汽车生产线上的机器人焊接夹具设计要点及达成效果
2018-06-13 15:33:16· 来源:机电帮
据统计,焊接生产线的60%-70%的工作量落在了装夹和辅助两项环节上,而所有的装夹都需在夹具上完成,因此夹具对整个汽车焊接占有不可估量的地位。今天为大家分享一篇文章,分析汽车生产线上机器人焊接夹具的设计要点以及采用此设计方案所达到的效果。
前 言
据统计,焊接生产线的60%-70%的工作量落在了装夹和辅助两项环节上,而所有的装夹都需在夹具上完成,因此夹具对整个汽车焊接占有不可估量的地位。今天为大家分享一篇文章,分析汽车生产线上机器人焊接夹具的设计要点以及采用此设计方案所达到的效果。
一焊接夹具设计要点
1.1 汽车焊接工艺
汽车焊接工艺是由零件到总成的组合过程,每个组合过程之间相互独立,互不干扰,但又具有承前启后的顺序关系。这种关系的存在保证了汽车焊接工艺的精确度,每一个组合过程都会影响总成焊接精度。因此车身每一个焊接总成夹具须建立统一、连续的定位基准。
1.2 机器人
在汽车设计与制造领域,为减轻劳动量,提升工作效率,机器人被广泛应用。事实证明机器人因缺乏灵活性,焊接质量难以得到保障。为解决因缺乏灵活性和判断能力所带来的困扰,设计人员不但要确保夹具可靠性,而且还须留有足够空间和路径供焊枪使用,为机器人提供舒适的焊接姿态;另外还要提升夹具的精度,确保机器人执行既定程序,减小焊接误差。
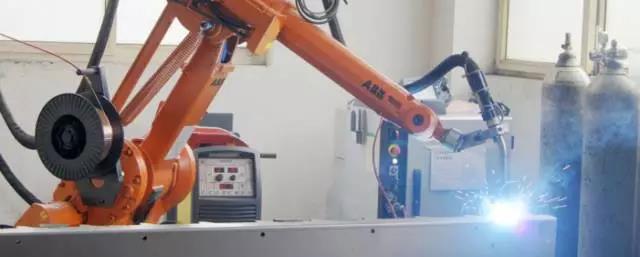
▲ 图1 焊接机器人
1.3 安全性
从劳动者的角度来看,焊接夹具设计的目的是在保障人身与设备安全的基础上减轻劳动量。故焊接夹具设计在满足人机工程的同时,方便工人在安全环境下装配和取出零部件总成。
二焊接夹具的构成
2.1 夹具体
夹具体是由定位和夹紧两项装置组成,它作为夹具基础单元起到吊装、三坐标检测及校验作用。检查工作面平整度,保证加工夹具体时,提升其精度来影响定位机构的准确度。夹具体设计时,要以实际装配和测量为最终目的,确保夹具体的设计强度和空间高度契合,最大限度减小夹具体自重。比如按照工件的外形,遵守焊接原则,以减少夹具自重、便于管路连接,以及为机器人提供足够焊接空间为目的,选择单梁或框架结构。
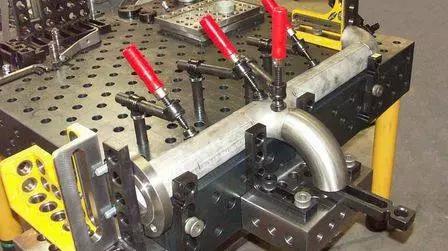
▲ 图2 机器人焊接工装
2.2 定位装置
定位装置中的核心部件为定位件,定位件种类多样,既有按照焊件实际形状来确认的定位块,也有如V形块、档铁、插销以及固定销等定位件。
对于夹具体,定位件必须选择孔定位或外形定位以保证定位精准,从定位件选择角度来看,夹具定位设计需注意以下几点:
(1)选择合适的材料及强度。定位件只有满足焊接所需的刚性与硬度才可确保定位件使用精度、减缓定位件磨损。通常定位件应选择45号钢,且为增大定位件的耐磨性需对其热处理; 65Mn可用于制作胀销;而铜亦可充当定位件材料。
(2)选择合适定位结构。定位件设计成具有可调性的定位结构,是为了应对零部件的复杂结构。可调性定位结构在设计时,定位件通常与支撑件分体设计。如图3所示,可利用垫片实现三个方向上的自由调整。
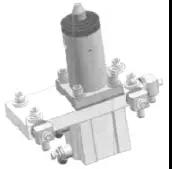
▲ 图3 可调式定位件
