轿车变速器倒挡齿轮的冷精密成形
2018-06-19 08:57:21· 来源:锻造与冲压
随着工业的发展,人们对齿轮齿形的精密成形的关注与期待越来越高,尤其是在世界制造业战略性转变期间,人们认识到只有精密成形齿轮才能更好满足传动系统重量轻、强度高、低成本制造的要求,势将逐步取代切削齿轮,这是完全符合环保要求的“绿色”制造。当前迫于原材料价格上涨和产品不断降价的双重压力,零部件加工企业必须进一步控制成本,提高材料利用率,不断开发新的产品和采用新的生产技术。
随着工业的发展,人们对齿轮齿形的精密成形的关注与期待越来越高,尤其是在世界制造业战略性转变期间,人们认识到只有精密成形齿轮才能更好满足传动系统重量轻、强度高、低成本制造的要求,势将逐步取代切削齿轮,这是完全符合环保要求的“绿色”制造。当前迫于原材料价格上涨和产品不断降价的双重压力,零部件加工企业必须进一步控制成本,提高材料利用率,不断开发新的产品和采用新的生产技术。
结合多年来利用冷温热精密成形工艺开发各种精密成形件(即精锻件)的经验,我公司成功实现了汽车变速器倒挡齿轮的“绿色”锻造,采用温锻预制坯冷精密成形工艺成功生产变速器倒挡齿轮,轮齿精度达到了GB/T 10095.1-2008 7级精度。
倒挡齿轮是汽车后退啮合传动的关键零件
汽车变速器倒挡齿轮是汽车后退时啮合传动的关键零件,在齿轮的每一个轮齿上设有倒棱,即在轮齿表面带有30`左右的倒锥。倒锥虽小,其作用非常重要,一方面确保汽车行驶稳定,防止变速器中齿轮滑挡,同时保证在倒挡时能够顺畅的挂入挡位。一般来说,轿车变速器上最为薄弱的零件也是倒挡齿轮。为了提高倒挡齿轮强度而随意改变模数是不可能的,这是因为轿车的外形尺寸固定,某一组啮合齿轮的中心距也应该是固定的,不能随意变动。如果要保证中心距不发生变化,又会影响到齿轮传动比。而通过采用精密成形倒挡齿轮,提高了齿轮的传动精度,保证了整车的质量,就能使该问题很容易得到解决。
与切削齿轮的轮齿相比,精密成形倒挡齿轮的轮齿金属纤维流线连续,弯曲疲劳强度提高20%~30%,寿命大大提高。轿车行驶时,在齿轮啮合传动过程中,它不仅避免了切削齿轮轮齿齿根容易断裂造成的事故和所产生的经济损失,也为主机生产厂大大节约了生产成本和市场成本。
国内轿车行业只有少数企业生产的变速箱中采用精密成形倒挡齿轮,然而,由于其生产工艺复杂,产品质量不能得到保证,因而绝大部分进口或由外资企业生产,国内真正实现其批量生产的企业极少,因此倒挡齿轮的市场前景非常好。
倒挡齿轮结构特征及其生产过程设计
倒挡齿轮是一种带毂直齿轮。某轿车变速器用倒挡齿轮零件实物照片如图1所示,该零件套装在传动轴上,中空。小端为短轴,大端为齿轮,齿轮端面有20个齿,其零件图如图2所示。
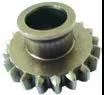
图1 某轿车变速器用倒挡齿轮
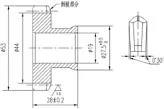
图2 某轿车变速器倒挡齿轮零件图
根据压力加工原理和我们的实际经验,该零件采用压力加工成形是没有问题的。在倒挡齿轮被汽车设计者设计出来以后,一般企业的生产工艺就是先生产不将齿轮齿形加工出来的锻坯,然后进行机械加工外形尺寸和热处理。后来才发展成将齿轮齿形模锻成形出来。然而,普通热模锻件的齿形精度往往达不到使用要求或者质量不稳定。即使生产出来勉强装配到汽车上也不能满足使用要求,在汽车行驶过程中噪声很大,转向费力,不灵活。
