汽车工业的涂装趋势: 进一步提升汽车涂装的质量、效率及灵活性
2018-06-13 15:44:26· 来源:表面工程展
外部金属板美丽的外观以及理想的防护是汽车喷涂的传统任务。但是需求已经发生了巨大的变化。例如,在越来越大的程度上对于汽车的内部及外部都需要个性化,因而最终会导致制造的批量为一台。
外部金属板美丽的外观以及理想的防护是汽车喷涂的传统任务。但是需求已经发生了巨大的变化。例如,在越来越大的程度上对于汽车的内部及外部都需要个性化,因而最终会导致制造的批量为一台。汽车车身和零部件的制造越来越频繁地来自于材料的不同组合,有助减轻汽车的重量,减少燃料消耗。汽车共享、电动及自动驾驶的趋势,以及生产过程的数字化和网络化,也为喷涂技术领域带来新的任务和要求。诸如提高首道漆配额、涂漆系统可用性以及能量和材料效率等因素,对于在全球市场中实施这些任务起着非常重要的作用。喷涂公司正努力改进目前的解决方案,并开发新的方案,包括整个生产流程的所有工序以便能实现上述这些目标。
匹配的前处理
在涉及复合材料设计时,特别是碳纤维增强塑料(Carbon-fibre Reinforced Plastics, CFRP)与金属部件的组合使用,仍然非常具有挑战性的。一方面,许多中间工序如研磨和填塞等仍被需要,以便能生成A级表面。另一方面,需要避免在碳纤维增强塑料部件的边缘出现电化学腐蚀,如果自由的碳纤维接触到金属部件的话,则在处理过程后会发生电化学腐蚀。各种应对这些问题的项目正在进展中,目的主要是开发一个适当的边缘封闭工艺。
对于温度敏感的轻质材料,如塑料和复合材料,阴极浸漆后的高温烘干温度范围从100~200°C,这也会带来问题。涂漆供应商正努力寻找解决这个问题的办法,使得较低的烘干温度也能满足要求。然而,还必须要保证其它的工序如粘合剂、封闭剂、烘干硬化合金的固化等也能在这些较低温度下可靠地实施。阴极浸漆工艺的质量检查是很耗时的,仍然是通过破坏性方法进行的,借助于适合的模拟技术可以减少检查或者完全取代检查。
传统使用的具有下游滞留水烘干机的动力清洗系统,对于由塑料及碳纤维增强塑料(CFRP)制成的部件的前处理,在很大程度上被二氧化碳雪喷射、等离子工艺、蒸汽清洗等替代技术所取代。除了大幅度降低成本、空间要求及能耗外,这个趋势的原因还包括能够方便地将这些替代技术结合到网络化制造环境中并加以控制。
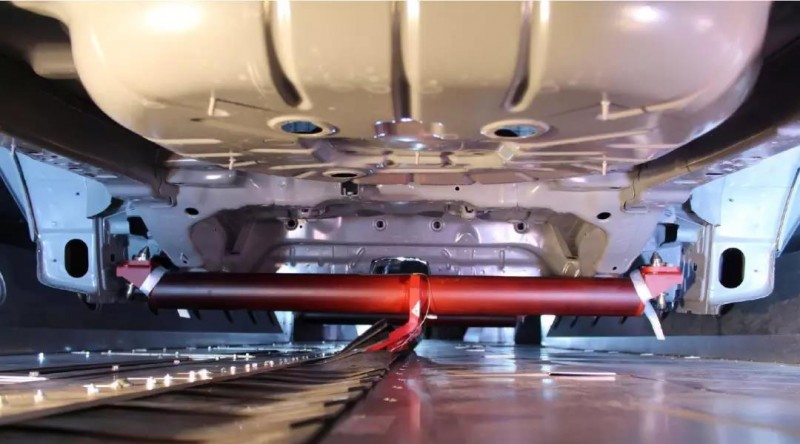
汽车车身通过无滑道的传送,节约了能源,提高了涂漆工艺的灵活性。
