汽车电驱系统小型化和轻量化现状及趋势
2018-06-11 12:13:32· 来源:NE时代/L
国内厂商对于汽车电动化的目光重点聚焦在动力电池系统上,而对于驱动系统市场主导权争夺的主要是国外的零部件大厂。本篇小编带大家一起关注同样潜力巨大的驱动系统电动化市场最新动态。
国内厂商对于汽车电动化的目光重点聚焦在动力电池系统上,而对于驱动系统市场主导权争夺的主要是国外的零部件大厂。本篇小编带大家一起关注同样潜力巨大的驱动系统电动化市场最新动态。
伴随汽车电动化的快速发展,影响电动汽车驾驶性能及成本的驱动系统预计也将进入飞速成长阶段,各种各样的公司展开了激烈的主导权斗争。从所谓的大型电器件供应商,到电机、逆变器等大型车载零部件制造商、以及提供功率器件和无源器件的领先设备制造商,各家企业都加强了新产品的开发、以及生产开发体制的强化。
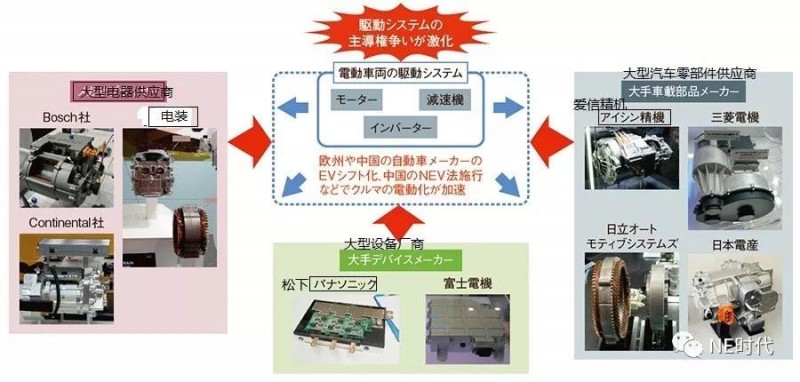
围绕驱动系统的开发竞争日益激烈。由于目前还没有掌握绝对主导权的零部件制造商,各种供应商鱼龙混杂,都加大了产品开发的投入力度。
1电驱动市场争夺战愈演愈烈
1.新的对手相继加入
竞争激化的表现就是新的对手不断加入。其中,最为气势凌人的是日本电产。
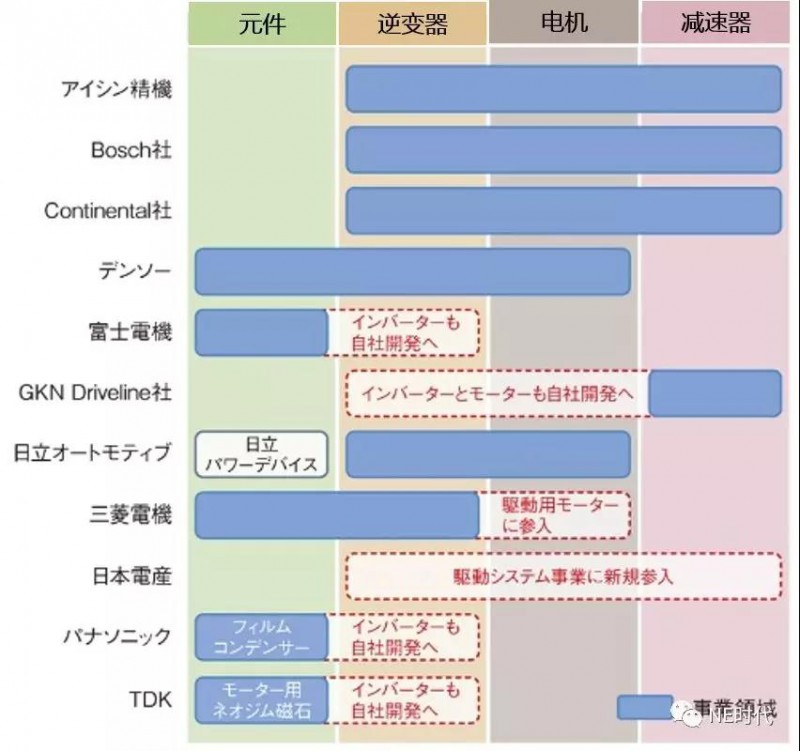
日本电产之前主要生产用于电动制动器的EPS电机,现在则开始商业化具有更高输出功率的驱动电机。未来还计划自产逆变器和减速器,进行一体化销售。到目前为止,在车载领域主营电动转向电机(EPS电机)、电动制动器用途的中小型电机、以及短距离运输用途的商用低速驱动电机。今后,则将全面进入驱动系统业务。该公司2017年9月发布的以小型轻量为主打的新产品‘E-Axle’就是这一信号的“先行官”。
2.上游元器件厂商进入下游供应链
驱动系统供应链“上游”侧的元器件制造商也正在进入“下游侧”的逆变器业务。例如,2016年TDK与东芝合作成立了开发,生产和销售逆变器的合资公司,预计2018年会正式开始产品的销售。
在汽车领域,TDK原本在电动机用钕磁铁和混合动力汽车DC-DC转换器中具有优势,再增加一个逆变器事业,期望由此强化其整个汽车电子关联业务。
此外,专攻逆变器所需功率器件的富士电机,掌握逆变器输入侧安装的平滑薄膜电容器绝大部分份额的松下等等公司,都加入到了逆变器的商业化竞争中。
3.随着“电动化市场“的飞速扩张,新的机会出现
根据英国调研公司IHS Market的预测,电动汽车将在2020年左右开始迅速增长,至2029年电动汽车将占到所有汽车出货量的一半左右。
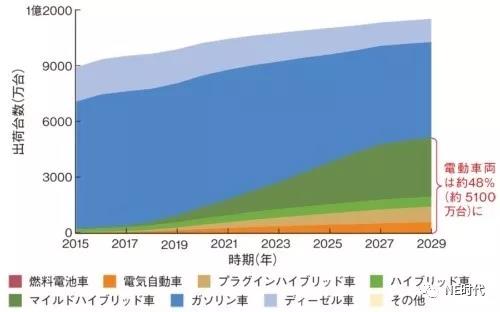
