自动化立体库在智能制造中的应用
2018-06-16 11:32:18· 来源:AI制造
近两年,我国汽车产销增速下降并放缓,汽车行业已进入了发展的拐点。汽车制造企业必须通过产品创新和管理变革,有效利用信息技术(如PDM、ERP、SCM、MES和移动互联等相关技术)、自动化技术(如自动识别、自动化控制、工业机器人、AGV、自动化仓库及其输送系统)和智能化技术(如智能装备、智能产线、智能车间和机器视觉等),建立差异化竞争优势,从而缩短产品上市周期、降低成本并提升产品质量,满足个性化需求,敏捷应对市场变化,实现可持续发展。
近两年,我国汽车产销增速下降并放缓,汽车行业已进入了发展的拐点。汽车制造企业必须通过产品创新和管理变革,有效利用信息技术(如PDM、ERP、SCM、MES和移动互联等相关技术)、自动化技术(如自动识别、自动化控制、工业机器人、AGV、自动化仓库及其输送系统)和智能化技术(如智能装备、智能产线、智能车间和机器视觉等),建立差异化竞争优势,从而缩短产品上市周期、降低成本并提升产品质量,满足个性化需求,敏捷应对市场变化,实现可持续发展。
随着汽车市场竞争的日趋激烈,各大汽车制造商不断加快新车型开发并不断降低开发成本,开发成本的降低主要集中在共用平台、动力总成和提高生产制造柔性等方面。一汽轿车现拥有多种平台,每个平台下还有多种车型,因而采用了多品种小批量的柔性化生产方式,并在智能制造系统中应用智能物流自动化仓库及其输送系统。
总装底盘合装线柔性化工艺分析
一汽轿车总装底盘合装线主要由RGV小车(含轨道)、装配高架平台和前托盘转交站组成,按装配内容分为底盘合装区、前机舱装配区、托盘转交区及外分装配区。底盘合装区设计了3个工位,其中2个操作工位、1个预留工位。底盘合装区的主要工作内容是完成前、后副车架与车身的装配(见下图)。第一步,RGV与车身自动找正,并与底盘线保持速度同步;第二步,人工控制RGV前、后举升台举升,并将副车架孔位与车身焊接螺栓对正;第三步,人工使用拧紧工具将前、后副车架紧固至车身。
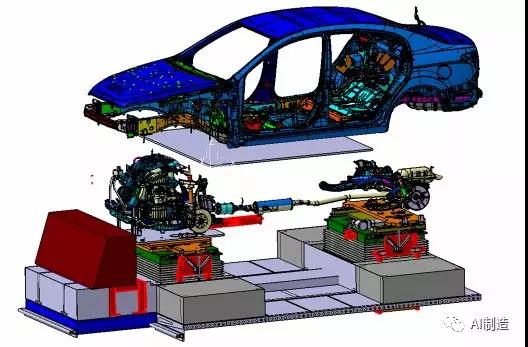
前后悬架总成底盘合装
后导入的平台车型悬架与车身采用螺栓连接固定,为保证合装过程中悬架与车身的准确定位,一是需要增加导向来保证悬架与车身的准确定位,缩短作业调整时间;二是最大限度地保证车辆外倾合格。定位销在合装举升过程中先与车身定位再装配螺栓,对辅助定位的定位精度要求较高。由于前轮外倾值需通过调整前滑柱与转向节连接螺栓实现,因此该工作必须在举升机上进行。在举升机上调整后再到四轮定位进行检测,每调整一次需要20~30min。后轮外倾值整车下线后均不可调,故必须在底盘合装时用专用托盘保证。如果前、后轮外倾值不合格将会导致整车跑偏、车轮偏磨等严重质量问题,因此必须在底盘合装工位保证前后轮外倾值。
本文对3种平台的不同车型前、后悬架总成与车身合装产品结构进行了分析,确定底盘合装工位需采用2种前悬架托盘和3种后悬架托盘,才可以满足各平台底盘合装的精度要求。由于底盘合装线面积有限,为保证承载多种托盘的生产线的柔性化生产,需建立托盘立体库用于托盘输送、存储和编组。
前、后悬架托盘立体库方案选择
