我国锻压行业发展及典型企业智造案例
2018-07-02 11:46:45· 来源:中国质量报
在国民经济生产和国防建设中,锻压行业是不可缺少的重要部分,它为各种机械产品和军工装备生产各种重要基础零件。锻压设备在航空航天、汽车制造、交通运输、冶金化工等重要工业部门得到广泛应用。锻件的质量直接决定主机的性能、整机质量、使用寿命、安全性和可靠性。
在国民经济生产和国防建设中,锻压行业是不可缺少的重要部分,它为各种机械产品和军工装备生产各种重要基础零件。锻压设备在航空航天、汽车制造、交通运输、冶金化工等重要工业部门得到广泛应用。锻件的质量直接决定主机的性能、整机质量、使用寿命、安全性和可靠性。
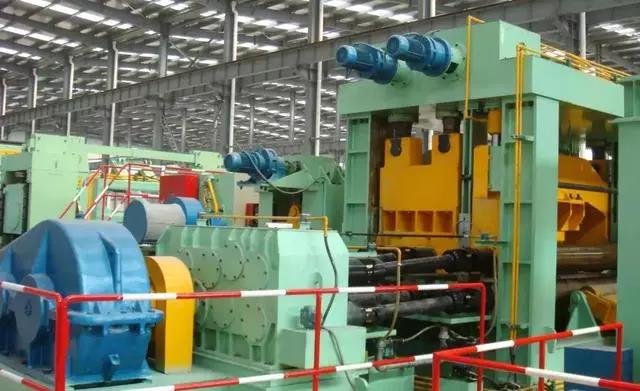
一、我国锻压行业发展现状
中国目前拥有万吨以上自由锻造液压机25台、万吨以上模锻液压机8台、万吨以上挤压机12台,在建和建成的万吨以上多向模锻液压机8台;2016年,中国锻件总产量1016.84万吨位居世界第一。具有全套水电锻件、航空、航天等高端装备制造业大型模锻件及精密环形锻件的生产能力、各种铝型材和合金铜材的生产技术,物理模拟实验方法与手段日益丰富,高温合金、钛合金、耐热不锈钢等高端材料开始进行锻造成形并交付使用。数字化、信息化工厂模式开始有应用尝试,锻造车间的现场管理得到很大改善,模具高速铣加工和锻造自动化等先进技术进入推广和普及阶段。
我国锻件产量虽已进入世界生产大国,但还不是锻件生产强国,设备构成、等级、技术水平和所生产的锻压件品种、精度、工艺水平与国外相比有很大差距,尚需要改进提高。
首先,现在我国大型自由锻件生产处于“过剩”与“短缺”的双重压力,一般性大锻件供大于求,对技术含量和质量要求很高的大型自由锻件,如百万千瓦汽轮机高中低压转子、特大支承辊、大型高温高压容器筒体等,生产能力低或不生产尚需进口。一辆汽车超过80%零部件为锻压设备加工,汽车工业是最庞大的锻压设备消费产业之一。在汽车锻件方面,现卡车用模锻件全部由我国自己生产,还接受国外订货,但轿车模锻件由于车型的知识产权不在我们手中,大部分仍需进口。
其次,我国目前锻压设备的发展尚不能完全满足国内锻压生产行业发展的需要,一些高端的锻压设备机会全部被发达国家的锻压设备企业所控制。长期以来,我国锻压装备制造企业,向市场提供同质化的锻压装备产品较多,而技术含量高、附加值高、个性化、专用的锻压装备较少,造成同质化产品竞争严重,利润率不高。在锻造设备方面,目前还没有一家企业能完整地、全系列、高质量地生产各种模锻机械压力机生产线。锻压设备性能和辅助设施的自动化、机械化水平偏低,影响锻件产量和精度,尚需不断提高。例如,我国热锻模寿命一般在4000~6000件,主要受工艺设计、锻造设备、加热、润滑等因素影响,国外模具寿命在10000~15000件,模具寿命是影响锻件成本的主要因素,提高锻模的寿命是锻造企业共同的使命。