说到电动汽车电机,目前为止主流的汽车厂商针对HEV或者PHEV主要都是采取内部生产的体制。但是今后,随着电动汽车的增加,预计汽车厂商外部采购的需求会增加。例如,本田与日立汽车系统(日立AMS)在2017年7月联合组队,成立了开发,生产和销售电动汽车驱动电机的合资公司,预计面向数量巨大,降本要求强烈的普通价格段电动车辆电机,本田会首先考虑从这个新公司进行采购。
此外,中国市场从2018年开始将实施“NEV法规”,2019年开始对新能源汽车销售比例进行规定,由此可以预见未来驱动系统市场将会进一步大幅增长。
4.通过开发新产品或增加产能迎接竞争
由于大部分汽车厂商都自己生产驱动系统相关产品,所以目前没有市场份额相当大的厂家存在,包括大型零部件供应商在内的行业新加入者,几乎都处于同一起跑线上。因此,各家之前专攻电机、电频器、或减速机的厂家,都加入到了新产品开发与生产体制强化的运动中,以此迎接竞争。
例如,德国零部件供应商博世开发了一种集成了电机,逆变器和减速机的小型化驱动系统,利用该系统作为武器,博世有望使其驱动系统业务增长到10亿欧元(约合1300亿日元)的规模。
在汽车逆变器方面大有优势的三菱电机也已经开始增加生产设备,投资约70亿日元在姬路制造所広畑工厂内建设了新的厂房,新厂房不是单纯的增加电动汽车逆变器产能,而是强化包括了起动功能与发电功能的“电动发电机”的整体生产体制。
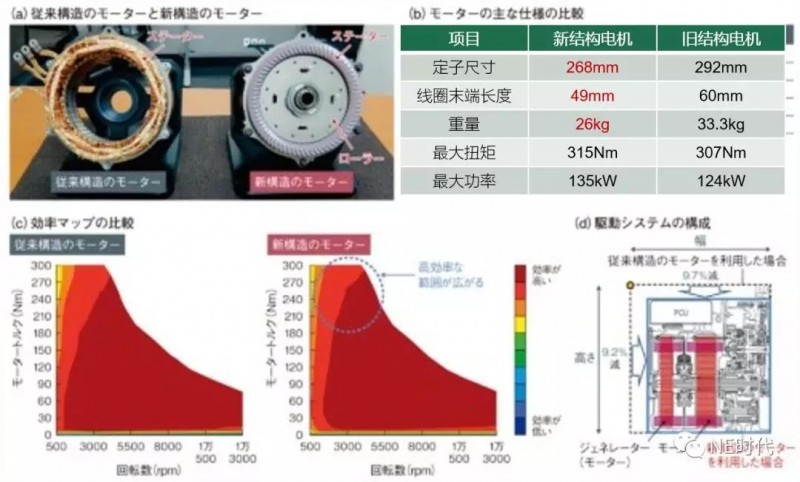
2体积更小,成本更低的驱动电机
围绕驱动系统的主要竞争主轴就是高效化,小型轻量化以及成本降低。许多制造商都试图通过整个驱动系统来实现这些目标,而不是依靠诸如电机、逆变器或减速器的单个单元。
2016年后本田混合动力车(HEV)上采用的全新结构驱动电机。与传统的驱动电机相比,在保持相同输出和扭矩的情况下,体积和重量分别减少了大约23%。因此,包括逆变器和减速器在内的i-MMD驱动系统的小型化成为可能。现行雅阁的HEV款中采用的2电机驱动系统(电机与发动机),与使用常规电机相比,高度缩减了9.2%,宽度缩减了9.7%。
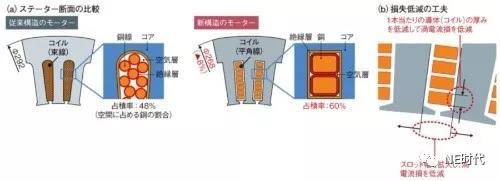
由于驱动系统变小,可以轻松地横向部署到更多车型上。而采用常规电机的驱动系统尺寸,能够横向部署的,以sedan车型为主,也就2~3款车型。
本田将以新型结构电机为标准,根据各个车型的要求稍作修改,从而应用到各种HEV车型上。通过批量生产结构大致相同的电机,从而降低零件的采购成本和制造成本。
1.增加线圈的占积率
为了实现电机小型化,本田增加了绕线的占积率(空间中铜的比例),使定子变小。通过使用大截面的方形导线作为线圈,使得占积率达到了60%。 在传统的电动机中,使用薄的圆形线圈,占积率一般只能达到48%。
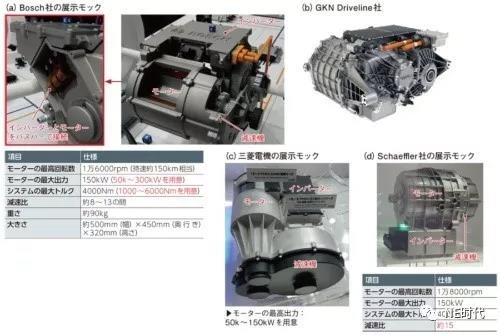
