车用复合材料新技术在汽车工业中的应用
2018-06-13 14:39:02· 来源:碳纤维研习社
随着科学技术的发展,具有轻质、高强度、耐腐蚀、易合成型等优点的非金属材料越来越多的取代传统的金属材料,在汽车上得到了应用。在汽车工业中非金属材料有塑料、橡胶、摩擦材料、涂料、胶黏剂、复合材料、玻璃、纺织材料、密封材料及润滑油等。其中汽车用复合材料在汽车工业中越来越得到广泛的重视和应用,而且有着一定的市场开发前景。
随着科学技术的发展,具有轻质、高强度、耐腐蚀、易合成型等优点的非金属材料越来越多的取代传统的金属材料,在汽车上得到了应用。在汽车工业中非金属材料有塑料、橡胶、摩擦材料、涂料、胶黏剂、复合材料、玻璃、纺织材料、密封材料及润滑油等。其中汽车用复合材料在汽车工业中越来越得到广泛的重视和应用,而且有着一定的市场开发前景。
车用复合材料的特点
一般称为复合材料的是由纤维等增强材料与基底(母体)等2种或2种以上性质不同的材料,通过各种工艺手段组合而成。它与纤维增强塑料(FRP)、纤维增强金属(FRM)、金属-塑料层叠材料等相当,具有质量轻、强度高、刚度好的特点,这些复合材料在汽车零部件上应用很盛行。
复合材料是并向异性的非均质材料,与其他材料相比有以下突出特点:
1)比强度与比模量高。比强度、比模量是指材料的强度和模量与密度之比,比强度越高,零件自重越小;比模量越高,零件的刚性越大。因此对高速运转的结构件或需减轻自重的运输工具具有重要意义。
2)纤维增强复合材料中的纤维与基体间的界面能够有效地阻止疲劳裂纹的扩展,外加载荷由增强纤维承担。大多数金属材料的疲劳强度极限是其拉伸强度的30%~50%,而复合材料则可达到60%~80%。
3)在热塑性塑料中掺入少量的短切碳纤维可大大地提高它的耐磨性,其增加的倍数可为原来的好几倍。如聚氯乙烯以碳纤维增强后为其本身的3.8倍,聚四氟乙烯为其本身的3倍;聚丙烯为其本身的2.5倍;聚酰胺为其本身的1.2倍;聚酯为其本身的2倍。选用适当塑料与钢板复合可作耐磨物件,如轴承材料等。用聚四氟乙烯(或聚甲醛)为表层、多孔青铜和钢板为里层的三层复合材料,可制成滑动轴承的良好材料。
4)化学稳定性优良。纤维增强酚醛塑料可长期在含氯离子的酸性介质中使用,用玻璃纤维增强塑料,可制造耐强酸、盐、酯和某些溶剂的化工管道、泵、阀及容器等设备。如用耐碱纤维与塑料复合,还能在强碱介质中使用。耐碱纤维可用来取代钢筋与水泥复合。
5)耐高温烧蚀性好。纤维增强复合材料中,除玻璃纤维软化点较低(700~900℃)外,其他纤维的熔点(或软化点)一般都在2000℃以上,用这些纤维与金属基体组成的复合材料,高温下强度和模量均有提高。例如:用碳纤维或硼纤维增强后,400℃时强度和模量基本可保持室温下水平。同样用碳纤维增强金属镍,不仅密度下降,而且高温性能也提高。由于玻璃钢具有极低的导热系数,可瞬时耐超高温,故可做耐烧蚀材料。
6)工艺性与可设计性好。调整增强材料的形状、排布及含量,可满足构件强度和刚度等性能要求,且材料与构件可一次成型,减少了零部件、紧固件和接头数目,材料利用率大大提高。
复合材料的功用和性能
复合材料与传统材料相比,具有比强度高、质量轻、比模量高、抗疲劳性能好及减振性能好等诸多优点。复合材料的各个组成材料在性能上起协同作用,具有单一材料无法比拟的优越综合性能。因此,在汽车工业中,复合材料被广泛应用于车身、灯壳罩、前后护板、保险杠、板弹簧、座椅架及驱动轴等部件的设计与制造。
在汽车工业中的复合材料设计应注意3个原则:1)比强度高和比刚度高;2)材料与环境相适应;3)性价比高。另外,在设计车身时,有一些经验方法,如:在应力高的区域适用碳纤维复合材料;在对韧性和刚度要求比较高的区域使用三合板复合材料;在几何形状复杂的区域可以使用层合板。