此外,钢厂未全面开发冷、温锻造专用钢材,年轻的专业人才缺乏,材料数据库的积累不足、数字化设计技术应用不广等等。行业里对材料、锻造、热处理和机械加工工艺一体化研究体系认识和实施也不广泛,锻压行业企业还没有一套影响或制约材料供应商的标准体系。
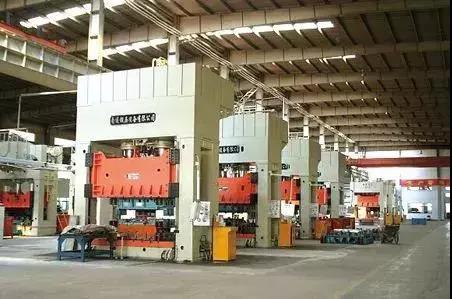
二、未来行业发展方向
未来,研究和推广锻压行业关键工艺和装备,提升智能化制造水平将成为重点。其中,不断提升我国锻压装备行业中的装备、工艺、模具、制造流程及服务耦合一体的智能化水平是关键。丰富的产品种类和行业飞速的新旧更替导致市场竞争激烈化。传统的加工单一品种的刚性生产线已不适应目前市场发展的需要,高柔性和高效率的自动化锻压设备,已成为锻造冲压技术及装备发展的主要潮流。
国内锻压企业应该从提高产品的质量、产品的一致性、产品精度等多方面着手,改变“制造大国”而不是“制造强国”的现状。减少低水平重复性投入,加大专业化设备的投入,建设绿色环保的锻压产业。
快速换模装置、封闭高度快速调整装置、步进梁机械手的开发、高性能滑动轴承的开发以及高性能加热设备的开发都是非常热门的方向。材料专家、锻造工艺专家、热处理专家以及模具设计、质量管理、企业管理、体系维护、模具加工中心操作和三维造型与编程等都是急需的人才。
同时,开发智能锻压制造系统,应用MES重点开发其中的计划与调度、工艺与执行、过程质量控制以及设备管理与远程诊断等模块;开发企业资源管理系统(ERP),针对用户需求订单下达生产计划,并接受生产反馈以及处理与存储相关信息。同时,采用工业以太网实现基础层、执行层与管理层的互联互通。
此外,锻压行业需要建立标准体系,制定和完善各类标准。以锻压制造过程的智能化为战略目标,当前应以数字化设计与制造为关键手段,在平台建设、材料及工艺环境数据库完善和典型件应用等方面着重推进,逐步建立锻压行业不同细分领域的工艺及模具数字化设计与制造平台及工程应用中心,从而提高全行业工艺及模具设计的科学化和智能化水平。
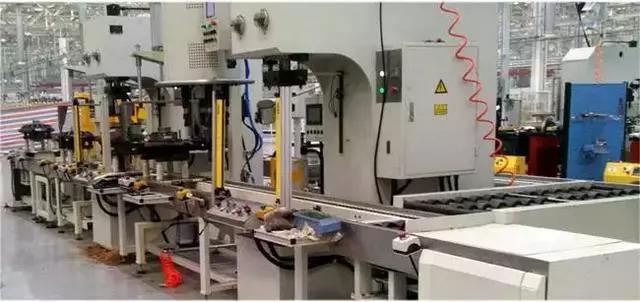
三、典型企业智造案例
扬力集团是实力雄厚的数控压力机、折弯机、剪板机、液压机、激光切割机、热模锻压力机和金属板材一体化解决方案的制造商。扬力多年坚持创新带动企业实现转型发展,领航我国成型机床产学研结合之路,研发成果层出不穷。截至今年一季度,扬力集团累计申请专利419项,其中发明专利62项。
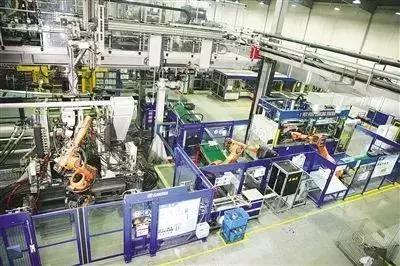
以市场为导向精准研发