为了使定子小型化,线圈使用截面积大的方形导线(a)。与传统的圆形线圈相比,方形导线可使占积率从48%增加到60%。但是,由于和圆线相比方线变粗,导体(铜)中的“过电流损失”会增大。通常通过增大定子的槽宽度或减小每个线圈的厚度来减小过电流损耗(b)。
2.缩短线圈末端
为了实现小型化,本田同时还缩短了从定子突出的线圈部分(“线圈末端”)。本田技术人员认为线圈末端部分“对电机工作没有贡献”。
为了缩短线圈末端,采用了新的绕线结构方法。首先,将矩形线圈塑形成U字形,以形成“并列分割线圈”。接下来,将该分割线圈从定子铁心的轴方向插入。之后,将插入侧以及对侧伸出的线圈前端焊接在一起而形成线圈。
新的绕线工艺,需要投资新的制造设备。与传统工艺相比,新工艺不需要绳子捆绑,也不需要将线圈末端压扁,从而更易于自动化。由此实现高效率大批量生产,成本也能降低。基于对未来电动汽车需求大幅增长的预期,本田采取了这样的具备大批量生产优势的工艺。
3.采用低成本易采购的电磁钢板
还有一点创新就是考虑到驱动电机产量的增加,定子采用了低成本易采购的电磁钢板。一般来说,定子是通过堆叠多层薄磁钢片制成的。然而,薄的电磁钢片制造难度大且价格昂贵。为了降低成本,本田最终使用了比常规电机更厚的电磁钢板。传统产品的厚度为0.25mm,但本田采用的厚度为0.3mm,这个厚度流通量很大,不但便宜,而且易于采购。
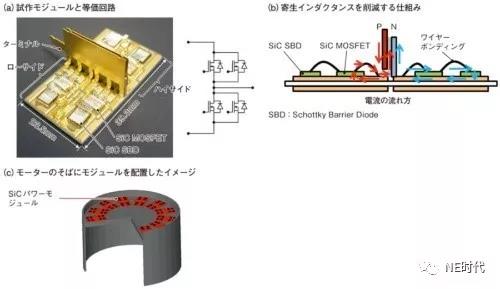
3小型化、轻量化趋势
近年,关于电动车辆驱动系统的一体化研究非常活跃,通过电机、逆变器,减速齿轮3个部件一体化,可以实现高效、小型和轻量化,同时降低成本。而将驱动系统安装在车轮内的轮毂电机,更是进一步推进了小型化和轻量化。
1.一体化实现小而高效
机电一体化活跃的原因在于可以实现驱动系统的小型轻量化以及降低成本,提高效率。如果是电机与逆变器一体,逆变器配置在电机旁边,连接电机与逆变器的线束就可以缩短或者置换。由此,减小了尺寸和重量,还降低了线束产生的损耗。又如果与减速箱一体,那齿轮的润滑油和电机的冷却油就可以共用,精简了冷却机构,可以轻松实现小型化。
例如,博世生产的电机、减速箱、逆变器三位一体的驱动系统,与传统驱动系统相比,体积得到了大幅减小。
三位一体的驱动系统方案不止一家,例如博世,GKN Driveline,三菱电机和舍弗勒。不仅实现了逆变器与电机之间的连接配线缩短,尺寸更小,还降低了连接部位的电力损耗,提升了驱动系统效率。
2.加入车载充电器功能
各家制造商为了使产品具备吸引力,在其展出的机电一体化驱动系统上,充分地利用自家所长,增加附加功能。
例如博世的三位一体驱动系统,电机的最大输出功率可达到50~300kw,电机与减速箱组合系统的最大扭矩可达到1000~6000Nm的宽广范围。