复合材料性能适合车身轻量化的要求,降低油耗。传统的汽车车身材料处于以薄钢板为主的单一状态,不能适应人们追求高速与轻量化的要求,为减轻其质量,改善风阻系数和降低油耗,许多汽车厂家都积极研究和利用新材料以达到上述要求。汽车自重减少50kg,1L燃油行驶距离可增加2Km;若自重减少10%,燃油经济性可提高约5.5%。许多类型的复合材料都在车身轻量化过程中得到了施展才能的舞台,并在汽车的轻量化进程中大显生手。汽车轻量化的目的就是节能和减轻排放污染。同时环境保护已成为可持续发展战略必不可少的条件,而复合材料的发展趋势正朝着延长使用期以及可再生的方向发展。
几种研发中的复合材料
1)碳纤维强化塑料(CFRP)。碳纤维由纤维和聚丙烯睛经高温加热处理制造而成,具有耐热性高,比重比铝和玻璃纤维还小,而且与塑料复合其强度可与钢和铝相匹敌。可是CFRP的成本与GFRP(玻璃纤维增强塑料)相比,远高很多,大多限于航空宇宙和体育用品范围内使用。
1979年,美国福特汽车公司发表了用GFRP制作轻型实验车的新构想(见图),其中使用CFRP约300kg,燃费约可降低35%。该实验车主要是将CFRP材料应用于车体面板,其他是传动轴和板弹簧等功能性零件,同时,还尝试在发动机机体和连杆、活塞等零部件上应用。CFRP材料质轻,刚度和强度也高,因材料的各向异性,设计时,可在所需的方向保持其强度和刚性。CFRP的弹性模量是GFRP的4~9倍,是金属材料的3~4倍。如果成批生产,成本将进一步下降,故而它将是一种期望很高的复合材料。
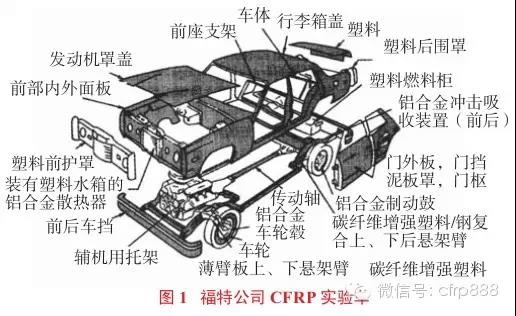
1979年,美国福特汽车公司发表了用GFRP制作轻型实验车的新构想
2)纤维增强金属(FRM)。CFRP与GFRP具有各种优越的机械性能,但其基底是塑料,与金属相比耐热性差。因此,作为高温强度材料使用的FRM的研究十分盛行,并且揭开了可将其在汽车上使用的可能性。增强纤维有:碳元素、碳化硅、硼、氧化铝等。基底,开始有铝、铜及镍,后又有与各种目的相适应的钛、镁、锌及锡等。增强纤维与各种金属相结合,将制造出各种特性的FRM。现正进行将FRM应用于活塞、连杆及其他一些滑动零件的研究。因这种纤维价格高,以及还未达到成批生产的规模,它作为高温强度好的材料,其利用价值是相当高的。
3)金属-塑料层辑材料。将高强度钢板和铝、塑料等紧密结合在一起的材料是种理想的轻型材料,也是种夹层结构的层叠材料。由于它是在塑料芯的两面粘结上薄钢板或铝板,具自优越的隔热和隔音性能。层叠材料,它叫发挥与钢板相匹敌的刚性好的特点,它由塑料芯两面的金属板承受弯曲应力,由塑料芯材承受剪切应力。在同样刚性下,层叠钢板与一般钢板相比,质量是其30%~-70%, 如果对于层叠板质量有一定限制要求时,可由改变芯两面的金属板与芯板的厚度等来解决。层叠材料的成本一般是钢板的1~3倍,但它还存在一些需要解决的问题,如:使用在车体面板时,与各面板如何粘结拼合;在其表面金属钢板锈蚀时,刚性会降低等。然而随着层叠材料研究开发的进步,使它实用化将有很大的可能性。
4)车用玻璃纤维增强复合材料。由于增强材料和填充材料品种繁多,因此将使用玻纤当做增强材料的材料称为GFRR。由于玻纤的加入大大地改善了塑料的物理机械性能,通过塑料经过增强后,也能作为工程材料应用。目前汽车上使用的玻纤增强塑料主要有玻纤增强PP、玻纤增强PA66或PA6以及少量PBT和PPO材料。汽车上应用的玻璃纤维增强复合材料包括玻璃纤维增强热塑性材料、玻璃纤维毡增强热塑性材料(GMT)、片状模塑材料(SMC)、树脂传递模塑材料(RTM)以及手糊FRP制品。
