等速万向节精锻的发展方向
2018-06-01 17:11:25· 来源:中国锻压协会
在筒形壳和三柱槽壳精锻件的机加工生产中,发现这些锻件车完倒角和端面以后的去除残留毛刺,是一个很难处理的技术问题(图8-5-1)。到目前为止,人们发明了许多去毛刺的设备和方法,最后还是觉得手工去毛刺最可靠。但是,在大批量生产时,往自动化生产线中插入几个手工操作的工序,无论是生产效率,还是保证作业质量,都不能使人满意。
1.等速万向节壳体锻件倒角成形
在筒形壳和三柱槽壳精锻件的机加工生产中,发现这些锻件车完倒角和端面以后的去除残留毛刺,是一个很难处理的技术问题(图8-5-1)。到目前为止,人们发明了许多去毛刺的设备和方法,最后还是觉得手工去毛刺最可靠。但是,在大批量生产时,往自动化生产线中插入几个手工操作的工序,无论是生产效率,还是保证作业质量,都不能使人满意。
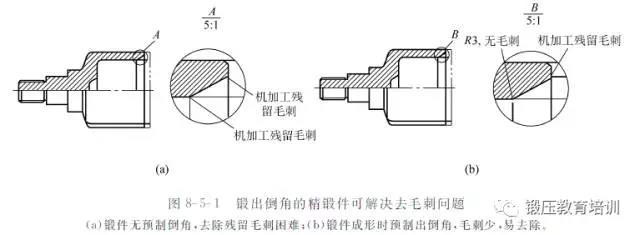
为了彻底解决这个技术难题,如在筒形壳和三柱槽壳温锻或冷精整时完成了倒角成形,这是一个可行的途径。对此,提出在三柱槽壳温锻时,最后增加一个倒角成形工步的方案。
但是,现有的3工位和4工位的温锻机上很难安排倒角成形工步。随着技术进步,5工位温锻压力机的出现解决了这个问题。图8-5-2为三柱槽壳5工位温锻的各个变形工步,在温锻的第5变形工步中完成了锻件倒角成形。在三柱槽壳温锻件杯口端部锻造成形了倒角,不但解决了毛刺问题,而且倒角尺寸的一致性也得到了提高。
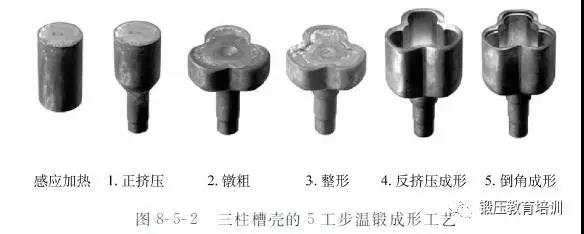
2.控制冷却在温锻生产中的应用
在等速万向节壳体的温锻成形生产中,锻后的退火或正火是一道关键工序。中碳钢温锻件进行退火或正火后,锻件组织和硬度、塑性等指标能充分满足后续机加工、冷滚轧花键和高频淬火的要求。
但退火或正火是一道生产周期长、能耗大的工序。一个退火周期往往要24h以上,而且需要配备无氧化退火设备。正火虽然时间周期较短,但无氧化的正火炉比无氧化的退火炉要求高得多,设备投资也大得多。显然,大能耗、长周期和间歇式的生产模式与当代汽车零部件低成本、高效率的生产目标则越来越不适应。
经研究发现,中碳钢的温锻加热温度只要满足材料基本奥氏体化,并且保持终锻温度在临界点以上,对锻后的温锻件降温速度进行适当的控制,能够使锻后锻件的组织、硬度、塑性等指标基本满足后续机加工、冷滚轧花键和高频淬火的要求。这种控制锻后锻件冷却来获得锻件预期组织的方法,被称为控制冷却。这种工艺最早应用在非调质钢的余热处理,现在已推广到中碳钢的温锻生产中。