后来人们采用冷锻成形,由于冷锻力太大、对设备的吨位要求太大且模具寿命低,以及预制坯工艺过程复杂等一系列原因在企业生产中很少使用。因此人们在热锻过程中不断总结经验,对坯料的加热温度、模锻温度及模锻后的冷却过程提出严格要求,在一定温度范围内将该产品的齿形锻出,这就是所谓的温锻。
随着汽车工业的发展,人们对温锻件齿形的精度提出更高的要求。我公司就是在温锻件的基础上再增加一道后续冷成形工艺,即采用温锻高精度制坯,然后进行冷成形。通过温锻实现较高的塑性变形将齿形锻出,通过微量变形的冷成形提高温锻齿形精度和表面质量。使倒挡齿轮温锻件(预成形件)产品的齿形精度满足技术要求。
其工艺路线大致为:下料→制坯→温锻预成形→退火→抛砂→润滑处理→冷精密成形→车端面、去毛刺→倒锥挤压成形→机加工→渗碳淬火。
倒挡齿轮轮齿的传统生产方式是先使用滚齿或插齿工艺粗加工齿形,再用剃齿工艺精加工齿形提高轮齿齿形精度;对于精度要求高的轮齿,热处理渗碳后还需作磨齿、珩齿,这些加工需要昂贵的专业设备,生产效率低,很难满足市场需要。
采用精密成形工艺生产倒挡齿轮,不需要增加投资,不需要采用切齿、倒棱加工设备,将机械加工难以实现的需要倒棱的轮齿成形,而且齿部也满足精度要求,质量稳定,不但满足人们轻松驾驶,行驶中噪声低、容易换挡的要求,而且能大幅度降低生产成本。
倒挡齿轮的数值模拟分析
温锻预成形数值模拟
为给后续冷精密成形工艺制造高精度预制坯,设计温锻预成形件图。温锻预成形件图的设计也是保证倒挡齿轮冷精密成形开发成功的关键。在设计温锻预成形件图时,要根据倒挡齿轮的结构特征判断坯料在温锻预成形时的金属流动特征和温锻预成形后温锻预成形件冷却时的收缩量和弹性变形量,合理给出后续冷精密成形时的余量,特别是倒锥工序余量及其分布。
利用UG建立该模型如图3所示。由UG分析功能计算出该模拟温锻预成形件体积,按体积不变原则,确定毛坯尺寸。在生产实践中确定坯料尺寸的过程也是一个很重要的环节。温锻模具模型也是采用UG软件建立的。利用DEFORM-3D软件进行数值模拟分析,设置参数如下:材料:AISI-5120(锻件材质为20CrMnTiH);坯料温度:(1150±15)℃;模具预热温度:200℃左右;摩擦因数:0.3;数值模拟得到的变形过程如图4所示。

图3 倒挡齿轮预锻温锻件模型
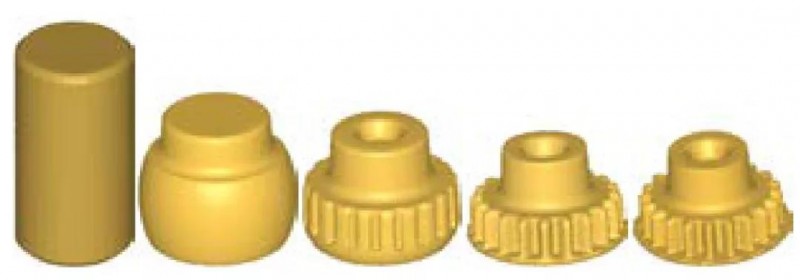
图4 预锻温锻数值模拟的塑性变形过程
结合我厂的实际情况,为利于齿部充填饱满,我们在温锻预成形件时,采用两个主要工步成形,即第一步镦粗成形和第二步镦挤齿形。镦粗成形的目的为合理分配毛坯体积,便于第二步镦挤齿形时的定位及齿部充填。
将加热到(1150±5)℃的毛坯镦粗后,放入带齿模芯的模膛之中;毛坯继续镦挤,此时毛坯的温度大约为1100℃左右。金属在模膛内产生轴向、径向流动,逐步充填轮毂和齿部型腔,最终充填轮齿齿部、棱部,完成温锻预成形件的成形。
图5所示为温锻预成形过程的流动矢量图,其运动矢量分布均匀、合理。图6所示为数值模拟的温锻预成形过程压力—时间曲线,成形载荷约3600kN。