2017年底,海尔集团第一智慧云厨房互联工厂在青岛海尔工业园区建成,同时海尔第一条由扬力自主研发的高端“云厨”设备生产的吸油烟机智能联线装备在海尔工厂下线。面对海尔互联工厂高端制造的创新理念,扬力集团充分进行现代信息技术与高端制造深度融合,为海尔集团量身定制了符合国际互联工厂和智能型“云厨”高端制造柔性冲压生产线。这一具有国际领先水平的高端装备,由7台扬力自主研制的龙门双点压力机、8台全伺服液压机、13台六轴机器人、5台桁架机械手、3套翻转式工作台、4套废料集成装置及1套视觉检测系统、1套成品升降式输送机和23套模具组成,实现了产品从各种合金钢原料自动上线,到多点冲压、自动传递、自动翻转、成品输送、废料收集、模具快速更换、到产成品在线视觉检测等全自动无人冲压作业。
“十二五”以来,扬力集团密切关注国家产业发展动向,紧密围绕我国汽车、船舶、电力、航天航空、轨道交通、新能源等国民经济支柱产业,针对高端成形机床国产化迫切需求,围绕高端数控冲床、折剪机、激光切割机、伺服液压机、大吨位闭式多点多工位压力机、热模锻压力机等8大系列产品体系,开发研制出TE42500型抗偏载闭式四点多工位压力机、HFP1350型热模锻压机、WL2404F型大幅面激光切割机等具有国内领先、局部达国际先进水平的新产品80多项,这些“重器”代表了我国成型机床转型发展、赶超国际先进水平的显著成就。其中由扬力自主研发的TS4-1500型闭式四点多工位压力机出口世界500强的美国伊莱克斯公司,使我国高精密多工位压力机实施由进口到出口的重大历史性转折。以YL234C-2500型液压机打头的6200吨大型液压机+机器人全自动冲压生产线填补我国空白,替代进口,投放上海大众汽车覆盖件制造厂。
目前扬力投放市场的主机设备及自动化联线装备,广泛配套应用于华晨宝马以及通用、大众等国内外品牌汽车制造商。顺应家电行业应用需求,开发研制的大型液晶电视机背板、电冰箱门壳,洗衣机、微波炉箱体等自动柔性冲压生产线,广泛应用于海尔、美的、长虹、TCL等国际知名家电制造业巨头。扬力以市场为导向的产品研发战略,为我国成形机床开拓国内外市场赢得了主动权,企业的产销规模也进一步刷新了历史纪录。今年1~3月,扬力实现销售额5.59亿元,其中整机销售5.02亿元,实现工业增加值1.56亿元,各项经济技术指标继续在全国同行业保持领先地位。
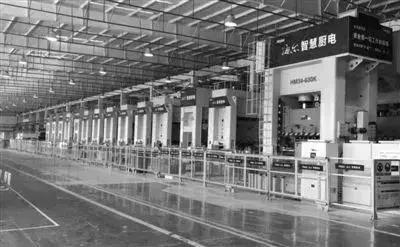
深化互联网“智造”
互联网作为新一代信息技术与现代工业融合发展催生的新生事物,是实现生产制造领域全要素、全产业链、全价值链的关键支撑,是工业经济数字化、网络化、智能化发展的重要载体。
早在“十二五”期间,扬力集团就在精机制造公司率先部署PLM生命周期管理与AMPC敏捷制造执行系统,实现资源配置与生产调度。2015年扬力集团在我国锻压机床行业率先推出P-MES制造执行系统,标志着“互联网+扬力冲压设备”已进入大数据应用平台。2016年以来,扬力在全行业率先推进数字化车间与智能型工厂建设。通过传感技术与控制系统,实施产品制造体系信息化与大数据处理,试行外销设备在用户生产过程的监控及使用故障远程诊断与处理,努力向数字化车间与智能型工厂迈进,对提升智能化设备制造,推动企业创新转型发挥了重大推动作用。
