宝沃汽车创新建设智能工厂与智慧物流系统
2018-06-26 15:40:40· 来源:物流技术与应用
宝沃汽车率先在国内汽车行业实现了工业4.0智能工厂部署,并入选工信部发布的“2017年中德智能制造合作试点示范项目”。作为智能工厂的重要组成部分,宝沃采用多项创新技术建设智慧供应链及物流系统创新,亮点颇多,值得借鉴。
宝沃汽车率先在国内汽车行业实现了工业4.0智能工厂部署,并入选工信部发布的“2017年中德智能制造合作试点示范项目”。作为智能工厂的重要组成部分,宝沃采用多项创新技术建设智慧供应链及物流系统创新,亮点颇多,值得借鉴。
随着《中国制造2025》战略的推广与实施,位于北京的宝沃汽车采用 “德国工业4.0”智能制造模式,率先在国内汽车行业建设智能工厂,以领先全球的智能制造体系入选工信部发布的“2017年中德智能制造合作试点示范项目”。宝沃汽车北京工厂实现智能制造的背后,离不开智慧物流系统及敏捷、透明化供应链体系的强大支撑力。日前,本刊记者采访了宝沃汽车集团物流规划部助理高级经理曹晓刚,请他分享了宝沃汽车智能工厂与物流系统的规划建设情况以及专业经验。
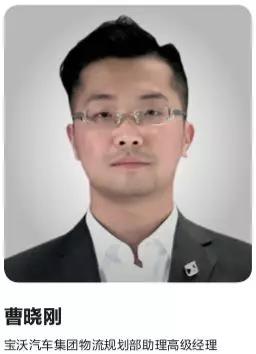
打造柔性智能工厂
2013年3月,宝沃汽车集团按照德国工业4.0标准开始建设柔性智能工厂。经过团队的精心规划设计,创新研发与严谨实施,2017年宝沃汽车柔性智能工厂正式亮相;同年9月该工厂被工信部正式评为“中德智能制造合作试点示范项目”;同年11月该工厂被科尔尼汽车商业评论授予“中国最佳工厂—柔性卓越奖”。
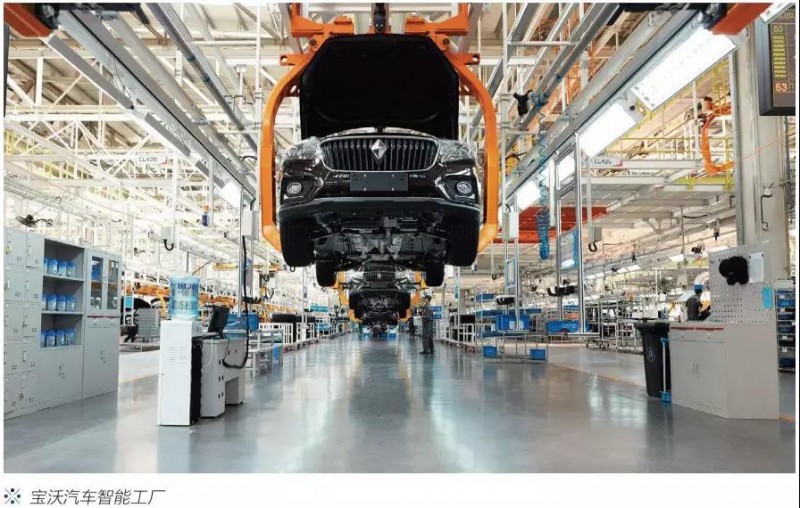
1.工厂概况
整个工厂占地面积110万m2,2015年6月工厂一期项目建设完成,生产节拍达到30JPH,生产能力达18万辆/年;2018年6月二期项目即将建设完成,生产节拍将达60JPH,生产能力将达36万辆/年。之所以说该工厂极具“柔性”,最为直观的体现就是,按照规划,宝沃汽车工厂一条生产线将可生产8种车型,从轿车到SUV,从小型车到大型车,只要整车尺寸不超过5300mm(L)×2000mm(W)×1850mm(H),轴距在2300mm-3200mm之间的车型都能够生产,甚至可支持左/右舵车型、汽油动力、柴油动力、混合动力以及新能源车型。
2.主要布局及功能
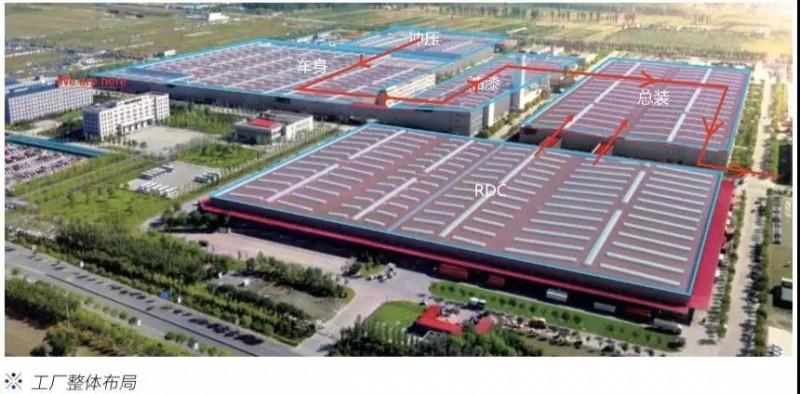
整个工厂包括冲压、车身、油漆、总装四大工艺车间以及RDC(物流分发中心),涵盖了冲压、焊装、涂装、总装、检测、物流、IT等完整的整车生产工艺。各车间主要布局及功能如下:
冲压车间占地面积2.4 万㎡,完成每个车型的23个大型内外覆盖件制造,生产线自动化程度100%。该车间应用TBS双机器人传输系统,提高不同工序间零件搬运的灵活度、负载能力及稳定性;应用线尾自动装箱系统,防止零件变形,减轻了员工作业强度。
车身车间总占地面积9.9万㎡,采用互联机器人、柔性NC定位系统、柔性夹具切换系统、自动化输送系统,标准化工艺体系、三层环网智能管理系统、国际安全标准,主线自动化率95%;采用柔性智能生产线,在同一条生产线可完成8个不同的车型无节拍损失自动切换和混线生产。
油漆车间总面积5.68万㎡,采用高泳透力电泳漆、水性面漆、2K清漆及免中涂喷涂工艺,车身防腐寿命长达12年;采用机器人自动涂胶、内外表面机器人自动喷涂、快速换色系统,快速响应客户对车身颜色的个性化需求;采用沸石转轮+RTO、TNV等废气处理技术,满足最严苛的环保标准。