德国大陆集团,甚至还开发了一套具备充电功能的驱动系统,除了电机,减速箱与逆变器,还集成了充电电路。此电路由用于鉴别AC / DC的鉴别电路、电流路径的开关电路,噪音抑制电路等回路构成,利用此附加电路,与逆变器以及另行准备的DC-DC转换器,实现为车载二次电池充电。
3.增加减速比成为趋势
机械零件具备优势的厂商则是将减速器作为了强项。例如,舍弗勒(Schaeffler)公司,在三位一体的驱动系统中使用了减速比约为15的高速减速器。其他公司的减速器一般减速比约为10,即使高速也最多13左右。减速比越高,作为系统越容易提高转矩。因此,与减速比为10左右的驱动系统相比,能够在利用高速旋转的小型电动机的情况下获得相同的扭矩,也就是说,实现了小型化。
4.轮毂电机成为可见现实
驱动系统小型轻量化最前沿的技术就是轮毂电机(以下称IWM)成为可见现实。IWM有很多优点。例如,将发动机或电机的驱动力传输给到车轮的传输机构可以省略,使得驱动效率提升与车辆空间扩大成为可能。此外,还可以独立地精准控制4个车轮的控制力,由此可以防止车轮打滑和空转等,提高了安全性。同时还能抑制转弯时产生的倾斜滚动,或者突然加速或急刹时车体前后的摇晃,提高了舒适性。此外,还有一个优点是四轮驱动车容易追加产品系列。前轮驱动(FF),或后轮驱动(FR)的车辆上增加2个IWM的话,就可以小改动轻松实现四驱化。
5.通过SiC功率元件实现逆变器的小型化
将电机、减速箱,逆变器3个同时安装到车轮内的话,尺寸还是太大。即使将逆变器安装在车体侧的场合,逆变器的数量会随着电机数量的增加而增加,因此对小型化的需求还是强烈。而且本身驱动系统就存在小型化需求,所以需要逆变器尺寸能进一步减小。换句话说,逆变器的小型化是加速电动化的关键。
作为逆变器小型化的王牌集聚了汽车行业众多期待的产品就是SiC(碳化硅)功率器件。与现有车载逆变器中使用的Si功率器件相比,逆变器的功率损耗可以显著降低到一半一下。损耗减小,即发热量减少,由此可以减小逆变器尺寸。
能够发挥SiC功率器件优势的逆变器和驱动系统的相关研究和开发正在蓬勃发展。例如,芝浦工业大学电气工程学科专门研究电机技术与机电一体化技术的教授赤津観先生的研究团队,就试做了用于逆变器的小型SiC功率模块。
上述模块中,半桥电路由SiC MOSFET与SiC肖特基势垒二极管(Schottky Barrier Diode, 缩写成SBD)组成。SiC功率器件由于损耗小,适合小型化。
从事驱动系统开发的各厂家负责人纷纷发表意见“2020年之后量产的下一代产品将以SiC逆变器为前提去思考设计。如果能维持现有的SiC功率元件的降价步伐,则这一产品优势明显,是完全可以利用的”。
由此,可以预见2020年后,车载用途上大规模使用SiC功率器件,逆变器以及驱动系统的小型化将会不断推进吧。