为了加快“互联网+先进制造”步伐,扬力目前推出了“设备在网上,服务在掌上,数据在云上,管理在线上”的四步走战略目标。第一步:设备在网上。通过MES、ERP的有效集成,自动采集生产现场的实时数据,实现生产的自动化管理,精确掌握生产流程,提高生产过程的可控性,减少生产线上人工干预,推进工业智能升级。第二步:服务在掌上。通过运行监控及远程管理,实现闲置资源调配,业务资源匹配,维修资源配套的网络化运作,提高企业的网络运行程序。第三步:数据在云上。未来全球竞争模式进入离线的物理世界和实时连线的比特世界与数字网络化空间,建立超大规模的海量数据分析系统,集成RCT大数据、云空间、人工智能、虚拟技术,形成大数据、云计算、移动互联三大技术支撑体系。第四步:管理在线上。通过企业链、价值链、供需链和空间链的优化配置与提升,打通上下游之间的各个环节,实现企业竞争力提升,使产业链上下游实现提高效率、降低成本的多赢局面,最终实现我国锻压设备智能制造少人及无人操作的控制目标。
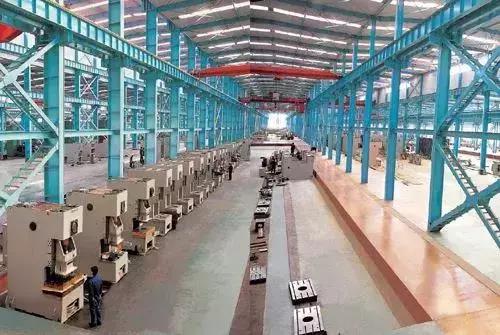
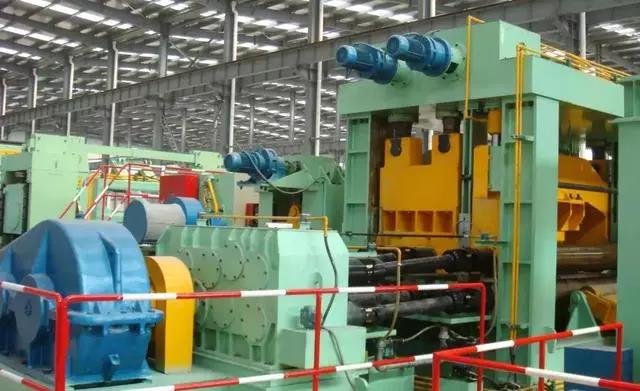
一、我国锻压行业发展现状
中国目前拥有万吨以上自由锻造液压机25台、万吨以上模锻液压机8台、万吨以上挤压机12台,在建和建成的万吨以上多向模锻液压机8台;2016年,中国锻件总产量1016.84万吨位居世界第一。具有全套水电锻件、航空、航天等高端装备制造业大型模锻件及精密环形锻件的生产能力、各种铝型材和合金铜材的生产技术,物理模拟实验方法与手段日益丰富,高温合金、钛合金、耐热不锈钢等高端材料开始进行锻造成形并交付使用。数字化、信息化工厂模式开始有应用尝试,锻造车间的现场管理得到很大改善,模具高速铣加工和锻造自动化等先进技术进入推广和普及阶段。
我国锻件产量虽已进入世界生产大国,但还不是锻件生产强国,设备构成、等级、技术水平和所生产的锻压件品种、精度、工艺水平与国外相比有很大差距,尚需要改进提高。
首先,现在我国大型自由锻件生产处于“过剩”与“短缺”的双重压力,一般性大锻件供大于求,对技术含量和质量要求很高的大型自由锻件,如百万千瓦汽轮机高中低压转子、特大支承辊、大型高温高压容器筒体等,生产能力低或不生产尚需进口。一辆汽车超过80%零部件为锻压设备加工,汽车工业是最庞大的锻压设备消费产业之一。在汽车锻件方面,现卡车用模锻件全部由我国自己生产,还接受国外订货,但轿车模锻件由于车型的知识产权不在我们手中,大部分仍需进口。