增强PP主要用于制作发动机冷却风扇叶片和正时齿带上下罩盖等制品,但有些制品存在外观质量不好、翘曲等缺欠,因此非功能件逐渐被滑石粉添充PP所替代。增强PA材料在轿车、厢式车及载货车上都已采用,一般都是用于制作些小的功能件,例如:锁体防护罩、保险楔块、嵌装螺母、油门踏板、换挡上下护架-防护罩和开启手柄等。GMT是目前国际上极为活跃的复合材料开发品种,这是种以热塑性树脂为基体,以玻璃纤维毡为增强骨架的新颖、节能及轻质的复合材料,一般可以生产出片材半成品,然后直接加工成所需形状的产品,纤维可以是短切玻璃纤维或连续的玻璃纤维毡。
SMC是一种较重要且用途广的模压复合材料制品的半成品。与钢制汽车零件相比,SC生产周期短,便于汽车改型,投资效益好;质量较轻,节约燃油;设计自由;制件的整体性好,零件的数量很少;耐用性和隔热性好。但是SMC不可以回收,污染环境;虽然性能价格比较好,但一次性投资往往高于对应的钢制件,如福特金牛座和水星黑貂轿车前围里的下散热器托架,原钢制的有22个零件,而SMC的只有2件,质量大减,成本降低14%。
尽管许多汽车厂在生产汽车车身时都已改用由玻璃纤维为增强的材料来替代相对笨重的金属,但是玻璃纤维是由熔融玻璃拉成的纤维,它在高温融化后非常容易重新凝固,这给废旧汽车回收处理带来了很大困难。为此,法国国家科学研究中心正在研究一种以大麻和聚氨酯为原料的合成材料,这种材料的特点是除具有金属和玻璃纤维各有的优点外,价格更便宜,质量更轻,韧度更强,而且叫以生物降解。现在,该中心正在对这种材料的强度及其他特性进行测试,一期目标是用这种材料生产出汽车车门。
金属基复合材料(MMC)在汽车工业中的应用
MMC用于汽车工业主要是颗粒增强和短纤维增强的铝基复合材料。MMC具有高的比强度和比刚度、耐磨性好、导热性好及热膨胀系数低等特性,已在工业中得到了较为广泛的应用。应用于汽车工业的MMC为铝或镁基质加粉末或碎屑纤维增强。在汽车制动盘、制动鼓、制动钳、活塞、传动轴以及轮胎螺栓上,采用MMC制造。
目前,铝基复合材料一般采用铝硅合金。常用的填充增强剂有陶瓷纤维和微粒等。它与铝合金相比具有质量轻、比强度高和弹性模量高、耐热性和耐磨性好等优点,是汽车轻量化的理想材料。
活塞是发动机的主要零件之,它在高温高压下工作,因而选合适的活塞材料是至关重要的。目前,应用于活塞的复合材料由低密度金属和增强陶瓷纤维组成,主要用于高性能铝活塞。近年来,有所发展的是纤维增强金属(FRM),铝合金基FRM具有抗拉强度高和耐磨耐热特性。纤维增强的轻金属能用于仅靠轻合金不能满足强度和耐磨性的部位上,是很有发展前途的材料。在此基础上,围外又推出了氧化铝纤维增强活塞顶的铝活塞及氧化铝增强的镁合金制造的活塞等,进一步扩大了它在活塞上的应用。
美国已将铝基复合材料应用于刹车轮。其特点是铝基复合材料使质量减轻了30%~60%,导热性好,最高使用温度叫达到450℃,其热性能己达到原先使用的铸铁水平。MMC必须用新的方法制造,限制应用的原理是是必须研制匹配的制动踏板。制动钳采用金属基复合材料制造时,除了降低质量外,最主要的益处是刚度。MMC制动钳应用于高性能体育赛车上,由于高成本而限制了其大量应用。MMC活塞主要用于柴油机上,但也可用于汽油发动机。因氧化铝和氧化硅短纤维增强,但是热疲劳易导致断裂。采用陶瓷纤维预型坯可弱化这一问题,提高活塞寿命。
轮胎螺栓采用MMC制造,质量减轻50%。2000年世界汽车工业对金属基复合材料的用量达到0.6万t。随着复合材料制备技术、性能的不断提高,以及价格的日益下降,MMC必将在汽午上得到越来越广泛的应用。
复合材料在车身 悬架系统上的应用
20世纪60年代以后,由于复合材料的深入研究,比如玻璃纤维增强材料、碳纤维增强材料及高弹性基体复合材料的出现,使大幅度降低整车质量成为可能。其中,玻璃纤维增强材料被较多的采用,原因是虽然碳纤维增强复合材料力学性质稳定,然而其价格昂贵,从经济性考虑,尽量多的使用玻璃纤维增强材料是一条设计准则。