经大量的试验和生产实践,得出中碳钢温锻件按图8-5-3的工艺曲线冷却后,能满足后续加工的需要。对此,先后开发了多种不同的控温冷却设备,来满足不同情况下控制冷却的要求。
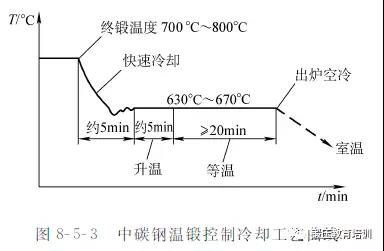
对于中小批量的手动温锻生产线,等速万向节温锻件每分种的产量为5件左右。由于单位时间内温锻件的数量少,热量的散失快,因此,温锻后控制冷却的设备是一条既有冷却风扇,又有补充加热器件的网带炉式控温冷却生产线。在生产线的各控制段,分别有控温装置根据实测温度来决定打开冷却风扇或加热器件,使温度控制在设定范围内。而冷却速度则由调速马达控制网带速度来调节。由于炉体是由保温材料构成,因此,该设备的加热功率只要能够补充锻件热量的散失,可见,控制冷却的能耗要比退火和正火大大减少。这样的一台控温生产线一般有近10m长,功率60kW~80kW,生产率为600kg/h左右。
在自动化多工位压力机组成的温锻自动生产线上,由于温锻件的生产率达到每分钟12件~22件,终锻件的温度高于手动温锻生产线,而且锻件自身热量远超过锻件散失的热量。这时,控温冷却生产线主要控制的是锻件的冷却速度,无需对锻件进行补充加热。所以,为温锻自动线配套的控制冷却生产线往往是一条带有冷却风扇的输送带,调节输送带的速度,并用人工或自动方式开关风扇来达到控温冷却的目的。
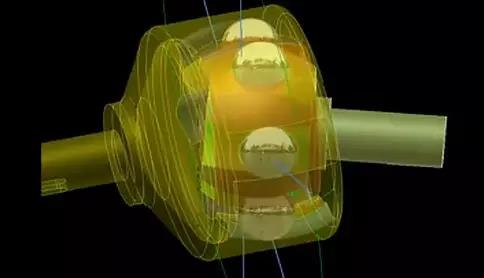
3.钟形壳锻件高速热镦工艺
近年来,随着汽车零部件集约化生产,传统的多工位热模锻和温锻生产效率已不能满足需要。在这种背景下,瑞士哈特贝尔公司推出了在高速热镦锻机上完成钟形壳热锻件的成形方案。
在高速热镦锻机上要完成钟形壳的成形并不是容易的事情。一开始,只有短柄和无柄的钟形壳能在高速热镦锻机上生产。后来,设备制造厂家开发出挤压型的高速热镦锻机,加强了凹模顶出机构的能力,加长了顶出长度,使之适应等速万向节杯杆类锻件的生产。这样的设备型号就是瑞士Hatebur-Hotmatic HM75挤压型高速热镦锻机(图8-5-4)。现在,钟形壳的高速自动热镦锻成形工艺已正式投产(图8-5-5),厂家正在积极研究将筒形壳和三柱槽壳锻件放到高速热镦锻机上生产。除瑞士哈特贝尔公司外,日本的阪村压力机公司也正在开发同样的项目。
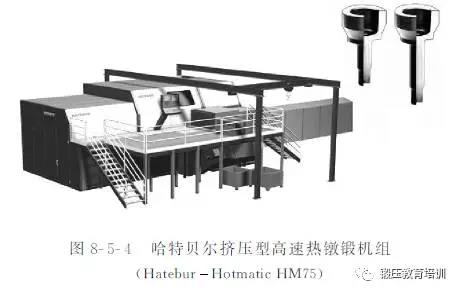
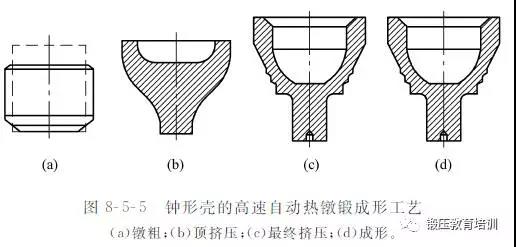
4.无磷化处理的冷精整工艺
(1)磷化、皂化处理对环境的影响