其次,我国目前锻压设备的发展尚不能完全满足国内锻压生产行业发展的需要,一些高端的锻压设备机会全部被发达国家的锻压设备企业所控制。长期以来,我国锻压装备制造企业,向市场提供同质化的锻压装备产品较多,而技术含量高、附加值高、个性化、专用的锻压装备较少,造成同质化产品竞争严重,利润率不高。在锻造设备方面,目前还没有一家企业能完整地、全系列、高质量地生产各种模锻机械压力机生产线。锻压设备性能和辅助设施的自动化、机械化水平偏低,影响锻件产量和精度,尚需不断提高。例如,我国热锻模寿命一般在4000~6000件,主要受工艺设计、锻造设备、加热、润滑等因素影响,国外模具寿命在10000~15000件,模具寿命是影响锻件成本的主要因素,提高锻模的寿命是锻造企业共同的使命。
此外,钢厂未全面开发冷、温锻造专用钢材,年轻的专业人才缺乏,材料数据库的积累不足、数字化设计技术应用不广等等。行业里对材料、锻造、热处理和机械加工工艺一体化研究体系认识和实施也不广泛,锻压行业企业还没有一套影响或制约材料供应商的标准体系。
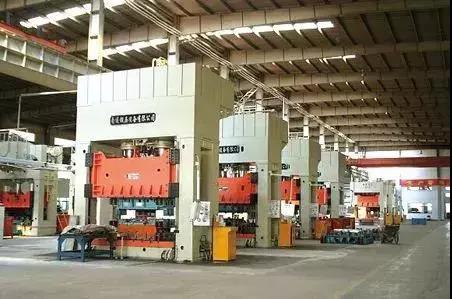
二、未来行业发展方向
未来,研究和推广锻压行业关键工艺和装备,提升智能化制造水平将成为重点。其中,不断提升我国锻压装备行业中的装备、工艺、模具、制造流程及服务耦合一体的智能化水平是关键。丰富的产品种类和行业飞速的新旧更替导致市场竞争激烈化。传统的加工单一品种的刚性生产线已不适应目前市场发展的需要,高柔性和高效率的自动化锻压设备,已成为锻造冲压技术及装备发展的主要潮流。
国内锻压企业应该从提高产品的质量、产品的一致性、产品精度等多方面着手,改变“制造大国”而不是“制造强国”的现状。减少低水平重复性投入,加大专业化设备的投入,建设绿色环保的锻压产业。
快速换模装置、封闭高度快速调整装置、步进梁机械手的开发、高性能滑动轴承的开发以及高性能加热设备的开发都是非常热门的方向。材料专家、锻造工艺专家、热处理专家以及模具设计、质量管理、企业管理、体系维护、模具加工中心操作和三维造型与编程等都是急需的人才。
同时,开发智能锻压制造系统,应用MES重点开发其中的计划与调度、工艺与执行、过程质量控制以及设备管理与远程诊断等模块;开发企业资源管理系统(ERP),针对用户需求订单下达生产计划,并接受生产反馈以及处理与存储相关信息。同时,采用工业以太网实现基础层、执行层与管理层的互联互通。
此外,锻压行业需要建立标准体系,制定和完善各类标准。以锻压制造过程的智能化为战略目标,当前应以数字化设计与制造为关键手段,在平台建设、材料及工艺环境数据库完善和典型件应用等方面着重推进,逐步建立锻压行业不同细分领域的工艺及模具数字化设计与制造平台及工程应用中心,从而提高全行业工艺及模具设计的科学化和智能化水平。
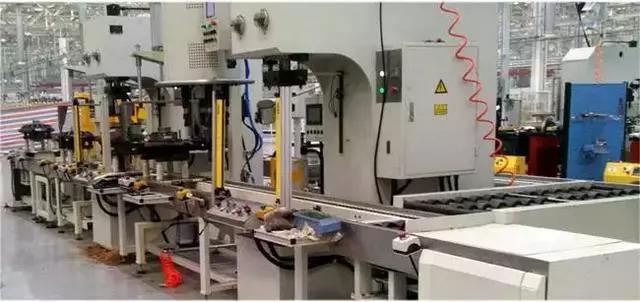
三、典型企业智造案例