(3)低碳钢板材是机器人焊接中应用最多的一类材料,其表面呈不规则形态。若选择如图4 所示的三圆柱销支撑式定位件,不但节材省料,而且加工成本也将大大降低,定位准确性将大大提高。
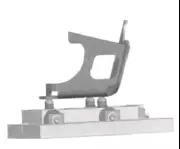
▲ 图4 三圆柱销支撑式定位件
(4)选择可拆工件。由于汽车零部件定位精度要求高,焊缝长,焊后易变形,工件难以拆卸,建议选择图5所示定位件,即胀销结构定位件。
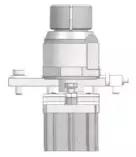
▲ 图5 胀销结构定位件
2.3 夹紧装置
夹紧装置的设计需注意以下几点:
(1)夹紧力作用点:针对薄板冲压件而言,夹紧力在支承点上作用需保证工件刚性良好,以防止工件受夹紧力影响而出现弯曲,甚至脱离定位基准;
(2)夹紧力大小:夹紧力一方面为防止工件变形,另一方面维持工件装配位置相对应,以此来贴合导电电极或定位支承。针对1.5-2.5mm 冲压件,夹紧力为500-3000N,贴合间隙≤1.5mm;针对≤1.2mm 冲压件,夹紧力为300-750N之间,贴合间隙≤0.8mm。
(3)夹紧装置需具有可调性:如图6所示,这种桥形夹紧装置,采用多点夹紧的形式,特别适用于形状复杂、高度不一的工件,即可确保工件与压紧点完全接触,还可满足复杂表面工件的加工要求。
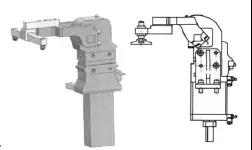
▲ 图6 桥形夹紧装置
结 语
在整个汽车制造中,汽车焊接生产线是一项核心环节,其中机器人焊接夹具属于重中之重。充分考虑焊接夹具设计要点,努力创新设计理念,以确保设计出的夹具能切实符合汽车生产要求,并推动现代化工业发展。
据统计,焊接生产线的60%-70%的工作量落在了装夹和辅助两项环节上,而所有的装夹都需在夹具上完成,因此夹具对整个汽车焊接占有不可估量的地位。今天为大家分享一篇文章,分析汽车生产线上机器人焊接夹具的设计要点以及采用此设计方案所达到的效果。
一焊接夹具设计要点
1.1 汽车焊接工艺
汽车焊接工艺是由零件到总成的组合过程,每个组合过程之间相互独立,互不干扰,但又具有承前启后的顺序关系。这种关系的存在保证了汽车焊接工艺的精确度,每一个组合过程都会影响总成焊接精度。因此车身每一个焊接总成夹具须建立统一、连续的定位基准。
1.2 机器人
在汽车设计与制造领域,为减轻劳动量,提升工作效率,机器人被广泛应用。事实证明机器人因缺乏灵活性,焊接质量难以得到保障。为解决因缺乏灵活性和判断能力所带来的困扰,设计人员不但要确保夹具可靠性,而且还须留有足够空间和路径供焊枪使用,为机器人提供舒适的焊接姿态;另外还要提升夹具的精度,确保机器人执行既定程序,减小焊接误差。
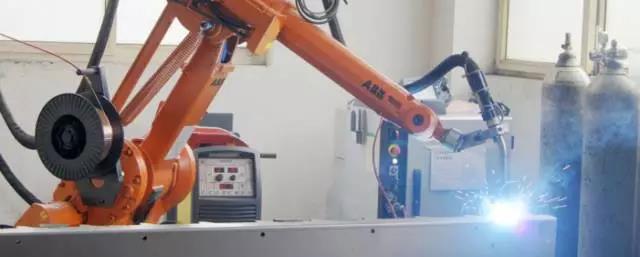
▲ 图1 焊接机器人
1.3 安全性
从劳动者的角度来看,焊接夹具设计的目的是在保障人身与设备安全的基础上减轻劳动量。故焊接夹具设计在满足人机工程的同时,方便工人在安全环境下装配和取出零部件总成。
二焊接夹具的构成
2.1 夹具体
夹具体是由定位和夹紧两项装置组成,它作为夹具基础单元起到吊装、三坐标检测及校验作用。检查工作面平整度,保证加工夹具体时,提升其精度来影响定位机构的准确度。夹具体设计时,要以实际装配和测量为最终目的,确保夹具体的设计强度和空间高度契合,最大限度减小夹具体自重。比如按照工件的外形,遵守焊接原则,以减少夹具自重、便于管路连接,以及为机器人提供足够焊接空间为目的,选择单梁或框架结构。