总装车间总面积6.41万㎡,采用“平台化+个性化”模块化技术、“h”型的生产布局及智能物流系统,满足客户个性化的定制需求:4条SPS地面自动输送线(内饰1/内饰2/车门/仪表),零件自动上线率45%;6条大件空中自动输送线(发动机变速箱/保险杠/前端模块/轮胎/座椅/仪表等大型零件),将物料空中自动直送工位,减少2400m地面人工配送距离,降低地面物流复杂度,防止零件磕碰损伤。
RDC占地面积5万㎡,分为中小件和大件两个库区,主要负责厂内零部件的分装和配送上线。
3.信息系统建设
信息系统对于智能工厂的打造尤为重要,宝沃汽车对此非常重视。结合客户个性化订单,以超级 BOM一车一单为基础,通过ERP系统协同 MES、物流执行系统LES(Logistics Excution System),实现大规模个性化定制生产。常规车型可实时交付客户,个性化订制车型从接到订单开始包括物料准备、生产排产、制造、运输等环节,交付时间最短23天。
其中,ERP系统采用目前全球最新的基于APO on HANA 的内存处理技术,在60JPH生产节拍下,能够在15 分钟内完成排产, 30 分钟内生成物料需求计划(MRP),可实现快速排产和插单,满足大规模个性化定制的要求,比传统技术节省70%时间,目前全球仅宝沃、戴姆勒、沃尔沃在使用这项技术。
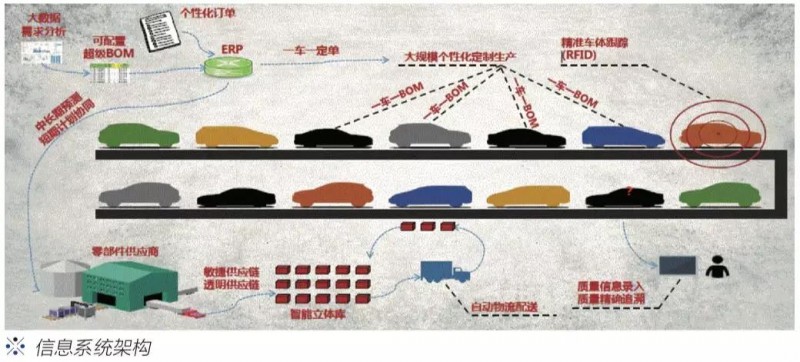
通过MES构建透明工厂,实现基于制造全流程的产线、工位及作业节点的标准化和数字化;采用工业以太网和HMI技术,实现设备互联;对生产计划、质量控制、防错、追溯进行可视化管理;对整车生产制造过程中的工艺数据及参数信息进行生命周期的数据管理。
创新开发的LES系统作为统一的物流执行平台,整合了基于GPS定位技术的运输管理系统、JIS/JIT准时化配送模式、基于RFID无线射频技术的自动化出入库管理、自动化立体库、SPS系统、大件直送等自动化上线技术,从而实现了敏捷、透明的供应链体系,能够满足8车型柔性化的生产物料需求,物流配送准确率100%,供货响应时间缩短80%。
敏捷透明化的供应链
1.循环取货规划
50%以上的供应商集中在江浙沪。限于工厂所处位置以及北京市政规划,宝沃汽车周边无法设立配套零部件产业园。在此条件下,要想降低物流运输成本和零件库存成本,节省库区面积,实现零件全过程在途监控,实施全国循环取货对于提升供应链效率、降低成本显得十分必要。因此,宝沃汽车制定了详细的循环取货机制,并在逐步实施:
对于供货距离60公里以内的本地供应商,直送到工厂;
供货距离300公里以内的京津冀供应商,优先循环取货到工厂;
供货距离1500公里以内的华东、东北供应商,优先循环取货到工厂/VMI库;
供货距离1500公里以上的其他供应商,占比很小,条件具备的循环取货。
2.创新的TWD物料拉动模式
传统的物料拉动模式依赖于现场作业人员,拉动方式粗放,异常频发,供应商装载率低,道口/叉车作业不均衡;宝沃汽车已经对119家供应商推广实施了TWD(层级拉动)模式,由信息系统替代人工,实行MIN/MAX/车辆过点拉动,时间窗合理均衡排布,最终供应商装载率、整体物流效率均大幅度提升。
3.智能入厂协同
受限于厂房面积,宝沃汽车需要严格控制供应商零部件的入厂时间,在时间和空间调度上做的更为精细。为此,通过ETCP、微信、RFID、LES多系统协作,实现了车辆即时扫描、即时排队,保证了入厂车辆均衡稳定,提高了50%作业效率。整套系统为业内首创。