高效涂漆工艺
不含填充剂的涂漆并不是完全新的,但却仍是非常相关的。对这种所谓的一体化概念而言,填充涂料的功能通常是利用水性涂漆系统来完成的。根据这种无填充剂的工艺所能达到的外观、色度、质量等级的不同,具有填充剂、底漆和面漆的常规工艺,是没有中间干燥工序的湿-湿涂漆应用的更有效的替代技术。
说到外观,目前的趋势正朝着多颜色及个性化涂漆方向发展。目标是能够在不需要掩膜的情况下涂覆,大大降低所需要的时间和人工。在航天工业的尾冀涂覆中已开始实施了无掩膜的涂覆,通过采用单独的漆滴,既增加了装饰但又没有过喷漆。喷膜是另一种方法,施用时具有锐边,然后可以再方便地撕下来。
一种新型不带滑道的传送带系统把汽车车身在整个涂漆车间内运输,可以降低能源成本,因为不再需要把滑道加温然后再冷却的过程了。此外,这还增加了涂漆过程的灵活性,因为运送的速度可以与相应的工序相适应。以这种方式可以灵活地设定和优化周期时间和生产率。
汽车内部的装饰性和功能性部件以及装饰模件,如与车身贴近的柱状装饰件,通常都是利用塑料注模进行制造的。这些部件的表面在光感和触感及耐久性方面都有非常高的单独的要求。借助于基于RIM幕帘涂覆工艺的先进方案可以满足这些要求。在塑料件成型或模内装饰工艺过程中将两种涂漆组分注射到注塑模中。如果把颜色作为第三种组分添加的话,三组分混合头可以将三组分直接注射到工件上,因此颜色的更换与喷涂工艺一样快速而便捷。因而,被涂覆的工件通过一次进料过程就完成了制造。
对于汽车塑料内饰件的常规喷涂的情况,单层涂漆系统可减少工序步骤,因而提高了生产率,同时还节约了时间、降低了材料消耗。对于精细木质装饰件也有新开发的涂漆系统,既能节省大量的时间,也能使用人工或自动化的喷涂工艺提高生产率。
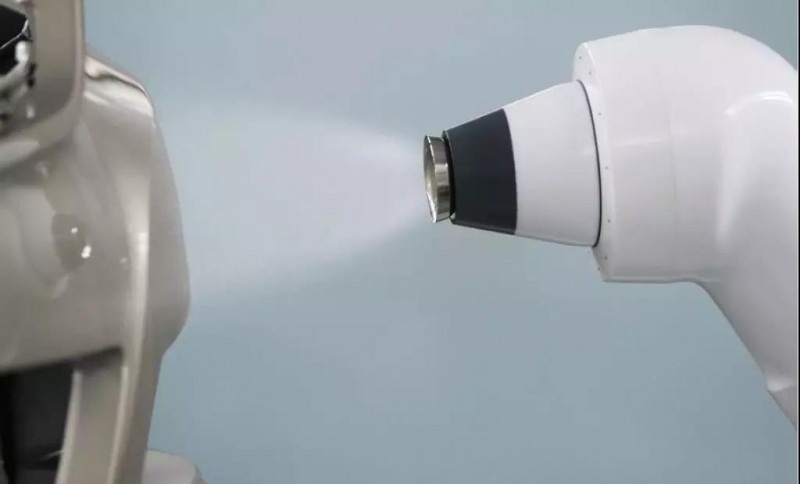
制造商正利用各种优化方案,为了进一步提高喷雾器的涂漆效率,例如可调节喷射宽度,更改空气控制装置和回转带。
高效喷涂技术
就涂覆而言,目标是能够进行涂覆而又没有过喷或过喷量极少的工艺。直到这种解决方案真正落实之前,最优选方案是提高涂覆效率。各家公司都为此采用了各种优化潜力,例如,改进空气控制装置及回转带及喷射漆调节能力。由于有了这些灵活性,水性漆的喷雾器就可用于喷涂汽车内部和外部的各种塑料部件以及组合区域。喷雾器的紧凑尺寸使其便于操作,甚至可用在几何形状复杂的区域。此外,这些新型喷雾器独特之处还在于其坚固的高电压技术和最少的污染,因而降低了清洁成本。就喷涂系统的清洁而言,一种新型不含VOC(挥化性有机化合物)的漂洗技术可以支持快速的颜色及涂漆系统更换,因而提高了涂漆工艺的灵活性和生产率。