立体库设计要求:前、后悬架托盘能够独立运行并自动完成托盘进库、出库、编组和输送,从而保证托盘先进、先出,防止个别托盘过度使用。同时通过查询车身VIN码可以追溯装配托盘编号,从而为产品质量追溯系统提供信息支持。
前、后托盘立体库结构种类很多,经深入分析对比,初步选用了高位货架立体库和存储线立体库(见下图)。根据总装底盘线现有布局共制定3种前、后悬架托盘立体库选择方案。
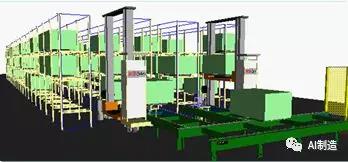
高位货架立体库
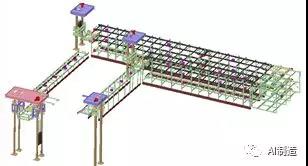
存储线立体库
1.方案一:地面高位货架托盘立体库
在地面建设高位货架立体库,通过有轨巷道车存取托盘。前、后悬架托盘存储货架通用,可提高托盘存储量并满足前、后悬架托盘柔性存储。该方案设计存储140个托盘。
2.方案二:空中存储线托盘立体库Ⅰ(5条存储线)
在空中建设输送线结构托盘立体库,该方式通过提升机自动转运托盘进出库。该方式需新增2条前悬架空中托盘存储线及3条后悬架空中托盘存储线。
3.方案三:空中存储线托盘立体库Ⅱ(4条存储线)
在空中建设输送线结构托盘立体库,该方式需新增1条前悬架空中托盘存储线及3条后悬架空中托盘存储线,原有平台前悬架托盘仍用动分线返回转运托盘。
3种方案综合评价对比如表所示。
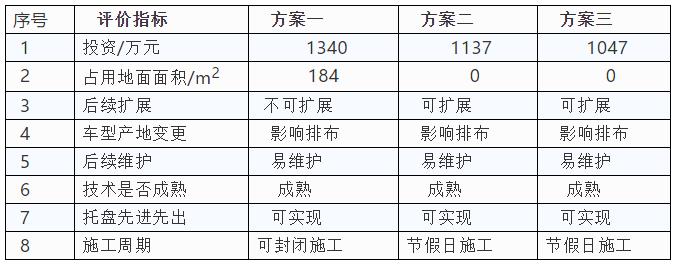
由于地面可用面积仅184m2,高位货架立体库后续货架无增加空间;移动距离短,有轨巷道车发挥不了快速移动功能;高位货架立体库无价格优势等原因,故不建议采用方案一。
方案三虽比方案二设计、施工难度大,但方案三比方案二少建设一条前悬架托盘输送线并能节省投资90万元,故建议采用方案三。
前、后悬架托盘立体库主要由前、后悬架托盘立体库,生产联网系统,质量追
溯系统和前、后悬架专用托盘组成,通过新增4台提升机实现托盘自动进库、出库功能(见下图)。
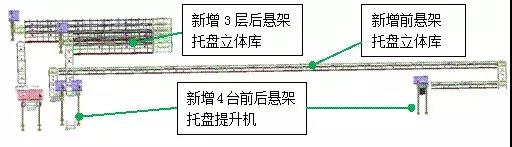
空中前后悬架托盘立体库
托盘立体库功能及实现方法
1.托盘出库编组功能
托盘立体库功能主要体现在提升机准确读取车型信息后,托盘需立体出库并自动编组。托盘立体库与生产信息系统联网,实现自动读取生产信息中的生产车序并将其转换成托盘种类信号,提升机根据托盘信息到相应存储线提取对应托盘。以前悬架托盘立体库为例:如车型信息为新平台车型,托盘提升机接收信号需到空中接取新平台专用托盘;如车型信息为原有平台车型,托盘提升机接收信号到地面动分线下层输送线接取原有平台托盘。
2.托盘入库编组功能
以后悬架托盘入库编组为例:后悬架托盘有3种平台专用托盘,分别存储到各自专用存储线中;后悬架托盘在底盘线完成合装装配后并在进入托盘立体库前,通过托盘上安装的RFID电子标签和线体上安装的接近开关对托盘型号进行电子和物理双重识别;如RFID读写头与接近开关判断的托盘型号一致,立体库系统通知提升机将托盘转运到托盘专用存储线中,如RFID读写头与接近开关判断的托盘型号不一致,立体库停止工作并报警,同时人工查找托盘出错原因。托盘采用RFID和物理结构双重识别,提高了托盘的入库准确率。
3.具备手动调整出库托盘编组功能