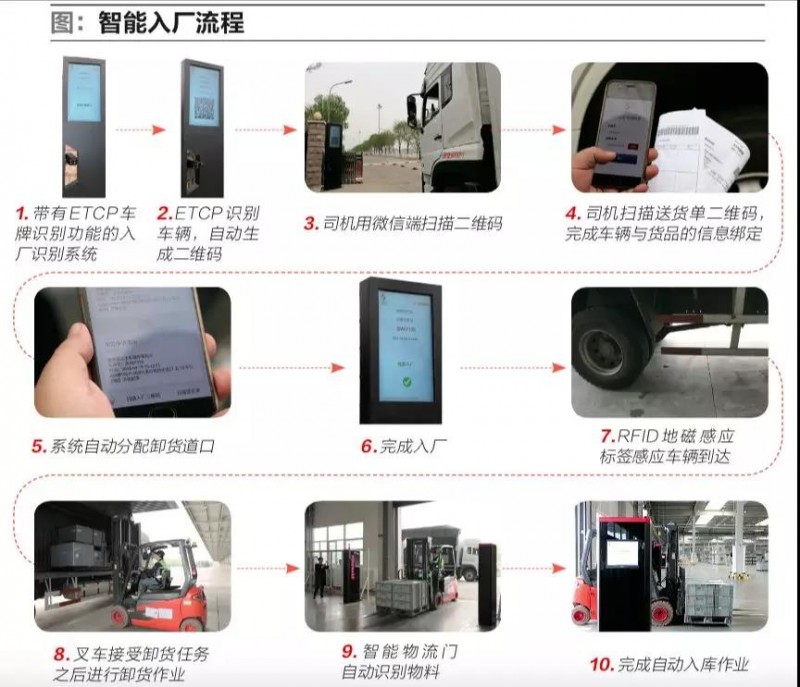
具体作业流程是:卡车到达厂区门口,ETCP车牌自动识别系统识别卡车车牌,并记录卡车出入厂时间;司机登录微信公众号,扫描送货单,送货单与卡车信息完成绑定;司机扫描门口显示屏上的二维码,系统自动分配车位;车辆进入指定区域等待,系统提示卸货时间,车辆到达卸货口;在每个卸货道口均装有RFID地磁感应标签,该标签可以自动识别车位占用及释放情况,进行卸货时间统计以及超时预警提示;车辆到达卸货道口,通过系统提示车载电脑并完成卸货作业。LES系统预提示空箱返空作业,并可统计卡车在厂时间。
4.透明供应链
曹晓刚提到,汽车产品更新换代很快,库存越多损失越大。为了降低供应链上整体库存,保证及时供应,避免断货情况,宝沃汽车将通过透明供应链管理把所有的库存和成本都实现目视化,带动整个产业链升级。
通过SAP、LES、TMS系统协作,实现供应商零部件从出厂到宝沃工厂全过程覆盖,实现低成本、高效率、高协同、透明化的供应物流模式。将LES系统管理范围从工厂扩展到VMI库甚至是零部件供应商,实现供应链全过程信息系统管理,同时与库存预警相结合,保证零件及时供应。
5.实施大数据管理
宝沃汽车与微软(Microsoft)合作,定制化开发了宝沃汽车的LES,目前已完成两期建设,完全可以支持多车型柔性化的物流及供应链业务需求。通过建立PFEP(Plan For Every Parts)数据体系,打造物流大数据系统。将零件信息、供应链物流信息、仓储信息、供应商信息、包装信息、线边信息等资源不断进行整合优化,将所有的信息化设备和系统都与大数据系统关联,并进行大数据分析。
6. 循环环保包装应用
宝沃汽车推动零部件物流全程应用循环围板箱,尺寸规格标准,便于仓储、运输等,提高了物流效率;比采用金属料架成本低;顶盖、底托为HDPE(低压高密度聚乙烯),围板为PP(聚丙烯)蜂窝板,材料环保。
智慧物流系统及装备
智慧物流系统与装备的创新应用是满足生产需求、保证物流效率的有效举措。曹晓刚坦言,想要满足8个车型的高效率混线生产对物流所带来的压力非常大。在宝沃汽车高层领导对物流系统建设的重视与支持下,经过不断的探索与实践,目前部分智慧物流系统及装备已经投入应用,还有部分项目正在实施。
1.SPS智能拣选系统
SPS智能拣选系统在汽车行业得到了普遍应用,但是宝沃汽车的SPS智能拣选系统有着独特的创新点,极度彰显了柔性化和智能化特点。
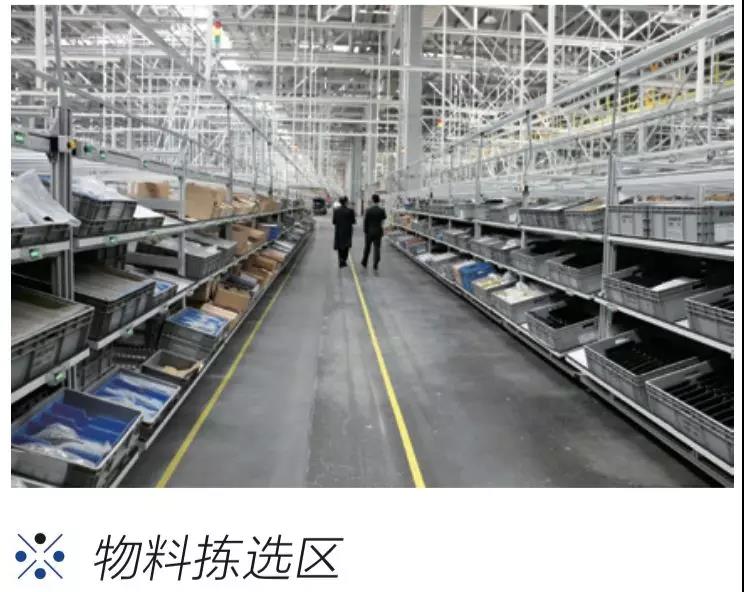
硬件方面,料架依据人体工程学设计,选用轻量化铝合金材质,采用方便、柔性化的标准件拼装。整个系统中还应用了红外体感式指示灯、扫码设备、车载电脑、穿戴设备、AGV等大量的先进硬件设备,。
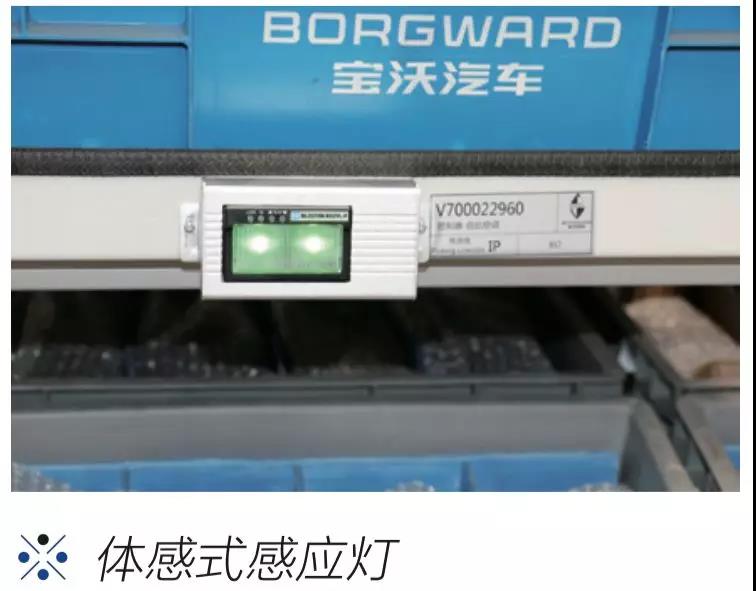
软件方面,业内首家通过LES、PTL系统的深度交互,可以满足8车型柔性化的智能拣货作业指示;首创投料防错功能,通过穿戴扫描设备和货架上安装的红外体感式指示灯,确保投料准确性;整个系统采用并联模式,以每个货格为一个单元,可以按照需求调整零部件存放位置,以满足不断增加的新车型生产需求;使用AGV智能调度系统,不同路段运行速度可调,可优化AGV数量。
整个系统的使用,减少了线边面积占用,降低了人员作业强度,使拣选和投料作业准确率高达100%。
2.无线射频识别技术(RFID)