伴随汽车电动化的快速发展,影响电动汽车驾驶性能及成本的驱动系统预计也将进入飞速成长阶段,各种各样的公司展开了激烈的主导权斗争。从所谓的大型电器件供应商,到电机、逆变器等大型车载零部件制造商、以及提供功率器件和无源器件的领先设备制造商,各家企业都加强了新产品的开发、以及生产开发体制的强化。
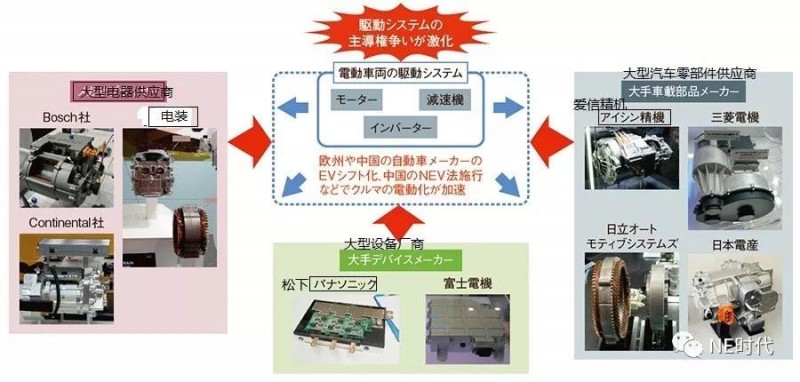
围绕驱动系统的开发竞争日益激烈。由于目前还没有掌握绝对主导权的零部件制造商,各种供应商鱼龙混杂,都加大了产品开发的投入力度。
1电驱动市场争夺战愈演愈烈
1.新的对手相继加入
竞争激化的表现就是新的对手不断加入。其中,最为气势凌人的是日本电产。
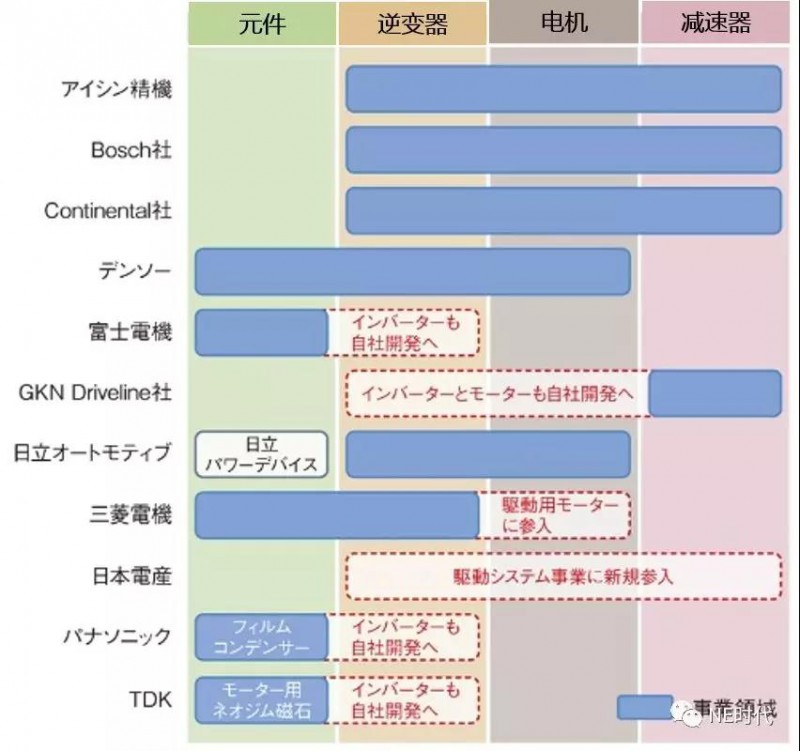
日本电产之前主要生产用于电动制动器的EPS电机,现在则开始商业化具有更高输出功率的驱动电机。未来还计划自产逆变器和减速器,进行一体化销售。到目前为止,在车载领域主营电动转向电机(EPS电机)、电动制动器用途的中小型电机、以及短距离运输用途的商用低速驱动电机。今后,则将全面进入驱动系统业务。该公司2017年9月发布的以小型轻量为主打的新产品‘E-Axle’就是这一信号的“先行官”。
2.上游元器件厂商进入下游供应链
驱动系统供应链“上游”侧的元器件制造商也正在进入“下游侧”的逆变器业务。例如,2016年TDK与东芝合作成立了开发,生产和销售逆变器的合资公司,预计2018年会正式开始产品的销售。
在汽车领域,TDK原本在电动机用钕磁铁和混合动力汽车DC-DC转换器中具有优势,再增加一个逆变器事业,期望由此强化其整个汽车电子关联业务。
此外,专攻逆变器所需功率器件的富士电机,掌握逆变器输入侧安装的平滑薄膜电容器绝大部分份额的松下等等公司,都加入到了逆变器的商业化竞争中。
3.随着“电动化市场“的飞速扩张,新的机会出现
根据英国调研公司IHS Market的预测,电动汽车将在2020年左右开始迅速增长,至2029年电动汽车将占到所有汽车出货量的一半左右。
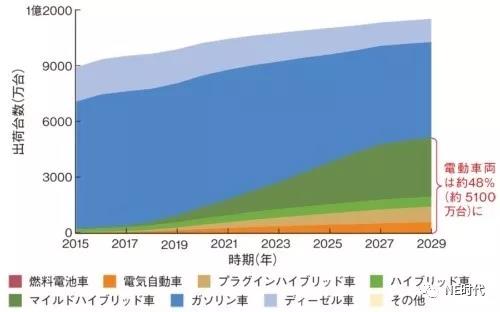
说到电动汽车电机,目前为止主流的汽车厂商针对HEV或者PHEV主要都是采取内部生产的体制。但是今后,随着电动汽车的增加,预计汽车厂商外部采购的需求会增加。例如,本田与日立汽车系统(日立AMS)在2017年7月联合组队,成立了开发,生产和销售电动汽车驱动电机的合资公司,预计面向数量巨大,降本要求强烈的普通价格段电动车辆电机,本田会首先考虑从这个新公司进行采购。
此外,中国市场从2018年开始将实施“NEV法规”,2019年开始对新能源汽车销售比例进行规定,由此可以预见未来驱动系统市场将会进一步大幅增长。