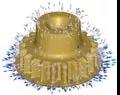
图5 温锻预成形件材料成形过程流动矢量图
冷精密成形数值模拟
温锻预成形件设计的合理与否,和后续冷精密成形能否获得合格产品的关系极大。温锻预成形件设计不合理得到的温锻预成形件的质量太低,就可能收不到理想的冷精密成形效果。其关键是要保证在冷精密成形过程中的受力和金属流动尽量均匀,要保证能提高轮齿的齿形精度。
将温锻预成形件模型重新划分网格,设置冷精密成形模拟所需参数,数值模拟分析室温下轮齿的金属流动,得到图7所示的冷精密成形件。在冷精密成形过程中,上冲头下压,齿部材料被镦挤完全充满轮齿型腔,满足高精度齿形成形。图8所示为冷精密成形结束时成形件的等效应变图。
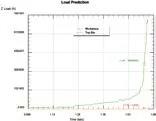
图6 模拟温锻预成形终了时的压力—时间曲线
倒挡齿轮的开发试制
下料、制坯
为保证毛坯内部组织性能均匀和消除热轧棒材表面缺陷,对棒材表面车削剥皮。精密锻造对坯料的尺寸要求高,重量公差在±3g。对坯料尺寸的高精度要求是保证精密锻造过程工艺正常和精锻后的产品质量稳定的重要条件。
下料采用全自动带锯床,带锯床优点有:机床上锯带的速度可以无限制调整,利用镀硬铬圆柱来调整带锯床锯架的上升与下降,锯切参数数字通过可编程控制器(PLC)方便快捷设定,灵活设定、转变锯切模式,非常灵活的人机界面,在指定范围内,锯床的进给可以进行调速,机床设置参数完成后,通过机械、电气、液压,具有自动夹紧、自动进刀、切割完毕自动快速上升(即退刀)、自动送料的功能,无需人工操作,送料定位误差小于0.02mm,定位非常精确,可以满足毛坯尺寸精度要求,一致性较好,同时加工效率较高,综合成本较低。
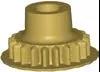
图7 冷精密成形数值模拟件
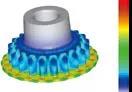
图8 冷精密成形数值模拟件的等效应变
制坯工艺方法有:车床单件加工和全自动剥皮、磨外圆生产线,全自动剥皮、磨外圆生产线加工质量和效率都比车床单件加工高,且剥皮前有校直工序,所以加工量可以减小,减少材料浪费,是精密锻造未来应用方向,后续倒角采用车床和全自动倒角机。
温锻预成形
根据数值模拟分析得到的负载,选取我公司FP-600型热模锻机械压力机如图9所示。热模锻机械压力机精度高,刚性足,所生产的温锻预成形件可以满足后续倒挡齿轮冷精密成形要求。图10反映了温锻预成形变形过程,产品无折叠、裂纹缺陷。设备仪器表盘吨位显示值范围在3300~3600kN,与数值模拟得到的数据接近。
在实际锻造过程中,温锻预成形分两步完成。必须控制温锻预成形需要的第一步预制件的形状。倘若温锻预成形需要的第一步预制件的形状不稳定,例如材料过早流动产生飞边,将会影响第二步温锻预成形件齿部充填不能满足后续冷精密成形的要求,也导致第二步温锻预成形时负载急剧上升,影响模具寿命和设备维修周期。第二步温锻预成形件一定要满足后续冷精密成形对坯料的要求。
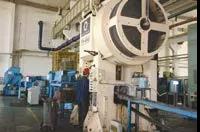
图9 FP-600型热模锻机械压力机
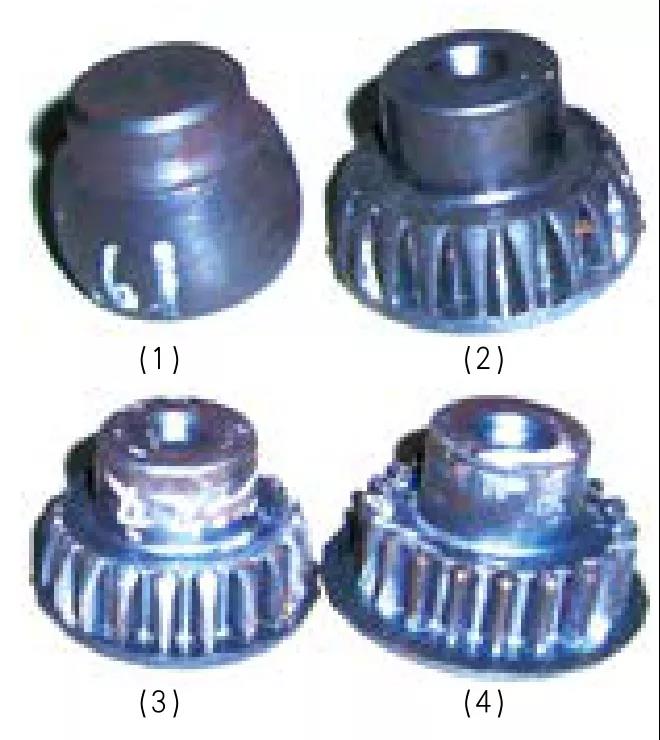
图10 倒挡齿轮温锻预成形变形过程