在宝沃汽车工厂中,可以看到大量的RFID技术应用。如,所有的周转包装器具上都将装有具备抗金属干扰、抗冲击特性的RFID标签;在物料入厂检收、入库以及出库等所有物流环节都将应用RFID智能物流门,智能物流门能够快速批量读取零件包装上的RFID标签数据,信息读取准确率高达99.99%,还能实现无人化作业;在高位货架及动态库位环节应用RFID车载模块,可实现库位自动校验,出入库准确率达100%。以包装箱为单位的RFID技术创新应用,实现了整个供应链过程透明、可追溯。

宝沃汽车成为业内首批实现汽车行业供应链RFID技术集成应用的企业,创造了多项专利技术,最终将打造出无人化、透明化的物流体系,今后通过配合无人机的使用还可以实现库存无人化盘点。这为宝沃汽车工业4.0工厂实现自动化、智能化生产与物流提供了强大助力。
3.AGV厂内物料配送
在厂内物流配送环节,大规模使用AGV代替叉车或牵引车作业,大幅提高物流作业自动化率。车间内行驶的AGV搭载多台套料架配送,配合SPS系统,实现了总装车间、车身车间内智能化物料配送;目前宝沃还在研究应用激光导航AGV搭载标准包装、器具,完成车身料架工序间转运以及RDC向总装车间配送,预计于未来两年内投入使用。
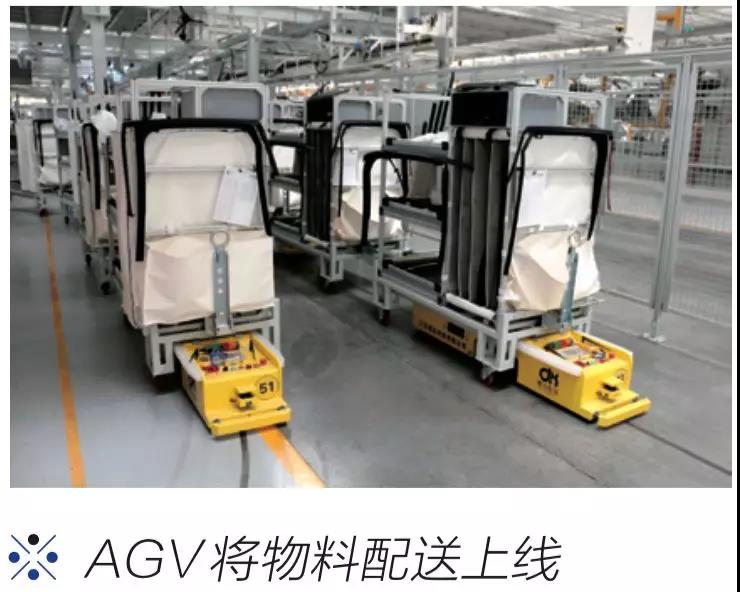
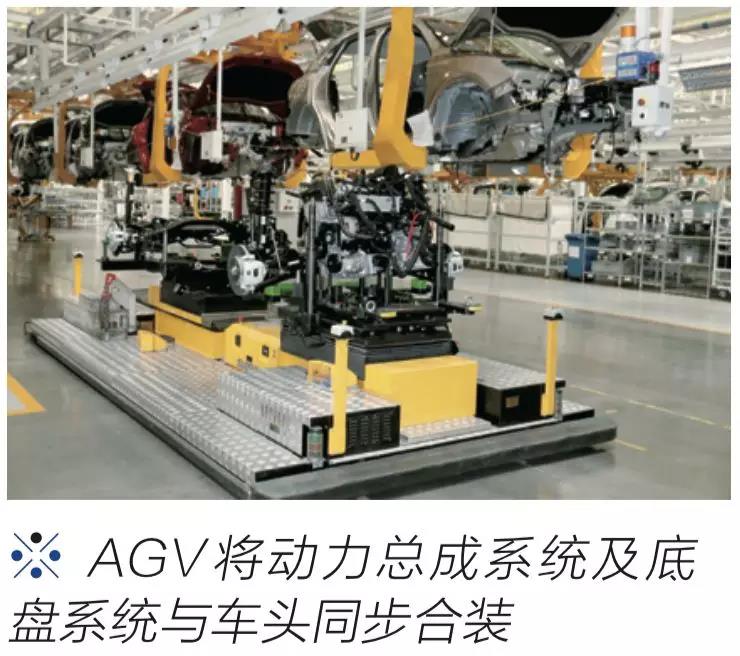
4.自动化立体库
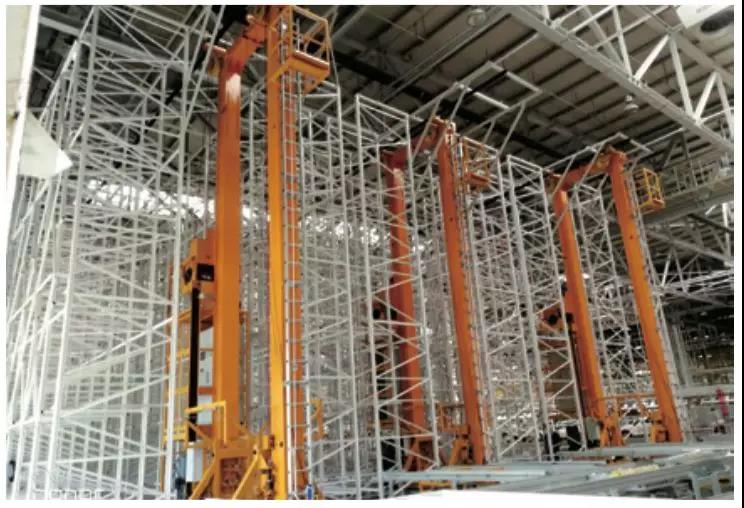
(1)座椅立体库
由于座椅供应商距离宝沃汽车工厂距离较远,且座椅种类多,库存管理难度高。经过严密考量,宝沃汽车发现无论是从成本、准确率还是效率方面考虑,在工厂内建设座椅立体库是最合适的选择。因此,宝沃汽车也成为了业内首家应用座椅立体库的企业。
整个立体库有3个巷道,1200个货位,使用高速堆垛机完成座椅的出入库、排序上线及库存管理等功能。在座椅翻包环节创新性采用了360度旋转的AGV,极大降低了机械机构的设计和制作难度。立体库作业能力可达90JPH,全部通过WCS系统管理,最大程度保障了座椅供应的柔性化和准时性。
(2)料箱立体库
在宝沃汽车的方案设计中,由料箱包装的物料入库后将被直接放置到入库道口,由一台机器臂抓取放到输送链上,自动输送入库;立体库系统与LES系统对接,LES下达出库任务后,立体库自动将物料下架并分配到相应道口,由机械手或者人放到AGV小车,完成配送。一期项目中主要实施自动化立体库,规划货位数量8000个,可兼容6种不同规格的箱型,零部件种类达2000多种。
通过料箱自动化立体库的应用,重点零部件可由自动立体库完成出入库、分拣作业,仓储能力提升5倍,分拣效率提升2倍;该自动化立体库将接RFID、SPS、自动化配送项目,实现互联互通,完成基础厂内物流的自动化平台搭建。
未来发展规划
随着智能制造的不断推进,汽车企业越来越重视搭建自动化与智能化物流体系,逐步加大投入。而宝沃汽车在智慧供应链及物流系统建设方面积极探索,勇于创新,已有多项应用成果落地,无疑走在了行业发展前列。但宝沃汽车在智慧物流体系方面的建设绝不止于此。
宝沃汽车计划到2020年初步建成智能化物流体系。为了实现这一目标,公司已经制定了三步走战略:第一阶段,完成标准化打造;第二阶段,实现自动化/省人化;第三阶段实现无人化/智能化。
曹晓刚表示,目前国内汽车产业上下游的物流自动化水平普遍较低,物流成本占比相当高。伴随着中国制造产业的不断升级,以及汽车行业竞争的不断加剧,发展智能物流必将被越来越多的汽车制造厂和零部件供应商重视。宝沃汽车高层十分重视和支持智能制造的建设,宝沃也将继续下大力气进行研发和实践,希望能够在智能物流领域的探索中为行业做出一些贡献。