在最近几年的车身制造业中,许多汽车公司开始大量使用一种叫SMC钣金复合成型的复合材料,低密度SMC的密度只有1.3g/cm3,而它的热膨胀系数却与钢铁一样,同时,它在耐腐蚀、抗损伤以及声学性质上均优于钢铁。比如雪弗兰的车型C5卡福特的金属车顶,自1999年出产以后,取得了巨大的商业成功。这个长140 cm,宽1.47 cm,顶部厚度0.168 cm,内板厚0.178 cm的框架顶部是普通SMC,侧面及内板由低密度SMC构成,它仅重10.5 kg。然而,SMC也有缺点,它的价格比较昂贵,同时在抗磨损的性能上比不上碳纤维复合材料。另外,高温时,会部分丧失承载能力。针对这些弱点,许多新型的SMC被开发出来,其中,SMC3374是 一种较典型的材料,它的密度仍然维持在1.3 g/cm3左右,然而它在93.3℃能够保持住75%的力学性能,与原来的SMC只能在65.5℃保持有了明显的提高。因此,在2001奥德汽车极光,庞帝阿克-邦奈威勒2000以及2000别克-萨罗上,都采用了SMC3374材料。
从以上的分析不难看出,SMC仅适用于制造车身上温度不高且承受的载荷不大的区域,比如顶部和侧面。而底部以及高温区域,就需要能够抗高温和耐高压的复合材料了。
戴尔福公司在1981年生产出第一个采用复合材料小弯曲的板掸簧。小弯曲材料有很高的刚度,也就是说,在很大的压力下,它的应变却可以保持在很小的范围内,同时它的密度很小,只有钢材的50%~70%,因此,小弯曲材料的承载与自身质量之比是钢材的5倍。另外,实验数据显示,它比钢材要坚硬3.5倍。这些优点都是由材料性能直接带来的,除此之外,复合材料板掸簧要比钢板弹簧的结构简单得多,很容易装配,维修以及采取防腐措施。而且,由于它比钢板弹簧小得多的厚度,使它叫以更接近地面,从而节省了汽车的有效空间。必要时,更可以用来降低汽车的底盘,提高汽车的舒适性能。
高温下材料的性能,一直是材料选择的因素。测试结果显示,车下板弹簧处的温度最高可以达到130℃,小弯曲材料在这个温度下性能是稳定的。正是基于以上的诸多优点,小弯曲材料被广泛应用于制造汽车的板弹簧,从轿车到轻型货午,甚至重型商业运输车都采用了这种板掸簧。
复合材料与未来汽车
未来的汽车是属于适应环境保护的绿色汽车,因而在此不可避免的要提到复合材料的环保意识。复合材料能提高材料性能,延长使用期,加强功能性,这些都是对环境有利的特性。但应认真对待并努力克服复合材料的再生问题,使复合材料朝着环境协调化的方向发展。
复合材料零件的再生利用是非常难的事,会对环境产生些不利的影响。如目前发展最快、应用最高的聚合物基复合材料中绝大多数属易燃物,燃烧时会放出大量有毒气体,污染环境;且在成型时,基体中的挥发成分即溶剂会扩散到空气中,造成污染。复合材料使用本身就是多种组分材料构成,属多相材料,难以粉碎、磨细、熔融及降解,复合零件首先分解成单一材料的零件,然而这种分解工艺成本和再生成本较高,而且要使其恢复原有性能十分困难。因此再生利用的主要条件之一是零件容易拆卸,尽可能是单一品种材料,即便是复合材料也要尽量使用复合性少的材料。基于上述原则上的考虑,热塑性聚烯烃弹性体、聚丙烯发泡材料及GMT增强板材的应用量还会大幅度增加,相反热固性树脂的用量将受到限制。目前在再生性和降解性方面的研究工作已经取得了很大的进展。当今社会,人们目光的角度逐渐转到人与自然的关系问题上,环境与能源问题成为世界上每个国家能否生存和发展的关键。随着人们环保意识的不断提高以及符合环保法规的相继出台,绿色汽车已经成为未来汽车发展的必然趋势,因而如何使汽车满足环境保护的要求,便提到了汽车厂商们的议事日程。而复合材料作为末来汽车材料发展的主流,必将在其中扮演非常重要的角色。