冷锻生产的磷化薄膜处理过程中,磷化液槽会产生令人讨厌的结渣现象。这种灰白色的渣层只要几天不去清理,就会在磷化槽壁和加热盘管上结成难以去除的坚硬的渣壳,不但影响加热管的热传导,而且并使槽的容积减少、槽液浑浊,影响磷化薄膜的质量。因此,磷化、皂化生产线上每天都要清扫出较多的含磷废渣。长期积累下去,大量高含磷量的废渣将无法妥善处理。
另外,磷化生产中清洗液一旦排放到河道沟渠中去,将造成河水的过度营养化,引起藻类或浮萍等水生植物的疯长,严重时造成大面积水面污染,致使水质变色、发臭、并放出有毒气味,影响人们的健康生活。因此,世界各国的环保部门对含磷废水的处理和排放都有严格的规定,对在生产中使用和排放含磷化合物的企业有严格的整治要求。由于含磷废弃物和含磷废水的处理成本高昂,使企业不得不尽量寻找避免使用含磷化合物的新工艺。
(2)无磷化处理的冷精整工艺
近年来由于环保的问题,有的企业正在推广应用无磷化的冷精整工艺,具体的做法是将温锻后的毛坯进行抛丸,然后喷淋冷镦油或拉深油进行润滑处理,再冷精整成形。这种方法避免了磷化处理过程对环境带来的严重污染,是应该大力推广的新工艺。但无磷化温锻件与模具间的摩擦较大,在冷精整成形过程中模具的发热和磨损比较严重,因此必需采用经TiC涂层的冷精整冲头和硬质合金制作的精整凹模,方能保证冷精整能正常进行。
在筒形壳和三柱槽壳精锻件的机加工生产中,发现这些锻件车完倒角和端面以后的去除残留毛刺,是一个很难处理的技术问题(图8-5-1)。到目前为止,人们发明了许多去毛刺的设备和方法,最后还是觉得手工去毛刺最可靠。但是,在大批量生产时,往自动化生产线中插入几个手工操作的工序,无论是生产效率,还是保证作业质量,都不能使人满意。
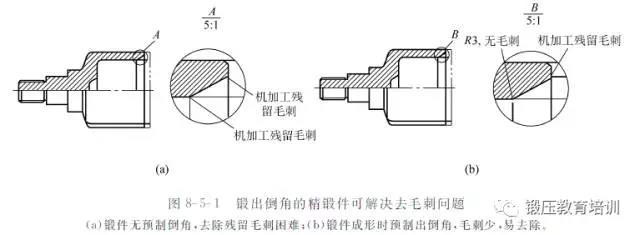
为了彻底解决这个技术难题,如在筒形壳和三柱槽壳温锻或冷精整时完成了倒角成形,这是一个可行的途径。对此,提出在三柱槽壳温锻时,最后增加一个倒角成形工步的方案。
但是,现有的3工位和4工位的温锻机上很难安排倒角成形工步。随着技术进步,5工位温锻压力机的出现解决了这个问题。图8-5-2为三柱槽壳5工位温锻的各个变形工步,在温锻的第5变形工步中完成了锻件倒角成形。在三柱槽壳温锻件杯口端部锻造成形了倒角,不但解决了毛刺问题,而且倒角尺寸的一致性也得到了提高。
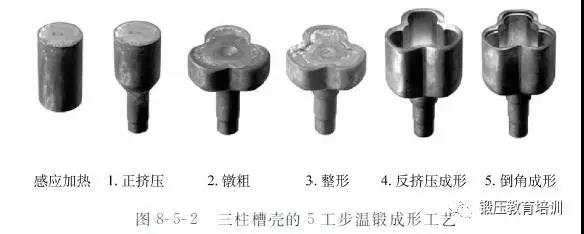
2.控制冷却在温锻生产中的应用
在等速万向节壳体的温锻成形生产中,锻后的退火或正火是一道关键工序。中碳钢温锻件进行退火或正火后,锻件组织和硬度、塑性等指标能充分满足后续机加工、冷滚轧花键和高频淬火的要求。