随着《中国制造2025》战略的推广与实施,位于北京的宝沃汽车采用 “德国工业4.0”智能制造模式,率先在国内汽车行业建设智能工厂,以领先全球的智能制造体系入选工信部发布的“2017年中德智能制造合作试点示范项目”。宝沃汽车北京工厂实现智能制造的背后,离不开智慧物流系统及敏捷、透明化供应链体系的强大支撑力。日前,本刊记者采访了宝沃汽车集团物流规划部助理高级经理曹晓刚,请他分享了宝沃汽车智能工厂与物流系统的规划建设情况以及专业经验。
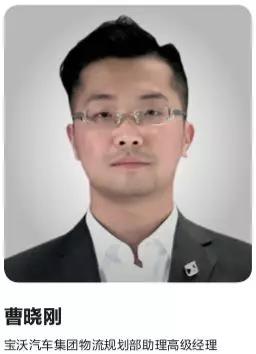
打造柔性智能工厂
2013年3月,宝沃汽车集团按照德国工业4.0标准开始建设柔性智能工厂。经过团队的精心规划设计,创新研发与严谨实施,2017年宝沃汽车柔性智能工厂正式亮相;同年9月该工厂被工信部正式评为“中德智能制造合作试点示范项目”;同年11月该工厂被科尔尼汽车商业评论授予“中国最佳工厂—柔性卓越奖”。
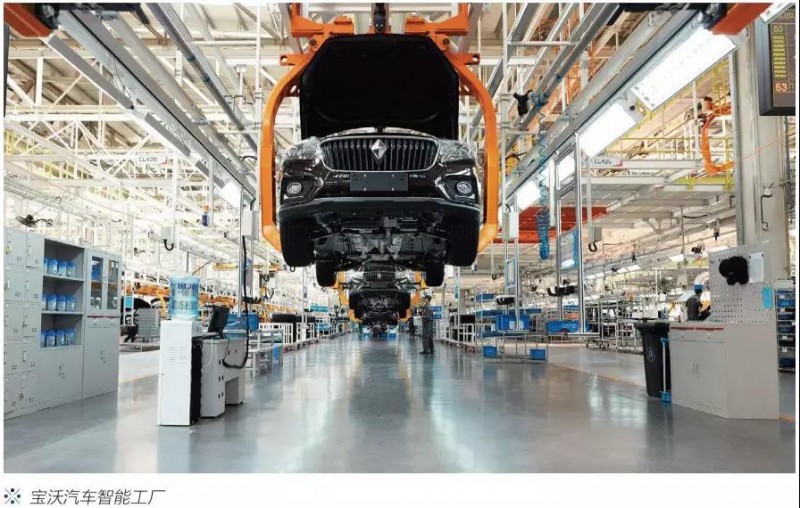
1.工厂概况
整个工厂占地面积110万m2,2015年6月工厂一期项目建设完成,生产节拍达到30JPH,生产能力达18万辆/年;2018年6月二期项目即将建设完成,生产节拍将达60JPH,生产能力将达36万辆/年。之所以说该工厂极具“柔性”,最为直观的体现就是,按照规划,宝沃汽车工厂一条生产线将可生产8种车型,从轿车到SUV,从小型车到大型车,只要整车尺寸不超过5300mm(L)×2000mm(W)×1850mm(H),轴距在2300mm-3200mm之间的车型都能够生产,甚至可支持左/右舵车型、汽油动力、柴油动力、混合动力以及新能源车型。
2.主要布局及功能
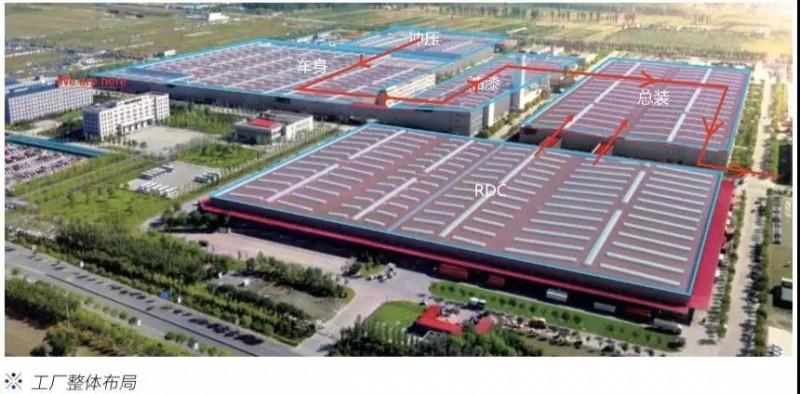
整个工厂包括冲压、车身、油漆、总装四大工艺车间以及RDC(物流分发中心),涵盖了冲压、焊装、涂装、总装、检测、物流、IT等完整的整车生产工艺。各车间主要布局及功能如下:
冲压车间占地面积2.4 万㎡,完成每个车型的23个大型内外覆盖件制造,生产线自动化程度100%。该车间应用TBS双机器人传输系统,提高不同工序间零件搬运的灵活度、负载能力及稳定性;应用线尾自动装箱系统,防止零件变形,减轻了员工作业强度。
车身车间总占地面积9.9万㎡,采用互联机器人、柔性NC定位系统、柔性夹具切换系统、自动化输送系统,标准化工艺体系、三层环网智能管理系统、国际安全标准,主线自动化率95%;采用柔性智能生产线,在同一条生产线可完成8个不同的车型无节拍损失自动切换和混线生产。
油漆车间总面积5.68万㎡,采用高泳透力电泳漆、水性面漆、2K清漆及免中涂喷涂工艺,车身防腐寿命长达12年;采用机器人自动涂胶、内外表面机器人自动喷涂、快速换色系统,快速响应客户对车身颜色的个性化需求;采用沸石转轮+RTO、TNV等废气处理技术,满足最严苛的环保标准。
总装车间总面积6.41万㎡,采用“平台化+个性化”模块化技术、“h”型的生产布局及智能物流系统,满足客户个性化的定制需求:4条SPS地面自动输送线(内饰1/内饰2/车门/仪表),零件自动上线率45%;6条大件空中自动输送线(发动机变速箱/保险杠/前端模块/轮胎/座椅/仪表等大型零件),将物料空中自动直送工位,减少2400m地面人工配送距离,降低地面物流复杂度,防止零件磕碰损伤。
RDC占地面积5万㎡,分为中小件和大件两个库区,主要负责厂内零部件的分装和配送上线。