扬力集团是实力雄厚的数控压力机、折弯机、剪板机、液压机、激光切割机、热模锻压力机和金属板材一体化解决方案的制造商。扬力多年坚持创新带动企业实现转型发展,领航我国成型机床产学研结合之路,研发成果层出不穷。截至今年一季度,扬力集团累计申请专利419项,其中发明专利62项。
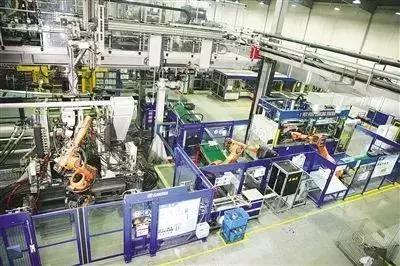
以市场为导向精准研发
2017年底,海尔集团第一智慧云厨房互联工厂在青岛海尔工业园区建成,同时海尔第一条由扬力自主研发的高端“云厨”设备生产的吸油烟机智能联线装备在海尔工厂下线。面对海尔互联工厂高端制造的创新理念,扬力集团充分进行现代信息技术与高端制造深度融合,为海尔集团量身定制了符合国际互联工厂和智能型“云厨”高端制造柔性冲压生产线。这一具有国际领先水平的高端装备,由7台扬力自主研制的龙门双点压力机、8台全伺服液压机、13台六轴机器人、5台桁架机械手、3套翻转式工作台、4套废料集成装置及1套视觉检测系统、1套成品升降式输送机和23套模具组成,实现了产品从各种合金钢原料自动上线,到多点冲压、自动传递、自动翻转、成品输送、废料收集、模具快速更换、到产成品在线视觉检测等全自动无人冲压作业。
“十二五”以来,扬力集团密切关注国家产业发展动向,紧密围绕我国汽车、船舶、电力、航天航空、轨道交通、新能源等国民经济支柱产业,针对高端成形机床国产化迫切需求,围绕高端数控冲床、折剪机、激光切割机、伺服液压机、大吨位闭式多点多工位压力机、热模锻压力机等8大系列产品体系,开发研制出TE42500型抗偏载闭式四点多工位压力机、HFP1350型热模锻压机、WL2404F型大幅面激光切割机等具有国内领先、局部达国际先进水平的新产品80多项,这些“重器”代表了我国成型机床转型发展、赶超国际先进水平的显著成就。其中由扬力自主研发的TS4-1500型闭式四点多工位压力机出口世界500强的美国伊莱克斯公司,使我国高精密多工位压力机实施由进口到出口的重大历史性转折。以YL234C-2500型液压机打头的6200吨大型液压机+机器人全自动冲压生产线填补我国空白,替代进口,投放上海大众汽车覆盖件制造厂。
目前扬力投放市场的主机设备及自动化联线装备,广泛配套应用于华晨宝马以及通用、大众等国内外品牌汽车制造商。顺应家电行业应用需求,开发研制的大型液晶电视机背板、电冰箱门壳,洗衣机、微波炉箱体等自动柔性冲压生产线,广泛应用于海尔、美的、长虹、TCL等国际知名家电制造业巨头。扬力以市场为导向的产品研发战略,为我国成形机床开拓国内外市场赢得了主动权,企业的产销规模也进一步刷新了历史纪录。今年1~3月,扬力实现销售额5.59亿元,其中整机销售5.02亿元,实现工业增加值1.56亿元,各项经济技术指标继续在全国同行业保持领先地位。
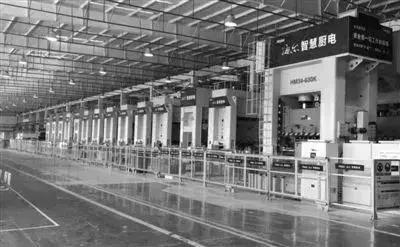