总装生产车序因突发情况变化时,需人工调整托盘出库车序。
4.质量追溯功能
我们搭建了立体库质量追溯系统,在托盘上安装RFID电子标签,实现每个托盘编号与生产整车VIN码绑定,并存储到立体库工控机中。由于托盘编号和整车VIN码均具有唯一性,当检测线检测出前后轮外倾值不合格时,根据车身VIN码可以在立体库工控机中迅速查找到生产该车的托盘,锁定托盘后用托盘检具对托盘进行检测,判断是否是托盘问题。制作前、后悬架标准托盘并放至立体库检具架。当出现批量外倾不合格车辆时,用标准托盘进行装配。如外倾值合格则为托盘问题,否则从产品质量问题入手。
托盘立体库方案虚拟评审
一汽轿车应用数字化仿真技术对总装底盘柔性化生产准备方案进行了仿真分析,仿真过程中运动部件如果干涉,程序字体会自动变红并提示干涉量。利用该功能,通过模拟前、后悬架托盘在立体库中的实际工作轨迹,检验立体库的通过性和干涉性,从而验证方案的可行性。以新增托盘立体库前悬架托盘工艺方案虚拟评审为例:在立体库仿真环境中对设备关键生准点(20个关键评审点)进行极限参数设定。通过方案仿真评审,实现方案制定、交流、评审和校对可视化,提高生产准备的准确性和效率。
结语
一汽轿车前、后悬架托盘立体库现已投入使用一年多,成功解决了多平台车型的总装底盘合装柔性化生产的瓶颈问题,同时在装配过程中保证了前束、外倾等关键参数精度,在质量、进度和成本上也得到了有效的控制。
托盘立体库在总装领域的应用越来越成熟,也越来越广泛,通过应用托盘立体库技术,一汽轿车积累了柔性化生产、底盘合装、立体库、虚拟仿真和质量追溯等方面的经验,在现有工厂改造以及新工厂建设中,这些经验可以扩展应用到线束存储线、车身存储线、物料分拣和物料自动输送等区域,可以实现减少人员和厂房面积、提高自动化程度和装配质量等方面的改善,同时达到公司降低成本、提高质量和劳动生产率的目标。
随着汽车市场竞争的日趋激烈,各大汽车制造商不断加快新车型开发并不断降低开发成本,开发成本的降低主要集中在共用平台、动力总成和提高生产制造柔性等方面。一汽轿车现拥有多种平台,每个平台下还有多种车型,因而采用了多品种小批量的柔性化生产方式,并在智能制造系统中应用智能物流自动化仓库及其输送系统。
总装底盘合装线柔性化工艺分析
一汽轿车总装底盘合装线主要由RGV小车(含轨道)、装配高架平台和前托盘转交站组成,按装配内容分为底盘合装区、前机舱装配区、托盘转交区及外分装配区。底盘合装区设计了3个工位,其中2个操作工位、1个预留工位。底盘合装区的主要工作内容是完成前、后副车架与车身的装配(见下图)。第一步,RGV与车身自动找正,并与底盘线保持速度同步;第二步,人工控制RGV前、后举升台举升,并将副车架孔位与车身焊接螺栓对正;第三步,人工使用拧紧工具将前、后副车架紧固至车身。
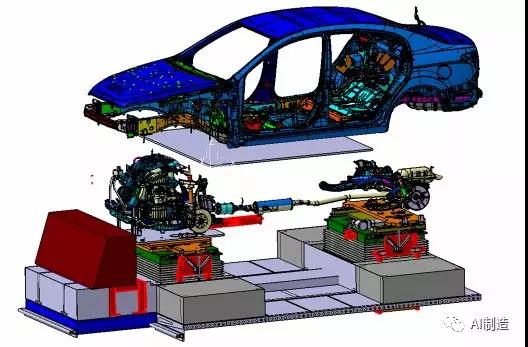
前后悬架总成底盘合装