3.信息系统建设
信息系统对于智能工厂的打造尤为重要,宝沃汽车对此非常重视。结合客户个性化订单,以超级 BOM一车一单为基础,通过ERP系统协同 MES、物流执行系统LES(Logistics Excution System),实现大规模个性化定制生产。常规车型可实时交付客户,个性化订制车型从接到订单开始包括物料准备、生产排产、制造、运输等环节,交付时间最短23天。
其中,ERP系统采用目前全球最新的基于APO on HANA 的内存处理技术,在60JPH生产节拍下,能够在15 分钟内完成排产, 30 分钟内生成物料需求计划(MRP),可实现快速排产和插单,满足大规模个性化定制的要求,比传统技术节省70%时间,目前全球仅宝沃、戴姆勒、沃尔沃在使用这项技术。
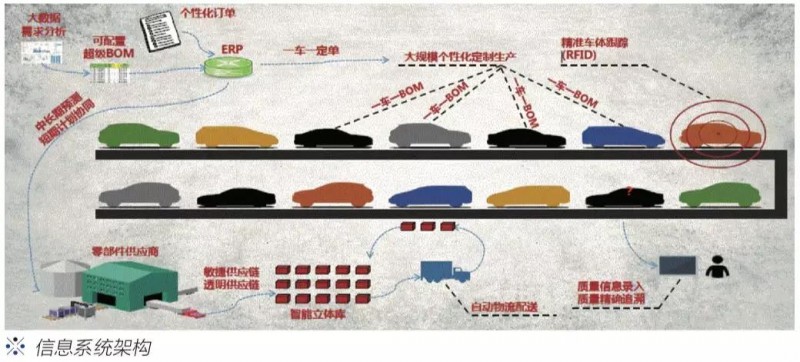
通过MES构建透明工厂,实现基于制造全流程的产线、工位及作业节点的标准化和数字化;采用工业以太网和HMI技术,实现设备互联;对生产计划、质量控制、防错、追溯进行可视化管理;对整车生产制造过程中的工艺数据及参数信息进行生命周期的数据管理。
创新开发的LES系统作为统一的物流执行平台,整合了基于GPS定位技术的运输管理系统、JIS/JIT准时化配送模式、基于RFID无线射频技术的自动化出入库管理、自动化立体库、SPS系统、大件直送等自动化上线技术,从而实现了敏捷、透明的供应链体系,能够满足8车型柔性化的生产物料需求,物流配送准确率100%,供货响应时间缩短80%。
敏捷透明化的供应链
1.循环取货规划
50%以上的供应商集中在江浙沪。限于工厂所处位置以及北京市政规划,宝沃汽车周边无法设立配套零部件产业园。在此条件下,要想降低物流运输成本和零件库存成本,节省库区面积,实现零件全过程在途监控,实施全国循环取货对于提升供应链效率、降低成本显得十分必要。因此,宝沃汽车制定了详细的循环取货机制,并在逐步实施:
对于供货距离60公里以内的本地供应商,直送到工厂;
供货距离300公里以内的京津冀供应商,优先循环取货到工厂;
供货距离1500公里以内的华东、东北供应商,优先循环取货到工厂/VMI库;
供货距离1500公里以上的其他供应商,占比很小,条件具备的循环取货。
2.创新的TWD物料拉动模式
传统的物料拉动模式依赖于现场作业人员,拉动方式粗放,异常频发,供应商装载率低,道口/叉车作业不均衡;宝沃汽车已经对119家供应商推广实施了TWD(层级拉动)模式,由信息系统替代人工,实行MIN/MAX/车辆过点拉动,时间窗合理均衡排布,最终供应商装载率、整体物流效率均大幅度提升。
3.智能入厂协同
受限于厂房面积,宝沃汽车需要严格控制供应商零部件的入厂时间,在时间和空间调度上做的更为精细。为此,通过ETCP、微信、RFID、LES多系统协作,实现了车辆即时扫描、即时排队,保证了入厂车辆均衡稳定,提高了50%作业效率。整套系统为业内首创。
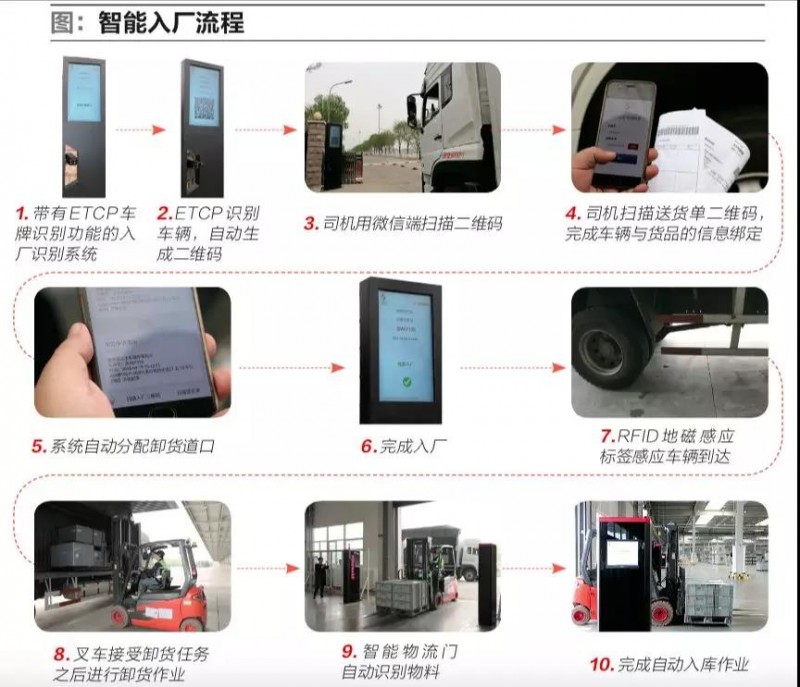
具体作业流程是:卡车到达厂区门口,ETCP车牌自动识别系统识别卡车车牌,并记录卡车出入厂时间;司机登录微信公众号,扫描送货单,送货单与卡车信息完成绑定;司机扫描门口显示屏上的二维码,系统自动分配车位;车辆进入指定区域等待,系统提示卸货时间,车辆到达卸货口;在每个卸货道口均装有RFID地磁感应标签,该标签可以自动识别车位占用及释放情况,进行卸货时间统计以及超时预警提示;车辆到达卸货道口,通过系统提示车载电脑并完成卸货作业。LES系统预提示空箱返空作业,并可统计卡车在厂时间。