生产时,将沾附有石墨的坯料在中频感应加热装置(KGPS03-250/2.5)中加热至750~800℃,这时产生的氧化较少,几乎无氧化现象发生。温锻预成形模具在加工制造时,模具模膛表面粗糙度要好。防止温锻预成形时变形力增加,温锻预成形后脱模困难,齿面划伤。
将温锻预成形件做流线分析,可以看出整个金属流线顺畅、对称,没有流线间的折叠,如图11所示,说明了倒挡齿轮温锻预锻过程材料流动合理。
冷精密成形
将温锻预锻件退火处理后,清理表面、进行润滑处理,然后放入冷精密成形模具内,通过镦挤成形使齿部充填饱满,提高齿部精度,获得较好的齿面粗糙度。
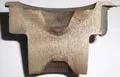
图11 温锻预锻件金属流线
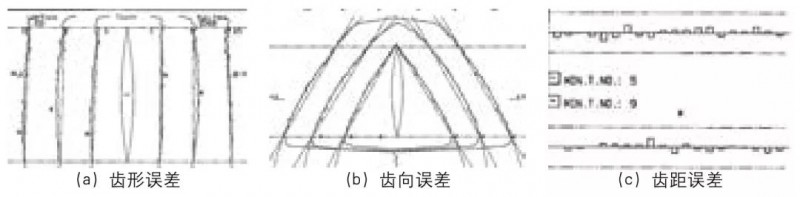
图12 精密成形件齿形精密测量结果
冷精密成形过程,对模具的制作精度要求高,对模膛精度要求更高,例如齿轮轮齿的制造精度要达到5~6级,型腔抛光处理。
倒锥成形
将冷精密成形后的锻件车端面去毛刺,进行表面润滑处理,然后放入模具模膛挤压成形30`的倒锥。由于该锥度为30`,精度要求高。外国人曾对我国长时间保守秘密。我国汽车的倒挡齿轮在相当长的一个历史时期是没有倒锥的,即倒锥为零,致使我国汽车驾驶性能的一项重要指标长时间处于落后。
因为这个数据30`很小,人们一开始用手感不容易发现,后来发现了觉得不好用机械加工,而且30`的量值很小,也没法测量。而倒锥的作用非常重要,它对汽车的行驶性能和安全性影响很大。因为没有倒锥,造成驾驶过程中换挡不灵活,不能顺畅挂入挡位;而在行驶的过程中,变速器中齿轮容易滑挡,又影响行驶过程稳定。
该倒锥成形同样要求模具的轮齿模膛加工精度高,一般轮齿精度要求达到4级以上,因为它直接决定了锻件的齿形、齿向、齿距误差。这样,它就要求有高精度的加工模具设备和量具,还要有高精度高刚度的锻压设备,这样才能有效地保证产品精度和生产过程稳定。
先对锻件冷精密成形过程数值模拟,确认成形方案可行后,进行初次开模;再根据冷精密成形件的轮齿尺寸、倒锥后锻件轮齿尺寸及齿形、齿向、齿距误差,对温锻预成形模、冷精密成形模、倒锥挤压模模膛的轮齿尺寸做适当的工艺调整。
计算机模拟无疑是一个很重要的工具,在开发产品时其作用不可低估。然而,有关现场经验非常重要。冷精密成形模和倒锥挤压成形模开模往往需要2~3次的工艺调整才能最终满足产品要求。
图12为倒锥后倒挡齿轮齿部的精密测量结果,a是齿形误差的检查结果,左右齿面最大偏差为0.009 μm,b是齿向误差的检测结果,左右齿面最大偏差为0.0065μm,c是累积偏差和单一偏差的检测结果,累积偏差和单一偏差分别为0.014μm和0.006μm,该齿形检测报告结果显示,我公司开发生产的倒挡齿轮的齿形精度完全符合图纸要求。表1是倒挡齿轮齿形检查结果汇总。
表1 倒挡齿轮精密成形件齿形检查结果
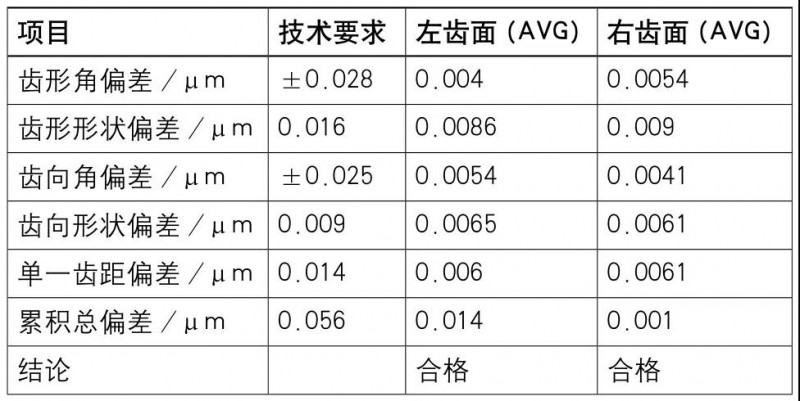
结束语
我公司生产的汽车变速器倒挡齿轮现已通过了台架试验、破坏性试验和路试等,有关试验数据和实际使用效果远好于切削加工倒挡齿轮,得到客户认可。