深化互联网“智造”
互联网作为新一代信息技术与现代工业融合发展催生的新生事物,是实现生产制造领域全要素、全产业链、全价值链的关键支撑,是工业经济数字化、网络化、智能化发展的重要载体。
早在“十二五”期间,扬力集团就在精机制造公司率先部署PLM生命周期管理与AMPC敏捷制造执行系统,实现资源配置与生产调度。2015年扬力集团在我国锻压机床行业率先推出P-MES制造执行系统,标志着“互联网+扬力冲压设备”已进入大数据应用平台。2016年以来,扬力在全行业率先推进数字化车间与智能型工厂建设。通过传感技术与控制系统,实施产品制造体系信息化与大数据处理,试行外销设备在用户生产过程的监控及使用故障远程诊断与处理,努力向数字化车间与智能型工厂迈进,对提升智能化设备制造,推动企业创新转型发挥了重大推动作用。
为了加快“互联网+先进制造”步伐,扬力目前推出了“设备在网上,服务在掌上,数据在云上,管理在线上”的四步走战略目标。第一步:设备在网上。通过MES、ERP的有效集成,自动采集生产现场的实时数据,实现生产的自动化管理,精确掌握生产流程,提高生产过程的可控性,减少生产线上人工干预,推进工业智能升级。第二步:服务在掌上。通过运行监控及远程管理,实现闲置资源调配,业务资源匹配,维修资源配套的网络化运作,提高企业的网络运行程序。第三步:数据在云上。未来全球竞争模式进入离线的物理世界和实时连线的比特世界与数字网络化空间,建立超大规模的海量数据分析系统,集成RCT大数据、云空间、人工智能、虚拟技术,形成大数据、云计算、移动互联三大技术支撑体系。第四步:管理在线上。通过企业链、价值链、供需链和空间链的优化配置与提升,打通上下游之间的各个环节,实现企业竞争力提升,使产业链上下游实现提高效率、降低成本的多赢局面,最终实现我国锻压设备智能制造少人及无人操作的控制目标。
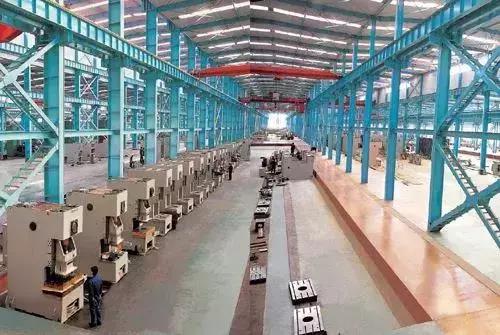
- 下一篇:锂电池制造工艺全解析
- 上一篇:KUKA 与伟本智能签订战略合作协议 打造双赢新格局
举报 0
收藏 0
分享 158
-
冲压技术在电机叠片制造的应用
2024-09-06 -
车身零部件包边质量控制要点
2024-09-05 -
轻量化技术——热汽胀形工艺技术解析
2024-09-04 -
高强板车身件冲压技术
2024-09-02
最新资讯
-
全球产业链聚沪 共探双碳新路径 SNEC
2025-04-18 18:05
-
柯马签订具有约束力的协议收购 Autom
2025-04-17 13:01
-
高效协同新范式:比亚迪叉车领创智能
2025-04-17 10:04
-
埃马克德国总部迎来中国社科院工业经
2025-04-15 09:40
-
埃马克这项全新应用即将在CIMT惊艳首
2025-04-15 09:37