一个明确的趋势是过喷漆的清洗系统。以这种方式涂漆室的空气在很大程度上被循环利用。此外,湿式清洗系统所需要的空气除湿则被取消了,为此可节约大量的能源。
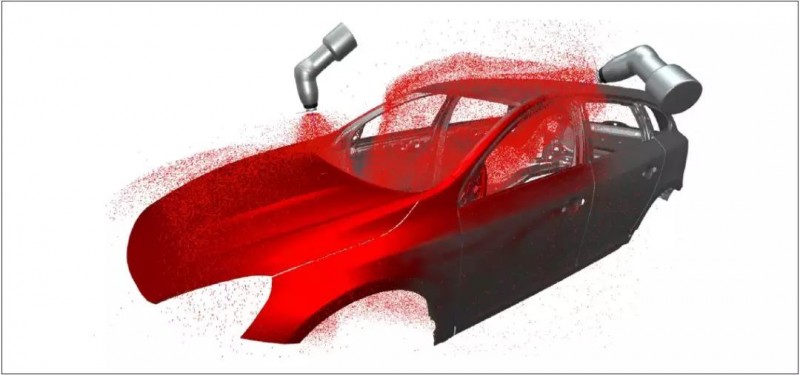
在自编程涂漆室的情况中,漆滴的轨迹是利用多个物理涂漆模型通过计算得到的—图中以Volvo V 60 车身为例。
烘干器的创新技术
新型烘干器也能为汽车车身喷涂操作节约大量的能源和空间。例如,已建造的一座烘炉,其中燃烧器和风机已装入到烘干机通道的侧板上,不仅使结构更紧凑、更节约空间,而且还减少了空气流量损失。通过使用旋转喷嘴,温度和空气流量可理想地与各种汽车车身类型和区域相匹配。例如,对于电动汽车的情况,这保证了材料厚度较高的车门槛板被加热到所需要温度的程度与基材上材料厚度较小的区域被加热的程度是相同的。这种新型烘干器的一个附加特性是依赖于负载的操作,有助降低操作成本。
汽车车身涂层厚度的检查,现在较多使用的仍然是通过生产工人的目测,这会导致疲劳,因而是一个误差源。新的解决方案,例如配备有节能LED技术的光通道,汽车车身在光通道中被均匀地照射,在很大程度上没有眩光,使工作站具有人体工程学,减少误差量。与此同时,也可以自动地获取检查数据,并传递到生产控制中。
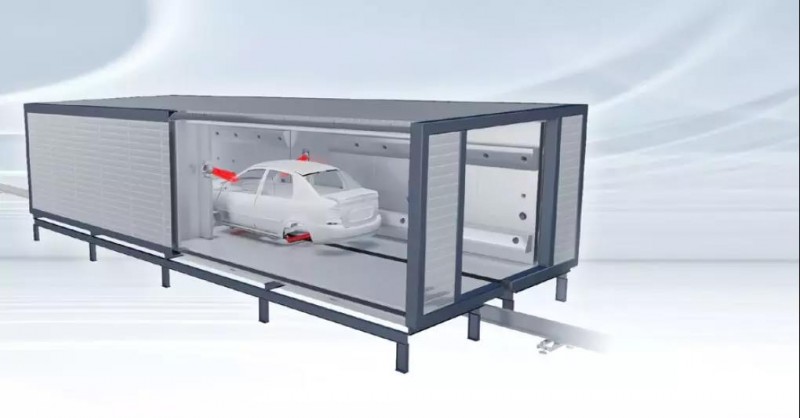
除了大幅度节约能源、占地面积和制造成本外,新型烘干机还把加热功能结合到烘干机通道和旋转喷嘴里,能够按照实际的要求来加热各种汽车车身类型和区域。
喷涂车间4.0和机器学习
监控生产过程的高性能制造执行系统(Manufacturing Execution System, MES)是高效制造的关键。把通过传感器从涂漆车间的各个区域获取的数据汇总起来,可以更有效地设定涂漆工艺。如果对与系统条件、工艺过程及产品相关的必要数据进行分析并相互关联,则通过基于知识的算法能给系统带来智能化和自调节的功能。对于涂漆车间内的各种功能已经开发了相对应的解决方案,例如,涂漆烘干机的空气管理及预防维护。