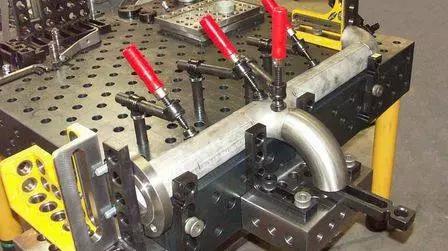
▲ 图2 机器人焊接工装
2.2 定位装置
定位装置中的核心部件为定位件,定位件种类多样,既有按照焊件实际形状来确认的定位块,也有如V形块、档铁、插销以及固定销等定位件。
对于夹具体,定位件必须选择孔定位或外形定位以保证定位精准,从定位件选择角度来看,夹具定位设计需注意以下几点:
(1)选择合适的材料及强度。定位件只有满足焊接所需的刚性与硬度才可确保定位件使用精度、减缓定位件磨损。通常定位件应选择45号钢,且为增大定位件的耐磨性需对其热处理; 65Mn可用于制作胀销;而铜亦可充当定位件材料。
(2)选择合适定位结构。定位件设计成具有可调性的定位结构,是为了应对零部件的复杂结构。可调性定位结构在设计时,定位件通常与支撑件分体设计。如图3所示,可利用垫片实现三个方向上的自由调整。
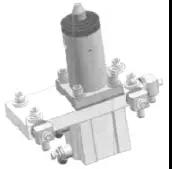
▲ 图3 可调式定位件
(3)低碳钢板材是机器人焊接中应用最多的一类材料,其表面呈不规则形态。若选择如图4 所示的三圆柱销支撑式定位件,不但节材省料,而且加工成本也将大大降低,定位准确性将大大提高。
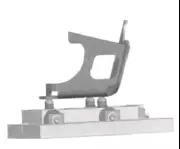
▲ 图4 三圆柱销支撑式定位件
(4)选择可拆工件。由于汽车零部件定位精度要求高,焊缝长,焊后易变形,工件难以拆卸,建议选择图5所示定位件,即胀销结构定位件。
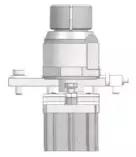
▲ 图5 胀销结构定位件
2.3 夹紧装置
夹紧装置的设计需注意以下几点:
(1)夹紧力作用点:针对薄板冲压件而言,夹紧力在支承点上作用需保证工件刚性良好,以防止工件受夹紧力影响而出现弯曲,甚至脱离定位基准;
(2)夹紧力大小:夹紧力一方面为防止工件变形,另一方面维持工件装配位置相对应,以此来贴合导电电极或定位支承。针对1.5-2.5mm 冲压件,夹紧力为500-3000N,贴合间隙≤1.5mm;针对≤1.2mm 冲压件,夹紧力为300-750N之间,贴合间隙≤0.8mm。
(3)夹紧装置需具有可调性:如图6所示,这种桥形夹紧装置,采用多点夹紧的形式,特别适用于形状复杂、高度不一的工件,即可确保工件与压紧点完全接触,还可满足复杂表面工件的加工要求。
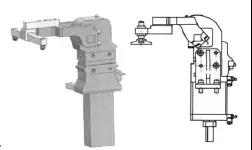
▲ 图6 桥形夹紧装置
结 语
在整个汽车制造中,汽车焊接生产线是一项核心环节,其中机器人焊接夹具属于重中之重。充分考虑焊接夹具设计要点,努力创新设计理念,以确保设计出的夹具能切实符合汽车生产要求,并推动现代化工业发展。
编辑推荐
最新资讯
-
果栗智造磁悬浮技术赋能汽车制造:破
2025-04-03 19:27
-
比亚迪叉车的智慧演变:从动力革新到
2025-04-02 09:15
-
重磅剧透!首批参展商名单曝光——这
2025-04-01 20:48
-
施耐德电气发布新一代Harmony XVB7模
2025-04-01 18:51
-
[转载] 机床巨头埃马克:百年跌宕再
2025-03-31 12:42