车用复合材料的特点
一般称为复合材料的是由纤维等增强材料与基底(母体)等2种或2种以上性质不同的材料,通过各种工艺手段组合而成。它与纤维增强塑料(FRP)、纤维增强金属(FRM)、金属-塑料层叠材料等相当,具有质量轻、强度高、刚度好的特点,这些复合材料在汽车零部件上应用很盛行。
复合材料是并向异性的非均质材料,与其他材料相比有以下突出特点:
1)比强度与比模量高。比强度、比模量是指材料的强度和模量与密度之比,比强度越高,零件自重越小;比模量越高,零件的刚性越大。因此对高速运转的结构件或需减轻自重的运输工具具有重要意义。
2)纤维增强复合材料中的纤维与基体间的界面能够有效地阻止疲劳裂纹的扩展,外加载荷由增强纤维承担。大多数金属材料的疲劳强度极限是其拉伸强度的30%~50%,而复合材料则可达到60%~80%。
3)在热塑性塑料中掺入少量的短切碳纤维可大大地提高它的耐磨性,其增加的倍数可为原来的好几倍。如聚氯乙烯以碳纤维增强后为其本身的3.8倍,聚四氟乙烯为其本身的3倍;聚丙烯为其本身的2.5倍;聚酰胺为其本身的1.2倍;聚酯为其本身的2倍。选用适当塑料与钢板复合可作耐磨物件,如轴承材料等。用聚四氟乙烯(或聚甲醛)为表层、多孔青铜和钢板为里层的三层复合材料,可制成滑动轴承的良好材料。
4)化学稳定性优良。纤维增强酚醛塑料可长期在含氯离子的酸性介质中使用,用玻璃纤维增强塑料,可制造耐强酸、盐、酯和某些溶剂的化工管道、泵、阀及容器等设备。如用耐碱纤维与塑料复合,还能在强碱介质中使用。耐碱纤维可用来取代钢筋与水泥复合。
5)耐高温烧蚀性好。纤维增强复合材料中,除玻璃纤维软化点较低(700~900℃)外,其他纤维的熔点(或软化点)一般都在2000℃以上,用这些纤维与金属基体组成的复合材料,高温下强度和模量均有提高。例如:用碳纤维或硼纤维增强后,400℃时强度和模量基本可保持室温下水平。同样用碳纤维增强金属镍,不仅密度下降,而且高温性能也提高。由于玻璃钢具有极低的导热系数,可瞬时耐超高温,故可做耐烧蚀材料。
6)工艺性与可设计性好。调整增强材料的形状、排布及含量,可满足构件强度和刚度等性能要求,且材料与构件可一次成型,减少了零部件、紧固件和接头数目,材料利用率大大提高。
复合材料的功用和性能
复合材料与传统材料相比,具有比强度高、质量轻、比模量高、抗疲劳性能好及减振性能好等诸多优点。复合材料的各个组成材料在性能上起协同作用,具有单一材料无法比拟的优越综合性能。因此,在汽车工业中,复合材料被广泛应用于车身、灯壳罩、前后护板、保险杠、板弹簧、座椅架及驱动轴等部件的设计与制造。
在汽车工业中的复合材料设计应注意3个原则:1)比强度高和比刚度高;2)材料与环境相适应;3)性价比高。另外,在设计车身时,有一些经验方法,如:在应力高的区域适用碳纤维复合材料;在对韧性和刚度要求比较高的区域使用三合板复合材料;在几何形状复杂的区域可以使用层合板。
复合材料性能适合车身轻量化的要求,降低油耗。传统的汽车车身材料处于以薄钢板为主的单一状态,不能适应人们追求高速与轻量化的要求,为减轻其质量,改善风阻系数和降低油耗,许多汽车厂家都积极研究和利用新材料以达到上述要求。汽车自重减少50kg,1L燃油行驶距离可增加2Km;若自重减少10%,燃油经济性可提高约5.5%。许多类型的复合材料都在车身轻量化过程中得到了施展才能的舞台,并在汽车的轻量化进程中大显生手。汽车轻量化的目的就是节能和减轻排放污染。同时环境保护已成为可持续发展战略必不可少的条件,而复合材料的发展趋势正朝着延长使用期以及可再生的方向发展。
几种研发中的复合材料