用于涂覆制造批量为1的产品的自编程涂漆室已不再是幻想。在项目研发过程中开发了一种自动涂漆工艺,包含五个工序。首先,被涂工件经过三维扫描,并在扫描数据的基础上生成流体动力学模型。涂漆液滴的轨迹被生成,并为所需要的涂膜厚度确定出理想的涂漆和空气量。第三步,该系统基于这些数据为涂漆工艺规划出最佳机器人路径。第四步就是实际的涂漆过程,最后一步,通过太赫兹技术(TerahertzTechnology)进行质量检查。(《国际表面处理》杂志)
匹配的前处理
在涉及复合材料设计时,特别是碳纤维增强塑料(Carbon-fibre Reinforced Plastics, CFRP)与金属部件的组合使用,仍然非常具有挑战性的。一方面,许多中间工序如研磨和填塞等仍被需要,以便能生成A级表面。另一方面,需要避免在碳纤维增强塑料部件的边缘出现电化学腐蚀,如果自由的碳纤维接触到金属部件的话,则在处理过程后会发生电化学腐蚀。各种应对这些问题的项目正在进展中,目的主要是开发一个适当的边缘封闭工艺。
对于温度敏感的轻质材料,如塑料和复合材料,阴极浸漆后的高温烘干温度范围从100~200°C,这也会带来问题。涂漆供应商正努力寻找解决这个问题的办法,使得较低的烘干温度也能满足要求。然而,还必须要保证其它的工序如粘合剂、封闭剂、烘干硬化合金的固化等也能在这些较低温度下可靠地实施。阴极浸漆工艺的质量检查是很耗时的,仍然是通过破坏性方法进行的,借助于适合的模拟技术可以减少检查或者完全取代检查。
传统使用的具有下游滞留水烘干机的动力清洗系统,对于由塑料及碳纤维增强塑料(CFRP)制成的部件的前处理,在很大程度上被二氧化碳雪喷射、等离子工艺、蒸汽清洗等替代技术所取代。除了大幅度降低成本、空间要求及能耗外,这个趋势的原因还包括能够方便地将这些替代技术结合到网络化制造环境中并加以控制。
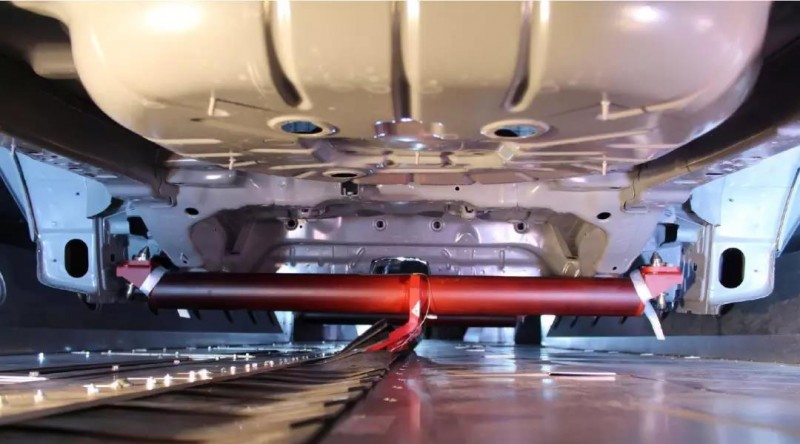
汽车车身通过无滑道的传送,节约了能源,提高了涂漆工艺的灵活性。
高效涂漆工艺
不含填充剂的涂漆并不是完全新的,但却仍是非常相关的。对这种所谓的一体化概念而言,填充涂料的功能通常是利用水性涂漆系统来完成的。根据这种无填充剂的工艺所能达到的外观、色度、质量等级的不同,具有填充剂、底漆和面漆的常规工艺,是没有中间干燥工序的湿-湿涂漆应用的更有效的替代技术。
说到外观,目前的趋势正朝着多颜色及个性化涂漆方向发展。目标是能够在不需要掩膜的情况下涂覆,大大降低所需要的时间和人工。在航天工业的尾冀涂覆中已开始实施了无掩膜的涂覆,通过采用单独的漆滴,既增加了装饰但又没有过喷漆。喷膜是另一种方法,施用时具有锐边,然后可以再方便地撕下来。