后导入的平台车型悬架与车身采用螺栓连接固定,为保证合装过程中悬架与车身的准确定位,一是需要增加导向来保证悬架与车身的准确定位,缩短作业调整时间;二是最大限度地保证车辆外倾合格。定位销在合装举升过程中先与车身定位再装配螺栓,对辅助定位的定位精度要求较高。由于前轮外倾值需通过调整前滑柱与转向节连接螺栓实现,因此该工作必须在举升机上进行。在举升机上调整后再到四轮定位进行检测,每调整一次需要20~30min。后轮外倾值整车下线后均不可调,故必须在底盘合装时用专用托盘保证。如果前、后轮外倾值不合格将会导致整车跑偏、车轮偏磨等严重质量问题,因此必须在底盘合装工位保证前后轮外倾值。
本文对3种平台的不同车型前、后悬架总成与车身合装产品结构进行了分析,确定底盘合装工位需采用2种前悬架托盘和3种后悬架托盘,才可以满足各平台底盘合装的精度要求。由于底盘合装线面积有限,为保证承载多种托盘的生产线的柔性化生产,需建立托盘立体库用于托盘输送、存储和编组。
前、后悬架托盘立体库方案选择
立体库设计要求:前、后悬架托盘能够独立运行并自动完成托盘进库、出库、编组和输送,从而保证托盘先进、先出,防止个别托盘过度使用。同时通过查询车身VIN码可以追溯装配托盘编号,从而为产品质量追溯系统提供信息支持。
前、后托盘立体库结构种类很多,经深入分析对比,初步选用了高位货架立体库和存储线立体库(见下图)。根据总装底盘线现有布局共制定3种前、后悬架托盘立体库选择方案。
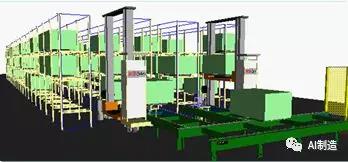
高位货架立体库
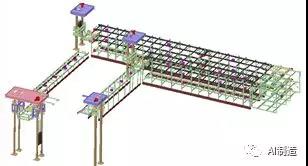
存储线立体库
1.方案一:地面高位货架托盘立体库
在地面建设高位货架立体库,通过有轨巷道车存取托盘。前、后悬架托盘存储货架通用,可提高托盘存储量并满足前、后悬架托盘柔性存储。该方案设计存储140个托盘。
2.方案二:空中存储线托盘立体库Ⅰ(5条存储线)
在空中建设输送线结构托盘立体库,该方式通过提升机自动转运托盘进出库。该方式需新增2条前悬架空中托盘存储线及3条后悬架空中托盘存储线。
3.方案三:空中存储线托盘立体库Ⅱ(4条存储线)
在空中建设输送线结构托盘立体库,该方式需新增1条前悬架空中托盘存储线及3条后悬架空中托盘存储线,原有平台前悬架托盘仍用动分线返回转运托盘。
3种方案综合评价对比如表所示。
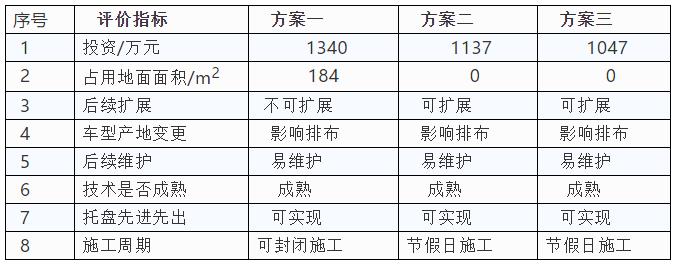
由于地面可用面积仅184m2,高位货架立体库后续货架无增加空间;移动距离短,有轨巷道车发挥不了快速移动功能;高位货架立体库无价格优势等原因,故不建议采用方案一。
方案三虽比方案二设计、施工难度大,但方案三比方案二少建设一条前悬架托盘输送线并能节省投资90万元,故建议采用方案三。
前、后悬架托盘立体库主要由前、后悬架托盘立体库,生产联网系统,质量追
溯系统和前、后悬架专用托盘组成,通过新增4台提升机实现托盘自动进库、出库功能(见下图)。
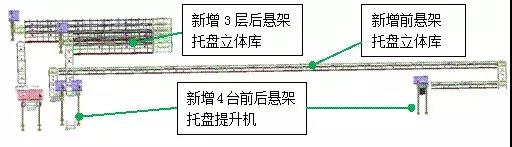
空中前后悬架托盘立体库
托盘立体库功能及实现方法
1.托盘出库编组功能
托盘立体库功能主要体现在提升机准确读取车型信息后,托盘需立体出库并自动编组。托盘立体库与生产信息系统联网,实现自动读取生产信息中的生产车序并将其转换成托盘种类信号,提升机根据托盘信息到相应存储线提取对应托盘。以前悬架托盘立体库为例:如车型信息为新平台车型,托盘提升机接收信号需到空中接取新平台专用托盘;如车型信息为原有平台车型,托盘提升机接收信号到地面动分线下层输送线接取原有平台托盘。