1)碳纤维强化塑料(CFRP)。碳纤维由纤维和聚丙烯睛经高温加热处理制造而成,具有耐热性高,比重比铝和玻璃纤维还小,而且与塑料复合其强度可与钢和铝相匹敌。可是CFRP的成本与GFRP(玻璃纤维增强塑料)相比,远高很多,大多限于航空宇宙和体育用品范围内使用。
1979年,美国福特汽车公司发表了用GFRP制作轻型实验车的新构想(见图),其中使用CFRP约300kg,燃费约可降低35%。该实验车主要是将CFRP材料应用于车体面板,其他是传动轴和板弹簧等功能性零件,同时,还尝试在发动机机体和连杆、活塞等零部件上应用。CFRP材料质轻,刚度和强度也高,因材料的各向异性,设计时,可在所需的方向保持其强度和刚性。CFRP的弹性模量是GFRP的4~9倍,是金属材料的3~4倍。如果成批生产,成本将进一步下降,故而它将是一种期望很高的复合材料。
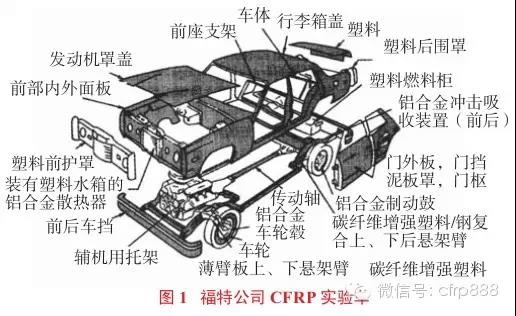
1979年,美国福特汽车公司发表了用GFRP制作轻型实验车的新构想
2)纤维增强金属(FRM)。CFRP与GFRP具有各种优越的机械性能,但其基底是塑料,与金属相比耐热性差。因此,作为高温强度材料使用的FRM的研究十分盛行,并且揭开了可将其在汽车上使用的可能性。增强纤维有:碳元素、碳化硅、硼、氧化铝等。基底,开始有铝、铜及镍,后又有与各种目的相适应的钛、镁、锌及锡等。增强纤维与各种金属相结合,将制造出各种特性的FRM。现正进行将FRM应用于活塞、连杆及其他一些滑动零件的研究。因这种纤维价格高,以及还未达到成批生产的规模,它作为高温强度好的材料,其利用价值是相当高的。
3)金属-塑料层辑材料。将高强度钢板和铝、塑料等紧密结合在一起的材料是种理想的轻型材料,也是种夹层结构的层叠材料。由于它是在塑料芯的两面粘结上薄钢板或铝板,具自优越的隔热和隔音性能。层叠材料,它叫发挥与钢板相匹敌的刚性好的特点,它由塑料芯两面的金属板承受弯曲应力,由塑料芯材承受剪切应力。在同样刚性下,层叠钢板与一般钢板相比,质量是其30%~-70%, 如果对于层叠板质量有一定限制要求时,可由改变芯两面的金属板与芯板的厚度等来解决。层叠材料的成本一般是钢板的1~3倍,但它还存在一些需要解决的问题,如:使用在车体面板时,与各面板如何粘结拼合;在其表面金属钢板锈蚀时,刚性会降低等。然而随着层叠材料研究开发的进步,使它实用化将有很大的可能性。
4)车用玻璃纤维增强复合材料。由于增强材料和填充材料品种繁多,因此将使用玻纤当做增强材料的材料称为GFRR。由于玻纤的加入大大地改善了塑料的物理机械性能,通过塑料经过增强后,也能作为工程材料应用。目前汽车上使用的玻纤增强塑料主要有玻纤增强PP、玻纤增强PA66或PA6以及少量PBT和PPO材料。汽车上应用的玻璃纤维增强复合材料包括玻璃纤维增强热塑性材料、玻璃纤维毡增强热塑性材料(GMT)、片状模塑材料(SMC)、树脂传递模塑材料(RTM)以及手糊FRP制品。
增强PP主要用于制作发动机冷却风扇叶片和正时齿带上下罩盖等制品,但有些制品存在外观质量不好、翘曲等缺欠,因此非功能件逐渐被滑石粉添充PP所替代。增强PA材料在轿车、厢式车及载货车上都已采用,一般都是用于制作些小的功能件,例如:锁体防护罩、保险楔块、嵌装螺母、油门踏板、换挡上下护架-防护罩和开启手柄等。GMT是目前国际上极为活跃的复合材料开发品种,这是种以热塑性树脂为基体,以玻璃纤维毡为增强骨架的新颖、节能及轻质的复合材料,一般可以生产出片材半成品,然后直接加工成所需形状的产品,纤维可以是短切玻璃纤维或连续的玻璃纤维毡。