一种新型不带滑道的传送带系统把汽车车身在整个涂漆车间内运输,可以降低能源成本,因为不再需要把滑道加温然后再冷却的过程了。此外,这还增加了涂漆过程的灵活性,因为运送的速度可以与相应的工序相适应。以这种方式可以灵活地设定和优化周期时间和生产率。
汽车内部的装饰性和功能性部件以及装饰模件,如与车身贴近的柱状装饰件,通常都是利用塑料注模进行制造的。这些部件的表面在光感和触感及耐久性方面都有非常高的单独的要求。借助于基于RIM幕帘涂覆工艺的先进方案可以满足这些要求。在塑料件成型或模内装饰工艺过程中将两种涂漆组分注射到注塑模中。如果把颜色作为第三种组分添加的话,三组分混合头可以将三组分直接注射到工件上,因此颜色的更换与喷涂工艺一样快速而便捷。因而,被涂覆的工件通过一次进料过程就完成了制造。
对于汽车塑料内饰件的常规喷涂的情况,单层涂漆系统可减少工序步骤,因而提高了生产率,同时还节约了时间、降低了材料消耗。对于精细木质装饰件也有新开发的涂漆系统,既能节省大量的时间,也能使用人工或自动化的喷涂工艺提高生产率。
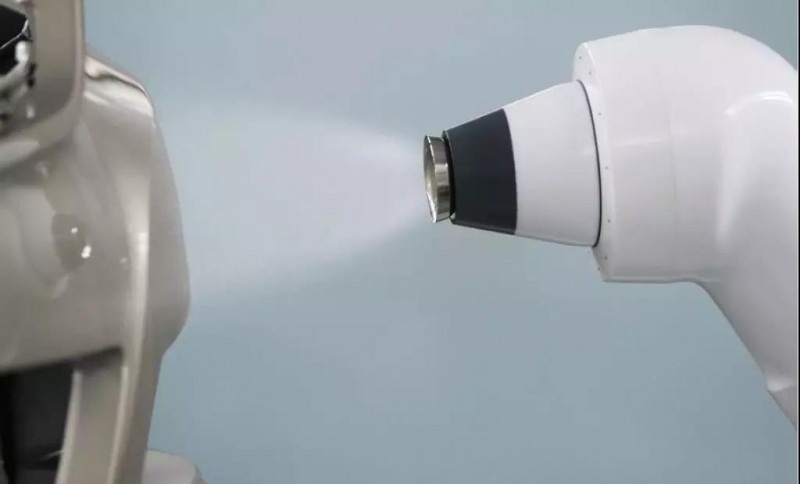
制造商正利用各种优化方案,为了进一步提高喷雾器的涂漆效率,例如可调节喷射宽度,更改空气控制装置和回转带。
高效喷涂技术
就涂覆而言,目标是能够进行涂覆而又没有过喷或过喷量极少的工艺。直到这种解决方案真正落实之前,最优选方案是提高涂覆效率。各家公司都为此采用了各种优化潜力,例如,改进空气控制装置及回转带及喷射漆调节能力。由于有了这些灵活性,水性漆的喷雾器就可用于喷涂汽车内部和外部的各种塑料部件以及组合区域。喷雾器的紧凑尺寸使其便于操作,甚至可用在几何形状复杂的区域。此外,这些新型喷雾器独特之处还在于其坚固的高电压技术和最少的污染,因而降低了清洁成本。就喷涂系统的清洁而言,一种新型不含VOC(挥化性有机化合物)的漂洗技术可以支持快速的颜色及涂漆系统更换,因而提高了涂漆工艺的灵活性和生产率。
一个明确的趋势是过喷漆的清洗系统。以这种方式涂漆室的空气在很大程度上被循环利用。此外,湿式清洗系统所需要的空气除湿则被取消了,为此可节约大量的能源。
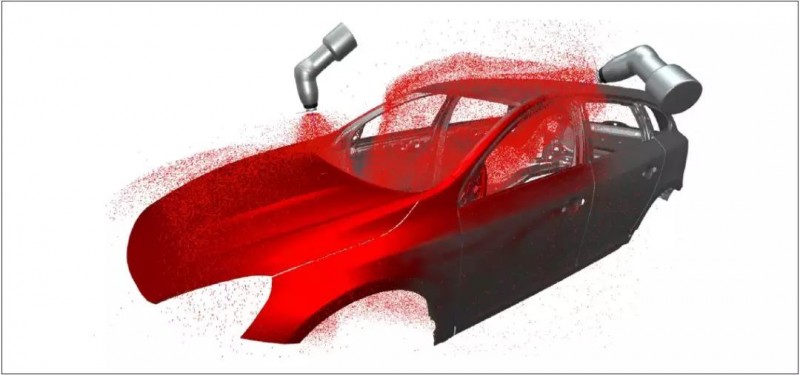
在自编程涂漆室的情况中,漆滴的轨迹是利用多个物理涂漆模型通过计算得到的—图中以Volvo V 60 车身为例。
烘干器的创新技术