4.通过开发新产品或增加产能迎接竞争
由于大部分汽车厂商都自己生产驱动系统相关产品,所以目前没有市场份额相当大的厂家存在,包括大型零部件供应商在内的行业新加入者,几乎都处于同一起跑线上。因此,各家之前专攻电机、电频器、或减速机的厂家,都加入到了新产品开发与生产体制强化的运动中,以此迎接竞争。
例如,德国零部件供应商博世开发了一种集成了电机,逆变器和减速机的小型化驱动系统,利用该系统作为武器,博世有望使其驱动系统业务增长到10亿欧元(约合1300亿日元)的规模。
在汽车逆变器方面大有优势的三菱电机也已经开始增加生产设备,投资约70亿日元在姬路制造所広畑工厂内建设了新的厂房,新厂房不是单纯的增加电动汽车逆变器产能,而是强化包括了起动功能与发电功能的“电动发电机”的整体生产体制。
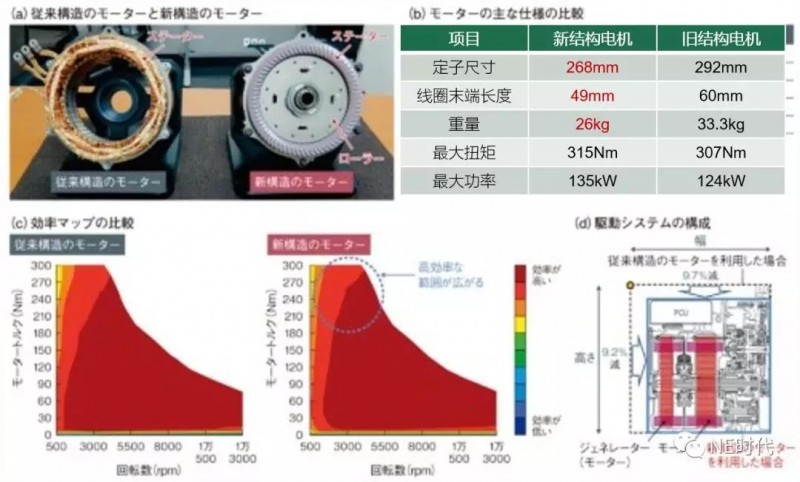
2体积更小,成本更低的驱动电机
围绕驱动系统的主要竞争主轴就是高效化,小型轻量化以及成本降低。许多制造商都试图通过整个驱动系统来实现这些目标,而不是依靠诸如电机、逆变器或减速器的单个单元。
2016年后本田混合动力车(HEV)上采用的全新结构驱动电机。与传统的驱动电机相比,在保持相同输出和扭矩的情况下,体积和重量分别减少了大约23%。因此,包括逆变器和减速器在内的i-MMD驱动系统的小型化成为可能。现行雅阁的HEV款中采用的2电机驱动系统(电机与发动机),与使用常规电机相比,高度缩减了9.2%,宽度缩减了9.7%。
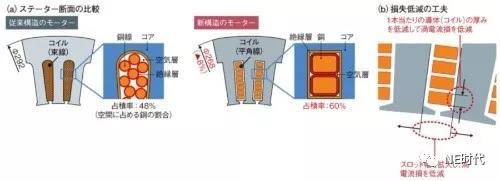
由于驱动系统变小,可以轻松地横向部署到更多车型上。而采用常规电机的驱动系统尺寸,能够横向部署的,以sedan车型为主,也就2~3款车型。
本田将以新型结构电机为标准,根据各个车型的要求稍作修改,从而应用到各种HEV车型上。通过批量生产结构大致相同的电机,从而降低零件的采购成本和制造成本。
1.增加线圈的占积率
为了实现电机小型化,本田增加了绕线的占积率(空间中铜的比例),使定子变小。通过使用大截面的方形导线作为线圈,使得占积率达到了60%。 在传统的电动机中,使用薄的圆形线圈,占积率一般只能达到48%。
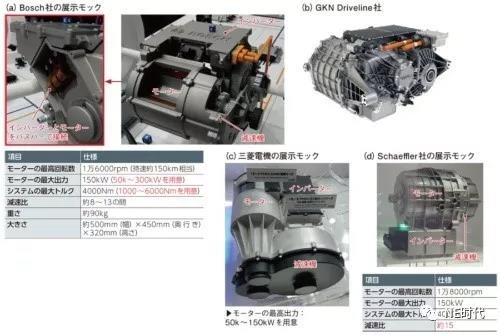
为了使定子小型化,线圈使用截面积大的方形导线(a)。与传统的圆形线圈相比,方形导线可使占积率从48%增加到60%。但是,由于和圆线相比方线变粗,导体(铜)中的“过电流损失”会增大。通常通过增大定子的槽宽度或减小每个线圈的厚度来减小过电流损耗(b)。
2.缩短线圈末端
为了实现小型化,本田同时还缩短了从定子突出的线圈部分(“线圈末端”)。本田技术人员认为线圈末端部分“对电机工作没有贡献”。