2.托盘入库编组功能
以后悬架托盘入库编组为例:后悬架托盘有3种平台专用托盘,分别存储到各自专用存储线中;后悬架托盘在底盘线完成合装装配后并在进入托盘立体库前,通过托盘上安装的RFID电子标签和线体上安装的接近开关对托盘型号进行电子和物理双重识别;如RFID读写头与接近开关判断的托盘型号一致,立体库系统通知提升机将托盘转运到托盘专用存储线中,如RFID读写头与接近开关判断的托盘型号不一致,立体库停止工作并报警,同时人工查找托盘出错原因。托盘采用RFID和物理结构双重识别,提高了托盘的入库准确率。
3.具备手动调整出库托盘编组功能
总装生产车序因突发情况变化时,需人工调整托盘出库车序。
4.质量追溯功能
我们搭建了立体库质量追溯系统,在托盘上安装RFID电子标签,实现每个托盘编号与生产整车VIN码绑定,并存储到立体库工控机中。由于托盘编号和整车VIN码均具有唯一性,当检测线检测出前后轮外倾值不合格时,根据车身VIN码可以在立体库工控机中迅速查找到生产该车的托盘,锁定托盘后用托盘检具对托盘进行检测,判断是否是托盘问题。制作前、后悬架标准托盘并放至立体库检具架。当出现批量外倾不合格车辆时,用标准托盘进行装配。如外倾值合格则为托盘问题,否则从产品质量问题入手。
托盘立体库方案虚拟评审
一汽轿车应用数字化仿真技术对总装底盘柔性化生产准备方案进行了仿真分析,仿真过程中运动部件如果干涉,程序字体会自动变红并提示干涉量。利用该功能,通过模拟前、后悬架托盘在立体库中的实际工作轨迹,检验立体库的通过性和干涉性,从而验证方案的可行性。以新增托盘立体库前悬架托盘工艺方案虚拟评审为例:在立体库仿真环境中对设备关键生准点(20个关键评审点)进行极限参数设定。通过方案仿真评审,实现方案制定、交流、评审和校对可视化,提高生产准备的准确性和效率。
结语
一汽轿车前、后悬架托盘立体库现已投入使用一年多,成功解决了多平台车型的总装底盘合装柔性化生产的瓶颈问题,同时在装配过程中保证了前束、外倾等关键参数精度,在质量、进度和成本上也得到了有效的控制。
托盘立体库在总装领域的应用越来越成熟,也越来越广泛,通过应用托盘立体库技术,一汽轿车积累了柔性化生产、底盘合装、立体库、虚拟仿真和质量追溯等方面的经验,在现有工厂改造以及新工厂建设中,这些经验可以扩展应用到线束存储线、车身存储线、物料分拣和物料自动输送等区域,可以实现减少人员和厂房面积、提高自动化程度和装配质量等方面的改善,同时达到公司降低成本、提高质量和劳动生产率的目标。
- 下一篇:沃克斯豪尔展示新款概念车 采用全新设计风格
- 上一篇:汽车仪表盘UI设计
编辑推荐
最新资讯
-
埃马克德国总部迎来中国社科院工业经
2025-04-15 09:40
-
埃马克这项全新应用即将在CIMT惊艳首
2025-04-15 09:37
-
展会预告 | 2025CIMT中国国际机床展
2025-04-11 14:44
-
航空发动机维修工装精准建模,3D扫描
2025-04-11 14:43
-
高歌猛进,奔赴“双碳”——比亚迪叉
2025-04-10 10:09