SMC是一种较重要且用途广的模压复合材料制品的半成品。与钢制汽车零件相比,SC生产周期短,便于汽车改型,投资效益好;质量较轻,节约燃油;设计自由;制件的整体性好,零件的数量很少;耐用性和隔热性好。但是SMC不可以回收,污染环境;虽然性能价格比较好,但一次性投资往往高于对应的钢制件,如福特金牛座和水星黑貂轿车前围里的下散热器托架,原钢制的有22个零件,而SMC的只有2件,质量大减,成本降低14%。
尽管许多汽车厂在生产汽车车身时都已改用由玻璃纤维为增强的材料来替代相对笨重的金属,但是玻璃纤维是由熔融玻璃拉成的纤维,它在高温融化后非常容易重新凝固,这给废旧汽车回收处理带来了很大困难。为此,法国国家科学研究中心正在研究一种以大麻和聚氨酯为原料的合成材料,这种材料的特点是除具有金属和玻璃纤维各有的优点外,价格更便宜,质量更轻,韧度更强,而且叫以生物降解。现在,该中心正在对这种材料的强度及其他特性进行测试,一期目标是用这种材料生产出汽车车门。
金属基复合材料(MMC)在汽车工业中的应用
MMC用于汽车工业主要是颗粒增强和短纤维增强的铝基复合材料。MMC具有高的比强度和比刚度、耐磨性好、导热性好及热膨胀系数低等特性,已在工业中得到了较为广泛的应用。应用于汽车工业的MMC为铝或镁基质加粉末或碎屑纤维增强。在汽车制动盘、制动鼓、制动钳、活塞、传动轴以及轮胎螺栓上,采用MMC制造。
目前,铝基复合材料一般采用铝硅合金。常用的填充增强剂有陶瓷纤维和微粒等。它与铝合金相比具有质量轻、比强度高和弹性模量高、耐热性和耐磨性好等优点,是汽车轻量化的理想材料。
活塞是发动机的主要零件之,它在高温高压下工作,因而选合适的活塞材料是至关重要的。目前,应用于活塞的复合材料由低密度金属和增强陶瓷纤维组成,主要用于高性能铝活塞。近年来,有所发展的是纤维增强金属(FRM),铝合金基FRM具有抗拉强度高和耐磨耐热特性。纤维增强的轻金属能用于仅靠轻合金不能满足强度和耐磨性的部位上,是很有发展前途的材料。在此基础上,围外又推出了氧化铝纤维增强活塞顶的铝活塞及氧化铝增强的镁合金制造的活塞等,进一步扩大了它在活塞上的应用。
美国已将铝基复合材料应用于刹车轮。其特点是铝基复合材料使质量减轻了30%~60%,导热性好,最高使用温度叫达到450℃,其热性能己达到原先使用的铸铁水平。MMC必须用新的方法制造,限制应用的原理是是必须研制匹配的制动踏板。制动钳采用金属基复合材料制造时,除了降低质量外,最主要的益处是刚度。MMC制动钳应用于高性能体育赛车上,由于高成本而限制了其大量应用。MMC活塞主要用于柴油机上,但也可用于汽油发动机。因氧化铝和氧化硅短纤维增强,但是热疲劳易导致断裂。采用陶瓷纤维预型坯可弱化这一问题,提高活塞寿命。
轮胎螺栓采用MMC制造,质量减轻50%。2000年世界汽车工业对金属基复合材料的用量达到0.6万t。随着复合材料制备技术、性能的不断提高,以及价格的日益下降,MMC必将在汽午上得到越来越广泛的应用。
复合材料在车身 悬架系统上的应用
20世纪60年代以后,由于复合材料的深入研究,比如玻璃纤维增强材料、碳纤维增强材料及高弹性基体复合材料的出现,使大幅度降低整车质量成为可能。其中,玻璃纤维增强材料被较多的采用,原因是虽然碳纤维增强复合材料力学性质稳定,然而其价格昂贵,从经济性考虑,尽量多的使用玻璃纤维增强材料是一条设计准则。
在最近几年的车身制造业中,许多汽车公司开始大量使用一种叫SMC钣金复合成型的复合材料,低密度SMC的密度只有1.3g/cm3,而它的热膨胀系数却与钢铁一样,同时,它在耐腐蚀、抗损伤以及声学性质上均优于钢铁。比如雪弗兰的车型C5卡福特的金属车顶,自1999年出产以后,取得了巨大的商业成功。这个长140 cm,宽1.47 cm,顶部厚度0.168 cm,内板厚0.178 cm的框架顶部是普通SMC,侧面及内板由低密度SMC构成,它仅重10.5 kg。然而,SMC也有缺点,它的价格比较昂贵,同时在抗磨损的性能上比不上碳纤维复合材料。另外,高温时,会部分丧失承载能力。针对这些弱点,许多新型的SMC被开发出来,其中,SMC3374是 一种较典型的材料,它的密度仍然维持在1.3 g/cm3左右,然而它在93.3℃能够保持住75%的力学性能,与原来的SMC只能在65.5℃保持有了明显的提高。因此,在2001奥德汽车极光,庞帝阿克-邦奈威勒2000以及2000别克-萨罗上,都采用了SMC3374材料。