作者简介 赵军华,模具车间主任,工程师,主要从事模具技术开发及生产管理,参与完成的“双离合器变速器齿轮冷温精密近净成形制造技术开发与应用”项目获得江苏省科学技术奖二等奖,参与国家重大专项和省科技成果转化专项资金项目各1项,拥有3项专利。
结合多年来利用冷温热精密成形工艺开发各种精密成形件(即精锻件)的经验,我公司成功实现了汽车变速器倒挡齿轮的“绿色”锻造,采用温锻预制坯冷精密成形工艺成功生产变速器倒挡齿轮,轮齿精度达到了GB/T 10095.1-2008 7级精度。
倒挡齿轮是汽车后退啮合传动的关键零件
汽车变速器倒挡齿轮是汽车后退时啮合传动的关键零件,在齿轮的每一个轮齿上设有倒棱,即在轮齿表面带有30`左右的倒锥。倒锥虽小,其作用非常重要,一方面确保汽车行驶稳定,防止变速器中齿轮滑挡,同时保证在倒挡时能够顺畅的挂入挡位。一般来说,轿车变速器上最为薄弱的零件也是倒挡齿轮。为了提高倒挡齿轮强度而随意改变模数是不可能的,这是因为轿车的外形尺寸固定,某一组啮合齿轮的中心距也应该是固定的,不能随意变动。如果要保证中心距不发生变化,又会影响到齿轮传动比。而通过采用精密成形倒挡齿轮,提高了齿轮的传动精度,保证了整车的质量,就能使该问题很容易得到解决。
与切削齿轮的轮齿相比,精密成形倒挡齿轮的轮齿金属纤维流线连续,弯曲疲劳强度提高20%~30%,寿命大大提高。轿车行驶时,在齿轮啮合传动过程中,它不仅避免了切削齿轮轮齿齿根容易断裂造成的事故和所产生的经济损失,也为主机生产厂大大节约了生产成本和市场成本。
国内轿车行业只有少数企业生产的变速箱中采用精密成形倒挡齿轮,然而,由于其生产工艺复杂,产品质量不能得到保证,因而绝大部分进口或由外资企业生产,国内真正实现其批量生产的企业极少,因此倒挡齿轮的市场前景非常好。
倒挡齿轮结构特征及其生产过程设计
倒挡齿轮是一种带毂直齿轮。某轿车变速器用倒挡齿轮零件实物照片如图1所示,该零件套装在传动轴上,中空。小端为短轴,大端为齿轮,齿轮端面有20个齿,其零件图如图2所示。
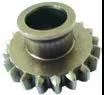
图1 某轿车变速器用倒挡齿轮
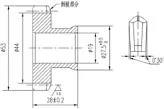
图2 某轿车变速器倒挡齿轮零件图
根据压力加工原理和我们的实际经验,该零件采用压力加工成形是没有问题的。在倒挡齿轮被汽车设计者设计出来以后,一般企业的生产工艺就是先生产不将齿轮齿形加工出来的锻坯,然后进行机械加工外形尺寸和热处理。后来才发展成将齿轮齿形模锻成形出来。然而,普通热模锻件的齿形精度往往达不到使用要求或者质量不稳定。即使生产出来勉强装配到汽车上也不能满足使用要求,在汽车行驶过程中噪声很大,转向费力,不灵活。
后来人们采用冷锻成形,由于冷锻力太大、对设备的吨位要求太大且模具寿命低,以及预制坯工艺过程复杂等一系列原因在企业生产中很少使用。因此人们在热锻过程中不断总结经验,对坯料的加热温度、模锻温度及模锻后的冷却过程提出严格要求,在一定温度范围内将该产品的齿形锻出,这就是所谓的温锻。
随着汽车工业的发展,人们对温锻件齿形的精度提出更高的要求。我公司就是在温锻件的基础上再增加一道后续冷成形工艺,即采用温锻高精度制坯,然后进行冷成形。通过温锻实现较高的塑性变形将齿形锻出,通过微量变形的冷成形提高温锻齿形精度和表面质量。使倒挡齿轮温锻件(预成形件)产品的齿形精度满足技术要求。