新型烘干器也能为汽车车身喷涂操作节约大量的能源和空间。例如,已建造的一座烘炉,其中燃烧器和风机已装入到烘干机通道的侧板上,不仅使结构更紧凑、更节约空间,而且还减少了空气流量损失。通过使用旋转喷嘴,温度和空气流量可理想地与各种汽车车身类型和区域相匹配。例如,对于电动汽车的情况,这保证了材料厚度较高的车门槛板被加热到所需要温度的程度与基材上材料厚度较小的区域被加热的程度是相同的。这种新型烘干器的一个附加特性是依赖于负载的操作,有助降低操作成本。
汽车车身涂层厚度的检查,现在较多使用的仍然是通过生产工人的目测,这会导致疲劳,因而是一个误差源。新的解决方案,例如配备有节能LED技术的光通道,汽车车身在光通道中被均匀地照射,在很大程度上没有眩光,使工作站具有人体工程学,减少误差量。与此同时,也可以自动地获取检查数据,并传递到生产控制中。
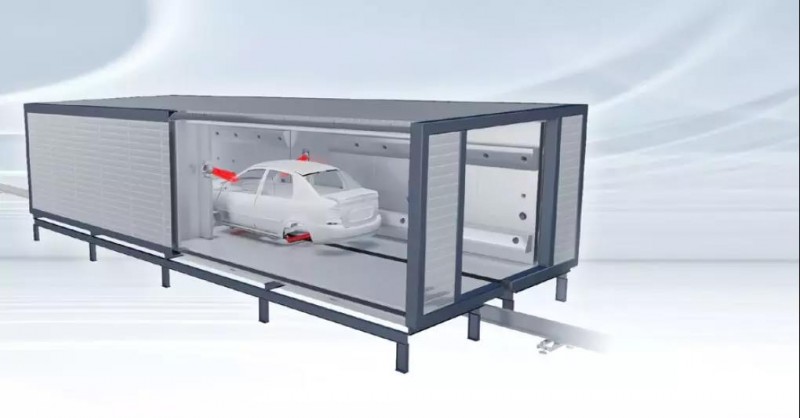
除了大幅度节约能源、占地面积和制造成本外,新型烘干机还把加热功能结合到烘干机通道和旋转喷嘴里,能够按照实际的要求来加热各种汽车车身类型和区域。
喷涂车间4.0和机器学习
监控生产过程的高性能制造执行系统(Manufacturing Execution System, MES)是高效制造的关键。把通过传感器从涂漆车间的各个区域获取的数据汇总起来,可以更有效地设定涂漆工艺。如果对与系统条件、工艺过程及产品相关的必要数据进行分析并相互关联,则通过基于知识的算法能给系统带来智能化和自调节的功能。对于涂漆车间内的各种功能已经开发了相对应的解决方案,例如,涂漆烘干机的空气管理及预防维护。
用于涂覆制造批量为1的产品的自编程涂漆室已不再是幻想。在项目研发过程中开发了一种自动涂漆工艺,包含五个工序。首先,被涂工件经过三维扫描,并在扫描数据的基础上生成流体动力学模型。涂漆液滴的轨迹被生成,并为所需要的涂膜厚度确定出理想的涂漆和空气量。第三步,该系统基于这些数据为涂漆工艺规划出最佳机器人路径。第四步就是实际的涂漆过程,最后一步,通过太赫兹技术(TerahertzTechnology)进行质量检查。(《国际表面处理》杂志)
编辑推荐
最新资讯
-
全球产业链聚沪 共探双碳新路径 SNEC
2025-04-18 18:05
-
柯马签订具有约束力的协议收购 Autom
2025-04-17 13:01
-
高效协同新范式:比亚迪叉车领创智能
2025-04-17 10:04
-
埃马克德国总部迎来中国社科院工业经
2025-04-15 09:40
-
埃马克这项全新应用即将在CIMT惊艳首
2025-04-15 09:37