但退火或正火是一道生产周期长、能耗大的工序。一个退火周期往往要24h以上,而且需要配备无氧化退火设备。正火虽然时间周期较短,但无氧化的正火炉比无氧化的退火炉要求高得多,设备投资也大得多。显然,大能耗、长周期和间歇式的生产模式与当代汽车零部件低成本、高效率的生产目标则越来越不适应。
经研究发现,中碳钢的温锻加热温度只要满足材料基本奥氏体化,并且保持终锻温度在临界点以上,对锻后的温锻件降温速度进行适当的控制,能够使锻后锻件的组织、硬度、塑性等指标基本满足后续机加工、冷滚轧花键和高频淬火的要求。这种控制锻后锻件冷却来获得锻件预期组织的方法,被称为控制冷却。这种工艺最早应用在非调质钢的余热处理,现在已推广到中碳钢的温锻生产中。
经大量的试验和生产实践,得出中碳钢温锻件按图8-5-3的工艺曲线冷却后,能满足后续加工的需要。对此,先后开发了多种不同的控温冷却设备,来满足不同情况下控制冷却的要求。
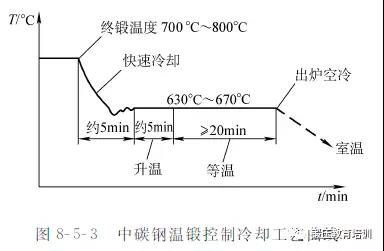
对于中小批量的手动温锻生产线,等速万向节温锻件每分种的产量为5件左右。由于单位时间内温锻件的数量少,热量的散失快,因此,温锻后控制冷却的设备是一条既有冷却风扇,又有补充加热器件的网带炉式控温冷却生产线。在生产线的各控制段,分别有控温装置根据实测温度来决定打开冷却风扇或加热器件,使温度控制在设定范围内。而冷却速度则由调速马达控制网带速度来调节。由于炉体是由保温材料构成,因此,该设备的加热功率只要能够补充锻件热量的散失,可见,控制冷却的能耗要比退火和正火大大减少。这样的一台控温生产线一般有近10m长,功率60kW~80kW,生产率为600kg/h左右。
在自动化多工位压力机组成的温锻自动生产线上,由于温锻件的生产率达到每分钟12件~22件,终锻件的温度高于手动温锻生产线,而且锻件自身热量远超过锻件散失的热量。这时,控温冷却生产线主要控制的是锻件的冷却速度,无需对锻件进行补充加热。所以,为温锻自动线配套的控制冷却生产线往往是一条带有冷却风扇的输送带,调节输送带的速度,并用人工或自动方式开关风扇来达到控温冷却的目的。
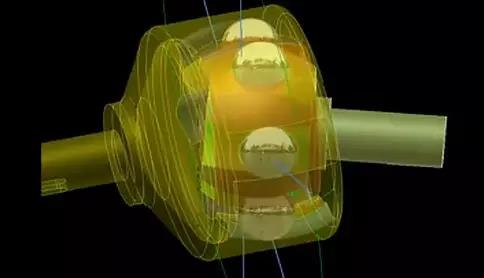
3.钟形壳锻件高速热镦工艺
近年来,随着汽车零部件集约化生产,传统的多工位热模锻和温锻生产效率已不能满足需要。在这种背景下,瑞士哈特贝尔公司推出了在高速热镦锻机上完成钟形壳热锻件的成形方案。