其工艺路线大致为:下料→制坯→温锻预成形→退火→抛砂→润滑处理→冷精密成形→车端面、去毛刺→倒锥挤压成形→机加工→渗碳淬火。
倒挡齿轮轮齿的传统生产方式是先使用滚齿或插齿工艺粗加工齿形,再用剃齿工艺精加工齿形提高轮齿齿形精度;对于精度要求高的轮齿,热处理渗碳后还需作磨齿、珩齿,这些加工需要昂贵的专业设备,生产效率低,很难满足市场需要。
采用精密成形工艺生产倒挡齿轮,不需要增加投资,不需要采用切齿、倒棱加工设备,将机械加工难以实现的需要倒棱的轮齿成形,而且齿部也满足精度要求,质量稳定,不但满足人们轻松驾驶,行驶中噪声低、容易换挡的要求,而且能大幅度降低生产成本。
倒挡齿轮的数值模拟分析
温锻预成形数值模拟
为给后续冷精密成形工艺制造高精度预制坯,设计温锻预成形件图。温锻预成形件图的设计也是保证倒挡齿轮冷精密成形开发成功的关键。在设计温锻预成形件图时,要根据倒挡齿轮的结构特征判断坯料在温锻预成形时的金属流动特征和温锻预成形后温锻预成形件冷却时的收缩量和弹性变形量,合理给出后续冷精密成形时的余量,特别是倒锥工序余量及其分布。
利用UG建立该模型如图3所示。由UG分析功能计算出该模拟温锻预成形件体积,按体积不变原则,确定毛坯尺寸。在生产实践中确定坯料尺寸的过程也是一个很重要的环节。温锻模具模型也是采用UG软件建立的。利用DEFORM-3D软件进行数值模拟分析,设置参数如下:材料:AISI-5120(锻件材质为20CrMnTiH);坯料温度:(1150±15)℃;模具预热温度:200℃左右;摩擦因数:0.3;数值模拟得到的变形过程如图4所示。

图3 倒挡齿轮预锻温锻件模型
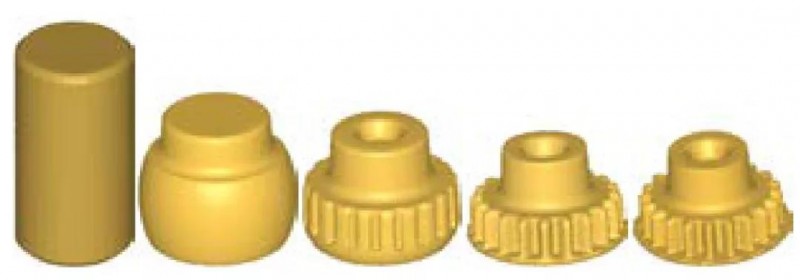
图4 预锻温锻数值模拟的塑性变形过程
结合我厂的实际情况,为利于齿部充填饱满,我们在温锻预成形件时,采用两个主要工步成形,即第一步镦粗成形和第二步镦挤齿形。镦粗成形的目的为合理分配毛坯体积,便于第二步镦挤齿形时的定位及齿部充填。
将加热到(1150±5)℃的毛坯镦粗后,放入带齿模芯的模膛之中;毛坯继续镦挤,此时毛坯的温度大约为1100℃左右。金属在模膛内产生轴向、径向流动,逐步充填轮毂和齿部型腔,最终充填轮齿齿部、棱部,完成温锻预成形件的成形。
图5所示为温锻预成形过程的流动矢量图,其运动矢量分布均匀、合理。图6所示为数值模拟的温锻预成形过程压力—时间曲线,成形载荷约3600kN。
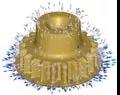
图5 温锻预成形件材料成形过程流动矢量图
冷精密成形数值模拟
温锻预成形件设计的合理与否,和后续冷精密成形能否获得合格产品的关系极大。温锻预成形件设计不合理得到的温锻预成形件的质量太低,就可能收不到理想的冷精密成形效果。其关键是要保证在冷精密成形过程中的受力和金属流动尽量均匀,要保证能提高轮齿的齿形精度。
将温锻预成形件模型重新划分网格,设置冷精密成形模拟所需参数,数值模拟分析室温下轮齿的金属流动,得到图7所示的冷精密成形件。在冷精密成形过程中,上冲头下压,齿部材料被镦挤完全充满轮齿型腔,满足高精度齿形成形。图8所示为冷精密成形结束时成形件的等效应变图。
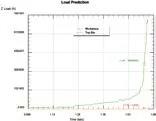