为了缩短线圈末端,采用了新的绕线结构方法。首先,将矩形线圈塑形成U字形,以形成“并列分割线圈”。接下来,将该分割线圈从定子铁心的轴方向插入。之后,将插入侧以及对侧伸出的线圈前端焊接在一起而形成线圈。
新的绕线工艺,需要投资新的制造设备。与传统工艺相比,新工艺不需要绳子捆绑,也不需要将线圈末端压扁,从而更易于自动化。由此实现高效率大批量生产,成本也能降低。基于对未来电动汽车需求大幅增长的预期,本田采取了这样的具备大批量生产优势的工艺。
3.采用低成本易采购的电磁钢板
还有一点创新就是考虑到驱动电机产量的增加,定子采用了低成本易采购的电磁钢板。一般来说,定子是通过堆叠多层薄磁钢片制成的。然而,薄的电磁钢片制造难度大且价格昂贵。为了降低成本,本田最终使用了比常规电机更厚的电磁钢板。传统产品的厚度为0.25mm,但本田采用的厚度为0.3mm,这个厚度流通量很大,不但便宜,而且易于采购。
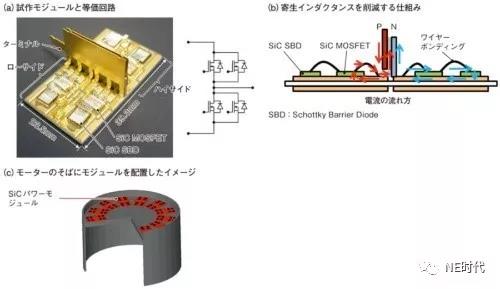
3小型化、轻量化趋势
近年,关于电动车辆驱动系统的一体化研究非常活跃,通过电机、逆变器,减速齿轮3个部件一体化,可以实现高效、小型和轻量化,同时降低成本。而将驱动系统安装在车轮内的轮毂电机,更是进一步推进了小型化和轻量化。
1.一体化实现小而高效
机电一体化活跃的原因在于可以实现驱动系统的小型轻量化以及降低成本,提高效率。如果是电机与逆变器一体,逆变器配置在电机旁边,连接电机与逆变器的线束就可以缩短或者置换。由此,减小了尺寸和重量,还降低了线束产生的损耗。又如果与减速箱一体,那齿轮的润滑油和电机的冷却油就可以共用,精简了冷却机构,可以轻松实现小型化。
例如,博世生产的电机、减速箱、逆变器三位一体的驱动系统,与传统驱动系统相比,体积得到了大幅减小。
三位一体的驱动系统方案不止一家,例如博世,GKN Driveline,三菱电机和舍弗勒。不仅实现了逆变器与电机之间的连接配线缩短,尺寸更小,还降低了连接部位的电力损耗,提升了驱动系统效率。
2.加入车载充电器功能
各家制造商为了使产品具备吸引力,在其展出的机电一体化驱动系统上,充分地利用自家所长,增加附加功能。
例如博世的三位一体驱动系统,电机的最大输出功率可达到50~300kw,电机与减速箱组合系统的最大扭矩可达到1000~6000Nm的宽广范围。
德国大陆集团,甚至还开发了一套具备充电功能的驱动系统,除了电机,减速箱与逆变器,还集成了充电电路。此电路由用于鉴别AC / DC的鉴别电路、电流路径的开关电路,噪音抑制电路等回路构成,利用此附加电路,与逆变器以及另行准备的DC-DC转换器,实现为车载二次电池充电。
3.增加减速比成为趋势