从以上的分析不难看出,SMC仅适用于制造车身上温度不高且承受的载荷不大的区域,比如顶部和侧面。而底部以及高温区域,就需要能够抗高温和耐高压的复合材料了。
戴尔福公司在1981年生产出第一个采用复合材料小弯曲的板掸簧。小弯曲材料有很高的刚度,也就是说,在很大的压力下,它的应变却可以保持在很小的范围内,同时它的密度很小,只有钢材的50%~70%,因此,小弯曲材料的承载与自身质量之比是钢材的5倍。另外,实验数据显示,它比钢材要坚硬3.5倍。这些优点都是由材料性能直接带来的,除此之外,复合材料板掸簧要比钢板弹簧的结构简单得多,很容易装配,维修以及采取防腐措施。而且,由于它比钢板弹簧小得多的厚度,使它叫以更接近地面,从而节省了汽车的有效空间。必要时,更可以用来降低汽车的底盘,提高汽车的舒适性能。
高温下材料的性能,一直是材料选择的因素。测试结果显示,车下板弹簧处的温度最高可以达到130℃,小弯曲材料在这个温度下性能是稳定的。正是基于以上的诸多优点,小弯曲材料被广泛应用于制造汽车的板弹簧,从轿车到轻型货午,甚至重型商业运输车都采用了这种板掸簧。
复合材料与未来汽车
未来的汽车是属于适应环境保护的绿色汽车,因而在此不可避免的要提到复合材料的环保意识。复合材料能提高材料性能,延长使用期,加强功能性,这些都是对环境有利的特性。但应认真对待并努力克服复合材料的再生问题,使复合材料朝着环境协调化的方向发展。
复合材料零件的再生利用是非常难的事,会对环境产生些不利的影响。如目前发展最快、应用最高的聚合物基复合材料中绝大多数属易燃物,燃烧时会放出大量有毒气体,污染环境;且在成型时,基体中的挥发成分即溶剂会扩散到空气中,造成污染。复合材料使用本身就是多种组分材料构成,属多相材料,难以粉碎、磨细、熔融及降解,复合零件首先分解成单一材料的零件,然而这种分解工艺成本和再生成本较高,而且要使其恢复原有性能十分困难。因此再生利用的主要条件之一是零件容易拆卸,尽可能是单一品种材料,即便是复合材料也要尽量使用复合性少的材料。基于上述原则上的考虑,热塑性聚烯烃弹性体、聚丙烯发泡材料及GMT增强板材的应用量还会大幅度增加,相反热固性树脂的用量将受到限制。目前在再生性和降解性方面的研究工作已经取得了很大的进展。当今社会,人们目光的角度逐渐转到人与自然的关系问题上,环境与能源问题成为世界上每个国家能否生存和发展的关键。随着人们环保意识的不断提高以及符合环保法规的相继出台,绿色汽车已经成为未来汽车发展的必然趋势,因而如何使汽车满足环境保护的要求,便提到了汽车厂商们的议事日程。而复合材料作为末来汽车材料发展的主流,必将在其中扮演非常重要的角色。
- 下一篇:浅谈ABB涂胶机器人的功能及应用
- 上一篇:机器视觉系统在汽车发动机装配线上的应用
编辑推荐
最新资讯
-
旭化成微电子开始批量生产用于环保发
2025-04-24 16:00
-
华为、地平线、大众、东风、起亚等引
2025-04-24 08:27
-
全球产业链聚沪 共探双碳新路径 SNEC
2025-04-18 18:05
-
柯马签订具有约束力的协议收购 Autom
2025-04-17 13:01
-
高效协同新范式:比亚迪叉车领创智能
2025-04-17 10:04