在高速热镦锻机上要完成钟形壳的成形并不是容易的事情。一开始,只有短柄和无柄的钟形壳能在高速热镦锻机上生产。后来,设备制造厂家开发出挤压型的高速热镦锻机,加强了凹模顶出机构的能力,加长了顶出长度,使之适应等速万向节杯杆类锻件的生产。这样的设备型号就是瑞士Hatebur-Hotmatic HM75挤压型高速热镦锻机(图8-5-4)。现在,钟形壳的高速自动热镦锻成形工艺已正式投产(图8-5-5),厂家正在积极研究将筒形壳和三柱槽壳锻件放到高速热镦锻机上生产。除瑞士哈特贝尔公司外,日本的阪村压力机公司也正在开发同样的项目。
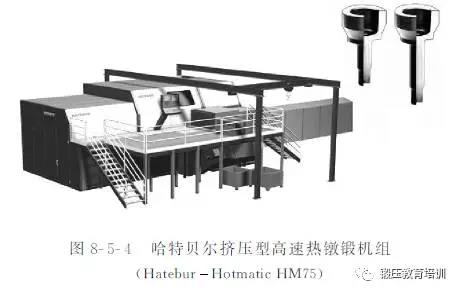
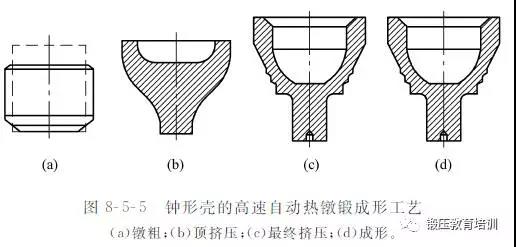
4.无磷化处理的冷精整工艺
(1)磷化、皂化处理对环境的影响
冷锻生产的磷化薄膜处理过程中,磷化液槽会产生令人讨厌的结渣现象。这种灰白色的渣层只要几天不去清理,就会在磷化槽壁和加热盘管上结成难以去除的坚硬的渣壳,不但影响加热管的热传导,而且并使槽的容积减少、槽液浑浊,影响磷化薄膜的质量。因此,磷化、皂化生产线上每天都要清扫出较多的含磷废渣。长期积累下去,大量高含磷量的废渣将无法妥善处理。
另外,磷化生产中清洗液一旦排放到河道沟渠中去,将造成河水的过度营养化,引起藻类或浮萍等水生植物的疯长,严重时造成大面积水面污染,致使水质变色、发臭、并放出有毒气味,影响人们的健康生活。因此,世界各国的环保部门对含磷废水的处理和排放都有严格的规定,对在生产中使用和排放含磷化合物的企业有严格的整治要求。由于含磷废弃物和含磷废水的处理成本高昂,使企业不得不尽量寻找避免使用含磷化合物的新工艺。
(2)无磷化处理的冷精整工艺
近年来由于环保的问题,有的企业正在推广应用无磷化的冷精整工艺,具体的做法是将温锻后的毛坯进行抛丸,然后喷淋冷镦油或拉深油进行润滑处理,再冷精整成形。这种方法避免了磷化处理过程对环境带来的严重污染,是应该大力推广的新工艺。但无磷化温锻件与模具间的摩擦较大,在冷精整成形过程中模具的发热和磨损比较严重,因此必需采用经TiC涂层的冷精整冲头和硬质合金制作的精整凹模,方能保证冷精整能正常进行。
- 下一篇:电池装配拧紧,面向新能源的技术升级
- 上一篇:埃马克期待与您相约CIMES 2018
最新资讯
-
展会预告 | 2025CIMT中国国际机床展
2025-04-11 14:44
-
航空发动机维修工装精准建模,3D扫描
2025-04-11 14:43
-
高歌猛进,奔赴“双碳”——比亚迪叉
2025-04-10 10:09
-
旭化成旗下旭塑洁螺杆清洗剂即将推出
2025-04-08 10:25
-
果栗智造磁悬浮技术赋能汽车制造:破
2025-04-03 19:27