机械零件具备优势的厂商则是将减速器作为了强项。例如,舍弗勒(Schaeffler)公司,在三位一体的驱动系统中使用了减速比约为15的高速减速器。其他公司的减速器一般减速比约为10,即使高速也最多13左右。减速比越高,作为系统越容易提高转矩。因此,与减速比为10左右的驱动系统相比,能够在利用高速旋转的小型电动机的情况下获得相同的扭矩,也就是说,实现了小型化。
4.轮毂电机成为可见现实
驱动系统小型轻量化最前沿的技术就是轮毂电机(以下称IWM)成为可见现实。IWM有很多优点。例如,将发动机或电机的驱动力传输给到车轮的传输机构可以省略,使得驱动效率提升与车辆空间扩大成为可能。此外,还可以独立地精准控制4个车轮的控制力,由此可以防止车轮打滑和空转等,提高了安全性。同时还能抑制转弯时产生的倾斜滚动,或者突然加速或急刹时车体前后的摇晃,提高了舒适性。此外,还有一个优点是四轮驱动车容易追加产品系列。前轮驱动(FF),或后轮驱动(FR)的车辆上增加2个IWM的话,就可以小改动轻松实现四驱化。
5.通过SiC功率元件实现逆变器的小型化
将电机、减速箱,逆变器3个同时安装到车轮内的话,尺寸还是太大。即使将逆变器安装在车体侧的场合,逆变器的数量会随着电机数量的增加而增加,因此对小型化的需求还是强烈。而且本身驱动系统就存在小型化需求,所以需要逆变器尺寸能进一步减小。换句话说,逆变器的小型化是加速电动化的关键。
作为逆变器小型化的王牌集聚了汽车行业众多期待的产品就是SiC(碳化硅)功率器件。与现有车载逆变器中使用的Si功率器件相比,逆变器的功率损耗可以显著降低到一半一下。损耗减小,即发热量减少,由此可以减小逆变器尺寸。
能够发挥SiC功率器件优势的逆变器和驱动系统的相关研究和开发正在蓬勃发展。例如,芝浦工业大学电气工程学科专门研究电机技术与机电一体化技术的教授赤津観先生的研究团队,就试做了用于逆变器的小型SiC功率模块。
上述模块中,半桥电路由SiC MOSFET与SiC肖特基势垒二极管(Schottky Barrier Diode, 缩写成SBD)组成。SiC功率器件由于损耗小,适合小型化。
从事驱动系统开发的各厂家负责人纷纷发表意见“2020年之后量产的下一代产品将以SiC逆变器为前提去思考设计。如果能维持现有的SiC功率元件的降价步伐,则这一产品优势明显,是完全可以利用的”。
由此,可以预见2020年后,车载用途上大规模使用SiC功率器件,逆变器以及驱动系统的小型化将会不断推进吧。
编辑推荐
最新资讯
-
全球产业链聚沪 共探双碳新路径 SNEC
2025-04-18 18:05
-
柯马签订具有约束力的协议收购 Autom
2025-04-17 13:01
-
高效协同新范式:比亚迪叉车领创智能
2025-04-17 10:04
-
埃马克德国总部迎来中国社科院工业经
2025-04-15 09:40
-
埃马克这项全新应用即将在CIMT惊艳首
2025-04-15 09:37