过实际采集刻线点的机床坐标值与数据模型中的理论坐标值进行比对,通过某种算法拟合程序。也就是说,它会对实际工件的偏差做出相对应的调整,使程序的轨迹更贴近于实际工件。但是这种策略几乎可以肯定,实际加工出来的工件会有所偏差。而数据点的采集一般设在较容易采集区域,只是根据这三个点间偏差来回移动坐标系,难免无法顾及全部。因此,在实际生产中,必须对程序进行调整。
(2)工装支架工装支架通常有两种制作方式。一种是插板式的,即通过切割出对应产品形状的钢板,彼此拼搭而成。这种方法速度快,效率高,是一种粗定位。另一种是用钢筋(管)焊在底座上和产品搭接部分或使用旧件的一部分(手工切割下来),或使用树脂块和产品贴附。这种方法更贴近实际工件。三维激光切割主要面对的是拉延件,无法用销子等孔来定位,只能靠工件的形状来定位,而薄板件的变形量又比较大,所以生产中在支架上辅以磁铁等加强定位。
(3)激光切割系统我厂的三维激光切割机床使用的是二氧化碳板条式激光器,激光发生器发出的激光需要经过由设在机床各自轴上的反射镜片组成的光路系统(所谓飞行光路)传到激光切割头的聚焦镜上,再通过聚焦使平行光束变成光点照射在工件上,通过烧熔、吹屑等动作完成切割工作。
影响激光切割质量的因素很多,激光的功率,模态频率,整个光路系统的传输效率,稳定性等,还有加工材料的光反射率,切割用气体种类,气体压力,切割喷嘴的口径大小,喷嘴的形状,切割时的焦点位置,打孔的焦点位置,切割功率与速度的对应等。这些是激光切割要考虑的因素,三维激光切割还需面对切割喷嘴与工件不垂直时加工状态。这是由产品形状与切割头干涉所造成的,有时这种干涉使得加工无法顺利完成,不得不更改工艺流程。三维激光切割对光路的准确性要求高,即使机床的A轴(B轴)和C轴转了很大的角度时,光斑也要保证出现在喷嘴的中间位置,不能有大的偏差。
3.结语
通过三维激光切割设备的生产实践,三维激光切割对加工效率的提升是非常显著的。对于二氧化碳板条式激光切割系统,激光器的各种性能光束的纯度,能量的密度,高负荷时输出的稳定性,激光气体的寿命与经济性,对电压变化的适应性等都将极大地提高三维激光切割的能力、质量与效率。机床方面光路系统的传输效率,激光头的灵活性,程序的易改与方便化,智能化都是用户期待的,也是厂家应该努力的方向。
- 下一篇:如何解决汽车冲压回弹问题
- 上一篇:解密冲压工艺中工业机器人应用技术
编辑推荐
最新资讯
-
全球产业链聚沪 共探双碳新路径 SNEC
2025-04-18 18:05
-
柯马签订具有约束力的协议收购 Autom
2025-04-17 13:01
-
高效协同新范式:比亚迪叉车领创智能
2025-04-17 10:04
-
埃马克德国总部迎来中国社科院工业经
2025-04-15 09:40
-
埃马克这项全新应用即将在CIMT惊艳首
2025-04-15 09:37