图6 模拟温锻预成形终了时的压力—时间曲线
倒挡齿轮的开发试制
下料、制坯
为保证毛坯内部组织性能均匀和消除热轧棒材表面缺陷,对棒材表面车削剥皮。精密锻造对坯料的尺寸要求高,重量公差在±3g。对坯料尺寸的高精度要求是保证精密锻造过程工艺正常和精锻后的产品质量稳定的重要条件。
下料采用全自动带锯床,带锯床优点有:机床上锯带的速度可以无限制调整,利用镀硬铬圆柱来调整带锯床锯架的上升与下降,锯切参数数字通过可编程控制器(PLC)方便快捷设定,灵活设定、转变锯切模式,非常灵活的人机界面,在指定范围内,锯床的进给可以进行调速,机床设置参数完成后,通过机械、电气、液压,具有自动夹紧、自动进刀、切割完毕自动快速上升(即退刀)、自动送料的功能,无需人工操作,送料定位误差小于0.02mm,定位非常精确,可以满足毛坯尺寸精度要求,一致性较好,同时加工效率较高,综合成本较低。
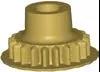
图7 冷精密成形数值模拟件
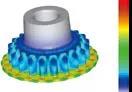
图8 冷精密成形数值模拟件的等效应变
制坯工艺方法有:车床单件加工和全自动剥皮、磨外圆生产线,全自动剥皮、磨外圆生产线加工质量和效率都比车床单件加工高,且剥皮前有校直工序,所以加工量可以减小,减少材料浪费,是精密锻造未来应用方向,后续倒角采用车床和全自动倒角机。
温锻预成形
根据数值模拟分析得到的负载,选取我公司FP-600型热模锻机械压力机如图9所示。热模锻机械压力机精度高,刚性足,所生产的温锻预成形件可以满足后续倒挡齿轮冷精密成形要求。图10反映了温锻预成形变形过程,产品无折叠、裂纹缺陷。设备仪器表盘吨位显示值范围在3300~3600kN,与数值模拟得到的数据接近。
在实际锻造过程中,温锻预成形分两步完成。必须控制温锻预成形需要的第一步预制件的形状。倘若温锻预成形需要的第一步预制件的形状不稳定,例如材料过早流动产生飞边,将会影响第二步温锻预成形件齿部充填不能满足后续冷精密成形的要求,也导致第二步温锻预成形时负载急剧上升,影响模具寿命和设备维修周期。第二步温锻预成形件一定要满足后续冷精密成形对坯料的要求。
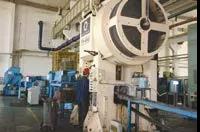
图9 FP-600型热模锻机械压力机
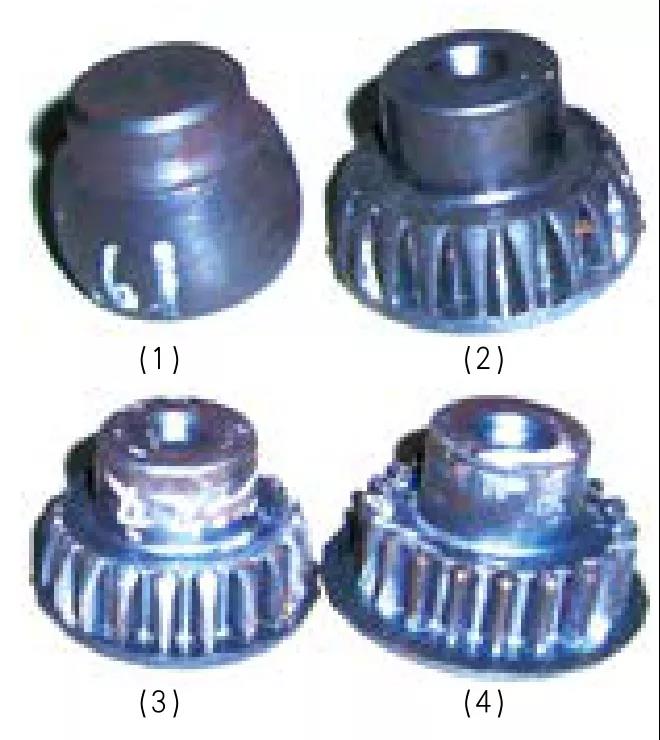
图10 倒挡齿轮温锻预成形变形过程
生产时,将沾附有石墨的坯料在中频感应加热装置(KGPS03-250/2.5)中加热至750~800℃,这时产生的氧化较少,几乎无氧化现象发生。温锻预成形模具在加工制造时,模具模膛表面粗糙度要好。防止温锻预成形时变形力增加,温锻预成形后脱模困难,齿面划伤。
将温锻预成形件做流线分析,可以看出整个金属流线顺畅、对称,没有流线间的折叠,如图11所示,说明了倒挡齿轮温锻预锻过程材料流动合理。
冷精密成形
将温锻预锻件退火处理后,清理表面、进行润滑处理,然后放入冷精密成形模具内,通过镦挤成形使齿部充填饱满,提高齿部精度,获得较好的齿面粗糙度。
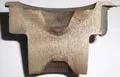
图11 温锻预锻件金属流线