4.透明供应链
曹晓刚提到,汽车产品更新换代很快,库存越多损失越大。为了降低供应链上整体库存,保证及时供应,避免断货情况,宝沃汽车将通过透明供应链管理把所有的库存和成本都实现目视化,带动整个产业链升级。
通过SAP、LES、TMS系统协作,实现供应商零部件从出厂到宝沃工厂全过程覆盖,实现低成本、高效率、高协同、透明化的供应物流模式。将LES系统管理范围从工厂扩展到VMI库甚至是零部件供应商,实现供应链全过程信息系统管理,同时与库存预警相结合,保证零件及时供应。
5.实施大数据管理
宝沃汽车与微软(Microsoft)合作,定制化开发了宝沃汽车的LES,目前已完成两期建设,完全可以支持多车型柔性化的物流及供应链业务需求。通过建立PFEP(Plan For Every Parts)数据体系,打造物流大数据系统。将零件信息、供应链物流信息、仓储信息、供应商信息、包装信息、线边信息等资源不断进行整合优化,将所有的信息化设备和系统都与大数据系统关联,并进行大数据分析。
6. 循环环保包装应用
宝沃汽车推动零部件物流全程应用循环围板箱,尺寸规格标准,便于仓储、运输等,提高了物流效率;比采用金属料架成本低;顶盖、底托为HDPE(低压高密度聚乙烯),围板为PP(聚丙烯)蜂窝板,材料环保。
智慧物流系统及装备
智慧物流系统与装备的创新应用是满足生产需求、保证物流效率的有效举措。曹晓刚坦言,想要满足8个车型的高效率混线生产对物流所带来的压力非常大。在宝沃汽车高层领导对物流系统建设的重视与支持下,经过不断的探索与实践,目前部分智慧物流系统及装备已经投入应用,还有部分项目正在实施。
1.SPS智能拣选系统
SPS智能拣选系统在汽车行业得到了普遍应用,但是宝沃汽车的SPS智能拣选系统有着独特的创新点,极度彰显了柔性化和智能化特点。
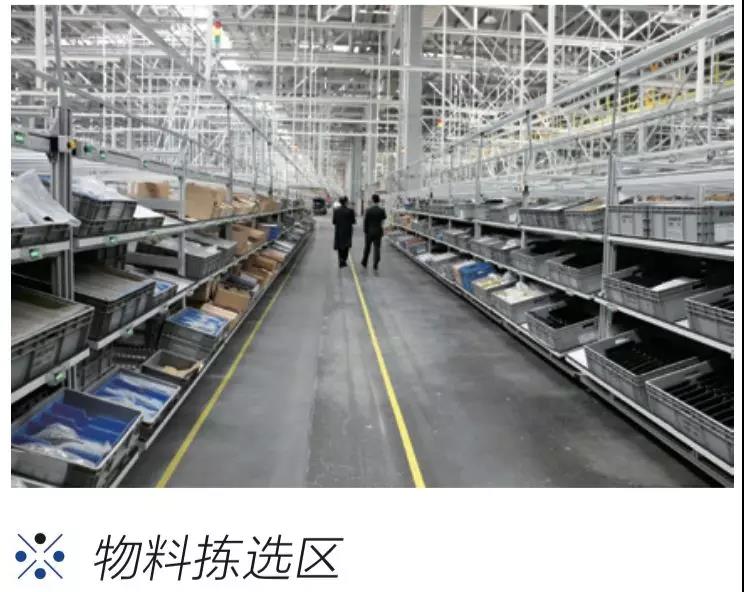
硬件方面,料架依据人体工程学设计,选用轻量化铝合金材质,采用方便、柔性化的标准件拼装。整个系统中还应用了红外体感式指示灯、扫码设备、车载电脑、穿戴设备、AGV等大量的先进硬件设备,。
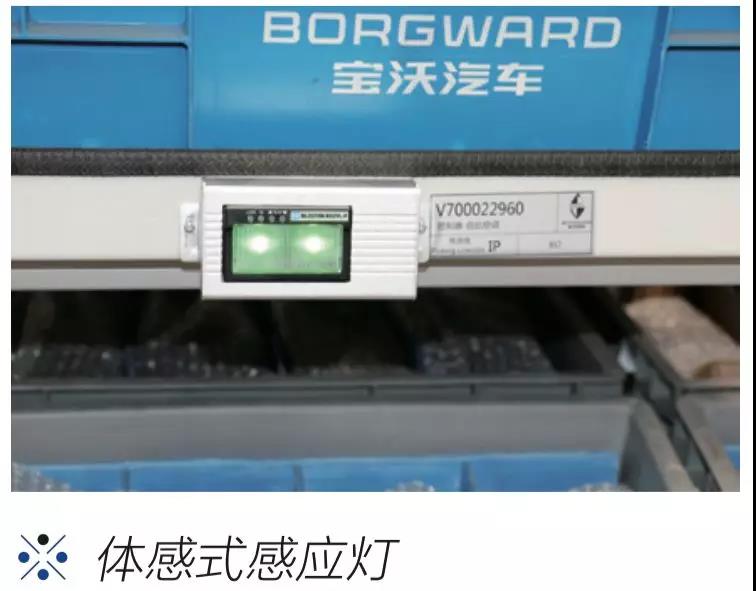
软件方面,业内首家通过LES、PTL系统的深度交互,可以满足8车型柔性化的智能拣货作业指示;首创投料防错功能,通过穿戴扫描设备和货架上安装的红外体感式指示灯,确保投料准确性;整个系统采用并联模式,以每个货格为一个单元,可以按照需求调整零部件存放位置,以满足不断增加的新车型生产需求;使用AGV智能调度系统,不同路段运行速度可调,可优化AGV数量。
整个系统的使用,减少了线边面积占用,降低了人员作业强度,使拣选和投料作业准确率高达100%。
2.无线射频识别技术(RFID)
在宝沃汽车工厂中,可以看到大量的RFID技术应用。如,所有的周转包装器具上都将装有具备抗金属干扰、抗冲击特性的RFID标签;在物料入厂检收、入库以及出库等所有物流环节都将应用RFID智能物流门,智能物流门能够快速批量读取零件包装上的RFID标签数据,信息读取准确率高达99.99%,还能实现无人化作业;在高位货架及动态库位环节应用RFID车载模块,可实现库位自动校验,出入库准确率达100%。以包装箱为单位的RFID技术创新应用,实现了整个供应链过程透明、可追溯。