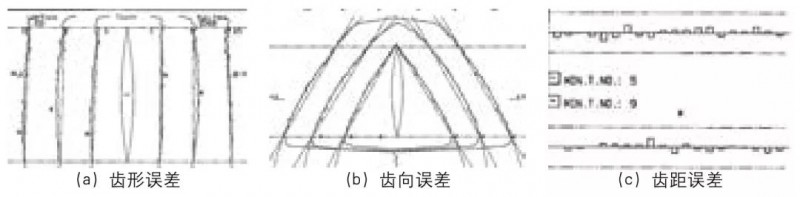
图12 精密成形件齿形精密测量结果
冷精密成形过程,对模具的制作精度要求高,对模膛精度要求更高,例如齿轮轮齿的制造精度要达到5~6级,型腔抛光处理。
倒锥成形
将冷精密成形后的锻件车端面去毛刺,进行表面润滑处理,然后放入模具模膛挤压成形30`的倒锥。由于该锥度为30`,精度要求高。外国人曾对我国长时间保守秘密。我国汽车的倒挡齿轮在相当长的一个历史时期是没有倒锥的,即倒锥为零,致使我国汽车驾驶性能的一项重要指标长时间处于落后。
因为这个数据30`很小,人们一开始用手感不容易发现,后来发现了觉得不好用机械加工,而且30`的量值很小,也没法测量。而倒锥的作用非常重要,它对汽车的行驶性能和安全性影响很大。因为没有倒锥,造成驾驶过程中换挡不灵活,不能顺畅挂入挡位;而在行驶的过程中,变速器中齿轮容易滑挡,又影响行驶过程稳定。
该倒锥成形同样要求模具的轮齿模膛加工精度高,一般轮齿精度要求达到4级以上,因为它直接决定了锻件的齿形、齿向、齿距误差。这样,它就要求有高精度的加工模具设备和量具,还要有高精度高刚度的锻压设备,这样才能有效地保证产品精度和生产过程稳定。
先对锻件冷精密成形过程数值模拟,确认成形方案可行后,进行初次开模;再根据冷精密成形件的轮齿尺寸、倒锥后锻件轮齿尺寸及齿形、齿向、齿距误差,对温锻预成形模、冷精密成形模、倒锥挤压模模膛的轮齿尺寸做适当的工艺调整。
计算机模拟无疑是一个很重要的工具,在开发产品时其作用不可低估。然而,有关现场经验非常重要。冷精密成形模和倒锥挤压成形模开模往往需要2~3次的工艺调整才能最终满足产品要求。
图12为倒锥后倒挡齿轮齿部的精密测量结果,a是齿形误差的检查结果,左右齿面最大偏差为0.009 μm,b是齿向误差的检测结果,左右齿面最大偏差为0.0065μm,c是累积偏差和单一偏差的检测结果,累积偏差和单一偏差分别为0.014μm和0.006μm,该齿形检测报告结果显示,我公司开发生产的倒挡齿轮的齿形精度完全符合图纸要求。表1是倒挡齿轮齿形检查结果汇总。
表1 倒挡齿轮精密成形件齿形检查结果
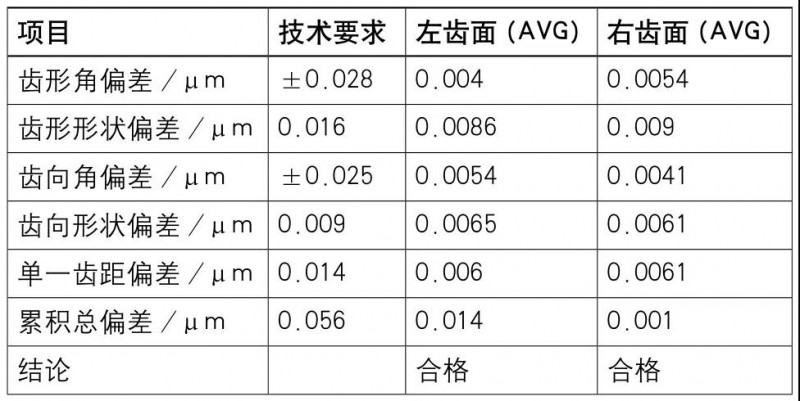
结束语
我公司生产的汽车变速器倒挡齿轮现已通过了台架试验、破坏性试验和路试等,有关试验数据和实际使用效果远好于切削加工倒挡齿轮,得到客户认可。
作者简介 赵军华,模具车间主任,工程师,主要从事模具技术开发及生产管理,参与完成的“双离合器变速器齿轮冷温精密近净成形制造技术开发与应用”项目获得江苏省科学技术奖二等奖,参与国家重大专项和省科技成果转化专项资金项目各1项,拥有3项专利。
- 下一篇:关于自动化的发展层次
- 上一篇:沃克斯豪尔展示新款概念车 采用全新设计风格
编辑推荐
最新资讯
-
杜尔中国海外项目-Stellantis 集团摩
2025-03-20 11:59
-
3D扫描仪新品 | KSCAN-X 重新定义工
2025-03-20 11:58
-
三维扫描仪新品 | NimbleTrack-CR 极
2025-03-20 11:53
-
浙江省委书记王浩调研思看科技
2025-03-19 08:33
-
旭化成精细化工(南通)新工厂竣工
2025-03-18 10:49