宝沃汽车成为业内首批实现汽车行业供应链RFID技术集成应用的企业,创造了多项专利技术,最终将打造出无人化、透明化的物流体系,今后通过配合无人机的使用还可以实现库存无人化盘点。这为宝沃汽车工业4.0工厂实现自动化、智能化生产与物流提供了强大助力。
3.AGV厂内物料配送
在厂内物流配送环节,大规模使用AGV代替叉车或牵引车作业,大幅提高物流作业自动化率。车间内行驶的AGV搭载多台套料架配送,配合SPS系统,实现了总装车间、车身车间内智能化物料配送;目前宝沃还在研究应用激光导航AGV搭载标准包装、器具,完成车身料架工序间转运以及RDC向总装车间配送,预计于未来两年内投入使用。
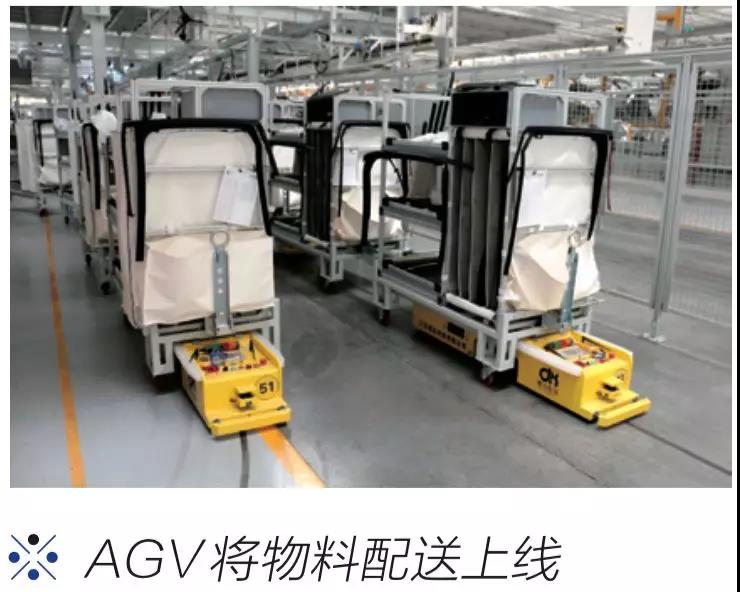
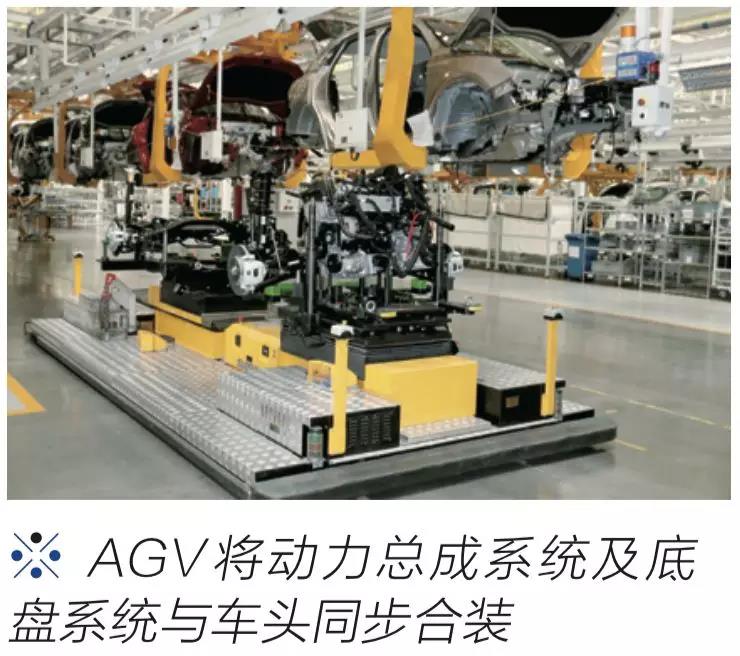
4.自动化立体库
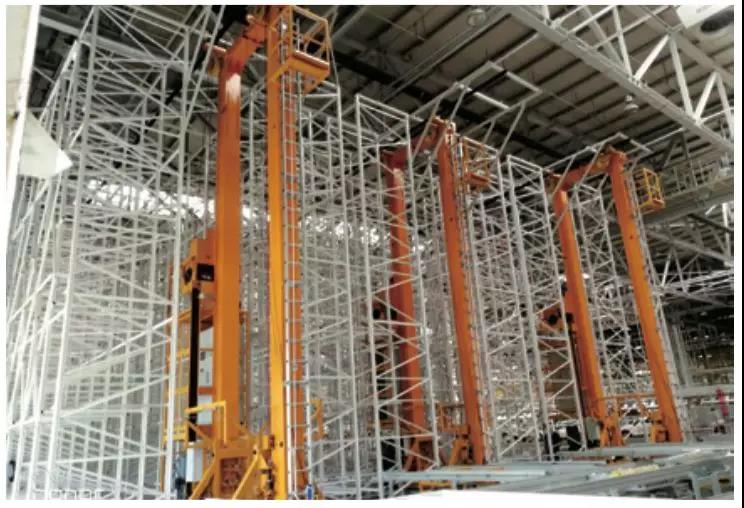
(1)座椅立体库
由于座椅供应商距离宝沃汽车工厂距离较远,且座椅种类多,库存管理难度高。经过严密考量,宝沃汽车发现无论是从成本、准确率还是效率方面考虑,在工厂内建设座椅立体库是最合适的选择。因此,宝沃汽车也成为了业内首家应用座椅立体库的企业。
整个立体库有3个巷道,1200个货位,使用高速堆垛机完成座椅的出入库、排序上线及库存管理等功能。在座椅翻包环节创新性采用了360度旋转的AGV,极大降低了机械机构的设计和制作难度。立体库作业能力可达90JPH,全部通过WCS系统管理,最大程度保障了座椅供应的柔性化和准时性。
(2)料箱立体库
在宝沃汽车的方案设计中,由料箱包装的物料入库后将被直接放置到入库道口,由一台机器臂抓取放到输送链上,自动输送入库;立体库系统与LES系统对接,LES下达出库任务后,立体库自动将物料下架并分配到相应道口,由机械手或者人放到AGV小车,完成配送。一期项目中主要实施自动化立体库,规划货位数量8000个,可兼容6种不同规格的箱型,零部件种类达2000多种。
通过料箱自动化立体库的应用,重点零部件可由自动立体库完成出入库、分拣作业,仓储能力提升5倍,分拣效率提升2倍;该自动化立体库将接RFID、SPS、自动化配送项目,实现互联互通,完成基础厂内物流的自动化平台搭建。
未来发展规划
随着智能制造的不断推进,汽车企业越来越重视搭建自动化与智能化物流体系,逐步加大投入。而宝沃汽车在智慧供应链及物流系统建设方面积极探索,勇于创新,已有多项应用成果落地,无疑走在了行业发展前列。但宝沃汽车在智慧物流体系方面的建设绝不止于此。
宝沃汽车计划到2020年初步建成智能化物流体系。为了实现这一目标,公司已经制定了三步走战略:第一阶段,完成标准化打造;第二阶段,实现自动化/省人化;第三阶段实现无人化/智能化。
曹晓刚表示,目前国内汽车产业上下游的物流自动化水平普遍较低,物流成本占比相当高。伴随着中国制造产业的不断升级,以及汽车行业竞争的不断加剧,发展智能物流必将被越来越多的汽车制造厂和零部件供应商重视。宝沃汽车高层十分重视和支持智能制造的建设,宝沃也将继续下大力气进行研发和实践,希望能够在智能物流领域的探索中为行业做出一些贡献。
编辑推荐
最新资讯
-
2025上海国际汽车成形制造产业对话会
2025-04-26 19:14
-
旭化成微电子开始批量生产用于环保发
2025-04-24 16:00
-
华为、地平线、大众、东风、起亚等引
2025-04-24 08:27
-
全球产业链聚沪 共探双碳新路径 SNEC
2025-04-18 18:05
-
柯马签订具有约束力的协议收购 Autom
2025-04-17 13:01